
- •МАТЕРИАЛОВЕДЕНИЕ
- •Оглавление
- •Общие организационно-методические указания
- •Лабораторная работа № 2 Изучение изломов (фрактография)
- •Лабораторная работа № 3 Изучение устройства металлографического микроскопа
- •Лабораторная работа № 5 Определение твердости металлов и сплавов
- •Лабораторная работа № 7 Определение величины зерна в стали
- •Лабораторная работа № 10 Пластическая деформация и рекристаллизация металлов
- •Лабораторная работа № 13 Зона термического влияния в сварных соединениях
- •Лабораторная работа № 14 Изучение структуры и свойств легированных сталей
- •Лабораторная работа № 15 Микроанализ цветных металлов и их сплавов
- •Лабораторная работа № 16 Микроанализ подшипниковых сплавов
- •Лабораторная работа № 17 Изучение структуры и свойств клеевых соединений
- •Лабораторная работа № 19 Изучения макроструктуры и микроструктуры полимеров
- •Лабораторная работа № 20 Газонаполненные пластмассы
- •Список рекомендуемой литературы
КАЛИНИНГРАДСКИЙ ГОСУДАРСТВЕННЫЙ ТЕХНИЧЕСКИЙ УНИВЕРСИТЕТ
МАТЕРИАЛОВЕДЕНИЕ
Методические указания по выполнению лабораторных работ для студентов высших учебных заведений всех технических специальностей
Калининград 1999
УДК 691:669.017(075)
УТВЕРЖДЕНО Ректором Калининградского
государственного технического университета
АВТОРЫ – Громыко А.Г., к.т.н., доцент кафедры технологии обработки материалов Калининградского государственного технического университета (лабораторные работы №9,11,13,15,16) Калачева М.С., старший преподаватель той же кафедры
(лабораторные работы №7,10,14,17,18,19,20)
ЕвсинаЕ.Н., старший преподаватель той же кафедры (лабораторные работы №1,2,3,4,5,6) ТарасовА.Н.,к.т.н.,доцент той же кафедры (лабораторные работы №8,12,21)
Методические указания рассмотрены и одобрены на заседании кафедры технологии обработки материалов Калининградского государственного технического университета 13 ноября 1996 г., протокол №3
РЕЦЕНЗЕНТ - кафедра технологии обработки материалов Калининградского государственного университета
© Калининградский государственный технический универси-
тет, 1999г.
2
ОБЩИЕ ОРГАНИЗАЦИОННО-МЕТОДИЧЕСКИЕ УКАЗАНИЯ
Настоящие методические указания содержат перечень, описаниеи методику выполнения лабораторных работ, рекомендуемых к выполнению при изучении курса "Материаловедение" для студентов (бакалавров) высших учебных заведения всех технических специальностей и направлений.
Лабораторные занятия по курсу "Материаловедение" строятся и планируются таким образом, чтобы студент имел определенную возможность закрепить и углубить теоретические знания, полученные на лекциях и приобрести навыки самостоятельного выполнения экспериментальных работ.
Глубокое знание свойств различных материалов позволяет правильно выбрать необходимый материал с учетом его качественных показателей, конкретных условий применения и стоимости.
Внеаудиторная подготовка студентов к лабораторным работам обязательна. Подготовленность студента проверяется по контрольным вопросам, в случае недостаточной подготовленности по теоретическим основам темы студент к лабораторной работе не допускается.
Перед началом работы студент знакомится с правилами по технике безопасности, условиями пользования приборами и оборудования, а затем под контролем преподавателя и лаборанта выполняет лабораторную работу.
Объем и выбор лабораторной работы определяется преподавателем в зависимости от специализации студента и объемом часов, планируемых учебным планом.
По окончании лабораторной работы студент оформляет отчет, используя методические указания (содержание отчета). Отчеты оформляются в отдельной тетради.
Необходимые в отчете рисунки следует выполнять аккуратно карандашом. Рисунки следует сопровождать номерами, поясняющей надписью, позициями и их наименованиями.
Отчет по лабораторной работе представляется к защите и защищается на следующем лабораторном занятии.
3
ЛАБОРАТОРНАЯ РАБОТА № 1 МАКРОСКОПИЧЕСКИЙМЕТОДИССЛЕДОВАНИЯМЕТАЛЛОВИСПЛАВОВ
I. ЦЕПЬ РАБОТЫ: ознакомить с методикой приготовлении макрошлифов; рассмотреть строение материала в приготовленных образцах, выявить характер макроструктуры и дефектов.
II. КРАТКИЕ ТЕОРЕТИЧЕСКИЕ СВЕДЕНИЯ 2.1. Цели и задачи макроскопического анализа
Макроструктура – это структура (строение) материала, видимое невооруженным глазом или при небольшом увеличении (до 30 раз) с помощью лупы или специального микроскопа. Макроструктура рассматривается на специально подготовленных образцах - макрошлифах. К анализу макроструктуры прибегают при проведении многих исследований и контроле готовой продукции. Существуют три основных способа изучения макроструктуры:
1.Просмотр хорошо отшлифованной и протравленной контролируемой поверхности готового металлического изделия. В этом случае изделие не разрушается и после контроля идет в эксплуатацию.
2.Просмотр специально приготовленных макрошлифов.
3.Изучение излома образца.
Спомощью макроанализа можно выявить:
1.Нарушение сплошности металла: усадочную рыхлость газовые пузыри
ираковины, трещины, пустоты; флокены - тонкое трещины, возникающие при выделении свободного водорода в процессе остывания металла; пороки сварки в виде непровара, пор и шлаковых включений ( рис. 1.1).
2.Дендритное и неоднородное строение литого металла (рис.1.1).
3.Химическую неоднородность сплава (ликвацию серы, фосфора, других элементов).
4.Неоднородность строения сплава, вызванную обработкой давлением: волокнистое строение, полосчатость и т.д.
5.Расположение волокон в композиционном материале.
6.При контроле и исследовании металла после термической или химикотермической обработки можно ориентировочно оценить толщину обработанного слоя (закаленного, цементированного и др.), структура которого отличается от структуры основного металла, выявить трещины и т.д.
4

Дефекты макроструктуры деталей
5

а – дефекты сварного шва; б – дендритное строение стальной отливки; в – волокнистое строение кованной детали; г – ликвация серы; д – ликвация фосфора; е – примеры неправильно изготовленных деталей; ж – примеры правильно изготовленных деталей
Рис. 1.1
6
2.2. Методика приготовления макрошлифа Место и направление вырезки образцов из изделия и их число зависит от
целей макроанализа. Образец должен правильно представлять свойства исследуемого металла. Для контроля металла слитков и отливок, проката и кованных заготовок образца (пробы) вырезают в направлении, перпендикулярном продольной оси; их называют темплетами.
При изучении строения слитка, макроанализа сварных швов образцы вырезают в продольном направлении (параллельно продольной оси).
Иногда у одной детали отбирают несколько образцов от характерных мест. Например, в случае исследования поломок или дефектов производства образцы берут так, чтобы сечение излома или дефектного места попало в плоскость шлифа.
В большинстве случаев образцы вырезаются ножовкой или на металлорежущих станках. Нагревание образца вше 100° С должно быть исключено. Если этого избежать невозможно (при газокислородной резке) или заготовка имеет очень высокую твердость, пробы можно подвергать термической обработке (отжигу, отпуску и др.).
Получение плоской поверхности образца и предварительное шлифование производится на шлифовальных кругах средней твердости и со средней величиной зерна. Окончательное шлифование производится на специальной шлифовальной бумаге (металлографической), положенной на жесткую, горизонтально расположенную подкладку (толстое стекло или лист металла). Шлифование производят возвратно-поступательными движениями, не допуская круговых движений. Поверхность образца должна полностью соприкасаться с бумагой. Операции шлифования последовательно повторяют, используя бумагу с меньшим номером зернистости (меньшим размером абразивного зерна) и каждый раз, изменяя направление движения шлифа на перпендикулярное. Это позволяет полностью уничтожить риски, оставшиеся после предыдущей обработки.
Закончив шлифование, на бумаге с самым мелким зерном, образец промывают проточной водой и просушивают фильтровальной бумагой.
Глубокое травление применяется Для выявления трещин волокнистого строения и пористости сталей. Травление проводится в 50%-ном водном растворе соляной кислоты при температуре 60° – 80°С в течение 0,25-1 часа. Сосуд с раствором соляной кислоты обязательно должен находиться в вытяжном шкафу, так как при травлении выделяется ядовитый газ. После травления обра-
7
зец промывается в воде, затем в 10-15%-ном водном растворе азотной кислоты, опять в воде и просушивается. После такой обработки на макрошлифе отчетливо видны трещины, волокнистое строение и пористость стали.
Волокнистое строение стали образуется при ковке или прокалке стальных слитков. Дендриты и междендритный металл при горячем деформировании вытягивается и образует волокна несколько различного состава. При травлении быстрее вытравливается междендритный металл, содержащий больше примесей.
Небольшие трещины плохо видны на шлифованной поверхности детали. При глубоком травлении кислота наиболее активно действует на острые кромки трещин, выходящих на поверхность изделия. Кроме того, кислота проникает в трещину и происходит травление ее внутренних плоскостей. Поэтому после глубокого травления все поверхностные трещины хорошо видны.
Волокнистое строение металла характеризуется резко выраженной анизотропией свойств, что особенно важно для изделий, работающих в условиях динамических нагрузок в напряженном состоянии (шестерни, коленчатые валы, шатуны, клапаны). В этом случае желательно распределение волокон по профилю изделия. Глубоким травлением можно установить и способ изготовления изделия (обработки давлением, резанием).
В табл. 1.1 приведены специальные реактивы, выявляющие дефекты макроструктуры.
Процесс травления должен проходить в строгой последовательности:
а) в фарфоровую ванну или стеклянную налить выбранный из табл. 1.1 реактив (если нужно - подогреть реактив на электроплитке) ;
б) образец при помощи щипцов погрузить шлифовальной поверхностью в реактив и выдержать необходимое время;
в) промыть шлиф проточной водой и просушить фильтровальной, бумагой;
г) протереть шлиф спиртом при помощи ватного тампона и снова просушить фильтровальной бумагой.
После выполнения этих операций готовый макрошлиф подвергают исследованию невооруженным глазом или с помощью лупы.
8
2.3. Исследования макрошлифов
2.3.1.Выявление строения литого сплава:
а) приготовить макрошлиф по вышеуказанной методике} б) травить в реактиве № 3 (табл. 1.1), выдержав 5-10 мин. Если реактив не
подогревается, выдержку увеличить в 2-2,5 раза. Можно применять реактив № 7, в) выдерживать в 15%-ном растворе азотной кислоты в течение 1-2 мин
для получения большей контрастности литого строения, г) снять образовавшийся на шлифе налет и погрузить шлиф в 15%-ный
раствор персульфата аммония} д) промыть макрошлиф в воде, затем в спирте, высушить;
е) исследовать макрошлиф визуально и с помощью лупы; зарисовать макроструктуру сплава (рис. 1.1). В металле отливки могут быть выявлены два различных характера его строения: зернистое и дендритное.
Дендритная структура (древовидная) образуется при кристаллизации отливки или слитка за счет роста зерен от стенок формы (от поверхности) в направлении, противоположном отводу теплоты, т.е. перпендикулярно стенке формы. Дальнейшая кристаллизация приводит к образованию зернистой структуры.
2.3.2.Выявление волокнистого строения стали.
а) приготовить макрошлиф по вышеуказанной методике;
б) травить в реактиве № I (табл. 1.1). Время травления в подогретом до
60-70ºС реактиве 15-20 мин, в холодном – время увеличивается в 2 раза. Можно применять реактив № 2;
в) промыть макрошлиф проточной водой, протереть спиртом, обсушить фильтровальной бумагой;
г) подготовленный макрошлиф исследовать визуально и с помощью лупы зарисовать и дать характеристику выявленной структуры (рис. 1.1).
2.3.3. Выявление структуры, созданной термической или химико-термической обработкой.
Методом макроскопического анализа можно определить глубину закаленного, цементированного, азотированного, цианированного слоев;
а) приготовить макрошлиф по вышеуказанной методике:
б) протравить его в 15%-ном водном растворе азотной кислоты или в реактиве № 4, табл.1.1;
9
в) макрошлиф исследовать визуально и с помощью лупы - определить глубину закаленного или химико-термически обработанного слоя;
г) зарисовать макроструктуру и дать пояснения к ней.
Отличить закаленный и цементированный слои от металла сердцевины можно по свету. Для этого образец нагревают до температуры 300º-500ºС. После этого поверхностный слой имеет темно-синий цвет, а сердцевина – светлосиний.
2.3.4.Выявление ликвации серы.
Макроанализ широко применяется для выявления неоднородности хими-
ческого состава (ликвации) металла. Для выявления ликвации серы применяют метод серных отпечатков»
а) приготовить макрошлиф по вышеуказанной методике; б) подготовить лист фотографической бромосеребрянной бумаги, погру-
зить его в 5%-ный водный раствор серной кислоты на 10 мин, слегка просушить между листами фильтровальной бумаги;
в) влажную фотографическую бумагу наложить на поверхность макрошлифа, прокатать резиновым валиком или пригладить рукой в резиновой перчатке для более плотного прилегания к поверхности шлифа; выдержать 3-5 мин;
г) бумагу, снять (осторожно) со шлифа, промыть водой и поместить в 10%-ный раствор гипосульфита на 5 мин, промыть и высушить.
На бумаге отпечатается поверхность макрошлифа серого цвета, а участки скопления серы имеют более темную окраску. Потемнение участков, содержащих повышенное количество серы, происходит в результате химических реакций. Сера присутствует в стали или в чугуне в виде сульфидов железа и мар-
ганца (FeS и MnS).
Сульфиды вступают в реакцию с серной кислотой, оставшейся на бумаге
FeS + H2SO4 → FeSO4 + H2S↑;
MnS + H2SO4 → MnSO4 + H2S↑.
Выделившийся сероводород вступает в реакцию с бромистым серебром фотобумаги.
2AgBr + H2S — 2HBr + Ag2S↓.
В результате образуется сернистое серебро, которое имеет темный цвет: д) полученный отпечаток наклейте в отчет.
10
|
|
|
|
|
Таблица 1.1 |
|
|
Реактивы, применяемые для травления макрошлифов |
|||
|
|
|
|
|
|
№ |
|
|
Режим травления |
Назначение и |
|
|
Состав реактива |
|
|
особенности |
|
|
|
время |
|||
п/п |
|
Т,° С |
|||
|
|
травления |
применения |
||
|
|
|
|
||
I. |
50% HCl, |
70-100 |
от 10 до45 |
Волокна, глубо- |
|
50% воды |
|
мин |
кое травление |
||
2. |
3 части воды, |
100 |
от 10 до30 |
То же |
|
2 части HCl, |
|
мин |
|
||
|
I часть H2SO4 |
20-80 |
До выявле- |
Дендритное стро- |
|
|
15г персульфата аммония |
||||
3. |
(NH4)2S3 |
2O6, |
|
ния струк- |
ение, кристалли-чес- |
|
100 см |
воды |
|
туры |
кая структура |
|
|
|
|
|
стали |
|
10г двойной соли хлорной |
20 |
I мин |
Места, богатые |
|
|
меди и аммония, |
|
|
фосфором, серой, |
|
4. |
CuCl2•NH4Cl•6H2O и 100см3 |
|
|
углеродом и др. |
|
|
воды |
|
|
|
Примеси окрашива- |
|
|
|
|
|
ются в темный |
|
5г хлорного железа, I0cm3 |
|
|
цвет |
|
|
20 |
До полного |
Медь, латунь, брон- |
||
5. |
НCl 100см3 воды |
|
выявления |
за. Хорошо выяв- |
|
|
|
|
|
структуры |
ляет эвтектику |
|
0,5см3 фтористой кислоты, |
|
|
бронзы |
|
|
20 |
До полного |
Алюминий и его |
||
6. |
99,5 см3 воды |
|
выявления |
сплавы, силумин, |
|
|
500см3 HCl, 70см3 H2S04, |
|
структуры |
дуралюмин и др. |
|
7. |
20 |
20-25 мин |
Строение любой |
||
180см3 Н2O |
|
|
стали |
2.3.5.Определение ликвации фосфора.
Ликвация фосфора определяется специальным травлением. Прошлифо-
ванный и протертый спиртом макрошлиф помещается в раствор, состоящий из 85г ChC£¿, 53гк/НчСС и 1л воды. При травлении железо от поверхности шлифа переходит в раствор, а вместо ее осаждается медь, которая предохраняет поверхность от дальнейшего растворения. В тех местах растворения шлифа, где скопилось большее количество фосфора, меньше осаждается меди, травление происходит интенсивнее.
После травления вся поверхность макрошлифа должна быть покрыта медью. Медный слой осторожно смывается водой, макрошлиф очищается ватой и просушивается.
Места скопления фосфора на поверхности макрошлифа более подвержены действию реагентов, поэтому они бывают более темными.
11
III. ОБОРУДОВАНИЕ, ПРИБОРЫ И МАТЕРИАЛЫ,
I. Набор образцов сплавов, изготовленных различными способами: литьем, ковкой, штамповкой, сваркой, термической обработкой.
2.Шлифовальная бумага.
3.Лупы с 5-, 10- и 20-кратным увеличением.
4.Вата, фильтровальная бумага, спирт, реактивы (табл.1.1), глянцевая бромосеребряная фотографическая бумага.
5.Электрическая плитка, фарфоровые или стеклянные ванночки, щипцы, резиновый валик.
IV. МЕТОДИЧЕСКИЕ УКАЗАНИЯ ПО ВЫПОЛНЕНИЮ РАБОТЫ. Необходимо приготовить макрошлиф, по ранее приведенной методике
п.2.2, провести исследования предложенного образца (п.2.3). Описать результаты исследований, сделать обоснованные выводы о характере распределения волокон (параллельные волокна или расположенные по профилю изделия видения), способ изготовления изделия (обработка давлением, резанием или сварка), качество стали (по количеству и расположению вредных примесей), обнаруженные дефекты (трещины, пористость), При исследовании макроструктуры сварных деталей, необходимо оценить качество отдельных элементов и сварного шва.
V. СОДЕРЖАНИЕ ОТЧЕТА
1.Описание, назначение и цель работы.
2.Указать перечень основных операций по приготовлению макрошлифа.
3.Привести рисунки исследуемых макроструктур.
4.Дать заключение о выявленных структурах и пороках.
VI. ВОПРОСЫ ДЛЯ САМОКОНТРОЛЯ
I.Что такое макроструктура?
2.Какими способами изучают макроструктуру?
3.Для каких целей применяют анализ макроструктуры?
4.Как подготавливают образцы для макроанализа?
5.Как выявляют макроструктуру?
6.Как выявляют макростроение литого образца?
7.Как выявляют волокнистое строение стали?
8.Как выявляют глубину закаленного и цементированного слоя?
12
ЛАБОРАТОРНАЯ РАБОТА № 2 ИЗУЧЕНИЕ ИЗЛОМОВ (ФРАКТОГРАФИЯ)
I. ЦЕЛЬ РАБОТЫ: ознакомиться с характерными изломами сталей; научиться по излому определять дефекты сталей.
П. КРАТКИЕ ТЕОРЕТИЧЕСКИЕ СВЕДЕНИЯ Одним из основных методов исследования макроструктуры и макроде-
фектов является исследование изломов. Он дает возможность определить причины разрушения детали. Если такая деталь имела невысокую твердость, излом чаще всего бывает вязким, волокнистым. В таких случаях очень трудно по излому определить дефекты стали. Если имеется хрупкий излом, можно определить причину разрушения детали по характеру излома. На практике встречается несколько характерных изломов. Вид излома зависит от условий нагружения - однократного (при статическом растяжении, кручении, изгибе или ударе) или от многократного (при усталости), а также от температуры и других внешних факторов.
2.1. Макроанализ излома Методом макроанализа при внешнем осмотре изломов различают разные
сплавы даже одной системы. Например, стали и белые чугуны, у которых весь углерод связан в цементит, имеют светлый излом, а серые, ковкие и высокопрочные чугуны - темные из-за присутствия графита.
По характеру разрушения различают два основных вида изломов - хрупкий и вязкий, а также смешанный, в нем есть области вязкого и хрупкого разрушения, рис. 2.1.
Вязкий излом имеет обычно матовый волокнистый вид, тогда как хрупкий - кристаллический блестящий, так как разрушение металла в этом случае в отличие от предыдущего развивается по определенным кристаллографическим плоскостям скола. Наиболее опасной для службы изделия является именно вероятность появления хрупкого излома как результата внезапного, т.е. быстро развивающегося разрушения, отличающегося существенно меньшей энергоемкостью по сравнению с вязким, происходящим относительно медленно. Однако хрупкий излом может оказаться результатом развития процесса разрушения по вязкому механизму.
В ряде случаев в изломе стальных поковок или проката больших сечений, особенно из легированной стали, видны белые пятна, называемые флокенами рис. 2.2.
Присутствие флокенов недопустимо, так как вызывает появление трещин и ведет к разрушению. Флокены появляются в результате микроликвации, а главное, повышенного содержания водорода, рис.2.3,
Флокенами называются круглые или эллиптические внутренние тре-
13

Виды изломов
а) б)
а – вязкий излом; б – хрупкий излом Рис. 2.1
Флокены в изломе
Рис 2.2.
14
щины диаметром от I до 100 мм. В изломе стали флокены видны как круглые или эллиптические серебристые пятна.
Чаще всего флокены образуются в высокоуглеродистых и высоколегированных сталях. Исключение составляют стали ледебуритного класса. Основная причина возникновения флокенов - повышенное содержание водорода в стали, как уже указывалось выше.
Когда сталь с высоких температур охлаждается до 250ºС, уменьшается растворимость водорода. Если сталь, имеющая повышенное содержание водорода, охлаждается с большой скоростью ниже 250º С, водород вызывает большие напряжения, которые, суммируясь с напряжениями, возникающими из-за структурных превращений, могут вызвать трещины-флокены.
Образовавшиесяфлокенывсталяхмогутбытьустраненыгорячей ковкой. Флокены необразуются, если послековкиилиотжигастальохлаждаетсямедленно.
2.2. Микроанализ изломов Вязкий излом, образующийся в условиях однократного нагружения, при
микроанализе, имеет ямочное строение - состоит из большого числа возникающим по границам зерен или в их объеме при разрушении ямок, т.е. микропор или микропустот различных размеров и форм, которые по мере разрушения сливаются (рис. 2.4). Размер этих ямок и их расположение зависят от присутствия различных неоднородностей - частиц избыточных фаз, дефектов кристаллов матричной фазы и т.д.
Хрупкий излом при однократном нагружении может быть 2-х видов - ручьистым, если разрушение развивалось внутри зерен, или межзеренным, если оно происходило по границам зерен или фаз (рис. 2.5 ),
Ручьистый излом развивается по определенным кристаллографическим плоскостям, образуя внешние плоские фасетки скола, состоящие в действительности из более мелких ступенек скола, на которых виден определенный узор, называемый ручьистым,- следствие развития разрушения от соседних трещинок, возникающих в параллельных плоскостях. Появление межзеренного или межкристаллитного хрупкого излома является следствием присутствия по границам зерен повышенного количества примесей, выделений частиц охрупчивающих фаз и т.п. Внешне такой межзеренный излом характеризуется наличием относительно гладких поверхностей. Следует отметить, что хрупкое разрушение может происходить и по границам субзерен (субзеренное разрушение) и по границам фаз (межфазовое разрушение).
Специфический вид имеет излом металлов, полученный в результате
15

Излом забракованной плавки хромоникелевой стали
Рис. 2.3.
Вязкий ямочный излом стали
Рис. 2.4.
16
многократного нагружения, как при усталостных испытаниях.
Этот излом в общем случае состоит из 2-х зон-собственно усталостной, характеризующейся наличием ряда криволинейных полос, где развивается трещина, возникшая в результате накопления дефектов строения, и зона макрохрупкого разрушения, или зоны долома, появляющейся уже после того, как металл, ослабленный в результате медленного развития трещины в первой зоне, оказывается уже сильно ослабленным.
Присутствие бороздок в изломе является показателем того, что разрушение металла произошло в результате усталости. Для анализа механизма разрушения определенное значение имеет расстояние между бороздками. Чем оно больше, тем быстрее распространялся фронт трещины, рис.2.6.
Усталостные изломы наиболее часто встречаются и легко опознаваемые. Как правило, так разрушаются детали, подвергаемые переменным нагрузкам. Направление излома в большинстве случаев бывает перпендикулярно максимальным напряжениям растяжения. Усталостный излом всегда имеет две зоны разрушения: прогрессивного распространения трещины и окончательного разрушения. Прогрессивное распространение трещины начинается из одного или нескольких очагов. Очагами бывают микродефекты металла: микротрещины, неметаллические включения, флокены и др.
При постепенном распространении трещины на изломе наблюдаются характерные, параллельные, в большинстве случаев кольцевые следы, имеющие гладкую поверхность. Под воздействием переменных нагрузок трещина увеличивается, а рабочее сечение детали уменьшается. Когда оно становиться незначительным, деталь разрушается. Зона окончательного разрушения для хрупких сталей – крупнозернистая, а для мягких – волокнистая.
На поверхностях деталей, подвергаемым контактным нагрузкам (шарикоподшипники, колеса вагонов), могут возникнуть усталостные выкрашивания – питинг.
Излом перегретой стали. При нагреве стали, содержащей 0,4% углерода, до 800-820ºС, ее структура состоит из мелкозернистого аустенита (при увеличении содержания углерода температура аустенитного превращения понижается до 730-740°С). Если температура нагрева стали повышается, аустенитное зерно увеличивается, что ведет к ухудшению механических свойств стали после ее охлаждения. Перегретые детали разрушаются от небольших нагрузок, образуя крупнозернистый излом. На практике сталь для закалки нагревают по возможности до наиболее низких допустимых температур. Это обеспечивает высокие механические свойства и мелкозернистый излом.
17

Виды хрупких изломов
а – ручьистый излом стали; б – излом межзеренного разрушения стали Рио.2.5
Излом зоны усталостного разрушения стали
Рис. 2.6
18
Камневидный излом. Если конструкционные стали нагреть до высоких температур, близким к температурам плавления, значительно вырастают аустенитные зерна, на их поверхности выделяются неметаллические примеси. Такие детали легко разрушаются. Полученный крупнозернистый излом напоминает излом камня. Микроструктуру перегретых деталей можно исправить только специальной, длительной термической обработкой.
Нафталинистый излом. Так разрушаются высоколегированные инструментальные, в основном, быстрорежущие стали. Такой излом крупнозернистый, имеет много гладких участков (размера зерна), отличающихся неметаллическим блеском, напоминающих зерна нафталина. Иногда блестящие области занимают большую часть излома. Нафталинистый излом встречается в инструментах, подвергнутых повторной закалке без промежуточного отжига.
Нафталинистый излом получается и в том случае, когда перед закалкой инструмент подвергался ковке и ковка заканчивалась при высокой температуре. После ковки такой инструмент необходимо отжечь и только после отжига его можно калить. Тогда нафталинистый излом не появляется.
Шиферный излом. Он напоминает слоистый излом дерева и наблюдается только в продольных изломах, когда деталь разрушается вдоль направления прокатки. Сталь, которая при разрушении дает шиферный излом, имеет низкие механические свойства. Основной причиной разрушения такого вида является неоднородность химического состава - ликвация.
Структуру и механические свойства стали, дающей шиферный излом, можно улучшить диффузионным отжигом (длительным нагревом при 11501250ºС). После диффузионного отжига для измельчения структуры необходимо выполнить еще обычный отжиг.
Черный излом. Излом такого рода встречается в высокоуглеродистых сталях, особенно в легированных кремнием, вольфрамом, молибденом. Его появлению способствует также ковка до низких температур, продолжительный нагрев вблизи температуры 700ºС, холодная деформация перед отжигом и другие причины. Черный цвет излому придает выцедившийся при отжиге графит. Черные пятна в изломе могут быть на поверхности или в центре прутка в зависимости от того, в каком месте детали были значительнее напряжения растяжения.
Черный излом чаще встречается в отоженных сталях. Закаленные стали по такому излому разрушаются только при наличии значительного количества графита.
Графит, выделившийся в микроструктуре стали, ухудшает ее механические свойства, особенно ударную вязкость.
19
Изучения изломов важно для определения надежности изделия, одним из главных критериев которой является, в частности для металлов и сплавов с решетками ОЦК и ГПУ, критическая температура хрупкости, T50, т.е. температура, при снижении которой осуществляется достаточно резкий переход от вязкого механизма разрушения к хрупкому. Критическая температура хрупкости, или порог хладноломкости, определяется по размеру той части площади излома
(%) на которой излом имеет вязкий (согласно макроанализу, волокнистый) характер, или, точнее, где путем микроанализа выявляется его ямочное строение. За критическую температуру хрупкости чаще всего принимают температуру испытаний на ударную вязкость, при которой 50% площади всего излома разрушается по механизму вязкого разрушения, а иногда - температуру испытаний, при которой площадь вязкого разрушения составляет 10 или 90% всей площади излома.
III. ОБОРУДОВАНИЕ, ПРИБОРЫ, МАТЕРИАЛЫ Коллекция образцов изломов; лупа с увеличением х50.
IV. МЕТОДИЧЕСКИЕ УКАЗАНИЯ ПО ВЫПОЛНЕНИЮ РАБОТЫ
Ознакомиться с коллекцией изломов и по предложенным и п.2 характеристикам определить вид излома, дать заключение о возможных причинах разрушения.
V. СОДЕРЖАНИЕ ОТЧЕТА
Отчет должен содержать в себе ряд теоретических сведений, зарисовки структуры изломов с описанием их характеристик, причины разрушения.
VI. ВОПРОСЫ ДЛЯ САМОКОНТРОЛЯ
1.Сущность исследования изломов стали.
2.Виды и характеристики изломов.
3.С какой целью проводят исследования изломов?
4.Что понимают под критической; температурой хрупкости?
5.Сущность вязкого разрушения.
6.Сущность хрупкого разрушения.
20
ЛАБОРАТОРНАЯ РАБОТА № 3 ИЗУЧЕНИЕ УСТРОЙСТВА МЕТАЛЛОГРАФИЧЕСКОГО МИКРОСКОПА
I. ЦЕЛЬ РАБОТЫ: ознакомиться с устройством металлографического микроскопа; научиться правильно выбрать оптику и настраивать микроскоп и освещение.
II. КРАТКИЕ ТЕОРЕТИЧЕСКИЕ СВЕДЕНИЯ
Металлографический микроскоп - прибор для наблюдения и фотографирования структуры металлов, использующий отраженный свет от непрозрачного объектива - шлифа. Набор объективов и окуляров обеспечивает в современных микроскопах полезное увеличение до 2000 раз.
На рис. 3.1 приведена оптическая схема микроскопа МИМ-7. Микроскоп представляет собой комбинацию двух увеличивающих оптических систем - объектива 12 и окуляра 19, разделенных значительным расстоянием. Расстояние между фокусами объектива и окуляра называется оптической длиной тубуса l. Эта величина близка по значению к расстоянию между опорной плоскостью объектива и верхним краем тубуса микроскопа (на схеме тубус не показан, окуляр 19 вставляется в его верхнюю часть). Исследуемый шлиф помещают на предметный столик 13 перед объективом немного дальше его фокуса так, что объектив дает увеличенное действительное изображение структуры. Это изображение при помощи линзы 14 переносится в плоскость, близкую к фокусу окуляра. Окуляр расположен относительно промежуточного изображения как лупа, в результат чего окончательное изображение получается мнимым, обратным, увеличенным, отстоящим на 250мм от глаза наблюдателя.
При визуальном наблюдении в ход лучей вводится зеркало 18, которое отклоняет лучи в сторону окуляра 19. При переводе изображения на фотокамеру зеркало выключается выдвижением тубуса вместе с окуляром и зеркалом и лучи направляются от объектива непосредственно к фотоокуляру 15.
Осветительная системе микроскопа состоит из лампы I, которая может центрироваться относительно оси (на схеме оптическая ось микроскопа показана сплошной черной линией, коллекторной линзы 2, проектирующей источник света на плоскость апертурной диафрагмы 5 и набора светофильтров 4.
Световые фильтры применяют при визуальном наблюдении и при фотографировании, они делают свет более монохроматичным. Поскольку в объективах - ахроматах сферическая аберрация исправлена только в отношения жел-
21
то-зеленого цвета и глаз человека обладает к указанному цвету большей чувствительностью, для визуального рассмотрения структуры следует применять желто-зеленые светофильтры.
Для получения лучшего изображения очень важно применять специальные диафрагмы, ограничивающие световые лучи. Диафрагма 5, ограничивающая пучок лучей, входящих в систему микроскопа, называется апертурной, диафрагма 8 - полевой, так как она ограничивает размер поля, освещаемого на шлифе. Степень раскрытия этих диафрагм изменяется в зависимости от выбранных для работы объектива и окуляра. Общий вид микроскопа (рис. 3.2).
Изображение предмета увеличивается в микроскопе дважды, поэтому увеличение микроскопа Nm определяется собственными увеличениями объектива Nоб и окуляра Nок и равно их произведению:
Nm= Nоб• Nок= |
250 |
|
, |
fоб f |
|
||
|
ок |
где fоб и fок - фокусные расстояния объектива и окуляра; 250 мм - расстояние наилучшего зрения глаза;
l - оптическая длина тубуса.
Главное увеличение обеспечивается объективом, оно может достигать 100. Увеличение окуляров не делают больше 20-24.
Характеристика увеличений объективов и окуляром, входящих в комплект микроскопа МИМ-7, приведена в табл. 2.1.
|
|
|
|
|
|
|
Таблица 2.1 |
||
|
Таблица увеличения объективов и окуляров |
|
|
|
|||||
|
|
|
микроскопа МИМ-7 |
|
|
|
|
||
|
|
|
|
|
|
|
|
|
|
Объективы |
|
При визуальном наблюдении |
При фотографировании |
||||||
|
|
окуляры |
|
|
окуляры |
|
|
||
|
|
7х |
10х |
15х |
20х |
7х |
10х |
15х |
|
8,6х |
60 |
90 |
130 |
170 |
70 |
120 |
160 |
|
|
F -23,2, A=0,17 |
|
||||||||
|
|
|
|
|
|
|
|
|
|
14,4х |
100 |
140 |
200 |
300 |
115 |
200 |
270 |
|
|
F=I3,89, A=0,3 |
|
||||||||
|
|
|
|
|
|
|
|
|
|
24,5х |
170 |
240 |
360 |
500 |
200 |
340 |
450 |
|
|
F=8,I6, A=0,37 |
|
||||||||
|
|
|
|
|
|
|
|
|
|
32,5х |
250 |
320 |
500 |
650 |
260 |
440 |
600 |
|
|
F=6,I6, A=0,65 |
|
||||||||
|
|
|
|
|
|
|
|
|
|
72,2х |
500 |
720 |
1080 |
1440 |
575 |
1000 |
1350 |
|
|
F=2,77, A=I,25 |
|
||||||||
|
|
|
|
|
|
|
|
|
22

Оптическая схема металлографического микроскопа МИМ-7
Рис 3.1
23

Микроскоп МИМ – 7
I-основание; 2- корпус; 3- устройство для фотографирования с рамкой; 4-мик- рометрический винт для тонкой настройки; 5-раздвижной тубус; 6-окуляр; 7- вертикальный иллюминатор; 8- держатели; 9-предметный столик; 10рукоятки для включения диафрагма при работе и темном поле; 11подвижный кронштейн; 12-микрометрический винт для грубой настойки; 13-диск с набором светофильтров; 14фонарь (лампа накаливания, закрытая кожухом); 15осветитель; 16зажимные винты; 17узел апертурной диафрагмы; 18фотозатвор 19поводок для установки отверстия диафригмы;20-центрировочные винты полевой диафрагмы; 21кожух; 22объектив; 23рамка с линзами для создания светлого и темного полой; 24зажимной винт, фиксирующий положение столика в вертикальной плоскости; 25рукоятка для переключения фотоокуляров; 26 - винт для смещения диафрагмы при установке косого освещения; 27винты для настройки освещения; 28винт для фиксирования положения апертурной диафрагмы при ее повороте
Рис. 3.2
24
Резкость и контрастность изображения достигается сложной конструкцией объективов и окуляров, устраняющих частично или полностью оптические дефекты. Однако возможности микроскопов используются наилучшим образом, если исследователь правильно пользуется коллектором 2 полевой и апертурной диафрагмами. Кроме того, для увеличения оптического констраста многие микроскопы позволяют применять специальные методы исследования: исследование при "косом освещении", метод темнопольного освещения, наблюдение в поляризованном свете и др. (рис. 3.1).
Для исследования рельефных структур применяют метод косого освещения, когда для передачи изображения используются преимущественно косые, не параллельные оси микроскопа, лучи. Образующиеся при этом освещении тени от выступающих частей структуры усиливают контраст. Косое освещение шлифа осуществляется смещением апертурной диафрагмы с оси. Для наилучшего выявления отдельных элементов структуры может оказаться полезным при этом изменить плоскости падения света на шлиф Это достигается вращением оправы апертурной диафрагмы 5.
Метод темнопольного освещения выгодно применять в том случае, когда исследуемый объект имеет фазы, по-различному рассеивающие свет (например, неметаллические включения в металлических сплавах, рельеф). При темпопольном освещении в формировании структуры прямые лучи не участвуют. Зеркально отполированная поверхность объекта при темнопольном освещении кажется темной, участки, вызывающие рассеивание света (рельеф, т.е. впадины, выпуклости), кажутся яркими. При исследовании неметаллических включений легко удается оценить прозрачность включений.
Для темнопольного освещения линза 10 перемещается вправо. На микроскопе линза 10 для светлого поля обозначается буквой С, для темного поля - Т.
Кроме того, включается специальная откидная диафрагма для того, чтобы на отражательную пластинку II падал параллельный пучок света в виде светового кольца, тем самым прямые лучи при полностью открытой апертурной диафрагме 5 в изображении участвовать не будут.
При анализе неметаллических включений и рельефных структур оптический контраст может усиливаться применением поляризованного света, для чего микроскоп снабжен поляризатором 21 для создания плоскополяризованного света и вкладным анализатором 20, который используется для анализа изменений света в результате рассеяния его объективом. Вращением анализатора 20 можно добиться изменения яркости свечения отдельных структурных составляющих и изменения контрастности структуры.
25

Под разрешающей способностью прибора понимают наименьшее расстояние между двумя точками, при котором они видны раздельно. Разрешающая способность микроскопа δ зависит от апертуры объектива А и длины световой волны λ:
0,61A , где А = nSin α,
так как от показателя преломления среды между объективом и предметом n и от отверстного угла линзы 2α будет зависеть количество лучей, отраженных предметом, которые попадут в объектив.
На рис. 3.3 показана схема влияния отверстного угла объектива и показателя преломления среды на разрушающую способность.
В объективе I слишком мелкие детали структуры не разрешаются микроскопом, так как дифрагированные лучи (стрелки) не попадают в объектив (половина отверстного угла α' меньше угла отклонения φ ). В объективе 2 детали структуры разрешаются (α''> φ). В объективе 3 действие масляной иммерсии сказывается на уменьшении угла отклонения дифрагированных лучей (φ1>φ ).
Разрешающая способность объектива используется полностью только в том случае, если раскрытие апертурной диафрагмы микроскопа обеспечивает полное заполнение светом диафрагмы объектива. Как увидим позже, при правильной установке диафрагмы это условие для объективов-ахроматов не реализуется.
Схема апертуры объектива
Фронтальная линза объектива
Рис. 3.3
26
Приработевсветломполеполяризатор21ианализатор20хранятвящикедляоптики. III. ОБОРУДОВАНИЕ, ПРИБОРЫ И МАТЕРИАЛЫ
1.Металлографический микроскоп МГТМ-7.
2.Набор объективов и окуляров.
3.Микрошлиф доэвтектоидной углеродистой стали.
IV. МЕТОДИЧЕСКИЕ УКАЗАНИЯ ПО ВЫПОЛНЕНИЮ РАБОТЫ
1.Ознакомиться со схемой микроскопа, обратить внимание на взаимное расположение деталей микроскопа и их назначение.
2.Поставить объектив и окуляр, обеспечивающие увеличение 200. Сфокусировать изображение структуры образца, представляющей смесь зерен феррита и перлита.
3.Отрегулировать освещение в светлом поле:
а) установить однородное освещение осветительной линзы 6. Для этого на оправку линзы положить матовую бумагу и проверить, фокусируется ли изображение нити лампы в центре отверстия апертурной диафрагмы. Такое положение достигается регулированием центрировочных винтов осветителя I. Фокусировку нити лампы студент выполняет в присутствии преподавателя (по рис. 3.1); б) правильно установить полевую диафрагму 8 относительно выбранного оку-
ляра 19. Закрыв предварительно полевую диафрагму и глядя в окуляр, раскрыть полевую диафрагму так, чтобы ее края совпадали с полем зрения окуляра. При наблюдаемом смещении полевой диафрагмы следует отцентрировать ее специальными центрировочными винтами. При освещении большей площади на шлифе изображение видимой части будет ухудшаться; в) правильно установить апертурную диафрагму 5 осветителя. Для этого вы-
нуть окуляр и, глядя на отражательное зеркало 18, где проектируется изображение светового поля объектива и апертурной диафрагмы, добиться того, чтобы апертурная диафрагма осветителя заполнила светом 75% поля объектива. Так достигается оптимальное сочетание хорошей контрастности при наименьшей потере разрешающей способности микроскопа для объективов-ахроматов. При большем раскрытии апертурной диафрагмы уменьшается четкость и контрастность изображения вследствие появления рассеянного света и сферической аберрации. При меньшем раскрытии уменьшается разрешающая способность микроскопа); г) рассмотреть и зарисовать видимую структуру.
4. Выбор оптики для образца:
а) определить требуемое увеличение микроскопа из соотношения
Nm=Nоб•Nок;
27
б) определить значение апертуры А для верхнего предела полезного увеличения из соотношения Аббе:
Nm= (500÷1000) А,
где 500 А - нижний предел увеличения, меньшее увеличение не дает возможности исследователю различать все детали объекта, передаваемые объективом с апертурой А; 1000 А - верхний предел, большее увеличение не дает каких-либо новых деталей структуры, а приводит к ухудшению качества изображения.
Из полученных предельных значений апертуры А выбрать объектив по табл. 2.1;
в) из соотношения найти требуемое увеличение окуляра; г) поставить выбранные по расчету окуляр и объектив, наладить освещение, рассмотреть и зарисовать структуру образца}
д) перевести изображение на фотокамеру, изменив при этом соответственно раскрытие полевой диафрагмы; е) образец рассмотреть при косом освещении, для чего необходимо, глядя в
окуляр, постепенно смещать апертурную диафрагму и следить за изменением изображения структуры; ж) шлиф рассмотреть в светлом и темном поле.
V. СОДЕРЖАНИЕ ОТЧЕТА
1.Зарисовать оптическую схему металлографического микроскопа МИМ-7.
2.Указать основные характеристики металлографического микроскопа
(увеличение, разрешающую способность и др.).
3. Определить увеличение микроскопа, рассмотреть и зарисовать видимую структуру при увеличении 130 и 500.
ВОПРОСЫ ДЛЯ САМОКОНТРОЛЯ.
1.Кратко охарактеризуйте устройство и принцип работы металлографического микроскопа.
2.На каком принципе построена работа металлографического микро-
скопа?
3.Как установить увеличение металлографического микроскоп?
4.Каков предел увеличения металлографического микроскопа?
5.Каково назначение основных элементов оптической схемы металлографического микроскопа?
6.Дайте характеристику разрешающей способности световой оптики.
7.Укажите, как настроить резкость и контрастность изображения на металлографическом микроскопе.
28
ЛАБОРАТОРНАЯ РАБОТА № 4 МИКРОСКОПИЧЕСКИЙ МЕТОД ИССЛЕДОВАНИЯ МЕТАЛЛОВ И
СПЛАВОВ (МИКРОАНАЛИЗ)
I. ЦЕЛЬ РАБОТЫ: ознакомиться с сущностью микроанализа; изучить методику и способы приготовления микрошлифов; ознакомиться со структурой материала на приготовленных образцах.
II. КРАТКИЕ ТЕОРЕТИЧЕСКИЕ СВЕДЕНИЯ.
2.1. Сущность микроанализа Сущностьмикроанализазаключаетсявизученииструктурыметаллов, сплавов
идругихматериаловспомощьюмикроскопаприувеличенияхот50 до300000 рази выше. Применениеэтогометодапозволяетознакомитьсясостроением(структурой) металловисплавов. Микроанализдаетвозможностьрешатьследующиезадачи:
а) установить тип сплава; б) определить форму и величину зерен в сплавах;
в) установить присутствие и характер расположения отдельных структурных составляющих;
г) определить состояние сплавов: закаленные, отожженные и т.д.
С помощью микроанализа можно решать много других задач, которые позволяют судить о строении и свойствах материалов.
Результаты металлографических исследований во многом зависят от способа приготовления образцов (микрошлифов).
Приготовление микрошлифов состоит из ряда операций, выполнить которые необходимо в строгой последовательности. Сначала отбирают пробу. Проба - часть металлопродукции, отобранная из наиболее характерных зон для изготовления из нее заготовок под образцы.
Место взятия пробы зависит от способа производства изделия, с других факторов и может быть определено макроанализом.
Например, при изучении литого материала необходимо отбирать пробы из толстых и тонких сечений, учитывая направленность кристаллизации, а при исследовании прокатного изделия необходимо отбирать образцы как в продольном, так и в поперечном сечениях. При исследовании поверхностных слоев применяются косые срезы.
Образцы из заготовки вырезаются ручным способом, чтобы не повысилась температура, приводящая к изменению структуры. Это особенно важно после закалки, так как выше 100С начинаются превращения отпуска. При вырезке механическим способом (например, шлифовальным тонким диском закаленных образцов) следует применять обильное охлаждение.
29
После вырезки приготовляемая поверхность выравнивается напильником, а при высокой твердости - наждачным диском (образец держать рукой, чтобы чувствовать степень нагрева).
По возможности образцы вырезаются такой величины, чтобы сторона прямоугольного или диаметр цилиндрического образца были не меньше 6-8 мм. В меньших образцах при шлифовании закругляются края, а у больших (более 3- 6 см2 )-труднее вывести все царапины и другие неровности поверхности. Высота образцов берется на 20-30% меньше. Размеры нормальных образцов показаны на рис. 4.1.
Когда размеры образцов очень малы, то следует их заливать в пластмассу, серу или легкоплавкий сплав, или закреплять в специальных струбцинках. Примеры таких приспособлений показаны на рис. 4.2; а - хомутик для мелких круглых образцов, б - струбцинка для плоских тонких образцов.
2.2. Методика приготовления микрошлифа.
Плоскую поверхность подготавливают на торцовой поверхности образца вращающимся шлифовальным кругом или опиливают напильником. Далее образец шлифуется. Существует два способа шлифования образцом: ручной и механический. При ручном способе шлифования на жесткую плотную подкладку (толстое стекло или лист металла) кладут наждачную бумагу, ставят образец заторцованной плоскостью и шлифуют с легким нажимом. Шлифование ведут до полного удаления рисок, оставшихся после предыдущей обработки.
После этого шлифование прерывают, удаляют остатки абразива с образца и подкладки и меняют шлифовальную бумагу на более мелкозернистую.
При повторном шлифовании на бумаге с более мелким зерном направление движения образца должно быть перпендикулярно направлению рисок, оставшихся от первого шлифования. Операции шлифования повторяют, используя последовательно бумагу с меньшим номером зернистости и каждый раз изменяя направление движения шлифа на 90º.
Наждачная бумага маркируется номером, показывающим среднюю величину абразивного зерна в сотых долях миллиметра. Очень мелкий порошок маркируется буквой "М" и крайней величиной абразивного порошка в микрометрах. Применяемый сортамент наждачной бумаги покапан в табл. 4.1.
30

