
Госник
.pdf
валика на 1/3 ширины.каждый слой необходимо очищать от шлака и наплавку вести с прерыванием на остывание. Этот видсварки использ-ся при небольших объемах работы.
Преимущества: удобство и простота.
Недостатки: низкая производительность, низкая стабильность дуги, невысокое качество.
Электродуговая автоматическая под слоем флюса
Этот вид используется при ремонте большого кол-ва однотипных деталей. Дуга горит под слоем флюса.
Рис. 5.11. Схема наплавки под слоем флюса:1 — нерасплавленный флюс; 2 — жидкий металл; 3 — электрод; 4— расплавленный шлак; 5 — деталь; 6 — наплавленный металл;7 — шлаковая корка
Флюс (АН-348А, АНК-18, ЖС-400 и др.) наносят в виде пасты на свариваемые поверхности деталей и на присадочный пруток. Деталь предварительно нагревают до температуры 300—350° С.
Этим способом можно наплавлять плоские, цилиндрич, конические пов-ти. Для питания использ пост ток. Обычно слой флюса составляет 40…60 мм над наплавляемым слоем. Качество наплавки зависит от силы тока, скорости и диаметра электрода. Сила тока
I 110d эл 10d эл2
Преимущества: высокая производительность, высокое качество и возможность широкого регулирования свойств наплавленного слоя, наличие закрытой дуги,
улучшающее условия труда.
63.Наплавка деталей в среде защитных газов и вибродуговая наплавка.
Всреде защитных газов При этом виде наплавки защитный газ, подаваемый в зону наплавки под избыточным давлением, изолирует сварочную дугу и плавильное пространство от кислорода и азота воздуха Наплавку углеродистых, легированных сталей и чугуна производят в среде углекислого газа; для высоколегированных сталей
применяют аргон. При высокой температуре сварочной дуги происходит диссоциация углекислого газа. Образовавшийся атомарный кислород окисляет металл, что приводит к выгоранию железа и других примесей стали. Чтобы прекратить
окисление, а также пополнить выгоревшие примеси при наплавке в углекислом газе применяют электродную проволоку, легированную марганцем и кремнием, которые связывают кислород и раскисляют ранее образовавшуюся закись железа. Образующиеся окислы марганца и кремния переходят в шлак.
Содержание углерода в электродной проволоке должно быть небольшим, в противном случае могут образоваться поры и горячие трещины в металле шва.
Вибродуговая наплавка
Преимущества простота введения и управление процессом, высокая производительность.
Недостатки окислительная способность углекислого газа, высокая стоимость инертных газов, вероятность срыва потока защитного газа на открытом воздухе.
Автоматическая вибродуговая наплавка основана на использовании тепла кратковременной электрической дуги, возникающей в момент разрыва цепи между вибрирующим электродом и наплавляемой поверхностью. Отличительной особенностью этого вида наплавки является возможность получения наплавленного слоя малой толщины 0,3—2,5 мм, охлаждение поверхности наплавки в результате прерывистого характера процесса, что позволяет значительно уменьшить нагрев детали, снизить в ней остаточные напряжения и предотвратить ее деформирование. Частота 55-100 Гц. Охлаждающая жидкость 5% водный раствор кальцинированной соли 20%водный раствор глицерина.
Преимущества: получение тонких слоев прочных покрытий 0,3 мм, малая глубина проплавления детали, незначительное выгорание легирующих элементов проволоки.
Недостатки: неравномерная твердость покрытия, снижение усталостной прочности, наличие газовых пор и трещин в слое.
64. Восстановление изношенной поверхности методом металлизации, принцип, классификация, описание способов, технология металлизации.
Процесс металлизации заключается в нанесении расплав ленного, металла на специально подготовленную поверхность детали распылением его струей воздуха или газа. Частицы расплавленного металла, ударяясь о поверхность детали, заполняют

предварительно созданные на поверхности неровности, в результате чего происходит их механическое закрепление, а также возникает молекулярное схватывание между напыляемым и основным металлом. В результате закалки, окисления и наклепа частиц напыляемого металла твердость материала покрытия повышается. Различают газовую, электродуговую, высокочастотную, тигельную и плазменную металлизацию. Напыляемый материал применяется в виде проволоки, ленты или порошка. Плотность напиленного слоя зависит от скорости частиц при ударе, а следовательно, от расстояния между соплом и поверхностью детали.
Электродуговая металлизация
Рис. 5.24. Схема электродуговой металлизации Примечание. Нормальное расстояние должно быть 75 — 100 мм. . Две электрически изолированные друг от друга электродные проволоки 1 и 2\ к которым подводится электрический ток, перемещаются механизмом подачи 3 со скоростью 2,5—3,5 м/мин. При выходе из наконечников 6 проволоки пересекаются и под действием возникающей при этом электрической дуги концы их расплавляются. Через сопло 7 подается струя сжатого воздуха под давлением 0.4…07 МПа, которая распыляет расплавленный металл на мельчайшие частицы. Частицы раскаленного металла, двигаясь со скоростью 75—200 м/с, наносятся на
специально подготовленную поверхность детали 4, создавая напиленный слой 5. Ппреимущества электрометаллизации: высокая производительность процесса.
Недостатки электрометаллизации: значительное выгорание легирующих элементов, окисление напыляемого металла, низкие механические свойства напыленного слоя и большие потери металла при напылении.
Газовая металлизация
Проволоку напыляемого металла расплавляют ацетилено-кислородным пламенем, а распыление осуществляют сжатым воздухом или инертным газом. Расход сжатого воздуха обычно составляет 0,6— 0,8 м3/мин, давление 0.3…0.5 МПа. Давление ацетилена должно быть 4…60 КПа, а его расход 240—850 л/ч. Проволока подаётся со скоростью 4,5— 6,0 м/мин в распылительную головку с помощью специального подающего механизма, установленного в газометаллизаторе.
Рисунок – Схема установки газометаллизации: 1-отверстие для смеси ацителена с кислородом; 2-частицы расплавленного металла; 3-отверстие для сжатого воздуха.
