
Шеремет Проектирование методики сборки машин
.pdf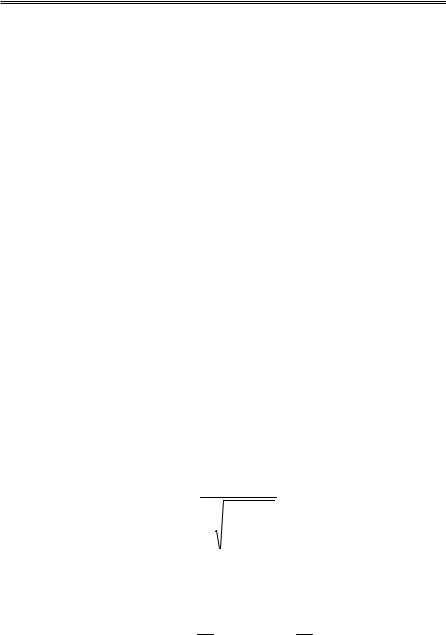
31
Коефіцієнт ризику t∆ вибирається з таблиць значення функції Лапласа Ф(t) у залежності від узятого ризику Р.
При нормальному законі розподілу відхилень і рівноймовірному їхньому виході за обидві границі поля допуску значення Р зв'язано із значенням Ф(t) формулою
Р = 100[1 – 2Ф(t)] %.
Ряд значень коефіцієнта t∆ наведений нижче:
Ризик Р, % |
– |
32,00 |
10,00 |
4,50 |
1,00 |
0,27 |
0,10 |
0,01 |
Коефіцієнт t∆ |
– |
1,00 |
1,65 |
2,00 |
2,57 |
3,00 |
3,29 |
3,89 |
Коефіцієнт відносного розсіювання відхилень λ2 для ряду законів розподілу можна взяти наступним: 1/9 для нормального (Гаусса); 1/6 для трикутника (Сімпсона); 1/3 для рівної ймовірності.
При наявності фактичних даних про закон розподілу відхилень значення коефіцієнта λ2i може бути розраховане за ГОСТ 19415-74.
4. Середнє значення допуску складових ланок Тср обчислюють у такий спосіб:
при розрахунку методом максимуму–мінімуму
|
T∆ |
; |
|||||
Tср = m−1 |
|||||||
|
|||||||
|
∑ |
|
ξi |
|
|
|
|
|
|
|
|
||||
|
|
|
|
||||
|
i=1 |
|
при ймовірнісному методі розрахунку
Tср = |
T∆ |
. |
|
m−1 |
|||
|
|
||
t∆ |
∑ξ2i λ2i |
|
|
|
i=1 |
|
5. Граничні відхилення i-ї ланки esi та eii обчислюють за формулами
esi = emi + T2i ; eii = emi − T2i .

32
6. Координату середини поля розсіювання замикальної ланки визначають за формулою
m−1
emω∆ = ∑ξi emω∆ .
i=1
7.Координата центра групування відхилень замикальної ланки
m−1
= ∑ ξ
M(x)∆ iemω∆
i=1
+ α ξi ωi . 2
8. Коефіцієнт відносної асиметрії i-ї ланки
αi = M(xi )− emωi .
ωi
2
9. Поле розсіювання замикальної ланки ω∆ обчислюють у такий спосіб:
при розрахунку методом максимуму–мінімуму
m−1
ω∆ = ∑ ξi ωi ;
i=1
при ймовірнісному методі розрахунку
m−1
ω∆ = t∆ ∑ξ2i λ2i ω2i .
i=1
Відносне середньоквадратичне відхилення
λi = 2σi , ωi
де σi – середньоквадратичне відхилення.

