
594704
.pdf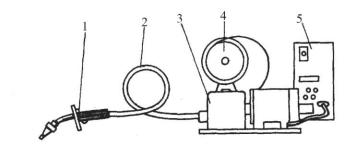
Рис. 11.1. Схема полуавтомата для дуговой сварки
Его назначение и компоновка примерно те же, что и у сварочных головок автоматов для дуговой сварки. Обычно она состоит из электродвигателя, редуктора и системы подающих и прижимных роликов. Механизм обеспечивает подачу электродной проволоки по гибкому шлангу в зону сварки. Приводом могут использоваться двигатели переменного или постоянного тока. Скорости подачи в первом случае изменяют сту- пенчато-сменными шестернями, во втором – плавное регулирование за счет изменения частоты вращения двигателя.
Конструктивное оформление механизма подачи во многом зависит от назначения полуавтомата. В полуавтоматах для сварки проволокой большого диаметра механизм подачи размещен на передвижной тележке и располагается в отдельном корпусе. В полуавтоматах с проволокой малого диаметра он установлен в переносном футляре и расположен непосредственно на корпусе держателя.
Наибольшее распространение получили полуавтоматы толкающего типа. Подающий механизм подает проволоку путем проталкивания ее через гибкий шланг к горелке. Устойчивая подача в этом случае возможна придостаточнойжесткости электроднойпроволоки.
В полуавтоматах тянущего типа механизм подачи или его подающие ролики размещены в горелке. В этом случае проволока протягивается через шланг. Такая система обеспечивает устойчивую подачу мягкой и тонкой проволоки. Имеются полуавтоматы с двумя синхронно работающими механизмами подачи, осуществляющими одновременно проталкивание и протягивание проволоки через шланг (тянуще-толкающий тип).
Гибкий шланг в полуавтоматах предназначен для подачи электродной проволоки, сварочного тока, защитного газа, а иногда и охлаждающей воды к горелке. С этой целью применяют шланговый провод специальной конструкции (рис. 11.2).
Внутри провода для направления проволоки расположена спираль 1, изолированная от токоведущей части 2 бензостойкой изоляцией.
151
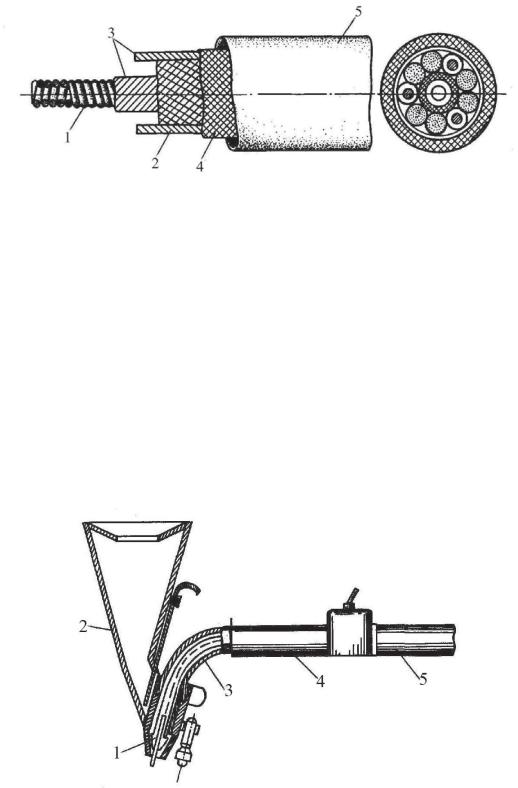
Рис. 11.2. Схема специального шлангового провода
Вместе с токоподводящей частью помещены изолированные проводники 3 цепей управления. Провод заключен в хлопчатобумажную оплетку 4 и покрыт резиновой изоляцией 5. Применяются и составные шланги, состоящие из нескольких трубок и проводов для подачи тока, газа и воды, собранных в общий жгут.
Сварочные горелки предназначены для подвода к месту сварки электродной проволоки, сварочного тока и защитного газа или флюса, а также для ручного перемещения и манипулирования им в процессе сварки. При этом сварщик удерживает держатель в руке и перемещает его вдоль шва. Быстро изнашивающимися частями держателя (при сварке в защитных газах – горелками) являются токоподводящий наконечник и газовое сопло, изготовляемые из меди. При сварке под флюсом на держателе устанавливается бункер для флюса (рис. 11.3).
