
С.Н. Ковальчук Статистический анализ точности операций механической обработки
.pdfМинистерство образования Российской Федерации Государственное учреждение
Кузбасский государственный технический университет
Кафедра технологии машиностроения
СТАТИСТИЧЕСКИЙ АНАЛИЗ ТОЧНОСТИ ОПЕРАЦИЙ МЕХАНИЧЕСКОЙ ОБРАБОТКИ
Методические указания к лабораторной работе по курсу «Технология машиностроения» для студентов направления 552900 «Технология, оборудование и автоматизация машиностроительных производств»
Составитель С.Н. Ковальчук
Утверждено на заседании кафедры Протокол №10 от 9.10.02
Рекомендовано к печати методической комиссией направления 552900 Протокол №9 от 11.10.02
Электронная копия хранится в библиотеке главного корпуса ГУ КузГТУ
Кемерово 2003
1
ВВЕДЕНИЕ
Для исследования точности технологических процессов в технологии машиностроения используют методы математической статистики. Эти методы используют для решения следующих основных задач:
1.Определение соответствия заданной на чертеже точности детали точности и устойчивости технологического процесса.
2.Определение суммарной погрешности обработки.
3.Установление показателей точности отдельных операций и технологического процесса в целом.
4.Оценка качества настройки и точности производственного оборудования.
Сущность статистических методов оценки точности технологических процессов изложена в специальной литературе по технологии машиностроения [2,3].
1.ЦЕЛЬ РАБОТЫ
Изучение методики и получение практических навыков исследования точности параметров операций механической обработки деталей машин с помощью нормального закона распределения.
2. ТЕОРЕТИЧЕСКИЕ ПОЛОЖЕНИЯ
Изделия, изготовленные при одном и том же технологическом процессе, отличаются одно от другого по всем характеристикам качества. Это явление получило название рассеяние характеристик качества.
Первой характеристикой явления рассеяния служит величина меры рассеяния МР:
М р = Хmax − Хmin , |
(1) |
где Хmax − наибольшее значение характеристики в партии изделий; Хmin − наименьшее значение характеристики в партии изделий.
Второй характеристикой является практическая кривая рассеяния и определяющие ее параметры. Для построения кривой рассеяния на практике измеренные значения партии заготовок разбивают на интервалы (или разряды) f и определяют количество заготовок с размерами

2
(или частотами) mi в пределах каждого интервала. По оси абсцисс от-
кладывают интервал размеров, а по оси ординат – соответствующие им частоты.
Наиболее часто кривая рассеяния подчиняется закону нормального распределения (закону Гаусса). Результирующая погрешность обработки в этом случае представляет собой сумму большого числа погрешностей технологической системы, которые не связаны между собой и среди которых отсутствует доминирующая погрешность.
Закон нормального распределения в большинстве случаев оказывается справедлив при механической обработке заготовок с точностью 8, 9, 10 квалитетов и грубее. При более точной обработке распределения размеров обычно подчиняется другим законам: закону Симпсона, Релея, закону равной вероятности.
Если при обработке заготовок на их точность воздействуют как случайные погрешности, так и систематические, то закон распределения представляет собой композицию нескольких законов.
Уравнение кривой нормального распределения имеет вид
y(x) = |
σ |
1 |
e−(x−x)2 / 2σ2 , |
(2) |
|
2π |
|
|
где x − текущий действительный размер партии деталей; x − среднее арифметическое значение действительных размеров деталей данной партии, определенное по формуле
x = |
1 |
∑f |
x m , |
(3) |
|
||||
|
n i=1 |
i i |
|
σ − среднее квадратическое отклонение, определяемое по формуле
σ = |
1 ∑f |
(x |
|
− x)2 m , |
(4) |
|
n i=1 |
i |
i |
|
где f − количество интервалов, выбираемое в зависимости от объема партии измеренных деталей n; xi − середина интервалов измеренных размеров; mi − частота (количество деталей данного интервала).
Графически уравнению нормального распределения соответствует симметричная колоколообразная кривая, представленная на рис. 1.
