
эксплуатация
.pdf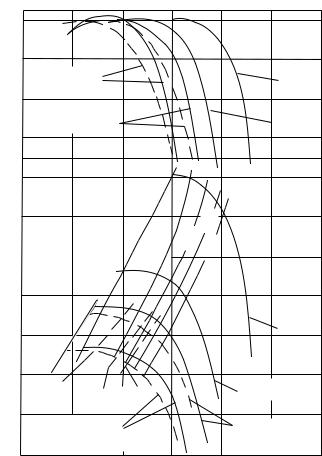
|
|
|
|
|
|
|
|
|
|
|
|
|
|
Снижение |
КПД компрессора |
||||||
ηк |
|
|
|
|
|
|
|
|
|
|
|
|
|||||||||
|
|
|
|
|
|
|
|
|
|
|
|
|
|
происходит из-за роста потерь на |
|||||||
0 ,8 |
ηК |
|
|
|
|
|
|
|
|
|
|
|
|||||||||
0 ,7 |
|
|
|
|
|
|
|
|
|
|
|
|
трение |
(влияние |
шероховатости |
||||||
|
|
|
|
|
|
|
|
|
|
|
|
отложений), |
перераспределения |
||||||||
|
|
nк = 2 0 0 0 0 |
|
|
|
|
|
|
|||||||||||||
|
|
|
|
|
|
2 8 0 0 0 |
скоростей |
движения |
воздуха и |
||||||||||||
0 ,6 |
об/мин |
|
|
|
|
|
|
||||||||||||||
|
|
|
|
|
|
|
|
|
|
|
|
|
|
отклонения |
от |
расчетных значе- |
|||||
|
|
2 2 0 0 0 |
|
|
|
|
|
|
|
|
|
||||||||||
|
|
|
|
|
|
|
|
|
2 4 0 0 0 |
ний |
углов |
атаки. |
Проведенные |
||||||||
0 ,5 |
|
|
|
|
|
|
|
|
|
|
|||||||||||
|
|
|
|
|
|
|
|
|
|
|
|
исследования |
по |
изучению раз- |
|||||||
πк |
π |
|
|
|
|
|
|
|
|
|
|
|
|||||||||
|
|
|
|
|
|
|
|
|
|
|
дельного влияния шероховатости |
||||||||||
1 ,8 |
К |
|
|
|
|
|
|
|
|
|
|
|
|||||||||
|
|
|
|
|
|
|
|
|
|
|
|
|
|
и суммарной толщины слоя пока- |
|||||||
1 ,7 |
|
|
|
|
|
|
|
|
|
6 |
|
|
зали, |
что |
снижение |
КПД ком- |
|||||
|
|
|
|
|
|
|
0 |
|
7 |
|
|
||||||||||
|
|
|
|
|
|
|
|
|
8 |
, |
|
|
|
|
|
|
|
|
|
|
|
|
|
|
|
|
|
|
|
|
8 |
0 |
|
|
прессора происходит практически |
||||||||
|
|
|
|
|
|
|
|
|
, |
7 |
4 |
|
|
||||||||
|
|
|
|
|
|
|
|
0 |
, |
|
|
||||||||||
|
|
|
|
|
|
|
|
= |
|
0 |
7 |
|
|
|
|
|
|
|
|
|
|
1 ,6 |
|
|
|
|
|
η |
к |
|
|
, |
|
|
пропорционально |
росту |
относи- |
||||||
|
|
|
|
|
|
|
|
0 |
|
|
|||||||||||
1 ,5 |
|
|
|
|
|
|
|
|
|
|
|
|
тельной шероховатости. |
Величи- |
|||||||
|
|
|
|
|
|
|
|
|
|
|
|
на относительной шероховатости |
|||||||||
|
|
|
|
|
|
|
|
|
|
|
|
|
|
||||||||
|
|
|
|
|
|
|
|
|
|
|
|
2 8 0 0 0 |
отложений |
в диффузоре |
состав- |
||||||
1 ,4 |
|
|
|
|
|
|
|
|
|
|
|
|
|||||||||
|
|
|
|
|
|
|
|
|
|
|
|
ляет обычно 0,004…0,006, фор- |
|||||||||
|
|
|
|
|
|
|
|
|
|
|
|
|
|
||||||||
1 ,3 |
|
|
|
|
|
|
|
|
|
|
|
|
мируется она в первые 50…100 ч. |
||||||||
|
|
|
|
|
|
|
|
|
|
|
|
работы и снижает КПД компрес- |
|||||||||
|
|
ηк= 0 ,7 8 |
0 ,7 6 |
|
0 ,7 4 |
|
|
|
2 4 0 0 0 |
||||||||||||
|
|
|
|
|
|
||||||||||||||||
1 ,2 |
|
|
|
|
|
|
|
|
