
Метод_практ_СДВЗ
.pdfПрименение чугуна с шаровидным графитом дает для валов следующие основные преимущества (по сравнению со стальными):
а) снижение стоимости изготовления за счет меньших затрат на материал (в ~3 раза) и время обработки (в ~2-3 раза);
б) возможность использования оптимальных конструктивных форм коленчатого вала, снижающих концентрацию напряжений и увеличивающих его прочность;
в) повышенную износостойкость шеек, благодаря наличию в чугуне графита и хорошей смачиваемости маслом поверхности шеек;
г) повышенную надежность работы коленчатого вала, благодаря относительно высокой циклической вязкости чугуна и меньшей чувствительности к концентрации напряжений (чем у стали);
д) хорошую обрабатываемость при твердости до НВ ≤265.
К основным недостаткам чугунных литых валов следует отнести: 1) более низкие механические свойства, чем у стальных кованых; 2) трудность обнаружения внутренних литейных пороков.
Термообработка у разных заводов различная. Более высокие механические свойства дает нормализация при t = 880 - 900° С и последующий отпуск при t = 570 - 600° С.
Анализ поломок коленчатых валов в эксплуатации показывает, что разрушения чугунных валов (как и стальных) почти всегда начинается в виде усталостных трещин в галтелях шатунной и коренной шеек.
Повышение усталостной прочности коленчатых валов достигается конструктивными и технологическими методами.
Основные методы, применяемые для поверхностного упрочнения валов, следующие:
1)химико-термические (азотирование, цементация, цианирование);
2)поверхностная закалка токами высокой частоты (т. в. ч.);
3)наклеп поверхностного слоя (обкатка роликами, обдувка дробью);
4)комбинированные методы.
При применении указанных методов происходит упрочнение металла поверхностного слоя и, кроме того, в детали создаются остаточные напряжения (обычно сжимающие) при этом повышаются пределы выносливости (до 2-3 раз) и долговечность детали.
Азотирование является одним из наиболее эффективных способов повышения усталостной прочности. Как показывают эксплуатационные исследования с коленчатыми валами из легированных сталей, азотирование повышает τ-1 коленчатых валов на 30-40%. При азотировании ослабляется также влияние концентрации напряжений на усталостную прочность поверхностного слоя поверхности. После азотирования не рекомендуется производить какую-либо механическую обработку, так как, например, сверление отверстия для масла после азотирования снижает примерно в два раза сопротивляемость вала знакопеременному кручению, а прижог галтели при шлифовке вызывает понижение усталостной прочности на 20-25%.
91
Цементация и цианирование также повышают усталостную прочность
валов.
Поверхностная закалка т. в.ч. повышает предел выносливости до 90% на гладких образцах и в 1,5—2,5 раза на надрезанных образцах.
Опыты с образцами из легированных сталей показали, что при цементации коэффициенты концентрации в зоне отверстий снижаются на
30—40%.
Помимо указанных методов упрочнения, с успехом применяются наклеп поверхностей вала и полировка внутренних и наружных поверхностей отверстий и др.
При наклепе создается поверхностный слой с остаточными сжимающими напряжениями и, кроме того, ликвидируются субмикроскопические трещины, являющиеся часто источником возникновения усталостных разрушений.
Поверхностный наклеп рассчитан на повышение предела выносливости гладких образцов до 40%, а образцов с концентрацией напряжений до 100—200%.
При обкатке роликами галтелей, обдувке дробью и обжатием
шариком краев масляных отверстий коленчатых валов многооборотных двигателей предел усталости при изгибе повышается до 40%, а при кручении -
до 20%.
Помимо повышения усталостной прочности при технологических методах поверхностного упрочнения, такие методы, как наклеп, поверхностная закалка т. в. ч., азотирование, являются вместе с тем весьма эффективными средствами повышения сопротивления коррозионной усталости коленчатых валов.
Следует еще отметить, что применение азотирования, хромирования и других видов термохимической и других видов обработки поверхностного слоя чугунных валов (как и у стальных) повышает их усталостную прочность и износостойкость.
Крейцкопфный механизм (рис. 12) применяется в основном в малооборотных и крупных судовых дизелях (D > 450 мм) для того, чтобы обеспечить возможно большую надежность и моторесурс поршневой группе. При наличии крейцкопфного механизма восприятие нормальных давлений поршня на цилиндровую втулку переносится на ползуны и их направляющие. В связи со значительно лучшими условиями работы крейцкопфа в качестве направляющего механизма для поршня отношение λ = R/L может быть сокращено до λ =1/4,0÷1/3,6. Благодаря соединению поршня с крейцкопфом с помощью штока имеется возможность надежно отделить полость цилиндра от полости картера сальником на штоке, что особенно важно при использовании тяжелых сернистых топлив. При проектировании крейцкопфного механизма следует обратить внимание на следующие конструктивные особенности отдельных частей механизма.