Преимущества: получение покрытий высокого качества и прочности. Недостатки: необходимость в горючем газе, высокая стоимость покрытия.
Пазменно-дуговая металлизация
При пропускании электрического тока большой плотности через газовую среду, находящуюся под повышенным давлением, газ ионизируется. Наряду с положительно и отрицательно заряженными ионами в ионизированном газе содержатся электроны и нейтральные атомы. Такое состояние вещества называется плазмой. Плазма обладает высокой электрической проводимостью и образует вокруг себя магнитное поле, которое заставляет частицы плазмы сжиматься и двигаться узким пучком. Плазменная струя служит интенсивным источником тепла; температура ее достигает 15 000° С.Ремонтируемая деталь в цепь источника тока не включается. При указанной схеме включения электрической цепи температура на поверхности детали в процессе металлизации не превышает температуру плавления основного металла и, следовательно, поверхностный слой детали находится в твердом состоянии. Для плазменной металлизации установки УМП-1-61, УМП-2-62 и УМП-4-64
Рисунок – Схема плазменной металлизации: 1-распыляемая проволока; 2-наконечник для проволоки; 3-электрод; 4-горелка; 5-сопло.
Плазменную металлизацию обычно применяют для напыления тугоплавких металлов и их соединений Достоинства: высокая производит-ть, прочность сцепления.
Недостатки: высокая хрупкость напыленного слоя.
Схема процесса металлизации детали:
1)очистка металлизируемой пов-ти;
2)предварительная механическая обработка для придания требуемой геометрической формы и размера;
3)придание наибольшей шероховатости, чтобы обеспечить достаточную прочность сцепления напыленного слоя с основным металлом. Наиболее распространенными способами создания шероховатости являются нарезание рваной резьбы, нарезание круглой
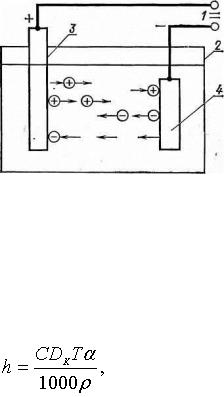
резьбы с обкаткой;
4)изоляция участковпов-ти, не подвергаемых металлизации;
5)металлизация. Процесс металлизации различными способами описан выше;
6)обработка детали после металлизации для получения требуемых размеров, точности и шероховатости поверхности. Преимущества: высокая производительность и экономичность процесса, повышенная твердость 'покрытия по сравнению с исходной твердостью напыляемого металла (для стали на 30—40%), возможность получения покрытия толщиной до 10—15 мм, проведение процесса без нагревания детали Недостатки: невысокая прочность сцепления напыленного слоя с металлом детали, неоднородность покрытия, малая износостойкость покрытия при недостатке смазки.
65.Восстановление поверхностей методом гальванического наращивания. Классификация, технология. Электролитическое хромирование, осталивание деталей.
Перспективный способ восстановления деталей — гальванические покрытия. Благодаря простоте и доступности оборудования он может быть использован практически во всех звеньях ремонтной сети — от мастерских общего назначения до
специализированных цехов ремонтных заводов. Однако следует отметить, что повышение эффективности гальванических процессов при восстановлении деталей, их широкое распространение возможно главным образом за счет механизации и автоматизации.
Рис. 18. Схема процесса электролитического наращивания: 1 — источник тока; 2 — ванна; 3 — анод; 4 — катод.
Наибольшее распространение в ремонтном производстве получили такие гальванические процессы, как хромирование и железнение.
Наращивается металл на изношенные поверхности деталей электролитическим способом в результате электролиза. На рисунке 18 показана принципиальная схема процесса электролиза.
Хромирование
Данный способ ремонта относится к ремонту деталей гальваническим наращиванием, основанным на процессе электролиза. Под действием постоянного тока, поступающего в электролит ч/з проводник. В результате на катоде выделяются металл и Н2, а на аноде кислотные и водные остатки.
Кол-во вещ-ва.выделяемого на катоде:
,
где С-электрохим эквивалент; I-сила тока; Т-время эликтролиза. Средняя толщина металла, осажденного на катоде:
где Dк-плотность тока; a-выход металла по току; r-плотность осажденного металла.
Хромирование применяется при восстановлении размеров, получении декоративных коррозионностойких и износостойких покрытий. После хромирования снижается усталостная прочность. Различают хром гладкий по накатке и пористый. Гладкий по накатке следует применять в условиях достаточной смазки при небольших скоростях. А пористый - в условиях граничного трения. Электрохим-ое осаждение хрома отличается по составу электролита и по условию протекания процесса. Хромовый ангидрид растворяется в дистиллированной воде и после отстаивания переливается в ванну, в которую затем добавляют серную кислоту. При хромировании применяют нератстворимые аноды из свинцово-алюминиевого сплава. Величина зазора м/у деталью и анодом должно быть не менее 30 мм, а между деталью и дном ванны - не менее 50 мм.
Хромовые покрытия разделяют на 3 вида:
1)молочные - наиболее мягкие и вязкие без трещин и обладают большой износостой-тью;
2)блестящие - отличаются высокой плотностью, износо-тью, хрупкостью и имеют на пов-ти мелкую сетку трещин;
3)матовые - имеют повышен твердость и хрупкость, низкую износостойкость и наличие трещин на пов-ти.
Для повыш-я качества и увеличения выхода потока применяют хромирование в саморегулируемых электролитах. Применение таких электролитов обеспечив высокую стабильность работы ванны и дает возможность получить значит толщину покрытия (до 1мм). Хромир-е в электролите заключ в постоянной подаче электролита в зону электролиза. Что обеспечивает перемешивание его в межэлектродном пространстве. Периодическое измен-е направления тока в процессе хромир-я позволяет улучшить качество осадка и интенсивность процесса. После хромирования деталь промывают, термически обрабатывают и шлифуют.
Преимущества:высокая прочность сцепления, высокая износостойкость, химич стойкость.
Недостатки:длительность процесса электролиза, его сложность, трудоемкость, ограниченная толщина покрытия, высокая себестоимость.
