
Аксенов А. А. Технология конструкционных материалов
.pdf
180
быть установлена в центрах станка, цанге, патроне или специальном приспособлении.
Скорость вращения заготовки при шлифовании зависит от ее диаметра и назначается от 10 до 50 м/с, а скорость вращения шлифовального круга – от 30 до 60 м/с.
При шлифовании с продольной подачей (рис. 7.24, а) заготовка вращается равномерно и совершает возвратно-поступательные движения. В конце каждого хода заготовки шлифовальный круг возвращается и при следующем ходе срезается новый слой металла определенной глубины, пока не будет достигнут необходимый размер.
Рис. 7.24. Схемы обработки на круглошлифовальных станках
Врезное шлифование (рис. 7.24, б) применяют при обработке жестких заготовок в тех случаях, когда ширина шлифуемого участка может быть перекрыта шириной шлифовального круга. В данном случае шлифовальный круг перемещается с постоянной скоростью подачи до достижения необходимого размера детали.
Глубинным шлифованием (рис. 7.24, в) за один проход снимают слой материала на всю необходимую глубину. На шлифовальном круге формируют конический участок длиной 8…12 мм, который в ходе шлифования удаляет ос-

181
новную часть срезаемого слоя, а цилиндрический участок зачищает обработанную поверхность.
Шлифование уступами (рис. 7.24, г) представляет собой сочетание первых двух методов, поэтому процесс шлифования состоит из двух этапов: первый – шлифуют врезанием с движением подачи, передвигая периодически стол на 0,8…0,9 ширины круга; второй – делают несколько ходов с движением продольной подачи для зачистки поверхности при включенном движении подачи.
Во многих случаях на деталях необходимо обеспечить правильное взаимное расположение цилиндрических и плоских поверхностей, для чего шлифовальный круг заправляют по схеме (рис. 7.24, д) и поворачивают на определенный угол или шлифуют коническими кругами.
Конические поверхности на шлифовальных станках получают так же, как и на токарных, только вместо токарного резца используют шлифовальный круг.
Обработка заготовок на внутришлифовальных станках. Внутреннее шлифование применяют для получения высокой точности отверстий на заготовках, как правило, прошедших термическую обработку. Возможно шлифование сквозных, глухих, конических и фасонных отверстий. Обычно диаметр шлифовального круга составляет 0,7…0,9 диаметра шлифуемого отверстия, причем чем меньше диаметр круга, тем больше частота его вращения.
На рис. 7.25, а показана схема шлифования с закреплением заготовки в кулачковом патроне. Внутришлифовальные станки позволяют также обрабатывать внутренние торцовые поверхности и фасонные поверхности, которые шлифуют специально заправленным кругом методом врезания. Внутренние конические поверхности шлифуют с поворотом передней бабки так, чтобы образующая конуса располагалась вдоль направления продольной подачи.

182
Для шлифования заготовок больших размеров и массы применяют планетарное шлифование (рис. 7.25, б), при котором заготовка неподвижно закреплена на станке, а шлифовальный круг вращается вокруг своей оси и оси отверстия (круговая подача).
Обработка заготовок на бесцентрово-шлифовальных станках. Про-
цесс шлифования на этих станках характеризуется высокой производительностью, так как заготовки обрабатываются в незакрепленном состоянии и для них не требуется центровых отверстий.
На станине 1 бесцентрово-шлифовального станка (рис. 7.26) установлены два круга: шлифующий на бабке 2 и ведущий на бабке 4. Каждый из кругов подвергается периодической правке с помощью механизмов 3 и 5. Заготовка вращается на ноже 6 и одновременно контактирует с обоими кругами. Чтобы заготовка перемещалась по ножу с движением продольной подачи, бабку ведущего круга поворачивают на небольшой угол. Если шлифуют заготовки с уступами, то бабку ведущего круга не поворачивают, а вся она перемещается по направляющим
Рис. 7.26. Общий вид бесцентрово-
станины до определенного положе- шлифовального станка ния.