Рис. 11.3. Держатель полуавтомата для сварки под флюсом:
1 – наконечник; 2 – бункер для флюса; 3 – сварочная проволока; 4 – ручка; 5 – шланг
152
Таблица 11.1
Технические характеристики сварочных полуавтоматов
Параметры |
|
ПДГ-160 |
ПДГ-200 |
ПДГ-251 |
ПДГ-252 |
ПДГ-352 |
|
Напряжение питающей |
220 |
220 |
3×380 |
3×380 |
3×380 |
||
сети, В |
|
|
|||||
|
|
|
|
|
|
|
|
Потребляемая |
мощ- |
4,5 |
6,8 |
17 |
9,1 |
16 |
|
ность, кВА |
|
|
|||||
|
|
|
|
|
|
|
|
Сварочный ток, А (ПВ) |
100 (25%) |
200 (10%) |
250 (60%) |
250 (40%) |
315 (60%) |
||
Диаметр |
сплошной |
0,8–1 |
0,8–1,4 |
0,8–1,4 |
0,8–1,2 |
0,8–1,6 |
|
электродной |
проволо- |
||||||
ки, мм |
|
|
|
|
|
|
|
Скорость подачи |
про- |
45–950 |
60–720 |
40–950 |
100–850 |
60–1200 |
|
волоки, м/ч |
|
|
|
|
|
|
|
Количество |
подающих |
1 |
1 |
1 |
1 |
2 |
|
роликов, шт. |
|
|
|||||
|
|
|
|
|
|
|
|
Напряжение |
холостого |
40 |
45 |
45 |
45 |
45 |
|
хода, В |
|
|
|||||
|
|
|
|
|
|
|
|
Масса, кг |
|
|
30 |
40 |
110 |
60 |
120 |
Габаритные |
размеры, |
325×470 |
810×350 |
815×345 |
810×350 |
815×345 |
|
мм |
|
|
×420 |
×680 |
×815 |
×630 |
×815 |
ВОПРОСЫ
1.Что представляют собой сварочные полуавтоматы? Их назначение и классификация.
2.Опишите устройство и принцип работы полуавтомата для сварки в защитном газе и под флюсом.
3.В чем заключается принципиальное различие сварочных головок в автоматах и полуавтоматах?
4.Какой тип подающего устройства более подходит для механизированной дуговой сварки тонкой и мягкой сварочной проволокой?
5.Можно ли полуавтоматом выполнять сварку в автоматическом режиме и как?
153
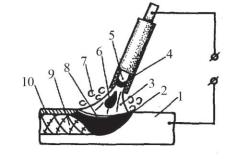
ГЛАВА 12. ТЕХНОЛОГИЯ РУЧНОЙ ДУГОВОЙ СВАРКИ
12.1.СУЩНОСТЬ СПОСОБА И ОБОРУДОВАНИЕ
Спомощью ручной дуговой сварки выполняется большой объем сварочных работ при производстве сварных конструкций. Наибольшее применение находит ручная дуговая сварка покрытыми электродами. Схема процесса ручной дуговой сварки металлическим покрытым электродом показана на рис. 12.1.
Рис. 12.1. Схема процесса ручной дуговой сварки с покрытыми электродами
Дуга 3 горит между стержнем 5 и основным металлом 1. Под действием теплоты дуги электрод и основной металл расплавляются, образуя сварочную ванну 2. Капли жидкого металла 6 с электродного стержня переносятся в ванну через дуговой промежуток. Вместе с металлическим стержнем плавится и электродное покрытие 4, образуя газовую защиту 7 и жидкую шлаковую пленку 8 на поверхности расплавленного металла. В связи с тем, что большая часть теплоты выделяется на торце металлического стержня электрода, на его конце образуется коническая втулка из покрытия, способствующая направленному движению газового потока. Это улучшает защиту сварочной ванны. По мере движения дуги сварочная ванна охлаждается и затвердевает, образуя сварной шов 9. Жидкий шлак также затвердевает и образует на поверхности шва твердую шлаковую корку 10, удаляемую после сварки. При этом способе выполняется газошлаковая защита расплавленного металла от взаимодействия с воздухом. Кроме того, шлаки позволяют проводить необходимую металлургическую обработку металла в ванне. Для выполнения функций защиты и обработки расплавленного металла покрытия электродов при расплавлении должны образовывать шлаки и газы с определенными физико-химическими свойствами. Поэтому для обеспечения заданного состава и свойств шва при выполнении соединений на разных металлах для сварки применяют электроды с определенным типом покрытий, к которым предъявляют ряд специальных требований (см. главу 12 «Сварочные материалы»).
