
книги / Ремонт шагающих экскаваторов
..pdf•обладают умеренным пенообразованием. Массовая доля их при температуре воды 75—95 °С составляет 16—26 г/л.
Препарат МС-8 относится к универсальным моющим сред ствам. Его можно применять как для струйной, так и для ван ной очистки деталей. Моющая способность и срок службы МС-8 выше, чем других СМС.
Все СМС не вызывают коррозии, могут применяться для очистки деталей из любых металлов, включая цветные сплавы, и обладают высокой моющей способностью при температуре не ниже 75 °С. При температуре до 60 °С моющая способность СМС уменьшается в 2—3 раза. При непродолжительном хра
нении (10—15 дней) |
детали после мойки с применением СМС |
|
не требуют антикоррозионной обработки. |
размерами до |
|
Для подшипников |
качения с наружными |
|
400 мм, деталей гидро- и пневмоаппаратуры |
и крепежных ре |
комендуется механическая очистка в ультразвуковых моечных ваннах типа УЗВ. Преимущество последних заключается в том, что за счет действия ультразвуковых колебаний загрязнения удаляются из всех труднодоступных мест детали. В этом слу чае в качестве моющих средств применяют уайт-спириты, бен зин (для подшипников) и СМС (для деталей гидро- и пневмо аппаратуры).
Для более крупных деталей используют серийную моечную машину 196-М с рабочим пространством размером 1080Х650Х Х850 мм. Ржавчину необходимо удалять механизированными щетками.
Первоначально очистку электродвигателей и генераторов не
обходимо производить сухим сжатым |
воздухом при |
давлении |
|||||||
0,6 МПа. |
|
|
|
|
|
|
|
|
|
Техническая |
характеристика ультразвуковых моечных ванн |
|
|||||||
|
|
|
|
|
|
|
|
УЗВ-17 |
УЗВ-18 |
Число встроенных |
магннтострикционных |
преобра |
3 |
4 |
|||||
зователей ПМС-7 |
|
|
|
|
|
||||
Частота |
колебаний, кГц |
. . |
. . |
. |
19—20 |
19—20 |
|||
Напряжение |
питания, |
В |
420 |
420 |
|||||
Общая |
площадь |
диафрагмы |
преобразователей, |
300X900 |
300X1200 |
||||
ммг ............................................. |
|
|
|
||||||
Рабочая |
вместимость |
ванны, |
л |
|
|
120 |
150 |
||
Внутренние размеры ванн, мм: |
|
|
|
1100 |
11 400 |
||||
длина |
|
|
|
|
|
|
|
||
ширина. |
|
|
|
|
|
|
450 |
450 |
|
высота |
|
|
|
|
|
|
|
300 |
300 |
4.3. ДЕФЕКТАЦИЯ
После завершения разборки узлов механизмов и устройств, очистки и мойки деталей экскаватора производится их дефекта ция. Под этим подразумевают определение физического (чаще
Состав синтетических моющих средств, %
Компонент |
Тракторин |
МС-8 |
Лабамид-101 |
||
МЛ-51 |
МЛ-52 |
||||
|
|
|
|||
Сода кальцинированная |
44 |
50 |
38 |
50 |
|
Триполифосфат натрия |
34,5 |
30 |
25 |
30 |
|
Метасиликат натрия |
— |
— |
29 |
16,5 |
|
Жидкое стекло |
20 |
10 |
— |
— |
|
Смачиватель ДБ |
1,5 |
8 ,2 |
— |
— |
|
Сульфонал |
— |
1,8 |
— |
— |
|
Синтанол ДС-10 |
— |
— |
— |
3 ,5 |
|
Синтамид-5 |
— |
— |
8 |
— |
|
геометрического), а не функционального |
несоответствия требо |
ваниям, установленным нормативной ремонтной и конструктор ской документацией.