Размеры микрошлифов
А - оптимальные; б - минимальные; в - максимальные Рис. 4.1
Струбцины для образцов малого размера
Рис. 4.2.
Установка для электролитического полирования
B- образец; Е -электролит; К - катод; М - смеситель;
Г- градусник
Рис. 4.3.
31

Эталоны для основных включений в стали
Рис. 4.4
32
|
Размер и нумерация абразивных частиц |
Таблица 4.1 |
|||
|
|
||||
|
|
|
|
|
|
Номер |
Величина |
Номер |
Величина |
Номер |
Величина |
зерна |
частиц, мкм |
зерна |
частиц, мкм |
зерна |
частиц, мкм |
12 |
150125 |
4 |
5328 |
М-14 |
1410 |
10 |
125105 |
3 |
4220 |
М-10 |
10- 7 |
8 |
10575 |
М-40 |
4028 |
М-7 |
7- 5 |
б |
8463 |
М-28 |
2820 |
М-5 |
5- 3,5 |
5 |
6342 |
М-20 |
2014 |
|
|
Закончив шлифование на бумаге с самым мелким зерном, образец промывают проточной водой и полируют до зеркального блеска. Существуют два вида полирования: механическое и электролитическое. Механическое полирование производится на полировальных станках с вертикально или горизонтально расположенными вращающимися дисками, обтянутыми мягкой тканью: сукном, фетром, драпом, шелком и др. Чем мягче полируемый материал, тем тоньше должно быть строение ткани.
После промывки водой шлифованный образец полируется т быстровращающемся (400-800 об/мин) диске, обтянутым фетром или сукном, который смачивается водой с мельчайшим порошком, например, окиси алюминия или хрома (до I мкм) - суспенсией. Часто на I л воды берется 5-10 г порошка, размешивается и дается отстояться. Чем дольше выдерживается, тем лучше сливается вода с более мелкой фракцией (осаждаются более крупные частицы).
При полировании образец прижимают к поверхности круга всей плоскостью. Во время полирования образец следует поворачивать. Полирование чугуна и стали должно продолжаться не более 3-5 мин. и прекращаться, как только будут выведены последние риски, оставшиеся на шлифе после шлифования.
После полирования шлиф промывают водой, затем спиртом и сушат, прижимая (не вытирая) к фильтровальной бумаге, или сушат струей воздуха.
Механическая полировка может оставить до 13 мкм упрочненный слой. Поэтому иногда применяется электролитическое полирование. Для этого берется одна часть азотной кислоты (уд. вес 1,4) и две части метанола (метилового алкоголя). При напряжении 40-70В и плотности тела 0,1-0,2 А/см2 продолжительность полирования 10-60с . Такой электролит подходит для сталей, медных сплавов, сплавов алюминия и некоторых других. Но во время процесса обязательно нужно охлаждать. Схема устройства электрополировки показана на рис. 4.3: в ванну с электролитом Е помещается полируемый образец В, кото-
33
рый подсоединяется как анод. Катод К делается из нержавеющей стали. Температуру показывает термометр Т, а выравнивает винт М.
Полированныйобразецназываетсянетравленныммикрошлифом. Разглядываячерезмикроскоп, всяметаллическаяповерхностьвиднакаксветлаяблестящаяповерхность.
При наличии в металле неметаллических включений, например, окислов, силикатов или сульфидов, они темными частицами выделяются на светлом фоне, так как часть света они абсорбируют, а часть рассеивают. Таким образом, для определения характера неметаллических включений следует применять нетравленные микрошлифы.
Нетравленные микрошлифы дают возможность выявить неметаллические включения (в травленном шлифе они сливаются с металлическими структурными составляющими). Вид и количество неметаллических включений устанавливаются по эталонным таблицам ГОСТа 1778-80. Учебные эталоны представлены на рис. 4.4. Здесь показаны неметаллические включения сталей: I- окислы строчечные, 2-окислы точечные, 3-хрупкие силикаты, 4 - пластичные силикаты, 5 - шарообразные силикаты, 6 - сульфиды, 7 - нитриды титана. Большую трудность представляет определение пластичных сульфидов и силикатов. Следует применить изображение в "темном поле": силикаты остаются светлыми, а сульфиды сливаются с темным полем.
Количество включений характеризуется баллами, сравнивая с эталоном при 100-кратном увеличении изображения. Разрешается оценивать и промежуточными баллами: 1,5; 2,5..., а также пометить "выше 5".
После любого полирования микрошлиф промывают проточной водой, просушивают фильтровальной бумагой, затем протирают ватным тампоном, смоченным в спирте, и снова просушивают.
Травление микрошлифа. Для того, чтобы под микроскопом можно было различить структурные составляющие, надо вызвать неодинаковое отражение света от каждой из них. Это достигается травлением полированной поверхности образца соответствующим реактивом. Наиболее часто применяемые реактивы приведены в табл.4.2.
При травлении на поверхности шлифа происходит растворение структурных составляющих и границ зерен, проявляются механические смеси, форма и расположение зерен.
Поцвету, формеиразмерамможновыявитьмикроструктурусплава(см. рис. 4.5). Травление шлифа сводится к следующим операциям:
I. Реактив наливают в ванночку и, если нужно, подогревают. 2. Поверхность шлифа обезжиривают спиртом или бензином.
34
3.Погружают полированную поверхность в реактив и выдерживают несколько секунд.
4.Протравленный шлиф промывают в проточной воде, затем в спирте и просушивают фильтровальной бумагой.
После этого микрошлиф можно рассматривать в микроскоп.
|
|
|
Таблица 4.2 |
|
Состав и применение реактивов |
|
|
|
|
|
|
Наименование |
Состав реактива |
Применение реактива |
Примечание |
реактива |
|
|
|
Спиртовойрас- |
I-5см2 азотнойки- |
Рекомендуетсядлявыяв- |
Следуетприменятьазот- |
творазотнойкислотыи100см3 |
ленияперлитапластинча- |
нуюкислотусуд. весом |
|
слоты |
этиловогоспирта |
того, сорбита, трастита. |
1,42.Чтобыизбежать |
|
илиметилового |
Хорошовыявляетгра- |
окисления, необходимо |
|
|
ницызеренферрита, а |
шлифпротереть, промыть |
|
|
такжемартенсит |
спиртомнеменеедвухраз |
Растворпер- |
10гперсульфата |
Окрашиваютферрит |
|
сульфатааммо- |
аммонияи100гво- |
|
|
ния |
ды |
|
|
Пикратнатрия |
25гедкогонат-рия, Длявыявленияцементита Следуетприменятькипя- |
||
|
100см3 воды, 2г |
идругихкарбидов |
щимпри100°С5-10 мин |
|
пикриновойки- |
|
|
|
слоты |
|
|
Царскаяводка |
3 частиHCl, I частьВыявляетструктурувысоДлялучшеговыявления |
||
|
HNO3 |
кохромистых, быстроре- |
рекомендуетсяпроизво- |
|
|
жущих, аустенитныхмар- |
дитьпопеременноетрав- |
|
|
ганцовистыхсталей |
лениеиполирование |
Хлорноежелезо 10гхлорногоже- |
Хорошовыявляетструк- |
Применять, протирая |
|
исолянаяки- |
леза,30см3 соля- |
турунержавеющейстали |
шлиф, смоченнойвэтом |
слота |
нойкислоты, |
|
растворе, затемобмыть |
|
120см3 воды |
|
водойиспиртом |
|
Для травления высоколегированны сталей |
||
Солянокислый |
10г хлорного же- |
Выявляет структуру меди, |
|
раствор хлор- |
леза, 25см3 солянойлатуни, бронзы |
|
|
ного железа |
кислоты, 100см3 |
|
|
|
воды |
|
|
Аммиак и пере- |
Водныйраствор |
Выявляет структуру бро- |
|
кись водорода |
аммиака5частей, |
нзы, латуни, силумина |
|
|
перекись водорода |
|
|
|
2-5частей |
|
|
Фтористая ки- |
0,5см3 фтористой |
Хорошо выявляет струк- |
|
слота |
кислоты и 99,5 см3 |
туру дуралюмина и силу- |
|
|
воды |
мина |
|
Едкий натрий |
Едкий натрий I-10 |
То же |
|
|
частей, вода - 99-90 |
Для травления меди, мед- |
|
|
частей |
ных сплавов, алюминия и |
|
|
|
алюминиевых сплавов |
|
35

Схема отражения световых лучей от плоской и неровной поверхности
Рис. 4.5
III. ОБОРУДОВАНИЕ, ПРИБОРЫ И МАТЕРИАЛЫ
1.Металлографический микроскоп.
2.Образцы металлов и сплавов.
3.Шлифовальная бумага различных номеров.
4.Реактивы, щипцы, вата, спирт, фильтровальная бумага, фарфоровые или стеклянные ванночки.
IV. МЕТОДИЧЕСКИЕ УКАЗАНИЯ ПО ВЫПОЛНЕНИЮ РАБОТЫ
1.Образец готовится по рассмотренной ранее методике, см. п.2.2. Просматривается полученный нетравленный микрошлиф.
2.Подбирается реактив по табл. 4.2.
3.Травится шлиф, промывается проточной водой, сушится фильтровальной бумагой.
4.Просматривается травленный микрошлиф.
V. СОДЕРЖАНИЕ ОТЧЕТА
Вотчете должно быть включено:
1.Описание назначения и цели работы.
2.Списание основных операций приготовления микрошлифа.
36
3.Рисунки микроструктур до и после травления.
4.Заключение о выявленной структуре и пороках.
VI. ВОПРОСЫ ДЛЯ САМОПРОВЕРКИ.
1.В чем заключается микроскопический метод исследования?
2.Как отбирают образцы для исследований?
3.Как подготавливается образец к шлифовке?
4.Как производят шлифование образца?
5.Как производят полирование образца механическим способом?
6.Какие правила техники безопасности необходимо соблюдать при приготовлении шлифов?
37
ЛАБОРАТОРНАЯ РАБОТА № 5 ОПРЕДЕЛЕНИЕ ТВЕРДОСТИ МЕТАЛЛОВ И СПЛАВОВ
I. ЦЕЛЬ РАБОТЫ: изучить методы определения твердости материалов на различных типах твердомеров. Определить условия испытаний для конкретных образцов и материалов.
II. КРАТКИЕ ТЕОРЕТИЧЕСКИЕ СВЕДЕНИЯ.
Одним из широко распространенных видов испытаний металлов и сплавов является определение твердости. Под твердостью понимается способность материала сопротивляться проникновению в него другого более твердого тела. Твердость можно определять прямыми и косвенными методами.
Прямые методы испытания на твердость состоят в том, что в образец вдавливают специальный твердый наконечник различной формы. После снятия нагрузки остается отпечаток, величина которого характеризует твердость образца.
При косвенных методах оцениваются свойства металла, пропорциональные его твердости.
Испытания на твердость могут быть статическими - методом вдавливания и динамическими - методом ударного вдавливания.
Испытания статическим вдавливанием производятся наконечником в виде стального шарика, алмазного конуса или пирамиды, которые вдавливаются в испытуемый материал под постоянной нагрузкой, а твердость определяется по глубине отпечатка (диаметру, диагонали) или его площади.
Испытания динамическим вдавливанием производятся шариком или конусом, падающим с некоторой высоты на испытуемое тело, а твердость определяется по размерам отпечатка или энергии удара.
При испытании царапанием алмазным или стальным острием твердость определяется по ширине и глубине образующейся канавки.
При измерении твердости по методу отскока твердость определяется по высоте отскока стального шарика, падающего на поверхность испытуемого изделия с определенной высоты.
По величине твердости металлов иди сплавов можно судить о таких свойствах, как прочность, пластичность, износостойкость, Для многих материалов установлена математическая зависимость между твердостью и пределом прочности при растяжении.
Твердость определяется на специальных приборах - твердомерах. Твердомеры бывают стационарные и переносные. Принципиальное устройство твердомеров для всех методов испытаний на твердость одинакова.
38
Методы измерения твердости могут базироваться на совершенно разных принципах, различающихся по характеру воздействия (вдавливание, царапание, удар, отскок наконечника), как указывалось вше. Наконечник - индентор, изготавливается из малодеформирующегося материала (твердая закаленная сталь, алмаз, сапфир, твердый сплав) и имеющего форму шарика, конуса, пирамиды, иглы.
Для количественной оценки твердости наиболее широко применяют статическое вдавливание по нормали к испытываемой поверхности под заданной нагрузкой в течение определенного времени. Твердость характеризует сопротивление материалов местной пластической деформации и представляет собой механическое свойство металла, отличающееся от других его механических свойств способом измерения. На твердость можно испытывать весьма хрупкие материалы (чугун, твердые сплавы).
Измерение твердости перед другими механическими характеристиками имеет особенности:
1.При определении твердости деталь не разрушается, следы испытаний могут быть удалены.
2.Испытания на твердость отличаются простотой и высокой производительностью.
3.Определение твердости является единственно возможным методом испытания материалов, не поддающихся обработке резцом для вырезки образцов на разрыв (инструмент, твердые сплавы).
4.Можно измерять твердость мелких деталей и крупногабаритных изделий.
5.Твердость можно измерить на деталях небольшой толщины и в очень тонких слоях, не превышающих десятых долей миллиметра.
6.Зная твердость материала, можно судить о его износостойкости, прочности, пластичности. В ряде случаев ограничиваются определением твердости, не производя испытаний на растяжение.
Между временным сопротивлением ( σ8, МПа) и числам твердости HB существует следующая приближенная зависимость:
σ8 = К•НВ, где к - коэффициент.
Сталь твердостью HB: |
σ8, МПа |
120 - 175 |
3,4 HB |
175 - 450 |
3,5 HB |
Медь, латунь, бронза: |
|
после отжига |
5,5 HB |
после наклепа (ХПД) |
4,0 HB |
Алюминий и алюминиевые сплавы |
|
твердостью 20-45 HB |
(3,3-3,6) HB |
Дюралюмин: |
|
после отжига |
3,6 HB |
39

после закалки и старения |
3,5 HB |
Выбор формы, размеров наконечника и величины нагрузки зависят от целей испытания структуры, ожидаемых свойств, состояния поверхности и размеров испытуемого образца. Если металл имеет гетерогенную структуру с крупными выделениями отдельных структурных составляющих, различных по свойствам (серый чугун, цветные подшипниковые сплавы), то для испытаний выбирают шарик большого диаметра. Если металл имеет сравнительно мелкую и однородную структуру, то можно применять алмазный конус или пирамиду при небольшой нагрузке.
Для определения твердости отдельных зерен, фаз, структурных составляющих (а не "усредненную твердость", как при измерении макротвердости) проводят определение микротвердости при вдавливании алмазной пирамиды. Прилагаемая нагрузка выбирается небольшой (от I до 500 г). Микротвердость измеряют и для характеристики свойств очень малых по размерам деталей.
У полимерных материалов измерение твердости дает меньше информации об их свойствах, так как между твердостью и прочностью этих материалов нет определенной зависимости.
Значительное влияние на результаты испытаний твердости оказывает состояние поверхности измеряемого материала. Чем меньше нагрузка для вдавливания индентора, тем более тщательно должна быть подготовлена поверхность.
Твердость обозначается буквой Н (от английского слова hardness), затем буквой, обозначающей метод измерения твердости.
2.1. Измерение твердости по методу Бринелля В испытуемый образец или изделие под определенной нагрузкой (Р) в те-
чение заданного времени (t) вдавливают стальной закаленный шарик диаметром Д, мм. После снятия нагрузки на поверхности образца остается сферический отпечаток диаметром d, мм (рис. 5.1).
Диаметр шарика Д выбирают в зависимости от толщины испытуемого образца, а нагрузку Р - от твердости материала по ГОСТ 9012-59. При испытаниях продолжительность приложения нагрузки и время выдержки должно быть строго определенным (10-60 с ).
Твердость по Бринеллю определяется по формуле:
если нагрузка Р выражена в кгс (килограмм-силе).
На практике пользуются готовыми таблицами с заранее подсчитанными значениями твердости для отпечатков различных диаметров, полученных при
40

Схема испытания твердости методом вдавливания стального шарика (способ Бринелля)
Рис. 5.1
разных нагрузках.
Измерение твердости по методу Бринелля не является универсальным методом. Этот способ не рекомендуется применять для стали с твердостью более 450 HB; а для цветных металлов - более 200 HB. По Бринеллю нельзя испытывать образцы после химико-термической обработки (цементация, азотирование и т.п.) из-за малой толщины азотируемого или цементированного слоя, а также мелкие детали.
Метод отличается недостаточной точностью измерения диаметра отпечатка (до 0,1 мм), так как замер производится с помощью лупы (рис. 5.2).
Схема измерения диаметра отпечатка
Рис, 5.2
41

2.2. Определение твердости способом Роквелла
Измерение твердости по способу Роквелла состоит в том, что ее измеряют по глубине отпечатка, получаемого в результате вдавливания наконечника с инденторами - алмазного конуса с углом при вершине α, равным 120º (шкалы А и С), или стального шарика диаметром 1,5875мм (шкала В) в испытуемый образец (изделие) под действием последовательно прилагаемой предварительной Fo (Po) - 10 кгс и основной F (Р) нагрузок на глубину ho и h соответственно (рис. 5.3).
Схема испытания твердости методом вдавливания алмазного конуса (способ Роквелла)
а- предварительная нагрузка;
б- окончательная нагрузка
Рис. 5.3
За меру твердости принимается разность .между глубиной отпечатков (ho
-h), причем внедрение наконечника в испытуемый материал на 0,002 мм соответствует перемещению стрелки на одно деление шкалы индикатора (рис.5.4). Индикатор прибора имеет две шкалы: черную (С) - для испытания с алмазным конусом, красную (В) - для испытания шариком.
Величину нагрузки (Р), тип наконечника выбирают по табл. 5.1 в зависимости от твердости испытуемого материала.
Шарик (шкала В) применяют для определения твердости мягкой (отоженной) стали, отоженных цветных металлов в образцах или деталих толщиной 0,8
-2 мм.
42

Схема индикаторной шкалы прибора Роквелла
а – установка шкалы в начале измерения; б - промежуточный этап; в - результат измерения
|
|
Рис.. 5.4 |
|
|
||
|
|
|
|
|
Таблица 5.1 |
|
|
|
|
|
|
|
|
Примерная |
Обозначе |
Тип |
Нагрузка |
Допускаемые |
Обозначение |
|
твердость по |
ние |
пределы |
||||
шкалы |
наконечника |
Р, кгс |
измерения по |
твердости |
||
Виккерсу, МПа |
Роквелла |
|
|
Роквеллу |
|
|
|
|
|
|
|||
|
|
|
|
|
|
|
600-2400 |
В |
Шарик |
100 |
25-100 |
HRB |
|
стальной |
||||||
|
|
|
|
|
||
2400-7000 |
С |
Алмазный |
150 |
20-67 |
HRC |
|
конус |
||||||
|
|
|
|
|
||
3800-9000 |
А |
Алмазный |
60 |
70-85 |
HRA |
|
конус |
||||||
|
|
|
|
|
Алмазный конус (шкала С) применяют для замера твердости закаленной или низкоотпущенной стали; для материалов средней твердости (более 240 HB); для определения твердости тонких поверхностных слоев, например, цементованного слоя, но толщиной более 0,5 мм.
Измерения алмазным конусом с нагрузкой 60 кГс (шкала А) применяют для очень твердых материалов (более 70 HRC), например, твердых сплавов, когда вдавливание с большой нагрузкой может вызвать выкрашивание алмаза, а
43

также для измерения твердых поверхностных слоев (0,3-0,5 мм), тонкого твердого листового материала.
HRC = 2HRA – 104
В связи с изменением эталона по ГОСТ 8.064-79 в измеряемых значениях твердости (шкала С) внесена поправка. Твердость обозначается HRC3, значения которой больше, чем HRC. Для пересчета пользуются специальными таблицами.
Большим преимуществом способа Роквелла является быстрота испытаний (30-60 сек), причем результат читается непосредственно на шкале прибора. На поверхности детали остается столь малый отпечаток, что при необходимости его можно легко снять.
2.3. Определение твердости по Виккерсу
Твердость материалов определяют вдавливанием под действием нагрузки Р в течение определенного времени (обычно 15 с) в образец правильной четырехгранной пирамиды с углом между гранями, равным 136º (ГОСТ 2999-75) –
рис. 5.5.
Величину нагрузки выбирают в зависимости от типа сплава в диапазоне от I до 100 кГс.
Схема измерения твердости по Виккерсу
1 – левый винт; 2 - микрометрический винт
Рис. 5.5.
44

Этот метод измерения твердости применим как к мягким, так и к твердым материалам. Широкое распространение он получил при испытании очень твердых образцов и изделий, имеющих малые сечения, а также для испытания твердости тонких поверхностных (толщиной 0,03-0,05 мм) цементированных, азотированных, хромированных слоев. Метод Виккерса дает высокую точность при измерении твердости (длина диагонали отпечатка замеряется с точностью до 0,001 мм с помощью микроскопа - рис. 5.5).
Полученные числа твердости почти полностью совпадают с числом твердости HB, т.е. HB = HV при значениях твердости до HB = 4500 МПа.
При замере твердости поверхность образца должна быть тщательно отшлифована или даже отполирована.
Для замера твердости отдельных фаз и структурных составляющих сплавов - микротвердости применяют прибор ПМГ-3 (ГОСТ 9450-75).
III. ОБОРУДОВАНИЕ, ПРИБОРЫ И МАТЕРИАЛЫ
Твердомеры Бринелля, Роквелла, Виккерса. Лупа к твердомеру Бринелля. Набор образцов различных металлов и сплавов, пластмасс. Таблицы для определения твердости по Бринеллю, Виккерсу.
IV. МЕТОДИЧЕСКИЕ УКАЗАНИЯ К ВЫПОЛНЕНИЮ РАБОТЫ
1.Студенты знакомятся с техникой определения твердости на перечисленных выше приборах.
2.Каждый студент измеряет твердость образцов комплекта материалов, выданных преподавателем, по Бринеллю, Роквеллу и Виккерсу.
3.Результаты испытаний заносятся в таблицу 5.2-5.4.
Таблица 5.2
Результаты измерения твердости по методу Бринелля
|
|
|
|
Диаметр отпечатков |
Твердость по Бри- |
||||
|
Условия испытаний |
неллю HB, МПа |
|||||||
Материал |
|
|
|
|
d, мм (м) |
(кГс/мм2) |
|||
образца |
нагрузка |
диаметр |
время |
|
|
|
|
|
|
|
шарика Д, |
1 |
2 |
3 |
сред. |
по формуле |
по таблице |
||
|
Р, кГс (Н) |
мм |
t,c |
|
|
|
|
|
|
|
|
|
|
|
|
|
|
|
|
|
|
|
|
|
|
|
|
|
|
45

|
Результаты измерения твердости по методу Роквелла |
Таблица 5.3 |
|
|||||||||||||||||
|
|
|
||||||||||||||||||
|
|
|
|
|
|
|
|
|
|
|
|
|
|
|
|
|
|
|
|
|
|
Инден- |
|
Нагрузка |
|
|
|
|
|
Обозна- |
Число твердости |
|
Твердость по |
|
|||||||
Материал |
|
Р,кГс, |
|
Шкала |
|
чение |
|
по Роквеллу |
|
Бринеллю HB |
|
|||||||||
|
тор |
|
(Н) |
|
|
|
|
твердоcти |
|
|
|
|
|
|
МПа (кГ с/мм2) |
|
||||
|
|
|
|
I |
|
|
2 |
3 |
Сред. |
|
||||||||||
|
|
|
|
|
|
|
|
|
|
|
|
|
|
|
|
|
|
|
|
|
|
Результаты измерения твердости по методу Виккерса |
Таблица 6.4 |
|
|||||||||||||||||
|
|
|
||||||||||||||||||
|
|
|
|
|
|
|
|
|
|
|
|
|
|
Твердость |
|
|||||
Материал |
Инден- |
|
Нагрузка |
|
Длина диагонали |
|
|
|
|
|
||||||||||
|
|
отпечатка мм (м) |
|
|
по Виккерсу |
по Бринеллю |
|
|||||||||||||
образца |
тор |
|
Р, кГс (Н) |
|
|
|
|
|
|
|
|
|
HV, МПа |
НВ, МПа |
|
|||||
I |
|
2 |
|
3 |
сред. |
|
|
|||||||||||||
|
|
|
|
|
|
|
|
|
(кГс/мм2) |
(кГс/мм2) |
|
|||||||||
|
|
|
|
|
|
|
|
|
|
|
|
|
|
|
|
|
|
|
|
|
V. СОДЕРЖАНИЕ ОТЧЕТА
1.Назначение и цель работы.
2.Краткое описание основных методов измерения твердости (Бринелля, Роквелла, Виккерса).
3.Таблицы результатов испытаний.
4.Выводы.
VI. ВОПРОСЫ ДЛЯ САМОКОНТРОЛЯ
1.Какие существуют виды механических испытаний?
2.В чем заключаются испытания на твердость?
3.Как проводят измерения твердости по Бринеллю?
4.В чем сущность метода Роквелла?
5.Особенности определения твердости по методу Виккерса?
6.Назовите характеристики прочности металла?
7.Что такое твердость?
8.Каким способом можно измерить твердость детали после химико-термичес- кой обработки, пластмасс, "мягких" металлических сплавов?
46
ЛАБОРАТОРНАЯ РАБОТА № 6 ПОСТРОЕНИЕ ДИАГРАММЫ СОСТОЯНИЯ СИСТЕМ СПЛАВОВ
МЕТОДОМ ТЕРМИЧЕСКОГО АНАЛИЗА
I. ЦЕЛЬ РАБОТЫ: ознакомиться с принципом действия термоэлектрического пирометра; научиться самостоятельно строить кривые охлаждения (нагрева) металлов и сплавов, по этим кривым определять критические температуры; при помощи критических температур построить диаграмму состояния сплавов.
II. КРАТКИЕ ТЕОРЕТИЧЕСКИЕ СВЕДЕНИЯ
Основной задачей современного металловедения является изучение строения и свойств сплавов в зависимости от концентрации и температуры. Закономерности строения сплавов описывают с помощью диаграмм состояния или диаграмм фазового равновесия. Диаграммы фазового равновесия в удобной графической форме показывают фазовый состав и структуру сплавов в зависимости от температуры и концентрации. Диаграммы строят в условиях равновесия или достаточно близких к ним. Равновесное или стабильное состояние соответствует минимальному значению свободной энергии. Оно достигается очень малыми скоростями охлаждения или нагревания. Равновесное состояние сплава зависит от внешних условий (температура, давление) и характеризуется числом и концентрацией образовавшихся фаз.
Правило фаз дает количественную зависимость между степенью свободы системы и количеством фаз и компонентов. Компонент - составная часть сплава. Взаимодействие компонентов приводит к образованию фаз (иногда компоненты могут являться фазами).
Фаза - однородная часть системы, отделенная от других частей системы поверхностью раздела, при переходе через которую химический состав и структура сплава изменяются скачком.
Правило фаз записывается в виде уравнения:
|
С = К + I – Ф , |
где С – |
степень свободы системы; |
К – |
количество компонентов; |
Ф – |
количество фаз; |
I – |
независимая переменная. |
Под степенью свободы "С" системы понимают число независимых переменных, которое можно изменять без изменения числа фаз в системе.
47
Это уравнение применяют к металлическим системам равновесия, считая давление во всех процессах неизменным,
2.1. Основные методы построения диаграмм состояния сплавов
Независимо от того, каким способом строятся диаграммы состояния сплавов, цель каждого метода - определить критические температуры сплавов при нагревании или охлаждении.
Критическими температурами называются такие температуры, при которых начинаются или заканчиваются любые химические или физические изменения в исследуемом сплаве.
Дилатометрический метод. Этот метод основан на регистрации изменений объема при структурных превращениях, так как различные структуры металлов и сплавов имеют различный удельный объем. Регистрируются изменения длины образца при изменении температуры. Когда в сплаве начинаются структурные превращения, кривая удлинения образца загибается. Эта кривая загибается значительно, когда удельный объем образовавшейся новой структуры значительно отличается от объема прежней структуры.
Метод электрического сопротивления. При изменении структуры сплава изменяется и его сопротивление. При регистрации изменения сопротивления, в зависимости от температуры сплава, можно определить его критические температуры. Этим методом исследуются сплавы в твердом состоянии.
Магнитометрический метод. Во время структурных превращений измеряются изменения магнитных свойств.
Метод закалки. При резком охлаждении исследуемого образца, нагретого до определенной температуры, не успевают произойти процессы диффузии атомов (ионов) компонентов в сплаве. После резкого охлаждения (закалки) исследуется структура образца или измеряется его твердость. Если образец был закален после нагрева выше критических температур, то соответственно изменяется его микроструктура и твердость.
Металлографический метод. Выплавляют сплавы исследуемых концентраций и исследуют их микроструктуру при высоких температурах, используя специальные микроскопы.
Термический метод. Каждое превращение в металле и сплаве (плавление при нагреве, кристаллизация при охлаждении, изменение кристаллического строения в твердом состоянии) сопровождается поглощением теплоты при нагреве и выделением при охлаждении. Это явление используется для построения диаграмм состояния сплавов. Для этого строятся кривые охлаждения или нагрева сплавов разных концентраций. На кривых находят критические точки, по которым строится диаграмма состояния сплавов. Термический метод является
48
простым, он позволяет рассматривать и процесс кристаллизации сплавов, а вышеизложенные методы применяются для исследования металлов и сплавов только в твердом состоянии.
Кроме вышеперечисленных существуют и другие методы: рентгенографический, электроннографический, метод внутреннего трения и другие.
В настоящей работе более подробно рассматривается термический метод. Термоэлектрические пирометры. Ртутные термометры позволяют измерять температуру только до 600°С, поэтому их применение для построения диаграмм состояния сплавов ограничено. Для построения кривых нагрева и охлаж-
дения широко используются термоэлектрические пирометры, которые позволяют измерять температуру до 2400-2800º С. Термоэлектрический пирометр состоит из термопары и гальванометра (рис. 6.1).
Термопара состоит из двух проволок различных металлов (термоэлектродов), сплавленных в одном конце. Свободные концы термопары соединительными проводами подключаются к гальванометру. При нагреве спая термопары в цепи термоэлектрического пирометра образуется электродвижущая сила (э.д.с.). Образовавшееся незначительное напряжение регистрируется гальванометром.
Создаваемая термопарой э.д.с. зависит от состава ее термоэлектродов (проволоки термопары). Термоэлектроды изготавливаются из меди, железа,
константана (58,5% Си + 1,5% Мп + 40% Ni), копеля (56% Си + 44% Ni), алю-
меля (95% Ni + 2% Al + 2% Мп + I% Si), платины и других сплавов. (Основные характеристики термопар даны в табл. 6.1).
Из представленных данных видно, что низкие температуры целесообразно измерять хромель-копелевыми термопарами, так как создают большую э.д.е., что уменьшает погрешность измерения. Термопары на основе платины используются для измерения только высоких температур, так как при измерении низких температур они не обеспечивают высокой точности.
Гальванометр состоит из постоянного магнита, между полюсами которого помещена рамка на оси. На рамку намотана катушка из тонкого алюминиевого провода (рис.6.2). При протекании по проводу термоэлектрического тока вокруг катушки образуется магнитное поле, которое под воздействием магнитного поля постоянного магнита создает момент кручения. Под воздействием этого момента катушка поворачивается, а вместе с ней отклоняется и прикрепленная на рамке стрелка. Величина отклонения стрелки отчитывается на шкале, указывающей напряжение (в милливольтах) или температуру (в°С). Шкала может быть и двойной,
49

|
|
Техническая характеристика термопар |
|
Таблица 6.1 |
|||
|
|
|
|
||||
|
|
|
|
|
|
|
|
|
|
|
|
Верхний температурный |
Чувствительность, |
Термо э.д.с. |
|
|
Т и п |
|
Градуировка |
предел измерения, ºС |
|||
|
|
длительного |
кратковре- |
мВ/°С |
мВ |
||
|
|
|
|
||||
|
|
|
|
|
|||
|
|
|
|
|
менного |
|
|
|
Медь-константановая |
|
М1) |
400 |
- |
0,015-0,04 |
20 |
Хромель-копелевая ТХК |
|
ХК |
600 |
800 |
0,08 |
66,40 |
|
Хромель-алюмелевая ТХА |
|
XA |
1000 |
1300 |
0,04 |
52,41 |
|
Платинородий-платиновая ТПП |
|
ПП-1 |
1300 |
1600 |
0,01 |
16,72 |
|
Платинородий-платинородиевая ТПР |
|
ПР-30/6 |
1600 |
1800 |
0,01 |
13,927 |
|
Вольфрам-молибденовая ТВМ |
- |
1800 |
- |
0,015-0,04 |
20 |
||
Вольфрам-рениевая ТВР |
|
ВР-5/202) |
2200 |
2500 |
0,01-0,015 |
31,45 |
|
|
|
|
|
|
|
|
|
________________
1)Нестандартная термопара.
2)Используется только в вакууме или в защитной атмосфере.
50

Схема пирометра
Рис.6.1
Схема милливольтметра
Рис 6.2.
Градуировочная кривая хромельалюмелевой Термопары
Рис. 6.3
51

когда одновременно можно отчитывать милливольты и градусы.
Если гальванометр имеет только одну шкалу (мВ), температура определяется при помощи градуированной кривой. Приблизительную градуировочную кривую можно построить по данным табл. 6.2, но здесь не учитвается погрешность гальванометра. Более точная градуировочная кривая строится экспериментальным методом. Для этой цели применяются чистые металлы, точные температуры плавления которых известны, например, олова - 231,85ºС, свинца - 327,3ºС, цинка - 419,4ºС, сурьмы - 630°С, серебра - 960ºС и т.д. С помощью специальной установки определяется, при каких показаниях гальванометра кристаллизуются (плавятся) подобранные металлы. По данным такого эксперимента строится градуировочная кривая (рис. 6.3). Описание установки и методика определения критических температур дается далее. Градуировать можно и точной контрольной термопарой.
|
Электродвижущая сила (мВ) термопар в зависимости |
Таблица 6.2 |
||||
|
|
|||||
|
|
|
от температуры |
|
|
|
|
|
|
|
|
|
|
Температура, |
|
|
Термопара |
|
|
|
ºС t |
|
|
|
|
|
|
|
ПП-I |
ПР-30/6 |
XA |
XK |
M |
|
100 |
|
0 |
0 |
0 |
0 |
0 |
0,643 |
- |
4,10 |
6,95 |
14,16 |
||
200 |
|
I 436 |
- |
8,13 |
14,66 |
8,87 |
300 |
2,314 |
0,456 |
12,21 |
22,91 |
14,13 |
|
400 |
3,249 |
0,812 |
16,46 |
31,49 |
20,04 |
|
500 |
4,218 |
1,268 |
20,65 |
40,16 |
26,19 |
|
600 |
5,220 |
1,821 |
24 91 |
49,02 |
- |
|
700 |
6,256 |
2,467 |
29,15 |
57,77 |
- |
|
800 |
7,325 |
3,201 |
33,32 |
66,42 |
- |
|
900 |
8,428 |
4,019 |
37,37 |
- |
- |
|
1000 |
9,564 |
4,913 |
41,32 |
- |
- |
|
1100 |
10,732 |
5,876 |
45,16 |
- |
- |
|
1200 |
11,923 |
6,902 |
48,87 |
- |
- |
|
1300 |
13,129 |
7,982 |
52,43 |
- |
- |
|
1400 |
14,398 |
9,109 |
- |
- |
- |
|
1500 |
15,597 |
10,274 |
- |
- |
- |
|
1600 |
16,714 |
11,741 |
- |
- |
- |
|
1800 |
- |
13,927 |
- |
- |
- |
2.2. Установкадляопределениякритическихтемпературметалловисплавов
Установка состоит из электропечи, термопары с гальванометром и термостата. Исследуемый металл плавится в тигле I, помещенном в лабораторную шахтную печь 2. Для защиты расплавленного металла 3 от окисления его поверхность покрывается измельченным древесным углем, рис. 6.4.
52
В расплавленный металл осторожно погружается термопара 4 с защитным кожухом. Термопара подсоединяется к гальванометру 5, который будет показывать э.д.е., соответствующую разности температур между спаем и свободными концами термопары. Поэтому очень важно, чтобы свободные концы термопары, к которым подсоединяются провода, идущие к гальванометру, все время сохраняли постоянную температуру. Для этого свободные концы термопары помещаются в термостат с таящим льдом или водой комнатной температуры. Когда применяется термостат с водой, к отсчитанной температуре металла необходимо добавить температуру воды.
Пример. Измеряется температура расплавленного металла. Холодные концы термопары ХА помещаются в термостат с водой, температура которой 20ºС. Гальванометр показывает э.д.с. 24,9 мВ. Из табл.6.2 видно, что такая э.д.с. соответствует температуре 600°С. Учитывая температуру воды термостата, получаем, что температура расплавленного металла – 620ºС.
Очень часто из-за небольшой длины термопары невозможно ее свободные концы поместить в термостат. Тогда к термопаре присоединяются провода, имеющие такие же термоэлектрические свойства, как и электроды. Они называются компенсационными проводами. Например, для термопары ПП-1 один компенсационный провод изготовляется из меди, а другой из сплава, состоящего из 99,4% Си и 0,6% Ni. Компенсационными проводами могут служить и материалы, из которых изготовлены электроды термопар.
Используя компенсационные провода, термостат можно установить в удалении от электропечи. Если компенсационные провода подсоединяются, как показано на рис .6.4, в термостат 6 достаточно погружать только одно соединение проводов.
2.3. Построение кривых охлаждения металлов и сплавов и определение критических температур
Для построения кривой охлаждения в тигле расплавляются 150-200г исследуемого металла или сплава. После этого в расплавленный металл осторожно погружается термопара с защитным кожухом. Температуру расплавленного металла необходимо повысить еще на 50-80°С и после этого выключить нагревательную печь. Когда жидкий металл в тигле начинает остывать, через каждые 0,5 мин записываются показания гальванометра. Через 3-4 мин после полного затвердения металла или сплава регистрация показаний гальванометра прекращается.
Если показания гальванометра записывались в милливольтах, соответствующие значения температуры определяются с помощью градуировочной
53

Схема установки для определения критических температур металлов и сплавов
Рис. 6.4
Кривые охлаждения
Рис.6.5
54
кривой. По данным эксперимента строится кривая охлаждения в координатах температура-время (рис.6.5).
Как видно из рис.6.5а, при охлаждении расплавленного чистого металла с достижением температуры кристаллизации наблюдается остановка падения температуры, т.е. на кривой охлаждения образуется горизонтальная ступенька. Когда металл кристаллизуется, выделяется скрытая теплота кристаллизации, которая и поддерживает температуру постоянной, хотя теплота непрерывно отводится в окружающую среду. Скрытая теплота кристаллизации - это количество тепла, которое придает атомам металла необходимую энергию колебания при плавлении металла, т.е то тепло, которое используется для "разрушения" кристаллической решетки при плавлении. По уровню горизонтальной ступеньки на кривой охлаждения (нагревания) можно точно определить температуру кристаллизации (плавления) чистых металлов. Точность определения температуры кристаллизации (плавления) зависит и от скорости охлаждения (нагревания). Например, при охлаждении расплавленного металла с большой скоростью температура его кристаллизации может понизиться на 10-20ºС. Поэтому при определении кривых охлаждения металлов и сплавов тигель охлаждается медленно.
Некоторые сплавы определенного состава имеют кривые охлаждения, подобные кривым охлаждения чистых металлов. Такие сплавы, образующие механические смеси, называются эвтектиками. Например, сплав, состоящий из 87% свинца и 13% сурьмы, кристаллизуется при температуре 246ºС. На кривой охлаждения такого сплава наблюдается только горизонтальная ступенька, как и у чистых металлов. Характерно, что температура плавления эвтектики всегда ниже температуры плавления компонентов, образующих эвтектику. Например, температура плавления свинца - 327°С, сурьмы - 631°С, а эвтектики, состоящей из 87% Pb и 13% Sb - 246ºС. Это свойство используется при создании легкоплавких сплавов. В микроструктуре эвтектических сплавов наблюдается упорядоченное расположение компонентов.
Сплавы, состав которых отличается от эвтектического, кристаллизуются в температурном интервале, поэтому и характер кривых их охлаждения отличается от характера кривых охлаждения чистых металлов. Например, кривая охлаждения сплава, состоящего из 99% Pb и 5% Sb, показана на рис.6.5б. Состав этого сплава не соответствует эвтектическому, так как вместо Sb 13% в нем есть только 5% Sb. Значит в таком сплаве есть избыток свинца. При охлаждении его до температуры 296°С, из расплава начинает выделяться избыточная фаза - кристаллы свинца. Вначале выделяется только незначительное количество кристаллов. При понижении температуры сплава, увеличивается количество и размерыткристаллов. Состав жидкой фазы, с выделением кристаллов,
55
свинца, приближается к эвтектическому. Одновременно с кристаллизацией свинца выделяется и скрытая теплота кристаллизации, которая замедляет охлаждение сплава. Поэтому от температуры 296ºС сплав охлаждается медленнее, на кривой охлаждения наблюдается изменение ее наклона. Когда сплав остывает до 246°С, заканчивается выделение кристаллов избыточного свинца, и состав жидкой фазы соответствует эвтектическому. Поэтому на кривой охлаждения получается горизонтальная ступенька - кристаллизуется оставшаяся жидкая фаза, образуя эвтектику. После полного затвердевания сплава его структура состоит из крупных темных зерен свинца, которые образовались между 296 и 246°С, и из мелкой смеси темных и светлых зерен (Pb и Sb) эвтектики, которая образовалась при температуре 246ºС.
При охлаждении сплавов с избытком сурьмы получаются аналогические кривые охлаждения. Но в этих сплавах из жидкой фазы вначале выделяются кристаллы сурьмы (избыточная фаза). Эвтектика таких сплавов также кристаллизуется при 246°С. В микроструктуре видны крупные светлые зерна сурьмы (избыточная фаза) и мелкая смесь зерен Pb и Sb – эвтектика. Количество эвтектики зависит от состава сплава.
2.4. Построение диаграмм состояния сплавов
Для построения диаграмм состояния двойных сплавов термическим методом строятся кривые охлаждения обеих компонентов и нескольких их сплавов. При увеличении числа исследуемых сплавов точность построения диаграммы увеличивается. Например, при построении диаграммы состояния сплавов свинец-сурьма необходимо построить кривые охлаждения для свинца и сурьмы и для нескольких их сплавов, имеющих разное соотношение обеих компонентов. Можно подобрать сплавы с 5, 13 и 40% Sb. Схематически построение кривых охлаждения таких металлов и сплавов показано на левой части рисунка 6.6. На кривых охлаждения находят критические точки, соответствующие началу и концу кристаллизации.
При построении диаграммы состояния сплавов на оси абсцисс, которая еще называется осью концентраций, откладываются концентрации одного из компонентов. Количество второго компонента дополняет сплав до 100%. На оси ординат откладываются температуры.
На оси концентраций, от точек, соответствующих составам сплавов, поднимаются перпендикуляры - линии сплавов. В правой части рисунка 6.6 линии сплавов обозначены теми же буквами, как и сплавы (a, b, c, d, e). На каждую линию сплава от соответствующей кривой охлаждения переносятся критические точки.
Соединив точки, соответствующие началу кристаллизации, получаем ли-
56
нию ABC, выше которой все сплавы находятся в жидком состоянии. Поэтому эта линия называется линией ликвидуса (от лат. liquidus – жидкий).
Соединив точки, соответствующие концу кристаллизации, получаем линию ВС. Ниже этой линии все сплавы находятся в твердом состоянии, поэтому она называется линией солидуса ( от лат. solidus – твердый). Она также называется эвтектической линией.
Построенная диаграмма называется диаграммой состояния сплавов сви- нец-сурьмах.
Аналогично строятся диаграммы и для сплавов, образующих твердые растворы, однако кривые охлаждения этих сплавов не имеют горизонтальных ступенек.
С началом кристаллизации охлаждение сплава замедляется, т.е. угол падения кривой уменьшается. По окончании кристаллизации охлаждение сплава опять ускоряется, угол падения кривой увеличивается.
Диаграммы состояния сплавов могут быть построены и по кривым нагрева. Для этого необходимо заранее в расплавленный исследуемый сплав на соответствующую глубину погрузить термопару с защитным кожухом и дать сплаву затвердеть.
Диаграммы состояния сплавов позволяют заранее прогнозировать, какие превращения произойдут в данном сплаве при нагреве и охлаждении, подбирать сплавы с хорошими литейными свойствами, подобрать оптимальные режимы термической и термохимической обработки, в некоторых случаях позволяют определить химический состав сплава по его микроструктуре и т.д.
III.ОБОРУДОВАНИЕ, ПРИБОРЫ И МАТЕРИАЛЫ
1.Установка для определения критических температур металлов и сплавов.
2.Секундомер.
3.Металлографический микроскоп МИМ-7.
4.Весы с разновесами.
5.Набор микрошлифов сплавов данной системы.
6.Металлы чистые или приготовленные сплавы с определенной концентрацией.
__________________
На рис.6.6 показана упрощенная диаграмма состояния сплавов свинецсурьма. При построении диаграммы условно принято, что свинец и сурьма не растворяются друг в друге. На самом деле они незначительно растворяются.
57