33
10. Найбільшу можливу компенсацію δк розраховують за формулою
|
|
|
δ |
к |
= Т′ |
− Т |
∆ |
. |
|
|
||||||
|
|
|
|
|
|
∆ |
|
|
|
|
|
|
||||
Величина поправки |
|
|
|
|
|
|
|
|
|
|
|
|
|
|
||
|
|
|
δк |
|
|
m−1 |
|
|
|
|
|
|
|
|||
∆ |
к |
= |
|
+ |
∑ |
ξ |
em′ − em |
∆ |
. |
|||||||
|
||||||||||||||||
|
2 |
|
|
|
i |
|
i |
|
|
|
||||||
|
|
|
|
|
|
|
|
i=1 |
|
|
|
|
|
|
|
|
Число ступенів нерухомих компенсаторів |
|
|||||||||||||||
|
|
|
|
|
|
|
|
T ′ |
|
|
|
|
|
|||
|
|
|
N = |
|
|
∆ |
|
|
, |
|
|
|||||
|
|
|
|
T∆ − Tк |
|
|
|
де Тк – допуск на виготовлення нерухомого компенсатора.
3.7. Використання теорії розмірних ланцюгів для визначення кількості і розмірів компенсаторів площинних розмірних ланцюгів
У реальних вузлах суднових машин і механізмів, технологічного устаткування й оснащення рідко зустрічаються умови, коли необхідне взаємне розташування деталей вузла може бути забезпечено методом повної взаємозамінності. Найчастіше це розташування деталей доводиться забезпечувати методом пригону чи методом використання компенсаторів.
Розрахунок кількості компенсаторів та їхніх розмірів може бути проведений у наступній послідовності:
1.Аналізуючи креслення механізму чи вузла і технічні умови на його роботу, необхідно виявити розмірний ланцюг цього механізму або вузла, побудувати схему розмірного ланцюга та визначити кількість ланок m розмірного ланцюга (включаючи замикальну ланку).
2.Виявити замикальний розмір А∆ і вимоги, поставлені до нього.
3.Виявити елемент Ак (ланка розмірного ланцюга), за допомогою якого буде виконуватися компенсація взаємного розташування деталей (забезпечуватися необхідна точність замикальної ланки А∆).

34
4.Задатися припустимим відсотком ризику Р, %, виходу бракованих виробів і визначити відповідний йому коефіцієнт t∆.
5.У залежності від умов виробництва деталей задати величину коефіцієнта відносного розсіювання λ2i для кожного розміру.
6.За робочими кресленнями деталей знайти номінальні значен-
ня розмірів розмірного ланцюга та їх верхні esi і нижні eii відхилення. Знак відхилень ураховувати обов'язково.
7.За схемою розмірного ланцюга визначити передатні відношення ξi кожної з його ланок.
8.Занести отримані значення в таблицю, що наведена нижче.
Дані таблиці відповідають рис. 3.1.
Позначення |
Передатне |
Номінальне |
|
Верхнє |
Нижнє від- |
Відносне |
відношен- |
значення |
|
відхилен- |
хилення eіi |
розсіювання |
|
розміру |
ня ξi |
розміру |
|
ня esi |
|
2 |
|
|
|
|
|
λ i |
|
|
|
|
|
мм |
|
|
|
|
|
|
|
||
|
|
|
|
|
||
А∆ |
– |
0 |
|
0,20 |
0,05 |
1/9 |
А1 |
–1 |
22,75 |
|
0,25 |
–0,25 |
1/9 |
А2 |
–1 |
150,00 |
|
0 |
–0,46 |
1/9 |
А3 |
–1 |
22,75 |
|
0,25 |
–0,25 |
1/9 |
А4 |
–1 |
10,00 |
|
0,10 |
–0,10 |
1/9 |
А5 |
1 |
0,25 |
|
0,05 |
–0,05 |
1/9 |
А6 |
1 |
218,00 |
|
0 |
–0,52 |
1/9 |
А7 |
1 |
0,25 |
|
0,05 |
–0,05 |
1/9 |
А8 |
–1 |
8,00 |
|
0,10 |
–0,10 |
1/9 |
А9 |
–1 |
5,00 |
|
0,025 |
–0,025 |
1/9 |
9. Підрахуватидопускиланокрозмірноголанцюгазазалежностями
Ti = esi − eii ; T∆ = es∆ − ei∆ .
Допуск на виготовлення компенсатора має бути значно меншим від допуску замикальної ланки.
10. Номінальний розмір компенсатора
m−1
А∆ − ∑ξi Аi
Aк = |
i=1 |
. |
|
ξк |
|||
|
|