Дефектами являются: отклонение размеров детали от до пустимых, а также отклонения формы и взаимного расположе ния поверхности от установленных, частичное разрушение и по вреждение рабочих поверхностей деталей и элементов конструк ций; повреждение покрытий; нарушение герметичности гидро- и пневмооборудования и соединений; нарушение магнитно-элект рических и изоляционных свойств электрооборудования.
Правильная и оперативная дефектация экскаватора возмож на, если на предприятии имеются квалифицированные специалис ты— дефектовщики (не относящиеся к ОТК), в распоряжении которых есть методики и средства для обнаружения дефектов. Совершенные методы дефектации во многом определяют как ор ганизационную, так и технологическую стороны ремонта, и в ко нечном счете позволяют дать более точную оценку состояния деталей.
При дефектации детали подразделяют по следующим груп пам:
1. Детали годные, у которых отклонения не превышают до пустимых по требованиям ремонтной документации.
2.Детали, подлежащие ремонту, у которых отклонения пре вышают допустимые, но их восстановление разрешается соглас но требованиям ремонтной документации.
3.Детали негодные (брак), у которых отклонения превыша ют допустимые и которые подлежат восстановлению согласно требованиям ремонтной документации.
Вгруппах 2 и 3 имеются детали, для которых восстановле
ние или выбраковку |
производят только парными |
деталями |
|
(в комплекте). В зависимости |
от принадлежности |
к той или |
|
иной группе детали |
рекомендуется маркировать красками ,(на |
||
заметных местах) различных |
цветов; 2-я группа — белой, 3-я |
группа — красной. У восстанавливаемых и негодных деталей дефектовщик краской того же цвета отмечает дефекты. Негодные детали сдают в металлолом.
Однако только цветная маркировка деталей недостаточна. Детали обязательного комплекта (плунжерные пары распре
делителей, цилиндров, роторная пара компрессора и т. п.) мар кируют индексами 1—1, 2—2, 3—3 и т. д. при левой (правой) установке— 1—1Л, 1—1П, 2—2Л (относительно продольной оси поворотной платформы, по ходу стрелы). При наличии одинако вых механизмов и устройств необходимо также маркировать ос новные детали, так как очень важно, чтобы детали были уста новлены на свои прежние места. Например, детали первого (от стрелы) справа редуктора поворотного механизма следует обо значать индексом 1П, второго слева соответственно 2Л. При симметричном расположении элементов деталей относительно базового корпуса, правая сторона (торец) обязательно марки руется индексом П.
При явно выраженных дефектах, имеющих браковочный при знак, детали не маркируются (утилизируются).
Дефектации подвергают все детали согласно требованиям ремонтной документации за незначительным исключением тех, которые входят в узлы, не подлежащие полной разборке. У де талей, подвергающихся дефектации, проверяют все параметры рабочих поверхностей деталей. В ы б о р о ч н ы й к о н т р о л ь п а р а м е т р о в не д о п у с к а е т с я !
При дефектации деталей необходимо соблюдать следующие правила:
1. Независимо от объема подетальной дефектации и степени разборки узлов все (максимально допустимые) их детали должны быть визуально осмотрены для выявления деформаций
итрещин.
2.Место контроля должно быть обязательно очищено от следов масла и краски (при частичной разборке узлов), а при измерении деталей зубчатых зацеплений сняты заусенцы и на кат металла.
3.При наличии двух и более видов дефектов оценка их должна даваться полностью, независимо от выбраковочного признака по одному из них. Это правило относится только к де талям основных механизмов и устройств экскаватора.
4.Оценка дефектов должна производиться по зонам наи больших износов. Очень важно при этом для определенных де талей механизмов фиксировать в ведомостях и положение этих
зон (вверху или внизу, слева или справа) относительно дета лей сопряжения данного узла. Соблюдать терминологию дефек тов и их точную оценку.
5. Проверка состояния металлоконструкций и определение износов недемонтированых корпусных и прочих деталей долж
ны производиться непосредственно на ремонтных площадках. Здесь же должно проверяться и состояние защитного покрытия
конструкций.
