
Сварка. Оконч
.pdfКонтроль оборудования
Оборудование должно быть в исправном состоянии и выдавать паспортные данные. Для дуговой сварки обеспечивать устойчивое горение дуги, правильность регулировки режима сварки. При газовой сварке — подачу чистого и сухого газа, при постоянном давлении.
Контроль квалификации сварщиков
Для проверки квалификации сварщиков администрация организует квалификационную комиссию. Испытания проводят по теории и практике сварочных работ и должны включать сварку образца соответствующего изделия в реальных условиях. После чего образцы проверяют всеми методами неразрушающего контроля и подвергают механическим испытаниям.
Контроль технологи
При этом контроле проверяют подготовку заготовок, исправность сварочных приспособлений, сборку узлов под сварку, состояние сварочных материалов, сварочного оборудования, соблюдение установленных режимов сварки. У свариваемых заготовок проверяют форму, размеры геометрию разделки кромок, отсутствие загрязнений, ржавчины и влаги.
Текущий контроль сварных соединений
В процессии сварки проверяют внешний вид шва, геометрические размеры, проводят обмер изделия, следят за исправностью сварочной аппаратуры, за выполнением технологического процесса.
Лабораторная работа № 4 ОПРЕДЕЛЕНИЕ ВЕЛИЧИНЫ ФИКТИВНОЙ УСАДОЧНОЙ СИЛЫ И
ПРОГИБА ПРИ НАПЛАВКЕ ВАЛИКОВОГО ШВА НА ПРОДОЛЬНУЮ КРОМКУ СТАЛЬНОЙ ПОЛОСЫ
Цель работы: Изучение остаточных деформаций, возникающих при электрической дуговой сварке плавлением. Экспериментальное определение прогиба полосы после наплавки валика сварного шва, определение фиктивной продольной усадочной силы.
Под воздействием сварочной дуги, вследствие неравномерного нагрева металла и фазовых превращений в зоне термического влияния происходят упругие и пластические деформации.
В любом сварном соединении имеется так называемая зона продольных пластических деформаций площадью Fпл , в которой во время нагрева при свар-
ке возникают пластические деформации металла в направлении движения источника тепла. После окончания сварки и полного остывания металла в соединении появляются остаточные пластические деформации пл. ост. , распреде-
ление которых по ширине зоны пластических деформаций неравномерно.
В рассматриваемой зоне металл стремится укоротиться в направлении
оси ОХ на величину пл. ост. (Рис. 1), но этому мешают соседние прилегающие зоны. По этой причине в зоне пластических деформаций возникают оста-
точные напряжения растяжения, а в примыкающих зонах уравновешивающие
61
их напряжения сжатия. Ширина зоны растягивающих напряжений 2bр несколько меньше ширины зоны пластических деформаций 2bп. Остаточные пластические деформации пл. ост. , вызывают продольную усадку сварного изделия.
В практических расчетах для наглядности действия продольных остаточных пластических деформаций их заменяют действием фиктивной усадочной
силы Pус . Эту силу получают интегрированием эпюры напряжений в зоне пла-
стических остаточных деформаций (Рис. 1, б). В нашем случае формула усадочной силы получает вид:
Pус |
bп |
пл.ост. E dy. |
(1) |
|
|||
|
bп |
|
|
где — толщина свариваемых пластин, м; y — координаты рассматриваемой точки, м;
Усадочная сила Pусвызывает продольное укорочение сваренных деталей,
а если сварной шов наложен не по центру тяжести сечения, то ещё и изгибающий момент, величина которого равна:
M ус Pус e. |
(2) |
По величине изгибающего момента можно определить прогиб детали, вызванный сваркой:
f |
M ус z2 |
. |
(3) |
||
8 |
E I |
||||
|
|
|
Используя закон Гука, по величине усадочной силы можно вычислить продольное укорочение детали по ее нейтральной оси:
|
|
Pус z |
. |
(4) |
|
||||
пр |
|
E F |
|
В приведённых формулах приняты следующие обозначения: Pус — усадочная сила, Н;
E — модуль продольной упругости, для стали — 2·1011 Н/м2;
e — расстояние от линии действия силы Pус до оси изгибающего элемента (эксцентриситет приложения силы Pус), м;
Z1 — участок полосы, на котором измеряется усадка — 0,1 м; z 2 — длина изгибающего элемента, 0,41 м;
F — площадь поперечного сечения детали, м2;
I b12h3 — момент инерции площади сечения детали относительно оси
у–у, м4.
