
Лаб_ работы по Сопромату часть 2
.pdf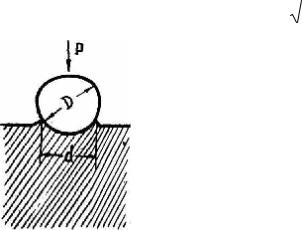
31
образец нагрузкой Р вдавливается на специальном прессе закаленный стальной шарик диаметром D, образующий на поверхности образца лунку диаметром d
(рис. 12.1). Твердость по Бринелю обозначается HB и подсчитывается по
формуле |
|
|
|
|
|
|
|
|
|
|
||
HB = |
P |
= |
|
P |
|
|
|
|
|
|
(12.1) |
|
|
|
|
|
|
|
|
|
|
|
|||
|
2 |
(D − |
D |
|
− d |
|
) |
|||||
|
Fот |
πD |
|
2 |
|
2 |
|
|
|
Для ускорения испытания на практике вместо подсчетов по формуле (12.1) пользуются таблицами, где приводятся числа
твердости в зависимости от диаметра отпечатка (приложение 2).
Методика испытаний по Бринелю регламентируется ГОСТом 9012-59. Для
Рис.12.1. Схема испытаний
на твердость по Бринелю получения сопоставимых результатов испытаний следует соблюдать закон подобия
P/D2 = const и время выдержки под нагрузкой (табл. 12.1).
Таблица 12.1
|
Интервал |
Толщина |
2 |
Диаметр |
Нагрузка |
Выдержка |
|
Материал |
значений |
образца, |
P/D , |
шарика D, |
под |
||
НB, 2 |
2 |
P, кг |
нагрузкой, |
||||
|
мм |
кг/мм |
мм |
||||
|
кг/мм |
|
|
|
|
сек |
|
|
|
Более 6 |
|
10 |
3000 |
|
|
Черные |
140 - 450 |
От 6 до 3 |
30 |
5 |
750 |
10 |
|
|
Менее 3 |
|
2,5 |
187,5 |
|
||
металлы |
|
|
|
||||
|
Более 6 |
|
10 |
3000 |
|
||
|
до 140 |
От 6 до 3 |
30 |
5 |
750 |
30 |
|
|
|
Менее 3 |
|
2,5 |
187,5 |
|
|
Медь, латунь, |
|
Более 6 |
|
10 |
1000 |
|
|
бронза, |
|
|
|
||||
31 - 130 |
От 6 до 3 |
10 |
5 |
250 |
30 |
||
магниевые |
|||||||
|
Менее 3 |
|
2,5 |
62,5 |
|
||
сплавы и др. |
|
|
|
||||
|
|
|
|
|
|
||
Алюминий, |
|
Более 6 |
|
10 |
1000 |
|
|
подшипни- |
8 - 35 |
От 6 до 3 |
2,5 |
5 |
250 |
60 |
|
ковые сплавы |
|
Менее 3 |
|
2,5 |
62,5 |
|
32
При испытании тонких изделий необходимо применять шарик с меньшим диаметром D, чтобы исключить влияние поверхности стола, на которую кладут образец.
Диаметр отпечатка измеряют специальной лупой с точностью до сотых долей миллиметра (причем сотые берутся на глаз) по двум взаимно перпендикулярным направлениям, и из этих измерений берется среднее. Для измерения твердости обычно делают три отпечатка. Центр отпечатка должен
находиться от края образца на расстоянии не менее диаметра шарика и не менее двух диаметров от центра соседнего отпечатка.
Способ Бринеля используется для определения твердости незакаленных материалов. Максимальная величина твердости, замеряемая этим методом,
ограничивается величиной HB = 400÷500 кг/мм2, которая определяется твердостью шарика. Нельзя замерять твердость тонкого поверхностного слоя, так как шарик проникает черев этот слой в более мягкую внутреннюю часть.
Метод Бринеля можно применять, если диаметр отпечатка d находится в пределах 0,2D < d < 0,6D.
Пресс Бринелля ПБМ. Испытания по Бринелю проводятся на специальном прессе, схема которого приводится на рис. 12.2. Испытуемый образец 4 кладется на столик 3, расположенный на подъемном винте 2. Винт при помощи маховика 1 поднимает столик с образцом до соприкосновения образца с шариком 5. Шарик входит в гнездо сменного наконечника 6, который вставляется в штемпель 7. При дальнейшем вращении маховика 1 вместе с образцом движется и штемпель 7, сжимая пружину 8, которая создает предварительную нагрузку в 100 кг для выборки зазоров и предохранения образца от смещений. Это движение проводят до совпадения рисок на штемпеле 7 и корпусе прибора.