92
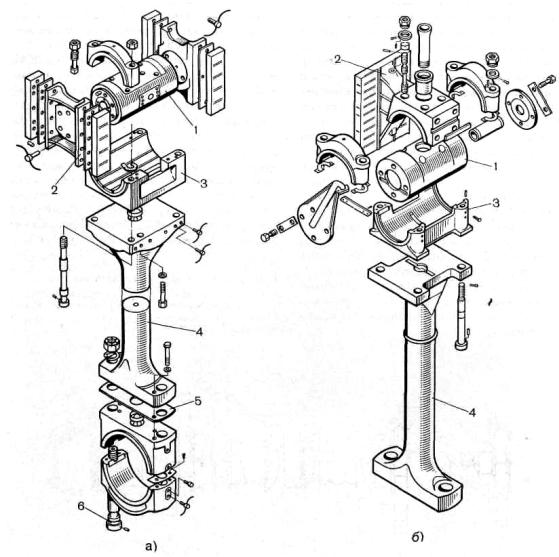
Рис. 12. Шатуны крейцкопфных двигателей:
а — с двусторонним ползуном; б — с односторонним ползуном; 1 — поперечина; 2 — ползун; 3 — верхняя (крейцкопфная) головка; 4 — стержень; 5 — прокладка; 6 — болт
Шток поршня (рис. 14), соединяющий поршень с поперечиной, как правило, крепится непосредственно к головке поршня при помощи круглого фланца и относительно длинных шпилек (чтобы увеличить их податливость). Переход от фланца к стержню штока выполняется на конус или с большим радиусом закругления; для сопряжения фланца с головкой последняя должна иметь центрирующую заточку. Сечение штока делают сплошным или полым; сверление штока применяют для облегчения его веса, а также для подвода и отвода через шток охлаждающей жидкости. Подвод и отвод жидкости должен осуществляться только с концов штока (см. рис. 14), так как радиальные сверления в теле штока вызывают концентрацию напряжений, опасную для его прочности. В случае подвода воды через полый шток необходимо изолировать сверление штока защитной тонкостенной трубой из нержавеющей стали либо предусмотреть антикоррозионное покрытие.
93

Конструкция соединения конца штока с поперечиной крейцкопфа
осуществляется посредством цилиндрического хвостовика с гайкой на конце (рис.15,а) , либо конуса с цилиндрическим хвостовиком (рис. 15, б), либо фланца прямоугольной формы (рис. 15,
в).
Рис.15.Конструкции соединений штока с поперечиной крейцкопфа.
Рис. 14.Соединение поршня с поперечиной крейцкопфа:
1 поперечина; 2- шток; 3- трубка охлаждения поршня; 4- центрирующая головка; 5- головка поршня
94
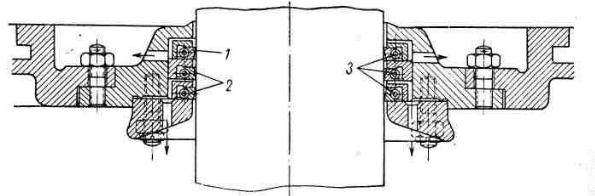
Соединение должно быть надежно зафиксировано, но вместе с тем доступно быстрой разборке. Уплотнение штока от проникновения отработавшего цилиндрового масла в полость картера или обратно должно осуществляться надежным сальником, укрепленным на диафрагме между цилиндром и картером (рис. 16).
Рис. 16. Сальник штока:
1 — верхнее маслосъемное кольцо; 2 — нижние маслосъемные кольца; 3 — спиральные пружины.
Вильчатый шатун (рис. 17, а) имеет, как правило, две опорные поверхности для поперечины, тогда как безвильчатый шатун либо две либо одну сплошную поверхность (см.рис. 14 и 15, в).
Преимущество последней в том, что при этой конструкции удает ся существенно снизить удельные давления на опорный крейцкопфный подшипник, работающий в тяжелых условиях (особенно при повышенных давлениях рг, доходящих у малооборотных дизелей с газотурбинным наддувом до 85 и более атм).
