
- •ПРЕДИСЛОВИЕ
- •1. МАТЕРИАЛЫ ТИПОВОЙ РЕАКЦИОННОЙ АППАРАТУРЫ
- •2. ЗАЩИТНЫЕ ПОКРЫТИЯ
- •3. ВЫБОР МАТЕРИАЛОВ ДЛЯ АППАРАТУРЫ
- •4. КОНСТРУКТИВНЫЕ УЗЛЫ
- •4.1. Элементы поверхности теплообмена вертикальных котлов
- •4.2. Гарнитура реакционных аппаратов
- •4.3. Арматура химических установок
- •4.4. Перемешивающие устройства
- •2.2. Аппараты для разделения неоднородных систем
- •2.3. Дробилки и мельницы
- •2.4. Сушилки
- •2.5. Смесители для твердых сыпучих тел
- •Рекомендуемая литература
- •Оглавление
Выбортрубопроводнойарматуры
Основной тип запорной арматуры, рекомендуемый для трубопроводов диаметром от 50 мм и более, - задвижка; она имеет минимальное гидравличе- ское сопротивление, надежное уплотнение затвора и допускает изменение на- правления движения среды.
Вентили рекомендуется устанавливать на трубопроводах диаметром до 50 мм; при диаметре более 50 мм вентили используют главным образом в случаях, когда по условиям технологического процecca требуется ручное дросселирование. Основное преимущество вентилей - отсутствие трения уплотнительных поверхно- стей, что позволяет их использование при более высоких давлениях. В связи с этим вентили устанавливаются на трубопроводах высокого давления.
Краны используют, когда требуются запорные устройства, обладающие не- значительным гидравлическим сопротивлением или способные управлять не- сколькими расходящимися потоками, в последнем случае используют трех- или четырехходовые краны.
4.4.ПЕРЕМЕШИВАЮЩИЕ УСТРОЙСТВА
Вхимической технологии перемешивание применяют для улучшения теп- ло- и массообмена, получения равномерных смесей нескольких жидкостей, жидкости и твердого тела, жидкости и газа. Хотя основной задачей перемеши-
вания в большинстве случаев является равномерное распределение вещества или температуры в перемешиваемом объеме, иногда задача перемешивания заключа-
ется в создании высоких скоростей среды около теплообменных поверхностей с целью интенсификации теплообмена.
Способы перемешивания. Известны несколько видов перемешивания:
-механическое;
-циркуляционное;
-барботажное.
Барботажное перемешивание осуществляется путем барботажа инертного газа или газообразных веществ через жидкость.
Циркуляционное перемешивание происходит за счет больших скоростей движения (насосом). Это перемешивание целесообразно применять в том случае, когда имеется необходимость отвода тепла через развитую поверхность теплооб- мена, т.е. через выносной теплообменник.
Механическое перемешивание в жидкой среде, а также в пастообразных и вязких материалах. Для интенсификации процессов массо- и теплообмена практически все емкостные аппараты снабжают перемешивающими устройст- вами - мешалками. Выбор конструкции мешалки зависит от необходимой ин- тенсивности перемешивания и консистенции (вязкости) реакционной массы. В случае гетерофазных систем (жидкость - жидкость, жидкость - твердое веще- ство и т. д.) перемешивание позволяет получить развитую поверхность кон- такта фаз, что способствует переходу процесса из диффузионной области в
51

кинетическую и увеличению скорости процесса. С ростом интенсивности пе- ремешивания (числа оборотов мешалки) увеличиваются значения критериев Рейнольдса и Нуссельта и, следовательно, значение коэффициента теплоотда- чи от стенки к реакционной массе или наоборот. Это позволяет устранить ме- стные перегревы и пригорание реакционной массы к стенкам аппарата.
Механические перемешивающие устройства состоят из трех основных час- тей: вала, на котором закреплена мешалка, мешалки, являющейся рабочим эле- ментом; и привода, с помощью которого вал приводится в движение за счет меха- нической энергии. Привод может быть осуществлен либо непосредственно от электродвигателя (для быстроходных мешалок), либо через редуктор или кли- ноременную передачу.
Мешалки по конструктивной форме, в зависимости от устройства лопастей, разделяются: 1) на лопастные; 2) листовые; 3) якорные; 4) рамные; 5) турбин- ные; 6) пропеллерные; 7) специальные.
В зависимости от числа оборотов мешалки условно делят на тихоходные и быстроходные. К тихоходным относят лопастные, рамные, якорные и листовые, имеющие скорость более 80-100 об/мин. К быстроходным - турбинные и пропел- лерные.
При выборе типа мешалки и ее параметров учитывают требования техноло- гического процесса, свойства жидкости, наличие осадков, форму аппарата и дру- гие факторы. К сожалению, отсутствуют единые критерии для выбора мешалки. Обычно при этом руководствуются производственным опытом или лаборатор- ными исследованиями. В некоторой степени можно предложить следующие ре- комендации.
Лопастные мешалки (рис. 29) применяют для перемешивания жидкостей с небольшой вязкостью (до 0,1 Па·с), растворения и суспензирования твер- дых веществ с малым удельным весом, а также для грубого смешения жид-
костей вязкостью меньше 20 Па.с и с плотностью до 2000 кг/м3.
Рис. 29. Двухлопастная эмалированная мешалка с углом наклона лопасти α = 45о
При высоте сосуда, превышающей диаметр, или при перемешивании вяз- кой жидкости устанавливают несколько пар лопастей по высоте вала. При пере-
мешивании очень вязких жидкостей на стенках сосуда устанавливают радиально расположенные перегородки, над которыми проходят лопасти мешалки. При этом поток дробится и повышается эффективность работы мешалки. Макси- мальный эффект турбулизации потока достигается при применении 4-х пере-
52
городок высотой (0,11-0,13) × D, где D - диаметр аппарата. Перегородки препят- ствуют образованию центральной воронки, а также увлечению жидкости вра- щающимися лопастями, что может привести и к прекращению эффекта переме- шивания. Установка слишком длинных лопастей нерациональна, так как с воз- растанием линейных размеров лопасти быстро растет потребляемая мощность.
Нормализованные диаметры мешалок от 700 до 2100 мм. Лопастные мешал- ки отличаются простотой конструкции и низкой стоимостью изготовления. Наибо- лее просты по устройству мешалки с плоскими лопастями из полосовой или угло- вой стали, установленные перпендикулярно или наклонно к направлению их дви- жения. Частота вращения таких мешалок колеблется от 18 до 80 мин-1.
Недостатки таких мешалок - малая интенсивность перемешивания и отсут- ствие значительных вертикальных потоков, вследствие чего их не рекомендуется
применять для взмучивания тяжелых осадков и работы с расслаивающимися жидкостями. Достоинство мешалок - они просты по конструкции, обеспечивают удовлетворительное перемешивание при работе с вязкими жидкостями, могут применяться в аппаратах значительного объема.
Пропеллерные мешалки. Для интенсивного перемешивания подвижных реакционных масс, позволяющего получить в емкостных аппаратах режим, близкий к идеальному смешению, используют пропеллерные мешалки. Они представляют собой обычный гребной винт с числом лопастей от двух до четырех.
Частота вращения пропеллера должна быть не менее 150 мин-1, а реко- мендуемая – 400-500 мин-1.