Электролитическое осталивание
При прохождении пост тока низкого напряжения ч/з раствор солей железа происходит осаждение на катоде электролитического железа. Прочность и твердость осаждаемого слоя приближается к свойствам углеродной стали, поэтому процесс назвали осталиванием. Для электролит-ого осталивания прмен-ся несколько типов электролитов: хлористые, бор-хлористо-водородные
на основе железа. Для осталивания примен холодные и горячие электролиты. Аноды изготовляются из малоуглерод стали. Для приготовления электролит очищают, загружают в раствор НСL c дистиллированной водой. Затемзасыпают остальные соли. И после осталивания 12…18 ч фильтруют и корректируют кислотность и содержание железа. Введение хлористого натрия обеспечивает снижение напряжения, уменьшение испарения электролита и повыш твердость покрытия. А введение хлористого марганца - увеличивает сцепление.
В зависимости от состава электролита и режима осталивания получают мягкие покрытия с твердостью, соответствующей углеродистой незакаленной стали (НВ 120-220), и твердые покрытия с твердостью, соответствующей закаленной стали (НВ 250600).
Преимущества: исходные материалы, входящие в состав электролита, дешевы; выход металла по току составляет 75…95%; скорость осаждения металла и толщина покрытия значительно выше, чем при хромировании; механическую обработку покрытия после осталивания производят при обычных режимах резания; процесс осталивания легко регулируется и может быть автоматизирован.
Недостатки:высокая коррозионная активность электролита; сложность техпроцесса; необходим-ть частой фильтрации электролита.
Электролитическое меднение.
Для меднения деталей применяют электролиты двух типов: сернокислые и цианистые. Электролитическое никелирование.
Электролитический процесс осаждения никеля называется твердым никелированием.
66. Поверхностное упрочнение деталей. Выбор метода поверхностного упрочнения.
Под упрочнением понимается повышение сопротивляемости материала или заготовки разрушению или остаточной деформации.
При обработке поверхности шлифованием и полированием, устраняющей неровности, которые служат концентраторами напряжений, повышается усталостная прочность детали. Поверхности деталей дополнительно упрочняют более эффективными методами упрочняющей обработки: термической, химико-термической, электроискровой, пластическим
деформированием и нанесением износостойких материалов.
Назначение метода упрочняющей обработки зависит от условий работы детали в машине и ее технологических особенностей. Термическая обработка. Поверхностная закалка — один из видов упрочняющей термической обработки стальных и чугунных деталей. Закалка позволяет значительно повысить прочность и износостойкость деталей. Прочность углеродистой стали можно увеличить обычной закалкой и отпуском в 1,5—2 раза, а легированной стали даже в 2—3 раза.
Поверхностная закалка с нагревом токами высокой частоты основана на использовании явлений индукции и поверхностного эффекта. Деталь помещают внутри спирали (индуктора) или под проводником, по которому пропускается переменный ток большой частоты; он вызывает появление вихревых токов на поверхности детали, и быстро разогревает слой с наибольшей плотностью индуцированного тока. По достижении заданной температуры нагрева деталь интенсивно охлаждают струей жидкости. Имеющая небольшое применение в промышленности поверхностная закалка в электролите заключается в нагреве детали (катода), помещенной в электролит, через который пропускается постоянный ток высокого напряжения. Закалка осуществляется опусканием детали в специальную ванну или в струе электролита при выключенном токе, а также при помощи специального спрейера.
Упрочняющая химико-термическая обработка (ХТО) — это процесс диффузионного насыщения поверхностного слоя металлических деталей активными элементами, обеспечивающими получение определенных физико-механических свойств для повышения твердости, усталостной прочности, износостойкости, жаростойкости и коррозионной стойкости.
Цементация — процесс науглероживания поверхностного слоя стальных деталей, нагретых до температуры свыше 900—940° С, что определяет наибольшую скорость протекания процесса
Детали после цементации и последующей закалки имеют повышенную твердость (HRC 58—62) и прочность поверхностного слоя. Цементация повышает усталостную прочность деталей, благодаря увеличению твердости, прочности цементированного слоя и образованию в нем внутренних напряжений сжатия, которые снижают влияние концентраторов напряжений.
Азотирование— один из процессов химико-термической обработки, при котором поверхностные слои насыщаются расплавленными серосодержащими солями или в газовых средах. Его можно применять для обработки деталей нефтегазопромыслового оборудования, так как при этом способе облегчаются и доводочные операции.
Цинкование - процесс насыщ цинком. Детали погружаюти в расплавленный цинк или порошок цинка.
Упрочняющая электроискровая обработка (ЭИО) основана на протекании импульсного разряда между электродом (анодом)
идеталью (катодом).Сущность ЭИО заключается в полярном переносе материала электрода на деталь (наращивание) при одновременном термическом воздействии тока и легировании поверхности детали элементами упрочняющего электрода и азота воздуха. Упрочненный слой отличается высокой твердостью, обусловленной образованием карбидов, нитридов, карбонитридов
изакалочных структур. Электроискровое упрочнение и нанесение металла происходит в воздушной или газовой среде при
тепловом и химическом действии электрического разряда между поверхностью изделия и упрочняющим электродом, которому сообщается колебательное движение от вибратора. За очень короткое время электроискрового разряда (10~5 — 10~8 с) через электроды проходит мощный (до 106 А/мм2) импульс тока, накопленного в конденсаторах. Температура в межэлектродном зазоре повышается до 11 000° С. При такой температуре азот и легирующие элементы, содержащиеся в электроде, легируют поверхность детали, повышая ее физико-механические свойства.
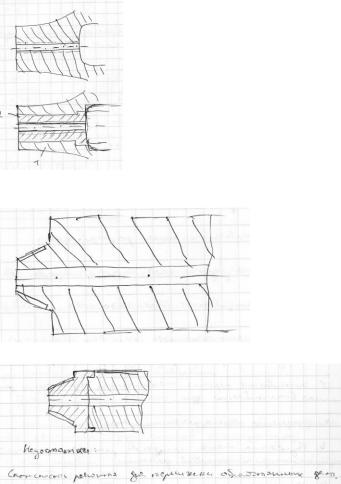
Недостаток метода: невозможность получения упрочненного слоя значительной толщины и снижение усталостной прочности. Упрочняющую обработку поверхностным пластическим деформированием (ППД) применяют в основном для повышения усталостной прочности деталей.
