
Экзаемн_сварка
.pdf
1. Основная терминлогия в области сварки
Сварка-процесс получения неразъемного соединения двух или более деталей из твердых материалов путем их местного плавления или совместного деформирования с нагревом и без нагрева с получением на границы прямых межатомных связей за счет сплавления основного и присадочного материала.
Дуга-устойчивый вид разряда, существ-х от 10 до 1000А.
Сварочная дуга -длительный разряд электрического тока в газовой среде, между находящимися под напряжением тонкими или жидкими веществами, которые являются концентрированным источником нагрева, использованных для сварки материалов.
Сварное соединение-участок конструкции, в котором отдельны ее элементы соединены с помощью сварки. В сварное соединение входят сварной шов, прилегающая к нему зона основного металла со структурными и другими изменениями в результате термического воздействия сварки(зона термического влияния) и примыкающие к ней участки основного металла.
Сварной шов-участок соединения, образующейся в результате кристаллизации материала, наход-ся в ранее расплавленном состоянии.
Свариваемость-характеристика металла отражающая его реакцию на физикохимическое воздействие в сварке и определяющего его пригодность для изготовления сварной конструкции.
Классификация сварки: 1. Сварка плавлением; 2. Сварка плавлением; По физическим признакам классифицируется: 1. Термической; 2.термомеханической; 3.
механической .
По техническим параметрам: 1. По способу защиты – на воздухе/под слоем флюса. 2. По непрерывности процесса. 3. По степени механизации – ручной/ механизированной/ автоматической.
По техническим признакам: 1. По виду. 2. Вид дуги. 3.род и полярность тока. 4. По способу формированию шва
1. Сущность пайки, классификация
Пайка-получение соединения с межатомными связями путем нагрева соединенных материалов до температуры ниже температуры плавления, последнего смачивания материалов расплавленным припоем, затеканием припоя в зазор и его кристаллизация.
Основные особенности: 1. Пайка осуществляется при температуре ниже точек плавления соединенных металлов. 2. Во всех случаях связана с введением в зазор между соединением металлов жидкой металлической прослойкой расплавленного металла, которая осуществляется капиллярным течением расплавленного припоя в зазоре. Введение в зазор припоя в виде фольги или нанесением на основной металл покрытия образующий припой путем контактного плавления покрытия на границы с основным металлом. 3. Соединения образуются в результате взаимодействия твердого основного металла с жидким припоем. Если условие для того взаимодействия отсутствует, то паяное соединение не образуется. 4. Завершающей стадией пайки во всех случаях является кристаллизация металлической прослойкой между соединенными поверхностями твердых металлов.
Паяеность – свойства материалов образовывать паяные соединения при заданном движении пайки
Преимущества пайки: 1. Возможность изготавливать по конфигурации узлы и целые конструкции за один нагрев, что позволяет рассматривать пайку в отличие от сварки как групповой метод соединения материалов и превращает ее в высокий технологический процесс легко поддающегося автоматизации и механизации. 2. Благодаря общему равномерному нагреву в печах и в ваннах, и последнему контролирующему охлаждению, позволяет существенно уменьшать, иногда полностью исключать остаточное напряжение и деформацию. 3. Соединять разнородные металлы, а так же металлы с неметаллами( графит, керамика). 4. Получать неразъемные, разъемные соединения. 5. Путем варьирования размеров соединенных

пайкой поверхностей получать равнопрочные с основным металлом соединения по своей надежности, превышающей в ряде случаев сварные соединения, получается более благоприятная форма соединений с меньшей концентрацией напряжения чем при контактной сварки. 6. Получать соединения в скрытых малодоступных местах изделий, изготавливать тонкостенные изделия с большой плотностью спаянных соединений и их объемным расположением.
