
12_100229_1_67139
.pdf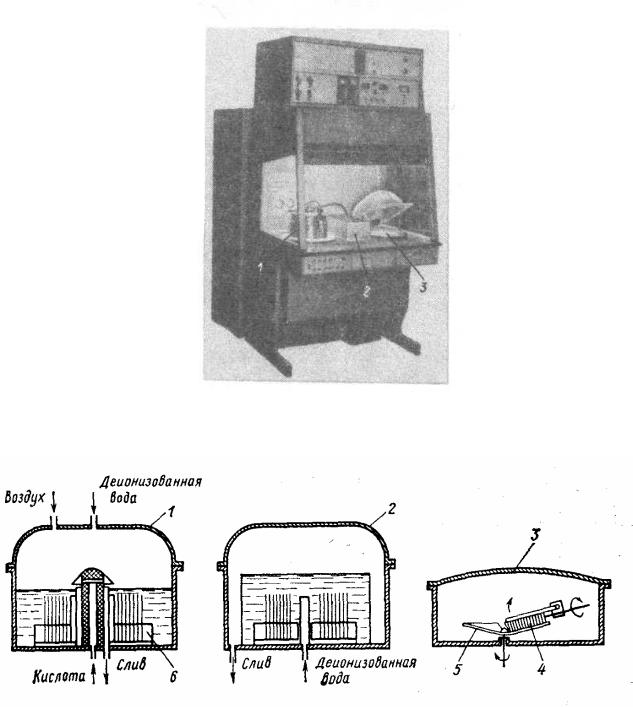
Рисунок 1.7- Установка для химического травления пластин типа ПВХО-ГК60-1:
Рисунок 1.8 - Схема рабочих органов установки ПВХО-ГК60-1
На рабочем столе в пылезащитной камере смонтированы три рабочих ванны 1—3. В ванне производится обработка кремниевых пластин погружением в холодные или горячие кислоты, или органические растворители. Крышка ванны в процессе обработки герметически закрыта. Обработка производится групповым методом в кассетах по 40—60 пластин в зависимости от их размеров. Из ванны кассеты 6 переносятся в ванну 2 для отмывки деионизованной водой. Степень отмывки контролируется прибором по разности сопротивления деионизованной воды на входе и выходе ванны. После этого в ванне 3 пластины по 10 шт. обрабатываются кистями 4 и сушатся на центрифуге 5.
11
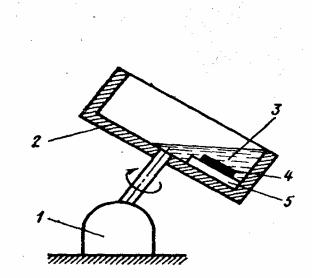
Химико-динамическое, или полирующее травление производится с помощью устройства, схема которого приведена на рис.1.9. Сущность его заключается в активном перемешивании травителя непосредственно у поверхности обрабатываемой пластины. Благодаря этому обеспечивается быстрое удаление продуктов реакции, равномерное поступление новых порций травителя, неизменность его состава и постоянство теплового режима обработки.
Во фторопластовый барабан 2, вращающийся на оси, наклоненной относительно нормали на угол 15—45°, заливают порцию травителя 3. Обрабатываемые пластины 4 наклеивают на фторопластовые диски 5, которые помещают на дно барабана пластинами вверх. Барабан приводится во вращение от электродвигателя через редуктор с частотой вращения 120 об/мин. При этом диски 5 перекатываются по его стенке, обеспечивая хорошее перемешивание травителя и создавая условия для равномерного травления.
Рисунок 1.9 - Схема установки полирующего травления.
Для полирования кремния применяют также электрохимическое полирование, в основе которого лежит анодное окисление полупроводника, сопровождаемое механическими воздействиями на окисную пленку. Принципиальная схема установки показана на рис. 66. Два дисковых электрода — анодный 2 и катодный 3 отделены друг от друга капроновой сеткой, натянутой с помощью кольца на катод 3. Сетка пропитана электролитом, постоянно подаваемым из бачка 1. Для изменения скорости протекания электролита угол отклонения катодного диска от вертикали может регулироваться от 0 до 20°. Электродвигатель 5 постоянного тока
12
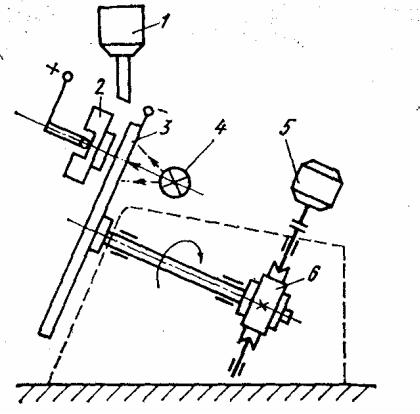
Рисунок 1.10 - Схема установки электрохимической полировки полупроводниковых пластин.
