
Rudnev V.Common misinterpretations and confusion appearing in induction heating publications
.pdf
International Scientific Colloquium
Modelling for Electromagnetic Processing
Hannover, March 24-26, 2003
Common Misinterpretations and Confusion Appearing in Induction Heating Publications. Presentation of New Handbook of Induction Heating
V.Rudnev
Abstract
During numerous discussions with users of induction heating technology we found that quite often some of them misinterpreted certain interrelated aspects involved in this process. One of the reasons for this is the fact that quite often descriptions of particular phenomena are contained in a variety of internal reports, scientific journals, or literature specializing in a particular (typically quite narrow) area. Some of these materials have been presented in a form that is nearly inaccessible to readers with limited experience in science or applied engineering. Some textbooks heavily emphasize the theoretical aspects, others are limited by a description of phenomena involved in induction heating on a “nuts-and-bolts” level only. An attempt has been made to bridge the gap between advanced theoretical information and information which is of concrete and
practical use to the induction heating practitioners.
In the newly published Handbook of Induction Heating (Fig.1) [1], an attempt has been made to continue the tradition of classical texts devoted to this process to educate the wide range of the specialists involved in this technology. Another goal of this handbook is to embark upon the next step in the study and design of modern induction heating processes and equipment. Thus, there is a hope that this 800-page handbook will serve the industry as a complete contemporary guide to induction heating. Some of the subjects discussed in this handbook are indicated below.
Introduction
What would be your answers to the following questions?
ØCan iron-iron carbide diagram be directly applied in induction hardening?
ØCan time-temperature transformation diagrams (TTT-diagrams) and continuous-cooling transformation diagrams (CCT diagrams) be automatically applied for prediction results of induction hardening?
ØCan results of Grossmann’s hardenability tests and Jominy end-quench tests be directly applied to selective hardening?
ØAre the procedures of choosing process parameters for induction hardening of steels and cast irons identical?
57
ØAre properties of induction tempered parts identical to properties of parts that have been tempered in conventional furnaces (gas-fired, infrared or resistance heater)?
ØIs eddy current induced within the heated body distributed according to exponential law?
ØDo magnetic flux concentrators always improve an efficiency of the induction coil?
ØIs it always preferable in induction brazing and soldering applications to have joint clearances as small as possible?
ØIs frequency selection in induction wire, cable and rope heating similar to bar and billet heating?
ØIs selection of the process parameters for induction heating of rectangular and trapezoidal shape workpieces (i.e., slab, strip, plate, bloom, transfer bar) similar to selection of the process parameters of cylinder billets and bars?
If your answers are “YES” you might be surprised after reading a new Handbook of Induction Heating (Fig.1) [1]. Below there will be a short discussion regarding some of above mentioned questions.
1. Can iron-iron carbide diagram be directly applied in induction hardening?
When heat treating steel parts the critical temperatures are often determined based on the iron-iron carbide phase transformation diagram (Fe-Fe3C). This widely used diagram represents a graph of temperature vs. carbon content of the steel and shows the effect of heating the metal to elevated temperatures or metal cooling that may cause a transformation in its crystalline structure. It is also used to determine the range of temperatures in which certain types of heat treatment of the steel may be carried out.
However, it is important to remember that this diagram might be misleading in some induction heat treating applications since it is valid only for the equilibrium condition of plain carbon steel. One of the major requirements of an equilibrium condition is sufficiently slow heating. Induction heating is a very fast process. Since heat intensity often exceeds a magnitude of 100oC/sec, this process cannot be considered by any means as an equilibrium process resulting in limiting the use of the iron-iron carbide phase transformation diagram. A high rate of induction heating affects the kinetics of the austenite formation process. In addition, Fe-Fe3C diagram does not take into consideration prior microstructure.
Section 2.1.1 of a Handbook of Induction Heating [1] discusses the effect of the heating rate on the Ac1 and Ac3 critical temperatures of steels and cast irons as well as grain growth phenomenon and how different prior microstructures (structure of the “green” part) influence the induction hardening temperatures, process parameters selection and results of the heat treatment.