Пропеллерные мешалки применяют для перемешивания взаимно раство- римых жидкостей, тонких суспензий, содержащих до 10 % взвешенных час- тиц с размерами до 0,15 мм, они не пригодны для совершенного смешивания
жидкостей значительной вязкости (более 0,6 Па.с). При работе мешалки осу- ществляется интенсивная циркуляция жидкости с сильным вихреобразованием. Их рекомендуют использовать для перемешивания сред вязкостью до 2 Па•с и плотностью до 2000 кг/м3. Чтобы избежать образования воронки, вал мешалки смещают по отношению к оси аппарата на величину до 0,25 мм, либо устанав- ливают его с наклоном 10-20° к оси сосуда.
Для улучшения циркуляции перемешиваемой жидкости пропеллерные мешалки часто устанавливают в диффузоре, который представляет собой ста- кан, имеющий форму цилиндра или слегка усеченного конуса.
В высоких аппаратах на одном валу устанавливают два, а иногда и три пропеллера. При установке второго пропеллера потребляемая мешалкой мощность увеличивается в 1,5 раза. Потребляемая мешалкой мощность зави- сит также от конструкции реактора. Так, при установке в аппарате змеевиков
расход мощности на перемешивание пропеллерными мешалками возрастает в 2 раза.
Для трудно смешиваемых вязких жидкостей применяются мешалки, состоя- щие из 2-х пропеллеров, установленных на одном валу. Оба пропеллера толкают жидкость в одну сторону или навстречу друг другу. Нормализованные диаметры мешалок — от 300 до 700 мм.
53
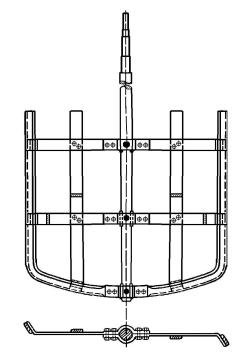
Турбинные мешалки работают по принципу центробежного насоса, т.е. вса- сывают жидкость в середину и за счет центробежной силы отбрасывают ее к пе- риферии. Их делают открытыми и закрытыми. Закрытые мало отличаются по кон- струкции от колеса центробежного насоса и подразделяются, в свою очередь, на мешалки одностороннего и двустороннего всасывания. Открытая мешалка пред- ставляет диск с радиально расположенными лопатками. Они более просты по конструкции и поэтому чаще применяются в технике.
Скорость вращения турбинной мешалки более 500-700 мин-1. Их приме-
няют для интенсивного перемешивания и смешения жидкостей с вязкостью до 50 Па.с, создания и перемешивания устойчивых суспензий , содержащих до 60 % и более твердой фазы с размерами до 2,5 мм.
Не рекомендуется их использовать в реакторах большой емкости. В аппара- тах с турбинными мешалками обязательна установка отражательных перегоро- док. При отсутствии такой перегородки образуется глубокая воронка, иногда до- ходящая до основания мешалки, и перемешивание резко ухудшается (обычно ус- танавливают четыре перегородки).
Рамные мешалки применяют для перемешивания жидкостей вязкостью
не более 10 Па.с, а также, когда возможно выпадение осадка или загрязнения теплопередающей поверхности, они очищают стенки и дно аппарата от на- липающих загрязнений. Они представляют собой комбинацию лопастных мешалок с вертикальными и наклонными лопастями (рис. 30). Эти мешалки применяются в тех же случаях, что и лопастные, а также при перемешивании значительных объемов вязких материалов. Нормализованные диаметры меша-
лок до 2520 мм. Эти мешалки используют в реакторах с большой емкостью (до
100 м3).
Рис. 30. Рамная мешалка
54
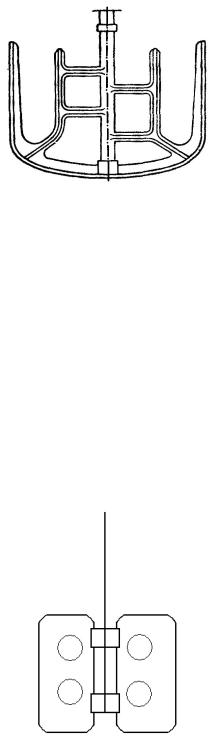
Якорные мешалки. По своей форме соответствуют сосуду, в котором рабо- тают. Расстояние между лопастью и стенкой реактора обычно выбирают в пре- делах 25—140 мм.
Рис. 31. Якорная мешалка
Якорные мешалки (рис. 31) предназначены для перемешивания жидкостей вязкостью 300 Па.с и выше, особенно при нагревании среды через стенку реак- тора. Вследствие небольшого зазора между лопастью и стенкой сосуда возни- кает сильное турбулентное движение, препятствующее выпадению на стенках осадка и перегреву среды. НИИХИММАШ рекомендует для якорных мешалок те же скорости, что и для лопастных. Следует отметить, что при перемешива-
нии очень вязких жидкостей якорные мешалки снабжаются дополнительными вертикальными лопастями — пальцами.
Листовые мешалки. Их применяют сравнительно редко, в основном для мало- вязких жидкостей (вязкостью менее 0.05 Па.с), при интенсификации теплообме- на, взвешивании твердого вещества, при проведении химической реакции в объеме и растворении. Конструкция мешалки приведена на рис. 32.Листовые мешалки имеют лопасти большей ширины, чем у лопастных мешалок.
Рис. 32. Листовая мешалка
Несколько слов о мешалках специальных типов. К ним относятся импел- лерные мешалки (рис. 33), которые применяют для обеспечения хорошего кон- такта газа с жидкостью при одновременном интенсивном перемешивании.
55
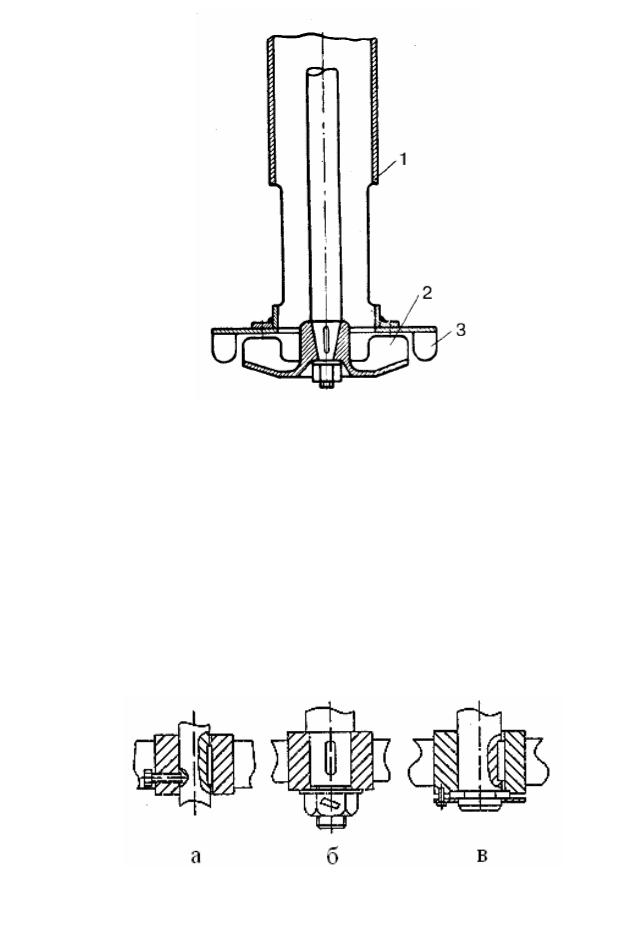
Рис. 33. Импеллерная мешалка:
1 – центральная труба; 2 – лопасти статора; 3 – лопасти мешалки (ротора)
Вал мешалки помещен внутри трубы, по которой подается воздух под не- большим избыточным давлением. На мешалке имеется ряд лопастей, а на конце трубы установлен статор с лопастями. Наличие двух рядов лопастей - подвижно- го и неподвижного - обеспечивает хорошее перемешивание жидкости и газа.