и редуктор 6 позволяют плавно изменять частоту вращения катодного диска 3 в пределах 80—200 об/мин. Катодный диск изготовлен из коррозионно-стойкой стали и имеет радиальные пазы, через которые пластины n-типа подсвечиваются мощной лампой 4 для генерации неосновных носителей (дырок), необходимых для протекания реакции. Анодный диск 2 с наклеенной на нем пластиной в процессе работы самоустанавливается по катодному диску. Данный метод обработки особенно эффективен при локальном травлении кремния.
Качество поверхности обработанных пластин определяется шероховатостью и глубиной нарушенного слоя. После резки, шлифовки и полировки пластины отмывают. Состояние поверхности пластин контролируют визуально или под микроскопом. При этом проверяют наличие на поверхности царапин, рисок, сколов, загрязнений и следов воздействия химически активных веществ.
Во всех установках контроль осуществляется оператором с использованием, например, микроскопов типов МБС-1, МБС-2 (с увеличением 88х) или МИМ-7 (с увеличением 1440х). Микроскоп МБС-1 благодаря специальному устройству осветителя позволяет наблюдать поверхность в лучах света, падающих под разными углами. На микроскопе МИМ-7 можно наблюдать поверхность в светлом и темном полях. Оба микроскопа позволяют измерять размеры повреждения поверхности специально установленными окулярами. В установках для визуального контроля пластин автоматизируется подача пластин из кассеты на
13
предметный столик под микроскоп и возвращение ее после контроля в соответствующую классификационную кассету. Иногда вместо оптического микроскопа применяют проекторы, позволяющие снизить утомляемость оператора.
Шероховатость поверхности в соответствии с ГОСТ 2789—73 оценивают средним арифметическим отклонением профиля Rа или высотой микронеровностей Rz. ГОСТ устанавливает 14 классов шероховатости поверхности. Для 6—12 классов шероховатости основной является шкала Rа, а для 1—5-го и 13—14-го — шкала Rz. Шероховатость измеряют в визуально определенном направлении, соответствующем наибольшим значениям Rа и Rz.
Для измерений используют стандартные профилографы-профилометры или с помощью сравнительного микроскопа поверхность обработанной пластины визуально сравнивают с эталоном. Современный профилографпрофилометр — универсальный высокочувствительный электромеханический ощупывающий прибор, предназначенный для измерения волнистости и шероховатости металлических и неметаллических поверхностей. Принцип действия прибора состоит в том, что колебательные движения ощупывающей иглы с радиусом закругления 10 мкм вызывают изменения напряжения, которые регистрируются отсчетным устройством. Прибор имеет также записывающий механизм и может выдавать профилограмму поверхности. Для бесконтактного измерения применяют микроинтерферометры МИИ-4 и МИИ-11 с пределами измерений Rz— 0,005—1 мкм.
Толщина слоя, в котором в результате механической обработки нарушена кристаллическая решетка полупроводника, является одним из критериев качества обработанной поверхности пластины. Толщина нарушенного слоя зависит от размера зерна абразивного порошка, примененного для обработки, и приближенно может быть определена по формуле:
H=K∙δ, |
(1.1) |
где δ — размер зерна; К — эмпирический коэффициент (K=для Si; K=2,2
для Ge).
Структура нарушенного слоя имеет зоны нарушенного рельефного и трещиноватого слоев (последняя самая большая) и зону упругих деформаций. Под ними расположен неповрежденный монокристаллический материал.
Толщину нарушенного слоя определяют только в процессе отладки технологии механической обработки пластин. Наиболее простым и удобным методом определения толщины нарушенного слоя является визуальный контроль под микроскопом поверхности после селективного травления. Существуют и другие методы.
После определения толщины нарушенного слоя и назначения припусков на обработку стремятся создать и поддерживать такой технологический процесс изготовления полупроводниковых пластин,
14
который гарантировал бы удаление дефектов, возникающих при механической обработке. Поэтому в установившемся производственном процессе толщину нарушенного слоя не контролируют.
Для контроля толщины, неплоскостности, непараллельности и прогиба пластин используют стандартные измерительные средства, такие, как индикаторы часового типа или другие аналогичные им рычажномеханические приборы с ценой деления 0,001 мм. В последнее время для контроля геометрических параметров пластин все чаще начинают применять бесконтактные пневматические или емкостные датчики. С их помощью можно быстро производить измерения, не подвергая пластину риску загрязнения или механического повреждения.