IV. МЕТОДИЧЕСКИЕ УКАЗАНИЯ ПО ВЫПОЛНЕНИЮ РАБОТЫ
1.Взвесить на весах определенное количество металла или сплава, заданного преподавателем.
2.Поместить приготовленный металл или сплав в установку для определения критических температур.
3.Включить установку в сеть, произвести нагрев до температур, заданных преподавателем.
4.По достижении заданной температуры отключить установку и снимать показания температуры через каждые 5-10 с.
5.Запись температуры прекратить после охлаждения сплава или металла ниже конца кристаллизации.
6.Построить кривую охлаждения заданного сплава или металла в осях "Темпе- ратура-время".
7.Определить на кривой охлаждения температуры начала и конца кристаллизации для данного сплава.
8.Данные свести в сводную табл.б.3.
|
|
|
|
Таблица 6.3 |
|
|
|
|
|
Микро- |
|
Состав |
Начало кристал- |
Конец кристал- |
Тип |
Примеча- |
|
сплава |
лизации |
лизации |
сплава |
структура |
ние |
|
|
|
|
|
|
9.Построить сводный график охлаждения сплавов и металлов на основании данных табл. 6.3.
10.Выполнить построение диаграммы состояния сплавов по методике V. СОДЕРЖАНИЕ ОТЧЕТА
Отчет должен содержать в себе ряд теоретических сведений; схему установки; сводную таблицу результатов; схему построения диаграммы состояния системы сплавов по кривым охлаждения с указанием структурных составляющих в каждой области диаграммы; рисунки микроструктур с обозначением структурных составляющих.
VI. ВОПРОСЫ ДЛЯ САМОПРОВЕРКИ
1.Что такое сплав, компонент, фаза, система сплавов, диаграмма?
2.Основные типы сплавов, образуемые при взаимодействии компонентов.
3.Основные типы диаграмм равновесного состояния.
4.Правило фаз и правило отрезков.
5.Что называется критическими точками?
58

6.Основные методы построения диаграммы состояния.
7.Принцип построения кривых охлаждения и диаграмм состояния систем сплавов.
8.Что такое ликвидус, солидус?
9.Дать определение эвтектики и эвтектической реакции.
10.Дать определение эвтектическому, доэвтектическому и заэвтектическому сплавам.
11.Особенности кристаллизации эвтектического сплава и сплава твердого раствора.
12.Построение кривых охлаждения с применением имеющейся диаграммы и правил отрезков и фаз.
Построение диаграммы состояния сплавов свинец-сурьма
Рис. 6.6
59
ЛАБОРАТОРНАЯ РАБОТА № 7 ОПРЕДЕЛЕНИЕ ВЕЛИЧИНЫ ЗЕРНА В СТАЛИ
I. ЦЕЛЬ РАБОТЫ: освоить методы определения величины зерна, установить зависимость свойств стали от величины зерна.
II.КРАТКИЕ ТЕОРЕТИЧЕСКИЕ СВЕДЕНИЯ:
Металлы, в том числе сталь, как тела поликристаллические; состоят из зерен. Размеры зерна стали определяются характером и технологией ее производства (температура литья, скорости разливки, охлаждения в форме и т.д.), а также различными видами последующих обработок: горячая деформация и термообработка.
Одной из важнейших структурных и технологических характеристик углеродистых и легированных сталей, претерпевающих при нагревании превращение в аустенит, является размер зерна аустенита. Различают начальное, наследственное (или природное) и действительное зерно аустенита.
Зерно аустенита, образовавшееся по завершении фазовой перекристаллизации доэвтектоидных сталей в точке Ac3, а эвтектоидных и заэвтектоидных сталей в точке Ас1, называется начальным зерном аустенита ( dH, рис. 7.1). Так как кристаллы аустенита зарождаются преимущественно на межфазных поверхностях феррита и цементита и на границах исходных зерен (dисх, рис. 7.1), то чем дисперснее феррито-цементитная смесь и мельче исходные зерна феррита и перлита, тем мельче начальное зерно аустенита. Обычно его диаметр не превышает 10-20 µkµ и дополнительно уменьшается при увеличении скорости нагрева.
Дальнейшее нагревание сталей выше критических точек Ас3 и Ас1 и (в меньшей мере ) увеличение времени выдержки при этих температурах приводит к росту начальных мелких зерен аустенита вследствие собирательной рекристаллизации. Для характеристики скорости их роста вводится понятие наследственного зерна аустенита. Стали, в которых зерно аустенита начинает быстро расти уже при незначительном превышении критических точек, называются наследственно крупнозернистыми (НКЗ) - (рис. 7.1, линия I). Стали, в которых зерна аустенита остаются мелкими до высоких температур, значительно превышающих критические точки, называются наследственно мелкозернистыми (НМЗ) (рис. 7.1 линия 2).
60

Увеличение размера зерна аустенита эвтектоидной стали при нагревании от точки Ac1
Рис. 7.1 1 – наследственно крупнозернистая сталь;
2 – наследственно мелкозернистая сталь; dисх – диметр исходного зерна перлита; dН – диаметр начального зерна аустенита
Скорость роста зерен аустенита зависит от химического состава и технологической предистории (наследственности) стали. Так, стали раскисленные Mn ( кипящие ) являются НКЗ. Дополнительное раскисление алюминием (спокойные стали) делает их НМЗ, так как образующиеся дисперсные оксида и нитриды алюминия, располагаясь по границам зерен аустенита, препятствуют их росту (перемещению границ) вплоть до высоких температур. Однако, начиная с температур 1000 - 1050ºС, эти химические соединения коагулируют или растворяются в γ – твердом растворе и перестают оказывать свое сдерживающее влияние: зерна аустенита в НМЗ стали могут даже стать крупнее, чем в НКЗ стали. Аналогичен механизм тормозящего влияния (барьерная функция) на рост зерен аустенита тех легирующих элементов (Nb, Ti, Zr,V и в меньшей степени W, Mo, Cr ), которые образуют стабильные при высоких температурах карбиды, нитриды, карбонитриды.
61
В литой стали зерна аустенита менее склонны к укрупнению при нагреве, чем в горячедеформированной, так как в последней карбиды, карбонитриды, нитриды, оксиды в процессе горячей пластической деформации перераспределяются с границ зерен и частично коагулируют и растворяются.
Экспериментально установлено, что Mn, Si, В и Р увеличивают скорость роста аустенитных зерен.
Наследственное зерно в значительной степени определяет температурные режимы горячей обработки. Так как НМЗ стали устойчивы к перегреву, то они могут нагреваться при термической обработке в более широком диапазоне температур и обрабатываться давлением при более высоких температурах, чем в НКЗ стали.
Фактическое зерно аустенита, образовавшееся при данных температурновременных условиях обработки стали обеспечивающее величину зерна в готовых изделиях, называется действительным зерном. Именно оно оказывает влияние на свойства стали. Так, стали с крупным действительным зерном аустенита прокаливаются на большую глубину; более склонны к короблению и образованию трещин от внутренних напряжений при термической обработке, литье, сварке; при их ускоренном охлаждении может возникнуть видманштетова структура с низким уровнем ударной вязкости.
Мелкозернистые стали имеют более высокую прочность, пластичность, ударную вязкость, более низкую критическую температуру хрупкости и меньшую чувствительность к концентраторам напряжений. Большинство деталей машин работает в сложных условиях, воспринимая одновременно нагрузки на изгиб, кручение, растяжение и другие знакопеременные нагрузки. Для таких деталей необходимо применять мелкозернистую сталь, которая лучше штампуется в холодном состоянии. Протяжки из мелкозернистой стали менее склонны к поводке и короблению при закалке, чем протяжки из крупнозернистой стали. Для изготовления же крупных сверл (диаметром 20 мм и выше) применяют крупнозернистую углеродистую сталь, так как в сверлах требуется сквозная про-
каливаемость; повышается обрабатываемость режущим инструментом. При крупном зерне повышается жаропрочность, общая коррозионная стойкость, магнитная проницаемость. Динамная и трансформаторная стали имеют наилучшие магнитные свойства при крупнозернистом строении, так как в мелкозернистой стали увеличиваются потери на гистерезис.
Приведенные примеры говорят о значении величины зерна в технологии производства, обработке и эксплуатации стали.
62

Для выявления границ зерен стали используют чаще всего методы окисления (для углеродистых и легированных сталей – конструкционных и инструментальных) или цементации (для низкоуглеродистых сталей). Стали нагревают и выдерживают при температуре 930°С в окисленной или науглероживающей среде. Размер зерна аустенита определяют после охлаждения металлографическим анализом по сетке окислов или сетке вторичного цементита, которые образуются по границам бывших зерен аустенита.
Используют также методы сетки перлита, травления. III. ОБОРУДОВАНИЕ »ПРИБОРЫ, ШЕРИАЛЫ
1.Металлографические микроскопы МИМ -7.
2.Объект - микрометр, окуляр - микрометр.
3.Набор микрошлифов с различной величиной зерна стали.
4.Шкала для определения величины зерна (увеличение 100).
IV. МЕТОДИЧЕСКИЕУКАЗАНИЯИЗАДАНИЯПОВЫПОЛНЕНИЮРАБОТЫ
I.Определение величины зерна методом сравнения
1)Микрошлифы стали рассмотреть под микроскопом при увеличении x100.
2)Зарисовать микроструктуры шлифов.
3)Сравнить зерна со стандартной шкалой величины зерна стали (рис.7.2). Размер зерна оценивается номером (баллом) соответствующего эталонного изображения зерен.
Зерна с номерами 1-5 считаются крупными, а с более высокими номерами
– мелкими. Стандартная шкала построена на основе соотношения:
= 8 • 2№;
где n - количество зерен на I мм2 площади микрошлифа;
№- номер зерна.
4)Вычислить n для каждого номера зерна и по формулам рассчитать Fcp и dcp, принимая форму зерен за шаровидную:
5)При наличии одновременно зерен двух номеров величину зерна обозначают двумя номерами, указывая (ориентировочно), какую площадь в процентах занимают те и другие зерна, например, № 5 – 25%, №6 – 75%.
Если один из размеров занимает площадь менее 10%, то такие зерна обозначают одним номером.
63

64

2.Определение величины зерна по среднему условному диаметру зерна.
I)Определить цену деления окуляр-микрометра.
В отверстие визуального тубуса вставить окуляр-микрометр. Подобрать объектив, чтобы увеличение микроскопа было хI000.
На предметный столик поместить объект-микрометр. Наблюдая в окуляр, вращением манометрического и микроскопического винтов навести на фокус шкалу объект-микрометра; перемещением оправы главной линзы окуляра получить резкое изображение шкалы окуляр-микрометра.
Вращением окуляра совместить шкалу окуляр-микрометра со шкалой объект-микрометра, установив параллельно штрихи обеих шкал (рис.7.3)
Совмещение в поле зрения микроскопа шкал (б) окуляр-микрометра и объект-микрометра (а)
Рис. 7.3
Подсчитать, какое число целых делений окуляр-микрометра совпадает с определенным числом делений шкалы объект-микрометра. Определить цену деления шкала окуляр-микрометра
65

где Цоб - цена деления шкалы объект-микрометра, равная 0,01 мм; Nоб - число совмещенных делений объект-микрометра;
Nок - число совмещенных делений окуляр-микрометра.
2)Рассмотреть микрошлиф в микроскоп, подсчитать, сколько зерен приходится на определенное число делений окуляр-микрометра (шкалу окуляр-мик-ро- метра располагают при этом горизонтально).
3)Подсчитать размер зерна в горизонтальном направлении
где Nок - число делений окуляр-микрометра;
Цок - цена деления шкалы окуляр-микрометра;
К- количество зерен, приходящихся на N делений окуляр-микрометра.
4)Вращением окуляра переместить шкалу в вертикальное положение и подсчитать, сколько зерен приходится на определенное число делений окуляр-микро- метра. Подсчитать размер зерна в вертикальном направлении
5)Определить средний размер зерна
6)Определить площадь зерна F, считая, что полученный средний размер зерна ℓcp равен среднему - диаметру зерна и dср
7)По полученной площади в мм2 определить номер зерна, пользуясь данными табл. 7.1.
Таблица 7.1
Геометрические параметры зерен разных размеров по ГОСТ 5639-82
|
Средняя |
Среднее |
Среднее |
Средний |
Средний |
|
площадь се- |
число зерен |
условный |
||
Номер зерна |
число зерен |
диаметр зер- |
|||
|
чения зерна |
на площади I |
3 |
|
диаметр зер- |
|
F,мм2 |
мм2 |
Nυ в I мм |
на dср, мм |
на dL, мм |
I |
2 |
3 |
4 ! |
5 |
6 |
-3 |
I |
1 |
I |
1,0 |
0,875 |
-2 |
0,5 |
2 |
2,8 |
0,707 |
0,650 |
-I |
0,25 |
4 |
8 |
0,5 |
0,444 |
66
|
|
|
|
Продолжение табл.7.I |
|
|
|
|
|
|
|
I |
2 |
3 |
4 |
5 |
6 |
0 |
0,125 |
8 |
22,6 |
0,353 |
0,313 |
1 |
0,0625 |
16 |
64 |
0,250 |
0,222 |
2 |
0,0612 |
32 |
181 |
0,177 |
0,157 |
3 |
0,0156 |
64 |
512 |
0,125 |
0,111 |
4 |
0,00781 |
128 |
1448 |
0,088 |
0,0783 |
5 |
0,00390 |
256 |
4096 |
0,062 |
0,0553 |
6 |
0,00195 |
512 |
11585 |
0,044 |
0,0391 |
7 |
0,00098 |
1 024 |
32768 |
0,031 |
0,0267 |
8 |
0,00049 |
2 048 |
92682 |
0,022 |
0,0196 |
9 |
0,000244 |
4 096 |
262144 |
0,015 |
0,0138 |
10 |
0,000122 |
8 192 |
741485 |
0,011 |
0,0099 |
11 |
0,000061 |
16 384 |
2097152 |
0 0079 |
0,0069 |
12 |
0,000031 |
32 768 |
5931008 |
0,0056 |
0,0049 |
13 |
0,000015 |
65 536 |
16777216 |
0,0039 |
0,0032 |
14 |
0,000008 |
131 072 |
47449064 |
0,0027 |
0,0027 |
V.ОФОРМЛЕНИЕ ОТЧЕТА
1.Кратко законспектировать теоретическую часть.
2.Зарисовать микроструктуры набора шлифов сталей.
3.Определить величину зерен на микрошлифах методом сравнения.
4.Определить величину зерен, микрошлифов стали по среднему условному диаметру зерна dcp.
5.Расчетные данные записать в табл. 7.2.
Таблица 7.2
Определение величины зерна в стали
|
|
|
|
|
Номер шлифа |
ℓгор, мм |
ℓверт, мм |
Fcp, мм2 |
Номер зерна |
|
|
|
|
|
VI.ВОПРОСЫ ДЛЯ САМОПРОВЕРКИ
1.Факторы, влияющие на величину зерна.
2.Какая сталь называется наследственно мелкозернистой (НМЗ)? Ее особенности.
3.Какаястальназываетсянаследственнокрупнозернистой(НКЗ)? Ееособенности.
4.Что такое действительное зерно?
5.Как влияет величина зерна на технологические и физические свойства стали?
6.Влияние величины зерна на механические свойства стали.
7.Какими методами можно выявить гранив зерен?
8.Приведите методику определения величины зерна.
67
ЛАБОРАТОРНАЯ РАБОТА № 8 ИЗУЧЕНИЕ МИКРОСТРУКТУРЫ УГЛЕРОДИСТЫХ СТАЛЕЙ
ВРАВНОВЕСНОМ СОСТОЯНИИ
I.ЦЕЛЬ РАБОТЫ Ознакомиться и провести практическое наблюдение и исследование микроструктуры сталей, формирующейся в соответствии с диа-
граммой Fе – Fе3С при медленном охлаждении. Уяснить закономерности образования типичных структур старей с содержанием углерода от 0,02 до 2,0% углерода. При наблюдении под микроскопами различных типов микроструктуры приобрести первичные навыки, установления марки углеродистых сталей и возможные направления применения стали.
II.ТЕОРЕТИЧЕСКИЕ СВЕДЕНТЯ
Стали, содержащие в соответствии с диаграммой состояния Fe-Fe3C (же- лезо-цементит) до 2,0% углерода в литом состоянии, имеют характерное дендритное макростроение. При этом превращения, протекающие при охлаждении в сплавах железо-углерод, фазовые превращения и конечная структура (а значит и свойства) могут быть определены при анализе "стальной части" диаграммы, приведенной на рис.8.1.
Равновесные микроструктуры сталей формируются при медленном охлаждении от температур ниже линии "солидуса" АНLЕСР (для cталей и чугунов), а практически при охлаждении из аустенитного состояния - для сталей NIESOS.
При этом структура сталей с различным содержанием углерода определяется существованием железа в двух модификациях (полиморфизм железа); α - Fe ниже 911°С и γ – Fe ( 9II-1392°С). Каждая из полиморфных модификаций железа образует с углеродом твердый раствор, растворимость углерода в каждой из полиморфных решеток α- γ- железа существенно различна и изменяется с ростом или снижением температуры.
Так линия на диаграмме железо-цементит соответствует при охлаждении температурам превращения γ→α. Критические точки, образующие в условиях равновесия линию GS, обозначаются А3, а критические точки, образующие линию ES, характеризующие снижение растворимости, углерода в γ-Fе при охлаждении, сопровождающееся выделением карбида Fe3C (цементита вторичного) обозначаются Аст (латинское m).
Основная терминология лабораторной работы приведена ниже.
68

69
ТЕРМИНЫ к лабораторной работе:
Феррит - (Ф) - твердый раствор внедрения углерода в γ железе (ОЦК). Различают низкотемпературный α - феррит с растворимостью углерода до 0,02% и высокотемпературный δ - феррит (см. диаграмму). Под микроскопом виден в виде однородных полиэдрических зерен, рис. 8,2а.
Феррит мягок, HB = 90 - 100, предел прочности σв около 250 Н/мм, предел текучести σт около 130 Н/мм, относительное удлинение δ до 50$, относительное сужение ψ до 80%.
Аустенит - (А) - твердый раствор внедрения углерода в γ - железе с предельной растворимостью углерода в γ - железе (ГЦК) до 2,14%. Полиэдрическая структура с более высокой твердостью HB = 200 - 230, более прочен и менее пластичен. Стабилен при комнатной температуре и хромоникелевых нержавеющих сталях с содержанием никеля выше 8-10%.
Цементит - (Ц) - (карбид железа Fе3С) - химическое соединение с С, с сложной ромбической кристаллической решеткой. Очень высокая твердость (до
8000 МПа). Содержит 6,67% С.
Техническое железо - железоуглеродистый сплав с содержанием углерода до 0,02%.
Доэвтектоидная сталь - сталь с содержанием углерода от 0,02 до 0,8% (на диаграмме точка S), имеет структуру феррит и перлит, образующийся из аустенита при температуре ниже A1 (линия PSK).
Эвтектоид (эвтектоидная сталь) - равновесная смесь твердого цементита и мягкого феррита, структура отожженной стали с содержанием 0,8% С,
Перлит - зернистый, является идеальной структурой эвтектоидной стали, прошедшей так называемый "маятниковый" отжиг. Эвтектоидные стали типа У8, У8А.
Заэвтектоидные стали - стали с содержанием углерода от 0,83 до 2,14%. В структуре стали кроме перлита (феррит+цементит) наблюдаются сетка или разрозненные участки цементита Fe3C, выделившегося из аустенита при температурах ниже линии ЕЭ и из аустенита по линии RSK.
Алмазная сталь - заэвтектоидная сталь с содержанием выше 1,2% С, закаленная в щелочных водных растворах, имеющая твердость выше НРСЭ = 64, а также легированная сталь ХВ5, закаливающаяся на твердость выше HRCЭ = 65 - 65,5.
К в а з и э в т е к т о и д (псевдоэвтектоид) - ферритно-цементитная смесь, получающаяся при распаде ayстенита, содержащая больше или меньше углерода, чем 0,8% при эвтектоидном распаде.
70
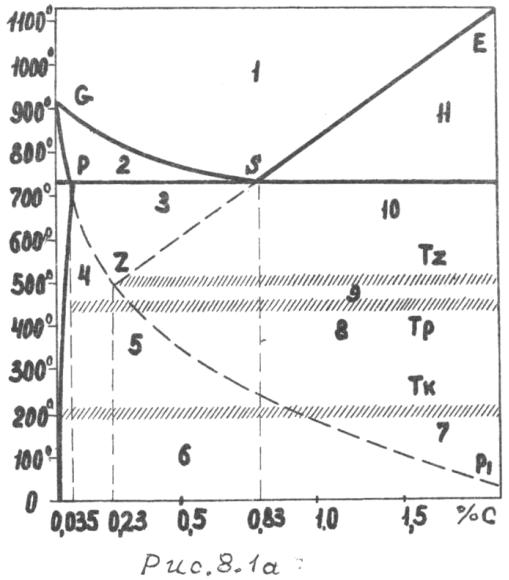
Распад аустенита может происходить только при температуре ниже 727°С (критическая точка A1), когда свободная энергия аустенита выше продуктов его разложения, связанного с выделением из твердого раствора γ - железа углерода.
Превращение аустенита в феррито-перлитную, перлито-цементитную смесь протекает не мгновенно, а протекает в течение определенного времени. В течение некоторого времени после охлаждения до температур ниже A1 аустенит остается нераспавшимся (это инкубационный период),а затем, в зависимости от скорости и времени изотермической выдержки распадается на ферритно-цемен- титную смесь. Кинетические кривые изотермического превращения аустенита для сталей с различным содержанием углерода и легирующих элементов служат основой для построения диаграмм изотермического превращения аустенита в стали.
Полная диаграмма превращения при охлаждении углеродистые сталей
71

Микроструктура углеродистых сталей в равновесном состоянии
Технически чистое железо, содержа- |
Доэвтектоидная сталь с содержанием |
ние углерода до 0,006%, структура |
углерода 0,1-0,15%, структура |
(Феррит - Ф) |
Перлит + Феррит (П+Ф). |
Доэвтектоидная сталь с содержанием |
Доэвтектоидная сталь с содержанием |
углерода 0,15-0,25%, структура Пер- |
углерода 0,45-0,55%, структура Пер- |
лит + Феррит (П+Ф) |
лит + Феррит (П+Ф) |
Рис. 8.2
72

Доэвтектоидная сталь с содержанием |
Эвтектоидная сталь- с содержанием |
углерода 0,60-0,70%, структура Фер- |
углерода 0,8%, структура Перлит пла- |
рит + Перлит (Ф+П) |
стинчатый (Ппл) |
Эвтектоидная сталь, с содержанием углерода 0,8%,структура Перлит зернистый (Пз)
Заэвтектоидная сталь, с содержанием углерода 1,2%, структура Перлит + Цементит вторичный (П+ЦII )
Рис.8.3
73
Превращение аустенита углеродистых стелей наиболее полно показаны на рис. 8.1а. Области на диаграмме: I - область устойчивого аустенита; 2 - область превращения в равновесный феррит; 3 - область превращения в пересыщенный феррит (черновит, а затем по линии SZ псевдоэвтектоид); 4 - область превращения в пересыщенный феррит (черновит); 5 - область превращения в нижний бейнит; 6 - область превращения в мартенсит; 7 - область переохлажденного аустенита; 8 - область обособления из аустенита карбидов и превращение в верхний бейнит; 9 - область превращения в верхний бейнит; 10 - область превращения карбидов и превращения в псевдоэвтектоид; 11 - область обособления из аустенита карбидов в точке S - превращение в перлит.
Эвтектика - смесь тонких кристаллов, закристаллизовавшихся из расплава одновременно, характеризующаяся постоянны.; составом, в сплавах железо-уг- лерод (железо-графит) эзтектика-ледебурит - смесь аустенита и цементита, образовавшаяся из расплава по линии ЕСF при 1147º С на диаграмме рис. 8.1.
Эвтектоид - смесь двух стабильных фаз, имеющих постоянный состав в чистых железо-углеродистък сплавах, образуется при 727°С по линии PSK в процессе распада аустенита при охлаждении литой или горячедеформировенной стали, подвергнутой отжигу или нормализации.
Перлит достаточно прочен и пластичен и в зависимости от формы цементитных образований может быт пластичным или зенистым (рис.8.2в, г), его свойства: твердость HB = 155 - 260, предел прочности 750-830 Н/мм2 относительное удлинение до 15-22%.
Классификация углеродистых сталей, содержащих кроме железа и углерода только постоянные, сопутствующие металлургическим процессам примеси - марганец, кремний, серу, фосфор в минимальных количествах, по структуре характерной для отожженного состояния, следующая:
-доэвтектоидные (до 0,8%С) по назначению, как правило, конструкционные стали, для изготовления различных деталей машин и механизмов;
-эвтектоидные (0,8%С) по назначению; инструментальные - для слесарных, измерительных инструментов и некоторых видов пружин-ленточных;
-заэвтектоидные (0,8-2,14%C) - инструментальные стали для слесарных и режущих инструментов, не обладающих теплостойкостью.
III.ОБОРУДОВАНИЕ, ПРИБОРЫ И МАТЕРИАЛЫ
1.Металлографические микроскопы ММР-3, ММР-4, МИМ-7 для изучения микроструктур при увеличениях 150-500 крат.
2.Набор микрошлифов технического железа, малоуглеродистой стали, эвтектоидной и высокоуглеродистой заэвтектоидной стали.
74
3. Атлас микроструктур.
IV.МЕТОДИЧЕСКИЕУКАЗАНИЯИЗАДАНИЯПОВЫПОЛНЕНИЮРАБОТЫ
Микроструктура отожженных углеродистых сталей (после медленного охлаждения от температур выше А3 на 30-50 С для доэвтектоидных сталей и от температур выше A1 на 20-30 С для эвтектоидных и заэвтектоидных сталей) позволяет судить о принадлежности сталей к группе конструкционных или инструментальных, оценить качество предварительной термической обработки. Полученные навыки могут быть полезны в практике работы инженера.
Самостоятельное изучение с применением металлографического микроскопа микроструктур сталей углубляет теоретические знания о металлах и сплавах. Рассматривание структуры сталей при различном увеличении, с перенастройкой системы объектив-окуляр и сравнение наблюдаемых микрошли- фов необходимо отразить в отчете.
V.СОДЕРЖАНИЕ ОТЧЕТА
1.Отчет должен быть кратким, но наглядным и отражать основную цель работы, содержать рисунок диаграммы железо-цементит и краткие пояснения по микроструктурам всех классов углеродистых сталей.
2.В отчете должны быть показаны данные и сведения по одной из наиболее подробно изученных студентом углеродистых сталей. Зарисовка трех типичных микроструктур сталей - доэвтектоидной, эвтектоидной, заэвтектоидной целесообразна.
3.Дополнительные данные, обнаруживаемые студентом при работе со справочным материалом и литературой желательны.
VI. ВОПРОСЫ ДЛЯ САМОПРОВЕРКИ'
1.Определение стали как сплава на основе железа; классификация по содержанию углерода, содержанию примесей, по назначению.
2.Эвтектоидное превращение в стали как определяющее структуру и свойства после отжиге; свойства феррита, аустенита, цементита, перлита, как структурных составляющих и фаз в сталях.
3.Назвать данные и примеры использования углеродистых сталей с различным содержанием углерода в машиностроении. Привести примеры конструкционных доэвтектоидных сталей различных способов выплавки, влияющих на конструкционную прочность и надежность деталей машин.
75
ЛАБОРАТОРНАЯ РАБОТА № 9 ИЗУЧЕНИЕ МИКРОСТРУКТУРЫ ЧУГУНОВ В РАВНОВЕСНОМ
СОСТОЯНИИ
I. ЦЕЛЬ РАБОТЫ: I) с помощью металлографического микроскопа изучить микроструктуру белых и графитизированных чугунов, сопоставляя ее с диаграммами состояния "железо-цементит" и "железо-графит";
2)по микроструктуре чугуна установить его тип и марку;
3)зная марку чугуна и его металлическую основу, определить его свойства и область применения в технике.
2. КРАТКИЕ ТЕОРЕТИЧЕСКИЕ СВЕДЕНИЯ
Чугун представляет собой сплав железа с углеродом, содержащий более 2,14% углерода. Такое содержание углерода приводит к образованию в структуре чугунов твердой, хрупкой эвтектики и цементита (рис. 8.1), либо к появлению свободного углерода е виде графита (рис.9.I).
При кристаллизации чугуна жидкая фаза по составу более близка к фазам цементита и аустенита. Поэтому кристаллизация цементита и аустенита из жидкой фазы протекает легче, чем графита, что и наблюдается по диаграмме "же- лезо-цементит".
При нагреве цементит разлагается на железо и графит, так как он является нестабильной фазой, чем цементит, что видно из диаграммы "железо-графит". Непосредственно из жидкой фазы графит выделяется при наличии в сплаве должного количества углерода и графитизанторов, кроме того, необходимо медленное охлаждение.
Белый чугун. Характерной особенностью белого чугуна является то, что в изломе он имеет белый цвет. Углерод в нем находится в химически связанном состоянии, в виде цементита Fe3C . Этим и объясняется его высокая твердость и хрупкость и плохая обрабатываемость резанием.
Область применения его весьма ограничена. Отливки из белого чугуна получают при быстром охлаждении сплава, содержащего повышенное количество марганца. Марганец является отбеливающим элементом.
Изучение микроструктуры белых чугунов производится по диаграмме состояния "железо-цементит" (рис.8.I). Согласно диаграмме по химическому составу и структуре белые чугуны можно разделить на три типа.
Доэвтектический белый чугун содержит от 2,14 до 4,3% углерода. Структура его состоит из перлита, цементита вторичного и ледебурита (рис. 9.2).
Эвтектический чугун содержит 4,3% углерода и структура его состоит из ледебурита (рис. 9.2).
76
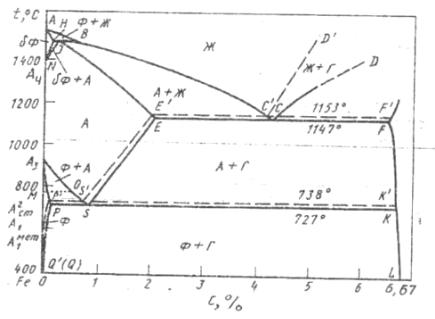
Заэвтектический чугун содержит от 4,3 до 6,67% углерода. Структура его состоит из первичного цементитат и ледебурита (рис.9.2).
Графитизированные чугуны являются наиболее распространенными сплавами для фасонного литья. Чугун обладает прекрасными литейными свойствами: более низкая температура плавления чем у сталей, высокая жидкотекучесть, малая усадка, высокое сопротивление образованию усадочных трещин.
Промышленные чугуны содержат 2,14 - 4,5% С, 1,0 - 3,5% Si , 0,5 - 1,0%
Мп, до 0,3% Р и до 0,2%S . Основой промышленных чугунов можно считать тройную систему Fe - C - Si (рис.9.3). В трехкомпонентной системе эвтектическое и эвтектоидное равновесия Ж+А+Г и А+Ф+Г наблюдается не при постоянной температуре, как в системе Fe - С, а в интервале температур. Под действием кремния двойная эвтектика смещается в сторону меньшего содержания углерода.
Структура чугуна зависит не только от его состава, но и от скорости охлаждения. При ускоренном охлаждении графит не успевает кристаллизоваться и формируется структура белого чугуна (диаграмма Fe - С), а при медленном охлаждении кристаллизуется серый чугун. От скорости охлаждения зависит и полнота графитизации серого чугуна в твердом состоянии: с уменьшением скорости охлаждения перлитная основа заменяется феррито-перлитной и ферритной.
Вертикальный разрез системы Fe -C-Si при содержании 3% Si
Рис. 9.1
77

Микроструктура белых чугунов
а - доэвтектический белый чугун х500; б - эвтектический белый чугун x500; в - заэвтектический белый чугун х500
Рис. 9.2
78

На полноту графитизации влияет увеличение содержания углерода и кремния, а марганец, наоборот, затрудняет графитизацию.
Структурная диаграмма Maypepa (рис.9.4) приближенно указывает границы структурных областей в зависимости от содержания углерода и кремния при постоянном содержании 0,5% Мп и заданной скорости охлаждения (при толщине стенки отливки 50 мм). Чем больше углерода в чугуне, тем меньше кремния требуется для полной графитизации. С увеличением скорости охлаждения (уменьшением толщины стенки отливки) линии диаграммы Маурера смещаются вправо и вверх.
Диаграмма состояния Fe-C-Si (стабильная)
Рис. 9.3
Чугун в ряде случаев благодаря наличию гранта имеет преимущества перед сталью: наличие графита облегчает обрабатываемость резанием (стружка делается ломкой), чугун имеет хорошие антифрикционные свойства благодаря смазывающему действию графита, наличие графитных выделений быстро гасит вибрации и резонансные колебания, чугун мало чувствителен к внешним концентраторам напряжений: надрезам, 5 точкам, резким переходам между сечениями отливки.
Механические свойства чугуна определяются строением металлической основы и формой гранитовых включений.
Пластичности чугуна мало зависит от строения металлической основы,
определяется, в основном, формой графита: |
|
|
||
Графит |
Пластинчатый |
Хлопьевидный |
Вермякулярный |
Шаровидный |
Относитель- |
|
|
|
|
ное удлине- |
0,2 - 0,5 |
2-10 |
0,9 - 3,0 |
2-20 |
ние δ, % |
|
|
|
|
79
Твердость HB определяется структурой металлической основы и мало зависит от формы графита.
Чугун |
Ферритный |
Феррито-перлитный |
Перлитный |
Твердость HB |
СЧ 12 |
СЧ 18 |
СЧ 28 |
МПа 10-1 |
150 |
200 |
250 |
Серый чугун. На долю серого чугуна приходится около 80% общего производства чугунных отливок.
Серый чугун имеет пластинчатую форму графита, что создает концентрацию напряжений. Поэтому чугун выгодно использовать для изготовления деталей, работающих на сжатии. В зависимости от технологического процесса и химического состава (графитизирующие элементы Si, Al)можно получить серый чугун с различной металлической матрицей: ферритной, феррито-перлит- ной, перлитной (рис.9.5).
Серый чугун маркируют (ГОСТ 1412-85) буквами СЧ, за которыми число обозначает временное сопротивление при растяжении Gв в кГс/мм2.
Увеличение скорости охлаждения способствует измельчению графита, уменьшается его количество, увеличивается доля перлита. С увеличением сечения стенок фасонных отливок из-за уменьшения скорости охлаждения Gв снижается.
Серый чугун обладает склонностью к росту при высоких температурах. В результате роста чугуна происходит необратимое увеличение его объема, искажающего размеры деталей и снижается его прочность. Явление роста чугуна объясняется окислением металла по границам включений графита и распадом цементита. С образованием феррита и графита, суммарный объем которых больше чем у цементита. Поэтому серые чугуны применяются при температуре до 250°С. Для снижения роста чугуна применяется модифицирование его никелем, хромом.
Основные области применения серого чугуна - станкостроение и тяжелое машиностроение (станины станков, корпусные детали), строительство и сани- тарно-техническое оборудование (колонны, секции отопительных радиаторов, ванны, канализационные трубы), автомобильная промышленность и сельскохозяйственное машиностроение (блоки цилиндров, картеры, шкивы, поршневые кольца и др.).
Высокопрочный чугун. При введении в чугун 0,05% магния или церия графит кристаллизуется в шаровидной или близкой к ней форме, поэтому включения графита не являются такими сильными концентраторами напряжений, как пластинчатый графит.
Высокопрочные чугуны маркируются (ГОСТ 7293-85) буквами ВЧ, за которыми следует число, указывающее гарантируемое значение в Gв кГс/мм2.
80

Структурные диаграммы для чугунов
а - влияние углерода и кремния; б - влияние толщины отливки (скорости охлаждения);
I - белые чугуны; II - половинчатые чугуны; III-V серые чугуны с перлитной, перлитно-ферритной и ферритной основой.
Рис. 9.4
Микроструктура серого чугуна
а- серый чугун с ферритной основой х500;
б- серый чугун с феррито-перлитной основой х500; в - серый чугун с перлитной основой х500
Рис. 9.5
81

Высокопрочные чугуны имеют такие же виды металлической матрицы, как и серые. Например, ВЧ38 имеет ферритную основу, ВЧ45 ферритно-пер- литную и ВЧ60 перлитную основу, рис. 9.6.
Их используют для замены литой стали в изделиях ответственного назначения (станины и рамы прокатных станов, валки горячей прокатки, тяжело нагруженные коленчатые валы дизельных, в том числе автомобильных двигателей). По сравнению со сталью они обладают более высокими литейными свойствами и на 8-10% меньшей плотностью, что позволяет снизить массу машин. Из высокопрочного чугуна изготавливают отливки массой от нескольких килограммов до десятков тонн.
Чугун с вермикулярным графитом.
Наряду с шаровидным графитом высокопрочные чугуны могут содержать некоторое количество вермикулярного (от лат. vermicul - червячок) графита. От пластинчатого вермикулярный графит отличается округлыми краями, меньшими размерами и меньшим отношением длины лепестка к его толщине, поэтому его можно рассматривать как переходную форму от пластинчатого к шаровидному графиту. В соответствии с ГОСТ 28394-89 чугун с вермикулярным графитом может содержать не более 40% шаровидного графита, весь остальной графит - вермикулярный (рис.9.7). Такой чугун обозначают буквами ЧВГ. за которыми следует число, указывающее гарантируемое значение (Gв, кГс/мм*.
Микроструктура высокопрочного чугуна
а- высокопрочный чугун с ферритной основой х500;
б- высокопрочный чугун с феррито-перлитной основой х500; з - высокопрочный чугун с перлитной основой х500
Рис. 9.6
Чугуны марок ЧВГ прочнее, а при одинаковой прочности пластичнее чугунов марок СЧ. Они превосходят чугуны марок ВЧ по демпфирующей способности и обрабатываемости резанием. Чугуны марок ЧВГ применяют для от-
82
ливки базовых деталей станков, корпусных деталей, массивных изложниц и кокильной оснастки.
Ковкий чугун. Хотя ковкий чугун не подвергается ковке, относительное удлинение и δ него может достигать 10-12%. Содержание углерода (2,4-2,9%) и кремния (1,0-1,6%) в ковком чугуне меньше, чем в сером, чтобы обеспечить по всему сечению отливки формирование структуры белого чугуна, при последующем графитизирующем отжиге, от которого графит получается хлопьевидной (компактной) формы (рис.9.8), чем больше сечение стенки отливки, тем меньше должно быть содержание кремния.
Металлическая основа ковкого чугуна при одноступенчатом отжиге - перлитная, при двухступенчатом - ферритная, рис. 9.9.
Ковкие чугуны (ГОСТ 1215-79) маркируются буквами КЧ, за которыми следуют два числа, обозначающие Gв (кГс/мм2) и δ (%). Наиболее часто применяются ферритные ковкие чугуны, обладающие повышенной пластичностью.
Достоинство ковкого чугуна - однородность свойств по сечению отливки: скорость охлаждения при кристаллизации не влияет на размер, количество и форму графитных включений, как в случае чугунов марок СЧ и ВЧ. Недостаток ковкого чугуна - худшие литейные свойства из-за меньшей степени эвтектичности. Другой недостаток - ограничение толщины стенок отливки величиной 50 мм.
Ковкий чугун используют при производстве мелких и средних по массе деталей (картеры, муфты, звенья цепей, детали рулевого управления и др.).
К чугунам со специальными свойствами относятся: антифрикционные (ГОСТ 1585-85), такие, как АЧС-1, АЧВ-1 и т.д.; износостойкие, жаростойкие и коррозионностойкие чугуны (ГОСТ 7769-82), легированные хромом, кремнием, алюминием и другими элементами.
Жаропрочные чугуны ЧХ28, ЧХ32, ЧС5 обладают высокой длительной прочностью и жаростойкостью до 700-800ºС на воздухе и в топочных и генераторных газах.
Высокой термостойкостью и сопротивляемостью окалинообразованию обладают аустенитные чугуны с шарообразным графитом ЧН15ДЗШ, ЧН19ХЗШ, ЧН11Г7Ш.
Для повышения жаропрочности легированные чугуны подвергают отжигу при 1020-1050С с охлаждением на воздухе и отпуску при 500-600º. После отжига легированные карбиды чугуна приобретают форму мелких округлых включений, а цементит Fe3С растворяется в аустените.
83

Микроструктура вермикулярного чугуна x100
Рис. 9.7
Схема получения ковких чугунов
а - первая стадия графитизации; б - вторая стадия графитизации
Рис. 9.8
84

Микроструктура ковкого чугуна
а- белый чугун до отжига х250;
б- перлитный ковкий чугун х250; в - ферритный ковкий чугун х250
Рис. 9.9
85
III. ОБОРУДОВАНИЕ, ПРИБОРЫ, МАТЕРИАЛЫ
Металлографические микроскопы МИМ-7 или ММУ-3М; твердомеры Роквелла и Бринелля; наборы микрошлифов белого, серого, высокопрочного и ковкого чугунов; атласы микроструктур чугунов; циркуль, линейка.
IV. МЕТОДИЧЕСКИЕ УКАЗАНИЯ ПО ВЫПОЛНЕНИЮ РАБОТЫ
1.Изучить изломы белых и графитизированных чугунов.
2.С помощью металлографического микроскопа исследовать структуру доэвтектического, эвтектического и заэвтектического белых чугунов. Замерить твердость на твердомере Роквелла, определить влияние содержания углерода на свойства.
3.Изучить микроструктуры графитизировгнных чугунов: серого, высокопрочного, ковкого с различными видами металлической основы. Замерить твердость чугунов, определить влияние матрицы на свойства.
V.СОДЕРЖАНИЕ ОТЧЕТА
1.Зарисовать диаграмму железо-углерод.
2.Рисунок микроструктуры белого доэвтектического, эвтектического и заэвтектического чугунов.
3.Привести определение структурных составляющих белого чугуна.
4.Рисунки серого, высокопрочного и ковкого чугунов в травленом и нетравленом состоянии.
5.Под каждым рисунком указать название чугуна, примерную марку, свойства (твердость), область применения и увеличения микроскопа.
6.У каждого рисунка указать стрелками структурные составляющие, рисунки выполнить карандашом в круге диаметром 40 мм или квадрате 40x40 мм.
VI. ВОПРОСЫ ДЛЯ САМОПРОВЕРКИ
1.Что такое чугун?
2.Какими характерными свойствами обладают чугуны?
3.Как классифицируются белые чугуны по содержанию углерода и структуре?
4.Какие чугуны относятся к графитизированным?
5.Какую форму графита имеют серые, высокопрочные, ковкие чугуны, чугуны с вермикулярным графитом?
6.Какие факторы влияют на структуру графитизированных чугунов?
7.Что изучается по диаграмме Маурера?
86
8.Как влияют форма графита и металлическая матрица на свойства чугуна?
9.Как маркируются графитизированные чугуны?
10.Какие чугуны и какой упрочняющей термообработке они подвергаются?
11.Где применяются графитизированные чугуны?
87
ЛАБОРАТОРНАЯ РАБОТА № 10 ПЛАСТИЧЕСКАЯ ДЕФОРМАЦИЯ И РЕКРИСТАЛЛИЗАЦИЯ МЕТАЛЛОВ
I. ЦЕЛЬ РАБОТЫ:
изучить влияние холодной пластической деформации на структуру и свойства металлов и сплавов; изучить влияние нагрева на твердость и структуру холоднодеформированных металлов.
П. КРАТКИЕ ТЕОРЕТИЧЕСКИЕ СВЕДЕНИЯ
Деформацией называется изменение первоначальной формы и размеров тела при приложении к нему внешней нагрузки. Различают два вида деформации: упругую и пластическую. Упругая деформация состоит только в изменении межатомных расстояний в кристаллической решетке металла и исчезает после снятия нагрузки, пластическая же деформация протекает при напряжениях выше предела упругости и вызывает необратимые изменения формы и размера тела (после снятия нагрузки сохраняется).
На практике металл часто подвергается пластической деформации: штамповке, волочению, ковке, прессованию и т.д. В результате пластической деформации изменяются механические, физико-химические свойства и структура металлов и сплавов.
Пластическая деформация осуществляется путем скольжения (сдвига) или двойникования (рис.10.1).
Основной механизм пластической деформации - сдвигово-дислокацион- ный. При этом происходит сдвиг части кристалла относительно другой по определенным кристаллографическим плоскостям, называемым плоскостями скольжения (плоскости наиболее плотно упакованные атомами), где величина сопротивления сдвигу наименьшая. Направление сдвига совпадает с одним из кристаллографических направлений. Характеристика системы скольжения определяется типом кристаллической решетки металла.
В металлах, имеющих решетку ГЦК (Feγ, Cu, Al и др.), скольжение протекает по плоскостям октаэдра и в направлении диагонали грани куба. В решетке ОЦК (Feα, Mo, V и др.) процесс скольжения наиболее легко осуществляется по плоскостям и в направлении пространственной диагонали куба. В металлах с решеткой ГПУ (Mq, Zn и др.) скольжение идет по плоскостям базиса. Чем больше в металле систем скольжения, тем выше его способность к пластической деформации. Металлы с решеткой ГЦК обладают высокой пластичностью.
Скольжение осуществляется в результате перемещения в кристалле дислокаций. Перемещение дислокации через весь кристалл приводи? к смещению (сдвигу) соответствующей части кристалла на одно межплоскост-
88