Конструирование и изготовление мешалок. Мешалки изготавливают из раз-
личных металлических и неметаллических материалов, обладающих достаточной механической прочностью. Наиболее распространены сварные перемешиваю- щие устройства, выполненные из легированной стали. Мешалки сложной кон- струкции отливают из чугуна. В простейших конструкциях лопасти приварива- ют непосредственно к валу. Однако, как правило, рабочие элементы крепятся на валу с помощью разъемных соединений.
Рис. 34. Способы крепления мешалок на валу:
а – стопорным винтом; б – концевой гайкой; в - полукольцами
56
Обычно к ступице приваривают лопасти. Ступица крепится на валу с помо- щью шпонки и стопорных устройств, препятствующих осевому смещению. В слу- чае установки мешалки в середине вала ее закрепляют стопорным винтом, как показано на рис. 34, а, при установке на конце вала - концевой гайкой (рис. 34, б) или полукольцами.
При конструировании мешалок необходимо учитывать условия их монтажа. Мешалки небольших аппаратов (диаметр 1200 мм и менее) обычно собирают со- вместно с крышкой и вместе с ней устанавливают в реактор.
Мешалки для крупногабаритных аппаратов целесообразно делать разъем- ными из частей таких размеров, которые можно пронести через лаз аппарата. Это дает возможность разбирать мешалку при ремонтных и монтажных работах, не снимая крышку и привод. В цельносварных аппаратах мешалка обязательно должна быть разборной. Необходимо иметь в виду, что резьбовые соединения внутри химических реакторов работают в очень тяжелых условиях. Резьба легко загрязняется и корродирует даже при действии слабых агрессивных сред. Поэто- му во многих случаях части мешалок изготавливают из нержавеющей стали.
Открытые турбинные мешалки выполняют сварными. Лопасти привари- вают к диску, который, в свою очередь, сварен со ступицей. Применение поли- мерных материалов для мешалок ограничено их низкой механической прочно- стью. Более распространены стальные мешалки, защищенные антикоррозион- ными покрытиями, или комбинированные из стального вала и неметаллических лопастей.
Приводы мешалок. Быстроходные мешалки при 400-500 об/мин и выше соединяются с электродвигателем через клиноременную передачу, а в некоторых случаях могут быть установлены и на одном валу с электродвигателем. Однако обычно привод осуществляется от электродвигателя через редуктор. Приводы мешалок могут быть с конической, червячной, цилиндрической или планетарной передачей. Конические и червячные приводы имеют горизонтальный быстро- ходный вал, соединенный с электродвигателем через муфту или клиноременную передачу. Конические и особенно червячные приводы до недавнего времени ши- роко применялись для аппаратов с мешалками.
В настоящее время выпускают планетарные приводы. Они компактны, на- дежны в работе, имеют высокий КПД и работают в значительном диапазоне час- тоты вращения и мощностей. Но эти приводы не дают возможности изменять число оборотов мешалки во время работы, что является существенным их недос- татком.
Изменение числа оборотов мешалки необходимо во многих случаях: при изменении консистенции перемешиваемой массы, при отработке нового, еще не- изученного процесса, а также, когда режим перемешивания должен меняться во времени. Приводы мешалок во взрывоопасных цехах снабжают взрывобезопас- ными электродвигателями. В помещениях, содержащих особо взрывоопасные вещества, установка электродвигателей иногда вообще исключается. Двигатель приходится выносить в соседнее взрывобезопасное помещение, передача осуще- ствляется с помощью горизонтального вала, проходящего через стену, разде-
57
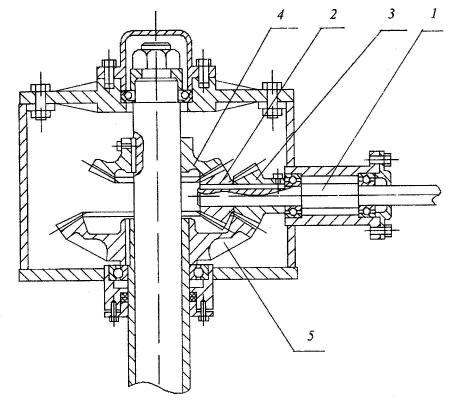
ляющую помещения. Вал в стене уплотняют сальниками. Приводы мешалок ус- танавливают на стойку, которую, в свою очередь, крепят к аппарату, для чего к его крышке приваривают толстые пластины. Стойки делают чугунными или стальными, сварными.
Для комбинированных мешалок применяются приводы типа, изображенного на рис. 35.
От вала 1 вращение передается через две конические зубчатые передачи: через колеса 3 и 5 в одном направлении и через колеса 2 и 4 в обратном на- правлении. Если передаточные числа обеих пар одинаковы, то валы колес 4 и 5 будут вращаться с одинаковой скоростью, но в разные стороны.
Если комбинированная мешалка состоит из тихоходной и быстроходной мешалок, ставятся два независимых привода. Якорная мешалка приводится во вращение от электродвигателя через пару конических колес, а турбинная - от своего электродвигателя (валы соединены муфтами).
Если места на крышке сосуда или над ней недостаточно, привод распо- лагают под сосудом, что, однако, требует установки хорошего сальникового уплотнения.
Рис. 35. Привод комбинированной мешалки: 1 – вал; 2, 3, 4, 5 – зубчатые колеса
Для улучшения работы вала мешалки устанавливают концевой подшипник (подпятник) или промежуточные подшипники в верхней части вала мешалки. Они служат для подвижного закрепления нижнего конца вала перемешивающе- го органа. Опоры состоят (рис. 36) из стойки 1, к которой болтами 7 прикреп- лен подшипник 2, в нем закреплена штифтами 5 неподвижная втулка 4. На
58
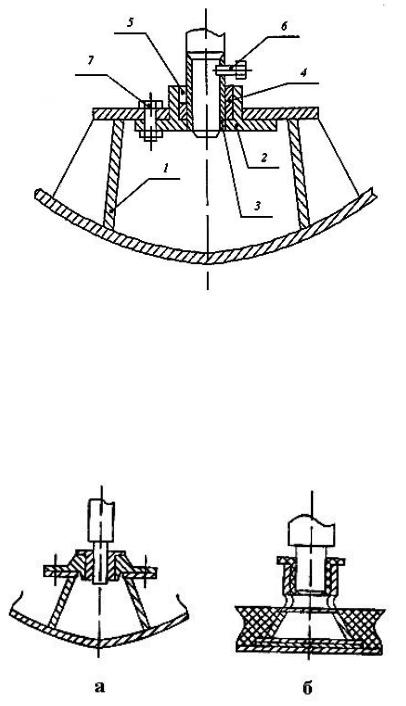
нижнем конце вала закреплена болтом 6 подвижная втулка 3, которая враща- ется вместе с валом внутри неподвижной втулки 4.