Заготовку 3 (рис. 7.27, а) устанавливают на нож 2 между двумя кругами – шлифующим 1 и ведущим 4, которые вращаются в одном направлении, но с разными скоростями. Трение между ведущим кругом и заготовкой больше, чем между ней и рабочим кругом, вследствие чего заготовка увлекается во вращение со скоростью, близкой к окружной скорости ведущего круга.
Заготовки ступенчатой формы или с фасонными поверхностями шлифуют методом врезания (рис. 7.27, б). Перед шлифованием ведущий круг отводят в сторону, заготовку устанавливают на нож и поджимают ведущим кругом. Об-
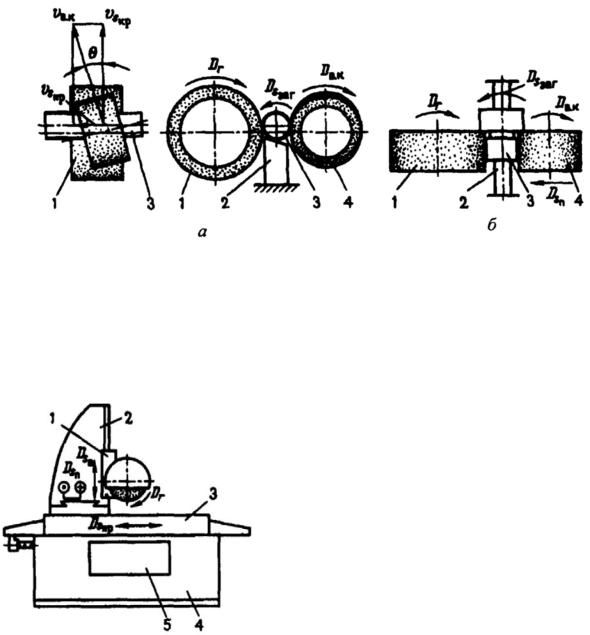
183
рабатывают с движением поперечной подачи до получения необходимого размера детали. После шлифования обработанная деталь удаляется из зоны резания выталкивателем. При шлифовании этим методом инструмент заправляют в соответствии с профилем детали.
Рис. 7.27. Схемы обработки заготовок на бесцентрово-шлифовальных станках
Обработка заготовок на плоскошлифовальных станках. Плоскошли-
фовальный станок с прямоугольным столом (рис. 7.28) состоит из станины 4, стола 3, стойки 2, шлифовальной бабки 1 и привода стола 5. Движение подачи возвратно-поступательное и осуществляется вручную или автоматическим приводом станка. У другого типа станков вместо воз- вратно-поступательного стол совершает вращательное движение, поэтому его выполняют круглым с вертикальной осью вращения. Компоновка такого станка также предусматривает вертикальное расположе-
Рис. 7.28 – Общий вид плоско- ние оси вращения шлифовального круга.
шлифовального станка
На практике наиболее распространены четыре схемы плоского шлифования (рис. 7.29), при которых шлифование производится периферией и торцевой поверхностью круга. Заготовки (одну или несколько) 2 закрепляют на прямоугольных или круглых столах 1 с помощью

184
магнитных плит или зажимных приспособлений. Шлифование периферией круга (рис. 7.29, а, в) менее производительно, чем шлифование торцом круга (рис. 7.29, б, г), так как в первом случае требуется производить дополнительную поперечную подачу. Однако шлифование периферией круга позволяет производить большее число разнообразных видов работ.
Рис. 7.29. Схемы обработки на плоскошлифовальных станках
185
8.ОТДЕЛКА ПОВЕРХНОСТЕЙ. МЕТОДЫ ОБРАБОТКИ БЕЗ СНЯТИЯ СТРУЖКИ. ЭЛЕКТРОФИЗИЧЕСКИЕ
ИЭЛЕКТРОХИМИЧЕСКИЕ МЕТОДЫ ОБРАБОТКИ
8.1МЕТОДЫ ОТДЕЛОЧНОЙ ОБРАБОТКИ ПОВЕРХНОСТЕЙ
Развитие машиностроения и автомобилестроения связано с увеличением нагрузок на детали машин, увеличением скоростей движения, уменьшением массы конструкций. Данные требования к деталям машин иногда невозможно выполнить описанными ранее способами, поэтому требуется дополнительная отделочная обработка для повышения точности, уменьшения шероховатости поверхностей или для придания им особого вида, что важно для эстетических или санитарно-гигиенических целей.