A “favorable” prior microstructure allows one to reduce the austenizing temperature leading to fast and consistent metal response to induction heat treatment with the smallest shape/size distortion, minimum amount of grain growth and required energy. If the initial microstructure of a steel part has a significant amount of coarse pearlite and, most importantly, coarse ferrites or clusters or bands of ferrites, then those microstructures cannot be considered “favorable” structures. Large areas, (clusters or bands) of ferrite require a long time for carbon to be able to diffuse into the poor carbon area of the ferrite. Those clusters or bands of ferrites could act as one huge grain of ferrite and, most likely, will be retained in the austenite. Upon quenching, a complex ferritic-martensitic microstructure will be formed. Scattered soft and hard spots and poor mechanical properties characterize this structure. Therefore, segregated and banded initial microstructures of “green” parts should be avoided.
Steels with large stable carbides (i.e. spherodized microstructures) have poor response to induction hardening as well and also result in the necessity to have prolonged heating and higher temperatures for austenization. Longer heat time leads to grain growth, the appearance
58
of coarse martensite, extended transition zone, surface oxidation/decarburization and increased shape distortion. Coarse martensite has a negative effect on such important properties as toughness, impact strength, bending fatigue strength and is susceptible to crack development.
2. Can time-temperature transformation diagrams (TTT-diagrams) and continuouscooling transformation diagrams (CCT diagrams) be automatically applied for prediction results of induction hardening?
Time-temperature transformation diagrams (TTT-diagrams) and the continuouscooling transformation diagrams (CCT diagrams) are also widely used in the heat treat industry and allow one to determine the end products of austenitic transformation upon its cooling by holding the steel at a fixed temperature below the A1 critical temperature (TTTdiagrams) or taking into account the continuous nature of the process during cooling of austenite. Although TTT (IT) and CCT diagrams are helpful, it is important to remember that there are several drawbacks when trying to apply those diagrams for the induction heat treating. The following are:
♦An assumption of a homogeneous austenite has been made in developing both the TTT and the CCT diagrams.
♦Although CCT diagrams take into consideration continuous cooling during quenching, they presume that the cooling curve has a constant cooling rate, which is often not a valid assumption.
♦It is important to remember that samples with small cross-sections were used to obtain these diagrams. Therefore, there will be some inherent errors in trying to apply those curves to moderate or large sized parts as well as complex-shaped parts.
♦In induction heat treating, the thermal heat exchange process between the surface of the heated workpiece and the quenchant, among other factors, is a function of the surface temperature, which obviously is not constant. In addition, the workpiece temperature (austenizing temperature) prior to applying quenchant is typically not the same as assumed in the CCT diagrams.
♦Finally, in surface hardening the temperature distribution prior to quenching is nonuniform. The existence of a cold core that acts as a heat sink, has a marked effect on the severity of the cooling rate during quenching.
3. Can results of Grossmann’s hardenability tests and Jominy end-quench tests be directly applied to selective hardening?
Hardenability is an important property of steel and cast iron defining the ability of the material to be hardened to a certain depth and can be parameterized as critical diameter. Three parameters influencing the value of the critical diameter (chemical composition, grain size and homogenization of austenite) can be relatively easily defined. The forth factor (the quenching condition) is often the least defined factor, particularly in the case of induction hardening.
The severity of cooling during spray quenching depends upon a combination of several factors (i.e., type and purity of the quenchant, quenching temperature, pressure and flow rate, specifics of the quench block design, number and distribution of quench holes, size and density of orifices, spray impingement, etc.). The complexity of determining the particular quenching condition makes it difficult to use a value for the critical diameter for a description of the hardenability.
59
There are several experimental techniques that exist for the determination of the hardenability of steel and cast iron. Among these techniques the Grossmann’s hardenability test and the Jominy end-quench test are two of the most widely used. Unfortunately, both techniques should be applied for induction hardening (particularly induction surface hardening) with a great deal of caution due to the assumptions of measurements that have been done. For example:
♦In its standard form, the Jominy end-quench test is only suitable for moderate cooling rates and can provide misleading results when cooling rates are about 150oC/sec or higher which is the case of the majority of induction hardening applications.