Втулки изготавливают из чугуна, графита, капрона, текстолита или фто- ропласта-4, остальные детали из углеродистой стали для нейтральных сред или из коррозионно-стойких материалов для агрессивных сред.
Рис. 36. Опоры концевые внутренние для вертикальных валов перемешивающих устройств: 1 – стойка; 2 – подшипник; 3 – подвижная втулка; 4 –
неподвижная втулка; 5 – штифты; 6,7 - болты
Концевые подшипники в аппарате работают в очень тяжелых условиях: их невозможно смазывать, они плохо доступны для осмотра и ремонта. Конст-
рукция подшипника должна обеспечивать свободную циркуляцию жидкости через него. На рисунке 37, а показан типовой концевой подшипник (подпят- ник).
Рис. 37. Концевые подшипники:
а – типовая конструкция; б – подпятник для футерованных аппаратов
Подпятник, показанный на рис. 37, б, применяется для футерованных аппаратов. Коническое основание этого подпятника обеспечивает ему высо- кую жесткость и предохраняет футеровку вблизи подпятника от разрушения.
59

При работе мешалки без концевого подшипника возможно появление крутильных колебаний консольного вала мешалки, являющихся следствием динамических нагрузок на вал от перемешиваемой среды, условий закрепле- ния вала в опорах, конструкции мешалки. При неправильном учете в процессе конструирования таких важных критериев надежности, как жесткость и вибро- устойчивость, эксплуатация аппаратов с мешалками встречает ряд затруднений.
С точки зрения распределения нагрузок наиболее рациональны приводы с концевыми подшипниками, однако, во многих случаях из-за коррозионного или абразивного действия среды их нельзя использовать, в полимерной среде тоже нельзя устанавливать подшипники.
Крепление мешалок. В простейших конструкциях лопасти приваривают не- посредственно к валу. Однако элементы крепятся на валу с помощью разъемных со- единений. Обычно мешалка состоит из ступицы, к которой привариваются лопасти. Ступица крепится на валу с помощью шпонки и стопорных устройств, препятст- вующих осевому смещению. В случае установки мешалки в середине вала ее закре- пляют стопорным винтом (рис. 34, а), при установке на конце вала - концевой гай- кой (рис. 34, б) или с помощью двух полуколец, которые закладываются в кольце- вую выточку на валу (рис. 34, в).
Муфты служат для соединения вала привода с валом мешалки. Приме- няют в основном нормализованные муфты трех типов - продольно-разъемные, зубчатые, фланцевые.
Рис. 38. Продольно-разъемная муфта:
1 – корпус; 2 – накидные фланцы; 3 – разъемное кольцо; 4 – пружины; 5 – шпильки.
Продольно-разъемные муфты применяют для жесткого соединения вы- ходного вала редуктора (мотор - редуктор) с валом перемешивающего устрой- ства с промежуточным валом при любом числе промежуточных опор. Муфта состоит (рис. 38) из корпуса 1 (образующегося двумя половинками), накидных фланцев 2 и шпилек 5 с шайбами и гайками. Соединяемые концы валов имеют
60

кольцевые проточки, на которые надето разрезное кольцо 3, половинки его скрепляются двумя пружинами 4. Сверху надеты на шпонке половины корпу- са, после затяжки шпилек фланцев получается жесткое соосное соединение ва- лов.
Зубчатые муфты применяют для соединения выходных валов мотор- редуктора и электродвигателя (гидромотора) с промежуточным валом при двух промежуточных опорах. Муфта состоит (рис. 39) из зубчатой обоймы 1, укрепленной шпонкой на валу мотор-редуктора, и зубчатой втулки 2, сидящей на шпонке на промежуточном валу. Зубья втулки входят во впадины обоймы. Муфта передает крутящий момент, но не соединяет валы жестко по оси.
Рис. 39. Зубчатая муфта: 1 – обойма зубчатая; 2 – втулка зубчатая; 3 – крышка; 4 – уплотнение; 5 – масленка.
Уплотнения вращающихся деталей
Для вывода вала мешалки из реактора используют специальные устрой- ства – уплотнения. Они должны обеспечивать возможность свободного вра- щения вала мешалки и не пропускать наружу газы и пары, находящиеся в ап- парате под давлением, или же не пропускать воздух в реактор, работающий под вакуумом. В зависимости от физико-химических характеристик и пара- метров рабочих сред, а также требований производственной санитарии и тех-
ники безопасности и пожароопасности аппараты для перемешивания жидких сред комплектуются сальниковыми или торцевыми уплотнениями и гидроза- творами или имеют герметичный привод.
Несмотря на то, что узел уплотнения занимает сравнительно небольшую часть реактора, от него зачастую зависит качество работы всей установки. Особенно это относится к производствам с ядовитыми и взрывоопасными ве- ществами и к аппаратам, работающим под вакуумом и давлением.
61
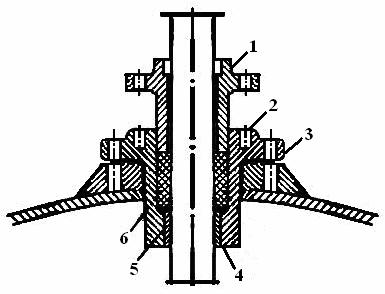
Сальники
Валы мешалок выводятся из реакционных котлов наружу через приспо- собления, называемыми сальниками. Эти приспособления обеспечивают воз-
можность свободного вращения вала мешалки и не пропускают наружу газы и пары. В технике используют весьма разнообразные сальники, однако сальники обычных реакционных аппаратов по устройству однотипны. Они состоят из сальниковой коробки (3), нажимной втулки (1), грундбуксы (5) и уплотни- тельного материала (рис. 40).
Сальниковая коробка отливается из чугуна и крепится шпильками к крышке аппарата. В сальниковую коробку вставляют грундбуксу и прочно за- крепляют ее при помощи стопорного винта. Назначение грундбуксы «направ- лять» вал мешалки, т.е. препятствовать его вибрированию и колебаниям при вращении, а также поддерживать уплотняющий материал. Зазор между валом мешалки и сальниковой коробкой заполняется уплотняющей набивкой, в каче- стве которой применяют льняную плетенку, асбестовый шнур или хлопчато- бумажные шнуры круглого или квадратного сечения, пропитанные маслом, воском, битумом, жидким стеклом, синтетическими материалами, графитом и т.д. Пропитка служит для улучшения герметизации и снижения коэффициента трения набивки о вал.
Рис. 40. Круглый сальник:
1 – нажимная втулка; 2 – шпильки; 3 – сальниковая коробка; 4 - стопорный винт; 5 – грундбукса; 6 – уплотняющий материал
При больших числах оборотов, высоких давлениях и температурах ис- пользуют сальники с твердой набивкой, выполненных из разрезанных колец цветного металла, твердых пластмасс или прессованного графита, фторопла- ста.