|
|
|
|
сора |
на 6…9 %. Дальнейшее |
|||||||
|
|
nк= 2 0 0 0 0 об/мин |
|
|
|
|
2 2 0 0 0 |
уменьшение КПД до 20…30 % |
|||||||||||||
|
|
|
|
|
|
|
|
||||||||||||||
1 ,1 0 |
|
|
|
|
|
|
|
1 ,0 |
|
G ,кг/ |
может |
произойти |
в |
результате |
|||||||
|
0 ,5 |
|
|
|
|
|
|
|
|||||||||||||
|
|
|
|
|
|
|
|
||||||||||||||
|
|
|
|
|
|
|
|
|
|
|
|
|
GкК, кг/с |
роста толщины слоя. |
|
|
|||||
Рис. 1.7. Влияние загрязнений на характеристики |
|
|
|||||||||||||||||||
компрессора ТК-18 ( |
чистый компрессор; |
Как показали опыты, компрес- |
|||||||||||||||||||
сор с безлопаточным диффузором |
|||||||||||||||||||||
|
|
----- |
|
- отложения в проточной части |
менее «чувствителен» к влиянию |
||||||||||||||||
|
|
|
|
|
|
отл = 1,0 мм) |
|
|
|||||||||||||
|
|
|
|
|
|
|
|
заноса, |
хотя толщина слоя отло- |
||||||||||||
|
|
|
|
|
|
|
|
|
|
|
|
|
|
жений достигает иногда 3…4 мм. Так как занос изменяет характеристику компрессора, то происходит смещение и линии рабочих режимов. Линия рабочих режимов ТК, совпадающая при схеме СТК с расходной характеристикой дизеля, при загрязнении смещается в зону меньших расходов и меньших КПД компрессора, а граница зоны помпажа смещается влево.
Для количественной оценки влияния, которое оказывает занос проточной части компрессора на параметры работы дизеля, были проведены натурные испытания вспомогательных дизелей типа 8ВАН-22, 6ВАН-22, 625МТВН-40, 6Д50М с турбокомпрессорами VTR-150, -200, -250, ТК-30 в два этапа [2]. На первом этапе измерялись параметры работы дизелей и ТК после 500…2100 ч. эксплуатации на судне. На втором этапе компрессор разбирали, очищали от отложений, и испытания повторялись. Никаких изменений в органах и узлах дизеля не производилось, турбина не вскрывалась. Первый этап испытаний продолжался 2…3 ч. Таким образом, разница в техническом состоянии газовыпускных трактов дизелей и турбин была несущественной.
Полученные результаты позволили сделать следующие общие выводы.
11
1.Толщина слоя отложений в проточном части компрессора с течением вре-
мени стабилизируется. Для дизелей с πк ≤ 1,5 стабилизация происходит на уровне 2,0…2,5 мм; при πк > 2,0 стабилизация происходит на уровне 1,0…1,5 мм. Наиболее интенсивный рост отложений наблюдается в первые 50…100 ч. работы.