6. Освещенность объекта дефектации должна быть не менее
150 лк при общей освещенности в помещении 26—40 лк. Предлагаемая классификация дефектов с их кодированием
дана в табл. 4.13.
При ремонте экскаваторов обнаруживают дефекты при ви зуальном, измерительном и неразрушающем контроле. Второй вид контроля наиболее объемен и производится с применением обычных универсальных и некоторых специальных инструмен
тов.
К специальным инструментам относят шаблоны разного на значения, специальные калибры и приспособления. Как прави ло, указанными инструментами следует пользоваться совместно с универсальными. Например, измеряя износ шпоночного паза
или шлицевого отверстия, |
пользуются |
специальными пазовыми |
калибрами (для данного размера паза) |
и набором щупов, а при |
|
измерении износа профиля |
блока — шаблоном и набором щу |
|
пов. |
|
|
П р и о п р е д е л е н и и и з н о с о в ш е е к в а л о в - о с е й и о т в е р с т и й , п о л ь з о в а т ь с я к а л и б р а м и ( с к о б а
ми и п р о б к а м и ) не р а з р е ш а е т с я ! |
|
соблю |
|
При измерительном контроле |
деталей необходимо |
||
дать следующие особые приемы: |
|
|
|
1. Измерение шеек валов-осей, отверстий следует |
произво |
||
дить в двух-трех сечениях, причем |
в каждом |
из них — в двух |
|
взаимно перпендикулярных направлениях. При |
длине |
измеряе |
мой поверхности более 250 мм идиаметре отверстия более 200 мм следует производить не менее трех измерений.
2. При измерении толщины зуба штангензубомером с увели
чением модулей зацепления |
( т ^ 1 6 |
мм) одноразовый замер |
толщины зуба недостаточен, |
так как |
износ зуба по высоте не |
равномерный и можно получить неточную характеристику изно са. При модуле т —18-5-26 мм необходимо производить не ме нее двух замеров, а при модуле т = 26 мм — не менее трех как в зоне головки зуба, так и у его вершины. Высота измерений должна быть указана в ремонтной документации.
При проверке зубчатых колес замерами должно быть охва чено не менее 25% зубьев (но не менее шести зубьев); у зубча тых венцов поворотного механизма — не менее 10%. Измерения по длине зуба следует производить в трех сечениях.
3. Поднутрения и прочие искажения профиля зуба следует замерять только специальными шаблонами и набором щуповигл. При величине поднутрения менее 0,5 мм данный прием измерений не применяют, а оценивают визуально.
|
|
|
|
|
|
|
|
|
|
|
|
|
|
Т а б л и ц а |
|
4.13 |
||
Классификация ремонтных дефектов деталей и металлоконструкций |
|
|
||||||||||||||||
механических систем экскаваторов |
|
|
|
|
|
|
|
|
|
|
|