Схемы упругой и пластической деформации металла под действием напряжения сдвига
а- первоначальный кристалл; б - упругая деформация;
в- увеличение упругой и появление пластической деформации, вызванной скольжением при нагружении, большем предела упругости; г - напряжение, обуславливающее появление сдвига; д - образование двойников
Рис. 10.1
89
ное расстояние, при этом на поверхности кристалла образуется ступенька. Обычно в одном месте выходит на поверхность кристалла группа дислокаций (10 - 100). Следует иметь в виду, что перемещение дислокаций, образовавшихся в процессе кристаллизации, ограничено. Большие деформации возможны только вследствие того, что движение этих дислокаций вызывает появление или размножение большого количества новых дислокаций в процессе пластической деформации (эффект ФранкаРида).
Деформация поликристалла происходит сложнее. В поликристаллическом металле вследствие разной кристаллографической ориентации зерен сначала деформируются зерна, имеющие благоприятную ориентировку по отношению к действующим напряжениям. При этом наряду со сдвигами в отдельных зернах происходит скольжение по границам зерен, вызывает поворот зерен относительно друг друга в направлении, например, растягивающей нагрузки. При малых нагрузках сдвиги развиваются только в отдельных зернах - образуются полосы скольжения, которые отделяются между собой областями, не испытавшими сдвига (полосы скольжения можно наблюдать в микроскоп на шлифах слабодеформированного металла - рис. 10.2).
С возрастанием степени деформации скольжение распространяется и на зерна с менее благоприятной ориентировкой. Число линий скольжения увеличивается, и при значительной деформации они проявляются в несколько пересекающихся направлениях.
При большей деформации в результате процессов скольжения зерна, кристаллиты меняют свою форму. Если до деформации зерно имело округлую форму, то после деформации в результате смещения по плоскостям скольжения зерна вытягиваются в направлении действующей силы, образуя волокнистую или слоистую структуру, что приводит к анизотропии свойств деформированного материала (рис.10.2).
Одновременно с изменениями формы зерна внутри него происходит дробление блоков и увеличение угла разориентировки между ними.
При большей степени деформации происходит преимущественная кристаллографическая ориентировка зерен. Закономерная ориентировка кристаллитов относительно внешних деформационных сил получила название текстуры.
В определенных условиях в металле при нагружении происходит двойникование - образование двойниковых прослоек, внутри которых кристаллическая структура является зеркальным отражением кристаллической структуры соседних областей (рис.10.1). Сдвойникованные кристаллы могут образоваться при росте из расплава, при отжиге после холодной деформации, при пластической деформации. Двойникованию способствуют
90

Схемы структуры технически чистого железа до и после пластической деформации
а- структура технического железа до деформации;
б- полосы скольжения после деформации 1%;
в - волокнистая структура после деформации 80%
Рис. 10.2
91

Зависимость механических свойств стали 08 кп (а), меди (б), алюминия (в) от степени пластической деформации
92

93
низкие температуры и высокие скорости деформирования (ударное нагружение, обработка взрывом).
Итак, основной вид пластической деформации металлов - скольжение. Пластическая деформация в зависимости от температурного интервала, в
котором она проходит, подразделяется на холодную и горячую.
Холодная пластическая деформация проводится при температурах ниже температуры рекристаллизации Тр (обычно ниже 0,25 - 0,3 от Тил).
Горячая деформация протекает выше Тр (выше 0,5 - 0,6 от Тпл).
С увеличением степени холодной деформации прочностные свойства и твердость металла возрастают, а относительное удлинение и сужение падают (рис. 10.3). При степенях деформации 50...70% временное сопротивление и твердость увеличиваются в I,5...3 раза. Относительное удлинение резко уменьшается уже при сравнительно небольших деформациях, а после больших обжатий может оказаться уменьшенным в десятки раз.
Упрочнение при обработке давлением называют наклепом или нагартовкой (от нем. hart - твердый).
Холоднодеформированный металл анизотропен - его механические свойства по разным направлениям различны. Анизотропия свойств обусловлена и металлографической, и кристаллографической текстурой.
При холодной пластической деформации изменяются также магнитные и электрические свойства: увеличиваются электросопротивление и коэрцитивная сила, снижается магнитная проницаемость; кроме того, уменьшается плотность
икоррозионная стойкость.
Впроцессе деформации увеличивается плотность дислокаций и число то-
чечных дефектов-вакансий. В металлах после отжига плотность дислокаций составляет 107 – 108 см-2, после сильной пластической деформации – 1011 – 1012 см-2. Увеличение плотности дефектов обусловлено наличием в металле источников, генерирующих дислокации. Накопление дислокаций в холоднодеформированном металле затрудняет их передвижение. Это повышает сопротивление деформации металла, т.е. упрочняет металл. Металлы с ГЦК-решеткой упрочняются сильнее, чем металлы с 0ЦК-решеткой.
2. Влияние нагрева на структуру и свойства холоднодеформированного металла (возврат и рекристаллизация).
Холоднодеформированный металл, характеризующийся высокой плотностью структурных дефектов и значительными внутренними напряжениями, обладает повышенной свободной энергией и находится в термодинамически неустойчивом состоянии. Поэтому даже при комнатной температуре в нем самопроизвольно протекают процессы, приближающие его к равновесному состоянию. Повышение температуры ускоряет эти процессы. Восстановление исходных свойств металла в зависимости от температуры происходит неравномерно.
94

Вначале наблюдается незначительное изменение свойств без видимых изменений микроструктуры металла. Это явление обусловлено уменьшением напряжений П рода и называется возвратом. При этом форма деформированного зерна сохраняется неизменной, а в пределах его изменяется плотность дефектов и их распределение. Возврат связан с уменьшением концентрации точечных дефектов, перераспределением дислокаций и уменьшением их плотности.
Самая низкотемпературная разновидность возврата - отдых - процесс связанный с перераспределением и уменьшением концентрации точечных дефектов.
Полигонизация (вторая стадия возврата) - процесс перераспределения дислокаций с образованием малоугловых дислокационных границ (и движения этих границ), разделяющих субзерна (от polygon - многоугольник).
При нагреве дислокации одного знака перераспределяются и выстраиваются в стенки одна над другой (рис. 10.4).
Схема полигонизации
а - хаотичное распределение краевых дислокаций в изогнутом кристалле; б - стенки дислокаций после полигонизации
Рис. 10.4
Рекристаллизация Начиная с определенной температуры (рис. 10.5), при нагреве холод-
но-деформированного металла происходят сильные изменения структуры: наряду с вытянутыми деформированными зернами можно различить новые более или менее равноосные зерна (рис. 10.5, структура 2). От старых
95

Рис. 10.5
96
зерен, деформированной матрицы они отличаются не только формой, но и более совершенным внутренним строением. Образование и рост зерен с более совершенной структурой, окруженных высокоугловыми границами, за счет исходных деформированных зерен той же фазы называют первичной рекристаллизацией. Резкое снижение плотности дислокаций при первичной рекристаллизации обусловливает сильное разупрочнение (рис. 10.5).
Температура появления рекристаллизованных зерен, т.е. температура начала рекристаллизации Трн, не является физической константой, такой, как точка плавления. С увеличением степени холодной деформации растет плотность дислокаций, новые зерна обнаруживаются при более низких температурах.
Наинизшая температура начала рекристаллизации, соответствующая большим деформациям (60...70%), служит характеристикой металла и называется температурным порогом рекристаллизации Тп.р. Температура рекристаллизации связана с одной из характеристик сил связи - с температурой плавления. Эта зависимость имеет вид
Тр = К • Тпл,
где Тр - температура начала рекристаллизации (порог рекристаллизации), К; К - коэффициент; Тпл - температура плавления, К.
Для металлов высокой степени чистоты К = 0,1 - 0,2; для технически чистых металлов К = 0,30 - 0,40, так как атомы растворимых примесей, взаимодействуя с дислокациями, уменьшают их подвижность и, следовательно, затрудняют формирование центров рекристаллизации.
Для сплавов К = 0,6 - 0,7.
Первичная рекристаллизация заканчивается (Трк), когда полностью исчезают деформированные зерна (рис. 10.5 , структура 3). Зернограничная энергия является термодинамическим стимулом роста одних рекристаллизованных зерен за счет соседних, называемого собирательной рекристаллизацией (рис. 10.5, структура 4).
В интервале собирательной рекристаллизации плотность дислокаций практически не изменяется, поэтому временное сопротивление уменьшается слабо (рис. 10.5).
Относительное удлинение изменяется обратно тому, как изменяется σв: частично восстанавливается в области возврата, резко увеличивается при первичной рекристаллизации из-за уменьшения плотности дислокаций и слабо изменяется при собирательной рекристаллизации. Начиная с температуры T1, называемой температурой перегрева, сильное укрупнение зерна приводит к плавному снижению δ. При температуре T2, называемой температурой пережога, и σв, и δ резко падают практически
97

Изменение механических свойств наклепанного металла в зависимости от температуры отжига
Рис. 10.5.I
98
до нуля. Пережог обусловлен сильным окислением и (или) оплавлением по границам зерен.
Минимальная температура рекристаллизации, кроме чистоты металла, зависит от степени, предшествующей деформации. Чем больше степень деформации, тем менее устойчива структура, тем больше ее стремление перейти в более устойчивое состояние. Следовательно, большая степень деформации облегчает процесс рекристаллизации и снижает минимальную температуру рекристаллизации. Температура рекристаллизации имеет важное практическое значение. Чтобы восстановить структуру и свойства наклепанного металла (например, при необходимости продолжать обработку давлением путем прокатки, протяжки, волочения и т.п.), его надо нагреть выше температуры рекристаллизации. Такая обработка называется рекристаллизационным отжигом (рис. 10.5.1).
Для отжига наклепанного материала в производственных условиях применяют более высокие температуры, чем минимальная температура рекристаллизации, для обеспечения достаточной скорости рекристаллизационных процессов (табл. 10.1).
Таблица 10.1
Температуры рекристаллизации и горячей обработки металлов давлением
|
|
Температура, °С |
|
|
|
Металл |
рекристаллизации |
рекристаллизацион- |
горячей обработки |
||
|
(теоретическая) |
ного отжига |
давлением |
||
|
при К = 0,4 |
||||
|
|
|
|
|
|
Железо |
450 |
600 |
- 700 |
800 - 1200 |
|
Сталь |
450 |
600 |
- 700 |
800 - 1200 |
|
Медь |
270 |
450 |
- 500 |
600 |
- 800 |
Латунь |
250 |
400 |
- 500 |
600 |
- 750 |
Алюминий |
50 |
250 |
- 350 |
350 |
- 460 |
Молибден |
900 |
1400 |
- 1600 |
1400 |
- 2000 |
Размер рекристаллизованного зерна - одна из важнейших характеристик отожженного металла. На размер зерна металла после отжига влияют:
1) Температура отжига.
Сповышением температуры отжига размер зерна увеличивается по экспоненте, как и коэффициент самодиффузии (рис. 10.6).
2) Время отжига.
Сростом продолжительности отжига при постоянной температуре зерно укрупняется по параболе (рис. 10.7) и размер зерна прибли-
99

100
жается к предельному для данной температуры значению. 3) Степень деформации.
При сравнительно небольшой, критической степени деформации (обычно от I до 15%) при отжиге вырастает очень крупное зерно, иногда достигающее размера в несколько сантиметров (малая плотность дислокаций для образования зародышей новых зерен). При обработке металлов давлением следует избегать этой степени деформации, так как последующий рекристаллизационный отжиг для снятия наклепа или повышение температуры в условиях эксплуатации могут вызвать резкое увеличение размеров зерна и, следовательно, значительное падение пластичности и ударной вязкости.
С увеличением степени деформации (превышающей критическую) возрастает плотность дислокаций, образуется много центров рекристаллизации, в результате чего металл получает мелкозернистое строение.
Горячая обработка давлением.
Пластическое деформирование выше температуры рекристаллизации, хотя и приводит к упрочнению, но это упрочнение устраняется протекающим при этих температурах процессом рекристаллизации. Следует отметить, что рекристаллизация протекает не во время деформации, а сразу после ее окончания и тем быстрее, чем выше температура.
Очень важно следующее отличие горячей деформации от холодной: при достаточно больших степенях горячей деформации сопротивление деформированию не зависит от степени, но зависит от скорости деформации.
Горячая обработка давлением всегда предшествует холодной обработке. Например, вначале проводят горячую прокатку плоских слитков, а затем холодную прокатку подката.
Если металл после горячего деформирования полигонизован (нерекристаллизован), то такая горячая деформация повышает прочностные свойства, особенно предел текучести (на 20...60%).
III. ОБОРУДОВАНИЕ, ПРИБОРЫ, МАТЕРИАЛЫ
1.Твердомеры Роквелла, Бринелля.
2.Муфельные печи.
3.Металлографические микроскопы МИМ-7 или ММУ-3М.
4.Наборы предварительно деформированных образцов металлов (меди, алюминия, железа) или стали 10 (стали 15).
101
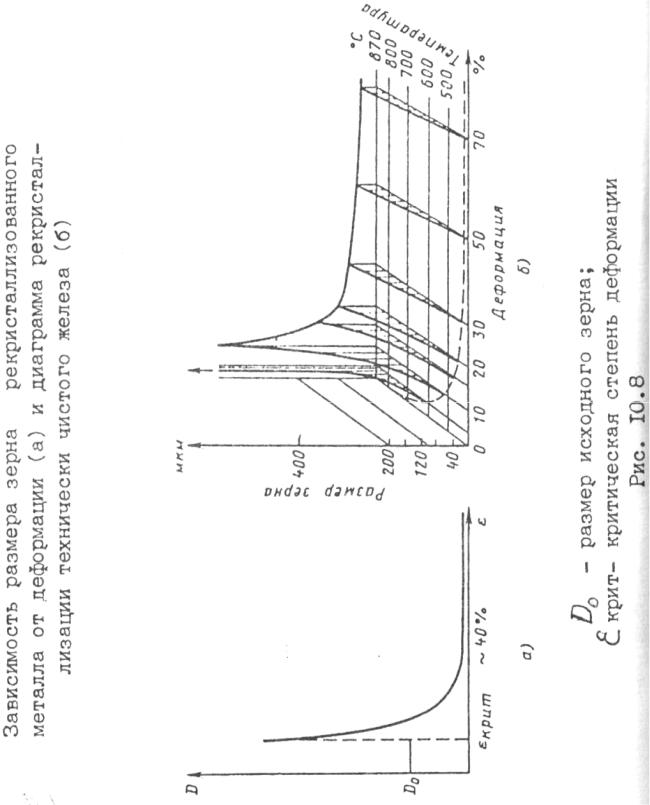
102
IV. МЕТОДИЧЕСКИЕ УКАЗАНИЯ ПО ВЫПОЛНЕНИЮ РАБОТЫ
Задание I
1.Установить влияние степени холодной пластической деформации на твердость технически чистого железа (степень деформации предварительно деформированных образцов 0,20 , 40 , 60 , 80%). Построить график.
2.Установить влияние температуры отжига (400, 500, 600, 700, 800°С, выдержка 30 мин) на твердость холоднодеформированного железа на образцах со степенью деформации 80%; построить график.
3.Определить температуру рекристаллизации.
4.Изучить влияние степени холодной пластической деформации и температуры отжига на микроструктуру железа, используя шлифы со степенью де-
формации 0,1, 20, 40, 60, 80%; шлифы после отжига при 550, 600, 700, 800°С.
Задание 2
1.Установить влияние степени холодной деформации на твердость алюминия (степень деформации предварительно деформированных образцов при растяжении составляет 0,3,7,10%). Построить график.
2.Произвести отжиг продеформированных образцов алюминия при 600ºС
втечении I ч (или при 560°С).
3.Выявить структуру образцов протравливанием в реактиве состава: НСl
-40 мл, HF - 15 мл, HNO3 - 12 мл, Н20 - 20 мл.
4.Изучить структуру, определить размеры рекристаллизованных зерен на
каждом образце, построить график в координатах: размер зерна - степень деформации.
Задание 3
1.Установить влияние степени холодной пластической деформации на твердость стали 20 (степень деформации 25, 50, 75%). Количество образцов в каждом случае не менее 3. Построить график.
2.Установить влияние температуры отжига (от 200 до 900°С с интервалом 50 или 100ºC) на твердость холоднодеформированной стали. Выдержка при температуре нагрева 30 мин. Твердость замеряется по методу Роквелла ( HRB ). Построить график в координатах: твердость - температура отжига.
3.Определить температуру рекристаллизации.
4.Изучить влияние степени холодной деформации и температуры отжига на микроструктуру стали 20.
103
V. ОФОРМЛЕНИЕ ОТЧЕТА
Отчет по лабораторной работе должен включать следующее:
1.Название, цель работы.
2.Краткие теоретические сведения.
3.Методику лабораторной работы (задание по лабораторной работе).
4.Данные испытаний, приведенные в табл. 10.2.
Таблица 10.2
Влияние степени деформации и температуры рекристаллизационного отжига на твердость и микроструктуру холоднодеформированного технического железа
Степень де- |
Температура |
Твердость |
Микроструктуры |
Характеристика |
|
формации |
отжига |
НRБ |
HB, МПа |
||
E, % |
Т, ºС |
|
|
|
|
|
|
|
|
|
|
5. Графики зависимости:
а) твердости от степени деформации; б) твердости от температуры нагрева и степени деформации;
в) величина рекристаллизованного зерна от степени деформации.
6.Анализ результатов испытаний.
7.Выводы по работе.
VI. ВОПРОСЫ ДЛЯ САМОПРОВЕРКИ
1.Чем характеризуется упругая деформация?
2.В чем различие между упругой и пластической деформацией?
3.Каким путем осуществляется пластическая деформация?
4.Какие напряжения вызывают пластическую деформацию?
5.Как влияет степень деформации на свойства металлов и сплавов?
6.Как изменяется плотность дислокаций при пластической деформации?
7.Как влияет плотность дислокаций на прочность металла?
8.Как изменяется структура металла при холодной деформации и как это влияет на свойства деформированного металла?
9.В чем сущность наклепа, и какое ок имеет практическое значение?
10.Как изменяются свойства деформированного металла при нагреве?
11.В чем сущность процесса возврата?
104
12.Что такое полигонизация?
13.В чем сущность процессов первичной и собирательной рекристалли-
зации?
14.Как влияет состав сплава и степень пластической деформации на температуру рекристаллизации?
15.От чего зависит величина зерна рекристаллизованного металла?
16.Что такое критическая степень деформации?
17.В чем различие между холодной и горячей пластическими деформа-
циями?
18.Для какой цели применяется рекристаллизационный отжиг?
105
ЛАБОРАТОРНАЯ РАБОТА № 11 ВЛИЯНИЕ ТЕРМИЧЕСКОЙ ОБРАБОТКИ НА МИКРОСТРУКТУРУ И
СВОЙСТВА УГЛЕРОДИСТОЙ СТАЛИ
a)3AКАЛKA И ОТПУСК СТАЛИ
I. ЦЕЛЬ PAБОТЫ. Выявить влияние закалки и отпуска на изменение структуры и механических свойств стали. 2. Овладеть методикой термической обработки стали.
II. КРАТКИЕ ТЕОРЕТИЧЕСКИЕ СВЕДЕНИЯ
Значения механических свойств во многом определяет поведение деталей и инструмента в эксплуатации.
Термическая обработка - один из основных способов влияния на строение, а следовательно, и на свойства стали. Основная цель термической обработки - изменение структуры и свойств металла без изменения формы и состава. Различают предварительную окончательную термическую обработку формирующих свойства готового изделия. Закалка к отпуск относятся ч окончательной термической обработке.
Для определения режима закалки и отпуска углеродистых сталей служит диаграмма состояния Fe – Fe3С% рис.8.1.
Закалка - вид термической обработки, заключающийся в нагреве выше критических температур Ас1 или Ас3 (расположенных по линиям РSK (A1) GSF (A3) на 30-50ºС, выдержки при этих температурах и последующего быстрого охлаждения в воде или масле. Доэвтектоидные стали нагревает выше Ас3, заэвтектоидные и эвтектоидные - выше Ас1 на 30-50ºС при неполной закалке и на 30-50ºС выше Асm при полной закалке. Цель закалки - получение закалочных структур (мартенсита, тробстита, сорбита и смешанных структур) и, следовательно, повышение твердости, прочности, износостойкости и других физикомеханических свойств.
Нагрев до определенной температуры можно провести любым нагревающим средством: в электропечах, газовых печах, токами высокой частоты и другими средствами. Выдержка при температуре нагрева чаще всего дается I мин на I мм сечения нагреваемого изделия. Охлаждающими средами могут быть:
вода, минеральное масло, растворы солей и щелочей.
Проведя закалку углеродистой стали с использованием различных охлаждающих сред можно получить для одной и той же стали структуру мартенсита, бейнита, троостита, сорбита. При охлаждении стали со скоростью выше критической V ≥ Vкр (диаграмма изотермического распада аустенита, рис.11.2) обра-
106
зуется структура мартенсит закалки. При этом превращении аустенита в мартенсит происходит перестройка решетки Feγ ГЦК в решетку Feα – ОЦК по сдвиговому механизму, без наделения углерода из решетки Feα – железа. Критической скоростью закалки (Vкр) называется минимальная скорость охлаждения, при которой получается структура мартенсит. Мартенсит - пересыщенный твердый раствор углерода в Feα. Мартенсит имеет тетрагональную кристаллическую решетку. Стальс мартенситной структурой имеет высокую твердость, прочность и малую пластичность.
Если использовать скорости охлаждения стали ниже критической (с температурой нагрева под закалку ), то можно получить продукты распада аустенита типа: бейните, троостита, сорбита, перлита.
Сущность превращения аустенита углеродистой стали при охлаждении может быть выражена схемой:
|
Feγ(с) → Ф + Ц[Feα(c) + Fe3С]. |
|
Троостит - |
мелкодисперсная смесь |
(Ф + Ц), |
Сорбит - |
мелкая смесь |
(Ф + Ц), |
Перлит - довольно-таки крупная смесь (Ф + Ц).
Отсюда по мере уменьшения дисперсности частиц феррите и цементите в структуре повышается твердость, прочность, но уменьшаются пластические свойства.
Сталь после закалки находится в напряженней состоянии, обладает высокой твердостью и хрупкостью. Для снятия внутренних напряжений, уменьшения твердости и повышения пластичности и ударной вязкости применяют операцию, называемую отпуском. Отпуск - это нагрев ниже температуры Acl , выдержка при данной температуре и произвольное охлаждение. Существуют три вида отпуска: низкий, средний, высокий. Отличаются они друг от друга температурой нагрева. Нагрев до определенных температур приводит к различным структурным превращениям, которые сказывают влияние на механические свойства. Низкий отпуск (150-200ºС) характеризуется тем, что структурных превращений не происходит. При данной температуре снимаются внутренние напряжения, мартенсит тетрагональный превращается в мартенсит отпущенный (кубический). При микроскопическом исследовании мартенсит отпуска имеет также игольчатое строение, но он более темный, чем мартенсит закалки. При среднем отпуске (300 450ºС) происходит распад твердого раствора (мартенсита) на дисперсную смесь феррита и цементита, называемую трооститом. Кроме этого, снимаются внутренние напряжения. При высоком отпуске.(500-600ºС) мартенсит также распадается на феррито-цементитную смесь, но более гру-
107

108
бую, которая называется сорбитом. Внутренние напряжения снимаются в большей степени нежели при первых двух видах отпуска.
С повышением температуры отпуска особенно выше 200ºС прочностные свойства как: твердость, временное сопротивление разрыву, предел текучести понижаются. Это объясняется размером и формой частиц феррита и цементита, из которых состоят продукты распада мартенсита (троостит, сорбит).
Высокие прочностные свойства и низкая пластичность при низком отпуске (150-200ºС) объясняются тем, что при этом сохраняется структура мартенсита отпуска. Свойства стали определяется содержанием; углерода в мартенсите.
При среднем отпуске (300-450°С) идет окончательный распад мартенсита отпуска на феррито-цементитную смесь большой степени диспэрсности - тростит. Это превращение характеризуется диффузионным перераспределением углерода по фазам (ферриту и цементиту). Выделение углерода из мартенсите способствует снятию напряжений II-го рода. Строение троостита различается только в электронном микроскопе. Для троостита характерна высокая упругость стали.
При высоком отпуске, проводимом при 500-600ºС, идет процесс сфероидизации цементных частиц с последующим укруплением. Такое зернистое строение средней степени дисперсности называется сорбитом.
В условиях высокого отпуска максимально снижаются внутренние закалочные напряжения, снижается твердость, прочность, но повышаются свойства пластичности. Сталь со структурой сорбита отпуска по сравнению со сталью, имеющей структуру сорбита закалки, имеет более высокую вязкость. Закалку с высоким последующим отпуском принято называть улучшением.
III. ОБОРУДОВАНИЕ, ПРИБОРЫ И МАТЕРИАЛЫ Для выполнения работы необходимо иметь:
1.Муфельную электрическую печь для закалки.
2.Муфельную электрическую печь для отпуска.
3.Термоэлектрические пирометры (термопары с гальванометрами).
4.Баки с различными закалочными средами,
5.Твердомер типа Роквелл (TК).
6.Образцы из углеродистой стали, напильник, шлифовальную бумагу, щипцы.
109
IV.МЕТОДИЧЕСКИЕУКАЗАНИЯИЗАДАНИЯПОВЫПОЛНЕНИЮРАБОТЫ
Работа выполняется бригадой в 5-6 человек, каждой бригаде преподаватель дает контрольное задание.
Задание I. Установить зависимость твердости от скорости охлаждения, для чего произвести закалку одной марки стали в различных охлаждающих средах: воде, масле, растворе каустической соды и подогретой до 70°С воде.
Задание 2. Установить зависимость твердости закаленной стали от содержания углерода, для чего произвести закалку различных марок сталей в одной и той не среде.
Задание 3. Установить влияние температуры отпуска на изменение твердости закаленной стали (по указанию преподавателя), произвести отпуск образцов закаленной слали на 200, 450, 600ºС.
Методические указания.
1.При заполнении любого задания подготовить образцы для определения твердости и для закалки.
2.Определить твердость образцов на приборе Роквелла.
3.Определить критического температуру нагрева под закалку по диаграмме состояния железо-углерод (см.рис.8.I) и результаты режима термической обработки записать в табл. 11.1. Эта таблица для первого задания.
4.Произвести закалку образцов по заданию.
5.Определить твердость образцов после закалки, предварительно зачистив образцы напильником, и наждачной бумагой.
6.Результаты испытаний твердости записать в табл. 11.2. Аналогичные таблицы для 2 и 3-го заданий составить самостоятельно.
|
|
|
|
|
|
|
Таблица 11.1 |
|
|
|
|
|
|
|
|
|
|
|
|
Диаметр или |
Температура на- |
Время выдержки, с |
|
|
||
№ |
Марка |
толщина об- |
грева, ºС |
|
|
|
Охлаждающая |
|
|
|
|
|
|
||||
п/п |
стали |
разца, мм |
под за- |
под от- |
для за- |
для от- |
|
среда |
|
|
|
калку |
пуск |
калки |
пуска |
|
|
|
|
|
|
|
|
|
|
|
7. Оформить табличные результаты:
а) построить график режима закалки и отпуска стали в осях "температуравремя" (примерный график показан на рис. 11 );
110

|
|
|
|
|
|
|
|
|
|
Таблица 11.2 |
|
||
|
|
|
|
Твердость образцов HB, кгс/мм |
после отпуска |
|
|||||||
|
|
|
|
|
|||||||||
№ |
Марка |
в исход- |
|
|
после закалки |
|
|
|
|||||
на |
в воде |
в мас- |
в воде |
в 10%-ном |
низко- |
сред- |
высо- |
|
|||||
п/п |
стали |
ном со- |
воз- |
при |
|
ле |
при |
растворе |
го |
|
него |
кого |
|
|
|
стоянии |
духе |
70°С |
|
|
20ºС |
каустиче- |
|
|
|
|
|
|
|
|
|
|
|
|
|
ской соды |
|
|
|
|
|
|
|
|
|
|
|
|
|
|
|
|
|
|
|
6) построить график зависимости твердости от скорости охлаждения содержания углерода в стали; температуры нагрева образцов при отпуске
V.ОФОРМЛЕНИЕ ОТЧЕТА
Вотчет должно быть включено следующее:
1.Описание назначения и цели работы.
2.Таблицы режима термической обработки и результаты замера твердости углеродистой стали после термической обработки (табл.11.1, 11.2).
3.Графики режима закалки и отпуска стали и зависимости твердости от различных параметров закалки и отпуска.
4.Заключение о проведенной работе.
VI. ВОПРОСЫ ДЛЯ САМОПРОВЕРКИ
1.Что такое закалка? Способы закалки доэвтектоидной и заэвтектоидной стали.
2.Цель закалки?
3.Какие структуры можно получить, проведя закалку?
4.Что такое мартенсит, бейнит, троостит, сорбит, перлит?
5.Что такое отпуск?
6.Цель отпуска?
7.Способы отпуска?
8.Какие структуры можно получить, проведя тот или другой отпуск?
9.Какими свойствами обладает сталь в состоянии мартенсита, бейнита, троостита, сорбита?
111
б) ИЗУЧЕНИЕ МИКРОСТРУКТУРЫ ТЕРМИЧЕСКИ ОБРАБОТАННЫХ УГЛЕРОДИСТЫХ СТАЛЕЙ
I. ЦЕЛЬ РАБОТЫ: I. С помощью металлографического микроскопа изучить микроструктуру углеродистых и легированных сталей после термической обработки.
2. Исследовать влияние отпуска на структуру и свойства стали. 2. КРАТКИЕ ТЕОРЕТИЧЕСКИЕ СВЕДЕНИЯ
Нагревая и затем быстро или медленно охлаждая сталь, можно изменить структуру металла и получить необходимые прочностные и технологические свойства. Такой процесс называется термической обработкой стали. Значение термической обработки весьма велико в машиностроении, поскольку без изменения состава стали можно получить необходимые свойства в деталях, а также подготовить металл к горячей и холодной обработке давлением и резанием.
Термической обработке подвергаются до 10% общей выплавки стали в стране. В машиностроении объем термической обработки достигает потребляемой стали этой отраслью промышленности.
Основными видами термической обработки являются отжиг, нормализация, закалка и отпуск. Отжиг производится для снятия внутренних напряжений, понимания прочности и твердости, уменьшает структурную неоднородность, измельчает зерно металла. Отжиг способствует повышению пластичности и ударной вязкости металла. Отжиг применяется для отливок, поковок, сортового и фасонного проката, труб, горячекатанных листов. В большинстве случаев отжиг является подготовительной термической обработкой, кроме крупных отливок и поковок. Полный отжиг заключается в нагреве стали на 30-50°С выше температуры точки Ас3, выдержке и последующем медленном охлаждении.
Изотермический отжиг обычно производится для легированной стали и осуществляется, как и полный отжиг, а затем производится быстрое охлаждение до температуры на 30-50ºС ниже точки Ач1. При этой температуре производят выдержку, после чего следует охлаждение на воздухе. Неполный отжиг отличается от полного тем, что сталь нагревается до температуры на 30-50°С выше точки Ac1. При неполном отжиге происходит только перекристаллизация перлита и последующее превращение его с пластинчатого в зернистый. Такой отжиг называют сфероидизацией. При этом не происходит измельчение зерна металла, а только устраняются внутренние напряжения и уменьшается прочность и твердость, с одновременным повышением пластичности и ударной вязкости.
112
Низкий отжиг или высокий отпуск широко применяется для снятия внутренних напряжений, возникших при сварке, в наклепанном металле, в отливках,
атакже для рекристаллизации металла.
Влегированных сталях после прокатки образуются закалочные структуры, что резко увеличивает твердость металла. Низкий отжиг способствует распаду закалочных структур, коагуляции и сфероидизации карбидов и в итоге снижает твердость металла. Низкий отжиг производится при температурах на
30-50ºC ниже точки A1 и последующем медлен ном охлаждением. Диффузионный отжиг или гомогенизация производится при температуре на 150-200ºС ни-
же точки Ас4 и последующем медленном охлаждении.
Диффузионному отжигу подвергаются слитки и стальные отливки с целью устранения дендритной и межзеренной ликвации.
Нормализация заключается в нагреве доэвтектоидной стали до темпера-
туры на 30-50ºС выше точки Ас3, а заэвтектоидной стали на 3050ºС выше точки Аст, выдержке и охлаждении на воздухе.
Нормализация вызывает полную фазовую перекристаллизацию стали и измельчает зерно стали, рис. 11.1.
Назначение нормализации различно в зависимости от состава стали. Для низкоуглеродистых сталей нормализация применяется, вместо отжига. Для средне- и высокоуглеродистой стали нормализация с высоким отпуском применяется вместо закалки и высокого отпуска и повышает твердость и прочность и измельчает зерно стали.
Нормализация легированных сталей повышает дисперсность ферритоцементной структуры и образует мелко-дисперсные смеси сорбит к троостит.
Основной диаграммой для изучения структуры и процессов, протекающих при нагреве и охлаждении стали, является диаграмма изотермического распада аустенита, рис. 11.2.
На диаграмме видны кривые начала и конца превращения и кривые раз-
личных случаев охлаждения V1, V2, V31, V4, V5. Отрезок времени от начала охлаждения до начала превращения называется инкубационным периодом. При высоких температурах (малая степень переохлаждения) процесс развивается медленно и инкубационный период большой, при снижении температуры инкубационный период снижается. Минимальная его величина при температуре 500-600ºС, при более низкой температуре инкубационный период увеличивается.
При малых V1 степенях переохлаждения аустенита (650-700ºС) получают структуру перлита. Перлит бывает пластинчатый и зернистый.
Пластинчатый перлит получается, когда сталь нагревается до тем-
113

114

Микроструктура стили после нормализации х200
Рис. 11.1
Диаграмма изотермического распада аустенита в эвтектоидной стали
а – диаграмма изотермического распада аустенита; б – влияние скорости охлаждения на температуру
превращения аустенита; в – количество структурных составляющих в эвтектоидной
стали
Рис. 11.2
115
пературы выше точки Ас3, рис.11.3. Зернистый перлит имеет место при нагреве стали до температуры ниже точки Ас3, рис.11.4. Частицы ферритоцементитной смеси просматриваются при увеличении в 200 раз. При средних V2 степенях переохлаждения аустенита (600-650ºС) происходит измельчение ферритоцементитной смеси. Такая структура называется сорбитом, рис.11.5. Частицы этой ферритоцементитной смеси просматриваются только при увеличении в 1000 раз. При переохлаждении аустенита до температуры минимальной устойчивости аустенита V3, вблизи изгиба кривой (500-600ºС), образуется мелкодисперсная ферритоцементитная смесь троостит, рис.11.6, Частицы этой ферритоцементитной смеси могут быть просмотрены только в электронный микроскоп при увеличении в 5000 раз.
Структура стали, полученная при температуре охлаждения ниже точки перегиба изотермического превращения V4, имеет игольчатый характер. Иглы эти состоят из пластинок феррита и цементита. Такая структура называется бейнит или игольчатый троостит, рис.11.7. Эта структура просматривается на электронном микроскопе при увеличении в 10000 раз.
Мартенситное превращение происходит при переохлаждении аустенита до таких температур, когда решетка неустойчива и происходит ее перестройка без выделения углерода V5. Такой процесс называется бездиффузионным. Мартенсит – это пересыщенный твердый раствор углерода в Feα - железе той же концентрации, что и у исходного аустенита, рис.11.8. Решетка перестраивается из гранецентрированной в объемноцентрированную. Решетка мартенсита тетрагональная, т.е. у нее параметр оси С больше параметра оси а.
Отношение Ca степень тетрагональности. Чем больше содержания угле-
рода в мартенсите, тем больше будет отношение и тем больше будут искажения кристаллической решетки. Из всех продуктов распада аустенита мартенсит обладает наибольшей твердостью и прочностью и наименьшей пластичностью.
Образование мартенсита происходит мгновенно и объясняется сдвиговыми явлениями, происходящими вследствие напряжений, возникающих при охлаждении аустенита. По мере охлаждения количество мартенсита увеличивается. Начало превращения отмечается точкой Мн, а конец – Мк. При конечной температуре все же остается какое-то количество аустенита, носящего название остаточного.
Превращению аустенита в перлит в заэвтектоидных сталях будет предшествовать выделение цементита. Так как при неполной закалке нагрев заэвтектоидной стали под закалку делается выше точки Ac1, но ниже Аст, то в результате такой закалки получают структуру мартенсит и вторичный цементит, рис.11.9.
116

Микроструктура пластинчатого перлита х500
Рис. 11.3
Микроструктура зернистого перлита х500
Рис. 11.4
Микроструктуре сорбита отпуска х500
Рис. 11.5
117
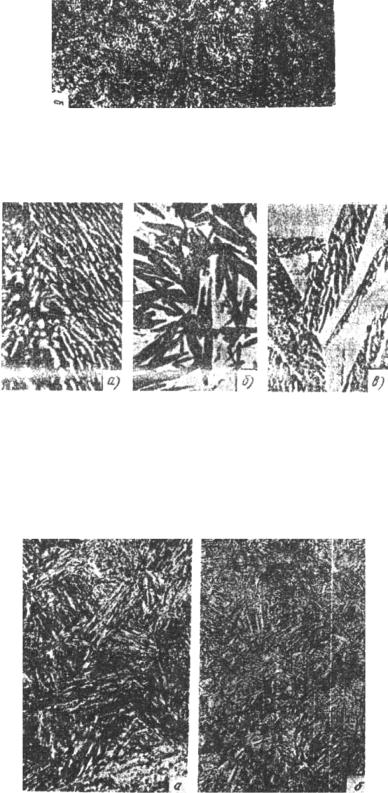
Микроструктуре троостита отпуска х500
Рис. 11.6
Микроструктура бейнита х500
а – верхний бейнит, б, в – нижний бейнит Рис. 11.7
Микроструктура мартенсита х500
а- кристаллы мартенсита крупные;
б- кристаллы мартенсита мелкие Рис. 11.8
118
Структура такой стали имеет высокую твердость, так как цементит, будучи сам по себе весьма твердым, не снижает твердость и износостойкость стали. Нагрев же под закалку заэвтектоидных сталей до температуры выше Асm приводит к перегреву стали, вырастают крупные зерна аустенита и после охлаждения стали получается хрупкий крупноигольчатый мартенсит.
Для разработки технологии термической обработки используют термокинетические диаграммы, рис.11.10. По этим диаграммам можно получить точные данные о температурных интервалах фазовых превращений при лэпрерьтном охлаждении и образующихся при этом структурных составляющих. Все легирующие элементы, кроме кобальта, замедляют изотермический распад аустенита и повышают тем самым прокаливаемость стали. Они сдвигают вправо с- образную кривую на диаграмме изотермического распада аустенита.
Превращение при отпуске происходит при температурах в интервале 70650ºС в закаленной стали. Основной структурой закаленной стали является мартенсит, поэтому процесс отпуска связан с изменением структуры мартенсита. Необходимо отметить, что мартенсит имеет максимальный объем, поэтому превращение аустенита в мартенсит связано с увеличением объема.
Превращение в мартенсите происходит в трех интервалах температур. Первое превращение при отпуске происходит в интервале температур от 70 до 200°С. Решетка мартенсита изменяется, переходя из тетрагональной в кубическую. Выделяется углерод в виде тонких пластинок карбида. После такого отпуска мартенсит называется отпущенным. Второе превращение происходит в интервале температур от 300 до 400ºС и характеризуется снятием внутренних напряжений. Одновременно с эти карбид обособляется с образованием мелких округлых включений в цементит. При температуре 400ºС превращение заканчивается, и структура состоит из троостита. Структура троостита отпуска состоит из дисперсных частиц феррита и цементита, причем эти частицы очень мелки по сравнению с перлитом. Сохранившаяся в троостите отпуска ориентировка по мартенситу в виде игольчатого строения отличает его от троостита закалки.
Третье превращение при отпуске происходит в интервале температур 500-650ºС и характеризуется не только снятием внутренних напряжений, но и одновременно распадом мартенсита на феррито-цементитную мелкодисперсную смесь-сорбит. Такой отпуск обеспечивает получение высоких пластических свойств и ударной вязкости, при сохранении достаточной прочности и твердости стали. Легирующие элементы замедляют процесс распада мартенсита при отпуске. Отпуск закаленных легированных сталей производится при более высоких температурах и длительности вдержки.
119

Микроструктура мартенсита и участков карбидов х200
Рис. 11.9
Термокинетические диаграммы превращения переохлажденного аустенита
а– эвтектоидная сталь;
б– доэвтектоидкая сталь
Рис. 11.10
120
3.ОБОРУДОВАНИЕ, ПРИБОРЫ И МАТЕРИМЫ
1.Металлографический микроскоп.
2.Набор микрошлифов термически обработанных сталей,
4.МЕТОДИЧЕСКИЕУКАЗАНИЯИЗАДАНИЯПОВЫПОЛНЕНИЮРАБОТЫ
1.Изучить микроструктуру углеродистой стали после закалки и отпуска и дать характеристику наблюдаемой структуры, указав наименование структуры и условия, необходимые для ее образования.
2.Установить зависимость между термической обработкой, структурой и механическими свойствами стали.
5.СОДЕРЖАНИЕ ОТЧЕТА
1.Зарисовать диаграмму изотермического превращения аустенита в эвтектоидной стали с наложенными на нее кривыми охлаждения.
2.Зарисовать микроструктуру стали с различной степенью переохлаждения аустенита, указав стрелками структурные составляющие и их наименование (феррит и перлит, перлит, сорбит, троостит, мартенсит, мартенсит и карбиды),
3.Указать условие образования структур при различной степени переохлаждения аустенита (феррит и перлит, перлит, сорбит, троостит, бейнит, мартенсит, мартенсит и карбиды).
4.Указать условия образования структур после различного вида отпуска и влияние вида отпуска на свойства стали.
6.ВОПРОСЫ ДЛЯ САМОКОНТРОЛЯ
1.Дайте определение диаграмме изотермического превращения аустенита при переохлаждении.
2.Укажите, при каких степенях переохлаждения образуются структуры – перлит, сорбит, троостит, бейнит, мартенсит.
3.Охарактеризуйте сущность бездиффузионного превращения аустенита в мартенсит.
4.Дайте определения продуктам распада аустенита: перлит, сорбит, троостит, бейнит.
5.Дайте определения мартенситу.
6.Для чего предназначены низкий, средний и высокий отпуски?
7.Какова структура закаленной стали после низкого, среднего и высокого отпуска?
8.Приведите режим и назначение нормализации.
121
9.Дайте характеристику физико-механическим свойствам продуктов распада аустенита.
10.Приведите режим и назначение улучшения стали.
11.Дайте характеристику полной и неполной закалки стали.
12.Приведите режимы и назначение отжигу I – рода.
13.Приведите режимы и назначение отжигу 2 – рода.
122

ЛАБОРАТОРНАЯ РАБОТА № 12 ИЗУЧЕНИЕ ОСНОВ ХИМИКО-ТЕРМИЧЕСКОЙ ОБРАБОТКИ СТАЛЕЙ.
ТЕХНОЛОГИЧЕСКИЕ ОСОБЕННОСТИ И МИКРОСТРУКТУРА
I. ЦЕЛЬ РАБОТУ: изучение структурных изменений и свойств в стали при диффузионном насыщении поверхностных слоев различными элементами (при цементации и нитроцементации, диффузионном хромировании борировании). Ознакомление с технологией химико-термической обработки сталей.
II. ТЕОРЕТИЧЕСКИЕ СВЕДЕНИЯ
ЦЕМЕНTAЦИЯ – процесс высокотемпературной обработки, заключающийся в насыщении поверхности стальных деталей при температурах выше С Ас3 из углеродосодержащей среды, находящейся в твердом, жидком или газообразном состоянии. Оптимальным содержанием углерода в диффузионном слое является 0,8-0,9% при толщине слоя до 1,2- 1,4мм .Однако для специальных конструкционных деталей и инструмента содержание углерода и толщина слоя могут быть выше.
Скорость диффузии атомарного углерода в железе характеризуется коэффициентом диффузии, величина которого зависит от количества вещества, продиффундировавшего через площадку в квадратный сантиметр в единицу времени при заданном перепаде концентраций. Коэффициент диффузии резко повышается с ростом температуры, зависимость от температуры выражается уравнением:
где А – коэффициент, характеризующий тип кристаллической решетки; Q – энергия активации; е – основание натурального логарифма;
В – газовая постоянная; Т – абсолютная температура.
Углерод и азот,образующие с железом твердые растворы .внедрения, диффундируют при прочих равных условиях в сталь быстрее, чем хром, бор, ванадий.
Легирующие элементы, не образующие карбидов (кобальт, никель) увеличивают коэффициент диффузии углерода в аустените, а карбидообразующие (хром, молибден, вольфрам) снижают коэффициент диффузии углерода.
123

Цементация стали непосредственно твердым углеродом невозможна, для диффузии необходимы активные атомы, образующиеся при диссоциации углеродосодержащих соединений -окиси углерода, метана и т.д.
2С0 C02+Сат; CH4 2H2+Caт.
При контакте атомарного углерода с поверхностью металла возникают химические связи, адсорбция углерода к поверхности. Прочность контактов адсорбированных атомов зависит от развитости и активности поверхности, наличия активаторов в этой зоне и от температуры процесса. Адсорбированные атомы проникают в глубинные подслои засчет диффузии. Для протекания процесса диффузионного насыщения необходима, постоянная стабильная диссоциация компонентов-источников углерода, адсорбция и температурное стимулирование процесса на границе газ-металл.
Все выше сказанное относится ко всем процессам химико-термической обработки, которые являются диффузионными будь-то цементация, азотирование, нитроцементация, либо диффузионной металлизации-борированию, хромированию, ванадированию, силицированию. I)
Виды химико-термической обработки по температурным интервалам и составам насыщающих сред многообразны. Так основные температурные интервалы диффузионной металлизации 1000-1100°C, цементации 900-1050ºС, нитроцементации 840-900°С, азотирования 520-600°С, карбонитрации 500700°С, сульфидирования – 200-350°С, оксидирования и нитрооксидирования 160-450°С. Цементация в твёрдом карбюризаторе, несмотря на вытеснение наст. время более прогрессивными процессами газовой цементации, и нитроцементации, является простым и универсальным процессом химико-термичес- кой обработки, осуществляемым в большинстве отраслей промышленности при мелкосерийном и разовом производстве деталей, а также на неспециализированных производствах и цехах ремонтных предприятий, в инструментальных цехах и участках судоремонта и судостроения.
Основой твердого карбюризатора, является древесный, березовый уголь фракций до 11-12мм ,в качестве активирующих, добавок на поверхность угля наносятся пасты из углекислого бария, углекислого кальция и мазута или патоки. В настоящее время применительно к легированным цементуемым сталям в качестве активаторов применяются углекислые соли и.ацетаты, оксалаты натрия.
I) - схема массопереноса диффундирующего элемента к поверхности стали приведена на рис. 12.1 на примере нитроцементации высоколегированной стали
20X13 (0,20%С и 13,0Сг%).
124

Перенос углерода и азота при нитроцементации стали в твердом карбюризаторе
1 - химреакции с образованием газовых компонентов;
2 - диффузия через газопроницаемый слой;
3 - хемсорбция и поверхностное окисление;
4- эвакуация продуктов реакций;
5- собственно диффузия атомарных углерода и азота
вметалле
Рис. 12.1
125