Причины стабилизации слоя отложений заключаются в следующем. Отложившиеся на поверхности компрессора частицы оказываются под воздействием давления воздушного потока, вызывающего сдвигающие напряжения на поверхности отложений. Вначале силы сцепления между частицами масла и металлической поверхностью (адгезия) превосходят силы сдвига. По мере нарастания слоя отложений на лопатке силы сцепления между частицами (силы когезии) уменьшаются и скорость течения потока вследствие уменьшения площади проходного сечения увеличивается, поэтому при определенной толщине слоя отложений наступает равновесие между силами когезии и силами сдвига. Частицы масла и пыли, попадающие на такой слой, уже не удерживаются силами сцепления, и поток воздуха сдувает их.
2.Снижение КПД компрессора на 1 % приводит к уменьшению πк на 0,4…0,45 %, росту температуры газов на 0,6…0,7 % и удельного расхода топли-
ва на 0,2…0,3 % (в зоне πк < 1,5). По мере роста πк это влияние увеличивается и в зоне πк ≥ 2,5 (дизели типа ЧН 16/17, MAN 9KZ 70/I20E и др.) изменение КПД компрессора (независимо от типа диффузора) на 1 % вызывает изменение πк на 0,65…0,7 %, температуры газа на 0,8…0,85 %, удельного расхода топлива на
0,4…0,6 %.
3. Кривые динамики изменения параметров работы дизелей качественно совпадают с кривыми темпа роста отложений в компрессоре и подтверждают вывод об определяющем влиянии начального периода эксплуатации.
2 ОЧИСТКА ГТН В УСЛОВИЯХ ЭКСПЛУАТАЦИИ
2.1Очистка фильтров
Впроцессе эксплуатации всасывающие воздушные фильтры и шумоглушители, проточные части компрессора и турбины, а также поверхности теплообмена ГТН должны поддерживаться в чистоте. Для этого предусматриваются периодические очистки указанных элементов ГТН.
Очищать сеточные набивочные фильтры рекомендуется бензином, осветительным керосином, дизельным топливом, сульфидным раствором, любым другим маслорастворяющим веществом, продувать влажным паром и сжатым воздухом.
12
Очистка секций фильтра проводится в ваннах с предварительным замачиванием в течение 30…60 мин. Затем интенсивными движениями фильтр прополаскивают. Очень хорошие результаты дает промывка фильтров в специальных моечных машинах (типа стиральных). Промытый растворителем фильтр обдувают сжатым воздухом или паром и просушивают.
Очистка фильтров только при помощи продувания паром или воздухом с избыточным давлением 2…3 бар может рекомендоваться лишь в случае их незначительного рыхлого загрязнения.
У некоторых ГТН, в частности типа С-045, применяются мас-лоомываемые всасывающие воздушные фильтры «Вокес». Такие фильтры запрещается чистить керосином или дизельным топливом. Их рекомендуется промывать в указанных заводом-изготовителем растворителях или в любом другом растворителе с нейтральным углеводородом, содержащим эмульгирующий агент, например нефтяной сульфонат. После обработки растворителем фильтрующий элемент тщательно промывают в пресной воде (лучше теплой с температурой 60 °С) и просушивают теплым воздухом. После окончания очистки фильтрующие элементы погружают на 1 минуту в гель или в масло SAE-30. Примерно на 8…10 ч фильтр оставляют в теплом помещении для стекания лишнего масла, после чего он готов к сборке и работе.
Элементы шумоглушителя рекомендуется очищать бензином, керосином или другой маслорастворяющей жидкостью и затем продувать сжатым воздухом с избыточным давлением 2…3,5 бар в направлении, противоположном движению всасываемого воздуха.
2.2 Безразборная промывка ГТН
Периодические вскрытия и очистки проточных частей газотурбонагнетателей химическим или механическим способом позволяют восстанавливать первоначальные параметры их работы, но в промежутках между очистками ГТН и дизель работают в условиях, отличных от оптимальных. Поэтому желательно непрерывно поддерживать чистоту проточных частей ГТН на ходу без их вскрытия.
