
Тех.маш.Ч
.1.pdfМинистерство образования и науки Российской Федерации Федеральное агентство по образованию Южно-Уральский государственный университет Кафедра «Технология машиностроения»
621(07) К906
В.Л. Кулыгин, В.И. Гузеев, И.А. Кулыгина
Технология машиностроения
Учебное пособие
Часть 1
Допущено Учебно-методическим объединением вузов по образованию в области автоматизированного машиностроения (УМО АМ) в качестве учебного пособия для студентов высших учебных заведений, обучающихся по направлению «Технология, оборудование и автоматизация машиностроительных производств» и специальности «Технология машиностроения» направления «Конструкторско-технологическое обеспечение машиностроительных производств»
Челябинск Издательский центр ЮУрГУ
2010
УДК 621.002. 2(075.8) К 906
Одобрено учебно-методической комиссией механико-технологического факультета
Рецензенты: д.т.н. проф. Султан-Заде Н.М., к.т.н. доц. Звонарёва Л.М.
Кулыгин, В.Л.
Технология машиностроения: учебное пособие / В.Л. Кулыгин, В.И. Гузеев, И.А. Кулыгина. – Челябинск: Изд-во ЮУрГУ, 2008. – Ч. 1. –
93с.
Вучебном пособии рассматриваются вопросы выбора способов получения заготовок, вопросы построения технологических процессов механической обработки различных групп деталей, особенности их базирования, обработки и контроля. Приведены типовые технологические процессы изготовления деталей-представителей.
Пособие рекомендуется для студентов направлений 150900, 151000, специальностей 151001, 151002, 151003, 220501 и других технологических и конструкторских специальностей.
При написании пособия использовались источники [1–10].
УДК 621.002.4(075.8)
© Издательский центр ЮУрГУ, 2010
2
ОГЛАВЛЕНИЕ
I СПОСОБЫ ПОЛУЧЕНИЯ ЗАГОТОВОК ДЕТАЛЕЙ МАШИН
1. ОСНОВНЫЕ ПРИНЦИПЫ ВЫБОРА СПОСОБА ПОЛУЧЕНИЯ ЗАГОТОВОК ПРИ ПРОЕКТИРОВАНИИ ТИПОВЫХ ТЕХНОЛОГИЧЕСКИХ ПРОЦЕССОВ….…...6
2.МАТЕРИАЛЫ, ИСПОЛЬЗУЕМЫЕ ПРИ ПОЛУЧЕНИИ ЗАГОТОВОК………………6
3.ОСНОВНЫЕ МЕТОДЫ ПОЛУЧЕНИЯ ЛИТЫХ ЗАГОТОВОК
3.1.Литьё в песчаные формы…………………………………………….………7
3.2.Литьё в оболочковые формы…….………………………………………….8
3.3.Литьё по выплавляемым моделям………………………….……………….9
3.4.Литьё в металлические формы (копили)…………………….……………10
3.5.Литьё под давлением………………………………………….……………10
3.6.Центробежное литье………………………………………….…………….11
3.7.Литьё в вакуумных печах…………………………………….…………….12
3.8.Литьё непрерывным способом……………………………….……………13
4.ОСНОВНЫЕ МЕТОДЫ ПРОИЗВОДСТВА ПОКОВОК
4.1.Штамповка на молотах…..…………………………………………………14
4.2.Штамповка на кривошипном горячештамповочном прессе
(КГШП)………………………………………………………………………15
4.3.Штамповка на горизонтально-ковочной машине (ГКМ)…..…………….16
4.4.Штамповка на ковочных вальцах…………………………….……………17
4.5.Штамповка на обжимных ковочных машинах…………….……………..17
4.6.Штамповка на высокоскоростных штамповочных молотах….…………18
4.7.Штамповка жидкого металла…………………………………….………..18
4.8.Холодная штамповка…………………………………………….…………19
4.9.Порошковое прессование……………………………………….………….20
5.ОСНОВНЫЕ МЕТОДЫ ПОЛУЧЕНИЯ ЗАГОТОВОК ДЕТАЛЕЙ ИЗ ПЕРИОДИЧЕСКОГО ПРОКАТА……………………………………………….21
II.ТЕХНОЛОГИЧЕСКИЕ ОСОБЕННОСТИ ИЗГОТОВЛЕНИЯ ВАЛОВ
