
otvety_PAHT
.pdf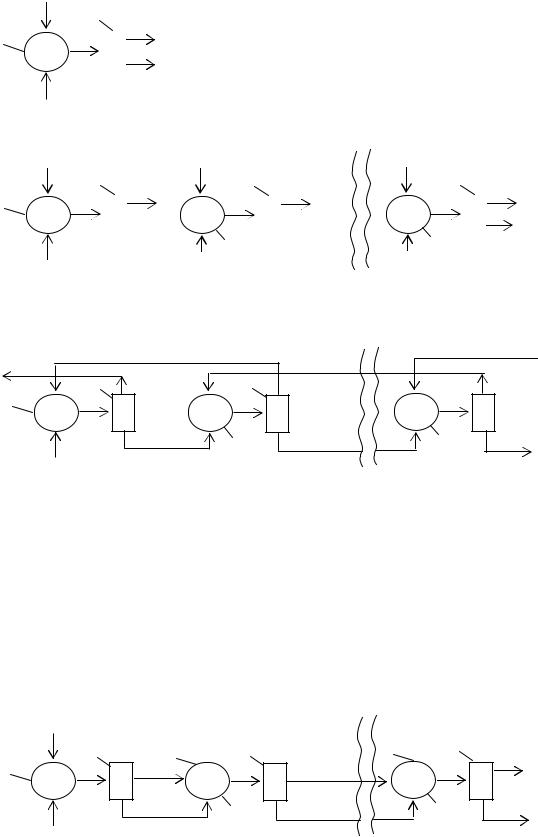
26. При проведении процесса разделения смесей жидкостной экстракцией наибольшую эффективность достигают:
а) однократная экстракция.
|
Р+В |
2 |
|
|
|
1 – смеситель |
|
|
|
|
|
|
|
|
|||||
|
|
|
Е |
2 - отстойник |
|
|
|
|
|
|
|
|
|||||||
1 |
|
|
|
|
|
|
|
|
|
|
|||||||||
|
|
|
|
Применяется на практике лишь когда коэффициент |
|||||||||||||||
|
Э |
|
|
|
R |
распределения в пользу экстрагента очень высок или |
|||||||||||||
|
|
|
|
||||||||||||||||
|
|
|
|
|
когда допустимы невысокие концентрации извлекаемого |
||||||||||||||
вещества в экстракте. |
|
|
|
|
|
|
|
|
|
|
|
|
|||||||
б) порционная экстракция. |
|
|
|
|
|
|
|
|
|
|
|
|
|||||||
|
|
|
|
|
|
|
|
|
|
|
|
|
|
|
|
|
|
|
|
|
Э1 |
2 |
|
|
Е1 |
Э2 |
2 |
|
|
|
Е2 |
|
Эn |
|
2 |
|
Еn |
||
1 |
|
|
|
|
|
|
|
|
|
|
|
|
|
|
|||||
|
|
|
|
|
|
|
|
|
|
|
|
|
|
|
|
|
|
||
|
Р+В |
|
|
|
R1 |
|
1 |
|
|
|
|
R2 |
|
|
1 |
|
|
Rn |
|
|
|
|
|
|
|
|
|
|
|
|
|
|
|||||||
|
|
|
|
|
|
|
|
|
|
|
|
|
|
|
|||||
|
|
|
|
|
|
|
|
|
|
|
|
|
|
|
|
||||
|
|
|
|
|
|
|
|
|
|
|
|
|
|
|
|
|
Схема позволяет из исходного раствора получить весьма чистый разбавитель. Применяется, когда необходимо получать достаточно чистый разбавитель с помощью дешевого экстрагента, не требующего регенерации.
в) противоточная непрерывная экстракция.
|
|
Ек |
2 |
Е2 |
Эn |
Еn |
1 |
2 |
|
|
|||
|
|
|
|
|
|
|
|
Р+В |
R1 |
1 |
R2 |
1 |
Rn |
|
|
Наибольшей эффективностью в аспекте полноты разделения обладает схема противоточной экстракции. Эта схема чаще всего применяется в многотоннажной промышленности. В таком процессе наиболее обедненная переходящим (экстрагируемым) компонентом фаза рафината на выходе из установки встречается со свежим экстрагентом, а наиболее богатая этим компонентом фаза экстракта на выходе контактирует с концентрированным исходным раствором. Благодаря этому достигается: - наиболее высокая средняя движущая сила процесса -максимальная степень разделения при заданном расходе экстрагента -наименьший расход экстрагента при заданной степени разделения.