|||||||
Дефект |
|
Характеристика |
|
дефекта |
Код |
|
Группа деталей, |
|||||||||||
|
|
частей элементов |
||||||||||||||||
Т рещ ина |
(тр ещ и |
Сквозная, замкнутая |
|
0101 |
Металлоконструкции, |
|||||||||||||
ны ) |
|
Сквозная, |
незамкнутая |
(вы |
0102 |
шлицы |
и |
шпоночные |
||||||||||
|
|
ходящая |
на край) |
|
|
0103 |
валы и пазы вал- |
|||||||||||
|
|
Несквозная, |
|
|
замкнутая |
шестерен, |
зубья |
ше |
||||||||||
|
|
(глубиной |
< 0,8 |
мм) — мик |
|
стерен |
и |
колес, |
шей |
|||||||||
|
|
ротрещина |
|
|
замкнутая |
0104 |
ки |
цапф, |
блоки, |
|||||||||
|
|
Несквозная, |
|
|
обоймы, |
подшипники, |
||||||||||||
|
|
(глубиной |
> 0,8 |
мм) |
|
|
0105 |
траверсы |
|
|
|
|||||||
|
|
Несквозная, |
незамкнутая |
|
|
|
|
|
|
|||||||||
|
|
(глубиной |
< |
0,8 мм) — мик |
|
|
|
|
|
|
|
|||||||
|
|
ротрещина |
незамкнутая |
0106 |
|
|
|
|
|
|
||||||||
|
|
Несквозная, |
|
|
|
|
|
|
||||||||||
|
|
(глубиной |
> 0,8 |
мм) |
|
|
0107 |
|
|
|
|
|
|
|||||
|
|
Множественные, |
|
сквозные, |
Металлоконструкции |
|||||||||||||
|
|
локальные |
|
|
сквозные, |
0108 |
||||||||||||
|
|
Множественные, |
|
|
|
|
|
|
|
|||||||||
|
|
незамкнутые |
|
|
|
|
|
|
То |
же |
|
|
|
|
||||
|
|
С деформацией, замкнутые |
0121 |
|
|
|
|
|
|
|||||||||
Разрыв |
(разрывы) С |
деформацией, незамкну |
0122 |
Элементы |
металло |
|||||||||||||
|
|
тые |
|
|
|
|
|
|
|
|
0131 |
конструкций |
(ковш, |
|||||
|
|
Торцевые |
|
|
|
|
|
|
опорная рама) |
|
|
|||||||
Сколы |
|
Внутренние |
(одиночные) |
0132 |
Зубья |
шестерен, коль |
||||||||||||
|
|
Торцевые |
и |
внутренние, не |
0133 |
ца подшипников, втул |
||||||||||||
|
|
одиночные |
|
|
|
|
|
0141 |
ки |
|
цементируемых |
|||||||
Задиры |
|
Местные |
|
мелкие |
|
(3—4 |
или |
сталей |
|
|
|
|
||||||
|
с |
охватом |
< 1/6 |
площади |
|
Шейки |
|
валов, |
|
вал- |
||||||||
|
|
элемента), |
|
|
глубиной |
|
шестерен, |
осей, |
втул |
|||||||||
|
|
< 0,4 |
мм |
|
|
|
|
|
|
|
0142 |
ки-подшипники |
сколь |
|||||
|
|
Мелкие |
(с |
охватом |
< 1/2 |
жения, |
ролики, |
поса |
||||||||||
|
|
площади |
|
элемента), |
глуби |
|
дочные отверстия кор |
|||||||||||
|
|
ной |
< 0,6 |
|
мм |
|
|
|
|
|
0143 |
пусов |
подшипников, |
|||||
|
|
Местные грубые |
|
(с |
охватом |
рельсы, цапфы |
|
|
||||||||||
|
|
< 1 /6 |
площади |
|
элемента), |
|
|
|
|
|
|
|
||||||
|
|
глубиной |
|
> 1 |
мм |
|
|
(с |
охва |
0144 |
|
|
|
|
|
|
||
|
|
Мелкие, |
сплошные |
|
|
|
|
|
|
|||||||||
|
|
том |
> 2 /3 |
площади |
элемен |
|
|
|
|
|
|
|
||||||
|
|
та), |
глубиной < 0,6 |
мм |
|
0145 |
|
|
|
|
|
|
||||||
|