Классификация пайки: 1. По удалению оксидной пленки. 2. По кристаллизации паяного шва. 3. Получения припоя. 4. Заполнение зазора припоем. 5. По источнику нагрева. 6. По наличию давлению на паяные детали. 7. По одновременности выполнения паяных соединений(ступенчатая, одновременная)
2.Состав клеев
всостав клеящих материалов входят следующие компоненты: пленкообразующее вещество-основа клея, которое определяет адагизионные, когезионные свойства клея и основные физико-механические характеристики клеевого соединения: растворители, создающие определенную вязкость клея; пластификаторы для устранения усадочных явлений в пленке и повышения ее эластичности; отвердители и катализаторы для перевода пленкообразующего вещества в термостабильное состояние; наполнители для уменьшения усадки клеевой пленки, повышения прочности склеивания и , следовательно, возможности менее точной подгонки поверхности и экономики клеящих материалов. В качестве пленкообразующего вещества в основном применяют синтетические смолы и каучуки. Растворителями служат спирты, ацетон, бензин и др., а наполнителями -порошки, волокна, ткани. Металлические порошки повышают теплопроводность клеевых соединений, серебро, медь, никель и графит сообщают пленке токопроводимость.
3.Сварочная проволока
основные виды сварочной проволоки – сплошного сечения, порошковая, активированная.
Сварочная проволока сплошного сечения -применяется для полуавтоматической и автоматической сварки, а так же для изготовления электродов и присадочных прутков. Химический состав и диаметр проволоки для сварки сталей регламентирует ГОСТ 224670. Проволока для наплавки выпускается по Гост 10543-75, проволока из меди и сплавов – по ГОСТ 16130-72, проволока из алюминия и сплавов по Гост 7871-75. Наиболее распространенной является стальная проволока. Она выпускается следующих диаметров(мм):
0,3;0,5;0,8;1,0;1,2;1,4;1,6;2,0;2,5;3;4;5;6;8;10;12
1.диаметр
2.марка проволоки:
назначение (СВ-сварочная, Нп-наплавочная).
Содержание углерода в сотых долях процента. Н-р, Св08-проволока содержит 0,08% углерода;
Может указываться содержание легирующих элементов, обозначающихся следующими буквами: Х-хром, Н-никель, С-кремний, М-молибден, Г-марганец, Т-титан, Ф-ванадий, Д- медь, Ц-цирконий, Ю-алюминий. За буквой, которая обозначает легирующей элемент, следует число, указывающее его в содержание в процентах. Если легирующей элемент содержится в

количестве около 1% то число не ставится. Н-р: Св08х21Н5Т расшифровывается следующим образом: проволока сварочная, содержание углерода 0,08%, хрома 21%, никеля 5%, титана
1%.
Могут указываться повышенные требования к чистоте проволоки по вредным примесям – серы и фосфора. Они отмечаются в марке буквами А и АА. Н-р, в проволоке Св08 допускается до 0,04% серы и фосфора, для Св08А – до 0,03% этих примесей, в Св08АА – до
0,02%.
3.Способ выплавки: ВД –вакуумно-дуговые печи, ВИ – вакуумно-индукционные печи; Ш-электрошлаковый переплав.
4.Если проволока предназначена для изготовления электродов, то ставится буква Э.
5.Если проволока выпускается с омедненной поверхностью, то ставится буква О
6.ГОСТ на проволоку.
Порошковая сварочная проволока представляет собой трубчатую проволоку, заполненную порошкообразным наполнителем. Отношение массы порошка к массе металлической оболочки составляет от 15 до 40%. Конструкция порошковой проволоки может быть разной – простой трубчатой, с различными загибами оболочки, двухслойной. Загибы используются для придания проволоке жесткости и предотвращения высыпания порошка при ее сдавливании подающими роликами сварочного полуавтомата. Порошкообразный наполнитель
представляет собой смесь руд, минералов, ферросплавов, химикатов. Он выполняет функции: защиту металла от воздуха, стабилизацию дугового разряда, раскисление и легирование шва, формирование шва, регулирование процесса переноса электродного металла и др.
По составу: 1. Рутилорганические: при больших силах тока сварочная ванна интенсивно поглащает газы, что приводит к пористости. В связи с этим сила тока ограничена, что снижает производительность сварки.