35
11. Розрахунковий допуск замикальної ланки: при m ≤ 4
m−1
T∆ = ∑ ξi Ti ;
i=1
при m > 4
m−1
T∆ = t∆ ∑ξ2i λ2i Ti2 .
i=1
12.Необхідна величина компенсації: при m ≤ 4
m−1
δ′к = ∑ ξi Ti − ξк Тк ;
i=1
при m > 4
m−1
δ′к = t∆ ∑ξ2i λ2i Ti2 − ξ2кλ2кТ2к .
i=1
13.Число ступенів компенсатора
Nк = |
δ′к |
|
. |
Т∆ − |
|
||
|
Тк |
14. Беремо Nк рівним найближчому більшому числу.
15. Крок ступенів компенсатора
Тст = δ′к .
Nк

36
16. Координати середин ланок
em |
= |
esi + eii |
; |
em |
∆ |
= es∆ + ei∆ . |
|
||||||
i |
2 |
|
|
2 |
||
|
|
|
|
|
17. Розрахункова координата середини компенсації
|
|
m−1 |
|
|
|
|
|
|
em′ |
= |
∑ |
ξ em |
− ξ |
к |
em |
к |
. |
∆ |
|
i i |
|
|
|
i=1
18.Поправка на координату середини поля допуску компенсатора першого ступеня
∆ |
к |
= |
δ′к − Т∆ + em′ |
− em |
∆ |
. |
|
|
|
2 |
∆ |
|
|
||
|
|
|
|
|
|
|
19. Розрахунковий розмір компенсатора першого ступеня
A′к = Ак + ∆ к .
20. Розрахунковий розмір компенсатора другого ступеня
А′′ |
= А′ |
+ Т |
ст |
. |
к |
к |
|
|
Розрахунковий розмір компенсатора i-го ступеня
Аiк = Аiк−1 + Тст .
21.Верхнє креслярське відхилення компенсатора і-го ступеня (і =
=1...N)
esкi = Aiк − Aк + T2к .
22.Нижнє креслярське відхилення компенсатора і-го ступеня (і =
=1...N)
eiк = Aiк − Aк − T2к .

37
23. Розмір компенсатора і-го ступеня на кресленні (і = 1...N)
Ак r = Aiк; + esк; − eiк .
Щоб полегшити розрахунки і забезпечити можливість швидкого розрахунку ряду варіантів задоволення точності замикальної ланки (при зміні точності й умов виготовлення деталей вузла), необхідно розробити відповідну програму для ЕОМ.
4. РОЗРОБКА ТЕХНОЛОГІЇ ЗАГАЛЬНОГО СКЛАДАННЯ ВИРОБІВ
4.1. Послідовність виконання складальних операцій
Інформаційною базою при встановленні послідовності складання є типові ТП і стандарти на ТО. Послідовність складання визначається конструкцією виробу і методами досягнення необхідної точності. Тому виняткове значення має процес відпрацьовування виробу на технологічність.
Прості складальні одиниці звичайно мають одноваріантну послідовність уведення деталей у ТП складання, складні – різноманітну. В останньому випадку технолог зустрічається з необхідністю вибору оптимального варіанта послідовності складання.
Установлення послідовності складальних робіт починається з визначення базової деталі, від якої залежить положення всіх деталей, що входять у СО. Роль базової деталі може виконувати інша СО. Порядок складання встановлюють з огляду на можливість і зручність монтажу наступних деталей і СО. Кожна раніше приєднана деталь (СО) не повинна перешкоджати подальшому складанню.
Деталі і СО, функціонально більш важливі в машині, бажано монтувати на початкових стадіях складання, передбачивши заходи проти можливих їхніх пошкоджень при наступному приєднанні менш відповідальних деталей. Це також стосується деталей, розміри яких