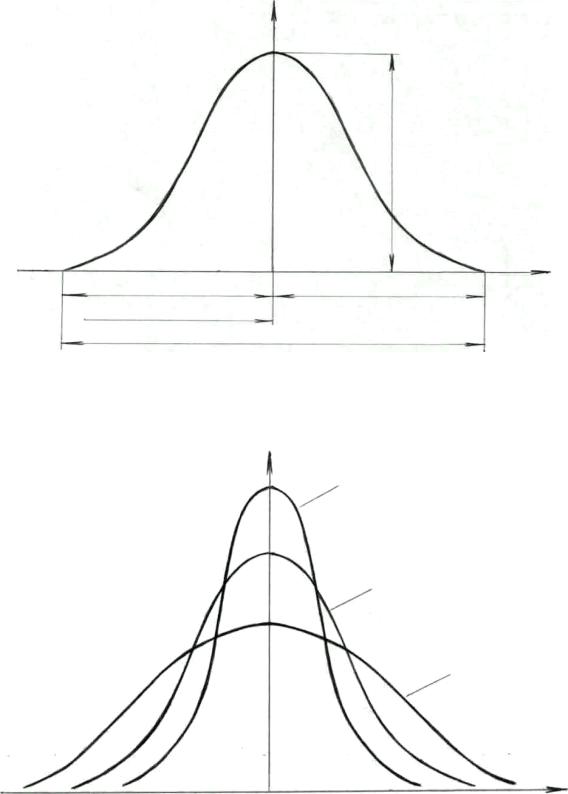
3
Y
Ymax
0 |
X |
-3σ |
+3σ |
X |
ω |
|
Рис. 1. Кривая нормального распределения
Y
σ < 1
σ = 1
σ > 1
X
Рис. 2. Кривые нормального распределения при различных значениях σ
4
Кривая нормального распределения симметрична относительно оси ординат. При х = х кривая имеет максимум. На расстоянии ±3σ от вершины ее ветви пересекаются с осью абсцисс. При этом поле рассеяния ω принимают равным 6σ, т.е.
ω = 6σ . |
(5) |
При увеличении σ значение ymax уменьшается, а поле рассеяния
ω возрастает. В результате этого кривая становится более пологой и низкой, что свидетельствует о большем рассеянии размеров и, следовательно, о меньшей точности. Значит σ является мерой рассеяния или мерой точности. Влияние σ на форму кривой нормального распределения показано на рис. 2.
Для приближения оценки соответствия распределения размеров партии деталей нормальному закону производят сравнение близости практической (опытной) кривой распределения размеров с наложенной на нее теоретической кривой.
Однако необходимо иметь уверенность, что данное распределение подчиняется закону нормального распределения. Для проверки этой гипотезы пользуются рядом критериев, которые называются критериями согласия. Наибольшее применение имеют критерии А.Н. Колмого-
рова λ и критерий Пирсона χ2 .
Статистический анализ точности операций механической обработки деталей в технологии машиностроения производят с помощью ряда показателей:
1.Коэффициента запаса точности на данной операции Кψ .
2.Коэффициента точности настройки станка Кн.
3.Количества вероятного брака деталей q .
4.Технологического допуска Ттехн..
3.ПОРЯДОК ВЫПОЛНЕНИЯ РАБОТЫ.
3.1.Исходные данные выборки партии деталей содержатся в табл. 1 прил. 2.
3.2.Построить практическую кривую распределения (полигон распределения) действительных размеров партии деталей, руководствуясь схемой, приведенной на рис. 3.

22
20
18
16
14
12
10
8
6
4
2
5
Частота де-
талей, mi Д
СС
T
X1 X2
|
|
|
|
|
_ |
|
|
|
|
|
|
|
|
|
|
|
|
|
|
Xдоп |
|
|
|
|
|
|
|
|
|
q1 |
|
|
|
|
|
|
|
|
E |
|
|
|
|
q2 |
|
|
|
|
|
|
|
|
|
|
|
|
|
|
|
А |
|
|
В |
|
|
|
|
|
|
В |
|
|
А |
|
|
|
|
|
|
|
|
|
|
|
|
|
|
||
20,00 |
20,01 |
20,02 |
20,03 |
|
20,04 |
20,05 |
|
20,06 |
20,07 |
20,08 |
20,09 |
20,10 |
20,11 |
Xi, мкм |
|
|
|
||||||||||||
0,05- |
|
0,04- |
0,03- |
0,02- |
0,01- |
|
_ |
+0,01 |
+0,02 |
+0,03 |
+0,04 |
|
+0,05 |
|
|
|
X |
|
|
||||||||||
|
|
|
|
|
|
|
|
|
|
|
|
|
|
Мр = Xmax - Xmin
ω = 6σ
Рис. 3. Схема построения полигона и кривая нормального распределения

6
Построение полигона распределения производят следующим образом. Середины интервалов хi откладывают по оси абсцисс, а соот-
ветствующие им частоты mi − по оси ординат. Полученные таким об-
разом точки соединяют ломаной линией.