Использовать формулы (1) и (2) для определения усадочной силы Pус в
технологических и прочностных расчётах не всегда удаётся. Усадочную силу проще вычислять через величину эффективной мощности сварочного источни-
ка тепла q кал/сек и скорости сварки vc , см/сек.
62
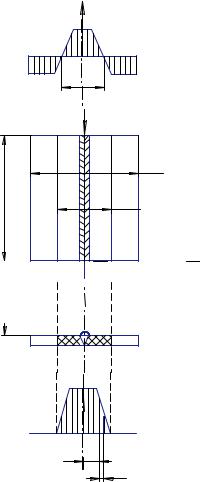
При однопроходной сварке малоуглеродистых и низколегированных ста-
лей для вычисления Pус используют формулу: |
|
|||
P |
(4 7) |
q |
, Н. |
(5) |
|
||||
ус |
vc |
|
|
|
|
|
|
|
x
x
а)
Z
2bp |
Pус |
2b
2bn
Y
Pус
пл.ост.
- bn y +bn
dy
б)
Рис. 1. Соединение стальных полос сварным швом
а) Эпюра остаточных напряжений в поперечном сечении образца; б) Эпюра остаточных пластических деформаций в том же сечении.
63
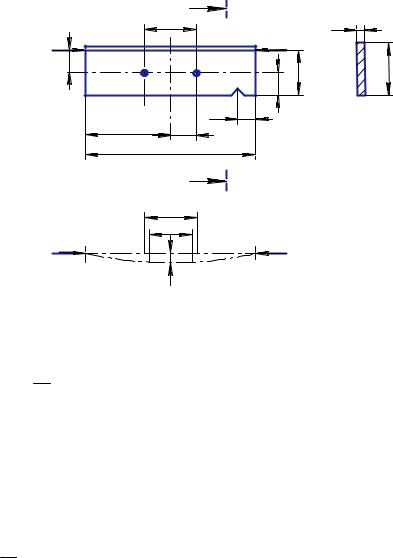
|
|
A |
A-A |
|
z= 100 |
|
|
Pус |
P |
b |
|
|
|
||
|
ус |
|
|
e |
|
|
|
|
|
60 |
h |
|
|
30 |
|
|
|
45 |
|
250 |
50 |
|
|
|
L= 500 |
|
|
|
z |
A |
|
P |
|
|
|
z1 |
Pус |
|
|
ус |
|
||
|
f |
|
|
Рис. 2. Лабораторный образец для определения сварочных деформаций
Величина коэффициента в формуле зависит от величины удельной по-
точной энергии q . vc
При |
q |
|
2 |
|
|
q |
2 |
|
|
= 1000 |
кал/см |
он близок к 7, при |
|
|
|
= 7000 кал/см он ра- |
|
v |
v |
|
|
|||||
|
c |
|
|
|
c |
|
|
|
q |
2 |
вен 4, при значениях |
|
= 1000–7000 кал/см коэффициент определяют ли- |
v |
||
|
c |
|
нейной интерполяцией.
Если q определить затруднительно, можно приближенно это значение vc
оценить по формуле:
q |
Qv Fнапл, |
(6) |
|
||
vc |
|
где Fнапл — площадь поперечного сечения наплавленного металла шва за
один проход, см2;
Qv — коэффициент, зависящий от способа сварки, кал/см3, принимают равным:
–при ручной дуговой сварке равным 10000–12000;
–при автоматической и полуавтоматической сварке в среде газа 9000;
–при автоматической и полуавтоматической сварке под флюсом 15000–
16000.