2. карбонатно-флюоритные: рекомендуется использовать для сварки низкоуглеродистых и низколегированных сталей ответственных конструкций. При этом механические свойства шва выше, чем для рутил-органических проволок. Сварные швы более пластичны и лучше работают при низких температурах.
3. флюоритные: по характеристикам занимают промежуточное место между рутилорганическими и карбонатно-флюоритными.
Использование порошковых проволок при сварке в углекислом газе позволяет существенно улучшить технологические параметры прочеса сварки и механические свойства шва по сравнению с проволоками сплошного сечения. Улучшается формирование и внешний вид шва, снижается разбрызгивание металла, повышаются механические характеристики сварного соединения.
2.Рутиловые: предназначены для сварки широкого круга конструкций из низкоуглеродистой и низколегированной стали
3.Рутил-флюоритные: обеспечивают высокую ударную вязкость и рекомендуются для сварки конструкций из легированных сталей, работающих в сложных климатических условиях при динамических нагрузках.
Условное обозначение:
1,2 –самозащитная группа; 3,4 – для сварки в защитных газах.
1.Назначение: ПГ-для сварки в защитных газов; ПС – самозащитная
2.Прочность наплавленного металла . Ч или Л- для сварки чугуна или легированной стали. Для низкоуглеродистых и низколегированных сталей буква не ставится.
3.Обозначение допустимых пространственных положений: Н-нижнее, В –нижнее, горизонтальное, вертикальное; ВТ –только горизонтальное; В^-только вертикальное; Т-все положения.

4. Температура перехода к крупному разрушению: 0 – 200С; 1- минус200С; 3- минус 300 С; 4- минус 400; 5 – минус 500С; 6 –минус 600С. Буква Д – требования не регламентированы.
ПП-АН3-3,0Пс-44-А2Н ГОСТ2671-84 ППпроволока порошковая;
АН3-марка проволоки; 3,0-диаметр проволоки ПС -самозащитная;
44-индекс предела прочности; А-категория хим состава 2- индекс температуры охрупчивания
Н-пространственное положение сваоки: нижнее
4.Технологические операции процесса пайки
1.подготовить поверхность под пайку: предварительное удаление жиров, масел, грязи, окалины и толстых неметаллических оксидных пленок
2.произвести сборку деталей: должна обеспечивать свободное расширение
3.укладка припоя: сборка включает в себя нанесение припоя, должно быть правильное дозирование припоя. Требуемое количество припоя нужно правильно рассчитать: Q=1.5 bhlp; b-наибольший зазор; h-высота или ширина соединения; l-длина соединения, p- плотность припоя.
4.произвести пайку
5.обработка деталей после пайки
5.Рекомендация по конструированию клеевых соединений
Подготовка поверхностей:
Удалить остатки лака, грязи, окислившиеся слои, окалины после прокатки, прессовачные пленки, прилипшие в-ва. Провести травление поверхности. Затем провести химическое травление.
Технологический процесс склеивания:
1.Подготовка поверхности
2.Подготовка клея
3.Нанесение клея
4.Сушка – выдержка перед соединением
5.Сборка детали
6.Запессовка
7.Отверждение
8.Зачистка клеевых соединений
9.Контроль качества.
Склеивание - это способ создания неразъемного соединения элементов конструкции с помощью клея. Процесс склеивания основывается на явлении адгезии - сцепления в результате физических и химических сил взаимодействия клея с различными материалами при определенных условиях.
Конструирование клеевых соединений
Элементы конструкции, сборка которых осуществляется склеиванием, должны иметь для этого специально спроектированное соединение. При проектировании клеевого соединения необходимо:
•определить величину и тип нагрузки на всю конструкцию и особенно на клеевое соединение;
•определить изменение свойств клеевого соединения под воздействием среды, в которой оно будет работать;
•выбрать материал конструкции;
•выбрать клей;

•рассчитать размеры и остальные конструкционные параметры соединения с учетом запаса прочности;
•выбрать технологию склеивания (обработку поверхности, способ нанесения клея, режим отверждения);
•экономически обосновать выбранную конструкцию и технологию.