1.ТИПОВЫЕ ТЕХНИЧЕСКИЕ ТРЕБОВАНИЯ, ПРЕДЪЯВЛЯЕМЫЕ К ДЕТАЛЯМ КЛАССА «ВАЛЫ»……………..………………………………………..…………………22
2.ВЫБОР СПОСОБА ПОЛУЧЕНИЯ ЗАГОТОВОК ДЕТАЛЕЙ
ИИХ ПРЕДВАРИТЕЛЬНАЯ ОБРАБОТКА…………………………….………..……..23
3.ХИМИКО-ТЕРМИЧЕСКИЕ МЕТОДЫ ОБРАБОТКИ ВАЛОВ………………..……28
3.1.Закалка токами высокой частоты (ТВЧ)…..………………………………28
3.2.Цементация, азотирование и цианирование….……….…………………..28
4.ЧЕРНОВЫЕ И ПОЛУЧИСТОВЫЕ МЕТОДЫ ОБРАБОТКИ ВАЛОВ…………..…...30
4.1.Особенности обработки валов одним резцом…………………………….30
4.2.Многорезцовая обработка валов…………………………………………..32
4.3.Особенности обработки гладких и нежестких валов…………………….36
3
5.ЧИСТОВЫЕ МЕТОДЫ ОБРАБОТКИ ВАЛОВ……………………………….……37
5.1.Тонкое точение валов………………………………………………………37
5.2.Круглое шлифование валов………………………………………………..38
6.ОТДЕЛОЧНЫЕ МЕТОДЫ ОБРАБОТКИ ПОВЕРХНОСТЕЙ ВРАЩЕНИЯ
НА ВАЛАХ……………………………………………………………..……....….42
7.ИЗГОТОВЛЕНИЕ НА ВАЛАХ ШПОНОЧНЫХ КАНАВОК………………………..46
8.ОБРАБОТКА ШЛИЦЕВЫХ ПОВЕРХНОСТЕЙ НА ВАЛАХ………………………...49
8.1.Технология обработки шлицев на валах при центрировании по внутреннему диаметру вала…………………………………………….50
8.2.Технология обработки шлицев на валах при центрировании по наружному диаметру вала………………………………………………52
8.3.Технология обработки шлицев на валах при центрировании по боковым сторонам шлица………………………………………………52
8.4.Технология обработки шлицев на валах методами накатывания………………………………………………………………...53
9.КОНТРОЛЬ КАЧЕСТВА ВАЛОВ………………………………………………….54
III.ТЕХНОЛОГИЧЕСКИЕ ОСОБЕННОСТИ ИЗГОТОВЛЕНИЯ МНОГООСНЫХ ДЕТАЛЕЙ
1.ИЗГОТОВЛЕНИЕ ДЕТАЛЕЙ ТИПА «КОЛЕНЧАТЫЙ ВАЛ»
1.1.Типовые технологические требования, предъявляемые
кколенчатым валам………………………………………………………...56
1.2.Способы получения заготовок и исходные материалы для коленчатых валов………………………………………………………57
1.3.Особенности методов базирования коленчатых валов…………………..59
1.4.Типовой технологический процесс изготовления коленчатого вала в серийном производстве……………………………………………..60
1.5.Контроль качества коленчатых валов……………………………………..68
2.ИЗГОТОВЛЕНИЕ ДЕТАЛЕЙ ТИПА «ПОРШЕНЬ»
2.1.Типовые технические требования, предъявляемые
кпоршням…………………………………………………………………...68
2.2.Способы получения заготовок и исходные материалы поршней……………………………………………………………………..70
2.3.Технологические особенности базирования поршней…………………...70
2.4.Типовой технологический процесс изготовления поршня
всерийном производстве…………………………………………………..71
2.5.Контроль качества поршней……………………………………………….74
3. ИЗГОТОВЛЕНИЕ ДЕТАЛЕЙ ТИПА «ШАТУН»
3.1.Типовые технические требования, предъявляемые к шатунам……………………………………………………………………75
3.2.Способы получения заготовок и исходные материалы шатунов…………………………………………………………….………..76
3.3.Типовой технологический процесс изготовления шатуна
4
в серийном (крупносерийном) производстве……………………………..77
3.4.Особенности обработки плоскостей стыка шатуна и крышки…………………………………………………………………….79
3.5.Контроль качества шатунов………………………………………………..80
IV. ТЕХНОЛОГИЧЕСКИЕ ОСОБЕННОСТИ ИЗГОТОВЛЕНИЯ ВТУЛОК…….…………………………………………………………………81
1.ИЗГОТОВЛЕНИЕ ДЕТАЛЕЙ ТИПА «ВТУЛКА ЦИЛИНДРА» ДВС
1.1.Типовые технические требования, предъявляемые