154
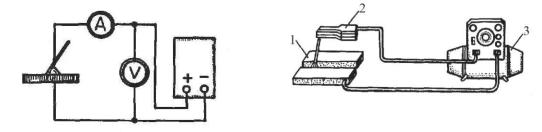
При сварке покрытыми электродами перемещение электрода вдоль линии сварки и подачу электрода в зону дуги по мере его плавления осуществляют вручную. При этом возникают частые изменения длины дуги, что отражается на постоянстве основных параметров режима: напряжения дуги и силы сварочного тока. С целью поддержания более стабильного теплового режима в ванне при ручной дуговой сварке применяют источники питания с крутопадающими вольтамперными характеристиками. Схема питания дуги при ручной дуговой сварке показана на рисунке 12.2.
б
а
Рис. 12.2. Схема поста ручной дуговой сварки покрытыми электродами:
а – электрическая сварочная цепь; б – компоновка сварочного поста; 1 – деталь; 2 – держатель; 3 – источник питания дуги
Кроме источника питания дуги основным инструментом сварщика при ручной сварке покрытыми электродами является электрододержатель, предназначенный для крепления электрода, подвода к нему сварочного тока и возможности манипулирования электродом в процессе сварки. По способу закрепления электрододержатели разделяют на вилочные, пружинные, зажимные.
Рациональная область применения дуговой сварки покрытыми электродами – изготовление конструкций из металлов с толщиной соединяемых элементов более 2 мм при небольшой протяженности швов, расположенных в труднодоступных местах и различных пространственных положениях.
Основными преимуществами способа является универсальность и простота оборудования. Недостаток – невысокая производительность и применение ручного труда. Невысокая производительность обусловлена малыми допустимыми значениями плотности тока. Для увеличения производительности используют сварку погруженной дугой, пучком электродов или применяют электроды с железным порошком в покрытии.
При сварке неплавящимся, обычно вольфрамовым, электродом в защитном газе применяются сварочные горелки (рис. 11.3). В настоящее время выпускают три типа горелок: ГСН-1, ГСН-2, ГСН-3 – на токи 450, 150, 70 А.
155
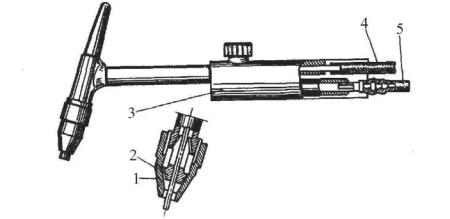
Рис. 12.3. Горелка для ручной дуговой сварки в защитном газе:
1 – сопло; 2 – наконечник; 3 – ручка; 4 – подвод тока; 5 – подвод газа
12.2. ПОДГОТОВКА ДЕТАЛЕЙ ПОД СВАРКУ
Для выполнения сварки соединяемые детали требуют определенной подготовки. Основной металл, предназначенный для изготовления сварных конструкций, предварительно выпрямляют, размечают, разрезают на отдельные детали и выполняют необходимое профилирование кромок.
Основные типы, конструктивные элементы и размеры сварных соединений из сталей, а также сплавов на железоникелевой и никелевой основах, выполняемых ручной дуговой сваркой, установлены ГОСТ 5264-80, которым предусмотрено четыре типа соединений в зависимости от толщины свариваемых деталей. По форме подготовленных кромок соединения бывают с отбортовкой кромок, без скоса кромок и со скосом кромок – одной или двух. Выполнять швы можно как с одной стороны соединений (односторонние), так и с двух сторон (двусторонние).