64
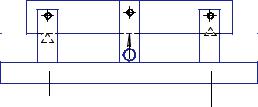
____Z2 = 410 ____
Рис. 3. Схема установки для измерения сварочных деформаций в лабораторных условиях
Порядок выполнения работы
Получить пластину длиной L = 500 мм, высотой h = 40–60 мм, толщиной b = 3–5 мм и измерить базу z — длину изгибающего элемента (примерно 100 мм) с двух сторон пластины (Рис. 2). Измерения произвести не менее трёх раз. Результаты измерения записать в таблицу 1.
|
|
Результаты испытаний |
Таблица 1 |
|||
|
|
|
|
|||
№ базы |
Начальные |
Среднее |
Замеры по- |
Средние |
Укорочение |
|
|
замеры z 1, |
значе- |
сле сварки |
значения |
базы |
|
|
мм |
ние zср , |
z1, мм |
z1ср, мм |
zср– z1ср, мм |
|
|
|
мм |
|
|
|
|
1 |
|
|
|
|
|
|
2 |
|
|
|
|
|
|
3 |
|
|
|
|
|
|
Установить полосу на призму в специальное приспособление, таким образом, чтобы надрез на полосе попал на острие правой призмы приспособления. Убедившись, что полоса плотно касается опорных призм, закрепить её двумя винтами (Рис. 3). Установить индикатор в среднее положение. Снять показания
индикатора (с1).
Снять полосу и проварить её кромку.
После полного остывания полосы произвести повторное измерение базы с двух сторон и результаты занести в таблицу. При выполнении измерений полосу необходимо прижать к стальной плите грузом или струбцинами.
Обработать полученные результаты измерений в табл. 1, т. е. выписать значение продольной деформации пр и по формуле (4) определить усадочную силу
Pус. В данном случае величину z надо брать равной базе измерений ( z = мм).
Установить полосу в приспособлении (Рис. 3) и произвести измерение прогиба полосы f на длине 410 мм после сварки, используя показания индика-
тора (с2)
f c2 c1.
65

Вычислить изгибающий момент усадочной силы, пользуясь формулой (3) при z2 = 410 мм.
Зная момент M ус и величину усадочной силы Pус, вычислите эксцен-
триситет приложения усадочной силы, используя формулу:
е M ус . Рус
Содержание отчёта
Описать причины возникновения сварочных напряжений и деформаций в стальной полосе.
Нарисовать эпюры остаточных напряжений и деформаций в поперечном сечении образца.
Привести основные формулы для расчёта усадочной силы, изгибающего момента с пояснениями.
Привести схему лабораторной установки для измерения сварочных деформаций и лабораторный образец с размерами.
Результаты испытаний с необходимыми расчётами. Проверка величины
P |
по величине удельной поточной энергии |
q |
. При этом необходимо учиты- |
|||||||
ус |
|
|
vc |
|
|
|
|
|
|
|
|
|
|
|
|
|
|
|
|
||
вать следующие соотношения размерностей: |
|
Дж |
|
кал |
; |
|
Дж |
10Н . |
||
|
|
|
4,1 |
|
|
|
||||
|
|
|
см |
|
см |
|
|
см |
|
Контрольные вопросы
1.Почему после сварки возникает усадочная сила?
2.Объясните причину появления изгиба полосы?
3.Как определить напряжения в пластине от сварки?
4.Каким способом можно уменьшить усадочные деформации?
Лабораторная работа № 5 ПОЛУАВТОМАТИЧЕСКАЯ СВАРКА В ЗАЩИТНЫХ ГАЗАХ
Сущность способа
Полуавтоматическая сварка плавящимся электродом отличается от ручной дуговой сварки тем, что механизируется подача электродной проволоки в сварочную зону, а остальные операции процесса сварки выполняются сварщиком вручную. Современная промышленность выпускает целую серию сварочных полуавтоматов, при помощи которых выполняют дуговую сварку в среде защитных газов. Их разрабатывают с использованием унифицированных узлов, что позволяет с наименьшими затратами выполнить наладку на сварку требуемых изделий. К таким унифицированным узлам относятся прижимные и направляющие устройства, подающие механизмы, узлы, осуществляющие подъем и перемещение, а также механизмы автоматической подачи присадочной проволоки. Полуавтоматы могут быть нескольких видов:
66

Рис 1. Схема и классификация полуавтоматической сварки
–для сварки сплошной стальной проволокой;
–для сварки сплошной алюминиевой проволокой;
–для сварки сплошной стальной и алюминиевой проволоками;
–для сварки сплошной стальной или алюминиевой порошковой проволо-
ками.