Нажимная втулка крепится к сальниковой коробке посредством шпилек (обычно две или четыре). При наличии двух шпилек фланцы нажимной втулки имеют форму эллипса, а при четырех – форму окружности. Сальники обычно
62
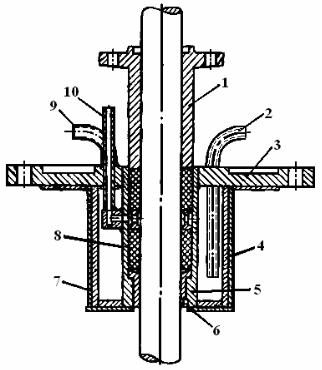
устанавливаются на бобышках. Сальниковая коробка может находиться вне аппарата или быть утоплена внутрь.
Хотя сальник, утопленный в реакторе, и позволяет несколько уменьшить высоту привода, эту конструкцию нельзя признать удачной, так как обслужи- вание такого сальника затруднено. Особенно нежелательно применять такой сальник при высокой температуре в реакторе.
При высоких температурах ускоряется процесс окисления сальниковой набивки, она теряет эластичность, нарушается ее герметичность. Другим ос-
ложняющим фактором является химическое воздействие перерабатываемых материалов.
Рис. 41. Сальник с водяным охлаждением и защитой от коррозии:
1 – нажимная втулка; 2 – трубка для подвода воды; 3 – фланец; 4 - коробка для охла- ждающей воды; 5 – корпус сальника; 6 – грундбукса; 7 – слой антикоррозионного металли- ческого покрытия; 8 – набивка; 9 – трубка для отвода воды; 10 – трубка для подвода смазки
На рис. 41 показана конструкция сальника с водяным охлаждением, за- щищенного от действия агрессивных сред. Сальник состоит из корпуса (5), при помощи которого сальник крепится к аппарату, грундбуксы (6), набивки (8), нажимной втулки (1), трубки (10) для подачи смазки и коробки (4) для ох- лаждающей воды. Вода подводится в коробку по трубке (2) и удаляется через трубку (9).
Торцовые уплотнения
Торцовые уплотнения предназначены для герметизации аппаратов, рабо- тающих под давлением, вакуумом, и валов центробежных насосов.
Торцовые уплотнения находят широкое применение, так как обладают следующими достоинствами:
63
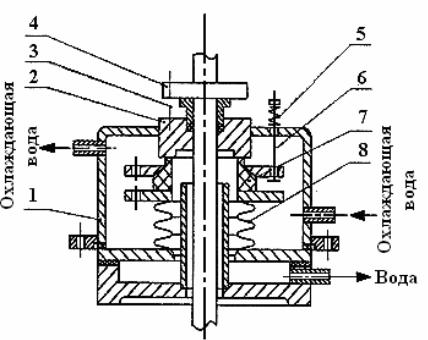
1)при нормальной их работе не требуется их обслуживания;
2)правильно подобранные торцовые уплотнения отличаются большей ус- тойчивостью и, следовательно, долговечностью;
3)торцовые уплотнения удовлетворительно работают при перекосах и бие- ниях вала;
4)торцовые уплотнения обладают высокой герметичностью.
Торцовое уплотнение состоит из двух колец – одного подвижного и дру-
гого неподвижного, которые прижимаются друг к другу по торцевой поверх- ности с помощью пружины сильфона (рис. 42).
Самым ответственным узлом торцового уплотнения является пара тре- ния. Качество уплотнения и надежность его работы зависят в основном от ма- териала и качества обработки поверхности трущихся колец. Материал, из ко- торого она изготовлена, должен обладать износостойкостью и малым коэффи- циентом трения. Обычно одно из колец изготовляется из более твердых мате- риалов. Используют следующие материалы: кислотостойкая сталь - одно кольцо; углеграфит, бронза или фторопласт – другое кольцо. Фторопласт при- меняется только в случае небольших давлений и при невысоких скоростях па- ры трения, так как он обладает хладотекучестью.
Рис. 42. Торцевое уплотнение:
1 – корпус; 2 – вращающееся кольцо; 3 – шпилька; 4 – водило; 5 - пружина; 6 – тяга; 7 – неподвижное кольцо; 8 – сильфон.
Уплотнение состоит из неподвижного кольца (7), связанного с валом с помощью хомута. Неподвижное кольцо прижимается к подвижному с помо- щью пружин и связано с корпусом с помощью сильфона (8). Водило (4) кре- пится на валу аппарата и связано шпильками с подвижным кольцом (2). Тру- щиеся детали закрыты корпусом (1), который соединяется с фланцем. Смазка
64
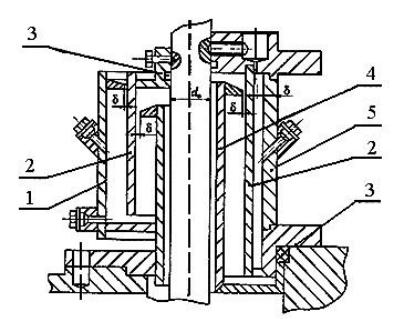
пары трения и охлаждение производится проточной водой, циркулирующей в полости корпуса.
Недостаток торцевых уплотнений – высокая стоимость и сложность ре- монта.
Гидрозатворы
Гидрозатворы представляют собой уплотнительный узел, предназначен- ный для предотвращения контакта газовой среды, заполняющей внутреннюю полость аппарата с атмосферой (рис. 43).
Гидрозатвор состоит из неподвижного цилиндрического корпуса, внутрь которого с зазором δ относительно его неподвижных элементов вставлен вра- щающийся совместно с валом мешалки цилиндрический колпак. При атмос- ферном давлении в корпусе аппарата и правильно выбранных размерах гидро- затвор надежно предохраняет уплотняемые плотности от взаимного контакта.
Рис. 43. Гидразатвор для аппаратов общего назначения (левая часть рисунка) и для малога- баритных аппаратов (правая часть рисунка): 1 – корпус; 2 – вращающийся колпак; 3 – коль- цо уплотнительное; 4 - неподвижный стакан; 5 - корпус
Манжетные уплотнения
Манжетные уплотнения применяют в аппаратах, работающих при атмо- сферном давлении и температуре до 120 оС. Конструктивно уплотнение пред- ставляет собой диск, укрепляемый на болтах над отверстием крышки, в коль- цевой проточки диска установлена стандартная манжета, герметизирующая за- зор между валом и внутренней поверхностью отверстия диска.
65
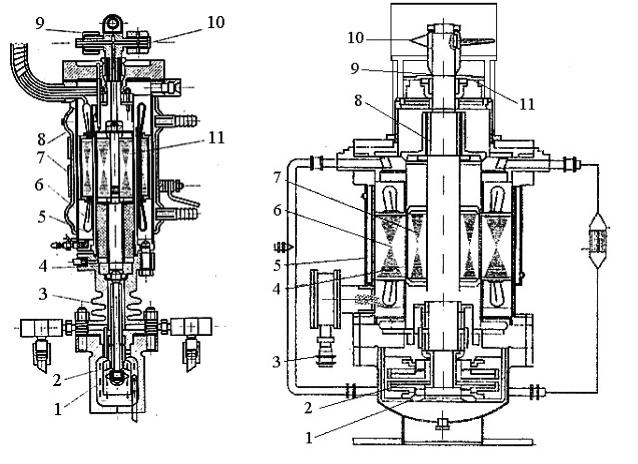
Герметичные электроприводы
Аппараты для перемешивания высокотоксичных, высокоагрессивных или пожароопасных сред обычно комплектуются герметичными электропри- водами.
