
Аксенов А. А. Технология конструкционных материалов
.pdf80
Волочение (рис. 4.4, д) заключается в протягивании заготовки 2 через сужающееся отверстие в инструменте, называемом волокой 1. Площадь поперечного сечения заготовки уменьшается и получает форму поперечного сечения отверстия волоки, а следовательно, длина (из условия постоянства объема при пластической деформации) увеличивается. Величина вытяжки в данном случае составляет 1,15…1,45.

81
5. ТЕХНОЛОГИЯ ОБРАБОТКИ МЕТАЛЛОВ ДАВЛЕНИЕМ СПОСОБАМИ ПРОКАТКИ, ПРЕССОВАНИЯ, ВОЛОЧЕНИЯ, ПРОФИЛИРОВАНИЯ, КОВКИ И ШТАМПОВКИ
5.1 ИЗГОТОВЛЕНИЕ МАШИНОСТРОИТЕЛЬНЫХ ПРОФИЛЕЙ
Классификация машиностроительных профилей. Машиностроитель-
ные профили – длинномерные изделия (у которых длина значительно больше поперечных размеров) с определенной формой поперечного сечения. Совокупность форм и размеров профилей называют сортаментом. Весь сортамент машиностроительных профилей, изготовляемых обработкой давлением и насчитывающий сотни тысяч типоразмеров, можно разделить на четыре основные группы: сортовые профили, листовой металл, трубы и периодические профили.
Сортовые профили (рис. 5.1, а) делят на профили простой геометрической формы (круг, шестигранник, квадрат, прямоугольник) и фасонные (рельс, швеллер, тавровый, угловой профили и т.д.). Их объем составляет 35 % сортамента.
Рис. 5.1. Примеры сортовых (а) и периодических (б) профилей
82
Листовой металл из стали и цветных металлов используют в различных отраслях промышленности. В связи с этим листовую сталь, например, делят на автотракторную, трансформаторную, кровельную жесть и т.д. Кроме того, листовую сталь делят на толстостенную (4…160 мм) и тонкостенную (0,2…4 мм). Листы толщиной менее 0,2 мм называют фольгой. Объем листового проката наибольший и составляет 50 % всего сортамента.
Трубы делят на бесшовные и сварные. Бесшовные трубы используют в наиболее ответственных случаях – в трубопроводах, работающих под давлением, в агрессивных средах. Трубный прокат составляет 10 % сортамента.
Периодические профили имеют периодически изменяющуюся форму и площадь поперечного сечения вдоль оси заготовки (рис. 5.1, б). Их применяют как фасонные заготовки для последующей штамповки и как заготовки под окончательную механическую обработку. Доля этих профилей в сортаменте составляет 5 %.
Для изготовления машиностроительных профилей применяют различные виды обработки металлов давлением: прокатку, прессование, волочение, профилирование листового металла. Поэтому кроме группирования по приведенным признакам профили различаются и по способу их изготовления.
Производство прокатанных профилей. Прокатке подвергают до 90 %
всей выплавляемой стали и большую часть цветных металлов, а в автомобилестроении прокаткой изготавливают свыше 90 % всех деталей. При прокатке металл пластически деформируется вращающимися валками. Взаимное расположение валков и заготовки, форма и число валков могут быть различными. Различают продольную, поперечную и поперечно-винтовую прокатки.
Продольная прокатка (рис. 5.2, а) – сама распространенная – осуществляется валками 1, вращающимися в разные стороны, заготовка 2 движется между ними и деформируется. При поперечной прокатке (рис. 5.2, б) валки 1, вращаясь в одном направлении, придают вращение заготовке 2 и деформируют ее. При поперечно-винтовой прокатке (рис. 5.2, в) валки 1 расположены под углом

