
594704
.pdf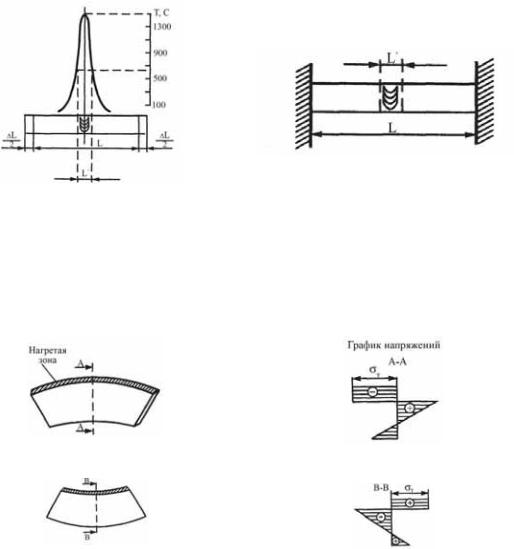
нии стержень должен бы укоротиться, но этому препятствует жесткое закрепление его, в результате чего в нем возникают растягивающие напряжения.
а |
б |
Рис. 6.2. Местный нагрев стержня: а – незакрепленного;
б – с жестким закреплением
Аналогичным образом возникают внутренние напряжения и деформации при наплавке валика на кромку металлической пластины
(рис. 6.3, а).
а |
б |
|
в |
г |
|
Рис. 6.3. Напряжения и деформации при наплавке валика на кромку полосы
Наплавленный валик и нагретая часть пластины будут расширяться и растягивать холодную часть, вызывая в ней деформацию растяжения с изгибом. Сам же валик и нагретая часть пластины будут сжаты, поскольку их тепловому расширению препятствует ее холодная часть. Характер распределения напряжений показан на рисунке 6.3, б. Растягивающие напряжения принято обозначать знаком «+», а сжимающие – знаком «–». В результате такого распределения напряжений пластина прогнется выпуклостью вверх. В процессе остывания наплавленный ва-
71
лик и нагретая часть полосы, претерпев пластическую деформацию, будут укорачиваться. Этому укорочению вновь будут препятствовать слои холодной части металла пластины. Теперь уже наплавленный металл и нагревшаяся часть пластины будут стягивать участки холодного металла. Они сожмутся, и пластина прогнется выпуклостью вниз (рис. 6.3, в), а остаточные напряжения в ней распределятся, как показано на рисунке 6.3, г. В реальных условиях изменение температуры от нагретой к холодной зоне пластины происходит постепенно, поэтому таким же образом происходит и распределение напряжений.
Литейная усадка наплавленного металла. При охлаждении и за-
твердевании жидкого металла сварочной ванны происходит его усадка. Явление усадки объясняется тем, что при затвердевании увеличивается плотность металла, в результате чего объем его уменьшается. Поскольку металл шва неразрывно связан с основным металлом, остающимся в неизменном объеме и противодействующим этой усадке, в сварном соединении возникают внутренние напряжения. При сварке происходит продольная и поперечная усадка расплавленного металла, в результате чего в шве образуются продольные и поперечные внутренние напряжения, вызывающие деформации сварных соединений. За счет продольной усадки возникает деформация изделий в продольном направлении относительно оси шва, а поперечная, как правило, вызывает угловые деформации в сварном соединении.
Напряжения от структурных превращений в металле. Наряду с термическими напряжениями при сварке могут возникнуть напряжения, обусловленные превращениями и изменениями структуры основного металла, нагревшегося выше критических температур. При сварке изделий из углеродистых и высоколегированных сталей особенно легко могут возникнуть напряжения при образовании мартенсита, обладающего наибольшим удельным объемом. При сварке низкоуглеродистой стали в интервале критических температур АС1 и АС3, в связи с тем что коэффициент линейного расширения для γ-железа составляет 1,2·10-5, а для α-железа – 2·10-5, наблюдается уменьшение объема при нагревании от АС1 до АС3. При охлаждении распад аустенита происходит в интервале АС2–АС1, когда сталь пластична и изменение объема происходит без образования напряжений. Иная картина наблюдается у легированных сталей, склонных к закалке. Распад аустенита в них происходит при более низких температурах (200–300 ºС), когда металл обладает высокой прочностью и меньшей пластичностью. Такое превращение сопровождается возникновением структурных напряжений. Растягивающие напряжения от структурных превращений вызывают дополнительное увеличение деформаций, которые в межпластичных сплавах могут привести к обра-
72

зованию трещин. Поэтому сварочные напряжения в закаливающихся сталях более опасны. Для сварки таких материалов необходимо разрабатывать более сложный технологический процесс.