При конструировании клеевых соединений необходимо учитывать следующие рекомендации:
•площадь склеивания должна быть как можно большей;
•нагрузку должна нести максимальная часть площади склеивания;
•необходимо добиваться, чтобы напряжение в клеевом шве действовало в направлении его максимальной прочности;
•оптимальные зазоры между склеиваемыми поверхностями в зависимости от марки клея и конструкции должны быть в пределах:
0,05...0,15мм при склеивании металлов между собой; 0,05...0,2мм при склеивании металлов с неметаллическими материалами; 0,1...0,2мм при склеивании металлов с резиной.
Впроцессе эксплуатации клеевые соединения воспринимают различные нагрузки, которые могут быть приведены к четырем основным типам (рис. 34). В табл. 42 представлены типы конструкций клеевых соединений, способных воспринимать различные нагрузки.
Рис. 34. Основные типы нагружения клеевого соединения:
а - сдвиг; б - равномерный отрыв; в - отдир; г - внецентровой отрыв
Рекомендуемые типы конструкции клеевых соединений в зависимости от направления нагрузки
Клеевые соединения |
Клеевые соединения |
Угловые стыковые
Стыковые с одной и двумя накладками
Стыковые нахлесточные
Угловые с загибом кромки
Соединения полых профилей
Угловые в паз
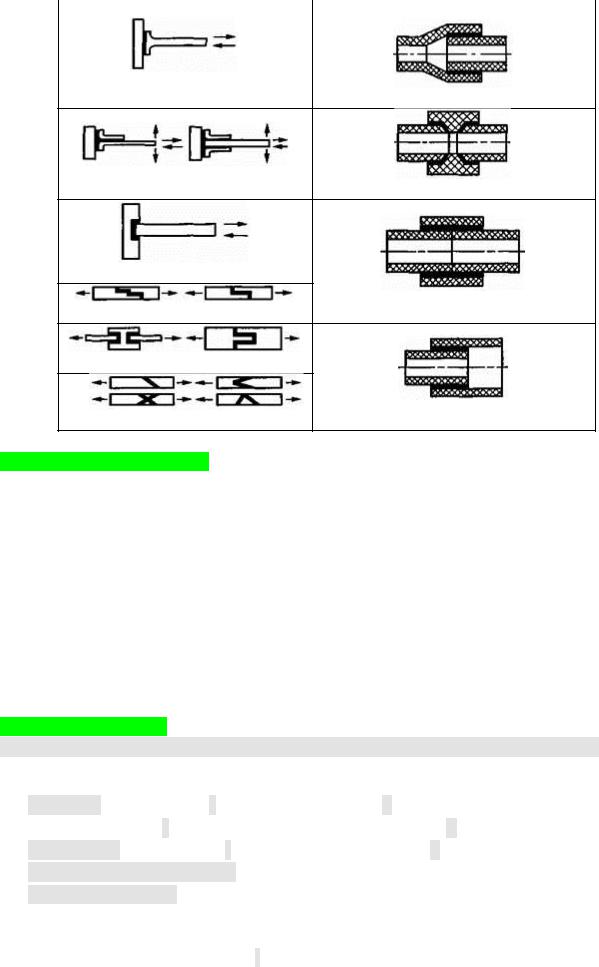
Соединение труб
Тавровые стыковые
С формированным гладким раструбом
Тавровые с уголком
С двухраструбной муфтой
Тавровые в паз
С гладкой надвижной муфтой
Стыковые с нахлестом
Стыковые в паз
Разных диаметров
Стыковые на ус
6. Технология точечной сварки
Точечная контактная сварка — сварочный процесс, при котором детали соединяются в одной или одновременно в нескольких точках.
Прочность соединения определяется
размером и структурой сварной точки, которые зависят от формы и размеров контактной поверхности электродов,
силы сварочного тока,
времени протекания сварочного тока через заготовки,
усилия сжатия и состояния поверхностей свариваемых деталей.