83
и сообщают заготовке 2 при деформировании вращательное и поступательное движения.
Рис. 5.2. Схемы продольной (а), поперечной (б) и поперечно-винтовой (в) прокатки: 1 – валки; 2 – заготовка; 3 – оправка
Инструментом для прокатки являются валки, которые в зависимости от прокатываемого профиля могут быть гладкими (рис. 5.3, а), применяемыми для прокатки листов, лент и т.п.; ступенчатыми, например, для прокатки полосовой стали, и ручьевыми (рис. 5.3, б) для получения сортового проката. Ручьем называют вырез на боковой цилиндрической поверхности валка, а совокупность двух ручьев образует полость, называемую калибром (рис. 5.3, в). Каждая пара ручьевых валков обычно образует несколько калибров. Валки состоят из рабочей части – бочки 1, шеек 2 и трефы 3. Шейки валков вращаются в подшипниках, которые у одного из валков 5 (рис. 5.3, г) могут перемещаться специальным нажимным механизмом 4 для изменения расстояния между валками и регулирования взаимного расположения их осей. Комплект прокатных валков со станиной называют рабочей клетью, которая вместе со шпинделем для привода валков 6, шестеренной клетью 7 для передачи вращения с одного на два вала, редуктором 8, муфтами и электродвигателем 9 образуют рабочую линию стана.
Рабочие клети по числу и расположению валков могут быть двухвалковые (рис. 5.3, а); четырехвалковые (рис. 5.4, а), у которых два валка рабочих и два опорных; многовалковые (рис. 5.4, б), у которых также два валка рабочих, а остальные опорные. Использование опорных валков позволяет применять ра-
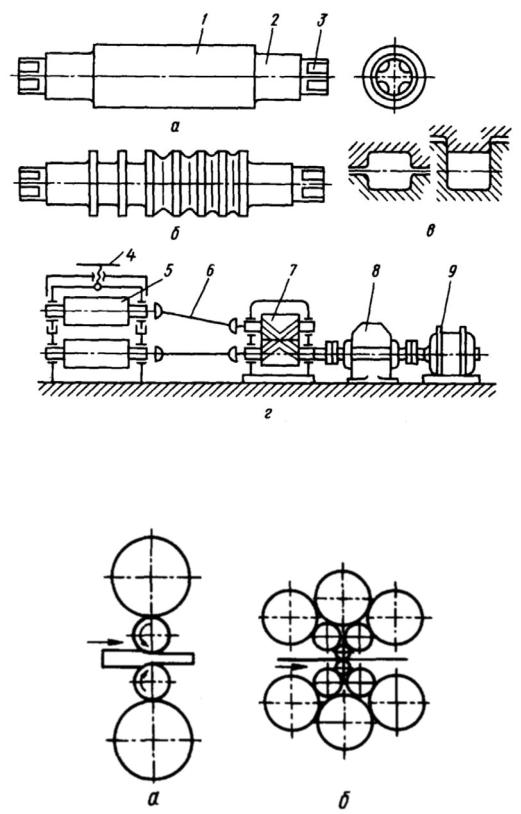
84
бочие валки малого диаметра, благодаря чему увеличивается вытяжка и снижаются деформирующие силы.
Рис. 5.3. Валки и схема их привода в рабочей линии прокатного стана:
а– гладкий валок; б – ручьевой валок; в – открытый и закрытый калибры;
г– схема рабочей линии прокатного стана
Рис. 5.4. Схемы четырехвалковой (а) и многовалковой (б) прокатки
85
Прокатные станы могут быть одноклетьевыми (с одной рабочей клетью) и многоклетьевыми.
Наиболее совершенные многоклетьевые станы – непрерывные, у которых рабочие клети располагают последовательно одну за другой. Прокатываемая полоса через каждую клеть проходит только один раз, т.е. число рабочих клетей этих станов равно требуемому числу проходов полосы. Расстояние между клетями обычно меньше длины прокатываемой полосы, следовательно, она прокатывается одновременно в нескольких клетях. На непрерывных станах достигается высокая производительность при полном исключении ручного труда.
По назначению прокатные станы подразделяют на станы для производства полупродукта и станы для выпуска готового проката. К первой группе относят обжимные станы для прокатки слитков в полупродукт крупного сечения (блюминги, дающие заготовку для сортового проката, и слябинги, дающие заготовку для листового проката) и заготовочные – для получения полупродукта более мелкого сечения.
К станам для производства готового проката относят сортовые, листовые, трубные и специальные. Размер блюмингов, слябингов, заготовочных и сортовых станов характеризуется диаметром бочки валков (например, блюминг 1500; сортовой стан 350); размер листовых станов определяется длиной бочки (например, стан 2600), а размер трубопрокатных станов – наружным диаметром прокатываемых труб.
Исходной заготовкой при прокатке служат слитки: стальные массой до 60 т, из цветных металлов и их сплавов обычно массой до 10 т. При производстве сортовых профилей стальной слиток массой до 15 т прокатывают на блюминге в горячем состоянии, получая заготовки квадратного сечения (от 140×140 до
450×450 мм), называемые блюмами. Блюмы поступают на заготовочные станы для прокатки заготовок требуемых размеров или сразу на станы для прокатки крупных профилей сортовой стали. На заготовочных и сортовых станах заготовка последовательно проходит через ряд калибров.
86
После прокатки профили режут на мерные длины, охлаждают, правят в холодном состоянии, термически обрабатывают, удаляют поверхностные дефекты.
Исходным материалом для холодной прокатки листа толщиной менее 1,5 мм обычно служат горячекатаные рулоны. На современных станах холодной прокатки производят листовую сталь с минимальной толщиной 0,15 мм и ленты с минимальной толщиной 0,0015 мм.
При прокатке бесшовных труб первой операцией является прошивка – образование отверстия в слитке или круглой заготовке. Эту операцию выполняют в горячем состоянии на прошивных станах. Наибольшее применение получили прошивные станы с двумя бочкообразными валками, оси которых расположены под небольшим углом (5…150) друг к другу (см. рис. 5.8, в). Оба валка 1 вращаются в одном направлении, т.е. в данном случае используется принцип поперечно-винтовой прокатки. Благодаря такому расположению валков заготовка 2 получает одновременно вращательное и поступательное движения. При этом в металле возникают радиальные растягивающие напряжения, которые вызывают течение металла от центра в радиальном направлении, образуя внутреннюю полость, и облегчают прошивку отверстия оправкой 3, устанавливаемой на пути движения заготовки.
Сварные трубы изготовляют из плоской заготовки – ленты (называемой штрипсом) – или из листов, ширина которых соответствует длине (или половине длины) окружности трубы. Процесс изготовления сварной трубы включает следующие операции: гибку плоской заготовки в трубу, сварку кромок, уменьшение (редуцирование) диаметра полученной трубы. Для сварки чаще применяют печную, дуговую сварку под флюсом и сварку сопротивлением. Трубы гнут на непрерывных станах (рис. 5.5), состоящих из 6…12 рабочих клетей, в которых валки образуют круглые калибры. При прокатке в калибрах прижимаемые друг к другу кромки, дополнительно нагретые до высокой температуры, обдуваются кислородом, свариваются. Выходящую из стана трубу разреза-