67
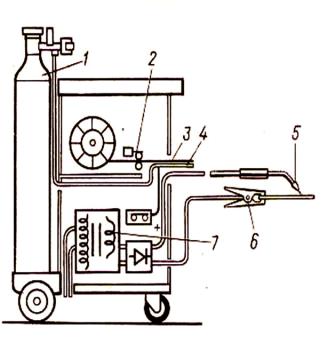
Кроме того, полуавтоматы могут различаться: по способу охлаждения горелки, регулировкой скорости подачи проволоки и методикой ее подачи, по конструктивным особенностям. При помощи этого универсального оборудования обеспечивается сварка практически всех труднодоступных мест с высоким качеством защиты сварочной ванны и дуги. Поэтому до 70 % сварочных работ выполняется полуавтоматами. Различают полуавтоматы по маркировке. Первые две буквы в маркировке обозначают тип оборудования и способ сварки: «ПШ» — полуавтомат шланговый, «УД» — установка для дуговой сварки. При помощи третьей буквы в маркировке указывают на способ защиты сварочной дуги: «Г» — газовая, «Ф» — флюсовая. Первая цифра, проставленная после буквенного индекса, указывает величину сварочного тока (в сотнях ампер), а последующие цифры обозначают конкретную модификацию изделия. И наконец, буквенный символ, проставленный после цифрового, обозначает климатическое исполнение полуавтомата: «У» — для эксплуатации в районах с умеренным климатом; «ХЛ» — в районах с холодным климатом; «Т» — тропическое исполнение.
Принципиальная схема полуавтоматической устаки представлена на Рис. 2.
Рис. 2. Принципиальная схема полуавтомата
1 — баллон с углекислотой; 2 — механизм подачи проволоки; 3 — проволока; 4 — трубопровод подачи газа; 5 — горелка; б — заземление; 7 — трансформатор с
блоком выпрямления
Как правило, в комплект установки входят: выпрямитель — источник питания сварочной дуги; подающее устройство, предназначенное для подачи электродной проволоки в зону сварки; газовый клапан, предназначенный для снижения давления защитного газа, находящегося в специальном баллоне, сменная горелка.
68
Подающее устройство сварочной проволоки может быть толкающего, тянущего и универсального типа. Как правило, оно состоит из следующих основных узлов: электродвигателя, планетарной головки, блока управления, катушки с проволокой, электропневматического газового клапана.
Заслуживают внимания новые безредукторные конструкции подающих механизмов серии «Интермигмаг» с пульсирующей подачей проволоки, являющиеся модификацией известного механизма «Изаплан». Состоит такой механизм из планетарной головки, корпус которой закреплен на полом валу электродвигателя постоянного тока. Укрепленные на ползунах подающие ролики прижимаются к сварочной проволоке и обкатываются вокруг нее при вращении якоря двигателя. Так как оси роликов расположены под углом 30–40° к оси проволоки, это усилие разлагается на две составляющие — закручивающее и осевое. Осевое усилие обеспечивает подачу проволоки, закручивающее — её движение по шлангу. Скорость подачи проволоки регулируется изменением частоты вращения ротора двигателя постоянного тока.
При помощи подающего устройства обеспечивается последовательность включения исполнительных органов сварочного полуавтомата, необходимая скорость подачи сварочной проволоки, выбор рабочего режима сварки и т. д. Стабилизация выходных параметров источника питания совместно со стабилизацией скорости подачи электродной проволоки позволяет получить сварные соединения высокого качества.
Горелка является одним из важных узлов сварочного полуавтомата. Она предназначена для направления в зону сварочной дуги электродной проволоки, защитного газа или флюса. С помощью горелки возбуждается сварочная дуга, осуществляется формирование и направление струи защитного газа. Конструкции сварочных горелок унифицированы в соответствии с технологическими требованиями. Рукоятка горелки должна быть прочной и удобной в работе, поэтому ее изготавливают в форме, позволяющей обхват рукой сварщика. Для управления сварочным процессом и защиты руки сварщика от ожогов на рукоятке устанавливается предохранительный щиток и пусковая кнопка.