6.3. МЕРЫ БОРЬБЫ С ДЕФОРМАЦИЯМИ
До сварки:
рациональное конструирование сварных изделий: в процессе конструирования необходимо ограничивать количество наплавленного металла уменьшением угла скоса кромок или уменьшения катетов швов, не допускать пересечения большого количества швов, не располагать сварные швы там, где действуют максимальные напряжения от внешних нагрузок, размещать их симметрично, применять, преимущественно, стыковые швы и т.п.;
правильная сборка деталей с учетом возможных деформаций:
заранее предугадать характер возможных напряжений и деформаций и произвести предварительный выгиб свариваемых деталей в противоположную сторону. При сборке следует избегать прихваток, которые создают жесткое закрепление деталей и способствуют возникновению значительных остаточных напряжений, Лучше применять сборочные приспособления, допускающие некоторое перемещение деталей при усадке металла.
В процессе сварки:
рациональная последовательность наложения сварных швов:
конструкции следует сваривать так, чтобы замыкающие швы, создающие жесткий контур, заваривались в последнюю очередь. Сварку нужно вести от середины конструкции к ее краям, как бы сгоняя при этом внутренние напряжения наружу. Каждый последующий шов при многослойной сварке рекомендуется накладывать в направлении, обратном наложению предыдущего шва;
уравновешивание деформаций: назначают такую последова-
тельность выполнения швов, при которой последующий шов должен вызывать деформации обратного направления по сравнению с деформациями от предыдущего шва;
жесткое закрепление деталей при сварке: детали закрепляют в сборочно-сварочых приспособлениях, обладающих значительной жесткостью.
После сварки:
механическая правка: при помощи молотов, домкратов, винтовых прессов ли других устройств создается ударная или статическая на-
73

грузка, которая обычно прилагается со стороны наибольшего выгиба изделия;
термическая правка: местный нагрев небольших участков металла деформированной конструкции. Нагрев, как правило, производят сварочными горелками большой мощности. Он ведется быстро и только до пластического состояния верхних волокон на выпуклой стороне изделия. При охлаждении нагретых участков последние сжимаются и выпрямляют изделие;
термомеханическая правка: данный способ состоит в сочетании местного нагрева с приложением статической нагрузки, изгибающей исправляемый элемент конструкции в нужном направлении. Такой способ обычно применяется для правки жестких сварных узлов.
ВОПРОСЫ
1.Каковы различия в понятиях «напряжение» и «деформация»?
2.Каков механизм образования напряжений и деформаций в процессе сварки?
3.Какие основные параметры режима влияют на величину сварочных напряжений?
4.Как классифицируют напряжения и деформации в процессе сварки?
5.Каким образом снижают деформации в процессе сварки?
6.Какими способами устраняют напряжения и деформации конструкций после сварки?
7.Каким образом можно уменьшить деформации за счет изменения условий сварки?
8.Как влияет погонная энергия на величину деформации?
9.Как предварительный подогрев влияет на образование напряжений и деформации?
10.Какие виды термической обработки существуют для снятия напряжений в изделии?
74
ГЛАВА 7. ОПРЕДЕЛЕНИЕ СВАРИВАЕМОСТИ
7.1.ОПРЕДЕЛЕНИЕ СВАРИВАЕМОСТИ И ЕЕ ВИДЫ
Внастоящее время сварка как технологический процесс образования неразъемного соединения деталей находит применение для соединения не только металлов, но и ряда неметаллов (пластмасс, керамики стекла и т.д.), а также разнородных материалов (металл не металлом). Конечной задачей сварки является обеспечение таких связей между соединяемыми деталями, которые удовлетворяли бы требованиям эксплуатации изделия. Возможность получения указанных связей характеризуется свариваемостью. Это понятие охватывает собой совокупность свойств материалов, обеспечивающих образование соединения без применения специальных крепежных деталей (заклепок и др.).