квтулке цилиндра…………………………………………………………..81
1.2.Способы получения заготовок и исходные материалы втулок……………………………………………………………….……….82
1.3.Технологические схемы изготовления чугунных и стальных втулок в серийном производстве…………………………………………..83
1.4.Контроль качества втулок ДВС……………………………………………88
2.ИЗГОТОВЛЕНИЕ ДЕТАЛЕЙ ТИПА «ПОРШНЕВОЙ ПАЛЕЦ»
2.1.Типовые технические требования, предъявляемые
кпоршневым пальцам……………………………………………………...89
2.2.Способы получения заготовок и исходные материалы поршневых пальцев………………………………………………………...90
2.3.Типовой технологический процесс изготовления поршневых пальцев………………………………………………………...90
БИБЛИОГРАФИЧЕСКИЙ СПИСОК……………………………………………93
5
I. СПОСОБЫ ПОЛУЧЕНИЯ ЗАГОТОВОК ДЕТАЛЕЙ МАШИН
1. ОСНОВНЫЕ ПРИНЦИПЫ ВЫБОРА СПОСОБА ПОЛУЧЕНИЯ ЗАГОТОВОК ПРИ ПРОЕКТИРОВАНИИ ТИПОВЫХ ТЕХНОЛОГИЧЕСКИХ ПРОЦЕССОВ
На этапе проектирования технологического процесса технолог в качестве первоочередной решает задачу выбора способа получения заготовки. Основными исходными данными для решения этой задачи являются:
–рабочий чертеж детали и технические требования на ее изготовление;
–сборочный чертеж узла с описанием условий работы детали в этом узле;
–материал детали с указанием пределов его физико-механических свойств;
–годовая программа и серийность выпуска.
Для одной и той же конструкции детали можно использовать различные заготовки в виде отливок, поковок или проката. Каждый из этих видов заготовок может быть получен различными методами в зависимости от материала, массы, конфигурации и габаритных размеров детали, технологических требований по точности и шероховатости, размеров партии детали и т.д.
Главным при выборе заготовки является обеспечение заданного качества готовой детали при ее минимальной себестоимости. Себестоимость детали определяется суммированием себестоимости заготовки по калькуляции заготовительного цеха и себестоимости ее последующей обработки до достижения заданных требований качества по чертежу. Выбор заготовок связан с конкретным техникоэкономическим расчетом себестоимости готовой детали.
Необходимо учитывать, что сложные методы получения заготовки, обеспечивающие ее высокую точность, приводят к удорожанию производства и увеличению сроков его окупаемости. И наоборот, простые методы получения неточных заготовок обеспечивают меньшую себестоимость их изготовления.
С другой стороны, более точная заготовка требует меньших производственных затрат на ее дальнейшую обработку до получения готовой детали (вплоть до возможности получения готовой детали на заготовительных операциях). И поэтому решение задачи формообразования деталей целесообразно перенести на заготовительную стадию и тем самым снизить расход материала, уменьшить долю затрат на механическую обработку в себестоимости готовой детали.
Таким образом, технологу необходимо рассматривать несколько возможных вариантов различных методов получения заготовки для проектируемого технологического процесса с учетом технико-экономического принципа проектирования, а именно: получения заготовки требуемой точности с минимальными затратами на производство готовой детали.