Рис. 44. Аппарат с герметичным |
Рис. 45. Жидкозаполненный герметичный электро- |
приводом перемешивающего уст- |
привод на подшипниках жидкостного трения: |
ройства: |
1 – упорная пята; 2 – центробежный насос, обеспечи- |
1 – мешалка; 2 – циркуляционная |
вающий циркуляцию жидкости в приводе; |
труба; 3 – вал; 4,8 – подшипники |
3,8 – опорные подшипники жидкостного трения; |
качения; 5 – защитная гильза; 6 – |
4 – защитная гильза ротора; 5 – защитная гильза ста- |
обмотка статора; 7 – железо стато- |
тора; 6 – железо статора; 7 – железо ротора; |
ра; 9 – штуцер подвода жидкой |
9 – вал; 10 – мешалка; 11 – торцевое уплотнение |
смазки; 10 – штуцер подвода |
|
инертного газа; 11 – железо ротора. |
|
В газозаполненном электроприводе (рис. 44) ротор, вращающийся в га- зовой полости, установлен на подшипниках качения. Статорная полость элек- тродвигателя защищена от контакта с парами перемешиваемой среды тонко- стенной защитной гильзой (5). В случае необходимости защитная гильза мо- жет быть также установлена на роторе (11). В электроприводах подобного ти- па подшипники качения обычно смазывают консистентной или обычной смаз- кой, подаваемой через штуцер (9). Герметичный электропривод на подшипни- ках качения выполняется обычно газозаполненным. В качестве газа, создаю- щего этот своеобразный буфер, препятствующий контакту перемешивающей
66
среды с подшипниками качения, используется один из компонентов реакцион- ной среды или какой-либо инертный газ.
Приводы такого типа представляют собой конструкцию, в которой ак- тивные элементы ротора и статора электродвигателя защищены от воздейст- вия перемешиваемой среды с помощью специальной изоляции (мокрый ста- тор) или специальных защитных гильз (сухой статор). Герметичные электро- приводы с «мокрым» или «сухим» статором могут быть газо- и жидкостноза- полненными.
Жидкостнозаполненный герметичный электропривод (рис. 45) представ- ляет собой конструкцию, в которой используются гидростатические или гид- родинамические опоры скольжения, смазываемые перемешивающей средой, не содержащей твердых взвесей. Между рабочим пространством аппарата и внутренней полостью жидкостнозаполненного электропривода обычно уста- навливают торцевое уплотнение, уменьшающее обмен между средами, запол- няющими эти полости.
Бессальниковые приводы
В аппаратах высокого давления с бессальниковым приводом энергия пе- редается на вал мешалки посредством вращающегося магнитного поля, разви- ваемого статором асинхронного электродвигателя. Вращающее магнитное по- ле, создаваемое статором, заставляет вращаться ротор, а вместе с ним и вал мешалки.
67
Глава II ВСПОМОГАТЕЛЬНОЕ ОБОРУДОВАНИЕ
2.1. Оборудование для транспортировки и дозирования жидкости, твердых тел и газов
Успешная работа химического предприятия во многом зависит от четкой работы промышленного транспорта. Промышленный транспорт делится на две основные группы: внешний и внутренний.
Внешний транспорт - предназначен для доставки на предприятие сырья, полуфабрикатов, топлива, отправки готовой продукции и вывоза с предприятия отходов производства. Внешнезаводские транспортные операции осуществляют- ся следующими видами транспорта: железнодорожным, речным, автодорожным, воздушным.
Внутренний или внутризаводской транспорт - предназначен для распреде-
ления поступающих грузов, полуфабрикатов и готовой продукции между цехами и складами, между отдельными агрегатами и рабочими местами согласно техно- логической схеме. Внутризаводские транспортные операции осуществляются местным железнодорожным и автомобильным транспортом, а также различными подъемно-транспортными машинами. На предприятиях химической промыш- ленности транспортируются грузы различного агрегатного состояния: твердые штучные, кусковые, зерновые, порошкообразные, пастообразные, жидкие и газо- образные.
При транспортировке жидкости используют цистерны, контейнеры, бочки.
Для хранения жидкостей применяют стальные хранилища, выполнен- ные в виде горизонтальных или вертикальных цилиндрических, реже прямо- угольных резервуаров. Горизонтальные или вертикальные цилиндрические резервуары имеют сферические (выпуклые или вогнутые) или плоские дни- ща в зависимости от способа эвакуации жидкости из хранилищ.
Для хранения больших количеств минеральных кислот используют же- лезобетонные резервуары – хранилища.
Оборудование для транспортировки и дозирования твердых материалов
В связи с резким уменьшением применения ручного труда в химической промышленности возросла роль транспортных средств, особенно для твердых сыпучих материалов. При транспортировке сырья и готового продукта необ- ходимо в частности учитывать их физико-химические свойства.
Наиболее широкое применение при транспортировке больших количеств продуктов приобрели ленточные транспортеры с плоской или желобковой лентой (рис. 46). Эти транспортеры имеют барабан привода (8) и барабан на- тяжения ленты (10). Производительность их достигает до 6 т/час, при угле поднятия ленты 45о.
68
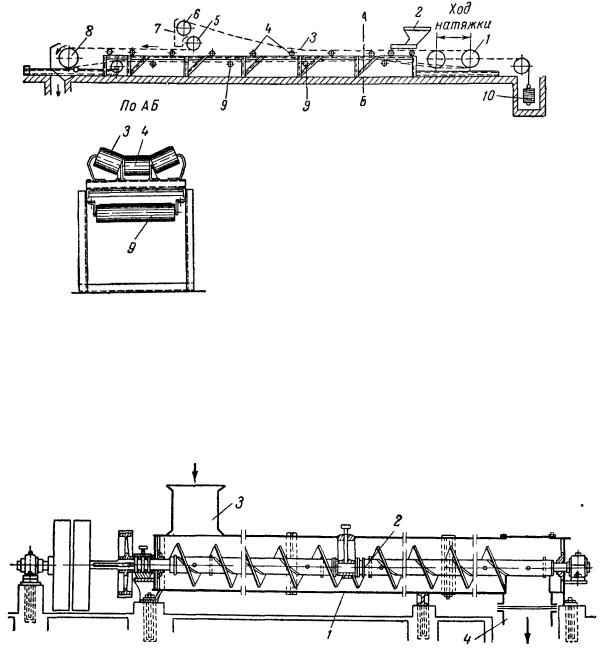
Рис. 46. Ленточный транспортер: 1 – натяжной барабан; 2 – загрузочная воронка; 3 – лента; 4,9 – опорные ролики; 5,6 – барабаны сбрасывателя; 7 – лоток; 8 – привод-
ной барабан; 10 – груз для натяжения ленты.
Наиболее широкое применение для передвижения твердых веществ на- шли винтовые транспортеры (рис. 47). Они удобны тем, что могут транспор- тировать продукты на большие расстояния, а также их удобно применять с до- зирующими устройствами.
Рис. 47. Винтовой транспортер:
1 – желоб; 2 – вал; 3 – загрузочное отверстие; 4 – разгрузочное отверстие.