38
є загальними ланками декількох, паралельно зв'язаних розмірних ланцюгів.
Паралельно з визначенням послідовності складання розробляють технологічну схему складання. На рис. 4.1 зображено креслення розподільного вала з регулятором, а на рис. 4.2 його технологічна схема складання. На схемі деталі і СО умовно зображують у вигляді прямокутників, у які заносять шифр деталей, кількість їх у СО та найменування. Схема складання наочно показує послідовність уведення деталей і СО в ТП, місце операції контролю, можливість організації паралельного виконання робіт, допомагає оцінити технологічність конструкції.
K61-2015
M-0609
K51-10 K11-10
M-0602
M-0605
A |
|
|
1M-0529 |
|
|
1M-0603 |
1M-0501 |
1M-0510 1M-0509 |
M-0503 |
||
1M-0504 |
1M-0505 N208 |
|
1M-0528 |
K71-0205 |
|
M-0502 |
|
|
Вигляд А |
|
|
|
|
M-0661
Закернити у трьох точках
M-0629
M-0606
M-0604a
Рис. 4.1. Розподільний вал з регулятором

Гайка
10509-М 1
Шайба
10510-М 1
Пружина
20605-М
Шплінтрозвідний
22015-61 К
Шайба
210-51 К
Палецьвантажу
20605-М
Муфта
10603-М 1
Гайка
10503-М 1
Шайба
10504-М 1
вала Шпонкарозподільного
10528-М 1
Храповик
10529-М 1
Кільце
10505-М 1
Шарикопідшипник№208
1
1 |
|
|
|
|
|
|
|
|
|
|
|
|
|
|
|
|
|
|
|
|
|
|
розподільногоГрупа регуляторомзвала |
|
|
|
|
|
|
|
|
|
|
|
|
|
|
|
|
|
|||
а0501-М1.ск |
|
|
|
|
|
|
1 |
|
|
|
1 |
|
|
|
|||||||
|
|
|
|
|
|
|
|
|
|
|
|
||||||||||
|
|
|
|
|
|
|
|
|
|
1 |
|||||||||||
|
|
|
|
|
|
|
|
|
|
|
|
|
|
|
|
|
|
||||
|
|
|
|
|
|
|
|
|
|
|
|
|
|
|
|
|
|
|
|
|
|
|
|
|
|
|
|
|
|
|
|
|
|
|
|
|
|
|
|
|
|
|
|
|
|
|
|
|
|
|
|
|
|
|
|
|
|
|
|
|
|
|
|
|
|
|
|
|
|
|
|
|
Контроль |
|
|
|
|
упорнийГвинт |
|
|
|
пружиниВісь |
|||||
|
|
|
|
|
|
|
|
|
|
|
|
|
0629-М |
|
а0604-М |
||||||
|
|
|
|
|
|
|
Контроль |
|
|
|
|
|
|||||||||
|
|
|
|
|
|
|
|
|
|
|
|
|
|
|
|
|
|
|
|
|
|
|
|
|
|
Підгрупавантажу |
|
|
|
|
|
|
|
|
|
|
|
|
|||||
|
|
1 |
|
|
1ск.1М-0601 |
|
|
|
|
|
|
|
|
|
|
|
|
||||
|
|
|
|
|
|
|
|
|
|
|
|
|
|
|
|
|
|
|
|
|
|
|
|
|
|
|
|
|
|
|
|
|
|
|
|
|
|
|
|
|
|
|
|
|
|
|
|
|
|
|
Контроль |
|
|
|
|
|
|
|
|
|
|
|
|
|
|
|
|
|
|
|
|
|
|
|
|
|
|
|
|
|
|
|
|
|
|
|
|
1 |
|
|
|
|
|
|
|
|
|
|
|
|
|
|
|
|
|
|
|
|
|
|
|
|
вала |
|
|
|
|
|
|
|
|
|
|
|
|
|
|
|
|
|
|
|
|
|
|
|
|
|
|
|
Штифтциліндричний |
|
|||||||||||
|
|
|
|
|
|
1 |
|
|
|
|
|
К71-0205 |
|
||||||||
|
Підгрупа розподільного |
|
|
|
|
|
|
|
|
||||||||||||
1 ск. М-0501а |
|
|
|
|
|
|
|
|
|
|
|
|
|
|
|
|
|
||||
|
|
|
|
|
|
|
|
|
|
|
|
|
|
|
|
|
|
|
|
|
|
|
|
|
|
|
|
|
|
|
|
|
|
|
|
|
|
|
|
|
|
|
|
|
|
|
|
|
|
|
Контроль |
|
|
|
|
|
|
|
|
|
|
|
|||
|
|
|
|
|
|
|
|
|
|
|
|
|
|
|
|
|
|
|
|
|
|
|
|
|
|
розподільноговала |
|
|
|
|
|
|
|
|
|
|
|
||||||
|
|
|
|
|
Підгрупашестерні |
|
|
|
|
|
|
|
|
|
|
|
|||||
|
|
|
1 |
|
2ск.1М-0502 |
|
|
|
|
|
|
|
|
|
|
|
|||||
|
|
|
|
|
|
|
|
|
|
|
|
|
|
|
|
|
|
|
|
|
|
|
|
|
|
|
|
|
Контроль |
|
|
|
|
|
|
|
|
|
|
|
|||
1 |
|
|
|
|
|
|
|
|
|
|
|
|
|
|
|
|
|
|
|
|
|
|
|
|
|
|
|
|
|
2 |
|
|
|
2 |
|
|
|
|
|
||||
1 М-0501а |
Розподільний вал |
|
|
|
|
|
|
|
Гайка АМ10 |
|
|
|
|
Шайба стопорна |
|||||||
|
|
|
|
|
|
К 11-10 |
|
|
М-0609 |
|
|||||||||||
|
|
|
|
|
|||||||||||||||||
|
|
|
|
|
|
|
|
|
|
|
|
|
|
|
|
|
|
|
|
|
|
|
|
|
|
|
|
39 |
|
|
|
||||
|
Вантаж |
|
|
|||
|
М-0601 |
|
|
|||
|
|
|
|
|
|
регулятором |
|
1 |
|
|
|
|
|
|
|
|
|
|
|
|
|
М-0602 |
Вилка |
|
вала з |
||
|
|
|
|
|
складаннярозподільного |
|
|
|
|
|
|
|
|
|
0602-М.Зеб |
Підгрупавилки |
|
|||
|
2 |
|
|
|
|
|
|
|
|
|
|
|
4.2. Технологічна схема |
|
|
|
|
|
|
|
1 |
|
|
|
|
||
|
|
|
Шестерня розподільного вала |
|||
|
1 М-0502 |
|
||||
|
|
|
|
|
|
|
|
|
|
|
|
|
Рис. |