Спомощью точечной сварки можно создавать до 600 соединений за 1 минуту. Сила тока от 10000 до 24000 Ампер, усилие от 100 до 300 кг. Применяется для соединения тончайших деталей (до 0,02 мкм) электронных приборов, для сварки стальных конструкций из листов толщиной до 20 мм в автомобиле-, самолёто- и судостроении, в сельскохозяйственном машиностроении и других отраслях промышленности.
7.Классификация пайки
Классификация способов пайки осуществлена по следующим независимым признакам:
По температуре: низкотемпературная м высокотемпературная
удалению окисной пленки(Флюсовая, бесфлюсовая),
получению припоя(Готовым припоем и без готового припоя),
заполнению зазора припоем(Капиллярная, некапиллярная),
кристаллизации паяного шва,
источнику нагрева(пайка паяльником, горелкой, электросопротивлением, в печи, погружением, индукционный способ, электролитический способ, с помощью света, лазера, теплоты, хим. реакций, потока ионов в тлеющем разряде, инфракрасное излучение, волны припоя, электронный луч),

наличию давления на паяемые детали,
одновременности выполнения паяных соединений (Ручная, механизированная, автоматизированная).
8.Классификация составляющих клея
Клеи состоят из нескольких компонентов: основного клеевого вещества, растворителя и добавок: отвердителя, наполнителя, пластификатора, стабилизатора, антисептика, гидрофобных добавок, вспенивающих веществ, которые в композициях имеют различное назначение:
Растворители – это жидкости, которые обеспечивают определенную консистенцию и содержание в клее сухих веществ. К ним относятся вода, спирты, бензин, этилацетат и др. Клееобразователями называют вещества, способствующие переходу клеевых веществ в коллоидный раствор. Это известь и щелочи для белковых клеев.
Отвердители – это вещества, ускоряющие реакцию поликонденсации синтетических смол, то есть процесс их перехода в нерастворимое состояние (слабые кислоты, хлористый аммоний и т.д.).
Наполнители применяются для повышения вязкости клея, уменьшения его расхода и снижения усадки клеевого слоя. В качестве наполнителя используют муку (древесную, пшеничную, ржаную и др.) и порошки (мел, гипс, сажа, цемент и др.).
Пластификаторы (глицерин, диэтиленгликоль, дибутилфталат и др.) применяются в клеевых растворах синтетических смол для придания пластичности клеевому шву и снижения его хрупкости.
Стабилизаторами называют вещества (ацетон, этиловый спирт и др.), которые вводят в
клеевой раствор на базе синтетических смол в экстремальных ситуациях для продления его жизнеспособности и8 сохранения уже приготовленного клея. Они сохраняют заданную концентрацию клея.
Дубители, придающие клею водоупорность (уротропин, формалин, медные соли).
Антисептиками называют вещества, применяемые для придания клеям биостойкости по отношению к грибам и плесени.
Антисептиками могут быть пентохлорфенолят натрия, фтористый натрий, фенол, крезол, формалин и др.
Антипирены обеспечивают склеенным материалам повышенную огнестойкость. Это бура, фосфорнокислый аммоний.
Гидрофобные добавки, например, парафин, церезин используют для повышения водостойкости древесностружечных плит.
Вспенивающие вещества (пылевидный альбумин) применяют для получения клеевой пены на основе карбамидоформальдегидных смол с целью снижения расхода клея
9.Обозначение сварочных швов на чертежах
1)Вспомогательные знаки шва
- шов по замкнутой линии

-шов на монтаже
2)Стандарты на швы и соединения, выполненные конкретным способом сварки(ГОСТ)
3)Группа центового обозначения стандартов на типы конструктивных элементов
4)Условные обозн. способа сборки ( допускается не проставлять)
5) Знак - катет для угловых швов
6)Для прерывистого шва: длина проваренного участка.