Влияние качества поверхностных слоев деталей машин на их эксплуатационные свойства очень велико. Например, при сравнительно небольших толщинах этих слоев (десятые доли миллиметра), формируемых в ходе соответствующих методов обработки, решающим образом изменяются износостойкость, коррозионная стойкость, контактная жесткость деталей, плотность соединений, отражательная способность, сопротивление обтеканию поверхностей газами и жидкостями, прочность соединений и другие свойства, что в конечном итоге значительно повышает надежность деталей машин.
Для отделочных методов обработки характерны малые силы резания, небольшие толщины срезаемых слоев материала, незначительное тепловыделение. Эти технологические особенности способствуют дальнейшему развитию и широкому применению данных методов.
Отделка поверхностей чистовыми резцами и шлифовальными кру-
гами. Тонким обтачиванием иногда заменяют шлифование. Процесс осуществляется при высоких скоростях резания, малых глубинах и подачах. В данном случае применяются токарные резцы с широкими режущими кромками, кото-
186
рые располагаются строго параллельно оси обрабатываемой заготовки. Подача на оборот заготовки составляет не более 0,8 ширины лезвия, а глубина резания
– не более 0,5 мм. Это приводит к уменьшению шероховатости обрабатываемой поверхности.
Обтачивание алмазными резцами применяют для заготовок из цветных металлов и сплавов, пластмасс и других неметаллических материалов потому, что алмазные резцы обладают высокой стойкостью и способны долгое время работать без наладки, обеспечивать высокую точность. По аналогии с тонким обтачиванием используют тонкое строгание и фрезерование.
Тонким растачиванием заменяют шлифование, особенно в тех случаях, когда заготовки из вязких цветных сплавов или стали выполнены тонкостенными. Оно целесообразно при точной обработке глухих отверстий или тогда, когда по условиям работы детали не допускается внедрение абразивных зерен в поры обработанной поверхности.
Тонкое шлифование выполняют мягким, мелкозернистым кругом при больших скоростях главного движения резания (до 40 м/с) и очень малой глубине шлифования. Естественно, оно сопровождается обильной подачей охлаждающей жидкости. Для тонкого шлифования характерен процесс «выхаживания», когда после окончания обработки заготовки движение подачи на глубину резания выключается, а движение продольной подачи не выключается, и процесс обработки продолжается за счет упругих сил, возникающих в станке и заготовке.
Данными методами производят обработку наплавленных поверхностей, размеры которых восстанавливают наплавкой после изнашивания (например, коленчатый и распределительный валы двигателей автомобилей).
Полирование заготовок. Полированием уменьшают шероховатость поверхности, получают зеркальный блеск на ответственных деталях (дорожки качения или скольжения подшипников) или на деталях, применяемых для декоративных целей (облицовочные части автомобиля). Для этого используют поли-

187
ровальные пасты или абразивные зерна, смешанные со смазочным материалом, которые наносят на быстро вращающиеся эластичные (например, фетровые или войлочные) круги или колеблющиеся щетки. Также применяют полирование быстродвижущимися бесконечными абразивными лентами (шнурками).
Взоне полирования одновременно протекают процессы тонкого резания, пластического деформирования поверхностного слоя и химических реакций – воздействия на металл химически активных веществ, находящихся в полировальном материале.
Вкачестве абразивного материала применяют порошки из электрокорунда и оксиды железа при полировании стали, карбиды кремния и оксиды железа при полировании чугуна, оксиды хрома и наждака при полировании алюминия
исплавов меди. Порошок смешивают со смазочным материалом, который состоит из смеси воска, сала, парафина и керосина. Полировальные круги изготавливают из войлока, фетра, кожи, капрона, спрессованной ткани и других материалов.