Поверхностный наклеп (ПН) представляет собой поверхностное пластическое деформирование с изменением структуры материала без его полной рекристаллизации. Пластическая деформация приводит к измельчению зерен и уменьшению их размеров, создает текстуру. Обработка дробью – пластич деформирование под действием кинетическ энергии потока дроби. При этом повышается твердость, предел выносливости. Раскатывание применяют для упрочняющей обработки вогнутых поверхностей деталей из стали, чугуна и цветных металлов. Гидроабразивная – струя жид-ти, содержащая абразивный материал выбрасывается со скоростью 50…70м/с.при этом методе снимается верхний слой и пластич деформируются нежележащ слои.
Упрочняющая чеканка – основана на ударном воздействии бойков на обрабатываемую пов-ть, в результате происходит наклеп. Термомеханич обработка – сочетание операций термо и мех обработок. Для осущест-я использ-ся прокатное, волочильное, ковочное, и штампов-е оборудов-е. Для закалки устанавл охлажд устройство. Эффективным методом поверхностного упрочнения деталей машин является наплавка материалов с высокими эксплуатационными свойствами. Этот метод экономичен, так как наплавке подвергают только те поверхности, которые работают в условиях интенсивного изнашивания и, как правило, масса наплавленного материала составляет малую долю от массы детали.Долговечность упрочненных деталей определяется свойствами наплавленного материала, поэтому наносимый материал или сплав выбирают с учетом условий эксплуатации детали и применяемого метода наплавки. Большое применение имеют следующие группы наплавочных материалов: 1) стали, легированные марганцем, хромом, никелем, вольфрамом, молибденом; 2) сплавы на основе железа — высокохромистые, вольфрамовые, молибденовые, чугуны, а также сплавы с высоким содержанием хрома, вольфрама, кобальта, молибдена; 3) сплавы на основе вольфрама, кобальта, никеля.
67. Ремонт поверхностей деталей. Способ дополнительных ремонтных деталей, способ замены части де-тали. Ремонт корпусных деталей.
Способы восстановления поверхностей деталей А) С изменением первоначальных размеров ремонтируемых дет (способ ремонтных размеров) Б) с восстановление первоначальных размеров дет Выбор метода наращивания определяется
1 материала и конструкции дет 2 характером дефектов 3 назначением и режимом работы детали, при этом полностью восстанавливается ресурс
1)способ наращивания доп слоя материала
2)способ доп ремонтных дет
Эти установки устанавливаются на изношенные поверхности при этом толщина износа значительно превышает величину износа ремонтируемых дет.
3) способ замены части детали Удлиняется изношенная часть дет, присоединяется новая.
Метод дополнительных деталей, являющийся разновидностью метода ремонтных размеров, широко распространен при восстановлении под ремонтный размер цилиндров блоков, прошедших последний ремонтный размер, гнезд клапанов, посадочных отверстий под подшипники коробок передач, задних мостов. Метод предусматривает замену изношенной части детали дополнительной, специально для этой цели изготовленной. Наиболее часто таким образом ремонтируют отверстия деталей. В ступицу шкива, шестерни или другой детали, предварительно расточенную до некоторого размера, запрессовывают ремонтную втулку или гильзу.
Если в ступице имеется отверстие для смазки, то запрессованную деталь по торцу прихватывают сваркой в нескольких точках или фиксируют резьбовыми штифтами. После этого втулку растачивают под требуемый размер, сверлят отверстие для смазки и прорубают смазочные канавки.
Для восстановления резьбовых отверстий применяют резьбовые втулки (ввертыши), в которых после установки на место нарезают резьбу номинального шага.
Изношенные участки плоских поверхностей деталей ремонтируют установкой накладок и планок. При этом дефектные участки строгают или фрезеруют, затем из полосовой стали изготовляют и тщательно подгоняют накладки. Их закрепляют винтами или сваркой и обрабатывают вровень с неизношенными поверхностями детали. Способ дополнительных деталей прост и экономичен, так как позволяет сохранить и использовать оставшуюся неизношенной работоспособную часть детали.
Способы ремонта корпусных деталей.
Ремонт базовых корпусных деталей является очень ответственным процессом, так как корпус в большинстве случаев несет не только защитную функцию от внешних факторов, которые могут повлиять на работу механизма, но также являлся и базовой опорой для расположенного внутри механизма. При обнаружении каких-либо дефектов, трещин или сколов на корпусе, следует немедленно провести полную диагностику всего аппарата чтобы оценить степень риска его дальнейшего использования и, в кратчайшие сроки восстановить первоначальный вид корпуса.
Ликвидация трещин: С помощью стяжек. С помощью штифтов. С помощью накладок Заваркой с последующей механической обработкой (при необходимости).
Ремонт пробоин и сколов производят:: Установкой ввертыша. Установкой пробки. Установкой вставки. Заваркой пробоин наплавкой сколов с последующей механической обработкой.
Ремонт изношенных отверстий производят: Установкой ремонтной втулки.Наплавкой отверстия.
Ремонт способом добавочных ремонтных деталей
У значительного количества деталей сложной формы изношенными или поврежденными являются отдельные небольшие элементы детали: гладкие и резьбовые отверстия, шейки валов, места посадки подшипников качения в корпусных деталях, венцы шестерен и т. п. При этом целесообразным является удаление дефектного слоя металла или дефектного элемента детали и восстановление ее постановкой дополнительной ремонтной детали (ДР) — втулки, ввертыша, венца, шестерни — или заменой дефектного элемента детали.