♦According to standard hardenability tests, a specimen is heated to austenitic temperature and held at that temperature for a sufficiently long time assuring that a homogeneous austenite has been formed. However, in the case of induction hardening when intense heating has been applied without any or very short holding time, the structure of the austenite and its homogenization differ compared to austenite formed on slow heating with a sufficiently long holding time. This feature can cause some differences in the hardenability curves.
♦The fact that heating during induction hardening is very intensive shifts the A1 and A3 critical curves toward higher temperatures. Quenching of specimens from temperatures that are often 100oC to 180oC higher than the temperature used during hardenability tests can also result in appreciable errors.
♦The ability of the cold core to increase the quenching severity in surface hardening applications is another factor that results in modification of the conventional hardenability curves.
♦Hardenability tests are primarily oriented toward specimens of cylindrical shape with limited ability to extend them to the square cross-sections. Unfortunately, these results cannot be easily transferred to complex geometry such as gears, etc.
4. Are the procedures of choosing process parameters for induction hardening of steels and cast irons identical?
Although induction surface hardening of cast irons have many similarities to induction hardening of carbon steels, there are some appreciable differences[1]. For example, due to relatively high silicon contents, commercial cast irons should be considered as at least ternary Fe-C-Si alloys. As a result, the critical temperatures of cast irons differ from those that show in Fe-Fe3C phase diagram. Both the eutectoid and eutectic reactions on the Fe-C-Si diagram occur at higher temperatures and over a range of temperatures that increases with an increase of both carbon content and silicon content.
Induction surface hardened iron castings usually have a well-defined case depth with a relatively shallow transition zone. The temperature range of 860 to 960°C is typical for induction hardening of gray, malleable, ductile and compacted graphite iron castings. Besides carbon and silicon, all commercial cast irons also have other intentionally added alloying elements and residual impurities that might affect critical temperatures. The possible variation of critical temperatures should be kept in mind when choosing hardening parameters.
The ability of gray irons to be hardened depends on the type of matrix (i.e., ferritic, ferritic-pearlitic, or pearlitic) and the amount, size, shape, and distribution of the graphite flakes. A pearlitic matrix provides a better response to heat treating by induction. The graphite flakes should be fine, uniformly distributed, and randomly oriented (type A fine graphite flakes are preferable). Gray irons having a ferritic matrix are not very suitable for induction hardening.
60
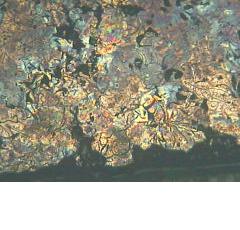
Gray iron’s brittleness may pose certain challenges to induction heat treaters, due to a tendency to crack during rapid heat-up or severe cooling. Part design, casting quality, process parameters, and prior microstructure are among the factors to be considered. Preheating and “soft quenching” are often used to reduce thermal stresses and shocks. On the other hand, there have been many cases where gray irons have been hardened without cracking using an intensive heating (heat time less than 3 sec.) and severe water quench.
Remember that the size, shape, dispersion, and amount of graphite flakes affect not only mechanical properties, but also electrical, magnetic, and thermal properties of gray iron castings. The effects of changes to these properties should be considered when modeling an induction process.
In contrast to gray irons, ductile or nodular irons contain carbon particles in the form of graphite nodules instead of flakes. Induction hardening is usually applied to the martensitic, pearlitic, and, to a lesser extent, pearlitic-ferritic grades of ductile iron. Martensitic ductile irons require the lowest hardening temperatures and shortest heat-up times. Because ductile irons are inherently strong, they can handle much greater stresses during heating and quenching without cracking than gray irons. Note, however, that although the graphite nodules serve as crack arresters, they provide no guarantee that a casting will not crack during intensive heating or/and severe quenching. Caution, common sense, and experience should be exercised when choosing parameters for induction hardening of ductile iron, particularly if it has a high phosphorous content.