40
4.2. Механізація та автоматизація, оцінка ефективності технологічного процесу складання
Механізація та автоматизація складального процесу. Складаль-
ний процес важче піддається механізації, ніж механічна обробка. У дрібносерійному виробництві підвищення продуктивності праці досягають застосуванням механізованого ручного інструменту: пневмо- і електрогайковертів, тисків, шліфувальних машинок тощо.
У масовому виробництві є численні приклади добре налагоджених автоматизованих складальних процесів. Труднощі автоматизації складання виробів, що випускаються серійно, пов'язані з необхідністю переналагодження устаткування. Таке устаткування повинно відповідати вимогам мінімальних витрат часу на переналагодження і низької вартості змінного оснащення.
Складальне устаткування для серійного виробництва, яке легко переналагоджується, у даний час доцільніше комплектувати з застосуванням промислових роботів (ПР), що здатні виконувати технологічні і допоміжні операції та переходи. Наведемо дві основні схеми такого компонування: одна з них передбачає використання од- ного-двох ПР, друга – стількох ПР, скільки є робочих позицій складального устаткування.
Складальний комплекс (СК), побудований за першою схемою, здійснює складання в залежності від складності виробу на одній чи декількох позиціях – пристроях (рис. 4.3,а). Основні переходи (з'єднання деталей і СО) та складання, установлення базових деталей у пристрої, видалення зібраного виробу виконуються послідовно в автоматичному режимі спеціалізованими швидкозмінними інструментами (складальними головками) і захоплювачами. Уже є значний досвід створення інструменту, яким можна виконувати технологічні та допоміжні переходи; у цьому випадку можливе переключення транспортно-завантажувального механізму. Набір інструменту визначається складом складальних переходів, його готують заздалегідь і встановлюють у гнізда інструментального магазина при налагодженні СК на складання конкретного виробу.
Побудований за першою схемою СК відрізняється високою універсальністю. Продуктивність складання залежить від складності виробу (числа і конструкцій вхідних деталей, виду з'єднань, вимог до з'єднань і т. д.). Для виробів середньої складності, зібраних з п'я-