Вопрос о свариваемости возник с появлением самого способа соединения деталей сваркой и его решению посвящено много работ, в которых дается определение понятию свариваемости, разрабатываются конкретные приемы сварки и т.д. Под свариваемостью понимают свойство твердых тел образовывать при определенном виде сварки неразъемное соединение, способное противостоять соразмерно с основным материалом заданному напряженному состоянию или химическому воздействию окружающей среды. Свариваемость следует рассматривать с двух точек зрения: физической и технологической.
Под физической (принципиальной) свариваемостью понимают способность данного материала (или разнородных материалов) давать неразъемное соединение путем установления внутренних связей между частицами (атомами, молекулами) соединяемых материалов вне зависимости от способа или технологии сварки, т.е. принципиальную возможность получения сварного соединения.
Под технологической свариваемостью понимают способность данного материала (или разнородных материалов) давать при выбранной технологии сварки неразъемное соединение, удовлетворяющее определенным требованиям. Свариваемость данного материала при различных способах сварки может быть различной.
Технологическая свариваемость металлов и их сплавов зависит от многих факторов – химической активности металлов, степени легирования, структуры и содержания примесей. Чем химически более активен металл, тем больше его склонность к взаимодействию с окружающей средой, в первую очередь к окислению, тем выше в этом случае должны быть качество защиты и возможность металлургической обработки при сварке. К наиболее активным металлам относят титан, цирконий,
75

ниобий, тантал, молибден. При их сварке необходимо защищать от взаимодействия с воздухом не только расплавленный металл, но и прилегающий к сварочной ванне основной металл и остывающий шов с наружной и обратной стороны. Наилучшее качество защиты обеспечивают высокий вакуум и инертный газ высокой частоты. Высокой химической активностью при сварке отличаются и другие цветные металлы: алюминий, магний, медь, никель и сплавы на их основе. Качество защиты обеспечивается инертными газами, а также специальными электродными покрытиями и флюсами.
При сварке сталей и сплавов на основе железа от взаимодействия с воздухом расплавленный металл защищают покрытиями, флюсами и защитными газами.
Наибольшее влияние на свариваемость сталей оказывает углерод. С увеличением содержания углерода, а также ряда других легирующих элементов свариваемость сталей ухудшается. Для сварных конструкций в основном применяют конструкционные низкоуглеродистые, низколегированные, а также легированные стали. Главными трудностями при сварке этих деталей является склонность к горячим трещинам, чувствительность к закаливаемости, и образованию холодных трещин обеспечение равнопрочности сварных соединений. Чем выше содержание углерода в стали, тем больше опасность трещинообразования, труднее обеспечить равномерность свойств сварного соединения. Ориентировочным количественным показателем свариваемости стали известного химического состава является эквивалентное содержание углерода, которое определяется по формуле
С |
С |
|
|
Cr Mo |
V Ni Ca . |
(7.1) |
|
6 |
5 |
||||||
Э |
|
15 |
|
||||
В ней содержание |
углерода и |
легирующих |
элементов берется |
в процентах. В зависимости от эквивалентного содержания электрода и связанной с этим склонности к закалке и образованию трещин стали по свариваемости делят на четыре группы: хорошо, удовлетворительно, ограниченно и плохо сваривающие стали (табл. 7.1).
Стали первой группы имеют СЭ≤0,25 %, хорошо свариваются без образования закалочных структур и трещин в широком диапазоне режимов, толщин и конструкционных форм. Удовлетворительно сваривающиеся стали (СЭ=0,25…0,35 %) мало склонны к образованию холодных трещин при правильном выборе режимов сварки, в ряде случаев требуется подогрев. Ограниченно сваривающиеся стали (СЭ=0,36…0,45 %) склонны к трещинообразованию. Возможность регулирования сопротивляемости образованию трещин изменением режимов сварки ограничена, требуется подогрев. Плохо сваривающиеся стали (СЭ>0,45 %) весьма склонны к
76
закалке и трещинам, требуют при сварке подогрева, специальных технологических приемов сварки и термообработки.