87
ют специальной пилой на куски требуемой длины и далее калибруют на калибровочном стане. Этим способом изготавливают трубы самой низкой стоимости из низкоуглеродистой стали (Ст2 кп) диаметром 10…114 мм.
Рис. 5.5. Последовательность процесса свертывания полосы в труб в шести клетях непрерывного стана
Периодические профили в основном изготовляют поперечной и попереч- но-винтовой прокаткой. На станах поперечно-винтовой прокатки получают не только периодические профили, но и заготовки шаров, роликов подшипников качения.
Показателем технологического процесса прокатки является коэффициент вытяжки, который колеблется от 1,25 до 1,6.
Производство прессованных профилей. При прессовании металл вы-
давливается из замкнутой полости через отверстие, соответствующее сечению прессуемого профиля. Этим процессом изготовляют не только сплошные профили, но и полые (рис. 5.6, в). В этом случае в заготовке необходимо предварительно получить сквозное отверстие, которое часто прошивают в том же процессе. Прессование может осуществляться двумя способами: прямым и обратным (рис. 5.6, а, б). В конце процесса прессования в контейнере остается небольшая часть металла, называемая пресс–остатком. При прямом способе движения пуансона выход готовой продукции идет в направлении пуансона, при обратном – в разные стороны. Обратный способ уменьшает усилие прессования до 30 %, а пресс-остаток составляет 5…6 %, когда при прямом способе пресс-остаток составляет 18…20 % и может доходить до 40 %.

88
Исходной заготовкой при прессовании служит слиток или прокат. Состояние поверхности заготовки оказывает значительное влияние на качество поверхности и точность прессованных профилей. Поэтому во многих случаях заготовку предварительно обтачивают на станке; после нагрева поверхность заготовки тщательно очищают от окалины.
Рис. 5.6. Схемы прессования обратным (а) и прямым способом (б); профили, полученные прессованием (в)
Прессованием изготовляют изделия разнообразного сортамента из цветных материалов и сплавов, в том числе прутки диаметром 3…250 мм, трубы диаметром 20…400 мм со стенкой толщиной 1,5…12 мм и другие профили.
При прессовании металл подвергается всестороннему неравномерному сжатию и поэтому должен иметь весьма высокую пластичность. Коэффициент, характеризующий степень деформации и определяемый как отношение площади сечения заготовки к площади прессуемого профиля, при прессовании составляет 10…50.
Прессованием можно обрабатывать такие специальные стали, цветные металлы и их сплавы, которые ввиду низкой пластичности (особенно в литом состоянии) другими видами обработки давлением деформировать невозможно или затруднительно.
Прессованием можно получать профили сложных форм, которые не могут быть получены другими видами обработки металлов давлением. Точность прессованных профилей выше, чем прокатанных.

89
Схема всестороннего сжатия металла при прессовании приводит к значительным давлениям, действующим на инструмент. Поэтому инструмент для прессования работает в исключительно тяжелых условиях, испытывая кроме действия больших давлений действие высоких температур. Инструмент для прессования изготовляют из высококачественных инструментальных сталей и жаропрочных сплавов. Износ инструмента уменьшают применением специальных смазочных материалов; например, при прессовании труднодеформируемых сталей и сплавов используют смазочные шайбы, укладываемые на матрицу под заготовку, изготовленные из крупки доменного шлака, связанной жидким стеклом.
Основным оборудованием для прессования являются горизонтальные и гидравлические прессы.
Волочение машиностроительных профилей. Исходными заготовками для волочения служат прокатанные или прессованные прутки и трубы из стали, цветных металлов и их сплавов.
Волочение различных профилей осуществляется в помощью инструмента, называемого волокой (рис. 5.7, а). Она состоит из четырех основных частей: I – смазочной, II – деформирующей, III – калибрующей и IV – выходной. Угол захвата (α ) в данном случае может быть от 10 до 200, а коэффициент вытяжки
1,15…1,45.
Рис. 5.7. Схема волочения проволоки (а), трубы (б) и примеры профилей, полученных волочением (в)