Основная нагрузка на образец через шарик прикладывается от подвески 12 со сменными грузами 13 через систему рычагов 10 и 11. При включении
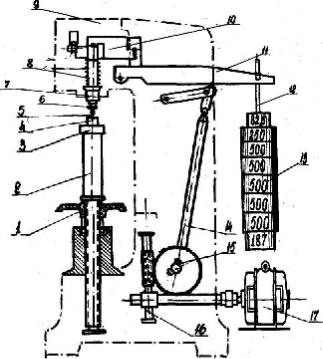
33
электромотора 17 вращение черев червячную передачу 16 передается шатуну 14, который, опускаясь, освобождает рычаг 11, и основная нагрузка передается на образец. При дальнейшем вращении червячного колеса упор 15 переключает направление вращения электромотора, и шатун 14, поднимаясь через установленное время выдержки, снимает нагрузку с образца, поднимая рычаг 11. В конце испытания второй упор 15 выключает электродвигатель. Путем вращения маховика 1 образец освобождается, и проводится замер диаметра получившегося отпечатка. Сменные грузы 13 устанавливаются согласно табл. 12.1.
Рис.12.2. Схема пресса Бринеля
4. Определение твердости по Роквеллу. Мерой твердости по Роквеллу
служит глубина отпечатка полученного при вдавливании алмазного конуса с углом при вершине 120° или стального шарика диаметром 1,588 мм. Методика испытаний регламентируется ГОСТом 9013-59. Форма вдавливаемого тела и нагрузки выбираются согласно табл. 12.2 в зависимости от предполагаемой

34
твердости испытываемого материала: шарик - для менее твердых, алмазный конус - для твердых (шкала С) и очень твердых поверхностей (шкала А).
Таблица 12.2
Характеристика шкал прибора Роквелла
Обозначение |
|
Нагрузка, кг |
|
Соответст- |
|||
|
Пределы |
вующие |
|||||
|
|
|
|
|
|||
|
|
|
|
|
приближенные |
||
|
|
Тип |
|
|
измерения |
||
|
|
|
|
в единицах |
значения чисел |
||
шкалы |
чисел |
наконеч- |
предвари- |
общая |
твердости |
твердости Hv, |
|
твер- |
ника |
тельная |
Р |
по |
измеренных |
||
|
дости |
|
Рп |
алмазной |
|||
|
|
|
Роквеллу |
||||
|
|
|
|
|
пирамидой по |
||
|
|
|
|
|
|
||
|
|
|
|
|
|
Виккерсу |
|
В |
HRB |
Стальной |
10 |
100 |
25 – 100 |
60 – 240 |
|
шарик |
|||||||
|
|
|
|
|
|
||
С |
HRC |
Алмазный |
10 |
150 |
20 – 67 |
240 – 900 |
|
конус |
|||||||
|
|
|
|
|
|
||
А |
HRA |
Алмазный |
10 |
60 |
70 - 85 |
390 - 1300 |
|
конус |
|||||||
|
|
|
|
|
|
Вдавливание наконечника производится действием двух последовательно прикладываемых нагрузок: предварительной Рп= 10 кг и основной Р . Общая
нагрузка выбирается в зависимости от принятой шкалы по табл. 12.2. Твердость характеризуется глубиной проникновения h наконечника от действия основной нагрузки (рис. 12.3). Число твердости по Роквеллу - отвлеченное число, определяемое
для алмазного конуса HRC = 100 − 0,002h ;
для стального шарика HRB =130 − 0,002h .
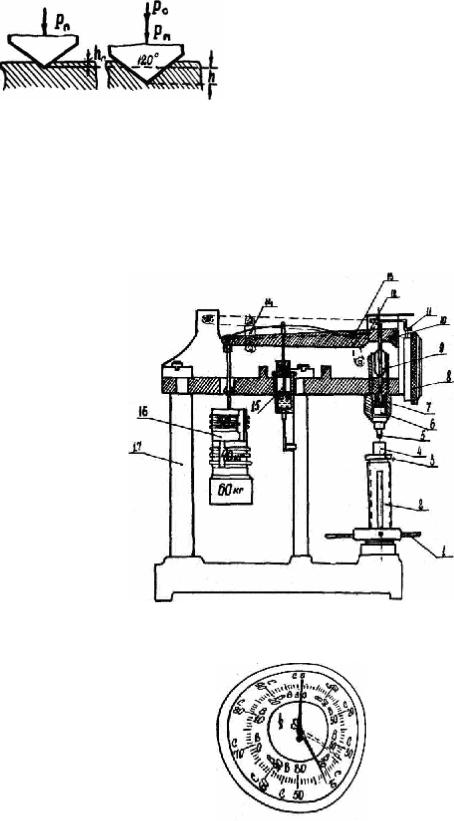
|
35 |
|
|
При испытании числа твердости не |
|
|
подсчитываются, так как шкала индикатора |
|
|
прибора проградуирована непосредственно в |
|
|
числах твердости. |
|
Рис. 12.3. Схема определения |
Преимуществами метода Роквелла является |
|
быстрота испытаний (на его производство |
||
твердости по Роквеллу |
затрачивается несколько секунд), получение числа твердости непосредственно на шкале прибора и широкий диапазон измеряемых твердостей.