Такую возможность дает водопромывка проточных частей, которая основана на использовании ударного эффекта мелких капель воды. Рекомендуется применять чистую пресную воду, подогретую до 55…70 °С, без присадок либо с присадками моющих веществ. Испытания показывают, что результаты промывки чистой пресной водой и моющим раствором в некоторых случаях практически одинаковы. Подвод воды желательно осуществлять равномерно по периметру окружности, направление впрыска воды должно совпадать с направлением входа потока на рабочее колесо.
Непременным условием водопромывки ГТН является ее регулярность и начало применения лишь после проведения химической или механической очистки проточных частей не позже чем через 100…150 ч. для компрессора и
13
250…300 ч. для турбины. В процессе подачи воды на промывку должен обязательно осуществляться дренаж моечных отходов из корпусных частей ГТН.
Для получения лучшего распыливания вода на промывку газотурбонагнетателя должна подводиться под давлением. Часто для этой цели используется сжатый воздух с избыточным давлением до 4…5 бар. Подача воды на компрессор осуществляется перед вращающимся направляющим аппаратом, на турбину
– перед защитной решеткой или перед сопловым аппаратом.
Распыливание воды, впрыскиваемой в ГТН, механическое. Для этого используется вода, отбираемая из напорной магистрали (например, санитарной горячей мытьевой воды), или вода вытесняется в ГТН из сосуда при помощи сжатого воздуха (сжатый воздух может также использоваться и для повышения качества распыливания воды).
Водопромывка компрессора проводится обычно при работе дизеля с номинальной (эксплуатационной) нагрузкой. После окончания впрыска воды дизель должен проработать не менее 1 ч. без снижения нагрузки для осушения воздушного тракта.
Проточная часть турбины промывается при нагрузке дизеля не более 25 % от номинальной (эксплуатационной). После окончания подачи воды вывод дизеля на режим полной мощности осуществляется в течение приблизительно 10 мин. Подвод промывочной воды к турбине желательно контролировать визуально, используя для этого прозрачные шланги. После впрыска воды в компрессор или турбину обязательно контролируется эффект водопромывки. Показания приборов должны фиксировать возрастание значений параметров πк, nк, nд и pi а Тг должна снизиться. Если проточная часть турбины промылась хорошо, из дренажной трубки будет вытекать чистая вода.
Если одноразовый впрыск воды не дал заметного эффекта, процесс промывки повторяется с интервалом приблизительно 10 мин. Отсутствие положительного эффекта после троекратной попытки означает, что проточные части необходимо очистить механическим или химическим способом с разборкой ГТН.
Водопромывку проточных частей ГТН в настоящее время рекомендуют применять многие фирмы. Для этого в конструкциях ГТН предусматриваются специальные штатные устройства (которыми целесообразно снабжать и необорудованные газотурбонагнетатели).
Рекомендованная схема промывки компрессора ГТН фирмы «Броун-Бовери» показана на рис. 2.1. В систему входит специальный сосуд, различающийся емкостью для ГТН различных типоразмеров. Его заливают чистой пресной водой, или раствором моющего средства, и соединяют резиновым шлангом с компрессором перед впрыском воды. Вода вытесняется из сосуда воздухом за 4…10 с. Предусматривается возможность промывки компрессора также газойлем, но при этом обязательно применение дозирующего устройства и строгое выполнение фирменной технологии.
14

Рис. 2.1 Схема водопромывки компрессора ГТН типа VTR:
А — емкость для VTR-160; VTR-200 емкостью 0.3 л. для VTR-250, VTR-320 емкостью 0,5 л., для VTR-400, VTR-500 емкостью 1 л., для VTR-630, VTR-750, VTR-900 емкостью 2,5 л;
В – крышка; С – пусковая кнопка; D, W – трубы ф12х1,5
Оборудованные ГТН типа VTR имеют штатную трубку для подачи воды перед вращающимся направляющим аппаратом, в необорудованных ГТН эту трубку следует подвести самостоятельно.