В процессе нагрева деталей при прогреве садки образуется двуокись углерода С02 как результат взаимодействия кислорода воздуха с активированным древесным углем. Одновременно соли бария, кальция, натрия разлагаются по реакциям:
Ca СО3→ CaO + СО2; Ва СО3→ВаО + CО2, Na2CO3→Na2O + СО2
ускоряют интенсифицирую процесс образования окиси углерода и увеличивают массоперенос атомарного углерода к поверхности стали:
СО2 + С = 2СО, а в присутствии в составе карбюризатора азотосодержащих компонентов по трем реакциям:
2СО СО2 + Сат; |
СН4 2Н2 + Сат; |
Вцементационном ящике при цементации в твердом карбюризаторе газо-
вая атмосфера содержит незначительное количество СО2 ≥ 0,7%, СО ≥ 28,5%, CH4 ≥ 0,45%, остальное азот.
Стандартные древесноугольные карбюризаторы для цементации содержат до 15-25вес% углекислого бария, до 3-5% углекислого кальция, до 1,5вес% связующей органики, остальное - древесный уголь. Они обеспечивают реальную скорость формирования диффузионного слоя при температурах процесса
900-940°С составляет 0,10-0,14мм/ч.
Цементация в твердом карбюризатора или диффузионная металлизация в порошковых составах осуществляется в камерных электропечах серии СНОреже в шахтных электропечах серии CШO- с укладкой деталей в цементационные сварные контейнеры или ящики с зазорами между деталями до 30мм при обязательной герметизации крышек глиняными и шамотносиликатными обмазками.
Лабораторные работы выполняются с применением малых камерных печей типа СНОЛ-1,6.2,5.1/9, СНОЛ-1,6.2,5.1/1 ОМ и аналогичных малой мощности. Металлографический анализ и изучение микро- и макроструктуры цементованных образцов проводится с использованием микроскопов ММР-4, МИМ-7 бинокулярных микроскопов MБС-9. Твердость после закалки и отпуска определяют на приборах Роквелл-ТК-2М.
Втабл. 12.1 приведены типовые составы, для проведения химико-терми- ческой обработки конструкционных деталей из углеродистых, легированных сталей, а также деталей приборостроения, режущего и формообразующего инструмента из легированных сталей в твердых смесях. Предварительно необходимо ознакомление с краткими данными по терминологии.
126

Цементация в твердом карбюризаторе в камерных печах СНО
I - ящик цементационный; 2 - крышка с шамотноглиняной обмазкой; 3 - контрольный образец-свидетель; 4 - детали; 5 - подовые нихромовые нагреватели печи.
Рис. 12.2.
127
Из основной терминологии:
ДИФФУЗИЯ – самопроизволъное распространение, перенос вещества в какойлибо среде в направлении убывания его концентрации, обусловленное тепловым движением ионов, атомов, молекул. Термодиффузия протекает при неравномерном или равномерном распределении температуры, которой и определяется скорость протекания физико-химических процессов.
ОБЬЕМНАЯ ДИФФУЗИЯ – в объеме материала характеризуется наиболее высоким значением энергии активации и низким коэффициентом диффузии в сравнении с п о в е р х н о с т н о й - диффузией.
ЭНЕРГИЯ АКТИВАЦИИ – наименьшая энергия, необходимая для интенсификации процесса физико-химического или химического, вследствие выведения системы из равновесного состояния, например, внешним, тепловым воздействием на обрабатываемый материал;
ЦЕМЕНТИТНАЯ СЕТКА – микроструктурная особенность малоуглеродистой стали после цементации при 900-1000°С с последующим замедленным охлаждением (карбиды цементитного типа Fе3С, (Fе, Сr)7С3 располагаются по границам зерен). Для разрушения цементитной сетки, исключения повышенной хрупкости диффузионного слоя проводят нормализацию деталей перед последующей закалкой.
АЗОТИРОВАНИЕ – насыщение азотом поверхностного слоя стали, чугуна, тугоплавких метилов при температурах от 500ºС до 1200°С для повышения износостойкости, коррозионной стойкости.
АЛИТИРОВАНИЕ – диффузионное насыщение поверхности сталей и сплавов алюминием для повышения жаростойкости, эрозионной и коррозионной стойкости.
БОРИРОВАНИЕ – насыщение поверхности бором для повышения поверхностной твердости, износостойкости и коррозионной стойкости.
СИЛИЦИРОВАНИЕ – диффузионное насыщение кремнием поверхности для повышения жаростойкости, кислотостойкости, износостойкости.
ДИФФУЗИОННОЕ ХРОМИРОВАНИЕ – насыщение поверхности стальных деталей хромом с целью повышения коррозионной стойкости, износостойкости, кавитационной стойкости при низких и высоких температурах, в том числе при действии магнитных и электрических полей.
БОРОСИЛИЦИРОВАНИЕ,БОРОТИТАНИРОВАНИЕ,КАРБОХРОМИРОВАНИЕи т.д. - процессы комплексного диффузионного насыщения деталей и инструмента одновременно несколькими элементами.
128

Таблица 12.1
Составы твердых смесей для проведения некоторых видов
сталей |
|
|
|
|
|
|
|
|
Температура и про- |
Наименование и ис- |
Активатор |
Наполнитель и способ |
|
|
точник основного |
процесса |
укладки деталей |
должительность про- |
|
диффундирующего |
диффузии |
|
цесса |
|
элемента |
|
|
|
|
Цементация |
|
|
|
|
Уголь древесный или ВаCO3, |
70% отработанного |
910-930ºС в контей- |
||
каменный бессерни- |
СаСО3, |
карбюризатора, остальнере 150x150мм, 9-11 |
||
стый фракции 6-10мм NaСO3 |
ное свежий, 15-20мм |
ч для слоя 1,2-1,4мм |
||
65-75%, обмазка ак- |
|
между деталями, |
на стали 15, 20 |
|
тиватором, суспен- |
|
крышка с прокладкой |
|
|
зией на мазуте – 4%, |
|
асбестом и обмазкой |
|
|
при сумме активато- |
|
глиной |
|
|
ров 21-31%. |
|
|
|
|
Диффузионное хромирование |
|
|
|
|
Порошок феррохрома NH4CI до |
25-30% окиси алюми- |
|
1050-1100ºС- в кон- |
|
или хрома металличе- 5-5,5% |
ния А12О3, предвари- |
|
тейнере диаметром |
|
ского электролизного или NН4F |
тельная обработка спе90мм, 6 ч, слой |
|||
заданной фракции, |
4-7% или |
ка, герметизация |
|
I20мкм на стали |
45-50% по весу, неодNaF, |
крышки сваркой, дре- |
|
10880 магнитомягкой |
|
нократное, использо- |
KBF4 до |
нажное отверстие в |
|
в приборостроении |
вание спека |
5% |
крышке. |
|
|
Борирование |
|
Расстояние между де- |
|
1000-1050°С, 6 ч, |
диффузионное |
|
талями не менее 8- |
|
слой 250-300мкм на |
Карбид бора В4С или |
|
10мм допускается притеплостойкой леги- |
||
аморфный бор, или |
|
менение плавких за- |
|
рованной стали в ин- |
ферробор 50-65%, ос- |
|
творов для герметиза- |
|
струментальном про- |
тальное наполнитель |
|
ции |
|
изводстве |
На рис.12.2 и 12.3 приведены эскизы контейнеров для проведения хими- ко-термической обработки в твердых карбюризаторах и смесях.
Более эффективными по производительности, по активному регулированию степени насыщения диффузионных свойств, а также по экологии являются процессы газовой цементации, нитроцементации, карбонитрирования, азотирования в атмосферах пиролиза органических бессажистых азотоуглеродосодержащих соединений и растворов в специальных шахтных и камерных муфельных печах, а такие в печах с вакуумированием рабочего пространства-серии СШЦ, США, СШВНЦ, СНВА.
В массовом и серийном производстве в машиностроении и автомобильной промышленности цементацию проводят в атмосфере неполного сжигания природного газа-эндогазе, а нитроцементацию в камерных агрегатах в природном газе с аммиаком и азотом.
129

Диффузионное карбоборирование деталей в шахтной малоэнергоемкой печи СШОЛ в цилиндрическом герметичном контейнере
1 - детали в порошковой засыпке;
2 - крышка, сваренная с контейнером;
3 - дренажное отверстие; 4 - силитовые нагреватели; 5 - ХА-хромель-алюмелевая термопара, при 1150 С - платино-плати- нородиевая термопара
Рис. 12.3
130
СТРУКТУРАИСВОЙСТВАСТАЛЕЙПОСЛЕХИМИКО-ТЕРМИЧЕСКОЙОБРАБОТКИ
Структура диффузионного слоя стала при высокотемпературной цементации и нитроцементации с последующим медленным охлаждением состоит из продуктов распада высокоуглеродистого аустенита-перлита и цементита избыточного вблизи поверхности. Вслед за заэвтектоидной зоной, содержащей до 1,1-1,2% углерода, наблюдается зона пластинчатого перлита со следами цементитной сетки. Далее, по мере плавного снижения через доэвтектоидную зону феррита и перлита переход к структуре феррита малоуглеродистой стали. На рис.12.4а приведена структура цементованной стали 10 с цементитной сеткой.
За глубину цементации принимают величину заэвтектоидной, эвтектоидной и половины доэвтектоидной зоны. После нормализации и закалки от температуры 780-800°С твердость поверхности составляет НRСЭ=60-62 при твердости переходной доэвтектоидной зоны HRCЭ=50-54.
При цементации и нитроцементации легированных цементуемых сталей зачастую закалку проводят непосредственно от температур диффузионного насыщения 860-900°С с охлаждением в масле и последующимнизким (160-180°С) отпуском на твердость слоя НRСЭ=60-64. Чаще проводят нитроцементацию в процессе нагрева, для закалки теплостойких штамповых сталей, при этом закалку проводят с охлаждением в масле или ступенчатым охлаждением в расплавах щелочей. На рис. 12.46 приведена структура легированной теплостойкой стали после нитроцементации, закалки и отпуска при твердости слоя НRСЭ=5256 и твердости основного металла НRСЭ=38-42.
Цементация и нитроцементация с последующей термообработкой повышает предел выносливости конструкционных деталей, износостойкость инструмента, при этом, как правило, снижает чувствительность к концентраторам напряжений, если слой непрерывен по всей поверхности.
Более высокую твердость получают при азотировании деталей из конструкционных сталей типа 38ХМЮ и инструмента из быстрорежущих .сталей ти-
па Р6М5, Р6М5К5, Р12 (рис. 12.4в) с микротвердостью выше Н0,49=1100...1150. Одновременно с повышением коррозионной стойкости увеличивается износо-
стойкость при всех видах контактного износа.
Высокотемпературной нитроцементацией в твердых карбюризаторах получают износостойкие формообразующие и режущие инструменты, например, при ротационном резании, из быстрорежущих сталей Р6М3, Р6М5, PОМ6ФЗС. Количество карбидов и карбонитридов в диффузионном слое составляет 6070%вес. Микроструктура нитроцементованной (карбидизированной) стали
131
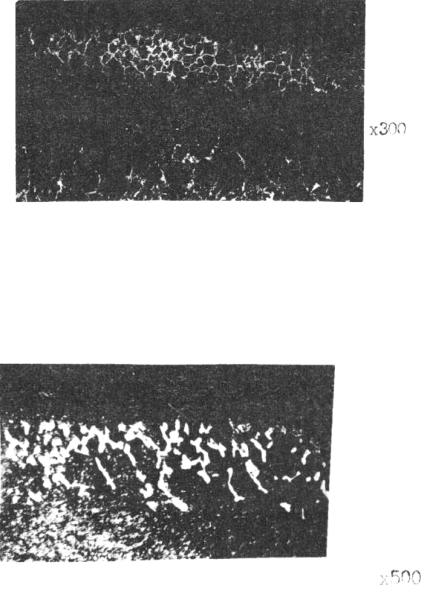
Микроструктура углеродистой (а) (г) цементованной стали, легированной (б) нитроцементованной и азотированной (в) высоколегированной стали, прошедших ХТО при различных температурах
а) Цементированная углеродистая сталь 10 (избыточные карбиды в заэвтектоидной зоне с 1,15%С и цементитная сетка в подслое-цементация в твердом карбюризаторе при 920 С)
б) Легированная сталь ЗОХМСФ после нитроцементации в процессе нагрева для закалки при 900 С (зона избыточных карбидов в диффузионном слое)
Рис. 12.4
132

в) Азотированный режущий инструмент из быстрорежущей стали PI2, слой Е - нитридов на рабочей поверхности метчиков по асботекстолиту и текстолиту. Газовое азотирование 560 С, 180 мин
Рис. 12.4
г) Слой диффузионного хрома на стали 10880 – х.т.о. в порошковой смеси, 1100ºС, 6 ч, х150
Рис.12.4
133

Макроструктура (а) и микроструктура (б) по центру нитроцементованного (карбидного) диффузионного слоя на режущих элементах ротационного резания из стали Р6М5-П
а) Макроструктура (косой |
б) Микроструктура-карбидная |
срез), х2,5 |
зона, х500 |
|
Рис. 12.5 |
Микротвердость по сечению борированного слоя на стали 4Х5МФС, х430. (Микротвердость последовательно Н0,49 = 1640, 1512, 1311, 870, 880)
Рис. 12.6
134
P6M5-П приведена на рис. 12.5. Твердость слоя, содержащего карбиды влажного состава ( Fe, Сr)7,С3, (Fe, Mo, W)2C, составляет Н = 980 - 1040, а износостойкость при резании улучшенных конструкционных сталей приближается к твердым сплавам вольфрамо-кобальтовой группы.
Боридные и карбоборидные слои, образующиеся при диффузионной металлизации в порошковых смесях имеют менее выраженную столбчатость зоны боридов, чем при борировании из паст или электролизном борировании, более плавный переход к подслою твердого раствора бора в железе. Но твердость боридного слоя также весьма высока H0,49 = 1600 - 1800, что обеспечивает стойкость поверхности против абразивного износа. На рис.12.5 приведен карбоборидный слой с отпечатками измерения микротвердости на приборе ПМТ-3.
III.ОБОРУДОВАНИЕ, ПРИБОРЫ И МАТЕРИАЛЫ
1.Малые камерные печи типа СН0Л-1,6.2,5.1/9; СН0Л-1,6.2,5.1/1ОМ.
2.Металлографические микроскопы МИМ-7, ММР-4, ММУ-3М.
3.Твердомеры Роквелла (модель ТК-2М).
4.Набор макромикрошлифов углеродистых и легированных сталей после цементации, нитроцементации, азотирования, борирования.
5.Атласы (альбомы) с фотографиями микроструктур сталей.
IV. МЕТОДИЧЕСКИЕ УКАЗАНИЯ ПО ВЫПОЛНЕНИЮ РАБОТЫ
1.Подготовить, уложить в малый контейнер с твердым карбюризатором (древесноугольный стандартный или в смесь древесного угля, соды кальцинированной) образцы для металлографического исследования и проволочные или ленточные контрольные образцы-свидетели из сталей 10; 15, ст.3.
2.Провести загрузку контейнера в печь и цементацию при 920-950ºС в течение 1,5-2 ч. с последующим охлаждением контрольных образцов в масле или воде,
аохлаждение остальных образцов на воздухе, в контейнере.
3.Провести дополнительную закалку нормализованных на воздухе образцов от температуры 780-800ºС в масле или воде, измерить твердость закаленных и отпущенных образцов по поверхности и сердцевине.
4.Ознакомиться с микроструктурой цементованной углеродистой стали при различных условиях термообработки, зарисовать структуру диффузионного слоя и сердцевины. Ознакомиться со структурами диффузионных слоев на легированных и высоколегированных сталях при цементации, хромировании, азотировании, нитроцементации.
135
V. СОДЕРЖАНИЕ ОТЧЕТА
Отчет по лабораторной работе должен включать следующее:
1.Название, цель работы,
2.Краткие теоретические сведения.
3.Методику лабораторной работы (задание по работе).
4.Указать состав твердого карбюризатора, режим цементации, термообработки.
5.Зарисовать микроструктуру (схематически) стали после цементации (до и после термообработки), азотирования, указав структурные составляющие.
6.Провести замер твердости различных зон образцов стали после ХТО.
7.Рисунки структур выполнять карандашом.
VI. ВОПРОСЫ ДЛЯ САМОПРОВЕРКИ.
1.Понятие химико-термической обработки, основные необходимые условия для проведения обработки.
2.Характер процессов, протекающих при химико-термической обработки, влияние температуры, строения элементов, времени выдержки на свойства и структуру диффузионных слоев.
3.Цементация сталей в твердом карбюризаторе, стали для цементации, особенности технологического процесса, пример осуществления.
4.Термическая обработка деталей из цементованной углеродистой и малолегированной конструкционной стали, пример.
5.Скорость цементации и глубина цементации, свойства цементованного слоя и сердцевины.
6.Эксплуатационные характеристики цементованных и термообработанных деталей машин.
7.Названия и примеры других видов химико-термической обработки, назначение и влияние на свойства сталей.
136
ЛАБОРАТОРНАЯ РАБОТА № 13 ЗОНА ТЕРМИЧЕСКОГО ВЛИЯНИЯ В СВАРНЫХ СОЕДИНЕНИЯХ
I. ЦЕЛЬ РАБОТЫ: изучить структурные превращения, протекающие при сварке в зоне термического влияния.
II. КРАТКИЕ ТЕОРЕТИЧЕСКИЕ СВЕДЕНИЯ
При электрической дуговой, газовой и других способах сварки металл в сварном шве и в прилегающих к нему участках нагревается. При сварке сначала происходит резкое повышение температуры в около шовной зоне, а затем замедленное, но все же достаточно быстрое охлаждение, главным образом за счет отвода тепла в прилегающие холодные слои металла (рис.13.I).
Максимальная температура, до которой нагревается металл в прилегающих к шву участках, зависит от расположения участков от расплавленного металла сварного шва. На границе шва максимальная температура равняется температуре плавления металла. По мере удаления от сварного шва температура металла понижается, вплоть до температуры окружающей среды.
Результаты теплового воздействия на металл зависят от способности данного металла подвергаться термообработке.
Участок свариваемого металла, в котором произошли структурные изменения, вызванные нагревом, называется зоной термического влияния. Малочувствительные к термообработке низкоуглеродистые стали при сварке мало изменяют свою структуру и механические свойства. Если же металл чувствителен к термообработке, то его структура и механические свойства резко изменяются. При этом могут образовываться как закалочные хрупкие структуры, приводящие к трещинам, так и крупнозернистые структуры, значительно снижающие предел прочности, текучести и другие свойства металла. В подобных случаях наиболее слабым местом сварного соединения будет не наплавленный металл, а металл зоны термического влияния. В связи с этим при сварке приходится применять специальные мероприятия: изменение теплового режима сварки, предварительный и сопутствующий подогрев и последующую термообработку.
Для некоторых материалов, например, дуралюмина, стали Гатфильда (11ОГ 13Л) и др. при сварке в зоне термического влияния происходят необратимые процессы, приводящие к ухудшению структуры металла, не восстанавливаемой последующей термообработкой.
Рассмотрим изменение микроструктуры низкоуглеродистой стали 20,
137
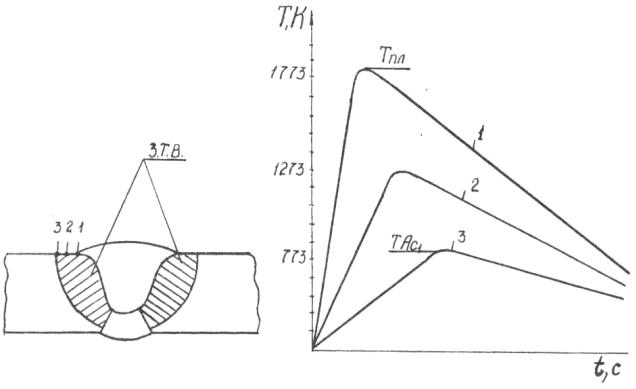
График термического цикла нагрева изделия дугой при сварке встык
Рис. I3.I
138
происходящие в зоне термического влияния при сварке (рис.13.2). Участок наплавленного металла получается за счет расплавления присадочного и свариваемого металла. Структура наплавленного металла зависит от скорости охлаждения. Чем быстрее охлаждение металла, тем больше образуется центров кристаллизации и тем мельче будет размер зерна.
При медленном охлаждении в процессе кристаллизации металл приобретает столбчатое строение. Зерна такой формы называются дендритами и имеют строение характерное для литого металла.
Участок частичного оплавления (1-2), находящийся в интервале температур между ликвидусом и солидусом, переходный от наплавленного металла к свариваемому металлу. Ширина этого участка мала, но его роль в сварном соединении велика. Здесь происходит образование металлической связи между металлом шва и свариваемым металлом. На этом участке произошел сильный рост зерен металла и наблюдается большая химическая неоднородность, вызванная перемещением углерода и приметой в жидкий металл. Ширина участка относительно невелика (0,1-0,5мм).
На участке перегрева - (2-3) температура изменяется в интервале 1500 - 1100°С. Тепловой цикл сварки вызвал значительный рост зерна. Этот участок бывает сильно развит у швов, имеющих большое сечение и сваренных ацети- лено-кислородной и дуговой сваркой. На этом участке можно наблюдать крупные пластинчатые выделения феррита (видманштетова структура). Зерно кипящей низкоуглеродистой стали склонно к росту, поэтому в сварных соединениях из этой стали участок с крупным зерном более широкий, чем в аналогичных соединениях из спокойной и полуспокойной стали.
Перегрев снижает механические свойства стали, главным образом пластичность и сопротивление ударным нагрузкам. Участок перегрева является самым слабым местом в сварном соединении, поэтому здесь чаще всего происходят разрушения. Ширина участка перегрева может достигать 3-4 мм.
По мере удаления от шва температура металла понижается. В пределах температур 900-1100°С находится участок нормализации (3-4) с мелкозернистой структурой. Металл участка нормализации обладает повышенными механическими свойствами в интервале температур от-40ºС до +200°С. Ширина его составляет до 4-5 мм.
На участке неполной перекристаллизации (4-5), в интервале температур 723-900°С, произошла частичная перекристаллизация. В первую очередь превращения захватили перлитные зерна, они и часть ферритных зерен превратились в аустенит и при охлаждении остались неизмельченными ферритные зерна и измельченные зерна перлита. Обычно ширина этого участка находится в пределах от 0,1 до 5 мм.
139

Микроструктура зоны термического влияния низкоуглеродистой стали 20
Рис. 13.2
140
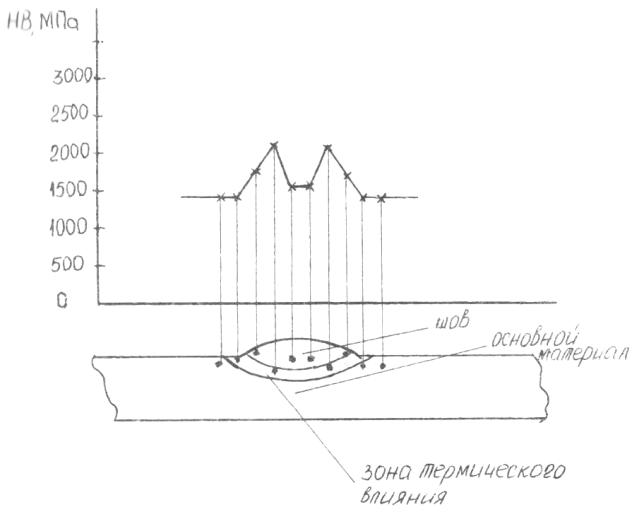
Изменение твердости по длине зоны термического влияния низкоуглеродистой стали
Рис. 13.3
141
Участок (5-6) - участок рекристаллизации. Он находится в интервале температур 450-727°С и существует только в наклепанной стали. Раздробленные и вытянутые при пластической деформации зерна в интервале температур 450727°С стремятся принять равноосную форму. При температуре 650-727ºС может произойти собирательная рекристаллизация, приводящая к росту зерна. Участок рекристаллизации сохраняет текстуру. Ширина этого участка 0,1-5 мм.
Участок (6-7) называется участком синеломкости. Он находится в интервале температур 200-450ºС. При этих температурах стали склонные к старению. По границам зерен выпадают нитриды и карбиды, в результате чего снижается пластичность стали. Обычные металлографические методы не позволяют обнаружить эти включения. У сталей, не склонных к старению, участок синеломкости отсутствует. Ширина этого участка достигает до 4 мм.
Нагрев стали ниже 200°С не вызывает изменений структуры и свойств Участок свариваемого металла, претерпевший изменение структуры и свойств под воздействием термического цикла сварки, называется зоной термического влияния. Ширина зоны термического влияния, в основном, зависит от погонной энергии при сварке. При ручной дуговой сварке она составляет 5-6 мм, при автоматической под флюсом - до 10 мм и при газовой сварке - до 25 мм.
Характерным является изменение твердости металла в зоне термического влияния (рис.13.3). Наибольшая величина твердости наблюдается в местах сплавления основного и наплавленного металла и на участке, прилегающем к наплавленному шву. Увеличение твердости на этих: участках у низкоуглеродистых и среднеуглеродистых сталей вызвано повышенным содержанием углерода за счет миграции его из основного в наплавленный металл. На участках с повышенной твердостью в этих сталях наблюдается значительное содержание перлита. Повышение твердости обычно связано с повышением прочности и снижением пластичности металла.
Увеличение твердости на этих участках достигает 20-30% и снижение пластичности на 10-15%, однако это не оказывает существенного значения на общую прочность сварного соединения. В сварных соединениях не допускается увеличение твердости в зоне термического влияния свыше HB = 2500 - 3000 МПа. Для снижения твердости в зоне термического влияния используют специальные технологические мероприятия или последующую термообработку.
Ш. ОБОРУДОВАНИЕ, ПРИБОРЫ И МАТЕРИАЛЫ I. Металлографический микроскоп МИМ-7.
142
2.Набор микрошлифов образцов из стали 20, сваренных ручной дуговой сваркой электродами с качественным покрытием, автоматической сваркой под слоем флюса, в среде углекислого газа и газовой сваркой.
3.Твердомер Роквелла.
4.Диаграмма железо-цементит (углерод).
IV. МЕТОДИЧЕСКИЕ УКАЗАНИЯ И ЗАДАНИЯ ПО ВЫПОЛНЕНИЮ РАБОТЫ
I. Просмотреть зону термического влияния на микрошлифе сварного соединения под микроскопом и зарисовать структуру и участок диаграммы железо-уг- лерод, соответствующий рассматриваемой марке свариваемой стали. Объяснить природу структурных превращений в зоне термического влияния.
2.Приготовить макрошлиф сварного соединения. Протравить макрошлиф реактивом состава 50% HCl и 50% Н2О в течение 15 мин.
3.Согласно схеме, рис.13.3, замерить твердость на приборе Роквелла по шкале В, через каждые 1-2 мм.
V. СОДЕРЖАНИЕ ОТЧЕТА
1.Зарисовать микроструктуру зоны термического влияния сварного соединения
и участок диаграммы Fe – Fe3C для рассматриваемой марки свариваемой стали,
рис.13.2.
2.Объяснить причину структурных превращений в зоне термического влияния.
3.Зарисовать график распределения твердости по сечению зоны термического влияния, согласно схеме (рис.13.3).
4.Объяснить причину увеличения твердости в околошовной зоне.
VI. ВОПРОСЫ ДЛЯ САМОПРОВЕРКИ
1.Дайте определение зоны термического влияния в сварных еоединениях.
2.Из каких участков состоит зона термического влияния в низкоуглеродистых конструкционных сталях.
3.Объясните причину структурных превращений в зоне термического влияния.
4.Объясните увеличение твердости металла в зоне термического влияния.
5.Укажите, как влияет способ и технологический режим сварки на протяженность участков зоны термического влияния.
6.Укажите, как влияет зона термического влияния на механическую прочность сварного соединения.
7.Укажите, какие технологические мероприятия применяются для снижения твердости в зоне термического влияния.
143
ЛАБОРАТОРНАЯ РАБОТА № 14 ИЗУЧЕНИЕ СТРУКТУРЫ И СВОЙСТВ ЛЕГИРОВАННЫХ СТАЛЕЙ
I.ЦЕЛЬ РАБОТЫ: изучить влияние легирующих элементов на структуру
исвойства легированных сталей; ознакомиться с различными классами сталей.
II.КРАТКИЕ ТЕОРЕТИЧЕСКИЕ СВЕДЕНИЯ
Современная техника предъявляет весьма разнообразные требования к материалам. Одни изделия должны обладать высокой прочностью как при низких, как и при высоких температурах, другие - устойчивостью против коррозии, третьи - высокой красностойкостью и т.д. Большое число такого рода задач решается на основе применения легированных сталей.
Легированными называют стали, содержащие в своем составе кроме железа и углерода специально введенные элементы и в таком количестве, которое способно изменить их строение, а следовательно, и свойства. Наиболее распространенными легирующими элементами являются: Cr, Ni, Mn, Si, W, V, Мо, Ti, Al, Nb, Cu и др.
Применение легированных сталей взамен менее прочных углеродистых позволяет значительно снизить металлоемкость конструкций. Свойства легированных сталей определяются типом твердого раствора, его составом, размером зерна, распределением в объеме второй фазы и дислокационной структурой.
Легирующие элементы изменяют свойства фаз, из которых состоит структура стали (феррита, аустенита, мартенсита, карбидов). При взаимодействии легирующих элементов с железом образуются легированные твердые растворы или интерметаллические соединения при высоком содержании легирующих элементов в стали (фазы Лавеса, сигма фазы).
Атомы легирующих элементов, не образующие карбидов (никель, кремний, медь, кобальт), полностью растворяются в Феррите или при температурах выше критических – в аустените, при этом изменяются свойства феррита и аустенита.
Атомы карбидообразующих элементов растворяются в карбиде железа (цементите) при содержании хрома до 2%, молибдена до 1%, вольфрама до 0,2% и т.д., образуя легированный цементит или при большом количестве карбидообразующих элементов образуют химические соединения с углеродом (специальные карбиды) - первичные или вторичные, которые при нагреве свыше критических точек растворяются в аустените. Устойчивые карбиды титана, циркония, ванадия, молибдена, вольфрама
144
(первичные) сохраняются в структуре при нагреве до высоких температур скрепляя дислокации.
В процессе закалки стали происходит превращение аустенита в мартенсит, что способствует сохранению высоколегированных твердых растворов, соответственно количество карбидов в сталях после закалки становится меньше, чем в отожженном состоянии.
По характеру влияния на критические температуры полиморфного превращения железа (А3 и А4) легирующие элементы можно разбить на две группы. К первой группе относят такие элементы как Ni, Mn, Cu, Pt, N и др., имеющие кристаллическую решетку ГЦК. Они расширяют область аустенита ( γ - область), а некоторые из них (например, Ni или Mn ) при содержании в сталях в достаточном количестве (точка х) могут снизить температуру превращения γ→α ниже комнатной температуры (рис.14.1). В этом случае сплавы даже при медленном охлаждении могут иметь структуру аустенита.
Другая группа элементов: хром, кремний, вольфрам, молибден, ванадий и др., имеющих кристаллическую решетку ОЦК, ограничивают область существования γ - раствора (рис.14.2). При содержании таких элементов более у%, сплавы теряют способность к переходу в аустенитное состояние и при всех температурах имеют строение α - твердого раствора (структура феррита).
Ферритные и аустенитные стали при нагревании не имеют вторичных превращений.
Легированный феррит и легированный аустенит прочнее соответствующих структур в углеродистых сталях. При легировании сталей 4-5% марганца или кремния их прочность повышается более: чем в 2 раза, однако следует иметь ввиду, что введение в стали более 0,5-1,0% легирующих элементов, за исключением никеля, значительно снижает ударную вязкость сплавов.
Все легирующие элементы (кроме кобальта) уменьшают критическую скорость закалки (Vkp) и поэтому легированные стали принимают закалку (т.е. приобретают структуру мартенсита) при меньших скоростях охлаждения (например, при охлаждении в масле или даже на воздухе).
Легирующие элементы способствуют измельчению структуры, что значительно повышает прочностные характеристики сплавов и обеспечивают большую глубину прокаливаемости деталей, изготовленных из легированных сталей.
Легированным сталям присуди и определенные пороки; так называемое явление отпускной хрупкости; дендритная ликвация (устраняется диффузионным отжигом); образование флокенов.
Классификация сталей по структуре в равновесном (стабильном)
145

146

147

148
состоянии отличается некоторой условностью. Существует два вида классификации:
а) по структуре после отжига; б) по структуре после нормализации (нагрева до температуры 900ºС и охлаждения на воздухе).
Необходимо отметить, что граница между доэвтектоидными, заэвтектоидными, ледебуритными легированными сталями проходит при меньшем содержании углерода, чем у углеродистых сталей, так как большинство легирующих элементов смещают точки S и Е диаграммы состояния Fe – Fe3C к меньшим концентрациям углерода (рис.14.3). Так, например, при содержании в стали 0,6% С и 5% Cr она является заэвтектоидной, а сталь с тем же содержанием хрома и 1,5% С - ледебуритной.
Легирующие элементы V , Ti ,Mb сдвигают точки S и Е вправо к большим концентрациям углерода.
При введении в сталь легирующих элементов, расширяющих α - область, получим структурную диаграмму (рис. 14.4а). В этом случае будем иметь следующие пять классов сталей: I - доэвтектоидный, II - заэвтектоидный, III - ледебуритный, IV - полуферритный, V - ферритный.
При введении в сталь легирующих элементов, расширяющих γ - область, получим структурную диаграмму (рис. 14.46). В этом случае будем иметь следующие классы сталей: I - доэвтектоидный, II - заэвтектоидный, III - ледебуритный, IV - полуаустенитный, V - аустенитный.
Доэвтектоидные, заэвтектоидные и эвтектоидные стали независимо от структуры (дисперсности) эвтектоида обычно объединяют в один класс-пер- литные стали.
Таким образом, основываясь на фазовом равновесии, по структуре после отжига легированные стали делят на классы: перлитный, аустенитный, ферритный, ледебуритный (карбидный) - рис. 14.6.
Классификация сталей по структуре после нормализации более условна, хотя удобна с практической точки зрения. По этой классификации стали делят на 5 классов: перлитный, мартенситный, аустенитный, ферритный, ледебуритный. По структуре сталей можно судить и о их свойствах. Например, стали перлитного класса обладают небольшой твердостью и высокой пластичностью, а стали мартенситного класса весьма твердые и хрупкие. Примерный состав и класс некоторых сталей приведен в табл. 14.1.
I. Перлитный класс. К этому классу относят низколегированные стали с суммой легирующих элементов не более 5% (например, 40Х, 30ХН3А, 15ХСНД и др.), поэтому эти стали сравнительно недорогие. Стали перлитного класса в литом состоянии имеют крупнозернистую фэрритоперлитную структуру (сорбитную, бейнитную). Поэтому заготовки сначала подвергают отжигу (иногда нормализации) для уменьшения
149

Структурная диаграмма коррозионностойких сталей (диаграмма Шеффлера)
Экв. Ni = %Ni + 30%C + 0,5%Мп; Экв. Сг = %Сг + %Мо + 1,5% Si + 0,5%Nb;
Ф - феррит; А - аустенит; М - мартенсит Рис. 14.5
150
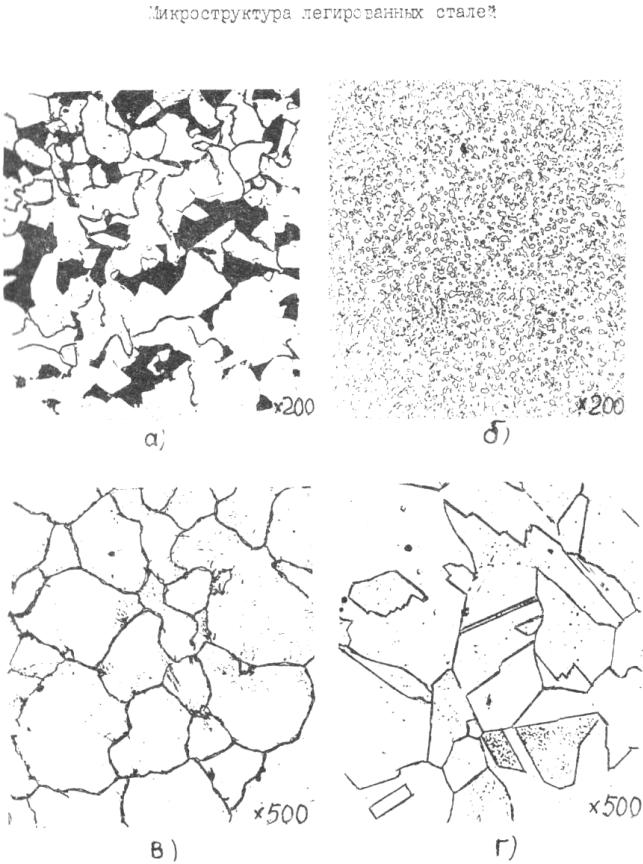
151

a - низколегированная корпусная (строительная) сталь, перлитный класс; б - шарикоподшипниковая сталь (после отжига), мартенситный класс; в - нержавеющая сталь, ферритный класс; г - нержавеющая сталь, аустенитный класс; д - быстрорежущая сталь в литом состоянии, ледебуритный класс; е - быстрорежущая сталь после термообработки, карбидный класс; ж - низколегированная инструментальная сталь; з - твердый вольфрамовый сплав
Рис. 14.6
152
зерна к степени ликвации - образуется дисперсная ферритокарбидная структура. К этому классу принадлежит большинство конструкционных и инструментальных сталей. Конструкционные судостроительные и строительные низкоуглеродистые стали (09Г2С, 10ГСНД, 10ХСНД и др.) отличаются хорошей свариваемостью, пластичностью, применяются при постройке (удов, конструкций. Конструкционные стали с содержанием 0,3 - 0,5%С (40Х, 45ХН, 38ХМА и др.) нашли широкое распространение при изготовлении деталей машин (оси, валы, шестерни). Стали с содержанием углерода 0,6-0,7% идут на изготовление
рессор и пружин (65Г2, 70СЗА и др.).
Легирующие элементы, увеличивающие прокаливаемость, дают возможность получать высокие механические свойства в деталях больших сечений. Из легированных сталей с содержанием 0,4-0,6%С (50ХНМ, 40ХНВ и др.) изготавливают инструмент для горячей обработки давлением (штампы, матрицы, пуансоны и др.). Для изготовления режущего и мерительного инструмента широко применяют легированные высокоуглеродистые стали с содержанием углерода 0,8% и более (90ХС, ХБГ). После соответствующей термической обработки (закалки с низким, отпуском) эти стали обладают высокой твердостью и износостойкостью.
2.Стали мартенситного класса содержат повышенное количество легирующих элементов, и их охлаждение на воздухе приводит к образованию мартенситной структуры с карбидами. Наибольшее распространение получили мартенситные нержавеющие стали, из которых изготавливают хирургический инструмент, ножи (30X13, 40X13) и другие стали, работающие в коррозионной среде.
3.Ферритный класс.
Стали ферритного класса имеют структуру феррита или феррита с карбидами. Наиболее известными являются стали, содержащие от 13 до 25-28% Cr
при содержании углерода менее 0,1-0,2% (08X13, 12X17, 15X25, 15X28). Они отличаются коррозионной стойкостью в агрессивных средах, высоким сопротивлением окислению при нагреве - окалиностойкостью (жаростойкостью).
Стали с повышенным содержанием кремния (до 4%) и малым содержанием углерода (0,01%) - электротехнические стали (1212, 2111, 3412 и др.) применяются для изготовления якорей и полюсов электротехнических машин, магнитопроводов и т.д. Они обладают высокой магнитной проницаемостью при малых потерях на перемагничивание.
4. Аустенитный класс. Стали аустенитного класса содержат до 20-30% легирующих элементов (в основном Ni, Сr, Мn.) при небольшом количестве углерода. Структура их в равновесном состоянии представляет аустенит или
153
аустенит с карбидами. К этим сталям относятся хромоникелевые нержавеющие коррозионностойкие стали, применяемые в пищевом машиностроении (I2XI8H9T, 08XI8HI0T, 10Х18Н12Б и др.), некоторые жаропрочные, немагнитные стали; высокомарганцевые износостойкие стали (Г13). Упрочнение этих сталей обычно проводят методами холодной обработки давлением (холодный прокат, наклеп дробью). Структурная диаграмма аустенитных сталей дана на рис.14.5.
Из аустенитных сталей изготавливают теплопередающие трубы различных диаметров, коллекторы.
Склонность к хрупким разрушениям у Сr-Ni аустенитных сталей практически отсутствует, благодаря чему они используются в криогенной технике до температуры - 253ºС.
Жаропрочные аустенитные стали с карбидным и интерметаллидным упрочнением (диски, лопатки газовых турбин, детали компрессоров и т.д.) работают до температур 650-800°C.
5. Ледебуритный класс. Стали ледебуритного (карбидного) класса содержат значительное количество углерода и легирующих элементов (Cr, W, V, Mo, Ti и др.). В литом состоянии первичные карбиды образуют грубую эвтектику типа ледебурит; с целью улучшения структуры и свойств стали данного класса подвергают прокату или ковке с последующим отжигом (для раздробления эвтектики на отдельные более мелкие составляющие). Структура сталей в равновесном состоянии состоит из феррита и карбидов, значительная часть которых является первичными, и которые отличаются от вторичных большими размерами. Вследствие большого количества карбидов стали этого класса после соответствующей термической обработки обладают высокой твердостью, хорошими режущими свойствами, высокой теплостойкостью, износостойкостью и поэтому применяются как инструментальные (Р9, Р6М5, Х12ТФ и др.) или особо износоустойчивые.
III.ОБОРУДОВАНИЕ, ПРИБОРЫ И МАТЕРИАЛЫ
1.Металлографические микроскопы МИМ-7 или ММУ-3М.
2.Наборы микрошлифов различных марок легированных сталей (конструкционных, инструментальных, с особыми свойствами);
3.Альбомы с фотографиями микроструктур легированных сталей.
IV. МЕТОДИЧЕСКИЕ УКАЗАНИЯ ПО ВЫПОЛНЕНИЮ РАБОТЫ
I. К выполнению лабораторной работы допускаются студенты, хорошо усвоившие теоретическую часть, так как изучение структуры и фазового состава легированных сталей намного сложнее, чем углеродистых сталей.
154
|
|
Состав и класс легированных сталей по структуре |
Таблица 14.1 |
||||
|
|
|
|||||
|
|
|
|
|
|
|
|
|
Химический состав, % |
Вид термиче- |
|
|
Класс стали в |
|
|
Марка |
|
|
ской обработки |
Микрострук- |
|
||
|
|
нормализован- |
Примечание |
||||
стали |
углерод |
легирующие элементы |
(температура |
|
тура |
ном состоянии |
|
|
|
|
ºС, среда) |
|
|
|
|
1 |
2 |
3 |
4 |
|
5 |
6 |
7 |
09Г2С |
≤0,I2 |
1,45-1,70Mn; 0,3Сг; |
Отжиг |
|
Феррит лег.+ |
Перлитный |
Корпусная |
|
|
0,3Ni; 0,3Cu; 0,7- 1,0Si |
|
|
+перлит |
|
|
10ХСНД |
≤0,12 |
0,8-1,1Sí; 0,5-0,8Mn; |
Отжиг |
|
Феррит лег + |
Перлитный |
Строительная с повышенной корро- |
|
|
0,6-0,9Сг; 0,5-0,8Ni; |
|
|
+ перлит |
|
зионной стойкостью в атмосфере |
|
|
0,4-0,65Cu |
|
|
|
|
|
40Х |
0,36-0,44 |
0,5-0,8Mn; 0,8-1,1Сг; |
З 860°С |
|
Сорбит |
Перлитный |
Коленчатые валы, оси, шестерни |
|
|
0,17-0,37Si |
0 500ºС |
|
|
|
|
70СЗА |
0,66-0,74 |
0,6-0,9Mn; 2,4-2,8Si |
3 860ºС |
|
Тростит |
Перлитный |
Пружины вагонов, автомобильное; |
|
|
0,3Сг; 0,2Cu, 0,25Cu. |
0 450°С |
|
|
|
рессоры; торсионные валы в станко- |
|
|
|
|
|
|
|
строении. |
ШX15 |
0,95-1,05 |
1,3-1,65Cu; 0,2-04Mn; |
З 840-860 |
|
Мартенсит+ Мартенситный Подшипниковые кольца, шарики и |
||
|
|
0,17-0,37Si |
0 150-170 |
|
+ карбиды |
|
ролики |
ХВГ |
0,95-1,05 |
0,6-0,9Mn; 0,6-1,1Сг; |
З 840-860 |
|
Мартенсит + |
Перлитный |
Сверла, развертки, плашки |
|
|
0,5-0,8W; 0,05-0,15V |
0 140-160 |
|
+ карбиды |
|
|
XI2M |
1,45-1,7 |
0 35Mn; 0,35Si: |
З 1030 |
|
Мартенсит + |
Ледебуритный Штампы для холодной штамповки |
|
|
|
11-12,5Сг; 0,35Ni; |
0 160 |
|
+карбиды |
|
|
|
|
0,4-0,6Mo |
|
|
|
|
|
PI8 |
0,7-0,8 |
3,8-4,4Сг; I7,5-I9W; |
Литье |
|
Ледебурит + |
Ледебуритный Режущий инструмент высокой теп- |
|
|
|
1,0-1,4V; 0,5-1,0Mo |
Отж |
|
+перлит |
(карбидный) |
лостойкости |
|
|
|
|
сорбит+ |
+ |
|
|
|
|
|
З 1270-1290 |
|
карбиды 290 |
|
|
|
|
|
|
мартенсит + |
|
|
|
|
|
|
0 550-570 |
|
+карбиды |
|
|
Г13 |
1-1,3 |
11-14Mn; 0,5Si |
З 1100 |
|
Аустенит |
Аустенитный |
Траки гусеничных машин, кресто- |
|
|
|
|
вины ж/д и трамвайных путей |
|||
|
|
|
|
155 |
|
|
|
|
|
|
|
|
Продолжение табл.14.I |
|
|
|
|
|
|
|
I |
2 |
3 |
4 |
5 |
6 |
7 |
40X13 |
0,35-0,45 |
0,6Mn; 0,6Si; I2-I4Cr |
З 1000-1050 |
Мартенсит + |
Мартенситный Режущий, мерительный и хирургиче- |
|
|
|
0,6Ni; 0,03S; 0.03P |
0 200-300 |
карбиды |
|
ский инструменты |
12X17 |
0,12 |
16-18Cr; 0,8Si; 0,8Mn |
Отжиг |
Феррит леги- |
Ферритный |
Оборудование заводов пищевой |
|
|
0,6Ni; 0,3Сu; 0,025S; |
760-780 |
рованный |
|
промышленности сварные конструк- |
|
|
0,035P |
|
|
|
ции |
I2XI8HI0T |
0,12-0,14 |
0,8Si; I-2Mn: 17-19Cr; |
З 1000-1100 |
Аустенит |
Аустенитный |
Сварные конструкции в агрессивной |
|
|
9-1Ni; до 0,6Ti |
|
легированный |
|
среде, жаростойкие жаропрочные |
40Х9С2 |
0,35-0,45 |
8-10Сг; 2-3 Si |
З 860 |
Тростит |
Мартенситный Клапаны автомобильных и авиаци- |
|
|
|
|
0 460-470 |
|
|
онных двигателей |
ЕХЗ |
1,0 |
3,0 Сr |
З 1250-1280 |
Мартенсит + |
Мартенситный Постоянные магниты |
|
|
|
|
0 580-600 |
карбиды |
|
|
2111 |
0,05-0,005 |
0,4-0,8 Si |
Отжиг 750- |
Феррит леги- |
Ферритный |
Магнитопроводы, статоры, роторы |
|
|
|
-900 |
рованный |
|
электродвигателей |
156
2. Для каждого микрошлифа (вида сплава) необходимо:
а) записать марку сплава, определить, к какой группе по назначению относится сплав;
б) пользуясь структурными диаграммами (рис.14.4), определить класс сплава по структуре;
в) зарисовать структуру сплава, указать структурные составляющие; г) указать вид термической обработки сплава; д) выписать химический состав сплава, конечные свойства;
е) указать области применения сплава, требования, предъявляемые к сплаву.
V. ОФОРМЛЕНИЕ ОТЧЕТА
Отчет по лабораторным работам должен включать следующее:
1.Название, цель работы.
2.Краткие теоретические сведения.
3.Рисунки микроструктур различных марок легированных сталей и сплавов (с разносом структурных составляющих). Указать увеличение микроскопа.
4.Для каждого микрошлифа (справа от рисунка) дать название, марку стали, структуру (указав вид термической обработки), класс стали по структуре, химический состав, свойства и области применения.
5.Рисунки выполнить карандашом.
6.Дать выводы о влиянии легирующих элементов на свойства изучаемых сталей.
VI. ВОПРОСЫ ДЛЯ САМОПРОВЕРКИ
1.Какие стали называются легированными?
2.Для какой цели используется легирование?
3.Какие фазы образуют легирующие элементы с железом?
4.Какие фазы образуют легирующие элементы с углеродом?
5.Как влияют легирующие элементы на эвтектоидную концентрацию углерода (тч. S) и предельную растворимость углерода в Fe-γ (тч. Е)?
6.Как влияют легирующие элементы на полиморфное превращение железа
(критические точки А3 и А4)?
7.На какие структурные классы делятся легированные стали после отжига?
8.На какие классы делятся по структуре легированные стали после нормализации?
157
9.На какие классы по назначению делятся легированные стали?
10.В каком состоянии, равновесном или термически обработанном, следует применять легированные стали?
11.Как влияют легирующие элементы на превращение А→М; на температуру мартенситного превращения и количество остаточного аустенита в стали?
12.Как влияют легирующие элементы на превращение аустенита при охлаждении стали?
13.Как следует охлаждать детали из легированных сталей при закалке? Почему?
14.Как влияет легирование на процессы отпуска стали?
15.Что такое отпускная хрупкость второго рода? Чем она обусловлена? Какие элементы способствуют снижение и устраняют отпускную хрупкость?
16.Как влияет легирование на свойства закаленной и отпущенной стали?
17.Какими свойствами обладают корпусные судостроительные стали? Назовите их марки.
18.Какие требования предъявляются к цементируемым легированным сталям? В чем отличие их свойств от углеродистых?
19.Какие требования предъявляются к улучшаемым сталям? Марки сталей, применение.
20.Какими свойствами должны обладать рессорно-пружинные стали? Их термообработка, марки.
21.Какие стали относятся к коррозионностойким?
22.В чем проявляется межкристаллическая коррозия? Как предупредить ее?
23.Какие сплавы называются жаропрочными? Марки жаропрочных сталей и сплавов, области применения.
24.Какие стали относятся к сталям повышенной прокаливаемости, не обладающими теплостойкостью (для режущего инструмента)?
25.Особенности и марки быстрорежущих сталей,
26.Штамповые стали холодной и горячей обработки давлением,
27.Какие стали и сплавы относятся к магнитотвердым? Какими свойствами, структурой они должны обладать?
28.Что относится к магнитомягким материалам? Какие требования предъявляются к ним?
29.Какие стали относятся к парамагнитным?
30.Назовите стали и сплавы с высоким электросопротивлением.
158
ЛАБОРАТОРНАЯ РАБОТА № 15 МИКРОАНАЛИЗ ЦВЕТНЫХ МЕТАЛЛОВ И ИХ СПЛАВОВ
I. ЦЕЛЬ РАБОТЫ: изучить строение и структуру цветных металлов и их сплавов в равновесном (отожженном) состоянии и после закалки и старения.
2. КРАТКИЕ ТЕОРЕТИЧЕСКИЕ СВЕДЕНИЯ
Все металлы и их сплавы, за исключением железа, относятся к цветным. Наибольшее промышленное применение получили медь, алюминий, титач " их сплавы. Медь в чистом виде нашла применение только и электоротехнике.
Наибольшее промыпланноз применение получили медные сплавы - латуни, бронзы.
Латуни. Диаграмма состояния медь-цинк дана на рис. 15.1. Как видно из рис. 15.1 до 39% содержания цинка латунь однофазная и состоит из α - твердого раствора замещения цинка в меди. Микроструктура однофазной латуни, рис.
15.2, имеет дендритное строение. Светлые участки-дендриты, богатые медью, затвердевают первыми, темные участки-линедендритное пространство, обогащенное цинком, затвердевают последними. Однофазные латуни нашли широкое применение. Из них изготавливают прокат холодной и горячей обработкой давлением.
Микроструктура двухфазной латуни, рис.15.3, содержащей от 39 до 45% цинка, состоит из α + β'твердых растворов. β' - фаза представляет собой твердый раствор на базе электронного соединена CuZn и имеет решетку гранецентрированного куба, на шлифе это темные включения. Двухфазные латуни обладают меньшей пластичностью и в основном используются для изготовления отливок.
Деформируемые латуни маркируются буквой Л и цифрами. Цифра указывает процент содержания меди. Например, латунь – Л63 содержит 63% меди, остальное цинк.
Если в состав латуни входят другие элементы, то они обозначаются буквами: О - олово, А - алюминий, Н - никель, С - свинец, Ж - железо, Мц - марганец. Например, ЛЖМц59-1-1 - латунь с содержанием 59% меди, I% железа, 1% марганца и остальное цинк.
В литейных латунях содержание компонентов сплава ставится в процентах сразу после буквы, обозначающей его название. Например, ЛЦ40С - латунь, содержащая 40% цинка, 1% свинца, остальное медь.
Однофазные латуни Л96, Л90, Л68, Л63 используются для изготовления трубок конденсаторов и теплообменников. Они склонны к коррозионному
159