Прибор Роквелла. Испытания по Роквеллу проводят на специальном прессе, схема которого приводится на рис.12.4, а.
а)
б)
Рис. 12.4. Схема пресса Роквелла
36
Образец 4 устанавливается на сменном столике 3 прибора. При вращении маховика 1 подъемный винт 2, перемещаясь вверх, прижимает столик с образцом к наконечнику 5, который закреплен в штемпеле 6, и сжатием пружины 7 сообщается предварительная нагрузка Рп = 10 кг для выборки зазоров и предохранения образца от смещений. Основная нагрузка от подвески со сменными грузами 16 передается на штемпель 6 посредством рычага 12, закрепленного на оси 10, и призмы 9. В нерабочем положении рычаг 12 опирается на подвеску 14. Для передачи основной нагрузки освобождают рукоятку 13, тогда подвеска 14 и рычаг плавно опускаются и передают нагрузку на образец. Для плавного опускания рычага и регулирования скорости передачи нагрузки используется масляный амортизатор 15.
Перемещение штемпеля 6 с наконечником 5 при помощи рычага 11 передается индикатору 8, на котором и отсчитываются числа твердости. На циферблате индикатора (рис.12.4,6) имеются две шкалы: внутренняя (красная) для испытаний шариком и наружная (черная) для испытаний алмазным наконечником, смещенные относительно друг друга на 30 делений.
Порядок испытаний на прессе Роквелла. Выбирают наконечник 5 по табл. 12.2 и закрепляют его винтом в штемпеле 6. Подвешивают сменные грузы 16 в соответствии с выбранной шкалой. Испытуемый образец помещают на столик прибора 3 и при помощи маховика 1 доводят его до соприкосновения с наконечником 5. После этого медленно вращают маховик 1 до тех пор, пока малая стрелка индикатора не окажется против красной точки на шкале, а большая не станет в вертикальное положение. В этом положении пружина 7 создает предварительную нагрузку в 10 кг.
Ободок индикатора поворачивают до тех пор, пока нуль черной шкалы или 30-е деление красной шкалы не совпадут с большой стрелкой. Затем рукояткой 13 включают основную нагрузку. После медленного опускания рычага 12 разгружают образец путем плавного возвращения рукоятки 13 в исходное положение. Производят отсчеты твердости по внутренней шкале, если наконечником является шарик и по внешней шкале, если используется

37
алмазный конус. Вращая маховик 1 по часовой стрелке, перемещают вниз столик с образцом и окончательно разгружают образец.
На каждом образце должно быть произведено не менее трех испытаний. За число твердости берут средний результат этих испытаний. Расстояние между центрами соседних отпечатков должно быть не менее 4 мм.
5. Определение твердости по Виккерсу. Мерой твердости по Виккерсу
являются напряжения на поверхности отпечатка при вдавливании четырехгранной алмазной пирамиды с углом между гранями α = 136°
(рис. 12.5). Число твердости по Виккерcу обозначается Hv и вычисляется по
формуле
|
|
|
P |
|
2PSin |
α |
|
P |
|
H |
V |
= |
= |
2 |
= 1,8544 |
, |
|||
F |
d 2 |
|
d 2 |
||||||
|
|
|
|
|
|
где Р - нагрузка на пирамиду; d - среднее арифметическое длин обеих диагоналей отпечатка.
|
Результаты измерений твердости не |
||
|
зависят от нагрузки Р. ГОСТ 2999-75 |
||
|
рекомендует выбирать нагрузки Р равными |
||
|
5; 10; 20; 30; 50 и 100 кг в зависимости от |
||
|
толщины образца, чтобы глубина отпечатка |
||
|
была меньше 1/10 толщины образца. Чем |
||
|
больше нагрузка, тем точнее результат |
||
Рис.12.5. Схема определения |
замера |
вследствие больших размеров |
|
отпечатка. Наименьшая допустимая толщина |
|||
твердости по Виккерсу |
|||
образца - |
0,3 мм, и испытания проводятся |
||
|
при нагрузке 5 кг для закаленной стали. Для твердых материалов во избежание повреждения алмаза не рекомендуется применять нагрузку более 50 кг . Рекомендации по выбору нагрузки содержатся в табл. 12.3.