|
Сплошные |
(с |
|
|
охватом |
|
|
|
|
|
|
||||||
|
|
> 1 /2 |
площади |
|
элемента), |
|
|
|
|
|
|
|
||||||
|
|
глубиной |
|
< 1 |
мм |
|
(с |
охва |
0146 |
|
|
|
|
|
|
|||
|
|
Грубые, |
сплошные |
|
|
|
|
|
|
|||||||||
|
|
том |
> 1 /2 |
площади |
элемен |
|
|
|
|
|
|
|
||||||
|
|
та), |
глубиной > 1 |
мм |
|
0151 |
|
|
|
|
|
|
||||||
Выкрашивание |
Мелкое, |
|
сплошное |
(глуби |
Зубья |
шестерен, |
ко |
|||||||||||
|
|
ной |
до |
|
0,4 |
мм) — «сыпь» |
|
лес, |
кольца подшип |
|||||||||
|
|
(см. рис. |
|
1.12, в) |
|
|
охватом |
0152 |
ников |
|
|
|
|
|||||
|
|
Сплошное |
|
(с |
|
|
|
|
|
|
|
|
||||||
|
|
>45% |
площади |
рабочего |
|
|
|
|
|
|
|
|||||||
|
|
элемента, |
|
|
|
глубиной |
|
|
|
|
|
|
|
|||||
|
|
< 0,8 |
мм) — «пятнистость» |
|
|
|
|
|
|
|
||||||||
|
|
(«пятно» — не более 4 мм) |
|
|
|
|
|
|
|
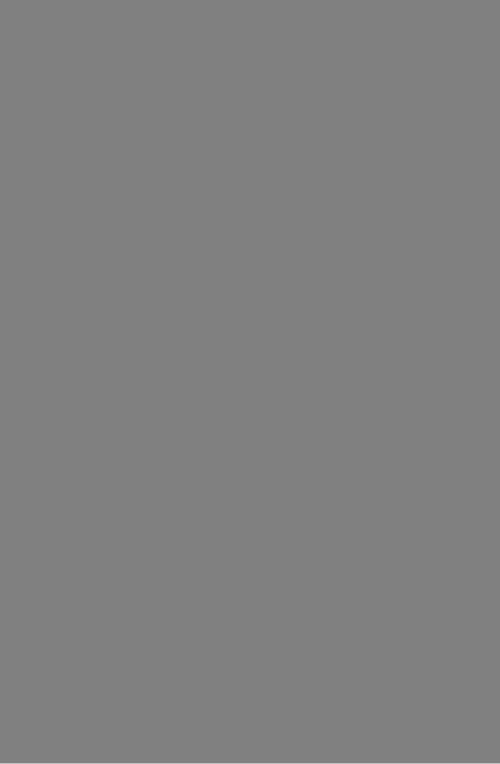
Рис. 4.27. Схема устройства для контроля подшипников качения:
а — радиального зазора; б — осевого биения; |
1 — основание; |
2, |
5 — зажимы; 3 — индика |
тор часового типа; 4 — салазки; 6 — стойка |
с индикатором |
на |
магнитном основании |
4. При оценке степени выкрашивания |
рабочей поверхности |
||
зуба необходимо определять максимальную |
глубину слоя вы |
||
крашивания, размеры наибольшего дефекта |
(в мм2) и общую |
площадь охвата выкрашиванием относительно рабочей поверх ности зуба (в %). При модуле зацепления более 10 мм следу ет указывать в ведомости и зоны выкрашивания (зоны головки» ножки или делительной окружности).
5. У подшипников качения следует проверять величины ра диального зазора, осевого биения, износ и деформирование се параторов, наличие выкрашиваний и повреждение беговых до рожек внутреннего и наружного колец подшипников, наличие выкрашиваний шариков (роликов). Величины наибольшего ра диального зазора подшипников (кроме конических) и осевого биения проверяют на специальных устройствах (рис. 4.27).
Из неразрушающих методов контроля наиболее распростра нен ультразвуковой (УЗД). Его применяют в основном для стыковых сварных швов, а также материала стыковых проушин стрелы и надстройки (согласно ремонтной документации). Этим же способом проверяют наличие скрытых трещин шеек валовосей. Контроль выполняют в соответствии с ГОСТ 14782—86, или специальными ОСТами, или инструкцией «Контроль нераз рушающий. Швы сварные. Метод ультразвуковой».
Основные дефекты пневмо- и гидроприборов — нарушение герметичности и заклинивание частей определяют при соответ ствующих испытаниях на специальных стендах, а также непо средственно на машинах в системе.