Диаграмма состояния медь - цинк
160

Микроструктура однофазной латуни
а - после отжига х150; б - литая x150
Рис. 15.2
Микроструктура двухфазной латуни
а - после деформации и отжига х100; б – литая х200
Рис. 15.3
Микроструктура однофазной оловянистой бронзы
а - деформированная, после рекристаллизации x200; б - деформированная, после отжига х200
Рис. 15.5
161

Диаграмма состояния медь - олово
Рис. 15.4
162
растрескиванию и обесцинкиванию в присутствии влаги. Большей стойкостью обладают многокомпонентные латуни Л062-1 и ЛАЖ60-1-1. Литейные многокомпонентные латуни используются для изготовления шпорной арматуры, червячных колес, подшипников скольжения.
Бронзы. Сплавы меди со всеми элементами, кроме цинка, называются бронзами. Наибольшее применение получили оловянистые, алюминиевые, свинцовистые и бериллиевые бронзы.
Медь с оловом, рис.15.4, образует ряд фаз, представляющих собой твердые растворы и химические соединения. При содержании до 5-6% олова микроструктура литой бронзы состоит из неоднородного α - твердого раствора олова в меди. На микрошлифе, рис. 15.5, α - твердый раствор имеет дендритное строение, темные участки, оси дендритов, более богаты медью, а светлые участки, междуосные пространства, более богаты оловом. При содержании олова более 6% бронза будет иметь уже двухфазною структуру - неоднородного α - твердого раствора и эвтектоида (α + Cu31Sn8). На фоне неоднородного α – твердого раствора, рис.15.6, эвтекто (α + Cu31Sn8) представляет собой светлый участок химического соединения Cu31Sn8 и темных точечных включений α, - твердого раствора. В промышленности оловянистые бронзы, с содержанием до 20% олова, применяются для изготовления зубчатых колес, подшипников скольжения и арматуры работающей в воде или паре.
Медь с алюминием, рис.15.7, до 9,8% алюминия образует α - твердый раствор замещения алюминия в меди.
Микроструктура такой бронзы, рис.15.8, состоит из светлых зерен α - твердого раствора. При содержании алюминия более 9,8% в структуре бронзы наряду с α - твердым раствором наблюдается эвтектоид (α + γ2). Микроструктура такой бронзы в литом состоянии, рис.15.9, состоит из белых участков α - твердого раствора и темных участков - эвтектоида ( α + γ2). γ2 - фаза, электронное соединение Cu32Al9, отличается повышенной твердостью и хрупкостью.
Двухфазные алюминиевые бронзы могут подвергаться закалке и отпуску. После закалки бронза приобретает игольчатую структуру подобно мартенситу. Двухфазные алюминиевые бронзы чаще всего применяются для изготовления отливок.
Алюминиевые бронзы нашли широкое применение для изготовления тяжелонагруженных подшипников скольжения и запорной арматуры.
Бериллиевая бронза имеет предельную растворимость бериллия в меди до 0,2%. При большем содержании бериллия наряду с α - твердым раствором имеются области существования β и γ - фаз. При закалке в воде с 800ºС фиксируется неустойчивое состояние пересыщенного α - твердого раствора, а при
163
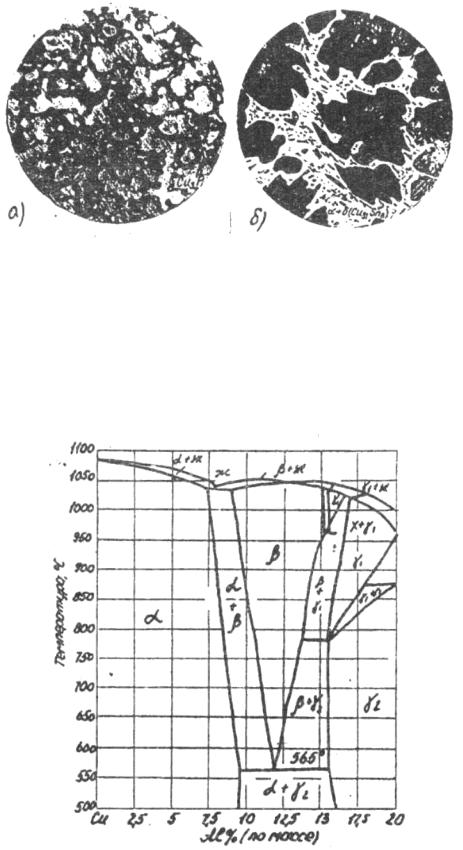
Микроструктура двухфазной бронзы.
а - литая оловянистая бронза х250; б - эвтектоид в литой оловянистой бронзе х1000.
Рис. 15.6.
Диаграмма состояния медь - алюминий
Рис. 15.7
164
последующем старении 300-350ºС происходит выделение γ - фазы, что сильно повышает прочность бронзы. Микроструктура бериллиевой бронзы БрБ2, с содержанием 2% бериллия, после старения и закалки представлена на рис.15.10. На фоне зерен α - твердого раствора видны мелкие светлые включения γ - фазы, соединение CuBe.
Бериллиевые бронзы применяются для пружин, мембран, пружинящих контактов. Обозначение марок бронз начинается буквами Бр. Далее в деформируемых бронзах следуют буквы, как и в латунях, соответствующие легирующим элементом и в конце последовательно цифры, указывающие содержание этих элементов. Например, БрАЖМц10-3-1,5 содержит 10% алюминия, 3% железа и 1,5% марганца, остальное медь. У питейных бронз процентное содержание легирующих элементов указывается сразу после буквенного обозначения их. Например, БрА10ЖЗМц2 додержит 10% алюминия, 3% железа и 2% марганца, остальное медь.
Сплавы алюминия. Алюминий в чистом виде используется только в электротехнике. Алюминий с магнием, медью, цинком, кремнием и др. элементами образует ряд технических сплавов, обладающих лучшими свойствами, чем чистый алюминий и широко применяются в промышленности. Все алюминиевые сплавы можно разделить на деформируемые и литейные.
Деформируемые алюминиевые сплавы. Деформируемые алюминиевые сплавы это сплавы меди с марганцем, магнием, медью и другими элементами, изделия из которых получают прокаткой. Деформируемые алюминиевые сплавы в свою очередь подразделяются на термически неупрочняемые и термически упрочняемые. Термически неупрочняемые алюминиевые сплавы это сплавы алюминия с магнием, марганцем и другими элементами.
Термически неупрочняемые алюминиевые сплавы АМг3, AМг5, АМг6 хорошо свариваются, обладают высокой стойкостью против коррозии и поэтому получили широкое применение в судостроении. Это сплавы содержат до 6% Mg. Диаграмма состояния алюминий-магний представлена на рис.15.11. Структура их состоит из α - твердого раствора магния в алюминий и частиц включающих химическое соединение Mg2Al3 (В - фаза) рис.15.12. АМг обозначает алю- миниево-магниевый сплав, а цифра среднее содержание магния. Термически упрочняемые алюминиевые сплавы-дуралюмины с рядом элементов образует ограниченные твердые растворы переменной концентрации. С понижением температуры растворимость компонентов уменьшается и из двойных твердых растворов выделяются кристаллы избыточной фазы. В системе Al - Cu такой избыточной фазой является CuAl2, рис. 15.13. Сплавы на основе алюминий-
165

Микроструктура алюминиевой бронзы х100
Рис. 15.8
Микроструктура алюминиевой двухфазной бронзы
а - литая алюминиевая бронза х250; б - эвтектоид в литой алюминиевой бронзе х500
Рис. 15.9.
Микроструктура бериллиевой бронзы х250
а - литая бериллиевая бронза; б - деформированная бериллиевая бронза
Рис 15.10
166

Диаграмма состояния алюминий - магний
а - диаграмма алюминий – магний; б - зависимость механических свойств от содержания магния
Рис. 15.11
Микроструктура термически неупрочняемого алюминиевого сплава
а- сплав АМг5 после гомогенизации х250;
б- сплав АгМ6 после литья х250
Рис. 15.12
167
медь представляют наиболее многочисленную группу и получили широкое применение. В их состав входят медь, марганец, магний, кремний, которые между собой образуют химические соединения переменной растворимости Mg2Si, Cu2FeAl7 и W - фаза. В структуре дуралюмина в равновесном (отожженном) состоянии присутствует α - твердый раствор, в состав которого входят медь и др. элементы, а также химические соединения - фаза W, CuAl2, Cu2FeAl7 в виде темных образований, рис.15.14. Термическая обработка дуралюмина состоит в закалке и естественном или искусственном старении. При нагреве фазы CuAl2, W, Cu2FeAl7 растворяются в α - твердом растворе и структура становится однофазной. Последующее быстрое охлаждение в воде позволяет зафиксировать этот пересыщенный однофазный твердый раствор. После закалки и старения дуралюмин упрочняется, однако сохраняет пластичность и легко деформируется.
Дуралюмины, например, Д16 маркируются буквой Д, обозначающей дуралюмин и цифры. Каждой цифре соответствует определенный химический состав и механические свойства. Дуралюмины плохо свариваются и поэтому конструкции из них изготавливаются клепкой. Они нашли широкое применение в авиации. Для повышения коррозионной стойкости они подвергаются плакированию.
Широкое применение получили сплавы системы AI - Mg - Si, называемые авиалями, AB и АД31, а также высокопрочные сплавы типа В95, В96. Сплавы АК6, АК8 отличаются высокой пластичностью, ковку и штамповку их производят при температуре 450-475°С. Жаропрочные сплавы типа AK4-I нашли широкое применение для изготовления поршней, головок цилиндров, крыльчаток.
Литейные алюминиевые сплавы на основе AI - Si содержат 5-14% Si и получили название силумины. Согласно диаграммы состояния А1-Si структура сплава при содержании до 11,6% кремния (доэвтектический сплав) состоит из α - твердого раствора кремния в алюминии и эвтектики (α + Si), рис.15.15.
При модификации сплавов силумина микроструктура сплава состоит из α - твердого раствора кремния в алюминии и мелкозернистой эвтектики (α + Si), рис.15.16. В доэвтектических сплавах после модифицирования возрастает количество первичных кристаллов - твердого раствора.
Линейные алюминиевые сплавы согласно ГОСТ 1583-89 маркируются буквой А, за которой указываются буквой легирующие элементы. Цифры после обозначения легирующего элемента указывают его среднее содержание, например, AKI2, содержит 12% кремния.
168

Диаграмма состояния алюминий – медь
Рис. 15.13
Микроструктура термически упрочняемого деформируемого алюминиевого сплава
а- литой дуралюмин Д16 х150;
б- деформируемый дуралюмин Д1 х250.
Рис. 15.14
169

Диаграмма состояния алюминий - кремний
Рис. 15.15
Микроструктура литейных алюминиевых сплавов
а- немодифицированный силумин AK10 х200;
б- модифицированный силумин АК10 х250
Рис. 15.16
170

Диаграммы состояния сплавов на основе титана
Рис. 15.17 Микроструктура титановых сплавов
а - в отожженном состоянии BT5-I х300; б - в литом состоянии ВТ6 х200; в - в закаленном состоянии ВТ4 х200
Рис. 15.18
171
Часто в литературе приводится старое обозначение, например, AJI9, где АЛ - алюминий литейный, а цифра - условный номер сплава. Изделия и конструкции из литейных алюминиевых сплавов нашли широкое применение в машиностроении, приборостроении и энергетике.
Жаропрочные литейные сплавы AЛ1, АЛ19 и АЛ33 применяются для отливки поршней, головок цилиндров двигателей, крыльчаток насосов.
Титан и его сплавы. Титан имеет два аллотропических модификаций, до 882ºС существует α - титан, а выше 882ºС В-титан.
Титановые сплавы с AI, Cr , V , Sn, Mo, Мп обладают высокой прочностью и коррозионной стойкостью. Структура большинства сплавов титана однофазная, состоящая из α или β - твердого раствора, либо двухфазная, состоящая из (α + β) - твердых растворов. К однофазным сплавам относится сплав титана с А1, Sn, рис.15.17. Он не упрочняется закалкой и старением и состоит из зерен α - твердого раствора алюминия в титане, рис. 15.18. Сплав титана с Mo, V , Cr расширяет область существования ß - фазы и обеспечивает структуру ß - твердого раствора. Сплавы с двухфазной структурой (α + β) подвергаются упрочняющей термической обработке - закалке и старению. После закалки они имеют структуру, состоящую из фазы мартенситного игольчатого вида – α1 и β - фазы, а при повышенном содержании элементов ß - стабилизаторов (хром, молибден) образуются метастабильные фазы (α1 и β) и α - твердый раствор. В процессе старения метастабильные α1 и β - фазы распадаются с образованием дисперсных частиц α1 и α - твердого раствора. Процесс старения улучшает пластические свойства, но снижает прочность и вязкость.
Титановые сплавы обозначаются буквами ВТ - высокопрочный титановый сплав и цифрами , указывающими условный номер сплава.
III.ОБОРУДОВАНИЕ, ПРИБОРЫ И МАТЕРИАЛЫ
1.Металлографический микроскоп МИМ-7.
2.Набор микрошлифов оловянистых, алюминиевых и бериллиевых бронз, латуней, деформируемых и литейных алюминиевых сплавов, титановых сплавов.
3.Твердомер Бринелля.
4.Диаграммы состояния двойных сплавов цветных металлов.
IV.МЕТОДИЧЕСКИЕУКАЗАНИЯИЗАДАНИЯПОВЫПОЛНЕНИЮРАБОТЫ
1. Рассмотреть под микроскопом при увеличении х500 и зарисовать структуру цветных металлов и их сплавов:
а) одно и двухфазной оловянистой бронзы;
172
б) одно и двухфазных латуней; в) алюминиевой бронзы; г) бериллиевой бронзы;
д) термически неупрочняемого деформируемого алюминиевого сплава; е) термически упрочняемого деформируемого алюминиевого сплава; ж) литейного не модифицированного и модифицированного алюминие-
вого сплава; з) одно и двухфазного титанового сплава.
2.Замерить твердость в 3 точках на макрошлифах цветных металлов и их сплавов на приборе Бринелля, под нагрузкой 750 кгс, шариком диаметром 5 мм, при времени выдержки 30 с.
V.СОДЕРЖАНИЕ ОТЧЕТА
1.Зарисовать диаграммы состояния медь-цинк, медь-олово, алюминий-медь, алюминий-кремний.
2.Нарисовать микроструктуру цветных металлов и их сплавов и указать их марку, примерный химический состав, твердость по Бринеллю и область применения. На каждом микрошлифе стрелками указать структурные составляющие сплава.
3.Для каждого сплава цветных металлов дать его наименование и подробное описание фаз и структурных составляющих.
VI. ВОПРОСЫ ДЛЯ САМОПРОВЕРКИ.
1.Укажите область применения латуней, бронз, алюминиевых и титановых пилавов?
2.Как маркируются латуни?
3.Из каких структурных составляющих состоят латуни?
4.Как маркируются бронзы?
5.Какие структурные составляющие входят в состав оловянистых, алюминиевых и бериллиевых бронз?
6.Как маркируются алюминиевые сплавы?
7.Какие структурные составляющие входят в состав деформируемых и литейных алюминиевых сплавов?
8.Объясните, как осуществляется термическое упрочнение алюминиевых деформируемых сплавов?
9.Как влияет модификация на структуру литейного алюминиевого сплава-си- лумина?
173
ЛАБОРАТОРНАЯ РАБОТА № 16 МИКРОАНАЛИЗ ПОДШИПНИКОВЫХ СПЛАВОВ
I. ЦЕЛЬ РАБОТЫ: изучить микроструктуру, свойства и область использования подшипниковых сплавов.
II. КРАТКИЕ ТЕОРЕТИЧЕСКИЕ СВЕДЕНИЯ
Наибольшее распространение в качестве подшипниковых сплавов получили баббиты, свинцовистая бронза, алюминиево-оловянистые сплавы и многослойные композиционные материалы.
Баббиты являются широко распространенными антифрикционными сплавами, обладающими высокой износостойкостью, низким коэффициентом трения, мало изнашивающими вал и хорошо прирабатывающимися к валу. Они обладают способностью впитывать продукты износа.
Главным недостатком баббитов является их низкая усталостная прочность.
Сплавы олова, сурьмы, меди иногда с небольшими добавками никеля, хрома получили наименование оловянистые баббиты. Наибольшее распространение в судовых машинах и механизмах получили оловянистые баббиты Б88 и
Б83.
Типичной структурой оловянистых баббитов является структура, состоящая из основы α - твердого раствора сурьмы в олове и равномерно распределенных в нем кубических кристаллов химического соединения ß – фаза (SnSb) и химических соединений меди с оловом и сурьмой Cu3Sn и Cu2Sb, рис. 16.1. На рис. 16.2 приведена диаграмма состояния олово-сурьма.
Химические соединения Cu3Sn и Cu2Sb, выделяясь при кристаллизации первыми, образуют каркас, затрудняющий ликвацию ß - фазы. Количество кристаллов ß - фазы и химических соединений меди с оловом и сурьмой понижается с повышением содержания в оловянистых баббитах олова и снижением содержания сурьмы и меди, поэтому оловянистые баббиты Б83, Б88 имеют более высокую пластичность, меньшую твердость и лучше прирабатываются к валу.
Проведенные исследования микротвердости структурных составляющих оловянистых баббитов показали, что мягкая пластичная основа α - твердый раствор имеет твердость = 24 кгс/мм , ß - фаза (SnSb) Hµ = 120 кгс/мм и химические соединения Cu3Sn - Нµ = 520 кгс/мм и Cu2Sb - Hµ = 370 кгс/мм.
При толщине слоя баббита более 2 мм он обладает хорошей способностью
174
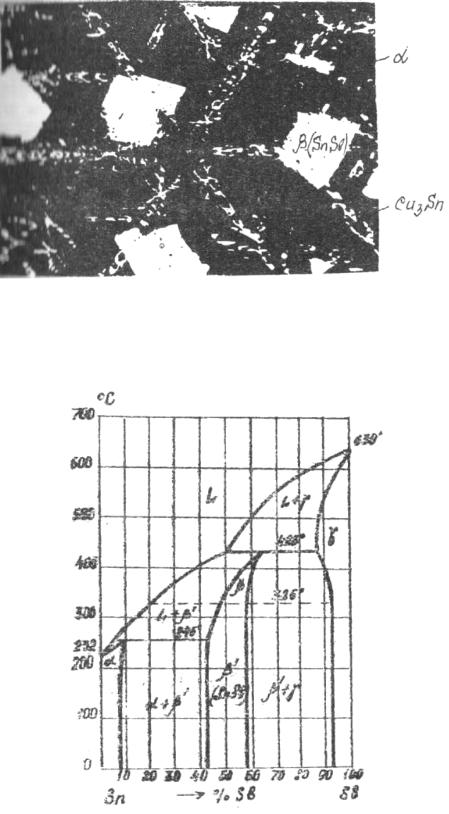
Микроструктура оловянистого баббита Б83 (11% Sb; 6% Cu; остальное Snп) x100
Рис. 16.I
Диаграмма состояния олово - сурьма
Рис. 16.2
175
собностью прирабатываться, поглощать продукты износа и компенсировать неточности обработки и монтажа узла трения и перекосов, возникающих в процессе эксплуатации. Мягкая пластичная основа, α - твердый раствор, изнашивается быстрее чем твердые частицы ß - фазы и химических соединений, и на поверхности трения вкладышей образуются каналы, по которым циркулирует смазка. При увеличении нагрузки на отдельных участках вкладышей воспринимающие нагрузку твердые частицы вдавливаются в мягкую основу и увеличивают площадь контакта, что приводит к снижению удельной нагрузки.
При толщине слоя баббита менее 0,3 мм большое значение приобретает его структуру. Крупные кристаллы ß - фазы и химических соединений способствуют резкому снижению усталостной прочности баббита и особенно при малой толщине слоя. На отдельных участках, особенно при ликвации баббита, крупные хрупкие кристаллы ß - фазы могут быть соизмеримы с толщиной слоя баббита и передавать нагрузки от шейки вала на стальное основание вкладыша. В этих условиях в них могут возникать микротрещины, переходящие затем в макротрещины.
Успешным оказалось легирование оловянистых баббитов малыми добавками хрома, кадмия, циркония, мышьяка и др. элементов.
Легирующие добавки, особенно хром, способствуют получению мелкозернистой структуры сплава, независимо от скорости охлаждения подшипников после заливки, повышают общую и усталостную прочность баббита. Так баббит Б88, содержащий кадмий, хром и следы других элементов, превосходит лучшие современные марки баббитов по прочности на 20-30%, удлинению 4060% и долговечности в 3-3,5 раза.
Сплавы свинца, олова, сурьмы, меди, никеля, мышьяка и небольших добавок натрия, называются свинцовистыми баббитами.
Свинцовистые баббиты нашли применение в менее нагруженных подшипниках судовых двигателей, компрессоров и валопроводов.
Наибольшее применение в судовых машинах и механизмах получили свинцовистые баббиты Б16 и БН, на железнодорожном транспорте БКА, БК2, БК2Ш. Свинцовистые баббиты отличаются низким содержанием олова. В качестве мягкой основы они имеют двойную и тройную эвтектику, состоящую из кристаллов твердых растворов α, (Sn, Sb и Cu в Pb).
Твердыми включениями служат кристаллы ß - фазы и интерметаллические (химические) соединения Cu3Sn и Cu2Sb. Баббит Б16 наиболее простой по химическому составу и нашел применение как заменитель баббита Б83 в подшипниках, работающих при спокойной нагрузке.
Баббит БН дополнительно легирован Cd , As , Ni. Кадмий повышает коррозионную стойкость баббита, мышьяк улучшает жидкотекучесть и теплопро-
176
водность, никель, упрочняя α - твердый раствор, повышает изноносостойкость баббита. Он нашел широкое применение для заливки подшипников судовых валопроводов, двигателей, компрессоров.
На рис.16.3 приведена микроструктура баббита БН. В основной пластичной массе, состоящей из эвтектики α (Pb) и твердого раствора β (SnSb) равномерно расположены кубические кристаллы химического соединения ß - фазы (SnSb) и серые включения химического соединения AsCd.
Сплавы БК принадлежат к системе Pb - Ca - Na. В основе мягкой пластичной составляющей α - твердом растворе Na и Ca в Pb, распределены светлые твердые дендриты химического соединения Pb3Ca, рис. 16.4.
Маркируются баббиты буквой Б - баббит и цифрами, которые показывают процентное содержание олова. В некоторых марках баббитов вместо цифры приводится наименование легирующего элемента. Например, баббиты БН и БК легированы никелем и кальцием.
Наряду с белым металлом для вкладышей подшипниковых судовых и транспортных тяжелонагруженных двигателей используется свинцовистая бронза. Свинцовистая бронза обладает высокой усталостной прочностью и износостойкостью, однако имеет ряд существенных недостатков. Проникновение меди в стальной вал при нарушении режима смазки приводит к схватыванию, из-за окисления свинца легко возникает коррозия свинцовичтой бронзы. На рис.16.5 приведена диаграмма состояния свинец-медь. Структура свинцовистой бронзы состоит из мягких включений свинца, равномерно распределенных в твердой основе, α - твердом растворе олова в меди, рис.16.6. В подшипниках скольжения судовых и транспортных двигателей свинцовистая бронза имеет рабочее гальваническое покрытие толщиной 0,02-0,06 мм, состоящее из олова и свинца. Для высоких нагрузок и скоростей скольжения используют гальваническое покрытие с индием.
В трехслойных подшипниках скольжения на свинцовистую бронзу, толщиной до 1,5 мм, гальваническим способом нанесен слой никеля толщиной 0,0015-0,003 мм; на слой никеля, также гальваническим способом, нанесен рабочий слой толщиной 0,03-0,1 мм, состоящий из 12% олова,.2,3% меди, остальное свинец.
Применение никелевого разделительного покрытия между свинцовистой бронзой и оловянисто-свинцовистым рабочим слоем вызвано образованием крупных химических соединений олова с медью на границе раздела, что резко снижает прочность соединения рабочего слоя со свинцовистой бронзой.
177

Микроструктура свинцовистого баббита БН
(10% Sn, 14% Sb, 2% Cu, 0,7% Cd, 0,5% Ni, 0,7% As, остальное Pb) х100
Рис. 16.3
Микроструктура свинцовистых баббитов
а - БК2 (0,8% Ca, 0,3% Na, 2% Sn, остальное Pb)х100 б - Б16 (I6%Sn, 16% Sb, 2% Cu, остальное Pb) x100
Рис. 16.4.
178

Диаграмма состояния медь – свинец
Рис. 16.5
Микроструктура свинцовистой бронзы Бр СЗО
(3% Pb, 1% Sn, остальное Cu) х200
Рис. 16.6
179
Для высоких нагрузок и больших скоростей скольжения используются сплавы свинцовистой меди KS 30 и KS 25, получаемые спеканием, с покрытием Р8, Р9, P10, состоящим из свинца и олова.
Вчетырехслойных подшипниках судовых двигателей на стальную основу наносятся методом спекания порошок свинцовистой меди KS 25, затем слой высокоолованистого баббита Б90 и сверху гальваническим! способом наносится покрытие P10.
Алюминиевые сплавы ACM, A09-I, А09-2, A020-I в последние годы заменяют белые металлы в судовых и транспортных двигателях. Эти сплавы обладают высокой усталостной прочностью, хорошо сопротивляются смятию при высоких температурах и при закаленных шейках вала не требуют покрытия их рабочей поверхности белыми металлами. Алюминиевые сплавы для среднескоростных двигателей, при закаленных шейках коленчатого вала, имеют долговечность свыше 10 лет или 35 тысяч часов. Основным недостатком алюминиевых сплавов является способность к схватыванию с шейками вала при попадании морской воды в смазочное масло при работе с незакаленными шейками валов и повышенный износ шеек вала по сравнению с белыми металлами. Диаграмма состояния сплава алюминий-олово приведена на рис.16.7.
Олово не растворяется в алюминии и выделяется в виде зерен, шариков и концентрируется, главным образом, на рабочей поверхности. По сопротивлению схватыванию алюминиевые сплавы близки к баббитам, нет упрочнения наклепом, при повышении температуры появляется ползучесть, а при обычных температурах их пластичность значительно выше, чем у белых металлов.
Алюминиевые сплавы классифицируются преимущественно по микроструктурному признаку. К первой группе относятся сплавы, имеющие включе-
ния твердых структурных составляющих. FeAl3, CbAl2, Al3Ni, AlSb в пластичной основе. Микроструктура сплава АСМ состоит из кристаллов химического соединения AlSb, равномерно распределенных в двойной эвтектике, α - твердом растворе магния и сурьмы и химического соединения AlSb, рис.16.8.
Всплавах второй группы A020-I, А30, А40, А55 наряду с твердыми составляющими имеются мягкие пластичные включения. Микроструктура сплава А020-1 состоит из α - твердого раствора меди в алюминии, твердых включений
химического соединения CuAl2 и равномерно распределенных включений олова, рис.16.9. Особенно высокими антифрикционными свойствами обладает оло- вянисто-алюминиевый сплав A55S , который по прирабатываемости, несхватываемости с валом, сопротивлению коррозии и кавитации соответствует высокооловянистым баббитам Б88, а по пределу усталости стоит между сплавами Б88 и А40.
180

Диаграмма состояния алюминий - олово
Рис. 16.7
Микроструктура алюминиевого сплава АСМ
(5% Sb$ 5% Мп, остальное Al) x250
Рис. 16.8
181
Для подшипников коленчатых валов низкоскоростных дизелей с неупрочненными валами используются оловянисто-алюминиевые сплавы Р10/А40, Р10А020-1 и Р10/А55 с рабочим гальваническим оловяно-свинцовым покрытием, толщиной 0,02 мм.
У алюминиевых антифрикционных сплавов снижение твердости с повышением температуры происходит значительно медленнее, чем у оловянистых баббитов. Особенно характерно то, что усталостная прочность алюминиевых антифрикционных сплавов значительно выше, чем у оловянистых баббитов и свинцовистой бронзы, что позволяет использовать их для высоких удельных давлений, скоростей скольжения и температуря смазочного масла.
Большой практический интерес представляет разработанный в КГТУ новый алюминиевый сплав, содержащий висмут и серу.
Структура этого сплава, рис.16.10, состоит из основы α - твердого раствора меди в алюминии, равномерно распределенных мягких включений висмута по границам зерен твердого раствора и включений химического соединения Bi2S3 , равномерно распределенных в висмуте. Наличие химического соединения обеспечивает низкий коэффициент трения, устраняет схватывание с валом при нарушении режима смазки.
Разработанный в КГТУ новый сплав на основе свинца, содержащий висмут, медь и серу является заменителем оловянистых и свинцовистых баббитов. Свинец с висмутом образует твердый раствор и эвтектику, растворимость висмута в свинце, в твердом состоянии составляет 18%, рис.16.11.
Основа сплава состоит из твердых растворов свинца, висмута и сурьмы, твердая составляющая сплава состоит из химических соединений, подобно дисульфиту молибдена (МоS2), висмут-сера (Bi2S3), сурьма-сера (Sb2S3), медьсурьма (Cu2Sb) и участков богатых сурьмой, твердого раствора висмут-сурьма, обладающего сильной дендритной ликвацией, рис.16.12.
Проведенные исследования показали, что предлагаемый сплав обладает лучшими антифрикционными свойствами, чем известные оловянно-свинцови- стые баббиты:
-наличие в сплаве мягкой пластичной основы, состоящей из твердых растворов свинец-висмут-сурьма, вместо механических смесей у оловянно-свинцо- вистых баббитов, устраняет хрупкость сплава и резко повышает его усталостную прочность;
-отсутствуют уплотнение сплава при небольших нагрузках в первый период работы;
-наличие в сплавах химических соединений висмут-сера (Bi2S3)
182

Микроструктура алюминиевого сплава АО 20-1 (1% Cu, 20% Sn, остальное Al) х250
Рис. 16.9
Микроструктура алюминиевого сплава AB 20-1 (20% Bi, 1% Сu, 0,5% S , остальное Al) х250
\
Рис. 16.10
183

Микроструктура алюминиевого сплава ABC (12% Bi, 1% Сu, 05% S, остальное Pb) х250
Рис. 16.11
Микроструктура алюминиевого сплава ABC (12% Bi, 1% Cu, 0,5% S, остальное Pb) х500
Рис. 16.12
184
и сурьма-сера (Sb2S3) обеспечивает, подобно дисульфиду молибдена (МоS2) низкий коэффициент трения, высокую износостойкость пары трения, особенно при граничном трении и при повышенных температурах, устраняет схватывание вала с антифрикционным сплавом при нарушении режима жидкостного трения;
- из-за отсутствия в сплаве дорогостоящего и дефицитного олова снижает его стоимость.
Технология выплавки и заливки в подшипники предложенного сплава не меняется по сравнению с используемой для известных оловянно-свинцовистых баббитов.
III.ОБОРУДОВАНИЕ, ПРИБОРЫ И МАТЕРИАЛЫ
1.Металлографический микроскоп МИМ-7.
2.Набор микрошлифов оловянистых и свинцовистых баббитов, свинцовистой бронзы, алюминиевых сплавов, многослойных композиций и новых подшипниковых сплавов.
3.Твердомер Бринелля.
4.Диаграммы состояния двойных подшипниковых сплавов.
IV.МЕТОДИЧЕСКИЕУКАЗАНИЯИЗАДАНИЯПОВЫПОЛНЕНИЮРАБОТЫ
1.Рассмотреть под микроскопом при увеличении х100 и х500 и зарисовать структуру подшипниковых сплавов:
и) свинцовистой бронзы БрС30; б) оловянистых и свинцовистых баббитов Б83, БН, БК;
в) алюминиево-оловянистых сплавов АСМ, A020-I;
г) сплавов на основе свинца, алюминия с добавкой серы и висмута; д) многослойных композиций.
2.Замерить твердость в 3 точках на микрошлифах подшипниковых сплавов на приборе Бринелля, под нагрузкой 250 кгс, шариком диаметром 10 мм, при времени выдержки 60 с.
V. СОДЕРЖАНИЕ ОТЧЕТА
1.Зарисовать диаграммы состояния сплавов: олово-сурьма, алюминий-олово, медь-свинец.
2.Зарисовать микроструктуру подшипниковых сплавов и под каждым рисунком указать марку сплава, примерный химический состав, твердость по Бринеллю. На каждом микрошлифе стрелками указать структурные составляющие сплава.
3.Дин каждого подшипникового сплава дать объяснение влияния структурных
185
составляющих на его антифрикционные свойства. Привести область применения подшипниковых сплавов.
VI. ВОПРОСЫ ДЛЯ САМОПРОВЕРКИ
1.Дайте определение антифрикционным свойствам подшипниковых сплавов
2.Как классифицируются подшипниковые сплавы по химическому составу и назначению?
3.Какие структурные составляющие входят в состав оловянистых и свинцовистых баббитов?
4.Какие структурные составляющие входят в состав свинцовистой бронзы и алюминиевых сплавов?
5.Какие структурные составляющие входят в состав новых алюминиевых и свинцовистых подшипниковых сплавов?
6.Как маркируются подшипниковые сплавы?
7.Укажите твердость подшипниковых сплавов и область их применения.
8.Объясните, как влияют структурные составляющие подшипниковых сплавов на их антифрикционные свойства.
186
ЛАБОРАТОРНАЯ РАБОТА № 17 ИЗУЧЕНИЕ СТРУКТУРЫ И СВОЙСТВ КЛЕЕВЫХ СОЕДИНЕНИЙ
I.ЦЕЛЬ РАБОТЫ: ознакомиться с основными группами клеев, изучить влияние состава клея и режима отверждения клеевых композиций на структуру
исвойства клеевых соединений.
II.ТЕОРЕТИЧЕСКИЕ СВЕДЕНИЯ
Впоследние годы клеевые соединения находят все большее применение для создания силовых конструкций из металлов и различных неметаллических материалов.
Сборка на клею конструкций из металлов, пластмасс, древесины, бетона, стекла и других материалов имеет ряд преимуществ, по сравнению с другими видами неразъемных соединений: атмосферостойкость и стойкость и коррозии клеевого шва, герметичность соединения. Сварные швы, отверстия под заклепку и болты снижают прочность соединяемых материалов, так как в зоне швов сосредотачиваются напряжения, ослабляющие конструкцию. Клеевые соединения, как правило, лучше выдерживают усталостные нагрузки. Клеи незаменимы при изготовлении трехслойных конструкций и соединений разнородных материалов в самых различных сочетаниях (металлы, бетон, дерево, стекло, керамика и т.д.). При использовании клеев масса конструкций увеличивается незначительно, упрощается технология работ.
Недостатками клеевых соединений являются их невысокая прочность при неравномерном отрыве и знакопеременных нагрузках, необходимость в ряде случаев применять нагревание при склеивании, невысокая теплостойкость большинства промышленных клеев, склонность к старению, токсичность. Основными условиями хорошего качества склеивания являются шероховатость поверхности склеивания и тщательное ее обезжиривание, толщина клеевого слоя (для большинства клеев и типов соединений ее следует выдерживать в пределах 0,05-0,25 мм). При толщине слоя более 0,5 мм прочность соединения резко падает. На качество клеевого соединения влияет также правильный выбор клея, состав композиции, режим отверждения.
Клеи - вещества или смеси веществ органической, элементоорганической или неорганической природы, обладающие хорошей адгезиейх, когезионной прочностью, достаточной эластичностью, минимальной усадкой,
____________________
хАдгезия (прилипаемость) -связь приведенных в контакт клеящего вещества (адгезив) и склеиваемой поверхности (субстрат); когезионная прочность (когезия) -сцепление молекул внутри физического тела под действием различных сил притяжения.
187
способные отвержаться с образованием прочных клеевых соединений.
По способу изготовления различают природные клеи (казеиновый, столярный, осетровый, гуммиарабик и др.) и синтетические клеи (эпоксидные, фенолформальдегидные, полиэфирные и др.).
По физическому состоянию клеи могут быть жидкими, пастообразными, пленочными, порошкообразными, в виде стержней.
По адгезионным свойствам клеи бывают универсальными, склеивающими различные материалы (например, эпоксидные, клеи БФ), и с избирательной адгезией (резиновые, белковые).
По назначению различают конструкционные-силовые и несиловые клеи. Многие клеевые составы могут служить одновременно лакокрасочными
материалами и герметиками.
Клеи по отношению к нагреву делятся на два класса: обратимые (на базе термопластов) и необратимые (на базе реактопластов), отверждающиеся за счет добавления отвердителя.
Обратимые клеевые составы содержат термопластичные полимеры, поэтому при нагревании пленка клея размягчается и изделие расклеивается (низкая теплостойкость). Термопластичные клеи находят ограниченное применение, их используют для склеивания материалов, обычно не подвергающихся высоким нагрузкам или нагреву (пластмассы, картон, бумага, ткан). Для склеивания изделий из термопластов пользуются растворами, вызывающими набухание поверхности, при этом повышается клейкость, необходимая для обеспечения достаточной прочности склеиваемых деталей. Чтобы повысить вязкость растворителя, в него вводят 2-4% того полимера, детали из которого надо склеить. Однако при этом в детали возникают значительные внутренние напряжения вследствие диффузии растворителя в глубь материала.
Необратимые клеи холодного отверждения отвердевают за счет реакции связующего с отвердителем без нагрева; клеи горячего отверждения отличаются тем, что переход полимера из термореактивной стадии в термостабильную осуществляется при повышении температуры. Клеи холодного отверждения более удобны, так как не требуют применения нагревательного оборудования, но обладают более низкой прочностью и теплостойкостью.
Самыми распространенными конструкционными клеями являются эпоксидные клеи и клеи типа "Спрут" на полиэфирно-уретановой основе, относящиеся к необратимым клеям, имеющие широкие возможности модификации с целью изменения прочностных, эластичных свойств и температурных характеристик.
Эпоксидные композиции применяются не только в качестве клеевых составов, но широко используются при ремонте металлических и пластмассовых
188
изделий (заделка литейных дефектов в отливках, трещин на водяной рубашке блоков цилиндров, при ремонте топливной аппаратуры и т.п.), как электроизоляционные компаунды для литой изоляции высоковольтных трансформаторов и некоронирующих проходных изоляторов, в судовой аппаратуре и аппаратуре автоматического управления объектами, в счетно-решающих устройствах и т.д. При модификации эпоксидных смол можно получить клеи с температу-
рой от 260 до 300°С.
Термореактивные полимеры, в основном, в отвержденном состоянии строение, причем часто структура бывает не детерминирована. Глобулярные полимеры, как правило, хрупки и сравнительно легко разрушаются при ударе (эпоксидные, фенолформальдегидные полимеры), поэтому для повышения пластичности в состав клеев вводят пластификаторы; количество пластификаторов должно быть строго оптимальным, так как при избытке пластификатора снижается адгезия и теплостойкость, но повышается морозостойкость.
Введение пластификаторов способствует увеличению жизнеспособности клеевых составов. Эпоксидные клеи могут пластифицироваться дибутилфталатом (ДБФ), трикрезилфосфатом (ТКФ). Чтобы придать большую гибкость и эластичность клеевым швам, эпоксидные клеи модифицируют тиоколам, полиэфирами и др.
Растворители вводят в тех случаях, когда для удобства нанесения клея требуется снизить его вязкость. В качестве растворителей используют ацетон, бензол, этилметилкетон. Введение растворителей увеличивает жизнеспособность клея. Перед соединением поверхностей растворитель должен быть полностью удален из клеевого состава.
Дли отверждения эпоксидных клеев применяются отвердители двух ви-
дов:
а) отвердители "холодного" отверждения - полиэтиленполиамин, гексаметилендиамин, отвердитель аминофенольного типа АФ-2, смолы – Л-18, JI-19, Л-20 и др.
Отверждение с помощью полиаминов можно вести как при обычной тем-
пературе (комнатной), так и при нагревании. |
|
|
|
Время отверждения |
при 18-23ºС |
минимальное – 18-24 ч, |
|
|
|
оптимальное – 3-4 |
сут, |
|
при +60ºС |
минимальное – 2-3 ч, |
|
|
|
оптимальное – 4-5 |
ч. |
Низкомолекулярные полиамиды (Л-18 и др.) играют роль отвердителей и пластификаторов, что увеличивает адгезию на 10-20%. Они отверждают смоли за 48-72 ч при комнатной температуре. При повышении температуры скорость отверждения резко возрастает, так при температуре 130ºС полное отверждение происходит за два часа.
189
Клеи с отвердителями аминами обычно имеют небольшую жизнеспособность (5-45 мин);
б) отвердители "горячего" отверждения - ангидриды двухосновных кислот (малеиновой и фталевой).
Отверждение происходит только при повышенных температурах (100140ºС). Во всех случаях ангидриды придают отвержденным композициям более высокую теплостойкость и лучшую адгезию, жизнеспособность клея значительна, иногда достигает нескольких месяцев. При процессе отверждения необходимы постепенный подъем температуры и постепенное охлаждение.
Отверждение эпоксидных смол происходит вследствие увеличения молекулярного веса, достигаемого поперечными сшивками (отвердитель) молекул смолы. Основной особенностью отвергаемых эпоксидных смол является образование неплавких и нерастворимых продуктов без выделения каких-либо летучих веществ, поэтому усадка клеевого шва практически отсутствует.
Кроме пластификаторов и отвердителей в клеи вводят наполнители. Наполненные полимеры, в том числе и клеи - это сочетание полимеров и
отвергающихся олигомеров с наполнителями с образованием гетерогенных композиций, обладающих новыми свойствами, отличными от свойств исходных компонентов, но сохраняющих индивидуальность каждого компонента. При наполнении полимер всегда образует непрерывную фазу (матрицу), а наполнитель – дисперсную или другую фазу.
Фазовая структура наполненных композиций задается формой наполнителя и его распределением в полимерной матрице, причем взаимодействие по- лимер-наполнитель осуществляется преимущественно за счет смачивания и адсорбции на границе раздела.
В зависимости от назначения наполнители подразделяются на усиливающие, или армирующие, улучшающие фрикционные, антифрикционные, диэлектрические, теплофизические и др. свойства.
Введение наполнителей позволяет регулировать вязкость клея, менять модуль упругости клеевого шва, уменьшать усадку, повышать коэффициент термического расширения, а тем самым статическую и ударную прочность, тепло- и морозостойкость клеевых швов. Наполнители, кроме того, снижают стоимость клеев.
По форме частиц наполнители делятся на два основных класса - волокнистые и дисперсные (порошковые, зернистые). К дисперсным наполнителям относятся природные или искусственные порошки - неорганические (силикаты, оксиды, гидроксиды, карбонаты, сульфаты, минеральные стекла и т.п.) и органические (древесная мука, молотая кора и т.п.).
190
При склеивании изделий необходимо знать не только свойства клеев, применяемых для соединения различных материалов, но и свойства склеиваемых материалов.
В практике различают два типа склеиваемых материалов: пористые и непористые. Следовательно, возникает необходимость в склеивании материалов пористых с пористыми, пористых с непористыми, непористых с непористыми. В табл. 17.1 приведены клеи, применяемые для склеивания тех или иных материалов.
Таблица 17.1 Виды клеев, применяемые для склеивания различных материалов
|
|
|
|
Резина |
Другие |
Бумага |
Древесина |
Ткань |
Металл |
непористые мате- |
|
с |
риалы (стекло, ке- |
||||
|
|
|
|
металлом |
|
|
|
|
|
|
рамика и т.д.) |
Мочевино- |
Мочевино- |
Мочеви- |
Эпоксидные, |
Резорцино- |
Поливиниловые |
формальде- |
меламино- |
нофор- |
фенолфор- |
формальде- |
эфиры, эпоксид- |
гидная смо- |
резорцино- |
мальде- |
мальдегид- |
гидные, мо- |
ные, фенолфор- |
ла, по- |
фенолфор- |
гидные |
ные, моди- |
дифициро- |
мальдегидные |
ливинило- |
мальдегид- |
|
фицирован- |
ванные по- |
смолы, модифици- |
вые эфиры |
ные |
|
ные поливи- |
ливинилаце- |
рованные поливи- |
|
|
|
нилацета- |
талями, и |
нилацеталями |
|
|
|
лями |
эпоксидные |
|
При выборе клея необходимо учитывать степень их водостойкости. Водостойкость клеев при различных температурах приведена в табл.17.2.
|
Водостойкость различных клеев |
Таблица 17.2 |
||
|
|
|||
|
|
|
|
|
|
Стойкие при температуре |
Неограниченно |
||
|
|
|
стойкие в |
|
20ºС |
70ºС |
100°С |
||
кипящей воде |
||||
|
|
|
|
|
Битумы, моче- |
|
Мочевиноформальдегидные, |
|
|
Мочевино- |
модифицированные меламино- |
|
||
виноформаль- |
формальде- |
или резорциноформальдегид- |
Меламино-ре- |
|
дегидные смо- |
гидные и по- |
ными смолами, эпоксидные, фе- |
зорцинофенол- |
|
лы с крахмалом, |
лиэфирные |
нолформальдегидные клеи, мо- |
формальдегид- |
|
поливиниловые |
смолы |
дифицированные поливинил- |
ные клеи |
|
эфиры |
|
ацеталями, некоторые поли- |
|
|
|
|
амидные смолы |
|
191
Виды клеев, технология склеивания |
|
|
|
|
|
|
|
Таблица 17.3 |
||
|
|
|
|
|
|
|
|
|||
|
|
|
Жизне- |
|
Условия склеивания |
|
Характеристика |
|||
Клей |
Состав |
Назначение |
|
|
дав- |
темпе- |
дли- |
после- |
||
способ- |
|
открытая вы- |
ление, |
ратура |
тель- |
дующ. |
клеевого |
|||
|
|
|
ность |
|
держка |
2 |
ºС |
ность, |
выдерж- |
соединения |
|
|
|
|
|
|
кг/см |
ч. |
ка, ч |
|
|
|
|
|
|
|
|
|
|
|
||
I |
2 |
3 |
4 |
|
5 |
6 |
7 |
8 |
9 |
10 |
Акрилатный |
Стружка орг- |
Склеивание ор- |
3 мес |
|
10-15 мин |
1-2 |
15-25º |
4-6 |
|
Прочность при от- |
|
стекла, раство- |
ганических сте- |
|
|
|
|
|
|
|
рыве - 80кг/см2; |
|
ритель - дихло- |
кол |
|
|
|
|
|
|
|
водостоек, прозра- |
|
рэтан |
|
|
|
|
|
|
|
|
чен |
Перхлорви- |
Перхлорвинил, |
Наклеивание ви- |
1 год |
|
На металл два |
1-2 |
20 |
24 |
|
Малая прочность, |
ниловый |
растворитель – |
нипласта на ме- |
|
|
слоя по 60 |
|
|
|
|
водостоек |
|
метиленхлорид |
талл |
|
|
мин при 20ºС, |
|
|
|
|
|
|
|
|
|
|
третий слой- |
|
|
|
|
|
|
|
|
|
|
18ч. при |
|
|
|
|
|
|
|
|
|
|
20ºС.На ви- |
|
|
|
|
|
|
|
|
|
|
нипласт- |
|
|
|
|
|
|
|
|
|
|
один слой |
|
|
|
|
|
|
|
|
|
|
18ч. при 20ºС |
|
|
|
|
|
Б-3, Ф-9 |
Фенолформаль- |
Склеивание дре- |
После |
|
5-10мин |
0,5-5 |
20 |
2-4 |
20 |
Водо-, грибо-, топ- |
ВИАЙ |
дегидная смола, |
весины, шпона, |
смешива- |
|
|
|
|
|
|
ливо- и масло- |
|
отвердитель - |
древеснослои- |
ния 2ч при |
|
|
|
|
|
стоек; прочность |
|
|
сульфоконтакт, |
стого пластика, |
15-20ºС |
|
|
|
|
|
|
при сдвиге - |
|
стабилизатор - |
текстолита, пе- |
|
|
|
|
|
|
|
120кг/см2 |
|
ацетон, спирт |
нопласта |
|
|
|
|
|
|
|
|
|
|
|
|
|
|
|
|
|
|
|
Карбамид- |
Мочевинофор- |
Склеивание дре- |
После |
|
- |
0,5-5 |
20 |
4-6 |
20 при |
Ограниченно водо- |
ный К-17 |
мальдегидная |
весины, шпона |
смешива- |
|
|
|
|
|
20ºС |
стоек (потеря |
|
смола, ускори- |
|
ния 3ч |
|
|
|
|
|
|
прочности до |
|
тель отвержде- |
|
|
|
|
|
|
|
|
50%), прочность на |
|
ния - щавелевая |
|
|
|
|
|
|
|
|
сдвиг - 130кг/см2 |
|
кислота, напол- |
|
|
|
|
|
|
|
|
|
|
нитель - древес- |
|
|
|
|
|
|
|
|
|
|
ная мука |
|
|
|
|
|
|
|
|
|
|
|
|
|
192 |
|
|
|
|
|