в) прямоточная непрерывная экстракция.
Э1 |
2 |
1 |
2 |
1 |
|
2 |
Еn |
|
|
||||||
1 |
|
Е1 |
|
Е2 |
|
|
|
Р+В |
|
R1 |
1 |
R2 |
1 |
|
Rn |
|
|
|
В таком процессе движущая сила с каждой ступенью уменьшается и поэтому процесс не очень эффективен.
21

27. В чем состоят преимущества проведения процесса выпаривания в прямоточной многокорпусной выпарной установке по сравнению с использованием однокорпусной установки? Составьте тепловой баланс для однокорпусной выпарной установки.
Ответ: экономии свежего греющего пара Преимущества использования прямоточной многокорпусной
выпарной установки по сравнению с однокорпусной установкой таковы: 1) С энергетической точки зрения удаётся использовать теплоту вторичного пара, полученного в предыдущем корпусе для обогрева следующего (благодаря уменьшению температуры кипения упариваемого раствора от корпуса к корпусу).
Тепловой баланс:
Задача теплового расчёта процесса выпаривания сводится к определению необходимого теплового потока Q, расхода теплоносителя Dгр, а также требуемой поверхности теплообмена F. Для стационарного режима работы выпарной установки тепловой баланс запишется следующим образом: Q+Socoto-Wi-S1c1t1=0. Отсюда имеем:
Q=Soco(t1-t0)=W(i-cpt1). Таким образом, необходимый тепловой поток расходуется на нагрев So кг/с исходного раствора от to до t1 и на последующее испарение растворителя W кг/с при температуре t1. П рассчитанному тепловому потоку Q найдём расход греющего пара Dгр :
Dгрh-Q-DгрскT=0, т.е. Dгр |
Q |
|
Q . Значит площадь поверхности |
|
h c T |
||||
|
|
r |
||
|
к |
|
|
теплообмена F равна: F kQt . Потери тепла в окружающую среду Qо при
определении расхода греющего пара: Dгр Q Qo . Однако при расчёте
rгр
площади теплообмена F труб нагревательной камеры учитывается лишь тепловой поток на процесс выпаривания Q.
22
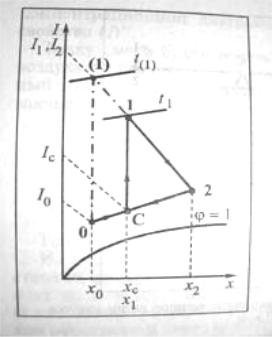
28. В чем преимущества проведения процесса сушки с частичной рециркуляцией сушильного агента по сравнению с процессом без рециркуляции? Представьте проведение этого процесса в I – d диаграмме.
Ответ: понижение температуры суш. Агента на входе в суш.камеру Частичная рециркуляция отработанного
сушильного агента позволяет снизить скорость сушки. Таким образом, СА на входе в сушильную камеру имеет более высокую влажность и более низкую температуру. Следовательно, процесс сушки проходит в более мягких условиях и требует более длительного времени (из-за понижения движущей силы процесса). С помощью частичной рециркуляции отработанного СА при высушивании термолабильных материалов можно избежать трудностей, указанных выше. Процесс идеальной сушки с частичной рециркуляцией отработанного СА в I-d диаграмме выглядит следующим образом:
23
29. Привести схему и принцип работы простого регенеративного цикла высокого давления (цикл Линде). Каким образом нужно изменять параметры воздуха (температуру, давление) в циклах глубокого охлаждения пред конечным дросселированием воздуху до жидкого состояния с целью увеличения удельной холодопроизводительности цикла (хр)?
Ответ: Понижать температуру воздуха перед дросселированием Это – наиболее простой из циклов, использующих только дросселирование.
Исходный воздух изотермически сжимается от давления р1 до р2 в компрессионном агрегате К и охлаждается в холодообменнике Х при постоянном давлении р2 (за счет обратного потока холодного воздуха). Затем сжатый воздух дросселируется в вентиле Др до давления р1. Полученная парожидкостная смесь поступает в сепаратор С, откуда жидкость (сжиженный газ) отводится от системы в количестве х, а газ в количестве (1-х) возвращается в холодообменник Х, забирая теплоту у потока сжатого газа, идущего на дросселирование.