Для транспортировки сыпучих материалов по вертикали применяются ковшовые элеваторы (рис. 48). Этот элеватор состоит из барабана привода (1) и барабана натяжения (6), замкнутой ленты (2), ковшов, закрепленных на лен- те (3), и каркаса (4) для защиты окружающей среды от пыли транспортируемо- го вещества.
69
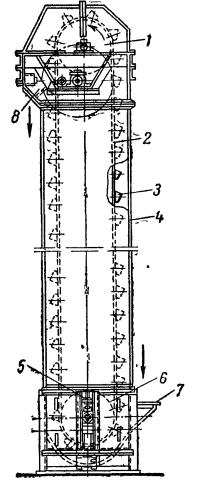
Рис. 48. Элеватор: 1 – приводной барабан; 2 – лента; 3 – ковши; 4 – кожух; 5 – винт; 6 - натяжной барабан; 7 – воронка; 8 – приемный желоб.
Пневмотранспорт (материал перемещается по трубам струей воздуха) яв- ляется наиболее эффективным видом передвижения твердых химических про- дуктов, например, по трубопроводу диаметром 100 мм можно передавать в час: 1,7 т поваренной соли, 1,4 т кальцинированной соды, 1 т чугунной струж- ки.
Косновным достоинствам этих установок следует отнести:
§полную герметичность и надежность;
§высокую скорость транспортировки;
§возможность перемещения пылевидных, гигроскопических пожароопасных материалов;
§незначительные потери материала.
Однако надо отметить, что установки пневмотранспорта не пригодны для пе- ремещения влажных и абразивных материалов.
Пневматические установки делят на всасывающие, нагнетательные и сме- шанные.
Всасывающие - это установки, в которых материал перемещается по трубам при давлении воздуха ниже атмосферного (до 0,01 MПа). Материал через сопло вместе с воздухом засасывается в трубопровод. Основное количество материала
70
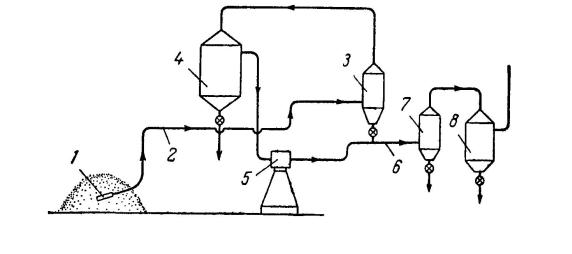
отделяется в разделителе, затем в циклоне и фильтре. В установках этого типа наблюдается большой расход энергии при всасывании, главным образом, из-за малой концентрации твердой фазы в воздухе (10 кг/кг) и высокой скорости воз-
духа (20-30 м/с).
Нагнетательные - это установки, в которых материал перемещается по тру- бам сжатым до 0,8 МПа воздухом. Установки нагнетательного типа более эконо- мичны, концентрация твердой фазы допускается до 100 кг/кг, возможно пере- мещение материала на большие расстояния (до 2000 м).
Установки смешанного типа - это установки, в которых часть трубопровода работает под разрежением, а другая часть - под давлением
Любая установка пневмотранспорта состоит из загрузочного и разгрузочно- го устройств, трубопровода, аппаратов для очистки воздуха (циклоны, фильтры) и воздуходувной машины (вакуумный насос, воздуходувка или компрессор).
Основными исходными данными для выбора и расчета транспортных уст- ройств являются:
-физико-химические характеристики насыпных грузов (дисперсность, размер кусков (зерен), удельный и насыпной вес, влажность, угол естественного отко- са, абразивность);
-токсичность, пожароопасность и взрывоопасность материала;
-температура материала;
-возможность совмещения разных технологических операций (охлаждение, сушка, доизмельчение и др.);
-траектория перемещения материала;
-производительность;
-режим работы.
На рис. 49 приведена схема пневматической установки транспортировки твердых продуктов. Установка состоит из воздуходувки или компрессора (5), всасывающего и нагнетающего трубопроводов (2, 6), системы улавливания, которая имеет циклон (3, 7) и пылеулавливатель (4, 8).
Рис. 49. Схема пневматической установки:
1 – приемное сопло; 2 – всасывающий трубопровод; 3, 7 – циклон; 4, 8 – пылеулавливатель; 5 – компрессор; 6 – нагнетательный трубопровод.
71
Перспективным способом является транспортировка сыпучих материа-
лов в псевдоожиженном состоянии с применением инертного газа или смеси воздуха с инертным газом.
Дозирование твердых веществ может производиться периодически или непрерывно, способы дозирования – взвешивание или измерение объема.
При периодическом дозировании твердых веществ обычно употребля- ются весы. Непрерывное дозирование твердых материалов осуществляется при помощи питателей и дозаторов различных конструкций. Из питателей, по конструкции мало отличающихся от представленных выше транспортеров, чаще всего применяются винтовые тарельчатые, плунжерные и ленточные пи- татели.
Оборудование для транспортировки и дозирования жидких и газообразных продуктов
Для транспортировки жидкости по внутрицеховым трубопроводам, а также от складов до места потребления, при небольшом их расположении друг от друга, применяют насосы, вакуум, сжатый воздух или инертный газ, т. е. следующими способами:
-объемными насосами - путем вытеснения жидкости из замкнутого пространства насоса телами, движущимися возвратно-поступательно или вращательно;
-лопастными или центробежными насосами - за счет центробежной силы, возни- кающей в жидкости при вращении лопастных колес;
-вихревыми насосами - за счет интенсивного образования и разрушения вихрей, возникающих при вращении рабочего колеса;
-струйными насосами - за счет движущейся струи воздуха, воды или пара;
-газлифтами (эрлифтами) - пневматическими подъемниками, в которых ис- пользуется сжатый воздух или технический газ;
-монтежю и сифонами - перемещение жидкости под давлением воздуха, пара или газа.
Однако перемещение жидкостей с помощью сжатого воздуха или вакуу- ма ограничено ввиду их существенных недостатков.
Наиболее широкое применение находят поршневые и лопастные насосы. Поршневые насосы рекомендуется применять для перекачивания не- больших количеств жидкости при высоких напорах, а также для перекачива- ния вязких и текучих горячих и холодных жидкостей. К поршневым насосам относятся приводные /ГОСТ 12052-66/, паровые /ГОСТ 11376-71/ и дозиро-
вочные.
Из лопастных насосов более широко применяются центробежно-кон- сольные и центробежно-погружные. Центробежно-консольные выпускаются типа Х /ГОСТ 10168-68/, 2Х – 6Т-1, 6Х-9Т-1 и ряд других.
Для перекачивания агрессивных жидкостей применяются погружные центробежные насосы (рис. 50). Насос устанавливается на люке аппарата, мон- тежю, к которому прикрепляется с помощью фланца (3).