Эта же фирма, называющаяся сейчас «ABB Turbo System», для своих ГТН в настоящее время категорически запрещает использование каких-либо растворителей или химических моющих препаратов. На рис. 2.2 показана схема промывки компрессора чистой водой, полностью аналогичная предыдущей.
Промывочная емкость 7 наполняется водой через соответствующую систему 4, 9, 11, 5 (уровень контролируется дренажным клапаном 6 – вариант 1) или вручную, путем снятия и последующего закрытия крышки сосуда 7. Предварительно нагрузка двигателя устанавливается на уровне не менее 80 % от номинальной для того, чтобы ротор ТК достиг достаточно высоких оборотов с целью повышения эффективности промывки. Открывается клапан 3 подачи воздуха к сосуду и затем производится впрыскивание воды в течение 10 сек. с помощью клапана 8 (вариант 1), или пусковой кнопки 10 (вариант 2).
15

2
К другому компрессору
Улитка
|
|
|
|
|
Вариант 1 |
|
|
|
|
|
Вариант 2 |
|
||
|
|
|||
|
|
|
|
|
|
|
|
|
|
Рис. 2.2 Схема промывки водой компрессоров фирмы «АВВ» 1-подача сжатого воздуха от улитки, 2-подача воды на промывку, 3, 5, 8, 9-запорные кла-
паны, 4-подвод воды к промывочному сосуду, 6-дренажный кран, 7-промывочный сосуд, 10кнопка впрыска воды, 11-воронка.
Для промывки турбины ГТН используется горячая пресная вода, отбираемая от санитарной системы. Патрубок-отборник воды соединяется резиновым шлангом с наконечником, вставляемым в газоход через штуцер для установки термометра. Количество воды, которая подается на промывку в течение 10…20 мин., зависит от размеров ГТН и составляет, например, от 8 литров для VTR320 до 60 для VTR-900.
Промывку турбины рекомендуется проводить через каждые 100 ч. работы дизеля, промывку компрессора – по обстоятельствам.
Внедрение и использование водопромывки проточных частей ГТН на судах различных пароходств дает положительные результаты, однако сведения по периодичности промывки несколько противоречивы. Так, компрессор рекомендуется промывать в одних случаях через каждые 24…48 ч. в других – через 100…150 или даже через 200 ч. работы дизеля. Промывка турбин рекомендуется через каждые 200…250 ч. работы дизеля, нижний предел относится, прежде всего, к случаям использования тяжелых сортов топлива. Противоречивость в периодичности промывки компрессоров в некоторой степени связана с конструктивными особенностями различных типов газотурбонагнетателей. Кроме того, это можно объяснить тем, что на различных судах отличается и качество воздуха в машинном отделении; улавливающая способность всасывающих воздушных фильтров и самих компрессоров также различна; в разной степени про-
16
является вероятность уноса смазочного масла компрессором из подшипниковой камеры и т. п. Кроме того, пока ни на одном судне не проводились длительные сравнительные испытания по определению эффективности водопромывки с различной периодичностью. Во всяком случае, опыт эксплуатации показывает, что периодичность водопромывки компрессоров менее чем через 24 ч. не оправдана.
Водопромывка проточных частей ГТН позволяет значительно увеличить время между двумя смежными очистками ГТН с их вскрытием (это и определяет в основном периодичность ревизии). С учетом надежности подшипников и регулярности водопромывки проточных частей компрессора и турбины срок ревизии в некоторых типах ГТН (VTR-400, VTR-750, TL и др.) может быть дове-
ден до 10 000–16 000 ч.
Химическая или механическая очистка проточных частей и поверхностей охлаждения корпусов ГТН и воздухоохладителей производится в случаях, когда в охлаждающую пресную воду попадает смазочное масло дизелей («Зульцер» RD76). В этих случаях целесообразно периодически на стоянках промывать всю систему охлаждения. Для этого рекомендуется вводить в систему 40…50 кг порошка моющего препарата МЛ-2, нагревать воду до 80 °С и при этой температуре промывать систему в течение одного дня (8…10 ч). Затем, отключив охлаждение вспомогательных дизелей, выпускают моющую воду, и систему заполняют свежей пресной водой. При отсутствии препарата МЛ-2 можно использовать иностранные препараты: «Гамлен-Сиклин», «Магнус», «Маритек корпорейшн» и др.