15
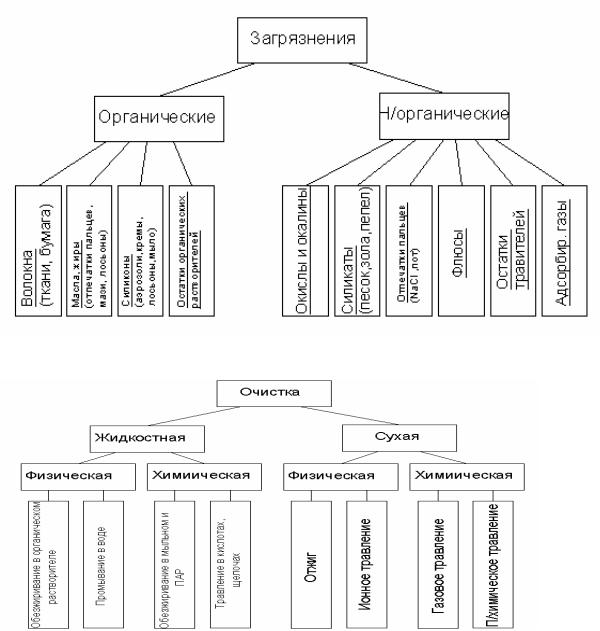
Тема №2
Оборудование для очистки поверхностей полупроводниковых подложек
В производстве полупроводниковых ИС важное место занимает очистка поверхности подложек как на начальных этапах формирования структуры, так и межоперационная обработка. Так как атомы полупроводника, расположенные на поверхности имеют много ненасыщенных (оборванных) связей, это объясняет высокие адсорбционные свойства и химическую активность поверхности.
Рисунок 2.1- Виды загрязнений в микроэлектронике
Рисунок 2.2 – классификация методов очистки Жидкостная очистка включает в себя три стадии очистки:
16
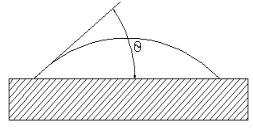
обезжиривание, травление и отмывку.
Обезжиривание ─ растворение, разрушение и удаление с поверхности загрязнений химически не связанных с материалом подложки.
Применяются горячие или кипящие бензин, бензол, толуол, спирты, ССL4 , дихлораты . Эти жидкости легко воспламеняются, ядовиты, поэтому для проведения процессов используются герметичные камеры с вытяжной вентиляцией.
Травление ─ растворение загрязнений, образующихся в результате химического взаимодействия материала подложки с окружающей средой.
При этом происходит удаление загрязнений и поверхностного слоя подложки.
Травители включают в себя окислитель и растворитель, в качестве которых применяются кислоты и щелочи (HF,HNO3, уксусная кислота, NaOH, KOH).
Отмывка ─ растворение в деионизованной воде остатков реагентов. Используется вода марки А с ρv=7-20 МОм·см и марки Б с ρv=1 МОм·см. Отмывку производят до выравнивания сопротивления воды на входе и выходе. Контроль чистоты поверхности можно осуществлять по значению краевого угла смачивания (рис.2.3). Угол должен составлять менее 750.
Рисунок 2.3- Определение чистоты поверхности
2.1 Оборудование для жидкостной очистки
Структурная схема любой технологической установки очистки состоит из следующих частей или узлов:
∙Рабочая камера или реактор;
∙Рабочий инструмент или устройство;
∙Устройства интенсификации очистки;
∙Приводные устройства, обеспечивающие необходимые механические перемещения подложек, рабочего инструмента или реагента или других элементов;
∙Пылезащитная камера;
∙Система подготовки и подачи реагентов;
∙Блоки питания и управления (датчики контроля и управления);
Установки бывают периодического и непрерывного действия. Преимущество установок непрерывного действия (рис.2.4) заключается в
17
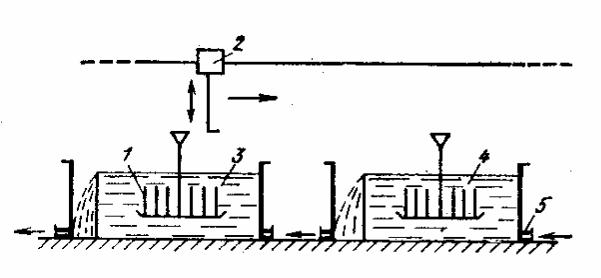
снижении эксплуатационных расходов, затрат времени (цикловые потери на загрузку и выгрузку), повышении устойчивости технологических параметров.
Рисунок 2.4 – Схема установки непрерывного действия
1 – кассета с подложками; 2- устройство для перемещения кассет; 3,4 – ванны; 5 – патрубок для слива реагента;
Ванна изготавливается из фторопласта. Реагент подается насосами через фильтровально – регенерационную систему.
2.2 Способы интенсификации очистки
Цель -увеличение скорости и качества очистки. Осуществляются путем нарева и перемешивания реагента, применением ультразвуковых колебаний. Нагрев осуществляется спиралями из нихрома, ТЭНами, лампами ИК - нагрева.