72
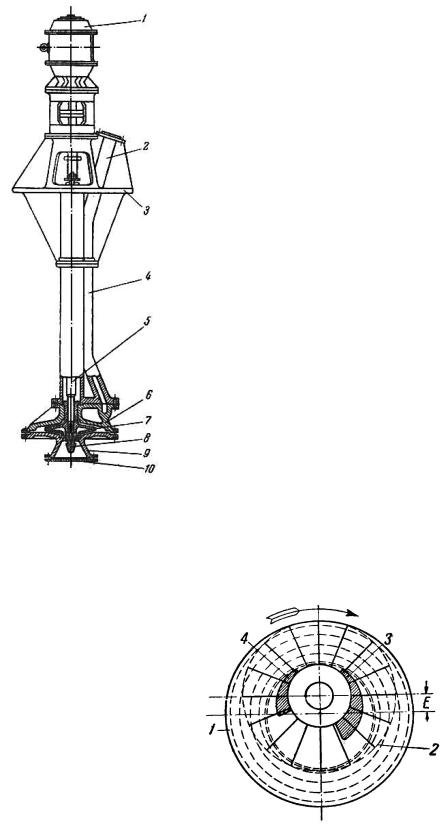
|
Насос состоит из корпуса (4), вала (5), турбинки (7), |
|
защитной втулки (8), всасывающего патрубка (9), |
|
решетки (10), нагнетательного штуцера (2), улитки |
|
(6). На крышке насоса установлен электродвигатель |
|
(1). Насосы изготовляются из серого чугуна или |
|
кислотостойкой стали. Глубина погружения насо- |
|
сов 2,5 – 3,3 м. При использовании погружных цен- |
|
тробежных насосов удается предотвратить утечку |
|
жидкостей через сальниковое уплотнение, в отли- |
|
чие от центробежно-консольных насосов. Произво- |
|
дительность выпускаемых насосов от 3 до 20 м3/ч, |
|
создаваемый напор до 30 метров. |
|
Сжатый воздух получают обычно поршневыми |
|
компрессорами, а вакуум – водокольцевым ротаци- |
|
онным вакуум-насосом, схема которого изображена |
|
на рис. 51. |
|
Корпус (1) вакуумного насоса заливается напо- |
|
ловину водой. При вращении ротора (2) она отбра- |
|
сывается к внутренним стенкам корпуса, образуя |
|
вращающееся жидкостное кольцо, вследствие экс- |
|
центричного размещения ротора в корпусе, созда- |
|
ется свободное серповидное пространство, перего- |
Рис. 50. Погружной центро- |
раживаемое лопатками на изолированные камеры. |
бежный насос |
Газ всасывается через отверстия (4), расположен- |
|
ные в самой свободной части серповидного прост- |
ранства, и при дальнейшем перемещении, благодаря непрерывно уменьшаю- щемуся свободному объему камер, сжимается и через отверстие (3) выталки- вается в нагнетательный газопровод.
Рис. 51. Схема водокольцевого ротационного вакуум-насоса:
1 – корпус; 2 – ротор; 3 – нагнетательное отверстие; 4 - всасывающее отверстие.
Компрессоры - это машины, предназначенные для перемещения газа и по- вышения его давления.
73
Компрессорные машины, в зависимости от создаваемой степени сжатия, т.е. отношения давления на выходе из нагнетательного патрубка к давлению на входе во всасывающий патрубок и наличия охлаждения газа в процессе сжатия, делятся на три класса:
-вентиляторы (степень сжатия 1-1,1);
-газодувки (степень сжатия 1,1-4);
-компрессоры (степень сжатия более 4).
Наибольшее распространение в химической промышленности получили лопастные машины для транспортировки жидкостей и газов, так как они обла- дают рядом преимуществ перед поршневыми:
-более равномерная подача жидкости и газа;
-простота устройства и компактность;
-надежная работа при небольших давлениях и высокой производительности;
-возможность перекачивания агрессивных жидкостей и жидкостей (газов), со- держащих твердые частицы.
Кнедостаткам центробежных машин следует отнести сравнительно не- большой КПД и некоторое уменьшение производительности при увеличении на- пора. Однако, несмотря на отмеченные недостатки, центробежные машины по- степенно вытесняют поршневые в области умеренных давлений.
Поршневые машины применяются, главным образом, когда требуется пе- рекачивать небольшие количества жидкости под большим (до 15 МПа и более) давлением.
Для транспортировки больших количеств жидкости с небольшими напора- ми (до 10 - 15 м) применяют осевые (пропеллерные) насосы. Осевые насосы имеют высокий КПД, компактны, быстроходны могут использоваться для пе- рекачивания загрязненных и кристаллизующихся жидкостей. Осевые компрес-
соры применяют для сжатия любых газов при больших производительностях и относительно высоких давлениях.
Для перекачивания высоковязких жидкостей, топлив, нефтепродуктов в области подач до 300 м3/ч и давлений до 20 МПа применяют винтовые насосы, эти машины компактны, бесшумны, быстроходны, их КПД составляет 0,75-0,8.
Для перекачивания вязких жидкостей, не содержащих твердых примесей, при высоких давлениях и производительности 300—360 м3/ч используют шесте- ренные насосы.
Пластинчатые насосы используются для транспортировки чистых, без твер-
дых примесей, жидкостей при умеренных давлениях и производительности 300350 м3/ч.
Вихревые насосы - просты, компактны и используются для перемещения маловязких жидкостей с напором до 250 м и сравнительно высокой производи- тельностью.
Поршневые компрессоры высокого давления используются в технологиче- ских схемах синтеза технических газов, для обдувки поверхностей нагрева ко- тельных агрегатов и др.
74
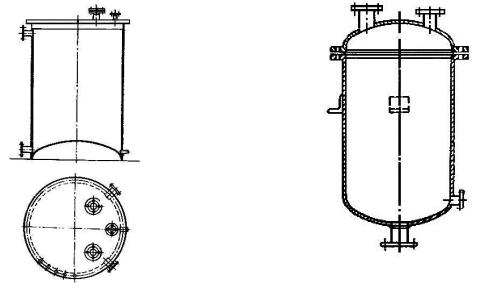
Струйные насосы, монтежю, подъемники чаще всего используются в тех случаях, когда недопустимо наличие движущихся и трущихся частей при перека- чивании агрессивных и пожароопасных жидкостей.
Выбор насоса должен производиться для конкретных условий работы на основе гидравлического расчета с учетом экономических требований и свойств транспортируемой жидкости или газа.
Отмеривание жидкостей в производственных условиях производится пе- риодически (мерниками) или непрерывно с помощью специальных приборов. К мерникам предъявляется ряд требований: полная эвакуация жидкости из мерника, наличие штуцеров для слива жидкости в емкость для хранения, по- вышенная точность отмеривания, установка контролирующих средств по от- мериванию, возможность необходимого предварительного отстаивания со- держимого мерника и т.д.
Материалами для изготовления мерников служат сталь, алюминий, спла- вы титана. Внутреннюю поверхность мерников в случае необходимости гум- мируют или футеруют. Мерники с плоскими днищами наиболее простые и дешевые. Применяют их в тех случаях, когда к операции не предъявляют спе- циальных требований. Эти мерники также не рассчитаны на работу под давле- нием. Мерники с коническими днищами применяются в тех случаях, когда при отмеривании требуется полное удаление жидкости или предварительное от- стаивание.
На рис. 52 и 53 представлены мерники с вогнутыми и сферическими днищами.
Рис. 52. Мерник с вогнутым днищем и пло- |
Рис. 53. Мерник со сферическими днищем и |
ской крышкой |
крышкой |
Мерники с вогнутыми днищами и плоскими крышками применяются при таких операциях, когда требуется полная эвакуация жидкости. Такие мер- ники несколько удобнее при монтаже, чем мерники с коническими днищами.
Мерники со сферическими днищами и крышками служат для отмеривания при разрежении или под давлением.
75