Токоведущая направляющая трубка соединяет токопровод с токо-
съёмным наконечником. Конструкция трубки определяется сечением токоведущей части и необходимостью подвода защитного газа. По своему конструктивному исполнению направляющие трубки должны соответствовать требованиям гибкости и достаточной проводимости. Поэтому токопроводы изготавливают из мягкого провода, заключенного в изоляционную оболочку, внутренний диаметр которой выбран таким образом, чтобы по ней можно было пропускать защитный газ или охлаждающую воду. Направляющие каналы токопровода служат для подачи электродной проволоки к сварочной горелке. Они представляют собой металлическую спираль, на которую надета стальная стягивающая оплетка и изоляционная трубка. Спираль может быть одноили двухзаходной.
Наиболее ответственными частями горелки является сопло, и токопроводящий наконечник. Эти детали горелки работает в условиях высокой температуры и механического воздействия подающейся сварочной проволоки.
Сопло ограничивает зону защитного газа и обеспечивает вылет проволоки.
69
Наконечник быстро изнашивается и требует замены. Для снижения изнашиваемости наконечника его хромируют, полируют или изготавливают из твердых составов на медно-вольфрамовой основе. При больших сварочных токах, достигающих более 315 А, применяют принудительное охлаждение наконечника.
Применяют два типа наконечников: с поджимным контактом и без поджимного контакта. Поджимной контакт применяется при сварке тонкими электродными проволоками диаметром 0,8–1,2 мм.
Для сварки в стесненных условиях используют сменные горелки различной длины. Технические характеристики унифицированных горелок типа ГДПГ для механизированной сварки плавящимся электродом приведены в табл. 1.
|
|
|
|
|
Таблица 1 |
|
Технические характеристики унифицированных горелок |
||||||
Тип горел- |
Номиналь- |
ø электрод- |
Длина |
Габариты |
Масса (без |
|
ный свароч- |
ной про- |
рукава, |
горелки, |
рукавов), |
||
ки |
ный ток, |
волоки, |
||||
м |
мм |
кг |
||||
|
А |
мм |
||||
|
|
|
|
|||
|
|
|
|
|
|
|
ДПГ–101– |
160 |
0,8–1,2 |
2 |
|
|
|
8УЗ |
|
|
||||
|
|
|
|
|
||
|
|
|
|
|
|
|
ГДПГ–101– |
160 |
0,8–1,2 |
1 |
|
0,45 |
|
9УЗ |
|
|||||
|
|
|
254×60×113 |
|
||
|
|
|
|
|
||
ГДПГ–Ю1– |
160 |
0,8–1,2 |
2 |
|
||
|
|
|||||
10УЗ |
|
|
||||
|
|
|
|
|
||
|
|
|
|
|
|
|
ГДПГ–102– |
160 |
1,2–1,6 |
2 |
|
|
|
УЗ |
|
|
||||
|
|
|
|
|
||
|
|
|
|
|
|
|
ГДПГ–301– |
315 |
1,2–1,4 |
3 |
|
|
|
6У4 |
|
|
||||
|
|
|
|
0,6 |
||
|
|
|
|
|
||
ГДПГ–301– |
315 |
0,8–1,4 |
1 |
|
||
|
|
|||||
7У4 |
|
|
||||
|
|
|
266×50×125 |
|
||
|
|
|
|
|
||
ГДПГ–301– |
315 |
1,2–1,4 |
3 |
|
||
|
|
|||||
8У4 |
|
|
||||
|
|
|
|
|
||
|
|
|
|
|
|
|
ГДПГ–302– |
315 |
1,6–2,0 |
2 |
|
|
|
У4 |
|
|
||||
|
|
|
|
|
||
|
|
|
|
|
|
|
ГДПГ–501– |
500 |
1,6–2,0 |
3 |
|
0,7 |
|
4У4 |
|
|||||
|
|
|
268×90×125 |
|
||
|
|
|
|
|
||
ГДПГ–603– |
630 |
1,6–2,5 |
3 |
|
||
|
|
|||||
У4 |
|
|
||||
|
|
|
|
|
||
|
|
|
|
|
|
|
|
|
70 |
|
|
|