Таблица 7.1
Классификация сталей по свариваемости |
|||
|
|
|
|
Группа свариваемо- |
Сталь |
|
|
|
|
конструкционная |
|
сти |
углеродистая |
|
|
|
легированная |
||
|
|
|
|
Хорошая |
Ст1, Ст2, Ст3, Ст4, 0,8, |
|
15Г, 20Г, 15ХМ, 10ХСНД, |
|
сталь 10,20, 12кп, 16кп, 20кп |
|
10ХГСНД, 15ХГСНД |
Удовлетворительная |
Ст5, сталь 30,35 |
|
12ХН2, 14Х2МР, 20ХН, |
|
|
|
20ХГСА, 25ХГСА, 30ХМ |
Ограниченная |
Ст6, сталь 40,45,50 |
|
35Г, 40Г, 30ХГСА, |
|
|
|
40ХМФА, 30ХГСМ |
Плохая |
Сталь 65,70,80, У7, У8, У9, У10 |
50Г, 8Х3, 45ХН3МФА, 5ХНТ |
Появление новых методов сварки расширяет перечень материалов, обладающих удовлетворительной или даже хорошей свариваемостью. В настоящее время практически нет ни одного металла или сплава, получившего применение в производстве, который не удалось бы сварить тем или иным способом. Очень ценным свойством материала является хорошая свариваемость несколькими различными видами сварки. К таким материалам относятся низкоуглеродистая сталь, технически чистый алюминий и другие. Отрицательное влияние на свариваемость могут оказать следующие явления:
1.Образование кристаллизационных (горячих) и закалочных (холодных) трещин.
2.Образование хрупких участков в металле шва и зоне термического влияния (структура закалки, выделение карбидов, ликвация, образование интерметаллических соединений и т.п.).
3.Окисление металла шва и другие процессы.
Для предупреждения или ослабления влияния этих явлений требу-
ется применение специальных технологических мер (приемов), например: сварка с предварительным подогревом или последующей термообработкой, сварка с определенным порядком наложения швов и т.п. Поэтому иногда о технологической свариваемости судят по сложности технологических приемов, которые используют для получения удовлетворительных свойств сварных соединений. Причем, чем сложнее технологические приемы, тем худшей технологической свариваемостью обладает материал.
Хотя физико-химические процессы в зоне сварки могут протекать по-разному при различных способах сварки, в любом случае образова-
77
ния неразъемного соединения необходимо либо установить непосредственную связь между поверхностными атомами (молекулами) свариваемых деталей, либо соединить их промежуточной связью. Именно поэтому в зону сварки вводят энергию и вещество одновременно.
ВОПРОСЫ
1.Что понимают под свариваемостью металлов?
2.Каковы способы оценки свариваемости металлов?
3.В чем различие между физической и технологической свариваемостью?
4.Как разделяют стали по свариваемости?
5.Как определить свариваемость по эквиваленту углерода?
6.Почему и как углерод влияет на свариваемость стали?
7.Какие условия могут повысить свариваемость углеродистой стали?
78
ЧАСТЬ 2
ГЛАВА 8. СВАРОЧНЫЕ МАТЕРИАЛЫ
8.1. ПРИСАДОЧНЫЕ МАТЕРИАЛЫ ДЛЯ СВАРКИ
Сварочными называют материалы, обеспечивающие возможность протекания сварочных процессов и получение качественных сварных соединений. К ним относят присадочные металлы, покрытые электроды, флюсы, защитные газы и некоторые другие.
Подавляющее большинство швов при сварке выполняют с применением присадочных материалов. Роль их заключается не только в получении необходимой геометрии шва, но и в обеспечении высоких эксплуатационных характеристик при минимальной склонности к образованию дефектов. В большинстве случаев состав присадочного металла мало отличается от химического состава свариваемого металла. Присадочные металлы разрабатывают применительно к конкретным группам свариваемых металлов и сплавов или даже к их отдельным маркам. При этом учитывают и методы сварки, определяющие потери отдельных элементов. Присадочный металл должен быть более чистым по примесям, содержать меньшие количества газов и шлаковых включений. Присадочные металлы используют в виде металлической проволоки сплошного сечения или порошковой проволоки (с порошковым сердечником). Применяют также прутки, пластины, ленты. К сварочной проволоке предъявляют высокие требования по состоянию поверхности, предельным отклонениям по диаметру, овальности и другим показателям.