Охладители продувочного воздуха загрязняются масляными отложениями со стороны воздуха и илисто-ракушечными – со стороны воды. В водяных камерах встречаются иногда ракушечные отложения с грязевыми осадками (ржавчина, ил, графитовые выделения) до 10 мм толщиной. Очистка воздухоохладителей производится обычно через 5000…7000 ч. непрерывной работы дизеля. Этот срок зависит от района плавания судов и часто достигает 7000…10000 ч.
Бороться с загрязнением проточной части компрессора можно путем его промывки эффективными моющими средствами. В настоящее время на судах используют воду, керосин, растворы поверхностно-активных веществ (ПАВ) - «Чистра», «Синвал», RMC и др. [2, 5]. Такой широкий набор м. с. и противоречивые сведения об их эффективности свидетельствуют о недостаточной изученности процессов очистки компрессора.
2.3Очистка проточных частей ГТН твердым агентом
Впоследние годы все большее применение находит очистка турбин и компрессоров от отложений с помощью твердых очистителей, которые, как показал опыт очистки газотурбинных двигателей (ГТД), значительно эффективнее многих известных жидких моющих средств. Такие твердые очистители должны обладать хорошим очищающим свойством и не вызывать повреждений поверхно-
17
стей проточной части ТК. Этим требованиям в наибольшей степени удовлетворяют твердые растительные вещества, например скорлупа орехов, абрикосов, алычи и др. Наибольшее распространение получил твердый органический очиститель (ТООЧ) представляющий собой тонко размолотую смесь скорлупы грецкого ореха и абрикосовых косточек, размер частиц которой лежит в пределах 1,0…1,5 мм. Для очистки компрессоров, и 1,5…3,0 мм для очистки турбин
[1, 6, 8]. Химический состав крошки: C – 7 %, (Nг + Ог) – 43 %, Нг – 6 %, зола 1,4 %, S – 0,2 %. Влажность крошки около 7 %. Теплота сгорания – 19260 кДж/кг.
В качестве твердых очистителей могут применяться шелуха пшеницы, риса или сами зерна в дробленом виде. Вводимый агент сгорает и выбрасывается в виде золы. Перед подачей ТООЧ на турбину главного газотурбинного двигателя нагрузку снижают до среднего хода судна. Это делается во избежание чрезмерного повышения температуры газа при сгорании крошки. Турбины ГТН очищают на полном ходу.
Крошка подается специальной пневматической системой. Режим подачи выбирается экспериментально. Например, для ГТД [6] рекомендуются следующие параметры: скорость подачи крошки – 0,15 кг/с, относительный расход, по отношению к расходу воздуха, – 0,006…0,005; окружная скорость лопаток компрессора в момент подачи крошки ~ 200 м/с, лопаток турбин ~ 290…300 м/с.
Крошка, попавшая на горячие части газового тракта на них не откладывается, т. к. при температуре 550…700 °С полностью выгорает и выдувается. В свою очередь частицы, находящиеся в потоке могут не успеть выгореть, и будут выноситься слегка обуглившись.
Вся операция очистки выполнятся за 6…10 мин. При этом отпадает необходимость остановки двигателя и его просушки. Нежелательным последствием такого метода очистки является возможное закупоривание уплотнений, каналов смазки или каналов охлаждающего воздуха остатками очистителя. Поэтому известны случаи применения химического твердого очистителя, который после выполнения своих функций, при высокой температуре испаряется [2].
2.4Примеры очистки ГТН из инструкций по эксплуатации
2.4.1Четырехтактные среднеоборотные двигатели «Pielstick, Мan» 2.4.1.1 Промывка компрессоров
Фирма рекомендует следующую технологию промывки ГТН (рис. 2.3).