Other “unfriendly” prior microstructures include those having alloy segregation or large clusters of graphite. When located near a gray iron casting’s surface, large graphite flakes or clusters of flakes having a preferred orientation serve as stress raisers (Fig. 2), making the casting more susceptible to crack development during rapid heating (particularly at frequencies of 30 kHz and higher) and severe cooling. When hardened, these cast irons also
may develop soft spots where the large clusters are located.
Also to be avoided are eutectic carbides, caused by insufficient time at austenitizing temperature, that can encourage cracking in all types of cast irons suitable for induction hardening. The propensity for cracking derives from the complex stress distribution created during quenching. Other potentially crack-prone structures include dendritic structures, and the undercooled graphite structure that results from rapid solidification and insufficient inoculation.
The same type of cast iron purchased from different suppliers can have appreciably different properties. Casting process variables such as the
solidification rate and amount of residual elements may cause those differences. Special attention should be paid to combinations of elements, such as carbon and silicon, sulfur and manganese that may have a synergistic effect. It is also important that close control be maintained over the CE (carbon equivalent) and TC (total carbon) values.
The proper recipe for the induction hardening process includes an appropriate austenitizing temperature and time, which are functions of the cast iron grade and specifics of the heating and quenching portions of the cycle. The austenitizing temperature should be sufficiently high and the austenitizing time sufficiently long to ensure that all required diffusion-type processes are completed, so that the martensitic structure formed during quenching will contain no “ghost pearlite” or “excessive amount of free ferrite.” This will
61
assure avoiding formation of a complex martensitic-pearlitic structure containing unacceptably large islands of “free ferrite”.
Heat treaters with extensive experience in induction hardening cast irons may have sometimes noticed that seemingly identical cast iron parts — parts having the same chemical composition, geometry, grain size, and microstructure, produced at the same foundry, and even coming from the same lot or batch — have different responses to induction hardening. Under identical heating and quenching conditions, some castings may process very easily, while others may have substantial cracking. One reason for this behavior is a phenomenon called “age strengthening.”
In the first systematic experimental study of this phenomenon, Nicola and Richards reported [2] that aging at room temperature for about 60 days can strengthen gray cast irons by up to 12%. Approximately 87% of the evaluated cast irons revealed this effect. The tensile strength-to-hardness ratio also increases because the Brinell hardness does not change with time.
Age strengthening occurs in both cupola and induction melted irons. Interstitial (free) nitrogen appears to be a controlling factor in determining whether aging will take place [2]. Therefore, age-strengthened castings would be less likely to crack when exposed to thermal gradients during heating and quenching. This may also explain the traditional foundry practice in the past of storing some gray iron castings for several months before heat treating them.
In order to ensure the reliability of a cast iron hardening process, it is important to conduct a run-off study using relatively new or “fresh” parts. If during lab development or run-off there have been used the parts that were on the shop floor for sometime then those parts might be “self age strengthened” resulting in reduced probability of cracking and leading to a dangerously optimistic result. However, during normal production environment, in order to minimize a required floor space to store parts, a time between casting and heat treating most likely will be a relatively short and age strengthening will not take place. As a result of that, experiencing a cracking problem that he/she did not observe during lab development or run-off study might suddenly unpleasantly surprise heat treaters.
Other challenges that can occur induction hardening of complex-shapes cast iron parts are also discussed in Handbook of Induction Heating [1].
Conclusion
Space limits discussion only to selected materials presented above. It is certainly not possible to mention even a small portion of the materials presented in this 800-page Handbook of Induction Heating that covers a broad range of induction heating aspects [1]. For example, Chapter 2 provides an overview of industrial applications of induction heating. Chapter 3 delves into the theoretical background and specifics of electromagnetic and thermal phenomena. An exceptionally useful part of chapter 3 is the section on mathematical modeling and computation. There are some guidelines provided for induction heating analysts in order to make the right choice regarding the advantages and limitations of the methods that are most often used for modeling induction heating processes. A description and comparison of the different numerical techniques including the finite element method (FEM), boundary element method (BEM), finite difference method (FDM) and mutual inductance method (MIM), is presented to allow the user to make an educated decision with respect to which computational technique is the best to use in a certain application.