Высокое качество сварочной проволоки и других присадочных металлов сохраняется при тщательной упаковке и консервации, а также правильном хранении и транспортировке. Наиболее часто сварочную проволоку поставляют в виде мотков, покрытых консервирующей смазкой. Поверхность мотка обертывают влагонепроницаемой бумагой, полимерной пленкой и т.п. Каждая партия проволоки должна снабжаться сертификатом завода-изготовителя, где указываются марка проволоки, ее химический состав, номер плавки и другие сведения. Присадочные материалы перед сваркой должны проходить тщательную очистку поверхности. Наличие следов смазки или других загрязнений не допускается. В большинстве случаев требуется и очистка от оксидов. Для удаления жировых загрязнений применяют обезжиривание. Оксидную пленку удаляют травлением, химическим и электрохимическим полированием. Для сварки необходимо применять преимущественно присадочные материалы, выпускаемые по специализированным стандартам или техниче-
79
ским условиям. Промышленность выпускает присадочные материалы для сварки сталей, чугуна, алюминия, меди, титана и их сплавов.
Присадочные металлы для сварки и наплавки сталей. Холоднотя-
нутую стальную сварочную проволоку сплошного сечения выпускают по ГОСТ 2246-70, который предусматривает 77 марок разного химического состава, разделяющихся на три группы: низкоуглеродистые, легированные с содержанием легирующих элементов 2,5–10 %, высоколегированные с содержанием легирующих элементов более 10 %. Химический состав некоторых проволок приведен в таблице 8.1. Условные обозначения марок сварочной проволоки состоят из индекса С (сварочная)
иследующих за ним цифр и букв. Цифры после индекса обозначают содержание углерода в сотых долях процента. Последующие буквы указывают на содержание в проволоке легирующих элементов, обозначаемых: алюминий – Ю, азот – А (только в высоколегированных сталях), бор – Р, ванадий– Ф, вольфрам– В, кремний– С, кобальт– К, марганец – Г, медь – Д, молибден – М, никель – Н, ниобий – Б, титан – Т, хром – X, цирконий – Ц. Цифры после букв указывают среднее содержание элемента в процентах (отсутствие цифры означает содержание данного элемента менее 1 %). Буква А в конце обозначений низкоуглеродистых и легированных проволок указывает на повышенную чистоту металла по содержанию серы и фосфора. В проволоке Св-08АА сдвоенная А указывает на пониженное содержание серы и фосфора по сравнению с проволокой Св-08А.
Проволоку различают также по назначению: для сварки (наплавки)
идля изготовления электродов (условное обозначение – Э). Низкоуглеродистую и легированную проволоку выпускают неомедненной и омедненной (условное обозначение – О) для предохранения ее поверхности от коррозии.
Пример условного обозначения сварочной проволоки диаметром 3 мм, марки Св-08А с омедненной поверхностью – проволока 3Св-08А-0 ГОСТ2246-70.
Стальную сварочную проволоку по ГОСТ 2246-70 выпускают сле-
дующих диаметров (мм): 0,3; 0,5; 0,8; 1,0; 1,2; 1,4; 1,6; 2,0; 2,5; 3,0; 4,0; 5,0; 6,0; 8,0; 10,0 и 12,0. Проволока поставляется свернутой в мотки с внутренним диаметром 150–750 мм, массой от 1,5 до 40 кг, а также намотанной на катушки и кассеты (для автоматической и механизированной сварки).
Стальная наплавочная проволока по ГОСТ 10543-75 изготовляется диаметром от 0,3 до 8,0 мм: из углеродистой стали – 9 марок (Нп-25, Нп-30 и т.д.), из легированной стали – 11 марок (Нп-10Г, Нп-50Г,
80