3.3 Рассчитать статистические характеристики эмпирической кривой распределения:
1.Меру рассеяния МР, формула (1).
2.Среднеарифметическое значение действительных размеров деталей х, формула (3). Определяют как сумму данных 5 и 3-й граф вспомогательной табл. 1 прил. 1.
3.Среднеквадратическое отклонение измеренных размеров σ , формула (4). Определяют использованием сумм данных 8 и 3-й граф вспомогательной табл. 1 прил. 1.
3.4.Произвести оценку близости эмпирической и теоретической кривых распределения. Для этого необходимо построить теоретическую кривую по четырем характерным точкам, пользуясь таблицей и схемой рис. 3.
Координаты характерных точек кривой нормального распределения
|
Характерные точки |
Абсцисса |
Ордината |
|||||||
|
Вершина кривой (Д) |
|
х = х |
у = 0,4 |
nс |
|
|
|
||
|
|
σ |
||||||||
|
|
|
|
|
||||||
|
Точка перегиба (С) |
х = ±σ |
y = 0,24 |
nc |
|
|
||||
|
σ |
|||||||||
|
|
|
|
|
|
|||||
|
Точка перегиба (В) |
х |
= ± σ |
y = 0,054 |
nc |
|
||||
|
|
|||||||||
|
2 |
|
|
|
σ |
|||||
|
|
|
|
|
|
|
||||
|
Точка перегиба (А) |
х = ±3σ |
y = 0 |
|||||||
|
|
|
|
|||||||
|
Примечание: c − цена |
интервала эмпирической |
совокупности. |
3.5. Произвести оценку соответствия опытного распределения нормальному закону с помощью критерия согласия Пирсона χ2 (хи
квадрат). Для этого определяют теоретическую частоту каждого интервала выборки m′:
m′ = |
nc |
|
1 |
−( x−x )2 / 2σ2 |
|
|
σ |
|
2π e |
|
. |
(6) |
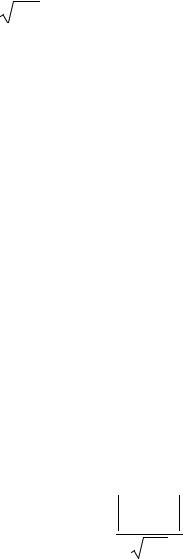
7
Обозначим
|
|
1 |
|
e |
−( x−x )2 |
/ 2σ2 |
= Zt . |
(7) |
||||||
|
|
2π |
|
|
|
|
|
|
|
|||||
|
|
|
|
|
|
|
|
|
|
|
|
|
||
Тогда формула (6) будет иметь вид |
|
|
|
|||||||||||
|
|
|
m′ = |
nc |
Zt , |
|
|
|
(8) |
|||||
|
|
|
|
|
|
|
|
|||||||
|
|
|
|
|
|
σ |
|
|
|
|
|
|
||
Величина Zt приведена в табл. 2 прил. 2. Расчетное значение кри- |
||||||||||||||
терия χ2 вычисляют по формуле |
|
|
|
′ )2 |
|
|||||||||
|
|
χ2 |
|
f ( m |
i |
−m |
|
|||||||
|
|
= ∑ |
|
|
|
i |
. |
(9) |
||||||
|
|
|
|
mi′ |
|
|||||||||
|
|
|
|
|
i=1 |
|
|
|
|
|||||
Расчет удобнее вести во вспомогательной табл. 2 прил. 1. |
||||||||||||||
Далее необходимо вычислить число степеней свободы k : |
||||||||||||||
|
|
|
|
|
|
k = f |
−3 . |
(10) |
||||||
Для того чтобы принять или забраковать гипотезу при помощи |
||||||||||||||
критерия |
χ2 , установлен уровень значимости его (или уровень веро- |
|||||||||||||
ятности) P = 0,05. Вероятности P(χ2 ) |
для различных значениях χ2 и |
|||||||||||||
k приведены в табл. 3 прил. 2. Если P(χ2 ) > 0,05, |
то гипотеза прини- |
|||||||||||||
мается. |
|
|
|
|
|
|
|
|
|
|
|
|
|
|
Можно так же определить величину A : |
|
|||||||||||||
|
|
|
|
|
A = |
|
χ2 −k |
(11) |
||||||
|
|
|
|
|
|
|
2k . |
|||||||
Если |
A < 3, то гипотеза о нормальности распределения измерен- |
ных размеров принимается, и данный теоретический закон для анализа точности данной операции механической обработки можно использовать.