У безвильчатого шатуна, кроме того, упрощается поковка шатуна и ужесточается опорная поверхность для подшипников головки шатуна. Из рис. 17, б крейцкопфа для дизелей типа RD Зульцера видно, что конструкция безвильчатого шатуна (по сравнению с вильчатым) обеспечивает жесткую опору, а податливые подшипники стального литья коробчатого сечения компенсируют деформации, имеющиеся у поперечины.
Смазка шеек поперечины (схему подвода масла см. рис. 17, б) производится либо от общей циркуляционной системы, либо от особого зубчатого насоса с давлением до 20 атм, либо от небольших поршневых маслонасосов высокого давления (до 100—150 атм), приводимых в движение от шатуна (см. рис. 17, а).
Ползуны (башмаки) стального литья выполняют двух типов: Односторонние (рис. 18, а), у которых нормальное давление при
переднем ходе воспринимается основной опорной поверхностью ползуна (залитой баббитом), а для обратного хода служат две узкие опорные поверхности, общая ширина которых составляет около 2/8 от ширины В.
95
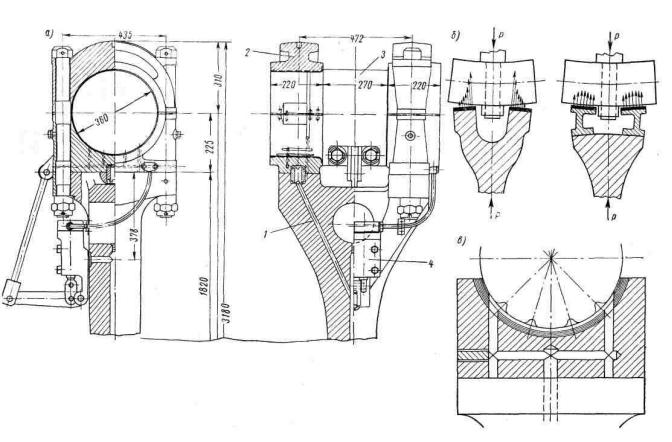
Рис. |
17. Верхняя головка вильчатого шатуна: |
а — конструкция; б — схема крейцкопфа дизелей типа RD; в — |
|
смазка шейки поперечины. |
|
1 — вилка; |
2 — опорные подшипники; 3 — поперечина; 4 — |
маслонасос высокого давления.
Двусторонние (рис. 18, б), имеющие четыре одинаковые опорные поверхности, из которых две служат для переднего и две для заднего хода. Эта конструкция несколько сложнее первой, зато обеспечивает свободный доступ с обеих сторон к деталям «движения» и одинаковые удельные давления как при переднем, так и заднем ходе.
У односторонних ползунов крепление их к поперечине производится болтами, пропущенными сквозь тело поперечины, или шпильками; для разгрузки болтов от срезывающих усилий должны быть предусмотрены особые выступы или шпонки. Двусторонние ползуны устанавливают на концевых шейках поперечины; они должны допускать некоторое перемещение вокруг шеек.
Трущуюся поверхность ползунов заливают баббитом и снабжают параллельно-расположенными смазочными канавками, имеющими конфигурацию, обеспечивающую заклинивание масла. Подвод масла осуществляется от общей циркуляционной системы.
96
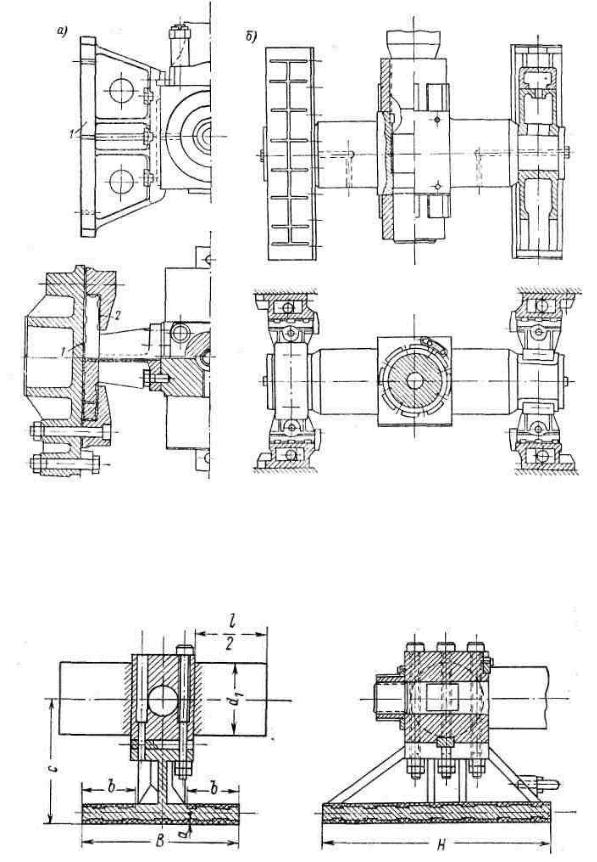
Рис. 18. Конструкции ползунов:
а — односторонний; б — двусторонний
Рис. 19. Эскиз к габаритам одностороннего ползуна
97
Материалы для шатунной группы.