38
Таблица 12.3
Толщина |
Твердость по Виккерсу, кг/мм2 |
||||||
|
|
|
|
|
|
||
образца, мм |
20 - 50 |
|
50 - 100 |
100 |
- 300 |
300 - 900 |
|
|
Рекомендуемая нагрузка, кг |
||||||
|
|
|
|||||
|
|
|
|
|
|
|
|
0,3 |
- 0,5 |
- |
|
- |
|
- |
5 - 10 |
|
|
|
|
|
|
|
|
0,5 |
- 1,0 |
- |
|
- |
5 - 10 |
10 - 20 |
|
|
|
|
|
|
|
|
|
1 |
- 2 |
5 - 10 |
|
5 - 10 |
10 |
- 20 |
20 |
|
|
|
|
|
|
|
|
2 |
- 4 |
10 - 20 |
|
10 - 30 |
20 |
- 50 |
до 120 |
|
|
|
|
|
|
|
|
|
4 |
> 20 |
|
> 30 |
> 50 |
до 120 |
|
|
|
|
|
|
|
|
|
Для подсчета твердости используют таблицы, составленные для
стандартных нагрузок и позволяющие по диагонали отпечатка установить число твердости (приложение 3).
Метод Виккерса имеет следующие достоинства:
1)позволяет замерять твердость в поверхностных слоях и тонких образцах толщиной до 0,3 им ;
2)полностью сохраняются условия подобия при испытаниях;
3)высокая точность замера размеров отпечатка;
4)широкий диапазон измерения твердостей и практическое совпадение чисел твердости по Виккерсу и Бринелю.
Разновидностью метода определения твердости путем вдавливания алмазной пирамиды является метод микротвердости, где применяются нагрузки от 1 до 200 г. Этот метод позволяет измерять твердость отдельных составляющих сплава в пределах одного зерна или кристаллита.
Твердомер ТК. Измерение твердости по методу Виккерса проводят на специальном прессе, схема которого приводится на рис. 12.6. Перед испытанием прибор должен быть взведен рукояткой 1. Образец помещается на предметный столик 4 и вращением штурвала 3 доводится до соприкосновения с торцом чехла алмазной пирамиды 5, что обеспечивает зазор между поверхностью образца и вершиной пирамиды в 0,1 - 0,З мм. Стержень 8 передает нагрузку на пирамиду от рычага 9, на конце которого укреплена

39
подвеска со сменными грузами 11. Грузовой привод включается нажимом на педаль пускового рычага 2.
Рис.12.6. Схема пресса Виккерса
Под действием груза 12 втулка 13 и опирающийся на нее стержень 10 опускаются, освобождая рычаг 9, и нагрузка плавно передается на пирамиду. Одновременно тяга 14 поднимает рычаг 15 навстречу стержню 10. Дальнейшее опускание втулки 13 продолжит подъем рычага 15 и стержня 10, который к
концу хода скалки масляного амортизатора придет в начальное положение и снимет нагрузку. Такое устройство способствует опусканию и подъему груза без толчков. В течение выдержки образца под нагрузкой горит сигнальная лампочка 7, включаемая контактом на рычаге 9.
Поворотом маховичка 3 опускают столик 4 так, чтобы не было касания пирамиды к образцу, и поворотом головки подводят окуляр микроскопа к отпечатку. В поле зрения микроскопа имеются два штриха. Микроскоп устанавливают так, чтобы неподвижный штрих совпал с углом отпечатка.
Второй штрих при помощи микрометрического винта передвигается до совпадения с другим углом отпечатка. Размер диагонали отсчитывают по шкале
40
микрометрического винта. Таким образом, измеряют обе диагонали отпечатка. Записав результат в журнал, проводят повторное испытание в другом месте образца.
6. Сравнение чисел твердости. Так как твердости при измерениях разными методами представляют собой условные числа, то сравнение их может производиться только с помощью эмпирических таблиц. Эти таблицы обычно
используются для пересчета чисел твердости на твердость по Бринелю (приложение 4).
Установлены экспериментальные корреляционные зависимости твердости HB, которая характеризует сопротивление материала пластическим деформациям, с другими механическими характеристиками (σ В, S К и ψ).
Широко применяется вычисление временного сопротивления σ В по значениям твердости HB
σB = (0,30 ÷ 0,36)HB
7.Проведение испытаний. Каждому студенту выдается плитка из мягкой
стали, на которой проводится три замера твердости по Бринелю и три замера твердости по Роквеллу (шкала В). Производится сравнение твердости,
полученной различными методами, путем перевода твердости на твердость HB
с помощью таблицы (приложение 4). По замеренной твердости HB
предлагается вычислить временное сопротивление материала. Кроме того,
производится замер твердости закаленной пластины по методу Виккерса и методу Роквелла (шкала С).
8.Вопросы для самопроверки
1.Что такое твердость материала?
2.Какие механические свойства материала характеризует твердость?
3.Основные преимущества испытаний на твердость по сравнению с другими видами механических испытаний?
4.Перечислите основные виды испытаний на твердость.
5.На чем основаны методы испытаний на твердость?