2. МАТЕРИАЛЫ, ИСПОЛЬЗУЕМЫЕ ПРИ ПОЛУЧЕНИИ ЗАГОТОВОК
В современном машиностроении для получения исходных заготовок используется весьма широкий спектр металлических и неметаллических основных материалов:
6
–чугуны (железоуглеродистые сплавы с содержанием углерода от 2,14% до 6,67%) – белые, серые (марок от СЧ 15 до СЧ 35), ковкие (КЧ 45–6), специальные высокопрочные легированные (ВЧ 38–17, ВЧ 45–5, ВЧ 50–2, ВЧ 60–2), в том числе с вермикулярной и шаровидной формой графита;
–низкоуглеродистые конструкционные стали обычного качества (Ст0, Ст3 и
т.д.);
–качественные конструкционные стали (сталь 10, сталь 20, сталь 35, стали 40, сталь 45 и т.д.);
–конструкционные стали, легированные хромом, никелем, молибденом, вольфрамом, ванадием с однокомпонентным (15Х, 20Х, 40Х, 65Г, 60С2) и многокомпонентным легированием (12ХН3А, 20ХГС, 18Х2Н4МА, 38ХМЮА и т.д.);
–алюминий (А00, А0, А1, А2 и А3);
–сплавы алюминиевые литейные (ГОСТ 1583-93) на основе систем:
–алюминий-кремний-магний – АК–12 (АЛ2), АК–7, АК–8 (АЛ34), АК7ч (АЛ9) и т.д.;
–алюминий-кремний-медь – АК5М (АЛ5), АК5М7, АК8М (АЛ32) и т.д.;
–алюминий-медь АМ5 (АЛ19) и т.д.;
–алюминий-магний АМг5К (АЛ13) и т.д.;
–медь (МО, М1, М2, М3 и М4);
–сплавы меди с оловом, свинцом, кремнием, алюминием (бронза БрАЖ9,
БрАМц9, БрАЖН10–4–4, БрОФ10–1, БрОЦС4–4–4) и т.д.;
–сплавы меди с цинком – латуни (обычные ЛС59, Л62 и т.д., и специальные типа ЛМцОС58–2–2–2);
Из неметаллических материалов для прокладок и уплотнений при сборке узлов
имеханизмов машин используются: графит, картон, паронит, кабельная бумага, маслостойкие резины (МБС), тепломорозокислотощелочностойкие резины (ТМКЩ), асбостальной лист, отдельные разновидности пластмасс, в том числе слоистые фенопласты (текстолит, асботекстолит, стеклотекстолит).
Выбор конкретной марки основного материала и назначение пределов физикомеханических свойств к нему для той или иной детали – прерогатива конструктора, учитывающего особенности работы детали в механизме и усилия, действующие на нее в процессе эксплуатации.
Для технолога машиностроения важен фактор обрабатываемости конкретного материала, а также особенности его поведения в процессе термической и механической (в том числе лезвийной) обработок.
3. ОСНОВНЫЕ МЕТОДЫ ПОЛУЧЕНИЯ ЛИТЫХ ЗАГОТОВОК
3.1. Литьё в песчаные формы
Литъё в песчаные формы – старый и универсальный способ, позволяющий получать заготовки из различных материалов в широком диапазоне размеров.
Песчаные литейные формы и стержни служат один раз, они изготовляются из формовочных и стержневых смесей, в состав которых входят: песок, глина, вода,
7
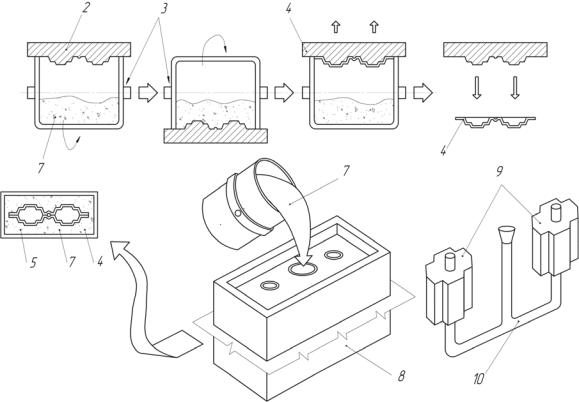
связующие и противопригарные добавки. Удачный подбор состава смеси обеспечивает ей хорошую пластичность, прочность, противопригарность, газопроницаемость и податливость, неудачный – приводит к образованию в отливках дефектов в виде наружных и внутренних раковин, поверхностной корки и горячих трещин.
Данный метод используется для получения заготовок с точностью 14–16 квалитет, шероховатостью Ra = 80 мкм и более, с минимальной толщиной стенки: 12 мм – для стальной отливки, 8 мм – для чугунной отливки, 5 мм – для алюминиевых сплавов.