Заметим: давление р1, как правило атмосферное: свежий воздух забирается из атмосферы; жидкий воздух храниться и транспортируется в сосудах Дьюара, где зона хранения соединена с атмосферой.
В связи с р1 =1 бар может возникнуть вопрос: зачем долю (1-х) возвращать в цикл, не проще ли направлять на сжатие в компрессор весь воздух (1 кг) из атмосферы, а не небольшую долю х? Дело в том. что воздух в циклах глубокого охлаждения проходит специальную подготовку (очистку от воды, диоксида углерода и др. примесей) Очистка воздушного потока Gx дешевле, чем полного потока G. Поэтому поток воздуха G(1-x), ранее уже прошедшего очистку, возвращают в цикл. В диаграмме Т-s (рис.21.16,б) стадии процесса изображены следующим образом:
1-2 – изотермическое (Т1=Т2=const) сжатие 1 кг воздуха;
2-3 – изобарическое (р2= const) охлаждение в холодообменнике; 3-4 – дросселирование (h=const);
4-0 и 4-5 - изобарическая (р1= const) сепарация (с выводом потока х жидкого воздуха);
5-1 – изобарическое (р1= const) нагревание потока (1-х) воздуха (с присоединением потока х свежего воздуха и направлением 1 кг смеси на сжатие в компрессор).
Далее стадии повторяются.
24
30. Назначение, принцип действия и схема работы щековой дробилки.
Ответ: крупного дробления
Щековые дробилки относятся (ЩД) к размольным машинам с преобладанием измельчения способами размалывания, раскалывания и раздавливания. Чаще всего ЩД используются при крупном и среднем дроблении.
Основными рабочими органами ЩД являются смонтированные на станине 1 стальная или чугунная неподвижная щека 2 и подвижная щека 4, защищенные плитами, изготовленными из очень прочного (износоустойчивого) материала. С торцов пасть закрыта гладкими плитами 3. ЩД работает циклично – в 2 стадии: измельчение ТМ; загрузка-выгрузка ТМ. На стадии измельчения подвижная щека перемещается влево, плиты сближаются, и происходит разрушение ТМ. На стадии загрузки-выгрузки подвижная щека перемещается вправо; при этом измельченный материал выгружается из ЩД через нижнее сечение пасти (шпальт), и одновременно
врабочий объем через верхнее сечение (зев) подается свежая порция исходного ТМ. Возвратнопоступательное перемещение щеки около оси 5 обеспечивается подъемно-опускным движением шатуна 8, сидящего на эксцентриковом валу 7, и распоротыми плитами 9, шарнирно соединяющими шатун с подвижной щекой (левая плита 9) и клиньями 12 (правая плита 9). При подъеме шатуна подъемные плиты располагаются почти в одну линию, так что подвижная щека идет влево (измельчение ТМ в пасти). При опускании шатуна распорные плиты располагаются
вломаную линию так, что подвижная щека идет вправо (разгрузка ТМ через шпальт и загрузка свежих его порций через зев). На стадии загрузки-выгрузки под действием собственного веса ТМ в рабочей зоне подвижная щека весьма медленно перемещается вправо; чтобы частота этого перемещения соответствовала режиму ЩД, пересмотрен принудительный возврат подвижной щеки в крайнее правое положение с помощью тяг 10 и пружин 11.
Для восприятия значительных инерционных усилий на эксцентриковом валу 7 устанавливается массивное моховое колесо 6.
Конечный размер куска измельченного ТМ регулируется шириной щели (нижнего сечения) шпальта за счет фиксации клиньев 12 в определенном положении.
При работе ЩД возможно случайное попадание в рабочий объем (в пасть) очень прочного куска какого-либо постороннего ТМ. Чтобы избежать поломки дорогостоящих узлов и деталей ЩД, на этот случай предусмотрена преднамеренная поломка какой-нибудь дешевой и легко заменяемой детали, чаще всего – специально ослабленной правой распорной плиты 9: она выполняет роль «предохранительного клапана» - при поломке его легко заменить на новую.
Достоинства: простота, надежность, легкость обслуживания, относительная компактность. Недостатки: периодичность цикла работ, следовательно, неравномерность нагрузки на рабочий орган в процессе измельчения, поломки, необходимость замены распорной плиты, шум
25