Шатун представляет собой типичную деталь, работающую при значительных знакопеременных нагрузках от максимального давления газов и сил инерции. Помимо напряжения сжатия, в стержне шатуна возникают напряжения изгиба, а иногда напряжения растяжения (например в 4-тактных ДВС и в двигателях двойного действия).
Вмногооборотных двигателях действительное усилие на стержень несколько больше статического усилия от давления газов вследствие динамического влияния быстрого нарастания давления газов при наличии упругой системы шатунно-мотылевого механизма. Таким образом, шатун при работе двигателя подвергается значительной динамической нагрузке. Для изготовления шатуна должны быть выбраны высококачественные материалы, обладающие высокими прочностью, относительным удлинением, сопротивлением удару, пределом усталости. Необходимо, кроме того, при выборе материала учитывать одно из основных требований к конструкции шатуна — получение минимального веса при необходимых прочности и надежности.
Стержень шатуна и шток. Основными материалами для деталей механизма «движения», в том числе для коленчатых валов и шатунов для шатунов и штоков являются углеродистые стали 35 и 45, а также легированные 18Х2Н4ВА, 40ХН и др. В тех случаях, когда повышенные механические качества не требуются, целесообразно применять углеродистые стали, отличающиеся простотой процесса изготовления, дешевизной и высокими пластическими свойствами.
Вкачестве заменителей этих сталей применяют 40Х, 35ХГС, 40ХНВА, 15Х2Г2СВА, 15ХНГ2ВА и др.; последние две марки чаще всего заменяют сталь 18Х2Н4ВА, особенно рекомендуемую для изготовления крупных поковок.
Хромистые стали 40Х и 45Х и хромокремнемарганцовистые 35ХГС относятся к более дешевым заменителям указанных выше сталей. Механические свойства приведенных выше сталей указаны
Для повышения усталостной прочности сильно нагруженных шатунов, изготовляемых из легированных сталей (например, из стали 18Х2Н4ВА), при окончательной механической обработке иногда вместо полирования стержня применяют дробеструйную обработку поверхности.
Болты шатуна. Болты шатуна, подвергающиеся значительной статической нагрузке от предварительной затяжки, а также переменной нагрузке от действия сил инерции, работают на усталость; поэтому на выбор материала болтов следует обращать особое внимание.
Основными марками сталей, применяемых для изготовления шатунных болтов, являются стали: 35, 40ХН, 40ХНМА; в качестве заменителей рекомендуются стали: 40Х, ЗЗХС, 27СГ, 18Х2Н4ВА и другие при условии, что они будут удовлетворять механическим свойствам, предусмотренным техническими условиями.
98
Шатунные болты должны изготовляться из катаного или тянутого материала ковкой или штамповкой.
Антифрикционные материалы для подшипников шатуна. В судовых двигателях применяют различные типы антифрикционных сплавов для подшипников шатуна в зависимости от нагрузки на подшипник и условий его работы, а также от степени быстроходности и форсировки двигателя.
Чтобы обеспечить надежную работу подшипников, антифрикционные сплавы должны обладать следующими основными свойствами: 1) пластичностью, 2) достаточной твердостью, 3) хорошей прирабатываемостью, 4) необходимой усталостной прочностью при повышенных температурах, 5) высокой износостойкостью, 6) достаточной теплопроводностью для отвода тепла трения, 7) коррозионной стойкостью, 8) хорошими технологическими свойствами и, наконец, 9) способностью противостоять заеданиям при недостаточной смазке и при кратковременных перерывах в подаче смазки.
В двигателестроении в качестве антифрикционных сплавов для заливки вкладышей применяются оловянистые и свинцовистые баббиты, свинцовистые бронзы и ряд других сплавов на основе кадмия, алюминия, цинка, серебра и пр.
Для изготовления цельных или разъемных втулок головного подшипника применяются различные антифрикционные сплавы на медной основе, как то: оловянистые, безоловянистые, алюминиевые.