Мешалки бывают лопастными, пропеллерными и турбинными.
УЗ – излучатели включают в себя пьезоэлектрические и магнитострикционные преобразователи. В качестве материалов для пьезоэлектрических преобразователей используют BaTiO3, цирконат – титанат – свинца (ЦТС). Можно изготавливать любой формы – преимущества. Недостатки – большие механические и диэлектрические потери – перегрев (max 90 0C). Р=100-300 вт/см2.
U= 100-300 В.
Магнитострикционные излучатели бывают двух типов: стержневые и плоские (рис.2.5).
Стержневые излучатели выполняют из стандартных никелевых трубок. При работе трубка сильно нагревается вихревыми токами, поэтому ее разрезают по образующей.
18
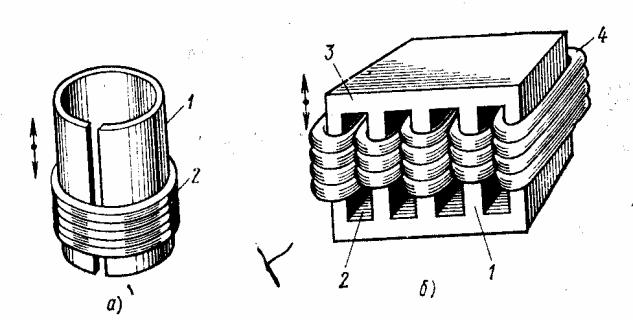
Рисунок 2.5 – Конструкции УЗ-излучателей: а) стержневой, б) плоский 1-трубка; стержень; 2,4- обмотка, окно; 3-ярмо
Более просты и надежны плоские излучатели. Они представляют собой пакеты из листов железа, никеля, кобальта и их сплавов. P=0.4 - 0.5 ВТ/см2, f=22; 44; 400 кГц.
2.3 Установки периодического действия
Несмотря на достоинство непрерывных процессов, в промышленности широко используют оборудование периодического действия. Преимуществами являются большая гибкость, меньшие капитальные затраты.
Широкое применение для очистки нашли вращающиеся столы или центрифуги с размещенными на них пластинами, обрабатываемых при помощи щеток и форсунок, распыляющих реагентов. Приводы вращения бывают с электродвигателем постоянного тока, с сельсином, электродвигатель переменного тока, с редуктором, с гидродвигателем, с пневмотурбиной. Конструкции узлов крепления пластин на столе центрифуги осуществляется вакуумными присосами, штырями, прижимами.
19
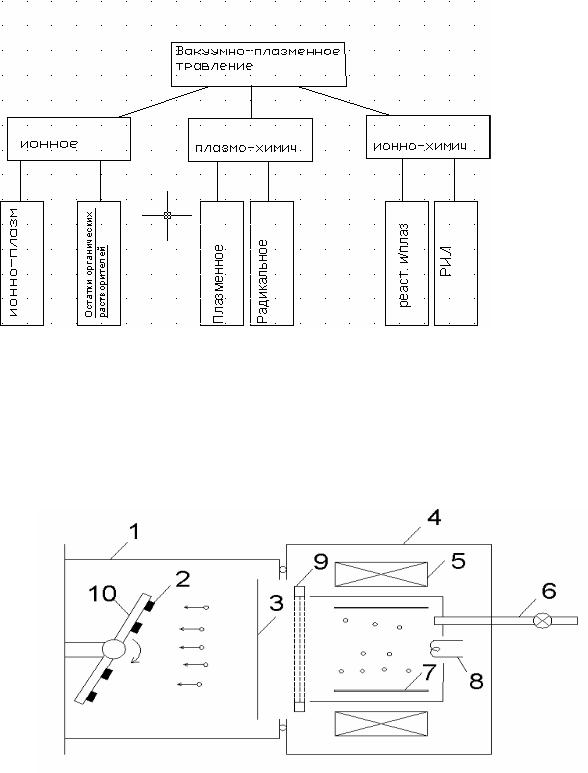
2.4 Вакуумноплазменное травление
Рисунок 2.6 – Разновидности вакуумно-плазменного травления
Преимущества: точность ±0.003 мм, универсальность, нет отходов. Недостатки: Е=1-10 кэв, j=10 А/м2
Источники: диодные и автономные ионные источники.
Подается постоянное или переменное (ВЧ – 13.56 МГц) напряжение.
Рисунок 2.7 – Установка плазмохимического травления с автономным ионным и источником
1-вакуумная камера, 2-подложки, 3- нейтрализатор, 4- газоразрядный и/источник, 5-соленоид, 6- натекатель, 7- анод, 8- катод, 9- сетки, 10подложкодержатель
20