1) Обеспечить нагрузку дизеля не менее 80 % от номинальной. 2) Открыть клапан 4 и наполнить через патрубок 5 и гибкий шланг 6 дозирующий сосуд 2 чистой водой без каких-либо растворителей или химических добавок. Сосуд находится под давлением воздуха, подведенного гибким шлангом 1 от улитки 7. 3) Закрыть клапан 4. 4) Нажать кнопку 3 в течение около 20 секунд. Вода в этот период по нагнетательной трубе 9 впрыскивается во всасывающий тракт ком-
18

прессора перед вращающимся направляющим аппаратом. 5) Проверить эффективность промывки, контролируя давление наддува, которое должно слегка увеличиться. 6) При отсутствии эффекта промывку повторить через 15 минут.
Рис. 2.3 Схема водопромывки ГТН четырехтактных дизелей «Ман & Бурмейстер и Вайн»
2.4.1.2 Очистка турбины твердым агентом
Для дизелей, работающих на тяжелом топливе, наиболее высокая эффективность очистки турбины от отложений отмечается при вдувании твердых частиц. Обычно используются: скорлупа орехов, размером не более 1,2 мм; дробленый активированный уголь с максимальным размером частиц dmax =1,0 мм; сухие
рисовые зерна, dmax = 1,7 мм.
Размеры частиц должны быть скорректированы таким образом, чтобы исключить повреждения лопаток турбины.
Представленное на рис. 2.4 устройство для очистки турбин ГТН используется следующим образом:
1.Двигатель выводится на режим работы, при котором температура выхлопных газов перед турбиной составляет менее 500 ºС.
2.Закрыть клапан 4, открыть клапаны 2, 3, затем 1 и проверить поступление воздуха.
3.Закрыть клапаны 1, 2 (если их оставить открытыми дальнейшие операции станут опасными).
4.Открыв клапан 4 загрузить гранулы через воронку 5 в контейнер 6. Количество загрузки выбирается по таблице 2.1.
5.Закрыть клапан 4, открыть 1, 2. Начнется вдув частиц, который может со-
19

провождаться проскоком некоторых частиц в дымовую трубу и легким помпажом компрессора. Такие явления допустимы, если помпаж носит кратковременный характер. Запрещается открывать что-либо на ГТН или на газовыхлопе для предотвращения внезапных струй газа. Необходимо контролировать выхлоп на предмет появления языков пламени при сгорании крошки, и, в случае опасности, немедленно прекратить очистку.
6. После 3…10 минут впрыска закрыть клапаны 1, 2, 3.
|
|
|
|
|
|
|
|
|
|
|
|
|
|
|
|
|
|
|
|
|
|
|
|
|
|
|
|
|
|
|
|
|
|
|
|
Выхлопные |
|
Газоприемный |
|
|
|
|
газы |
|
|
корпус |
|
|
|
|
|
|
|
|
|
|
|
|
|
|
|
|
Рис. 2.4 Устройство системы очистки турбины твердым агентом для ГТН фирмы «АВВ»
Эффективность очистки зависит от размеров, состава, твердости и удельного веса частиц.
В случае необходимости повторной промывки, ее следует проводить не ранее чем через 15 минут. При чрезмерной передозировке очистителя возможны эрозионные повреждения деталей.
Таблица 2.1 Нормы загрузки твердого очистителя для турбин типа VTR
Тип ТК |
Частота вращения, мин-1 |
Масса гранул, кг |
|
VTR 304 |
15 000 |
– 18 000 |
0.5 |
VTR 354 |
12 000 |
– 15 000 |
0.8 |
VTR 454 |
9 500 – 12 000 |
1.3 |
|
VTR 564 |
7 500 |
– 9 500 |
1.8 |
VTR 714 |
6 000 |
– 7 500 |
2.3 |
Если на двигателе есть другие ГТН, или имеются несколько подводов газа к турбине, очистка осуществляется отдельно для каждого подвода и для каждого ГТН.
Запрещается использовать воду в данном устройстве.
20