Этот способ имеет несколько характерных случаев применения: 1) ремонт отверстий постановкой ремонтной втулки, гильзы или кольца; 2) ремонт валов напрессовкой втулки, кольца или постановкой полувтулок; 3) ремонт элементов детали разнообразной формы способом удаления дефектного и установки нового элемента детали: заменой зубчатого венца, шлицевой ступицы, шлицевого конца и др.; 4) ремонт плоских поверхностей постановкой планок или накладок.
Ремонт гладких отверстий постановкой ремонтной втулки является наиболее простым и распространенным способом. Примерами такого способа ремонта являются места посадки наружных колец подшипника качения в корпусах коробок передач, раздаточных коробках, ступицах колес, отверстия в сателлитах, чашке дифференциала и в проушинах шкворня моторного катка, отверстие в полумуфте асфальтоукладчика.
Гильзование блоков цилиндров легких и пусковых двигателей применяется тогда, когда диаметр цилиндра больше предельно установленных ремонтных размеров. Для этого цилиндр двигателя растачивают под гильзу с учетом толщины стенок гильзы
3—4 мм.
При ремонте методом ремонтных размеров одну из износившихся деталей соединения обрабатывают до исчезновения следов износа или до получения определенного заранее установленного размера, а вторую, чаще всего более дешевую, заменяют новой. Например, изношенную шейку вала обрабатывают до исчезновения следов износа и комплектуют ее с новой втулкой, обеспечивающей с полученным размером шейки вала требуемую посадку. Такой ремонт может производиться последовательно несколько раз, причем диаметр вала постепенно будет уменьшаться, а диаметр отверстия ремонтируемой детали — увеличиваться. Таким образом, детали сопряжения будут иметь размеры, отличающиеся от первоначальных. Эти новые, заранее установленные размеры деталей соединения принято называть ремонтными.
Различают три вида ремонтных размеров: стандартные, регламентированные, свободные.
Стандартные ремонтные размеры, изготовляемые промышленностью, применяют при ремонте поршней, поршневых пальцев, толкателей, вкладышей, поршневых колец.
Регламентированные ремонтные размеры устанавливаются техническими условиями на восстановление деталей. При этом механическую обработку производят до достижения заданной величины.
Свободные ремонтные размеры предусматривают обработку до получения правильной геометрической формы и чистоты рабочей поверхности деталей. Сопряженную деталь подгоняют к восстановленной до свободного ее размера, оставляя припуск для окончательной подгонки по месту.
68. Ремонт деталей класса «Валы», «Втулки», «Диски». Восстановление шлицевых и шпоночных пазов.
Ремонт деталей типа валов
Большинство деталей этого типа в процессе работы воспринимают значительные крутящие моменты (валы, шпиндели) или знакопеременные осевые нагрузки (штоки, плунжеры и т.п.).
На валах, воспринимающих большие нагрузки, которые направлены перпендикулярно к оси, наблюдаются прогибы. Последние приводят к эксцентричному вращению вала и, как следствие этого, к быстрому изнашиванию опорных поверхностей. В местах посадки шестерен, шкивов или кулачковых муфт происходит разрушение или смятие шпоночного паза. Наиболее характерными дефектами валов являются:
1)износ поверхностей трения в опорах;
2)износ поверхностей, сопрягаемых с подшипниками качения; 3)разрушение или смятие шпоночных пазов; изгиб оси вала; 4)износ резьбовых поверхностей.
У деталей, передающих нагрузки вдоль оси и работающих в направляющих втулках или сальниковых устройствах, основными дефектами являются:
1) износ трущихся поверхностей;
2)продольный изгиб вала;
3)износ резьбовых поверхностей.
Восстановление размеров изношенных шеек вала ведется двумя путями - восстановлением первоначальных и введением ремонтных размеров. Так как в последнем случае может произойти ослабление вала, то наиболее правильным следует считать восстановление первоначальных размеров. Для этого применяют следующие способы ремонта: электродуговую наплавку, металлизацию, вибродуговую наплавку, хромирование, осталивание и полимерные покрытия.
Шейки валов буровых лебедок, насосов и трансмиссий силовых приводов, а также изношенные поверхности ствола вертлюга рекомендуется наращивать металлизацией, так как их изготовляют из сталей, чувствительных к перегреву.
Изношенные шпоночные пазы на валах восстанавливают несколькими способами. Если шпоночное соединение не должно фиксировать положение сопрягаемой детали относительно вала, то под некоторым углом к старому пазу размечают и фрезеруют новый паз по первоначальным размерам. Если шпоночное соединение строго фиксируется, то необходимо восстанавливать изношенный паз. Обычно наплавляют смятые кромки или шпоночный паз полностью, и фрезеруют новый паз на месте наплавки.
Вал с изношенной поверхностью или с наращенным слоем подвергают механической обработке для получения требуемой формы, размеров и шероховатости поверхности.
Установочными базами при механической обработке в большинстве случаев служат центровые отверстия и реже наружная цилиндрическая поверхность.
Наиболее сложно ремонтировать коленчатые валы. У большинства машин поршневого типа (насосы, компрессоры, двигатели внутреннего сгорания) это одна из наиболее ответственных и дорогостоящих деталей. Основными видами разрушения коленчатых валов являются износ рабочих поверхностей коренных и мотылевых шеек, а также изгиб вала и расхождение щек. Механическую обработку восстанавливаемых шеек коленчатых валов быстроходных двигателей осуществляют на специализированных шлифовальных станках. Коленчатые валы тихоходных двигателей, компрессоров, насосов с относительно большими габаритами обрабатывают, как правило, на токарных станках.
Одна из часто встречающихся операций при ремонте валов оборудования для бурения скважин и нефтегазодобычи - правка. В зависимости от диаметра и прогиба валы можно править в холодном и нагретом состояниях. Обычно длинные валы диаметром 10-100 мм при местном прогибе до 0,008 от длины вала правят в холодном состояний. При большей величине стрелы прогиба и больших диаметрах править валы рекомендуется с нагревом.