7)Доп. Знаки:
10. Шовная сварка плюсы и минусы
«+»
Герметичность сварного соединения
Экономичность процесса, значит, отсутствует расход на материал
Возможность полной автоматизации процесса
«-»
Необходимость отчистки свариваемой поверхности от окалины, ржавчины, окислов и разл. загрязнений
Сравнительно не высокая скорость сварки
11.Наплавка: сущность, назначение отличия в способах
Наплавка - нанесение с помощью сварки слоя металла на поверхность изделия. При восстановлении, ремонте наплавку выполняют примерно тем же металлом, из которого изготовлено изделие, однако такое решение не всегда целесообразно. Иногда при изготовлении новых деталей (и даже при ремонте) целесообразней на поверхности получить металл, отличающийся от металла детали. Действительно, в ряде случаев условия эксплуатации поверхностных слоев значительно отличаются от условий эксплуатации всего остального материала изделия. Так, например, если деталь (изделие) должна определять общую прочность, которая зависит от свойств металла и его сечения, то поверхностные слои часто дополнительно должны работать на абразивный или абразивно-ударный износ (направляющие станин, зубья ковшей землеройных орудий, желоба валков канатноподъемных устройств и др.). Условия работы могут усложняться повышенной температурой, эрозионно-коррозионным воздействием окружающей среды (морской воды, различных
реагентов в химических производствах и др.). В качестве примера можно указать клапаны двигателей, уплотнительные поверхности задвижек, поверхности валков горячей прокатки и т.п. Иногда такие детали и изделия целиком изготовляют из металла, который обеспечивает и требования к эксплуатационной надежности работы его поверхностей. Однако это не всегда наилучшее и, как правило, не экономичное решение. Часто оказывается целесообразней все изделие изготовлять из более дешевого и достаточно работоспособного металла для конкретных условий эксплуатации и только на поверхностях, работающих в особых условиях, иметь необходимый по толщине слой другого материала. Иногда это достигается применением биметаллов (низкоуглеродистая сталь + коррозионно-стойкая сталь; сталь + титан и др.), а также поверхностным упрочнением (поверхностной закалкой, электроискровой обработкой и др.), нанесением тонких поверхностных слоев (металлизацией, напылением и пр.) или наплавкой слоев значительной толщины на поверхность.
В изготовлении новых изделий в целях обеспечения надлежащих свойств конкретных поверхностей обычно применяют относительно простые стали (например, низкоуглеродистые), а на рабочие поверхности наплавляют, например, бронзу, заменяя тем самым целиком бронзовую деталь, кислотостойкую сталь (для работы в условиях воздействия соответствующей химически агрессивной среды) или материал, хорошо работающий на истирание (при наличии трения с износом) и т.п.
Такие слои можно наносить на наружные поверхности деталей (например, валы, валки прокатного оборудования, рельсовые крестовины и др.) или внутренние поверхности - обычно цилиндрических изделий (корпуса химических и энергетических реакторов, оборудование химических производств и др.).
Наплавку осуществляют нанесением расплавленного металла на поверхность изделия, нагретую до оплавления или до температуры надежного смачивания жидким наплавленным металлом. Наплавленный слой образует одно целое с основным металлом (металлическая связь). При этом, как правило (кроме некоторых случаев ремонтной наплавки, применяемой для восстановления исходных размеров деталей), химический состав наплавленного слоя может значительно отличаться от состава основного металла. Толщина наплавленного металла, образованного одним или несколькими слоями, может быть различной: 0,5 ... 10 мм и более.
Необходимые свойства металла наплавленного слоя зависят от его химического состава, который, в свою очередь, определяется составом основного и дополнительного металлов и долями их участия в образовании шва. Влияние разбавления слоев основным металлом тем меньше, чем меньше доля основного металла в формировании слоя (γ0). В связи с этим для случаев (а их большинство), когда желательно иметь в наплавленном слое состав, максимально приближающийся к составу наплавляемого металла, необходимо стремиться к минимальному проплавлению основного металла, т.е. к уменьшению доли основного металла в металле шва (γ0).