Абразивно-жидкостная отделка. Отделка объемно-криволинейных, фасонных поверхностей обычными методами вызывает большие технологические трудности, которые решаются просто при использовании абразивножидкостной отделки. На обрабатываемую поверхность, имеющую следы пред-
Рис. 8.1. Схемы сглаживания микронеровностей при абразивно-жидкостной отделке (а) и жидкостном полировании (б)
шествующей обработки, подают струи антикоррозионной жидкости со взвешенными частицами абразивного порошка (рис. 8.1, а). Данная смесь перемещается под давлением с большой скоростью, в результате чего частицы абразива ударяются о поверхность заготовки и сглаживают микронеровности.
188
Интенсивность съема обрабатываемого материала регулируется зернистостью порошка (обычно применяют электрокорунд), давлением струи и уг-
лом β (наибольший съем металла при β =450), т.е. изменением пластической деформации материала заготовки под воздействием суспензии. Абразивные зерна, попадающие на микровыступы, легко преодолевают сопротивление материала и удаляют его; а зерна, которые попадают на впадины, встречают большее сопротивление, и съем материала замедляется, из-за чего в совокупности шероховатость поверхности уменьшается.
На рис. 8.1, б показана схема жидкостного полирования. Обрабатываемая заготовка 3 сложного профиля перемещается в камере 4 так, что все ее участки подвергаются полированию. Абразивная суспензия 1, помещенная в баке 2, подается насосом 6 в рабочую камеру через твердосплавное сопло 5, а отработанная суспензия падает обратно в бак 2 и может быть использована многократно. Метод жидкостного полирования особенно эффективно применяется при обработке фасонных внутренних поверхностей – сопло вводится в полость заготовки, которая совершает вращательные и поступательные перемещения.
Абразивно-жидкостную отделку проводят также в вибрирующих резервуарах, содержащих абразивную суспензию. Режим колебания резервуаров обеспечивает относительное перемещение заготовок и абразивных зерен, которые сглаживают микронеровности на наружных и внутренних поверхностях заготовок одновременно.
Притирка поверхностей. Поверхности деталей машин, обработанные на металлорежущих станках, всегда имеют отклонения от правильных геометрических форм и заданных размеров. Эти отклонения могут быть устранены притиркой (абразивной доводкой), которая обеспечивает шероховатость поверхно-
сти до RZ =0,05…0,01 мкм, отклонения размеров и формы обработанных по-
верхностей до 0,05…0,3 мкм. Притирка может осуществляться вручную и механическим способом.
189
По сравнению с ручной притиркой механическая притирка позволяет повысить производительность в 2…6 раз, и при этом обеспечивается стабильность выходных характеристик деталей агрегатов и машин. Притирке подвергаются детали гидравлической, пневматической и топливной аппаратуры (например, клапаны двигателя), зубчатых колес, шариков и колец подшипников качения.
Процесс осуществляется с помощью притиров соответствующей геометрической формы, на которые наносят притирочную пасту или мелкий абразивный порошок со связующей жидкостью. Материал притиров, как правило, мягче обрабатываемого, для того, чтобы паста или порошок внедрился в его поверхность и удерживался ею, но так, что при относительном движении каждое абразивное зерно могло снимать весьма малую стружку. Поэтому притиры можно рассматривать как очень точные абразивные инструменты.
Притир и заготовка должны совершать разнонаправленные движения, причем наилучший результат дает процесс, в ходе которого траектория движения каждого зерна не повторяется. Микронеровности сглаживаются за счет совокупного химико-механического воздействия на поверхность заготовки.
В качестве абразива для притирочной смеси используют порошок электрокорунда, карбидов кремния и бора, оксида хрома и железа и др. Притирочные пасты состоят из абразивных порошков и химически активных веществ (например, олеиновой и стеариновой кислот), играющих одновременно роль связующего материала. Материалами притиров являются серый чугун, бронза, красная медь, дерево. В качестве связующей жидкости используют машинное масло, керосин, стеарин, вазелин.
Хонингование. Его применяют для получения поверхностей высокой точности и малой шероховатости, а также для создания специфического микропрофиля обработанной поверхности в виде сетки. Такой профиль необходим для удержания смазочного материала при работе машины на поверхности ее деталей (например, внутренняя поверхность цилиндров двигателей).