При расположении свариваемых деталей под углом основные типы, конструктивные элементы и размеры швов сварных соединений установлены ГОСТ 11534-75, которым предусмотрены формы подготовки кромок и размеры выполнения швов угловых и тавровых соединений.
От состояния поверхности свариваемых кромок в значительной мере зависит качество сварных швов. Подготовка кромок под сварку состоит в тщательной очистке их от ржавчины, окалины, грязи, масла и других инородных включений. Кромки очищают стальными вращающимися щетками, гидропескоструйным и дробеметным способами, шлифовальными кругами, пламенем сварочной горелки, травлением в растворах кислот и щелочей.
156

Подготовленные детали собирают под сварку. При сборке важно выдержать необходимые зазоры и совмещение кромок. Точность сборки проверяют шаблонами, измерительными линейками и различного рода щупами (рис. 12.4). Сборку выполняют в специальных приспособлениях или на выверенных стеллажах. Временное закрепление деталей производят струбцинами, скобами или прихваткой короткими швами.
Рис. 12.4. Контроль качества сборки с помощью шаблонов
12.3. РЕЖИМЫ РУЧНОЙ ДУГОВОЙ СВАРКИ ПОКРЫТЫМИ ЭЛЕКТРОДАМИ
Под режимом сварки понимают совокупность контролируемых параметров, определяющих сварочные условия. Выбор режима предусматривает определение значений параметров, при которых обеспечивается устойчивое горение дуги и получение швов заданных размеров, формы и свойств. Параметры режима подразделяют на основные и дополнительные. К основным параметрам ручной дуговой сварки покрытыми электродами относят диаметр электрода, силу сварочного тока, род и полярность его, напряжение дуги. К дополнительным относят состав и толщину покрытий, положение шва в пространстве, число проходов.
Диаметр электродов выбирают в зависимости от толщины металла, катета шва, положения шва в пространстве. Примерное соотношение между толщиной металла S диаметром электрода d при сварке шва в нижнем положении составляет (табл. 12.1).
Таблица 12.1
Соотношение между толщиной металла и диаметром электрода
S, мм |
1–2 |
3–5 |
4–10 |
12–24 |
30–60 |
|
d, мм |
2–3 |
3–4 |
4–5 |
5–6 |
6 и более |
|
|
|
|
|
|
|
157
Выполнение вертикальных, горизонтальных и потолочных швов независимо от толщины свариваемого металла производится электродами небольшого диаметра (до 4 мм), так как при этом легче предупредить стекание жидкого металла и шлака из сварочной ванны. При сварке многослойных швов для лучшего провара корня шва первый шов сваривают электродом диаметром 3–4 мм, а последующие – электродами большего диаметра.
Сила сварочного тока обычно устанавливается в зависимости от выбранного диаметра электрода. При сварке швов в нижнем положении шва для электродов диаметров 3–6 мм сила тока может быть определена по соотношению
IД=(20+6×d)×d, |
(12.1) |
для электродов диаметром менее 3 мм |
|
IД=30×d. |
(12.2) |
Из приведенной зависимости следует, что допустимая сила тока ограничена. При большой силе тока наблюдается перегрев стержня электрода. В результате ухудшаются защитные свойства покрытия, его осыпание со стержня, нарушается стабильность плавления электрода.
При сварке на вертикальной плоскости силу тока уменьшают на 10–15 %, а в потолочном положении – на 15–20 % против выбранного для нижнего положения шва.
Род тока и полярность устанавливаются в зависимости от вида свариваемого металла и его толщины. При сварке постоянным током обратной полярности на электроде выделяется больше теплоты. Исходя из этого обратная полярность применяется при сварке тонких деталей с целью предотвращения прожога и при сварке легированных сталей во избежание их перегрева. При сварке углеродистых сталей применяют переменный ток исходя из учета экономичности процесса.
Основные положения сварки. Ручную сварку можно производить во всех пространственных положениях шва, однако следует стремиться к нижнему положению, как более удобному и обеспечивающему лучшие условия для достижения высокого качества сварного шва.