Достоинство метода: возможность получения заготовок сложной конфигурации любой массы при относительно низкой себестоимости отливок.
Недостатки метода: невысокая точность изготовления и низкая прочность стальных деталей из-за литой зернистой структуры, имеющей внутренние дефекты в виде скрытых полостей, газовых и песочных раковин, трещин, коробления, неравномерной прочности в разных частях и сечениях.
3.2. Литьё в оболочковые формы
Литъё в оболочковые формы применяется для получения отливок простой формы из черных металлов и цветных сплавов (рис. 1.1).
Рис. 1.1. Литьё в оболочковые формы:
1 – смесь кварцевого песка и смолы; 2 – модельная плита; 3 – бункер; 4 – оболочка; 5 – опока; 6 – дробь; 7 – расплав; 8 – литейная форма; 9 – отливка; 10 – литник
8

Процесс литья основан на свойстве ряда термореактивных синтетических смол при небольших температурах (до 70ºС) плавиться и совместно с кварцевым песком образовывать оболочковую форму толщиной 6–10 мм.
Затем в другой печи эта оболочка нагревается до 700ºС, смола необратимо затвердевает и получаются две полуформы по формовочной модели, которые обладают хорошей газопроницаемостью и малой теплопроводностью. После получения эти две полуформы склеиваются, размещаются в опоке и заливаются расплавом металла (рис. 1.1).
Например, литьём в оболочковые формы получаются заготовки чугунных коленчатых валов автомобильных и тракторных двигателей внутреннего сгорания.
Данный метод более точный, по сравнению с литьем в песчаные формы. Точность получаемых размеров 10–12 квалитет, шероховатость Ra = 5–10 мкм.
3.3. Литьё по выплавляемым моделям
Литъё по выплавляемым моделям применяется для получения мелких стальных заготовок простой и сложной формы. Модели для изготовления неразъёмных форм получаются из легкоплавких материалов, таких как смесь стеарина и парафина, в специальных пресс-формах и собираются в блок, имеющий общую литниковую систему. Полученные блоки покрываются огнеупорной суспензией и обсыпаются песком. Затем смесь парафина и стеарина выплавляется, оболочка обжигается в печи, и в нее заливается расплав (рис. 1.2).
Точность получаемых размеров 10–12 квалитет, шероховатость – Ra = 5–10 мкм. Данный метод позволяет получать отливки, не требующие дальнейшей механической обработки.
Возможно получение отливок с минимальной толщиной стенки для стальных заготовок – 2…2,5 мм.
а) |
б) |
Рис. 1.2. Литьё по выплавляемым моделям:
а) керамическая форма – оболочка; б) возможные изделия
9

3.4. Литьё в металлические формы (кокили)
Кокиль – это металлическая форма многократного использования (рис. 1.3). Этот метод применяется для получения заготовок из алюминиевых сплавов, чугуна и простой углеродистой стали. Для получения отверстий в заготовках для таких форм могут изготавливаться песчаные стержни, а получаемые с помощью таких стержней отверстия не имеют литейных уклонов. Минимальная толщина стенки: 2,0–2,5 мм для алюминиевых сплавов, а для чугуна – 1,2–2,0 мм.
Достоинство метода:
–метод в 2…3 раза производительнее по сравнению с литьём в песчаные фор-
мы;
–отсутствие формовочной смеси.
Недостатки метода: высокая стоимость изготовления форм при их невысокой эксплуатационной стойкости (выдерживают изготовление до 300 мелких или 50 крупных отливок).
а) |
б) |
Рис. 1.3. Литьё в кокиль: а) кокиль; б) отливка
3.5. Литьё под давлением
Литъё под давлением применяется для получения сложных тонкостенных отливок из цветных сплавов, реже из чугуна и стали. Литьё осуществляется на специальных машинах в пресс-формах. Жидкий металл сжимается поршнем и подаётся под давлением в разъёмную металлическую форму (рис. 1.4, см. с. 11).
Достоинства метода: высокая точность 10–11 квалитет, шероховатость – Rа ≈ 5 мкм (можно получать резьбу в отверстии), минимальная толщина стенки для алюминиевого сплава – 1,5 мм, высокая производительность (300–400 отливок в час), часто не требуется дальнейшая механическая обработка.
10