К специальным методам дефектации можно отнести провер ку геометрии стрелы, нивелировку которой проводят с одновре менной настройкой (см. разд. 4.8)— доведение до проектного положения стыковых узлов.
По результатам дефектации оформляются документы: ведо мости технического состояния экскаватора (раздельно на меха ническую и электрическую части), протоколы ультразвуковой дефектоскопии, акт на проведение нивелировки геометрии стре лы экскаватора.
Под восстановлением деталей понимают такую последова тельность операций, в результате которых возобновляется год ность деталей на уровне исходной. Исключение составляет лишь восстановление деталей при разрушениях.
В ряде случаев при повреждении элементов ответственных металлоконструкций очень трудно добиться гарантированной ис ходной годности (расчетной прочности), что требует особого подхода к выбору метода и приемов воссстановления. В таких случаях специалистам по ремонту экскаваторов рекомендуется привлекать экспертов заводов-изготовителей (фирменное об служивание).
Выбор метода и способа восстановления деталей шагающих экскаваторов диктуется:
характером (параметрами) износа или повреждением дета лей, элементов;
исключением риска крупной аварии и безопасностью экипа жа из-за выхода из строя деталей;
реальной технологической возможностью ремонтного пред приятия;
экономической целесообразностью (серийность ремонта ма шин, возможность одновременного ремонта и экскаваторов-мех- лопат, ритмичность сдачи машин и узлов в ремонт, экономия металла);
конструкцией деталей (материал, масса, габариты, концент рация нагрузок, характер нагрузок, положение детали в прост ранстве, наличие нарушений сопряжений).
Следует обратить о с о б о е в н и м а н и е на второе условие, когда на детали директивно вводится ограничение или запреще ние на определенные методы (способы) восстановления. К чис лу таких деталей относят: оси подвески и основания стрелы, оси
надстройки, оси блоков надстройки, |
оси секций стрелы, коуши |
|||||
подвески стрелы, коуши |
и оси вантов стрелы, |
вал-шестерня |
||||
{входная) привода поворота. |
О ни |
не |
д о п у с к а ю т с п о |
|||
с обов |
в о с с т а н о в л е н и я , |
с в я з а н н ы х |
с т е р м и ч е |
|||
с к и м |
в о з д е й с т в и е м |
на |
д е т а л ь , |
т. е. |
возможностью |
появления резких концентраторов напряжений. Здесь необходи мо применять «холодные» способы восстановления. Практика же замены данных деталей пока обоснована.
Из-за конструктивно-технологических особенностей деталей (элементов) шагающих экскаваторов выбор способов восстанов ления все же ограничен. Ограничения, в первую очередь, связа ны с двумя противоречивыми свойствами данных машин. С од ной стороны, современные экскаваторы имеют (до 30% общего числа) детали механизмов и устройств длительного срока служ бы (практически до списания, т. е. их восстановления как тако-
вого не требуется). Наблюдается и явная тенденция на еще больший охват таких деталей. И одновременно пока наблюдает ся и низкий уровень ремонтной технологичности (показатель ре монтопригодности). Детали из группы зубчатых зацеплений (особенно колеса), например, практически невозможно восста новить из-за малой толщины обода, хотя они наиболее материа лоемкие и дорогостоящие в группе зубчатых. Накладываются ограничения по восстановлению и на детали из хромоникелевых, молибденовых сталей, очень чувствительных к термовоздействи ям. Более технологичны следующие методы восстановления: сварка, наплавка, металлизация (напыление) ремонтной втул ки, бандажирование, ремонтное корригирование ремонтного раз мера. Из них наиболее эффективны и широко применимы мето ды сварки и наплавки.
Электродуговая сварка сводится к следующим основным опе рациям: заварке трещин, приварке (установке) накладок и ре бер жесткости, замене отдельных участков или элементов ме таллоконструкций и снятию сварочных напряжений.