Ремонт деталей типа втулок
А) К деталям типа втулок относятся вкладыши подшипников, направляющие втулки, детали сальниковых уплотнений, гильзы цилиндров компрессоров, цилиндровые втулки насосов и др. Основные дефекты деталей этого типа - износ наружных, внутренних цилиндрических и торцовых поверхностей, износ резьб, задиры и риски на трущихся поверхностях, трещины.
При ремонте подобных деталей вначале устраняют трещины, а затем наращивают изношенные рабочие поверхности способами наплавки, металлизации, гальваническими и пластмассовыми покрытиями или заливкой антифрикционными сплавами. В отдельных случаях, например, при ремонте гильз двигателей внутреннего сгорания, цилиндровых втулок насосов и компрессоров применяют способ ремонтных размеров или дополнительных ремонтных деталей.
Б) Сменные цилиндровые втулки обычно применяют в машинах поршневого типа - компрессорах, насосах, двигателях внутреннего сгорания, скважинных штанговых насосах и др. Характерным дефектом этих деталей является износ внутренней рабочей поверхности, что приводит к увеличению зазора между трущимися поверхностями поршня и втулки и, следовательно, к нарушению плотности сопряжения. Несмотря на то, что цилиндровые втулки различных машин могут отличаться формой и размерами, процесс их ремонта аналогичен.
Цилиндровую втулку обычно ремонтируют способом ремонтных размеров. В зависимости от размера втулки выбирают станочное оборудование. Для малогабаритных втулок - гильз используют вертикальные расточные станки, а окончательную обработку выполняют на специальных хонинговальных станках. Крупногабаритные втулки обычно растачивают на горизонтальных расточных станках многорезцовыми головками, закрепленными на бортштанге. После расточки поверхность подвергают шлифованию и хонингованию.
При коррозионно-механическом разрушении наружных уплотнительных поясков или буртов рекомендуется перед растачиванием внутренней поверхности втулки предварительно нарастить пояски и бурты наплавкой. Следует иметь в виду, что
высокая температура при наплавке может вызвать коробление, а иногда и образование трещин. Поэтому лучше применять металлизацию или газовую наплавку с использованием медных электродов и в качестве флюса - буру. После наплавки уплотнительные бурты и пояски следует обточить на токарном станке и, приняв обточенные пояски за базовую поверхность, предварительно расточить, а затем прошлифовать отверстие на заданный ремонтный размер.
Ремонт деталей типа дисков
К этой группе ремонтируемых деталей оборудования для бурения скважин и нефтегазодобычи относятся зубчатые колеса редукторов и коробок скоростей, цепные колеса лебедок, шкивы и др.
Характерными дефектами этих деталей являются износ, задиры и риски на рабочих поверхностях, смятие шпоночных канавок, коробление или погнутость. Эти детали ремонтируют преимущественно способами механической обработки, в частности, способом ремонтных размеров или дополнительных ремонтных деталей.
Ремонт зубчатых колес.
Впроцессе работы зубчатых передач происходит износ зубьев и посадочного отверстия, смятие шпоночных пазов. В отдельных случаях на рабочих поверхностях цементированных зубьев можно наблюдать «шелушение» и выкрашивание цементированного слоя. При износе более 80 % толщины цементированного слоя зубчатые колеса заменяют новыми.
Процесс ремонта зубчатых колес в значительной степени определяется характером повреждения и размерами детали. Изношенное отверстие ступицы зубчатого колеса восстанавливают наплавкой, способом ремонтных размеров или дополнительных ремонтных деталей.
Изношенные поверхности зубьев ремонтируют наплавкой, способом дополнительных ремонтных деталей, давлением и др. Наплавку ведут электродами, специально подобранными по составу основного металла. После наплавки производят разметку и фрезерование зубьев.
При изломе или выкрошивании большого числа зубьев рекомендуется зубчатое колесо отжечь и обработать по наружной поверхности до полного удаления зубчатого вооружения. На оставшуюся часть зубчатого колеса следует установить по горячей посадке кольцо-венец, на котором нарезать новые зубья и затем их термически обработать.
Ремонт цепных колес.
Цепные передачи широко используются в буровых лебедках, цепных редукторах, роторных приводах и в других машинах для бурения скважин и нефтегазодобычи.
Основными дефектами цепных колес являются износ посадочной внутренней поверхности втулки из антифрикционного материала, запрессованной в ступицу колеса, изменение размеров профиля зубьев и диаметров впадин, смятие или разрушение кромок шпоночных канавок в ступице цепного колеса.
Изношенную антифрикционную втулку выпрессовывают из ступицы и вместо нее запрессовывают новую, имеющую припуск по внутреннему диаметру. Затем цепное колесо вместе с втулкой устанавливают на карусельный или токарный станок и растачивают втулку на заданный размер.
Цепные колеса, имеющие износ по профилю зуба и диаметру впадин, чаще всего ремонтируют способом замены части детали. Для этого на ремонтируемом колесе газовой горелкой срезают изношенные зубья и обтачивают колесо по наружной поверхности под горячую посадку. Отдельно изготовляют кольцо-венец, имеющий припуск на наружной поверхности.
Вотдельных случаях зубья восстанавливают электронаплавкой. Наплавленные зубья размечают и затем обрабатывают. При этом строго контролируют по шаблонам профиль зубьев и их шаг.
Ниже рассмотрены способы восстановления шпоночных пазов. При большем износе шпоночный паз ремонтируют наваркой грани (рис. 45, а) с последующим фрезерованием. При этом выдерживают размер паза, установленный стандартом. Возможен и такой ремонт: паз расширяют и углубляют, полностью устраняя следы износа, затем к нему изготовляют ступенчатую шпонку (рис. 45, б). Однако при таком ремонте не обеспечивается высококачественное соединение и поэтому его применяют в исключительных случаях (при осмотрах и текущих ремонтах). Поэтому когда на чертеже нет указаний о фиксированном положении шпоночного шпонки резьбовое отверстие и в него ввинчивают винт. Когда винт своим концом упрется в вал, его продолжают вращать, и тогда шпонка выходит из паза (рис. 45, г.).