При многослойной наплавке состав каждого слоя различен, так как различна доля участия основного металла (на который наплавляют) в образовании наплавленного слоя. Если при наплавке 1-го слоя основной металл непосредственно участвует в формировании шва, то при наплавке 2-го и последующих слоев он участвует косвенно, определяя состав предыдущих слоев. При наплавке большого числа слоев при некоторых условиях наплавки состав металла поверхностного слоя может быть идентичен дополнительному наплавляемому металлу.
Доля участия основного металла в формировании наплавленного металла зависит как от принятого способа, так и от режима наплавки. Различные дуговые методы наплавки отличаются друг от друга тепловой подготовкой основного и наплавляемого металлов. Так, например, при плазменной наплавке с токоведущей присадочной проволокой тепло-вложение преимущественно осуществляют в присадочную проволоку, основной металл подогревается достигающими его поверхности остывающими потоками плазмы дуги и теплотой перегретого жидкого наплавляемого металла. Проплавление основного металла в этом случае может быть заметно уменьшено. Наоборот, при дуге прямого действия, когда на основном металле

располагается катодное или анодное пятно дуги, ограничить расплавление основного металла значительно труднее, особенно при значительном сосредоточении дугового разряда (уменьшении диаметра плавящегося электрода, увеличении плотности тока в электроде). Рассредоточение тепловложения в основной металл, например при ленточном электроде, когда дуга перемещается по торцу ленты от одного конца к другому и иногда возникает одновременно в нескольких местах, может заметно снизить долю расплавляемого основного металла. При ручной дуговой наплавке покрытыми электродами, а особенно при механизированной наплавке плавящейся электродной проволокой в среде защитных газов или под флюсом, доля основного металла в наплавленном слое γ0, как правило, не может быть, без опасности получения непровара, снижена менее чем до 0,2 мм.
В зависимости от условий эксплуатации поверхностных слоев различных изделий требования к наплавленному слою различны. Наибольшее распространение получили наплавочные слои, которые можно классифицировать в основном по пяти группам:
1.Стали (углеродистые и высокоуглеродистые, хромомарганцовистые, хромистые и высокохромистые, хромоникелевые, высоковольфрамовые и молибденовые);
2.Специальные сплавы на основе железа (высокохромистые чугуны, сплавы с хромом и бором, сплавы с кобальтом, молибденом и вольфрамом);
3.Сплавы на основе никеля и кобальта (хромоникелевые сплавы с бором и кремнием, никелевые сплавы с молибденом, кобальтовые сплавы с хромом и вольфрамом);
4.Карбидные сплавы (с карбидами вольфрама, ванадия, хрома);
5.Сплавы на медной основе (бронзы алюминиевые, оловянно-фосфористые).
Вцелях уменьшения локализации напряжений целесообразно предварительно на основной металл наплавлять подслой с промежуточным значением коэффициента линейного расширения. Такой подслой ограничивает развитие диффузионных прослоек (обезуглероживание в углеродистой стали и появление карбидной прослойки в более легированной аустенитной стали возле линии сплавления), которые после длительной работы, наплавленной детали при высоких температурах или после термообработки изделия в некоторых случаях могут снижать эксплуатационные характеристики изделия.
12.Основные операции технологического процесса склеивания
При разработке технологического процесса склеивания металлических конструкций следует руководствоваться прежде всего назначением и условиями работы изделия, свойствами выбранных клеев и склеиваемых материалов, учитывая также вопросы, связанные с возможностями и экономическими аспектами промышленного производства. Исключительно важно понимать, что эффективность всех операций технологического процесса, а следовательно, и качество клееных изделий зависят от правильного и рационального сочетания основных параметров конструкции и технологии клеевого соединения.
Технологический процесс склеивания металлов складывается из следующих основных операций:
1.Подготовка поверхностей деталей
2.Подготовка клея;
3.Нанесение клея на склеивающие поверхности
4.сушка
5.сборка деталей
6.запрессовка
7.отверждение клеевых швов(открытая выдержка при определенной температуре в течение заданного времени)
8.зачистка клеевых соединений
9.контроль качества