12.4. ТЕХНОЛОГИЯ ВЫПОЛНЕНИЯ РУЧНОЙ ДУГОВОЙ СВАРКИ
Технология выполнения ручной дуговой сварки предусматривает способ возбуждения дуги, перемещения электрода в процессе сварки, порядок наложения швов в зависимости от особенностей сварных соединений.
Возбуждение дуги осуществляется при кратковременном прикосновении конца электрода к изделию и отведении его на расстояние 3–5 мм.
158

Технически этот процесс можно осуществлять двумя приемами: касанием электрода впритык и отводом его вверх; чирканьем концом электрода, как спичкой, о поверхность изделия.
В процессе сварки необходимо поддерживать определенную длину дуги, которая зависит от марки и диаметра электрода. Ориентировочно нормальная длина дуги должна быть в пределах
Lд=(0,5…1,1)×d, (12.3)
где Lд – длина дуги, мм; d – диаметр электрода, мм.
Длина дуги оказывает существенное влияние на качество сварного шва и его геометрическую форму. Длинная дуга способствует более интенсивному окислению и азотированию расплавляемого металла, увеличивает разбрызгивание, а при сварке покрытыми электродами основного типа приводит к пористости металла.
Для образования сварного шва электроду придается сложное движение в трех направлениях. Первое движение – это поступательное движение электрода по направлению его оси. Оно производится со скоростью плавления электрода и обеспечивает поддержание определенной длины дуги. Второе движение электрода направлено вдоль оси шва и производится со скоростью сварки. В результате этих двух движений образуется узкий, шириной не более 1,5 диаметра электрода, так называемый ниточный шов. Такой шов применяется при сварке тонкого металла, а также при выполнении корня шва при многослойной (многопроходной) сварке. Третье движение – это колебание конца электрода поперек оси шва, которое необходимо для образования валика определенной ширины, хорошего провара кромок и замедления остывания сварочной ванны. Колебательные движения электрода поперек оси шва (рис. 12.5) могут быть различными и определяются формой, размером и положением шва в пространстве.
Рис. 12.5. Колебательные движения электрода при ручной дуговой сварке
159

При горении дуги в жидком металле образуется кратер, являющийся местом скопления неметаллических включений, что может привести к возникновению трещин. Поэтому в случае обрыва дуги (а также при смене электрода) повторное зажигание ее следует производить впереди кратера, а затем переместить электрод назад, переплавить застывший металл кратера и только после этого продолжить процесс сварки. Сварщик должен внимательно следить за расплавлением кромок деталей и торца электрода, проплавлением корня шва и не допускать затекания жидкого металла впереди дуги.
Заканчивают сварку заваркой кратера. Для этого или держат неподвижно электрод до естественного обрыва дуги, или быстро укорачивают дугу вплоть до частых коротких замыканий, после чего ее резко обрывают.
Выполнение стыковых швов. Стыковые швы применяют для получения стыковых соединений. Стыковые соединения со скосом одной или двух кромок могут выполняться однослойными или многослойными швами. При сварке однослойным швом дугу возбуждают на краю скоса кромки, а затем, переместив ее вниз, проваривают корень шва. На скосах кромок движение электрода замедляют, чтобы лучше проварить их. При переходе дуги с одной кромки на другую скорость движения электрода увеличивают во избежание прожога в месте зазора между кромками. При сварке многослойным швом после заполнения каждого последующего слоя предыдущий слой тщательно зачищают от шлака, так как в противном случае между отдельными слоями могут образоваться шлаковые включения. Последними проходами создается небольшая выпуклость шва высотой 2–3 мм над поверхностью основного металла.
Сварку соединений ответственных конструкций большой толщины (свыше 25 мм), когда появляются объемные напряжения и возрастает опасность образования трещин, выполняют с применением специальных приемов заполнения швов блоками или каскадом. При сварке блоками (рис. 12.6) сначала в разделку кромок наплавляют первый слой небольшой длины 200–300 мм, затем второй слой, перекрывающий первый и имеющий примерно в два раза большую длину.
а |
б |
в |
Рис. 12.6. Способы заполнения разделки кромок: а – заполнения блоками;
б – односторонний каскад; в – двусторонний каскад
160