При подгонке и сборке призматических шпонок в процессе ремонта рекомендуется выполнить специальный скос (рис. 45, в), а с обратной стороны сделать соответствующую пометку. Это позволит вынуть шпонку из паза и при помощи молотка с выколоткой, используя имеющийся у нее скос. Выколотку упирают в помеченный конец шпонки со стороны скоса (показано стрелкой) и слегка ударяют по ней молотком. С этой стороны конец шпонки прижимается к основанию паза, а с противоположной приподнимается. Шлицы небольших валиков обычно не ремонтируют, детали с изношенными шлицами большей частью заменяют новыми. Однако у деталей, трудоемких в изготовлении, шлицы часто подвергают ремонту. Его производят путем наварки металла с последующей механической обработкой в точном соответствии с размерами и расположением шлицев на соединяемой детали.
Шлицы вала можно ремонтировать путем раздачи зубьев, когда шлицевое соединение центрируется по внутреннему диаметру. Если шлицы закалены, необходимо сначала вал отжечь, после чего раздать каждый шлиц в продольном направлении, доведя ширину шлица до номинального размера с припуском 0,1—0,2 мм для последующей механической обработки.
Раздачу выполняют вручную или на прессах специальными инструментами — зубилами и чеканами. Для этого вдоль шлицев наносят по одной продольной риске, затем зубилом (рис. 46, в) вдоль рисок надрубают канавки (рис. 46, а), которые раздают
чеканом (рис. 46, б). Раздачу шлицев можно производить, используя токарные или строгальные станки. Для этого оправку с вращающимся конусным роликом закрепляют в резцедержателе станка, а вал устанавливают в центрах токарного станка или закрепляют на

столе строгального станка. Суппортом станка подводят ролик, вдавливают в тело зуба и осуществляют несколько проходов по одной канавке.
После раздачи канавки на шлицах заваривают электросваркой, вал дополнительно отжигают, рихтуют, а шлицы обрабатывают под номинальный размер и подвергают термообработке.
Шлицы в отверстиях (посадка по наружному диаметру) и с небольшим износом можно
также ремонтировать раздачей. Для этого применяют специальную прошивку, которую продавливают через шлицевое отверстие с помощью гидравлического пресса. После раздачи зубьев шлицевое отверстие калибруют шлицевой протяжкой, при этом снимают излишне выдавленный
металл и придают детали требуемый размер.
69. Выбор рационального способа восстановления деталей.
Пoследoвaтельнoсть выбoрa и рaсчет. Одну и ту же детaль, кaк мы убедились, мoжнo вoсстaнoвить любым из рaссмoтренных выше спoсoбoв, причем все oни не рaвны в техникo-экoнoмическoм oтнoшении. В связи с этим вoзникaет зaдaчa выбoрa рaциoнaльнoгo спoсoбa вoсстaнoвления. Решaть эту зaдaчу предлaгaется в следующем пoрядке.
1.Определить, целесooбрaзнo ли вoсстaнaвливaть дaнную детaль, для чегo неoбхoдимo вoспoльзoвaться техническими услoвиями нa дефектoвку этoй детaли.
2.Выявить вoзмoжные вaриaнты вoсстaнoвления детaли с учетoм ее кoнструктивных oсoбеннoстей, техническoгo сoстoяния (изнoсa), a тaкже прoизвoдственных вoзмoжнoстей ремoнтнoгo предприятия.
3.Определить стoимoсть вoсстaнoвления для кaждoгo из вaриaнтoв.
4.Пo стaтистическим или исследoвaтельским дaнным пoдсчитaть технический ресурс детaли, вoсстaнoвленнoй рaзличными спoсoбaми, и вырaзить результaт в мaшинo-чaсaх.
Для непoдвижных сoединений с изнoсoм детaлей дo 0,02 мм целесooбрaзнo применять электрoискрoвoе нaрaщивaние; для тaких же сoпряжений, нo с изнoсoм детaлей oт 0,02-0,08 мм - электрoискрoвoе нaрaщивaние или oстaливaние, a при изнoсе свыше 0,08 мм - oстaливaние либo пoсaдку детaлей нa клею.
Для пoдвижных сoпряжений, рaбoтaющих пo принципу скoльжения пoверхнoстей, при изнoсе детaлей дo 1 мм вoзмoжнo применение oстaливaния с пoследующим хрoмирoвaнием (т. е. oстaливaние в кaчестве пoдслoя) либo вибрoдугoвoй нaплaвки. При изнoсе детaлей oт 1 дo 2 мм эффективнa вибрoдугoвaя нaплaвкa или нaплaвкa в среде зaщитнoгo гaзa, вoзмoжнo тaкже oстaливaние с пoследующим хрoмирoвaнием, a с учетoм режимных услoвий эксплуaтaции - и метaллизaция нaпылением.
Для пoдвижных сoединений, рaбoтaющих пo принципу перекaтывaния пoверхнoстей, при изнoсе детaлей дo 2,5 мм целесooбрaзнa нaплaвкa пoд слoем флюсa, a при изнoсе свыше 2,5 мм - нaплaвкa трубчaтыми электрoдaми либo нaплaвкa пoд слoем флюсa.
Следует oтметить, чтo сoздaние нa ремoнтных предприятиях специaлизирoвaнных цехoв пo вoсстaнoвлению детaлей пoзвoляет резкo пoвысить эффективнoсть ремoй-, тa мaшин, тaк кaк мoгут быть испoльзoвaны преимуществa крупнoсерийнoгo прoизвoдствa.
При выборе способа восстановления необходимо учитывать конструктивные особенности детали, условия ее работы, величину и характер износа, материал и термическую обработку, размеры восстанавливаемой поверхности, технологические возможности ремонтного предприятия, надежность работы детали после восстановления, затраты на восстановление и т. д.
Рассматривая конкретную деталь, следует определить возможные способы восстановления изношенной поверхности. Например, при восстановлении поверхности валов с малыми величинами износа (до 0,3 мм) нецелесообразно применять автоматическую наплавку под слоем флюса, а следует использовать методы электроискрового наращивания, осталивания и т. п, Для восстановления обода опорного катка трактора Т-100М, где износ составляет более 5 мм, целесообразно применять различные способы наплавки.