Восстановление сваркой несущих металлоконструкций экс каватора (поворотной платформы, стрелы, надстройки, опорной рамы) — самый сложный и ответственный технологический про цесс, от качества выполнения которого зависит в основном ка чество ремонта всего экскаватора.
Значительные по величине зоны термического влияния, оста точные растягивающие напряжения, пересечение сварными шва ми разнородных по толщине и рабочим напряжениям элементов конструкций, трудодоступность поля сварки, необходимость сварки при низких температурах (ниже —15°С), различная квалификация сварщиков — все это налагает особые требования на разработку технологических процессов восстановления свар кой.
Дальнейшие рекомендации будут относиться только к несу щим металлоконструкциям: корпусу ковша, стреле, поворотной платформе, надстройке и опорной раме.
При выборе марок электродов (ручная электродуговая свар ка) следует ограничиться наиболее технологически целесооб разными: УОНИ-13/55, УП-2/55У, К-5А типа Э50А по требова ниям ГОСТ 9467-75 и ГОСТ 9466-74. Для ковшей применяют электроды марок УОНИ-13/45 (ГОСТ 9466-75) типа Э42А (ГОСТ 9467-75) и нержавеющие (аустенитные) НИИ-48Г, ЭА-473/3 и ЭА-395/9 для сварки отливок из стали марки 110Г13Л.
Электроды марки УОНИ-13/45 типа Э42А рекомендуют для сварки сталей ЮХСНД при температурах окружающего возду ха ниже —15 СС; образующийся сварочный шов обладает высо кой пластичностью, хотя несколько снижает его прочность.
|
|
Т а б л и ц а 4.14 |
Параметры режимов сварочных работ |
|
|
Диаметр |
Сварочный ток, А |
Назначение электрода |
электрода, |
||
!ММ |
|
|
4 |
160— 180 |
Первый слой и последующие |
5 |
200—220 |
слои |
Последующие слои |
||
'6 |
250—320 |
То же |
Диаметр |
электродов 4, 5 и 6 мм. |
Первые применяют для |
подварки корня шва, а также для потолочных швов.
При сварке особенно важен правильный выбор режима сва рочных работ (табл. 4.14).
Для сварки горизонтальных и вертикальных швов силу сва
рочного тока по сравнению с силой тока при сварке |
в нижнем |
||
положении следует принимать |
(А): |
|
|
Диаметр электрода, мм |
4 |
5 |
6 |
Положение шва: |
120— 160 |
160—210 |
210—250 |
нижнее |
|||
горизонтальное |
100— 130 |
140— 170 |
140— 170 |
вертикальное |
100— 130 |
160— 180 |
160— 180 |
Сварку аустенитовыми электродами |
(заварка трещин и свар |
ка деталей отливок из стали 110Г13Л) выполняют на постоян ном токе, обратной полярности минимальной величины. Резку и разделку кромок трещин отливок из данной стали производят сваркой рекомендуемыми выше электродами. При этом надо обеспечить свободное вытекание расплавленного металла. При менима в данном случае и воздушно-дуговая резка. Разделку трещин на отливках из сталей 110Г13Л не рекомендуется вести «огневой» резкой: следует применять шлифовальные машинки со специальными абразивными кругами для резки и зачистки металла (ТУ 36-1394577-002—85).
При сварочных работах требуется соблюдать следующие об щие правила.
1.Объемы и номенклатура восстановления сваркой опреде ляются техническими требованиями нормативных ремонтных документов.
2.Перед проведением сварочных работ все конструкции дол жны быть максимально разгружены от рабочих нагрузок.
3.Места сварки следует тщательно очищать от ржавчины, краски, следов масла и грязи.
4.Все заменяемые элементы, вставки, а также устанавливае мые накладки, ребра должны быть изготовлены из стали марки 10ХСНД-6 по ГОСТ 19282—73 (кроме корпуса ковша, где до