Лучшим антифрикционным сплавом для заливки шатунных подшипников является коррозионностойкий высокооловянистый баббит Б83, у которого высокая пластичность основной массы сплава обеспечивает хорошую прирабатываемость, а наличие твердых кристаллов позволяет воспринимать сравнительно высокие удельные давления (180—200 кГ/см*) при скорости скольжения v = 4 ÷ 6 м/сек. Баббит заливают либо непосредственно в кованые головки шатуна, либо во вставные разъемные вкладыши головки, изготовленные из стали или бронзы. Основной недостаток баббита Б83 — его сравнительно низкая температура плавления (240—350° С), из-за которой баббит быстро теряет свою твердость при повышении температуры подшипника, поэтому не следует допускать нагрев подшипников свыше 110° С. Кроме того, при больших удельных давлениях и нагрузках ударного характера баббит имеет свойство растрескиваться и выкрашиваться, что делает его непригодным для многооборотных и форсированных типов двигателей.
Учитывая дефицитность и сравнительную дороговизну олова, вместо Б83 применяют ряд его заменителей, а именно свинцовистые баббиты марок БН, Б6, БК2 и др.
Баббит БН, содержащий, помимо 9—11% олова, еще мышьяк, кадмий и никель, является одним из лучших заменителей Б83 и хорошо зарекомендовал себя в эксплуатации для удельных нагрузок подшипников до 150—180 кГ/см2; механические свойства БН мало отличаются от Б83, однако
износостойкость БН несколько |
ниже. |
Другим заменителем |
Б83 является щелочноземельный баббит, |
|
99 |
например, БК2, у которого упрочнение мягкой свинцовистой основы достигается добавлением щелочных и щелочно-земельных металлов, как, например, натрия, кальция. Помимо указанных компонентов, в состав БК2 входит ~1,5—2,5% олова. Необходимо отметить, что в присутствии воды БК2 быстро корродирует и разрушается.
Сопоставление механических свойств различных типов баббитов показывает, что оловянистые и свинцовистые баббиты обладают примерно одинаковой прочностью при температурах менее 80—90° С, однако свинцовистые баббиты более хрупки и быстрее разрушаются от усталости. Поэтому оловянистые баббиты обычно применяются при более высоких ударных нагрузках и при более высоких температурах, а свинцовистые при температурах, не превышающих 80—90° G, и невысоких ударных нагрузках. Щелочноземельные баббиты обладают большими твердостью и прочностью, чем оловянистые и свинцовистые баббиты, но они более теплопроводны, более хрупки и имеют более сложную технологию заливки.
В зависимости от конструкции подшипников и рода антифрикционных сплавов изменяется и технология заливки сплавов. Баббит Б83 у малооборотных двигателей часто заливают непосредственно в нижнюю головку шатуна или на поверхность толстостенных вкладышей (б =& 5-=-15 мм). В двигателях средней оборотности и многооборотных применяется центробежный способ заливки, при котором предварительная толщина слоя баббита составляет около 3 н-5 мм, а окончательная после расточки — около 1,5+1,0 мм.
В быстроходных и форсированных типах двигателей, где от антифрикционного сплава требуются более высокие теплопроводность, прочность при повышенных температурах и сопротивление усталости, для заливки вкладышей широко применяют свинцовистую бронзу, представляющую собой высококачественный антифрикционный сплав, у которого, в отличие от баббита, основной массой является более твердая медь, содержащая включения более мягкого свинца (около 30%). Подшипник из свинцовистой бронзы в процессе изготовления не должен подвергаться шабровке (в отличие от залитых баббитом).
Свинцовистая бронза марки Бр.С-30 по своим механическим качествам превосходит баббит Б83, допу^ екает удельные нагрузки до 300—600 кГ1смг (и выше), окружные скорости до 10 м/сек и температуры подшипников до 200° С; кроме того, имеет наиболее высокую теплопроводность (1,0 кал/см-сек °С) по сравнению с прочими сплавами. К недостаткам сплава Бр.С-30 следует отнести некоторую сложность заливки подшипников, необходимость точной обработки вкладышей, необходимость повышения твердости шеек коленчатого вала (#б > 300), необходимость тщательной фильтрации масла и, наконец, применение масел повышенного качества, которые не оказывают окислительного действия на свинец.
Для изготовления вкладышей в качестве антифрикционного металла широко применяются различные сорта бронз— оловянные и безоловянные. Среди оловянных бронз, представляющих собой сплавы меди с оловом, а
100