|
|
|
|
|
|
|
|
Продолжение табл. 17.3 |
|
|
|
|
|
|
|
|
|
|
|
10 |
|
I |
2 |
3 |
4 |
5 |
6 |
7 |
8 |
9 |
|
|
БФ-2, |
Фенолформаль- |
Склеивание ме- |
6 мес |
Два слоя по |
5-20 |
140- |
1 |
- |
Прочность при сдвиге |
|
БФ-4 |
дегидная смола, |
таллов, пластмасс, |
|
30мин при |
|
160 |
|
|
– 100кг/см2, водо-, |
|
|
поливинилаце- |
керамики, стекла |
|
30ºС, затем |
|
|
|
|
масло-, бензо- и гри- |
|
|
таль, раствори- |
|
|
второй слой |
|
|
|
|
бостоек. Рабочая тем- |
|
|
тель - спирт |
|
|
при 60ºС, тре- |
|
|
|
|
ператур от -60 |
|
|
|
|
|
тий слой 15мин |
|
|
|
|
до+60ºС |
|
|
|
|
|
при 90ºС |
|
|
|
|
Прочность при сдвиге |
|
ЭД холод- |
Эпоксидная |
Склеивание ме- |
20-30 |
- |
0,2-2 |
20 |
4 |
|
|
|
ного отвер- |
смола, отверди- |
таллов, пластмасс, |
мин при |
|
|
|
|
|
– 200-250кг/см2, теп- |
|
ждения |
тель - гексамети- |
пенопластов, де- |
20ºС |
|
|
|
|
|
лостойкость до 60ºС |
|
|
лендиамин или |
ревянных изде- |
|
|
|
|
|
|
|
|
|
полиэтиленпо- |
лий, шпона, стек- |
|
|
|
|
|
|
|
|
|
лиамин |
ла |
|
|
|
|
|
|
Прочность при сдвиге |
|
ЭД горячего |
Эпоксидная |
Склеивание ме- |
4-6 ч |
- |
0,2-2 |
160- |
12 |
12 |
|
|
отверждения |
смола, отверди- |
таллов, стекла, ке- |
|
|
|
180 |
|
при |
- 300-350кг/см2; теп- |
|
|
тель - малеино- |
рамики |
|
|
|
|
|
20ºС |
лостойкость - до 80ºС; |
|
|
вый ангидрид |
|
|
|
|
|
|
|
водо- и топливостоек |
|
Мати K-I |
Сплав эпоксид- |
Склеивание ме- |
2-3 мес |
- |
0,2-2 |
150 |
6 |
- |
Прочность на сдвиг - |
|
|
ной смолы с фе- |
таллов, керамики, |
|
|
|
|
|
|
350кг/см2; теплостой- |
|
|
нолформальде- |
стекла |
|
|
|
|
|
|
кость до 150ºС; водо- |
|
|
гидной и поли- |
|
|
|
|
|
|
|
и топливостоек |
|
|
винилацетатом |
|
|
|
|
|
|
|
Прочность при сдвиге |
|
ВС-10-Т |
|
Склеивание ме- |
6 мес |
Два слоя по |
0,5-5 |
140- |
1-2 |
- |
|
|
|
|
таллов |
|
60мин при |
|
180 |
|
|
- 160кг/см2; тепло- |
|
|
|
|
|
20ºС |
|
|
|
|
стойкость до 300ºС; |
|
|
|
|
|
|
|
|
|
|
удовлетворительно |
|
|
|
|
|
|
|
|
|
|
водо-, масло- и бензо- |
|
|
|
|
|
|
|
|
|
|
стоек |
|
К-153 ком- |
Эпоксидная |
Склеивание ме- |
0,7-1,0ч |
- |
0,2-2,0 |
20 |
18-24 |
72 |
Прочность при сдвиге |
|
паунд |
смола, тиокол, |
таллов, пластмасс, |
|
|
|
|
|
|
130-150кг/см2, тепло- |
|
|
МГФ-9; отвер- |
стекла, деревян- |
|
|
|
|
|
|
стойкость до 60ºС |
|
|
дитель - ПЭПА |
ных изделий |
|
|
|
|
|
|
|
|
193
III. ОБОРУДОВАНИЯ, ПРИБОРЫ, МАТЕРИАЛЫ
Для выполнения работы необходимо иметь следующее; I. Образцы для склеивания.
2.Клеи, наполнители, ацетон, бензин - растворитель.
3.Приспособления для склеивания, гидропресс или разрывную машину, приспособления для испытаний.
4.Штангенциркуль, микрометр, напильники, шаберы, бумагу наждачную.
5.Микроскоп МИМ-7 или ММУ-3М.
IV. МЕТОДИЧЕСКИЕ УКАЗАНИЯ ПО ВЫПОЛНЕНИЮ РАБОТЫ
1.Ознакомиться с техникой безопасности.
2.Получить трубчатые образцы, образцы "грибок", прямоугольные образцы из стали, винипласта, органического стекла или других материалов (рис. 17.I).
3.Подготовить поверхность образцов к склеиванию, по указанию преподавателя произвести механическую или химическую очистку.
4.Произвести замеры образцов микрометром или штангенциркулем. Результаты занести в протокол испытаний (табл. 17.5).
5.Обезжирить склеиваемые поверхности образцов ацетоном или бензи- ном-растворителем и высушить в течение 10-15 мин.
6.Подобрать составы клеев (табл. 17.4), приготовить клей.
7.Нанести клей шпателем на склеиваемые поверхности, выдержать образцы на воздухе при комнатной температуре в течение 5-10 мин, произвести склеивание образцов.
8.Режим склеивания (температура и время отверждения) выбрать по указанию преподавателя.
9.Убрать рабочее место.
10.После отверждения клеевых композиций замерить длину склеивания ℓ трубчатых образцов.
10.Произвести испытание образцов на сдвиг и равномерный отрыв на гидропрессе или разрывной машине. Скорость движения нагружающего зажима 10 мм/мин. Показания манометра ρ (в момент разрушения клеевого соединения) занести в протокол испытаний.
12.Рассчитать прочностные характеристики клеевых соединений по формулам, приведенным в протоколе.
13.Изучить структуру клеевых соединений на микроскопе ММУ-3М или МИМ-7 в отраженном свете при увеличениях в 100 и в 500 раз. Определить форму частиц наполнителя.
Зарисовать структуры в отчете.
194

Об резцы для склеивания
а– трубчатые образцы для определения прочности при сдвиге;
б– образцы "грибок" для определения прочности при равномерном отрыве;
в– образцы - пластины для определения прочности при сдвиге (15±0,5
мм- длина склеивания);
I – склеиваемые образцы; 2 - клеевой слой.
Примявшие. Скорость движения нагруженного зажима 10 мм/мин
Рис. 17.1
195
14. Пользуясь табл. 17.I; 17.2; 17.3; 17.4 выбрать вид клея (композиции) для склеивания деталей (заданных преподавателем), технологию склеивания, режим отверждения; описать свойства клея.
V. СОДЕРЖАНИЕ ОТЧЕТА
1.Дать сведения о выбранных клеях, их свойствах, особенностях и областях применения.
2.Зарисовать эскизы склеиваемых образцов с указанием размеров, материала образца, дать метод очистки поверхности образцов и вид растворителя для обезжиривания образцов.
3.Дать клеевые составы с указанием назначения компонентов.
4.Указать режим отверждения клеевых составов (температура, время минимальное и оптимальное).
5.В протокол испытаний занести результаты испытаний, произвести расчеты прочностных характеристик клеевых соединений, табл. 17.5.
6.Зарисовать структуру клеевого соединения: структуру склеиваемого материала образцов - субстрата и структуру клеевого шва (увеличение в 100 раз).
7.Зарисовать структуру клеевой гетерогенной композиции (увеличение в
500 раз);
а) определить тип надмолекулярной структуры эпоксидной или полиэфирной композиции в случае ее детерминации;
б) определить вид, форму и размеры частиц наполнителя.
8.Объяснить влияние состава клея и режима отверждения на свойства клеевых соединений.
VI. ТЕХНИКА БЕЗОПАСНОСТИ
Эпоксидные, полиэфирные смолы токсичны. Пары и пыль смол и отвердителей действуют раздражающе на слизистые оболочки горла, носа и глаз, вызывают кашель, головокружение, припухлость лица и рук, дерматиты. Поэтому при выполнении лабораторной работы соблюдаются следующие правила:
I.Работа проводится при включенной приточно-вытяжной вентиляции;
2.Студенту необходимо одеть спецодежду - халат;
3.На руки надеть резиновые перчатки или нанести "биологические пер-
чатки";
4.Рабочие столы покрыть бумагой, которую после окончания работы уб-
рать;
196

|
Рецептура клеевых составов на основе эпоксидных и полиэфирных смол |
|
|
|
|
|
Таблица 17.4 |
||||||||
|
|
|
|
|
|
|
|
||||||||
|
Компонент состава |
Роль компонента |
|
|
|
Содержание компонента, М, ч |
|
|
|
||||||
|
|
|
|
|
|
|
номера клеевых составов |
|
|
|
|||||
|
|
|
1 |
2 |
3 |
|
4 |
|
5 |
6 |
7 |
|
8 |
9 |
10 |
|
1 |
2 |
3 |
4 |
5 |
|
6 |
|
7 |
8 |
9 |
|
10 |
11 |
12 |
I. ЭПОКСИДНЫЕКЛЕИ |
|
|
|
|
|
100 |
|
|
|
|
|
|
|
|
|
1. |
Смола эпоксидная |
Связующее |
100 |
- |
- |
|
|
- |
- |
100 |
|
- |
- |
100 |
|
|
ЭД-20 |
|
|
|
|
|
- |
|
|
|
|
|
|
|
|
2. |
Смола эпоксидная |
То же |
- |
100 |
- |
|
|
|
|
- |
|
100 |
- |
- |
|
|
УП-5-177-1 |
|
|
|
|
|
|
|
|
|
|
|
|
|
|
|
|
|
|
|
|
- |
|
|
|
|
|
|
|
|
|
3. |
Смола эпоксидная |
-"- |
- |
- |
100 |
|
|
- |
- |
- |
|
- |
100 |
- |
|
|
УП-5-177 |
|
|
|
|
|
|
|
|
|
|
|
|
|
|
|
|
|
|
|
|
- |
|
|
|
|
|
|
|
|
|
4. |
Полиэтиленполиамлн |
Отвердитель |
10-12 |
- |
- |
|
|
- |
- |
10-12 |
|
- |
- |
10-12 |
|
|
(ПЭПА) |
|
|
|
|
|
- |
|
|
|
|
|
|
|
|
5. |
УП-5-159 |
То же |
- |
10 |
10 |
|
|
- |
- |
- |
|
10 |
10 |
- |
|
6. |
УП-5-583 |
-"- |
- |
11 |
- |
|
- |
|
- |
- |
- |
|
11 |
- |
- |
7. |
Низкомолекулярные |
-"- |
- |
- |
- |
|
100 |
|
- |
- |
- |
|
- |
- |
- |
|
полиамиды Л18 (Л20) |
|
|
|
|
|
|
|
|
|
|
|
|
|
|
|
|
|
|
|
|
- |
|
|
|
|
|
|
|
|
|
8. |
Дибутилфталат (ДБФ) |
Пластификатор |
10-15 |
- |
- |
|
|
- |
- |
10-15 |
|
- |
- |
10-15 |
|
II. КЛЕЙ «СПРУТ-9М» |
|
|
|
|
|
- |
|
|
|
|
|
|
|
|
|
9. |
Смола полиэфирная |
Связующее |
- |
- |
- |
|
|
100 |
100 |
- |
|
- |
- |
- |
|
|
НПС-609-21М |
|
|
|
|
|
- |
|
|
|
|
|
|
|
|
10. Полиуретановая сос |
То же |
- |
- |
- |
|
|
70 |
70 |
- |
|
- |
- |
- |
||
|
тавляющая АТЖ-М |
|
|
|
|
- |
|
|
|
|
|
|
|
|
|
11. Перекись метилэтил- |
Инициатор |
- |
- |
- |
|
|
4 |
4 |
- |
|
- |
- |
- |
||
|
|
|
|
|
|
|
|
|
|
|
|
|
|||
|
кетона (ПМЭК) |
|
|
|
|
|
|
|
|
|
|
|
|
|
|
197
|
|
|
|
|
|
|
|
|
Продолжение табл.17.4 |
|||
|
1 |
2 |
3 |
4 |
5 |
6 |
7 |
8 |
9 |
10 |
11 |
12 |
12. |
10%-ный раствор неф- |
Ускоритель |
- |
- |
- |
- |
4 |
4 |
- |
- |
- |
- |
|
тената кобальта в |
|
|
|
|
|
|
|
|
|
|
|
|
стироле (НК) |
|
|
|
|
|
|
|
|
|
|
|
13. |
Портландцемент |
Наполнитель |
- |
- |
- |
200 |
- |
- |
150-200 |
- |
- |
- |
14. |
Графит серебристый |
То же |
- |
- |
- |
- |
- |
- |
- |
50-100 |
- |
- |
15. |
Маршалит |
-"- |
- |
- |
- |
- |
100 |
- |
- |
- |
100 |
- |
|
(кварцевая мука) |
|
|
|
|
|
|
|
|
|
|
|
|
|
|
|
|
|
|
|
|
|
|
|
|
16. |
Железный порошок |
-"- |
- |
250 |
- |
- |
- |
- |
- |
- |
- |
- |
17. |
Асбестовая крошка |
-"- |
- |
- |
- |
- |
- |
10 |
- |
- |
- |
10 |
|
(асбест распушонный) |
|
|
|
|
|
|
|
|
|
|
|
|
|
|
|
|
|
|
|
|
|
|
|
|
18. |
Пудра алюминиевая |
-"- |
10-15 |
- |
- |
- |
- |
- |
- |
- |
- |
- |
19. |
Пудра бронзовая |
-"- |
- |
- |
10-15 |
- |
- |
- |
- |
- |
- |
- |
198

Таблица 17.5
|
|
|
|
|
Протокол испытаний |
|
|
|
|
|
|
|
|
|
|
|
||||||
|
|
|
|
|
|
|
|
|
|
|
|
|
|
|
|
|
|
|
|
|
|
|
|
Трубчатые |
|
|
|
|
С к л е и в а е м ы й |
м а т е р и а л |
|
|
|
|
|
|
|
||||||||
|
образцы по |
|
|
|
|
|
|
|
|
|
|
|
|
|
|
|
|
|
|
|
|
|
|
d1 |
|
d2 |
|
dср |
t= |
d2 d1 |
ℓ |
|
ρ |
P=50ρ |
τсдв |
|
P |
|
|
|
50 |
|
|||
|
рис. 17.1. Ис- |
|
|
|
|
|
|
|||||||||||||||
1 |
|
|
2 |
|
|
F |
|
dc |
||||||||||||||
пытание на |
|
|
|
|
|
|
|
|
|
|
|
|
|
|
|
|
|
|||||
мм |
|
мм |
|
мм |
|
|
мм |
мм |
кГс/см2 |
кг |
МПа(кГс/мм2) |
|||||||||||
|
сдвиг |
|
|
|
|
|||||||||||||||||
|
|
|
|
|
|
|
|
|
|
|
|
|
|
|
|
|
|
|
|
|
|
|
|
Образцы |
|
|
|
|
С к л е и в а е м ы й |
м а т е р и а л |
|
|
|
|
|
|
|
||||||||
|
«грибок» по |
|
|
|
|
|
|
|
|
|
|
|
|
|
|
|
|
|
|
|
|
|
|
d |
|
|
|
ρ |
|
|
|
|
t |
|
отр |
|
4P |
|
|
|
|||||
|
рис. 17.1. |
|
|
|
|
|
|
|
|
|
|
|
||||||||||
2 |
|
|
|
|
|
|
|
|
d 2 |
|
|
|||||||||||
Испытание на |
|
|
|
|
|
|
|
|
|
|
|
|
|
|
|
|
|
|
|
|
|
|
мм |
|
кГс/см2 |
|
кг |
|
|
мм |
|
МПа(кГс/мм2) |
|||||||||||||
|
равномерный |
|
|
|
|
|
||||||||||||||||
|
отрыв |
|
|
|
|
|
|
|
|
|
|
|
|
|
|
|
|
|
|
|
|
|
|
|
|
|
|
|
|
|
|
|
|
|
|
|
|
|
|
|
|||||
|
Плоские об- |
|
|
|
|
С к л е и в а е м ы й |
м а т е р и а л |
|
|
|
|
|
|
|
||||||||
|
разцы по рис. |
|
|
|
|
|
|
|
|
|
|
|
|
|
|
|
|
|
|
|
|
|
|
F |
|
|
|
ρ |
|
P=50ρ |
|
t |
|
τсдв= |
P |
|
|
|
|
|
|||||
|
17.1. Испыта- |
|
|
|
|
|
|
|
|
|
|
|
||||||||||
|
|
|
|
F |
|
|
|
|
|
|||||||||||||
|
|
|
|
|
|
|
|
|
|
|
|
|
|
|
|
|
|
|
|
|
||
3 |
ние на сдвиг |
|
|
|
|
|
|
|
|
|
|
|||||||||||
мм2 |
|
кГс/см2 |
|
кг |
|
|
мм |
|
МПа(кГс/мм2) |
|||||||||||||
|
|
|
|
|
|
|
|
|
|
|
|
|
|
|
|
|
|
|
|
|
|
|
t – толщина клеевого слоя;
ρ – давление в цилиндре гидропресса (показание манометра); 50 – площадь поршня гидропресса, см2;
P – разрушающее усилие;
F – площадь поверхности склеивания; τсдв – предел прочности при сдвиге;
σотз – предел прочности при равномерном отрыве
199
5. Брызги смолы, отвердителя или клея при попадании на кожу смыть марлевым тампоном, смоченным этиловым спиртом, затем пораженное место тщательно промыть теплой водой с мылом, высушить.
VII. ВОПРОСЫ ДАЯ САМОПРОВЕРКИ
1.Какие вещества называются клеями?
2.В чем преимущество клеевых соединений перед сваркой, клепкой и другими механическими способами крепления?
3.В чем недостатки клеевых соединений?
4.Какие факторы влияют на качество клеевого шва?
5.Классификация клеев по способу изготовления, по физическому состоянию до отверждения.
6.Отличие и примеры обратимых и необратимых клеев.
7.Что такое адгезия и когезия?
8.Особенности эпоксидных клеев, области применения.
9.Какова роль пластификаторов и наполнителей в клеевых композициях?
10.Отвердители холодного и горячего отверждения.
11.Особенности клеев типа "Спрут", области применения.
12.Каким испытаниям подвергаются клеевые соединения?
13.Что такое гетерогенные композиции? Как определить их структуру?
14.Как повысить теплостойкость клеев? Виды термостойких клеев.
200
ЛАБОРАТОРНАЯ РАБОТА № 18 ИЗУЧЕНИЕСТРУКТУРЫИСВОЙСТВЗАЩИТНЫХПОЛИМЕРНЫХПОКРЫТИЙ
1. ЦЕЛЬ РАБОТЫ: ознакомиться с важнейшими классами защитных полимерных покрытий; изучить влияние состава покрытия, технологии формирования покрытия на его свойства, структуру.
II. КРАТКИЕ ТЕОРЕТИЧЕСКИЕ СВЕДЕНИЯ
Полимерные материалы применяются для защиты материалов (метало, бетона, дерева и др.) от коррозии, разрушения; как декоративные покрытия, а также для специальных целей: теплоили злектроизоляции, предохранения подводной части морских судов от обрастания раковинами, холодного свечения поверхности (люминесценция), увеличения огнестойкости, маслостойкости, антифрикционных свойств и т.д.
Долговечность покрытия зависит от ряда факторов: тщательной подготовки поверхности, правильного выбора соответствующего покрытия и состава покрытия, метода нанесения (формирования), условий отвердевания (высыхания) покрытия.
Наиболее широко применяются лакокрасочные материала (лаки, эмали, краски, грунты, шпаклевки), основными компонентами которых являются пленкообразующие вещества, растворители, сиккативы или отвердители, красители или пигменты и др.
В последние годы все большее применение находят покрытия (Пк), получаемые на основе твердых порошкообразных полимеров - порошковые «краски». Эти ПК наносят более производительными и экономичными методами, при реализации которых меньше загрязняется окружающая среда летучими компонентами (растворители, сиккативы). В формируемом ПК отсутствуют низкомолекулярные продукты, что обеспечивает повышенные защитные и диэлектрические свойства. Кроме того, создается возможность нанесения на детали слоя ПК до I мм и более.
Процесс нанесения ПК осуществляется следующими способами:
1) напыляя расплавленный порошок полимера на слабо нагретую деталь (газопламенное напыление); 2) нанося порошок полимера на поверхность нагретых деталей (пневмораспыление, в псевдокипящем слое, электростатическое напыление и др.).
Порошковые материалы (полимеры, наполнители и др.), применяемые для получения Пк имеют размер частиц примерно 10-7-10-4м. Мелкие частицы склонны к агрегации; установить их истинный размер можно специальными методами. Порошки могут быть монодисперсными и полидисперсными. Промышленные полимеры всегда полидисперсны. Чем выше степень дисперсности
201
порошка, тем более он подвержен увлажнению, что отрицательно сказывается на технологических свойствах порошков при формировании покрытия.
Общими требованиями для порошковых полимеров являются:
-способность находиться в дисперсном (порошковом) состоянии до нанесения;
-способность к пленкообразованию, т.е. формированию монолитной сплошной пленки на защищаемой поверхности.
Для покрытий используются термопласты - полиамиды, полиолефины, полихлорвинил и др.; реактопласты - полиэпоксиды, полиэфиры, полиуретаны и др.
Достоинством термопластов являются стабильность получаемых на их основе композиций, быстрое (в течении нескольких минут) формирование покрытия, доступность материалов, связанная с большим масштабом их производства. Однако покрытия из термопластов обратимы, имеют невысокую теплостойкость и во многих случаях (при использовании аморфных полимеров) неустойчивы к действию растворителей.
Реактопласты образуют необратимые покрытия с повышенной тепло- и химической стойкостью, адгезионной прочностью, однако характеризуются более длительным временем формирования Пк.
Для получения покрытий применяют как аморфные, так и кристаллические полимеры. Аморфные полимеры имеют более высокую адгезию, но уступают кристаллическим по химической стойкости, проницаемости к жидкостям и газам и по защитным свойствам покрытий. Полимеры с менее упорядоченной кристаллической структурой легче перерабатываются, образуют покрытия с меньшими внутренними напряжениями, лучшей адгезией и более долговечны, поэтому они более применяются в практике.
При формировании Пк полимер нагревают до состояния расплава (вязкотекучего состояния). Температуру текучести и часто температуру плавления полимеров определяют по положению термомеханической кривой (рис. 18.I), выражающей зависимость деформации растяжения (под влиянием внешней нагрузки) от температуры. Температура текучести Тт аморфных полимеров - средняя температура, определяющая область перехода полимера из высокоэластичного состояния в вязко-текучее. Кристаллические полимеры характеризуются температурой плавления Т пл, подразумевая под этим среднюю температуру плавления кристаллических образований. В табл. 18.1 даны температуры фазовых и агрегатных переходов полимеров, температуры нагрева изделий.
202

Таблица 18.1 Температура фазовых, агрегатных переходов полимеров
Полимеры |
Степень кристал- |
Тс,°С |
Тпл, °С |
Тт, °С |
|
|
личности, % |
|
|
|
|
1 |
2 |
3 |
4 |
5 |
|
*Полиэтилен низкого дав- |
80-90 |
-60 |
120-125 |
145 |
|
ления |
|||||
|
|
|
|
||
*Полиэтилен высого дав- |
53-67 |
-70 |
108-115 |
130 |
|
ления |
|||||
|
|
|
|
||
*Полиэтилен среднего |
85-93 |
-60 |
127-130 |
146 |
|
давления |
|||||
|
|
|
|
||
Полипропилен |
40-65 |
-15 |
164-170 |
160 |
|
Фторопласт-4 |
50-70 |
-120 |
327 |
415 |
|
Фторопласт-42Л |
44-45 |
- |
150-160 |
- |
|
Полиамид П-68 |
40-85 |
50 |
210 |
310 |
|
Поликапролактам |
46-60 |
-25 |
210-218 |
220 |
|
Поливинилбутираль |
Аморфный |
53 |
165 |
180-195 |
|
Эпоксиолигомеры |
- |
30-85 |
- |
55-130 |
*В графе Тс для этих полимеров приведены температуры хрупкости
Термомеханические кривые аморфного (I) и кристаллического (К) полимеров
Рис. 18.I
203
Температура разложения (деструкции) полимера условно определяет верхний температурный предел формирования покрытий из расплавов (нижний предел характеризуется температурой текучести).
Полимеры и олигомерные пленообразователи редко применяют для получения Пк в индивидуальном виде. В большинстве случаев для придания необходимых технологических и эксплуатационных свойств их совмещают с различными ингредиентами: пластификаторами, стабилизаторами, отвердителями, пигментами, наполнителями и т.д. Получаемые в результате порошковые смеси (или композиции) по аналогии с жидкими лакокрасочными материалами называют "Порошковыми лаками и красками". Пластификаторы применяют для снижения температуры формирования Пк, улучшения их механических свойств (пластичности) и часто морозостойкости, снижения внутренних напряжений в Пк. Кроме того, для многих пластифицированных Пк характерна более высокая адгезия. Однако при пластификации ухудшаются диэлектрические показатели и химическая стойкость покрытий.
Наполнители вводят для улучшения механических свойств, повышения защитных качеств и атмосферостойкости, уменьшения усадки, направленного изменения электрических, теплофизических и других показателей Пк. Оптимальное содержание наполнителей для композиций на основе поливинилбутираля не выпе 15-20% (масс.), на основе полиэтилена - 3-5% (масс.).
Формирование структуры и свойств полимерного покрытия При образовании твердой пленки полимер переходит из вязкотекучего
состояния в стеклообразное или кристаллическое. Этот переход связан со структурными превращениями пленкообразователей в Пк. Особенно сильно режим охлаждения сказывается на структуре и свойствах (степени кристалличности, размере кристаллов, размере и морфологии сферолитов) кристаллических полимеров.
Различные полимеры кристаллизуются по разному. Так полиолефины обладают высокой скоростью кристаллизации. Область наиболее интенсивной кристаллизации ПЭНД лежит в пределах 100-120°С, т.е. на 10-20°С ниже температуры плавления. Применяя медленное охлаждение (отжиг) или быстрое (закалку), можно получить покрытия, отличающиеся по степени кристалличности в случае ПЭНД на 12-15%, ПЭВД на 2-3%, ПЭСД - на 5-6%.
Поликапролактам кристаллизуется инстенсивно при 185°С. В случае быстрого охлаждения расплава под водяным душем (скорость охлаждения 4550°С/мин) наблюдаются бесструктурные поля.
204
Режим охлаждения влияет не только на первичную кристаллическую структуру полимеров, но в еще большей степени на вторичную, надмолекулярную структуру. Сферолитная кристаллизация обычно происходит в той же области температур, что и формирование первичной структуры поэтому для каждого полимера важно выбрать правильный режим охлаждения именно в этом температурном интервале. Структурные изменения в полимерах сказываются на свойствах получаемых покрытий. Так, со степенью кристалличности α определенным образом коррелируются внутренние напряжения в покрытиях: в покрытиях из ПЭСД (α =93%) внутренние напряжения в 5 раз больше, чем в покрытиях из ПЭВД (α =62%).
На внутренние напряжения влияет также режим охлаждения покрытия. Для большинства кристаллических полимеров (ПЭВД, полипропилен, полиамиды и др.) при увеличении скорости охлаждения покрытий внутренние напряжения снижаются. Для аморфных полимеров быстрое охлаждение покрытий способствует увеличению внутренних напряжений.
Адгезия с ростом степени кристалличности α понижается, так как всякое упорядочение структуры приводит к уменьшению поверхностной энергии на границе пленка-подложка. Закалка, как один из способов уменьшения упорядоченности, обычно повышает адгезию.
Надмолекулярная структура полимеров существенно влияет на свойства покрытий. С ростом дискретных (надмолекулярных) структур ухудшатся механические, электрические, антифрикционные и защитные свойства пленки.
Свойства пропиленовых покрытий толщиной 300-500 мкм, полученных при различных скоростях охлаждения, приведены в табл. 18.2.
Свойства полипропиленовых покрытий |
Таблица 18.2 |
|||
|
||||
|
|
|
|
|
Показатель |
Скорость охлаждения, °С/мин |
|||
1 |
10 |
150 |
||
|
||||
Размер сферолитов, мкм |
150 |
30-40 |
10 |
|
Прочность при растяжении, МПа |
6,9 |
11,5 |
14,8 |
|
Относительное удлинение при разры- |
5 |
100 |
1500 |
|
ве δ ,% |
||||
|
|
|
||
Твердость, МПа |
49 |
47,4 |
38,4 |
|
Прочность на удар по У-IA, Н•м |
1,0 |
4,9 |
4,9 |
|
Внутренние напряжения, МПа |
2,6 |
2,3 |
1,1 |
|
Гибкость по ШГ-1, мм |
15 |
3 |
I |
Многие свойства Пк определяются его толщиной. Толщина Пк зависит от времени напыления, числа слоев Пк, температуры предварительного нагрева детали и др. факторов (рис. 18.2).
205

Зависимость толщины покрытий из полиэтилена высокой плотности ( - ) и поливинилбутираля (- - -) от продолжительности выдержки изделия в кипящем слое
Рис. 18.2
Недостатком большинства Пк, получаемых из порошковых пленкообразователей, является наличие газовых включений, которые отрицательно влияют на адгезию Пк, механическую прочность и изолирующие свойства пленок. Эффективным путем уменьшения газовых включений является нанесение порошков более тонким слоем (использование принципа многослойных покрытий) и соблюдение требуемых режимов формирования Пк.
III. ОБОРУДОВАНИЕ, ПРИБОРЫ, МАТЕРИАЛЫ
1.Установка для нанесения покрытий в псевдокипящем слое, муфельная печь для нагрева образцов, термометры.
2.Толщиномер покрытий ТПМ-Л5, микрометр, дефектоскоп ЛКД-1, дефектоскоп ЭД-5, прибор У-IA, шкала гибкости ШГ-1, маятниковый прибор МЭ- 3, секундомер.
3.Порошкообразные полимеры, "краски", растворители для обезжиривания образцов.
206

IV. МЕТОДИЧЕСКИЕ УКАЗАНИЯ ПО ВЫПОЛНЕНИЮ РАБОТЫ
I.Оформить протокол испытаний (табл. 18.4).
2.Включить муфельную печь и установить ее терморегулятор на заданную температуру.
3.Ознакомиться с оборудованием для нанесения покрытий в псевдокипящем слое полимера. Зарисовать схему лабораторной установки (рис. 18.3).
Схема установки для нанесения покрытия в псевдокипящем слое
1 - камера; 2 - изделие; 3 - осевшие на изделие частицы полимера; 4 - не осевшие на изделие частицы полимера; 5 – пористая перегородка.
Рис. 18.3
4. Зачистить поверхности образцов (кроме стеклянного) шлифовальной бумагой до металлического блеска, тщательно обезжирить поверхность ацетоном или бензином – растворителем. Замерить толщину образцов микрометром, результаты занести в протокол.
207

5. Нагреть образцы в муфельной печи в течение заданного времени. Основные технологические параметры получения покрытий в псевдокипящем слое (ориентировочные!) для изделий с толщиной стенки 1-8 мм приведены в табл. 18.3.
Таблица 18.3
Температурные режимы получения покрытий в псевдокипящем слое (на стальных образцах)
|
Температура |
Продолжи- |
Темпера- |
Продолжи- |
|
Порошковый полимерный |
предвари- |
тельность |
тура оп- |
тельность |
|
материал |
тельного на- |
напыления, |
лавления |
оплавле- |
|
|
грева, ºС |
с |
или отвер- |
ния, мин |
|
|
ждения, ºС |
||||
Полиэтилен низкого давления |
320-350(280) |
3-20 |
200 |
|
5 |
Полиэтилен среднего давления |
280 |
3-10 |
200 |
|
5 |
нестабилизированный |
|
|
|
|
|
Полиэтилен высокого давления |
240-320 |
3-10 |
200 |
|
5- 7 |
Полипропилен: |
|
|
|
|
|
нестабилизированный |
240 |
|
180-200 |
|
1-2 |
стабилизированный |
280-300 |
|
240-250 |
|
3-7 |
Поливинилбутиральная краска |
250-320 |
2-4 |
200-230 |
|
2-5 |
ПВЛ-212 |
|
|
|
|
|
Эпоксидная краска П-ЭП-967 |
120-150 |
3-10 |
190 |
|
240 |
6. Нанести покрытие вихревым методом (в псевдокипящем слое полимера): а) включить в сеть электрокомпрессор; б) внимательно следя за уровнем "вскипающего" полимера в камере ус-
тановки, постепенно открывать вентиль на ресивере компрессора, добиваясь увеличения объема порошка полимера в 1,2 - 1,5 раза.
в) вынуть из муфельной печи образец 70x70 мм, опустить в слой полимера на заданное время, затем снова ввести его в печь (не класть!) и дождаться оплавления нанесенного ПК. Повторить напыление заданное количество раз (число слоев покрытия);
г) охладить образец в заданной охлаждающей среде, с указанной скоро-
стью.
7.Нанести покрытие на остальные образцы.
8.Записать в протокол результаты визуального осмотра качества покрытия образцов.
9.Определить свойства покрытия (согласно методическим указаниям, имеющимся в лаборатории), результаты исследований, выраженные в системе СИ, занести в протокол испытаний (табл.18.4):
208
Таблица 18.4
Протокол испытаний покрытий
Способ нанесения: |
|
|
|
|
|
|
Размеры образцов, мм |
70x70 |
70x70 |
120x20 |
120x20 |
90х60 |
|
|
|
|
|
|
|
стекло |
Материал образца |
сталь 15(10) |
жесть черная |
фотоне- |
|||
|
|
|
|
|
|
гативно |
|
|
Замер |
толщины покрытия |
|
||
|
|
определение |
испытание на |
|
||
|
|
изгибостой- |
опреде- |
|||
Вид испытаний покрытия на соответ- |
сплошности по- |
кость. Опреде- |
ление |
|||
|
ствующем образце |
крытия, проч- |
ление прочно- |
условно |
||
|
|
ности на элек- |
сти на электро- |
твердо- |
||
|
|
троискровой |
||||
|
|
искровой про- |
сти |
|||
|
|
пробой, удар |
бой |
|
||
1. |
Толщина образца, мм |
|
|
|
|
|
2. |
Температура в муфельной печи, °С |
|
|
|
|
|
3. |
Время нагрева образца в печи рас- |
|
|
|
|
|
четное, с |
|
|
|
|
|
|
4. |
Название, марка порошкового По- |
|
|
|
|
|
лимера |
|
|
|
|
|
|
5. |
Число слоев покрытия |
|
|
|
|
|
6. |
Время выдержки образца в слое по- |
|
|
|
|
|
лимера (время напыления), с |
|
|
|
|
|
|
7. |
Среда для охлаждения образцов с |
|
|
|
|
|
покрытием |
|
|
|
|
|
|
8. |
Режим (скорость) охлаждения по- |
|
|
|
|
|
крытия, ºС/мин |
|
|
|
|
|
|
9. |
Внешний вид покрытия (характер и |
|
|
|
|
|
месторасположение дефектов) |
|
|
|
|
|
|
10. Толщина покрытия, мм |
|
|
|
|
|
|
11. Сплошность покрытия (по ЛКД-1) |
|
|
|
|
|
12. Прочность на электроискровой пробой (по ЭД-5), кв 13. Электрическая прочность Е, кв/мм
14. Прочность на удар (по У-1А), Н.м 15. Прочность на изгиб (по ШГ-1), мм 16. Условная твердость покрытия (по МЭ-3)
17. Адгезия покрытия (по методу решетчатого надреза)
209
а) замерить толщину покрытия на образцах с помощью толщинометра ТПМ-Л5 или микрометром;
б) определить сплошность покрытия (прибор ЛКД-1); в) испытать покрытие на электроискровой пробой ( прибор ЭД-5), рас-
считать электрическую прочность;
г) определить прочность покрытия на удар, ГОСТ 4765-73, (прибор У-IA); д) провести испытание покрытия на изгиб (прибор ШГ-1) ГОСТ 6806-73; е) испытать покрытие стеклянного образца на условную твердость (при-
бор МЭ-3) - ГОСТ 5233-67;
ж) определить адгезию покрытия методом решетчатого надреза - ГОСТ
15140-78:
10.Построить графики зависимости: время напыления - толщина покрытия; толщина покрытия - прочность на удар.
11.Изучить микроструктуры покрытия в зависимости от режима охлаждения в отвержденном поляризованном свете на микроскопах МИМ-7 или ММУ-3М, зарисовать микроструктуру покрытия подготовленных микрошлифов, указать увеличение микроскопа; определить вид надмолекулярной структуры полимера и первичных образований (аморфный или кристаллический полимер).
V. ОФОРМЛЕНИЕ ОТЧЕТА
Отчет по лабораторной работе включает:
1.Название, цель работы, краткое теоретическое обоснование.
2.Ход выполнения работы.
3.Рисунок (схему) лабораторной установки для нанесения покрытия в псевдокипящем слое полимера с кратким описанием принципа действия установки.
4.Протокол испытаний полимерного покрытия. Все графы протокола должны быть заполнены, результаты испытаний дать в системе СИ.
5.Графики зависимости: I) время напыления, с - толщина покрытия, мм;
2)толщина покрытия, мм - прочность покрытия на удар, Н•м.
6.Зарисовки микроструктур покрытия после различных режимов охлаждения с указанием вида надмолекулярной структуры полимера.
7.Вывод о влиянии режима охлаждения покрытия, толщины покрытия на микроструктуру и свойства покрытия.
VI. ТЕХНИКА БЕЗОПАСНОСТИ
I. При нагреве образцов в муфельной печи дверцу печи открывать аккуратно, образцы брать только пассатижами или щипцами (температура образцов выше 300°С!).
210
2.Не допускать перегрева образцов при оплавлении покрытия, так как при длительном нагреве происходит частичная деструкция (разложение) полимера с выделением токсичных низкомолекулярных продуктов (цвет оплавленного покрытия не должен быть желтым).
3.Оплавление покрытия проводить только при включении приточновытяжной вентиляции.
4.При испытании покрытий на электроискровой пробой после включения прибора ЭД-5 в электросеть не касаться зажима "крокодил" и щетки щупа руками (напряжение на щупе до 10 кВ.)
5.При работе на микроскопах не трогать оптику руками.
VII.ВОПРОСЫ ДЛЯ САМОПРОВЕРКИ
1.Для какой цели наносятся полимерные покрытия?
2.В чем преимущества порошковых "красок" перед лакокрасочными покрытиями?
3.Каковы недостатки покрытий, полученных на основе порошкообразных полимеров?
4.Какова га технология подготовки порошковых полимеров перед нанесением покрытия?
5.Какие факторы влияют на качество формируемого покрытия?
6.Какие существуют методы нанесения порошковых "красок"?
7.В чем преимущество модернизированных методов нанесения покрытий
сприменением электрического поля?
8.Какие термопласты применяются для нанесения покрытий?
9.Какие термореактивные полимеры применяются для порошковых "кра-
сок"?
10.Какие компоненты вводят в состав порошковых композиций для напыления покрытий и для какой цели?
11.Какими свойствами характеризуются покрытия на основе аморфных полимеров?
12.Какие свойства покрытий возрастают с повышением степени кристалличности полимера?
13.Какие факторы влияют на толщину покрытия?
14.От чего зависит величина зерна надмолекулярных образований полимера (величина сферолитов)?
15.Какие факторы влияют на тип первичной структуры при кристаллизации полимеров?
16.От чего зависят внутренние напряжения покрытий?
17.Как оценивается качество нанесенных покрытий?
18.Какие существуют методы испытаний покрытий?
211
ЛАБОРАТОРНАЯ РАБОТА № 19 ИЗУЧЕНИЯ МАКРОСТРУКТУРЫ И МИКРОСТРУКТУРЫ ПОЛИМЕРОВ
I. ЦЕЛЬ РАБОТЫ: изучить виды макроструктур и макродефектов пластических масс; ознакомиться с различными морфологическими образованиями надмолекулярных структур полимеров.
II. КРАТКИЕ ТЕОРЕТИЧЕСКИЕ СВЕДЕНИЯ
Пластические массы - композиционные материалы, в которых основным компонентом (матрицей) является связующее - полимер, а другими составляющими: наполнители, отвердители, пластификаторы и т.д.
Меняя состав пластмасс можло изменять механические, физические и другие свойства материала в широком диапазоне.
МАКРОСТРУКТУРА ПЛАСТМАСС
Перед выполнением работы необходимо ознакомиться с краткими теоретическими сведениями по макроанализу (лабораторная работа №1).
Композиционные материалы классифицируют по основным признакам типу матрицы, виду армирующего элемента, особенности макростроения.
По типу материала матрицы различают: композиты на основе термопластов (полиамиды, полиолефины, фторопласты и др.), на основе реактопластов (смолы полиэфирные, эпоксидные, фенолформальдегидные и др.).
Матрица придает изделию из пластмасс заданную форму и монолитность, обеспечивая передачу и перераспределение нагрузки по объему материала, защищает армирующие элементы от внешних воздействий. Тип; матрицы непосредственно определяет термическую и коррозионную стойкость, электрические и теплозащитные свойства, технологию изготовления и другие важнейшие характеристики пластмасс и изделий из них.
По виду армирующих элементов (наполнителей композиты (пластмассы; классифицируют в зависимости от геометрических размеров и порядка их расположения в матрице, целей армирования. Армирующие элементы (наполнители) вводят в композиционные материалы с целью изменения из свойств: увеличения прочности, жесткости и пластичности; изменения плотности, электрических, теплофизических и других характеристик в различных направлениях и отдельных местах изделия. Важнейшими являются деформационно-прочнос- тные характеристики конструкционных материалов. По этому признаку для удобства дальнейшего рассмотрения целесообразно различать собственно наполнители и армирующие элементы. Наполнители - это преимущественно дисперсные и коротковолокнистые вещества, введение которых позволяет достичь не более чем 1,5-2-кратного повышения прочности матрицы. Армирующие элементы (арматура) - высокопрочные усы, волокна, ткани, которые при соответствующем содержании в композиции способствуют повышению прочности
212