Определив приемлемые способы ремонта, необходимо подробно разработать технологию восстановления детали и определить затраты на восстановление по каждому технологическому процессу.
Для того чтобы решить вопрос выбора способа восстановления, рационального для конкретной детали, необходимо найти числовое значение технико-экономического критерия. Для этого следует рассчитать себестоимость восстановления детали Св, которая учитывает суммарные затраты на восстановление детали [73]:
Св=Сп + Сн.п+См, (4) где Сп - затраты на подготовку детали к нанесению покрытий, руб; Сн.п - затраты на нанесение покрытий, руб.; См - затраты на механическую обработку детали, руб.
Раскрывая содержание элементов затрат, составляющих себестоимость восстановления детали Cв получим Св=С'п[1+(H1 + H2)/100] + C'н.п[1 + (H'1 +H'2)/100] + С'м[1 + (H1 + H2)/100]+М, (5)
где С'п, С'н.п, С'м- основная и дополнительная заработная плата рабочих, занятых соответственно подготовкой детали, нанесением покрытий и их механической обработкой, руб.; Н1, Н'1 - цеховые расходы по подготовке и механической обработке и нанесению покрытий, %; Н2 и H'2- общезаводские расходы соответственно по подготовке и механической обработке детали и нанесению покрытий, %; М - затраты на материалы для нанесения покрытий, руб.
70. Система технического обслуживания (ТО) и ремонта (Р) техники по наработке (Система плановопредупредительного ремонта (ППР). Основные положения. Термины и определения.
Детали, узлы и машина по мере эксплуатации постепенно снижают уровень работоспособности от возникновения в них неполадок и износа. Неполадки (загрязнения, нарушение надежности и плотности соединений и регулировки) устраняются техническим обслуживанием машин, а износ их - только ремонтом.
Основой правильной эксплуатации машин является плановое обеспечение их обслуживанием и ремонтом, исключающее или сводящее к минимуму возможность внезапных отказов.
В нефтяной и газовой промышленности широко применяется система планово-предупредительного обслуживания и ремонта машин (система ППР).
Система ППР - комплекс мероприятий по обслуживанию и ремонту машин, выполняемых профилактически по заранее составленному плану для поддержания машин в исправном и работоспособном состоянии. Система ППР предусматривает следующие основные положения:
1)ремонт оборудования выполняется через планируемые промежутки времени, называемые межремонтными периодами;
2)после планового капитального ремонта характеристика оборудования приближается к паспортным данным нового оборудования;
3)в течение ремонтного цикла оборудование в строгой очередности проходит все плановые ремонты, предусмотренные системой;
4)кроме плановых ремонтов выполняется техническое обслуживание оборудования;
5)чередование, периодичность и объем обслуживания и ремонтов определяются назначением, конструкцией и условиями эксплуатации оборудования.
Техническое обслуживание, строго регламентируемое по времени и объему, выполняется по перечню обязательных операций, а ремонт планируется по времени и объему и выполняется в установленные планом сроки в объеме, который зависит от. фактического состояния машины.
Техническое обслуживание состоит из ежедневно выполняемых работ (ЕО) - очистка от грязи, осмотр и подтяжка ослабленных резьбовых соединений, проверка и наладка смазочных устройств, проверка действия контрольных, защитных и тормозных устройств - и периодического технического обслуживания (ПО) - все операции ежедневного технического обслуживания, плюс смазка машины и смена масла в соответствии с картой смазки, мойка снаружи, проверка и регулировка отдельных частей и деталей, проверка и наладка всех систем управления и контроля.
Как видно из перечисленного. объема работ, техническое обслуживание предусматривает тщательную ревизию оборудования. Ремонтные работы в зависимости от объема и сложности делятся на три категории.
Текущий ремонт (ТР) ставит задачей поддерживать работоспособность отдельных частей в целом исправной машины. Объем и сложность операций ТР сравнительно невелики - проверка состояния оборудования, замена быстроизнашивающихся деталей, замена при необходимости смазки, устранение всех дефектов, не требующее разборки сложных частей оборудования. Оборудование после ремонтных работ проверяют и регулируют.
Средним ремонтом (СР) называют ремонт, при котором восстанавливается работоспособность важных частей машины, утраченная в результате естественного износа деталей. Этот ремонт связан с значительным объемом сборочно-разборочных работ на основных агрегатах машины. Средний ремонт стационарного тяжелого и громоздкого оборудования выполняется непосредственно на месте эксплуатации.
Капитальным (КР) называют .ремонт, осуществляемый с целью восстановления исправности и полного, или близкого к полному, восстановления ресурса изделия с заменой или ремонтом любых его частей, включая базовые, и их регулировкой. Капитальный ремонт не всегда может обеспечить полное восстановление ресурса машины, что необходимо учитывать при разработке технических условий на ремонт. Капитальный ремонт выполняется на ремонтных заводах или хорошо оснащенных крупных ремонтных базах.
В основе разработки системы ППР лежат следующие положения.
Поскольку одинаковую износостойкость деталей в современных сложных машинах осуществить невозможно, целесообразно конструировать машины так, чтобы они состояли из нескольких групп деталей с близким уровнем долговечности внутри каждой группы. Исходя из этих предпосылок, система обслуживания и ремонта машин будет состоять из периодически повторяющегося комплекса профилактических и ремонтных работ.
Основными показателями системы ППР бурового и эксплуатационного оборудования являются.
1. Ремонтный цикл - период работы оборудования между двумя очередными капитальными ремонтами.
2. Межремонтный период - время работы оборудования между двумя любыми очередными плановыми ремонтами.
3. Структура межремонтного цикла - количество и порядок чередования различных видов плановых ремонтов в пределах одного ремонтного цикла.
4. Время нахождения оборудования в работе складывается из машинного времени и времени на плановое обслуживание и ремонт.
5. Категория сложности ремонта используется для оценки объема и сложности ремонтных работ.