A discussion of different coupling techniques for the electromagnetic–thermal problem (i.e., two-step approach, indirect coupling and direct coupling) is presented in this section as well. This will be helpful for the reader to be aware of the dangerous pitfalls in
62
using some of the commercially available software for computation of the induction heating process.
One crucial requirement in the verification of theoretical calculations is the ability to accurately measure the temperature. Chapter 4 gives a comprehensive description of the different methods of temperature measurement available ranging from temperature sensitive paints to advanced multi-color infra-red optical systems. From a practical standpoint, the care and maintenance of temperature measuring systems is discussed here with special emphasis on the specifics of induction applications, as well as, typical measurement errors and methods to prevent them.
Chapter 5 describes a wide range of methods of induction heat treating of metals, with emphasis on surface and through hardening, tempering, stress relieving, annealing, etc. This includes, but is not limited to camshafts, crankshafts, axle shafts, gears and other critical components. Concrete engineering recommendations and guidelines to choose optimal process parameters, design criteria and machine concepts are presented here. There is a detailed discussion regarding inductor design, coil fabrication, spray quenching, formation of stresses, crack development prevention, coil maintenance, contradictions and intricacies of using magnetic flux concentrators, as well as different aspects of metallographic sample preparation and principles of microscopic analysis.
Chapter 6 provides an overview of special applications such as brazing, soldering, bonding, shrink fitting, cap sealing, etc. A sufficient background to determine the effectiveness of using induction for other special applications is also provided here.
Chapter 7 provides detailed descriptions of applications that belong to the group of induction mass heating. Mass heating involves heating of ferrous and non-ferrous bars, billets, rods, blooms, slabs, plates and sheets prior to rolling, forging, extrusion, up-setting, etc. Numerous important electromagnetic and thermal effects are described since a knowledge of these effects is essential for a successful equipment design. Special consideration is devoted to induction heating of tubes, pipes, wires, cables, ropes and strips for a variety of applications including bending, drying, galvanizing, galvannealing, galvaluming, etc. Customer requirements may vary from the necessity to heat the entire workpiece, or a certain portion of the workpiece, for example bar end heating or slab end or edge re-heating. A description of some of the unique applications of induction heating such as aluminum slug heating for semi-solid forming and induction re-heating for the world’s largest carbon steel slabs, will be given here as well.
One of the most critical parts of any induction heating machine is the power supply. The old saying: “It only takes a mouse in the elephant show to ruin the whole circus” can be re-phrased as “It only takes a bad power supply to ruin the most sophisticated induction heating machine”. The power supply affects practically all critical parameters of the induction heating system, including reliability, maintainability, compactness, system flexibility, energy efficiency and cost. Many different power supply types and models are available to meet the heating requirements of a nearly endless variety of induction heating and heat treating applications. Chapter 8 rounds out the materials intended to be discussed in this handbook by providing a comparison of the different types of power supplies used for induction heating. Most types of inverters used in induction heating are discussed with coverage of circuit topology, operating characteristics and load matching. The characteristics of high frequency transformers are discussed here as well.
Special attention has been paid to quality assurance, process control and monitoring. This includes, but is not limited to, a discussion on the basic principles of “close-loop” and “open-loop” control approaches, various control modes, PLC controllers, energy monitoring, “signature” monitoring, etc. Subsequent sections of chapter 8 enter into a discussion of power
63
supply maintenance, protective devices, specifics of cooling, power/energy quality, harmonics and safety principles.
Handbook of Induction Heating [1] can be purchased from www.dekker.com or www.inductoheat.com.
References
[1]Rudnev,V., Loveless,D., Cook,R., Black,M.: Handbook of Induction Heating. Marcell Dekker, NY, 2003, 800pp.
[2]Nicola,W., Richards,V.: Age strengthening of gray cast iron. An AFS Research Report 2000.
Author
Dr.Rudnev, Valery Inductoheat, Inc.
32251 N.Avis Dr., Madison Heights, Michigan 48071 USA E-mail: rudnev@inductoheat.com
64