материала в 2-10 и более раз по сравнению с прочностью матрицы. В композиционном материале могут находиться и наполнители и армирующие элементы.
Простейшие случаи хаотического (а-г, и), одноосно- (д-з) и сложноориентированного (к-м) расположения армирующих элементов и наполнителей в матрице композиционного материала
а - порошки, б - коротких волокон, в - чешуек, г - смеси порошка с короткими волокнами, д - коротких волокон, е - длинных волокон, ж - тканей или фольг, и - длинных волокон
рис. 19.I
Композиты могут содержать армирующие и наполняющие компоненты различных размерностей.
К нульмерным наполнителям относят дисперсные (преимущественно порошковые) наполнители (сажа, песок, мелкодисперсные металлы, фосфаты, стеклянные и кремнеземные микросферы и т.д.); к одномерным - волокнистые наполнители и армирующие элементы: природные коротковолокнистые (асбест), растительные (сизаль, джут), высокомодульные нитевидные кристаллы (оксид и нитрид алюминия, оксид бериллия, карбид бора, нитрид кремния); длинномерные стеклянные, углеродные, базальтовые, борные, керамические,
213
низко- и высокомодульные органические волокна. К двухмерным относятся ленточные, тканевые (состоящие из любых видов волокон и их сочетаний), сеточные и другие армирующие элементы.
По макростроению композиционные материалы различают в соответствии с геометрическими параметрами относительного расположения компонентов. В матрице армирующие элементы могут быть расположены хаотично, но чаще их стараются разместить в определенном порядке (рис.19.I ). Возможности количественного сочетания и объемного расположения нульмерных, одномерных и двухмерных армирующих элементов весьма широки.
Композиционные материалы, имеющие одинаковые свойства во всех направлениях, называют изотропными. К ним относят хаотически наполненные порошками, короткими волокнами и чешуйками композиты. Материалы, свойства которых неодинаковы по различным направлениям, называют анизотропными. Это композиты с армирующими элементами в виде непрерывных волокон, пластин, тканей, сеток.
Порошковые пластики содержат дисперсные наполнители в твердой фазе.
Вэту группу входят:
-конструкционные (общетехнические) пластики - с матрицей из термопластов, содержащей твердые дисперсные наполнители преимущественно неметаллической природы. Из них изготавливают слабо- и средненагруженные зубчатые колеса, подшипники, корпуса и т.п.;
-металлонаполненные пластики, содержащие в качестве наполнителя металлические порошки. Металлонаполненные пластики имеют более высокие, чем исходные полимеры характеристики прочности, термостойкости и теплопроводности. Электрическая проводимость металлонаполненных пластиков зависит от природы металла, степени наполнения, адгезии матрицы к частицам металла. Железо и никель придают материалам ферромагнетизм; алюминий, медь и др. - низкую газо - и паропроницаемость; свинец, кадмий, вольфрам - свойство поглощать излучения высоких энергий и т.д. Металлонаполненные пластики применяют при изготовлении электрических контактов, уплотнителей, экранов для защиты от электромагнитных волн и ионизирующих излучений, элементов радио- и электротехники и др.
Волокниты - пресс-материалы, состоящие из рубленного волокна, пропитанного термореактивной смолой. Волокниты, содержащие хлопковое или химическое волокно, называют органоволокнитами, углеродное - карбоволокнитами и т.д. Из волокнитов изготавливают детали с высоким сопротивлением ударным нагрузкам: корпуса и крынки аппаратов, шестерни, строительные панели и др.
214

СЛОИСТЫЕ АРМИРУЮЩИЕ ПЛАСТИКИ
ГЕТИНАКС - слоистый пластик на основе бумаги, пропитанной термореактивной смолой (фенолформальдегидная, эпоксидно-фенольная и др. Применяется в производстве трансформаторов, радиоаппаратура и т.п.
ТЕКСТОЛИТЫ (рис. 19.2.) - материалы, состоящие из слоев ткани, пропитанной термореактивной смолой. Различают текстолиты на основе хлопчатобумажной ткани, стеклотекстолиты (стеклоткань), асботекстолиты (асбестовая ткань) и т.д. Из текстолитов изготовляют электротехнические изделия, вкладыши подшипников; из стеклотекстолитов – корпуса судов и т.д.; асботекстолиты для теплозащиты ракет и как фрикционные материалы.
Структура стеклопластиков
а - микроструктура стеклотекстолита (5x1), видны извилистые пинии слоев стеклоткани; б - макроструктура стекловолокнита типа "фанера"; в - макроструктура стекловолокнита неориентированного; г - микроструктура стеклопластика, видно сечение волокон и связующее
Рис. 19.2
Древесно-слоистые пластики - материалы, получаемые "горячим" прессованием тонких листов древесины - шпона, пропитанного термореактивными смолами. Древесно-слоистые пластики применяют в качестве конструкционного и антифрикционного материала в авиа- и судостроении, в электротехнике и др.
215
Газонаполненные пластмассы - гетерогенные дисперсные системы, состоящие из твердой и газообразной фазы. В зависимости от физической структуры (строения ячеек) это: - пенопласты (ячейки изолированы друг от друга);
-поропласты (губчатые материалы) с открыто-пористой структурой;
-сотопласты изготовляют из тонких листовых гофрированных материалов, с последующим склеиванием листов гофра в виде пчелиных сот.
Для улучшения мехнических и других свойств для пластмасс часто применяют металлическую и другую арматуру (шестерни, зубчатые колеса и т.д.).
ИЗУЧЕНИЕ МИКРОСТРУКТУРЫ ПОЛИМЕРОВ
Полимеры, подобно низкомолекулярным веществам, в зависимости от строения молекул и температурных условий могут находиться в кристаллическом и аморфном состояниях. Многие из них (целлюлоза и др.) существуют только в аморфном состоянии и по ряду причин неспособны кристаллизоваться, но большую группу составляют кристаллизующиеся полимеры, для которых, как и для низкомолекулярных веществ, характерно образование кристаллической решетки, в углах которой расположены идентичные группы атомов цепных макромолекул.
Для осуществления кристаллизации в полимерах необходимо соблюдение некоторых условий:
1.Молекулы полимера должны быть построены регулярно, т.е. обладать линейным строением: цепи с определенным чередованием звеньев и однотипным их расположением в пространстве.
2.Осуществление принципа плотной упаковки. Коэффициент упаковки у большинства закристаллизованных полимеров равен 0,62-0,67.
3.Молекулы полимера должны обладать определенной подвижностью, чтобы цели могли перемещаться и укладываться в кристаллическую решетку
(область температур Тс – Тпл).
Физико-механические свойства полимеров в значительной мере зависят от степени кристалличности, т.е. от структурной упорядоченности его молекул,
атакже от морфологических форм кристаллических образований. Степень кристалличности полимера может колебаться от 20 до 80%. Поэтому проблемы переработки и эксплуатации полимерных материалов в изделия, возможность получения полимерных материалов с заранее заданными свойствами тесно связаны с изучением их структуры.
В зависимости от условий кристаллизации (температуры кристаллизации, режима охлаждения, молекулярного веса, степени регулярности молекулярных цепей и др.) даже в пределах одного и того же полимера может быть реализовано большое разнообразие морфологических структур,
216
напоминающих ледяные узоры кристаллов воды.
Кристаллизация полимера может остановиться на любой из стадий. Наиболее часто встречаются три основных типа надмолекулярных структурнх образований (рис. 19.3 ):
1)фибрилярные (нитевидные) кристаллы;
2)сферолитные кристаллы (сферолиты): а) радиальные, б) кольцевые.
3)монокристаллы.
Самой типичной и самой распространенной формой кристаллов является сферолитная.
Кольцевые сферолиты легко образуются в полимере при длительном отжиге и характеризуются высокой упорядоченностью молекулярных цепей. Размер сферолитов может достигать от нескольких микрон до нескольких сот микрон, поэтому они легко просматриваются в обычных поляризационных микроскопах (МИН-8) или в металлографических микроскопах (МИМ-7).
Область науки о структуре полимеров, устанавливающая морфологию надмолекулярных образований и их взаимодействия с физико-химическими свойствами называется ПОЛИМЕРОГРАФИЕЙ.
Сферолиты - это специфические агрегаты кристаллов, обладающие центром и радиальной или кольцевой ориентацией кристаллов относительно центра. Строение и структура сферолитов полимеров и низкомолекулярных веществ аналогичны.
Термин сферолит заимствован из минералогии и кристаллографии по чисто формальной аналогии со сферолитами многих низкомолекулярных веществ.
Сферолиты исследуют в поляризационных микроскопах.
Вполяризованном свете сферолиты радиального типа в скрещенных николях дают темный крест (напоминающий мальтийский крест), ветви которого расширяются от центра к периферии.
Сферолиты кольцевого типа состоят также из фибрилл, расходящихся из единого центра. В поляризованном свете такие сферолиты помимо мальтийского креста дают систему концентрических колец, расположенных на равных расстояниях. Один и тот же полимер в зависимости от условий кристаллизации может давать сферолиты различного типа. Сферолиты наблюдаются у различных полимеров (полипропилен, полиэтилен, полиамиды и др.) на образцах в виде тонких пленок (20-40 мкм) - в проходящем свете на поляризационном микроскопе или на образцах, срезанных с блоков полимерного материала в отраженном свете на металлографическом микроскопе.
Ваморфном полимере надмолекулярные структуры не детерминованы
(не выявлены).
217

Виды надмолекулярных структур кристаллических полимеров
218

3
I - фибриллярные (нитевидные) кристаллы;
2 - сферолитные кристаллы: а- радиальные; б - кольцевые; 3 - монокристаллы
Рис. 19.3
При помощи полимерографии можно в общих чертах заранее предсказать механические и другие свойства полимеров.
III. ОБОРУДОВАНИЕ, ПРИБОРЫ, МАТЕРИАЛЫ
I. Трубчатые печи дли кристаллизации полимеров; баллон с азотом; микроскопы МИН-8; МИМ-7.
2.ЛАТРы; потенциометр электронный; термопары; термометры ртутные; покровные стекла.
3.Порошок полипропилена; образцы из полиамида; шлифовальная бумага; реактивы для травления.
IV. МЕТОДИЧЕСКИЕ УКАЗАНИЯ ПО ВЫПОЛНЕНИЮ РАБОТЫ
I. Изучить различные виды образцов, деталей из пластмасс, определив вид наполнителя (армирующего материала); объяснить влияние наполнителя на свойства пластмасс.
II. Изучить виды надмолекулярных структур полимеров. Задание I.
Изучить различные типы сферолитов на образцах в виде тонких пленок (толщиной 30-40 мкм) изотактического полипропилена (ТПЛ=165°С).
Прежде чем приступать к исследованию структуры полимеров на микроскопах, необходимо ознакомиться с их устройством.
219
ПРИНЦИП РАБОТУ ПОЛЯРИЗАЦИОННОГО МИКРОСКОПА
Для получения поляризованного света в микроскопе используют призмы Николя или поляроиды. В основу конструкции призм положено свойство лучей поляризоваться при прохождении через кристаллы. Но так как луч света, попавший в кристалл, распадается на два луча поляризованных в двух взаимно перпендикулярных направлениях, то для того, чтобы иметь свет, поляризованный в одной плоскости, надо освободиться от одного из лучей. Это достигается тем, что лучи на своем пути встречают расположенную под определенным углом пластинку с показателем преломления, подобранным таким образом, что для одного из лучей осуществляется полное внутреннее отражение.
Этот луч отклоняется и поглощается оправкой Николя.
Оптическая схема микроскопа включает два Николя (две призмы), расположенных один над другим. Если расположить их так, чтобы оба они пропускали лучи с колебаниями в одной и той же плоскости, поле зрения будет освещено так же, как в случае прохождения света через один Николь. Такое положение Николей носит название параллельного, если же повернуть один из Николей на 90º, то поле зрения окажется затемненным. Такое положение Николей называется СКРЕЩЕННЫМ.
На поляризационном микроскопе можно работать в параллельном или скрещенном положении Николей.
Для обнаружения сферолитов пользуются скрещенным положением Николей.
Основными частями поляризационного микроскопа МИН-8 (рис.19.4.) являются: станина (I), к которой при помощи шарнира присоединена рукояткавинт (18), предназначенная для вертикального перемещения тубуса. Тубус включает в себя следующие части микроскопа (2,3,4,5,6,12,13), предметный столик (8), и расположенный под ним поляризатор (10), осветительное устройство (11) и др. части микроскопа.
Фокусировка осуществляется с помощью рукоятки-винта (18). Винт (16) служит для тонкой фокусировки. В верхнюю часть тубуса вставляется окуляр
(2). На нижней части тубуса с помощью щипцов (6) укрепляется объектив (13). Различные комбинации окуляров и объективов дают увеличения от х15 до х1020. Для определения степени увеличения нужно перемножить числа, указанные на объективе и окуляре. В нижней части тубуса располагается верхний Николь - анализатор (4). Осветительная часть микроскопа состоит из зеркальца (11), нижнего Николя - поляризатора (10), снабженного ирисовой диафрагмой и линзы ЛАЗО. Свет от лампы, отраженный зеркальцем, освещает препарат.
220

Схема поляризационного микроскопа МИН-8
Рис.19.4
221
Поляризатор с помощью рукоятки (12) может вращаться вокруг оси микроскопа. Линза Лазо вводится над поляризатором с помощью поворота ручки (18); линза Лазо нужна для получения сильно сходящегося пучка света.
Объективный столик может вращаться в своей плоскости. Закрепление столика в нужном положении осуществляется с помощью винта (7). Образец материала кладется на середину столика и зажимается двумя пружинамилапками.
УСТАНОВКА ДЛЯ ПРОВЕДЕНИЯ ПРОЦЕССА КРИСТАЛЛИЗАЦИИ ПОЛИМЕРОВ В ПЛЕНКАХ (рис. 19.5 )
Установка состоит из следующих основных частей: двух трубчатых печей (2), (3) с крышками из фторопласта (4), штативов (5), ЛАТРов (7), питающих печи термопар (9), термометров электрических (10) и ртутных (8), баллона с азотом (11), покровных стекол (1),
Порядок проведения эксперимента на установке Полимер в виде порошка помещается между предметным и покровным
стеклами (1) и нагревается в специальной трубчатой печи (2) в инертной среде (азот) в течение 10-15 мин при температуре 220°С (выше ТТ).
Через 7-8 мин после начала нагрева, не вынимая образца из печи, надавливают на покровное стекло для получения пленки надлежащей толщины. Через 15 мин снижают температуру печи, задавая температуру, при которой проводят изотермическую кристаллизацию образца.
Таким способом готовят пленки полипропилена при одной из указанных ниже температур кристаллизации: 100 , 120, 130 ;134 , 138°С, устанавливая время кристаллизации от 60 до 120 мин.
Задание 2.
Изучить структуру полимеров в блоке (полиамиды).
I. На образце полимерного материала (капрон, капролон) делается срез и выбранный участок подвергается полированию до получения гладкой поверхности. Шлифование производится вручную (как при приготовлении микрошлифов металлов), не допуская нагревания образца. Затем образец подвергают полированию также вручную на толстом сукне
222

223
(всухую) до появления блеска на поверхности.
Для выявления надмолекулярной структуры проводят травление. В качестве реактива применяется 6%-ный водный раствор фенола. Время травления зависит от структуры и указывается преподавателем (обычно 25-30 мин ).
Травление проводят на различных участках отличающихся временем травления с разницей в 5 мин (5, 10,15, 20, 25, 30).
По истечении необходимого времени травления растворенная часть полимера смывается струей воды в течение 3-4 мин. Лучшее удаление влаги и растворителя достигается при вакуумной сушке при комнатной температуре в течение 40-45 мин. Удалив осторожно влагу фильтровальной бумагой, образцы устанавливаются на металлографический микроскоп МИМ-7 и исследуются при увеличении х500. Полученную структуру зарисовать в тетрадь и определить морфологический тип.
2. Для получения хрупких изломов образцы полимерных материалов надрезают лезвием бритвы и подвергают изгибу до хрупкого излома или разрушают ударом тяжелого предмета. Хрупкий излом образцов можно получить, выдержав их в сосуде Дюара с жидким азотом в течение 35-40 мин. После извлечения образцов из жидкого азота их разрушают ударом по поверхности. Полученную поверхность после излома исследуют на микроскопе МИМ-7.
V. СОДЕРЖАНИЕ ОТЧЕТА
Отчет по лабораторной работе включает:
1.Название, цель работы.
2.Краткие теоретические сведения.
3.Рисунки макроструктур и макродефектов деталей и образцов пластмасс (для пластмасс с различными видами наполнителей выписать из литературы механические свойства).
4.Методику изучения надмолекулярных структур полимеров.
5.Схему установки для кристаллизации полимеров.
6.Краткую характеристику исследуемых полимеров и рисунки надмолекулярных структур.
7.Выводы.
VI. ВОПРОСЫ ДДЯ САМОПРОВЕРКИ
1.Какие материалы называются пластмассами?
2.Что такое макроанализ и макроструктура?
3.Что можно изучить с помощью макроанализа?
4.Какие существуют виды макроструктур (по виду наполнителя)?
224
5.В чем отличие по свойствам, виду наполнителя ориентированных и неориентированных стекловолокнитов?
6.Какие виды наполнителей применяют для слоистых пластиков? Как называются эти материалы?
7.Для какой цели в пластмассах применяется металлическая арматура?
8.Какие существуют виды газонаполненные пластмасс (по структуре)?
9.Виды надмолекулярных структур кристаллических полимеров.
10.Условия, необходимые для кристаллизации полимеров?
11.Методика кристаллизации полипропилена.
12.Как готовятся микрошлифы полимеров для изучения на металлографических микроскопах?
225
ЛАБОРАТОРНАЯ РАБОТА № 20 ГАЗОНАПОЛНЕННЫЕ ПЛАСТМАССЫ
I. ЦЕЛЬ РАБОТЫ: изучить различные виды легковесных пластиков, их свойства; ознакомиться с технологией получения и испытания пенопластов.
II. КРАТКИЕ ТЕОРЕТИЧЕСКИЕ СВЕДЕНИЯ
Газонаполненные пластики получили широкое распространение в различных отраслях промышленности.
Газонаполненными называют пластмассы, представляющие собой гетерогенные дисперсные системы, состоящие из твердой и газообразной фаз. В качестве связующего, образующего стенки ячеек или пор, используются термопластичные (полистирол, поливинилхлорид, полиэтилен) или термореактивные (эпоксидные, фенолформальдегидные смолы, полиуретаны) полимеры; наполнителем является газовая фаза (углекислый газ, азот, воздух).
По физической структуре (строению) газонаполненные пластмассы делят на : пенопласты, поропласты и сотопласты.
1. Пенопласты - материалы с изолированными ячейками, содержащими газ и разделенными друг от друга и от окружающей среды тонкими стенками полимерного связующего. Структура этих материалов напоминает как бы затвердевшую пену. Объемная плотность пенопластов колеблется от 20 до 300 кг/м3.
2. Поропласты (губчатые материалы) – полимер образует систему с от- крыто-пористой структурой (сообщающихся ячеек или полостей, заполненных газом). Кажущаяся плотность поропластов изменяется от 25-60 до 130-500 кг/м3.
3. Сотопласты изготавливают из тонких листовых материалов (ткани, пропитанные различными связующими), которым придается вид гофра, а затем листы гофра склеивают в виде сот.
ПЕНОПОЛИСТИРОЛ. Его получают прессовым (ПС-I, ПC-4) и беспрессовым (ПСВ, ПСВ-С) методом. Пенополистиролы могут работать от -60 до +6075°С; применяются для наплавов, поплавков; как тепло- и звукоизоляционный материал; из-за хороших амортизационных свойств и малой плотности - в качестве упаковочного материала. Пенополистирол устойчив в биологическом отношении – не гниет, стоек к действию грибков, бактерий.
Прочность ПС зависит от размера, формы и прочности стенок пор. Механические свойства беспрессового пенополистирола ниже, чем прессового.
226
ПЕНОПОЛИВИНИЛХЛОРИДЫ. Они во многом сходны с пенополистиролами. Пенополивинилхлориды могут быть жесткими, полужесткими и эластичными. Применяются в радиосвязи и радиолокации, на транспорте и т.д.
ПЕНОПОЛИУРЕТАНЫ. Получаются самовспениванием (процесс идет при температуре). Пенополиуретаны (ППУ) делят на две группы:
1) эластичные пенопласты (поролон);
2)жесткие пенопласты.
Объемная плотность поролона изменяется от 25 до 59 кг/м3. Разрушающее напряжение составляет 35-20 МПа, относительное удлинение находится в приделах 400-350%. Эластичные ППУ являются хорошими тело- и звукоизоляторами, а также амортизирующими материалами. Они могут склеиваться с деревом, бумагой, тканью. В качестве теплоизоляции они могут работать как при низких температурах (жидкий азот), так и при повышенных (до 120°С) температурах.
Жесткие пенополиуретаны получают либо методом заливки, либо путем напыления на поверхность каких-либо материалов. Жесткие ППУ имеют большую объемную плотность от 60 до 220 кг/м3, разрушающее напряжение при сжвтии от 20 до 250 МПа, а верхний рабочий пределдо 100-170ºС. Жесткие ППУ обладают высокими электроизоляционными, теплоизоляционным свойствами, хорошей вибростойкостью, адгезией к металлу, дереву, тканям. Их применяют для изготовления трехслойных и многослойных конструкций, в судостроении; для заполнения зазоров в железобетонных конструкциях, внутренней полости кухтылей; в холодильной промышленности
ГАЗОНАПОЛНЕННЫЕ ФЕНОПЛАСТЫ Газонаполненные пластмассы на основе фенолформальдегидных смол
(ФФ) делят на ячеистые и сотовые. Объемная плотность ФФ меняется от 30 до 200 кг/м3. Недостатком их является низкая ударная вязкость. Для снижения хрупкости их модифицируют каучуком (ФК-20) или стекловолокном (ФС). Фенопенопласты применяют в радиотехнике, судостроении, строительстве при работе до температур 120-160°С.
ПЕНОПОЛИЭПОКСИДЫ (ПЭ), как и пенополиуретаны являются самовспенивающимися материалами. Они отличаются химической стойкостью, высокими электроизоляционными свойствами, низким водопоглощением. Их широко используют для заливки деталей электронной аппаратуры.
III. ОБОРУДОВАНИЕ, ПРИБОРЫ, МАТЕРИАЛЫ
1.Пресс малый гидравлический, баня водяная, лабораторная мешалка, форма для вспенивания.
2.Штангенциркуль, весы электрические.
3.Полистирол гранулированный, глицерин, смола резольная ФРВ, вспенивающий агент ВАГ.
227
IV. МЕТОДИЧЕСКИЕ УКАЗАНИЯ ПО ВЫПОЛНЕНИЮ РАБОТЫ
1.Ознакомиться с техникой безопасности.
2.По указанию преподавателя получить пенопласт одним или двумя нижеописанными способами.
ПОЛУЧЕНИЕ ПЕНОПЛАСТА ПСБ БЕСПРЕССОВЫМ МЕТОДОМ
1.Отвесить навеску гранулированного полистирола - 10 г (гранулы на-
сыщены низкокипящей жидкостью - изопентана.
2.Навеску полистирола поместить в специальный ковш, который опустить в водяную баню с кипящей водой и выдержать при температуре 97-99°С в течение 1-3 мин.
3.Вспененные гранулы отделить одна от другой стеклянной палочкой.
4.Дюралюминовую форму (размером 5x5x9) смазать глицерином.
5.Вспененные гранулы загрузить в форму и опустить ее в кипящую воду на 25 мин, время от времени переворачивая в водяной бане.
6.Форму вынуть из воды, охладить, открыть и вынуть образец.
7.Образец высушить при комнатной температуре в течение 12 ч. ПОЛУЧЕНИЕПЕНОПЛАСТАМАРКИФРП-I,ФРП-2САМОВСПЕНИВАНИЕМ Пенопласт применяется в качестве теплоизоляционного материала и в
трехслойных конструкциях как заполнитель. Недостаток его состоит в том, что при соприкосновении с металлическими поверхностями вызывает их коррозию, так как содержит кислоты.
|
|
Рецепты пенопластов марки ФРП-I и ФРП-2 |
Таблица 20.1 |
||
|
|
|
|
||
Номер |
|
|
Рецептура в весовых |
||
рецеп- |
|
Наименование компонентов |
частях |
||
та |
|
|
ФРП -1 |
|
ФРП-2 |
I |
1. |
Смола резольная ФРВ-1 |
100 |
|
- |
2. |
Вспенивающий агент ВАГ-1 |
20 |
|
- |
|
|
|
||||
2 |
1. |
Смола резольная ФРВ-2 |
- |
|
100 |
2. |
Вспенивающий агент ВАГ-2 |
- |
|
20 |
|
|
|
Примечание. Дозировка указана для объемной плотности 30-40 кг/м3 для ФРП-I и 60-70 кг/м3 для ФРП-2. При получении пенопластов более высокой объемной плотности (до150 кг/м3) количество вспенивающего агента снижается до
13-16%.
Техника безопасности при работе с резольными смолами должна соблюдаться особенно строго. Резольные смолы попадая на кожу, могут вызвать раздражение и слабые ожоги, так как в этих смолах содержится свободный фенол. Вспенивающие агенты имеют в своем составе концентрированные кислоты; ра-
228

бота с ними проводится только в резиновых перчатках. При попадании вспенивающих агентов на кожу следует быстро вымыть пораженное место водой.
Вспенивание композиции надо проводить под тягой.
Получение пенопластов марок ФРП сводится к механическому смешиванию (вручную или с помощью мешалки) при комнатной температуре соответствующих количеств резольных смол (20г) и вспенивающих агентов (4г):
1.Отвесить 20 г резольной смолы и 4 г вспенивающего агента.
2.Включить форму разделительным составом, высушить состав.
3.Включить мешалку и быстро вылить вспенивающий агент в резольную смолу, перемешивать в течение 30-60 с.
4.Композицию вылить в подогретую форму.
5.Через 5-10 мин полученный жесткий пенопласт вынуть из формы выдержать при комнатной температуре 10-20 ч.
ПРОВЕСТИ ИСПЫТАНИЯ ПОЛУЧЕННЫХ ПЕНОПЛАСТОВ
а) определить объемную плотность пенопласта. Взвесить полученный образец на электрических весах, замерить его объем.
где m |
- масса образца пенопласта, кг; |
V |
- объем пенопласта, м3, |
б) определить прочность образца на сжатие на ручном гидропрессе. По достижении 10%-ной линейной деформации (уменьшение высоты образца под нагрузкой на 1/10 часть) замерить показания манометра (р):
где P - нагрузка, кГс;
F - начальная площадь поперечного сечения образца, см2 р - показания манометра, кГс/см2;
S - площадь поршня, 26,4 см2.
Зарисовать макроструктуру пенопласта.
229
V. СОДЕРЖАНИЕ ОТЧЕТА
1.Дать краткие теоретические сведения.
2.Описать технологию изготовления пенопласта.
3.Привести результаты испытаний пенопласта (в системе СИ).
4.Зарисовать макроструктуру пенопласта с разносом составляющих материала.
VI. ВОПРОСЫ ДЛЯ САМОПРОВЕРКИ
1.Какие материалы называются газонаполненными пластмассами?
2.Какие полимеры применяются в качестве связующего?
3.На какие группы делятся по структуре газонаполненные пластмассы?
4.Какими особыми свойствами обладают легковесные пластики?
5.Какие существуют методы получения газонаполненных пластмасс?
6.Какие пенопласты получают на основе термопластичных полимеров? Их свойства, области применения.
7.Какие легковесные пластики получают на основе термореактивных полимеров? Особенности их свойств, области применения.
8.В чем особенности метода самовспенивания? Какие газонаполненные пластмассы получают этим методом?
230
ЛАБОРАТОРНАЯ РАБОТА № 21 ИЗУЧЕНИЕ СТРУКТУРЫ И ФИЗИКО-МЕХАНИЧЕСКИХ СВОЙСТВ
КЕРАМИЧЕСКИХ МАТЕРИАЛОВ I. ЦЕЛЬ РАБОТЫ:
ознакомление с новыми керамическими материалами - конструкционной керамикой общемашиностроительного и специального приборного назначения, а также получить представление о керамике для режущих инструментов. На базе сравнительных измерений свойств и изучения структуры определить тип керамики, изучить состав и технологические особенности изготовления керамических заготовок и деталей из керамики.
II. ОСНОВНЫЕ ТЕОРЕТИЧЕСКИЕ СВЕДЕНИЯ
Керамические материалы как неорганические вещества, проведшие высокотемпературное спекание, обладают высокой твердостью, прочностью при сжатии, изгибе, практически не деформируются, имеют ряд специальных характеристик - термостойкость, вакуумную плотность, стабильные диэлектрические характеристики, что позволяет применять их в современном машиностроении, приборостроении, автомобилестроении. В клеено-сборных и паяных конструкциях керамика надежно работает в узлах автомобилей, авиационных и космических двигателях.
Диапазон рабочих температур различных видов конструкционной керамики достигает в настоящее время 1000-1100°С.
Керамические материалы, как правило, стойки к воздействию излучений высоких энергий - радиационностойки, устойчивы к воздействию влажных и агрессивных сред, а также грибков и органических растворителей, что позволяет расширить диапазон их применения от бытовой техники до энергетики и ионно-плазменных источников технологического и специального назначения, в том числе в лазерной технологии.
В табл.21.1 приведены физико-механические свойства конструкционных керамик различного состава и назначения. На рис.21.1 и 21.2 приведен внешний вид деталей из термостойкой борнитридкремниевой керамики (разрядная камера технологического источника плазмы, полученной горячим прессованием в графитовых формах, а также из алюмооксидной вакуумплотной керамики (изоляторы токоподводов катода стационарного плазменного двигателя малой тяги, полученные шликерным литьем с последующим спеканием в вакууме и в водороде).
Исходными веществами для получения керамических заготовок и деталей являются дисперсные порошки двуокиси кремния, окиси алюминия, нитрида кремния, нитрида бора, модификаторами являются окись циркония, а также окись иттрия.
231
Для изготовления деталей и заготовок различной конфигурации в смесь порошков керамики вводят пластификаторы и связующие, которые позволяют вести прямое прессование в гранитовых и металлических формах, а так изготовлять детали шликерным литьем на литьевых машинах. При этом после сушки пластифицированных заготовок проводится предварительное спекание при температурах до 1000°С и спекание-обжиг при температурах 1800-2000°C в атмосфере водорода или в вакууме. Конструкционная керамика типа АБН (алюмонитридборная) и БГП (Борнитридкремниевая) изготовляется прямым прессованием при индукционном нагреве при 1750-2000°C в порошковых засыпках или в графитовых пресс-формах с предварительной обмазкой пастой нитрида бора.
Наиболее эффективно применение конструкционной керамики в паяных и клеено-сборных узлах в сочетании с металлическими корпусами, обечайками. При этом проектирование узлов ведется с учетом исходной пористости керамики, а также в согласованности коэффициентов линейного термического расширения соединяемых деталей. В качестве клеев используются огнеупорные клеи на основе алюмохромофосфатного связующего с наполнителями - окисью иттрия, окисью циркония, кварца, электрокорунда. Пайку керамики проводят в вакууме с применением медненой титановой фольги или медноникелевых припоев ВПР-2, ВПР-4. На рис. 21.3 и 21.4 приведены эскизы двух видов соединения керамической камеры ЭРДМТ (электрического реактивного двигателя мало тяги) склеиванием с титановой обечайкой и паяного пускового электрода в катоде технологического источника плазмы.
III.ОБОРУДОВАНИЕ, ПРИБОРЫ, МАТЕРИАЛЫ
1.Весы лабораторные РЛ, бинокулярным микроскоп МБС-2, МБС-9; металлографические микроскопы ММР-4, МИМ-7.
2.Твердосплавный переносный индентор прибора ТК, микропроцессорный твердомер МИТ-2.
3.Мегаомметры настольные трехпозиционные с электродами на базе 3-5мм из бериллиевой бронзы БрБ-2, накладные электроды цилиндрические из меди МО.
4.Плоские заготовки керамики ВК-94-1, БГП, микрошлифы металлизованной и неметаллизованной керамики ВК-94-1 (22XС), 3 образца режущей керамики.
IV.МЕТОДИЧЕСКИЕУКАЗАНИЯИОБЪЕМВЫПОЛНЯЕМОЙРАБОТЫ
1.Провести внешний осмотр, определить цветовое отличие керамик (белая алюмооксидная типа ЦМ-332; розовая беспористая-ВК-94-1; cepoвато-белая с точечными вкраплениями, талькоподобная БГП, темно-серая, ровная, литая Si3N4; черная, полированная - гексанит, силинит - Р).
2.Методом царапания твердосплавным наконечником определить относительную твердость по Моосу относительно твердого сплава 9,0.
232

Внешний вид деталей из конструкционной горячепрессованной и вакуумплотной литой керамики
Керамическая разрядная камера из керамики БГПтехнологический источник плазмы М-70
Рис. 21.1
Электроизоляторы из вакуумплотной керамики BK-94-I - для пайки токоподвода катодного элемента двигателя Рис.21.2
233

234
Основные термины к лабораторной работе.
КЕРАМИКА - камневидные материалы неорганического происхождения, получаемые спеканием пластифицированных порошков и шликеров, содержащих окислы, карбиды, нитриды, преимущественно кремния, алюминия, бора. Различают керамические материалы но степени уплотнения (пористости), по тонкости помола исходных материалов, по назначению (строительные, бытовые, технические керамические материалы).
КЕРАМИКА ВАКУУМНАЯ - материалы повышенной плотности - вакуумплотные с высокими механическими свойствами, низкими диэлектрическими потерями при различных частотах. Имеет согласованные с радиотехническими металлическими материалами коэффициенты линейного термического расширения, хорошо паяются в вакууме и защитной атмосфере. КОНСТРУКЦИОННАЯ КЕРАМИКА - материалы для изготовления деталей и конструкционных элементов в машиностроении, авиации, спецтехнике, приборостроении и высокотемпературном нагревательном оборудовании - электропечах и высокочастотных установках.
ИНСТРУМЕНТАЛЬНАЯ, РЕЖУЩАЯ КЕРАМИКА - твердые и сверхтвердые керамические плотные материалы для режущих инструментов, фильер, калибров бывает алюмооксидная, борнитридная и нитридкремнистая - гексаниты, силиниты и др.
ПЕТРОГРАФИЯ - наука о формировании структуры и свойств керамических материалов различных методов изготовления и химического состава, в зависимости от условий спекания, обжига.
ШЛИКЕР - керамическая масса, получаемая сырым перетиром микропорошков для изготовления деталей с введением технологической связки (парафина, олеиновой кислоты, спиртов). Керамические детали могут изготовляться методом шликерного литья или прессования в металлические формы. ЭЛЕКТРОКОРУНД - корунд. AI2O3,получаемый из природного корунда, сырье для изготовления вакуумплотной, конструкционной и режущей керамики. Применяется также для изготовления абразивных кругов и шлифбумаг; микропорошки используют для напыления металлических материалов.
ЭЛЬБОР - кристаллическая кубическая модификация нитрида бора BN, синтезируется в виде монокристаллов размером выше 400мкм. Существует также гексагональный нитрид бора, применяемый для изготовления весьма термостойкой борнитридкремнистой горячепрессованной керамики, в том числе для непрерывного литья в металлургии.
МЕТАЛЛИЗОВАННАЯ КЕРАМИКА - преимущественно вакуумплотная с нанесенным слоем металлической пасты на поверхностях, подлежащих пайке с металлическими деталями. Металлизация проводится вжиганием пасты в водороде или в вакууме.
235

Примеры конструкторско-технологического варианта использования керамики в приборостроении и спецтехнике
Клеено-сборная конструкция из керамики БГП в технологическом источнике плазмы с применением огнеупорного клея KM-4IM
Рис. 21.3
Паяное соединение керамики с двумя сплавами с согласованными К.Л.Т.Р. в конструкции катода
Рис. 21.4
236
3.Определить плотность керамики методои гидростатического взвешивания, измерить электросопротивление электродами на базе 3мм.
4.Определить под бинокулярным микроскопом при увеличении 7-12х наличие сколов, пор большого диаметра, трещин и неслитин.
5.Рассмотреть структуру керамики ВК-94-1; структуру металлизованного слоя; микроструктуру паяного соединения: керамика-металл через металлизованный слой.
6.Сравнить твердость твердого сплава ВК-6М и твердость керамики гексанит-
Р.
V.СОДЕРЖАИЕ ОТЧЕТА
1.Зарисовать (эскизировать) внешний вид одной из заготовок керамики.
2.Указать степень пористости и сравнить линейную (объемную) усадку спеченой шликерной керамики и пористой горячепрессованной, сопоставить плотности.
3.Зарисовать вид типового клееного и паяного соединения керамики с металлом, отметить характер литой зоны спая керамики, наблюдаемый под микроскопом.
VI. ВОПРОСЫ ДЛЯ САМОПРОВЕРКИ
1.B каких областях техники применяются керамические материалы?
2.Назвать классификацию керамик по пористости, зернистости и способу изготовления.
3.Каковы основные прочностные и эксплуатационные свойства керамик, отличающиеся от аналогичных у металлов и сплавов?
4.Привести примеры применения керамических материалов в бытовой технике, приборостроении, электротехнике.
5.Назвать наиболее надежные способы крепления керамики в конструкционных деталях.
6.Каковы преимущества режущей керамики в сравнении с металлическими порошковыми режущими пластинами и инструментами из них?
7.Каковы недостатки керамических материалов в сравнении с металлами и сплавами?
237
СПИСОК РЕКОМЕНДУЕМОЙ ЛИТЕРАТУРЫ
Основная
1.Арзамасов Б.Н., Сидорин H.H., Косолапов Г.Ф. и др. Материаловедение. -М.: Машиностроение, 1986. -384 с.
2.Конструкционные материалы: Справочник /Под ред. Б.Н. Арзамасова. - М.: Машиностроение, 1990. -687с.
3.Лахтин Ю.М., Леонтьева В.П. Материаловедение. -М.: Машинострое-
ние, 1990. -528с.
4.ТравинО.В., ТравинаН.Т. Материаловедение. -М.: Металлургия, 1989. -320с. Дополнительная
5.ГеллерЮ.А., РахштадА.Г. Материаловедение. -М.: Металлургия, 1989. - 456с.
6.Металловедение и термическая обработка стали: Справочное издание
/Под ред. М.Л. Берштейна, А.Г. Рахштада. -М.: Металлургия,1991.
7.Новиков И.И., Строганов Г.Б., Новиков А.И. Металловедение, термообработка и рентгенография. -М. : "МИСИС", 1994. -480с.
8.Ульянин Е.А. Коррозионностойкие стали и сплавы. -М.: Металлургия, 1991. -256с.
Нормативно-техническая документация I. Сталь
Углеродистая обыкновенного качества |
- ГОСТ 380-88 |
Углеродистая качественная |
- ГОСТ 1050-88 |
Легированные строительные |
- ГОСТ 19281-73 |
|
- ГОСТ 19282-73 |
Легированные цементуемые |
- ГОСТ 4543-71 |
Легированные улучшаемые |
- ГОСТ 4543-71 |
Легированная конструкционная, качественная, рес- |
|
сорно-пружинная |
- ГОСТ 14959-79 |
Подшипниковая |
- ГОСТ 801-78 |
Конструкционные повшенной и высокой обрабаты- |
|
ваемости резанием |
- ГОСТ 1414-75 |
Жаростойкие и жаропрочные |
- ГОСТ 5520-79 |
|
- ГОСТ 20072-74 |
Коррозионностойкие |
- ГОСТ 5632-72 |
- ГОСТ 5532-72 |
|
Стали для холодной штамповки |
- ГОСТ 9045-80 |
Сталь для отливок |
- ГОСТ 977-75 |
Поковки из конструкционной углеродистой и |
|
легированной стали |
- ГОСТ 8479-70 |
Отливки из высоколегированной стали со |
|
специальными свойствами |
- ГОСТ 2176-77 |
238 |
|
Отливки из хладостойкой и износостойкой стали |
- ГОСТ 21357-77 |
Проволока стальная углеродистая пружинная |
- ГОСТ 9389-75 |
2. Чугуны |
|
Серы |
- ГОСТ 1412-85 |
Ковкий |
- ГОСТ 1215-79 |
Высопрочный |
- ГОСТ 7293-85 |
Жаростойкий |
- ГОСТ 7769-82 |
Чугун с вермикулярным графитом |
- ГОСТ 28394-89 |
3. Медь и ее сплавы |
|
Медь |
- ГОСТ 859-78 |
Латунь двойная и многокомпонентная деформируемая |
- ГОСТ 15527-70 |
Латунь литейная |
- ГОСТ 17711-80 |
Бронза оловянистая деформируемая |
- ГОСТ 5017-74 |
Бронза безоловянистая деформируемая |
- ГОСТ 18175-78 |
Бронза оловянистая литейная |
- ГОСТ 613-79 |
Бронза безоловянистая литейная |
- ГОСТ 493-79 |
Медно-никелеевые сплавы |
- ГОСТ 492-73 |
4. Антифрикционные сплавы |
|
Алюминиевые |
- ГОСТ 14113-78 |
Цинковые |
- ГОСТ 21437-75 |
Баббиты на основе свинца, олова |
- ГОСТ 1320-74 |
Кальциевые баббиты |
- ГОСТ 1209-78 |
5. Алюминий и его сплавы |
|
Алюминий |
- ГОСТ 4784-74 |
Деформируемые сплавы, термически неупрочняемые |
- ГОСТ 4784-74 |
Деформируемые, термически упрочняемые сплавы |
- ГОСТ 4784-74 |
Литейные сплавы |
- ГОСТ 1583-89 |
6. Титан и его сплавы |
|
Титановая губка |
- ГОСТ 17746-79 |
Титановые сплавы |
- ГОСТ 19807-74 |
239