3.6. Произвести оценку точности механической обработки по следующим характеристикам теоретического закона распределения:
Коэффициент запаса точности Kϕ характеризует влияние случайных факторов на точность обработки размеров:
Kϕ = |
T |
, |
(12) |
|
ω |
||||
|
|
|
где Т – допуск на обработку размера детали.

8
Если Kϕ >1, то обработка деталей возможна без брака (при усло-
вии правильной настройки станка).
При Kϕ ≥1,2 технологический процесс обеспечивает определен-
ный резерв точности, процесс обработки считается надежным.
При Kϕ ≤1 брак является весьма вероятным, т.к. технологиче-
ский процесс не обеспечивает требуемой точности.
Коэффициент точности настройки станка K H оценивает положе-
ние середины поля рассеяния размеров заготовок относительно середины поля допуска. Он характеризует влияние систематических погрешностей обработки деталей и определяется следующим образом:
K H = |
E |
, |
(13) |
|
T |
||||
|
|
|
где E = X − X доп − величина фактического смещения вершины кривой рассеяния от середины поля допуска X доп , см. рис. 3.
Если коэффициент точности настройки удовлетворяет условию
K H < |
T −ω |
, |
(14) |
|
2T |
||||
|
|
|
то считается, что настройка станка обеспечивает получение годных деталей (при Kϕ >1). В случае невыполнения данного условия настройка
станка вышла за допустимые пределы, что влечет за собой появление бракованных деталей.
Количество вероятного брака заготовок q характеризует возмож-
ный выход за границы поля допуска определенного количества деталей: при Кϕ ≤1 или КН ≥ (Т −ω/ 2Т). При этом количество деталей,
которые могут выйти за пределы допуска, выражается графически заштрихованной площадью, показанной на рис. 3. Площадь, ограниченная кривой распределения и осью абсцисс, равна 1 и выражает собой 100 % деталей выборки (партии), а площадь заштрихованных участков представляет собой вероятное количество деталей, выходящих по своим размерам за пределы поля допуска Т.
Площадь левого и правого заштрихованных участков q1 и q2 определяется путем вычисления интегралов по формулам

9
|
|
|
|
1 |
−x |
|
q1 |
= 0,5 |
− |
σ |
∫ |
1 e−(x−x)2 / 2σ2 dx; |
|
|
|
|
2π |
0 |
|
(15)
|
|
|
|
1 |
x |
2 |
q2 |
= 0,5 |
− |
σ |
∫2 e−(x−x) 2 / 2σ |
dx. |
|
|
|
|
2π |
0 |
|
Эти интервалы обычно представляют в нормированном виде в форме известной функции Лапласа Ф(t). Поэтому на практике вероят-
ности получения брака вычисляют следующим образом:
q1 |
= 0,5 −Ф( t1 ); |
(16) |
|
q2 = 0,5 −Ф( t2 ). |
|||
|
Значения функции Ф(t) приводят в табл. 4 прил. 2. Величина t
представляет собой коэффициент риска, определяемый по формулам t1 = σx1 ;
(17)
t2 = xσ2 ,
где x1 и x2 − расстояние от среднеарифметического размера партии
деталей x до соответственно нижней и верхней границ поля допуска, см. рис. 3.
Технологический допуск Ттехн. характеризует тот допуск, кото-
рый фактически обеспечивается при существующем технологическом процессе. Он определяется следующим образом:
Ттехн. =ω + E. |
(18) |
3.7. По результатам анализа сделать выводы о точности механической обработки деталей на исследуемой операции.
КОНТРОЛЬНЫЕ ВОПРОСЫ
1.Что понимается под точностью механической обработки?
2.Для решения каких задач в технологии машиностроения используют методы математической статистики?