
ves_kurs / practicum
.pdf
Чтобы обеспечить нужное натяжение ленты для передачи ей движения трением, применяют винтовое или грузовое устройство.
2.2 Расчет ленточного конвейера.
По заданной производительности (таблица 2.11) определяем площадь поперечного сечения материала на ленте конвейера:
F |
П |
|
|
||
3,6 |
,
(2.1)
где П – производительность конвейера, т/ч; |
|
|
|
|
|
|||||||||
|
– скорость движения ленты в зависимости от транспортируемого мате- |
|
||||||||||||
риала (по табл.2.1), м/с; |
|
|
|
|
|
|
|
|
||||||
– насыпная плотность материала, кг/м3 (по табл. 2.2). |
|
|
|
|||||||||||
Таблица 2.-Скорость движения ленты от вида транспортируемого материала |
|
|||||||||||||
|
|
|
Транспортируемый материал |
|
|
|
υ, м/с |
|
||||||
Крупнокусковые абразивные грузы (руда) |
|
|
|
|
|
|
1,6-3,15 |
|
||||||
|
|
|
|
|
|
|
||||||||
Среднекусковые абразивные грузы (камень, щебень) |
|
|
|
1,6-4,0 |
|
|||||||||
|
|
|
|
|||||||||||
Малоабразивные кусковые грузы (кокс, уголь) |
|
|
|
|
|
|
1,6-5,0 |
|
||||||
|
|
|
|
|
|
|
||||||||
Абразивные мелкокусковые и зернистые грузы (песок, гравий, земля) |
|
2,5-6,3 |
|
|||||||||||
|
|
|||||||||||||
Пылевидные грузы (цемент, гипс, мел, бентонит, печная пыль) |
|
0,8-1,25 |
|
|||||||||||
|
|
|||||||||||||
Примечание – Значение скорости следует выбирать из нормативного ряда ско- |
|
|||||||||||||
ростей ГОСТ 22644-77; 0,8; 1,25; 1,6; 2,5; 3,15; 4,0; 5,0; 6,3. |
|
|
|
|
|
|||||||||
|
|
|
Таблица 2.2-Насыпная плотность груза |
|
|
|
||||||||
Вид груза |
|
|
ρ, кг/м3 |
|
Вид груза |
|
ρ, кг/м3 |
|
|
Вид груза |
|
ρ, кг/м3 |
|
|
Руда |
|
|
1750 |
|
Уголь |
|
1300 |
|
|
Цемент |
|
1300 |
|
|
|
|
|
|
|
|
|
|
|||||||
Камень |
|
|
1900 |
|
Песок |
|
1550 |
|
|
Мел |
|
950 |
|
|
|
|
|
|
|
|
|
|
|||||||
Щебень |
|
|
1700 |
|
Гравий |
|
1800 |
|
|
Гипс |
|
1100 |
|
|
|
|
|
|
|
|
|
|
|||||||
Кокс |
|
|
650 |
|
Земля |
|
1250 |
|
|
|
|
|
|
|
|
|
|
|
|
|
|
|
|
|
|
Определяем ширину ленты по одной из формул (2.2)-(2.4) в зависимости от формы ленты (рис. 2.2). Форма ленты выбирается по последней цифре зачетки(рис. 2.2,а – 0,1,2; рис.2.2,б – 3,4,7; рис 2.2,в – 5,6,8,9).
Лента плоская без бортов (рис. 2.2, а), м:
В |
F |
|
|
, |
|
0,25 С K |
2 |
tg |
|||
|
|
||||
|
|
3 |
|||
|
|
|
|
(2.2)
где С – коэффициент, учитывающий уменьшение площади сечения от ссыпания материала назад при транспортировании его наклонным конвейером выбираем
по таблице 2.3. |
|
|
|
|
|
|
|
|
|
|
||
|
|
3 – угол при основании площади поперечного сечения материала равен 15о, а |
||||||||||
tg 3 |
=0,27. |
|
|
|
|
|
|
|
|
|
|
|
|
|
Таблица 2.3-Величина коэффициента С |
|
|
|
|
||||||
|
|
Угол наклона транспортера β, рад |
0-0,175 |
|
0,1925-0,2625 |
|
0,28-0,385 |
|
|
|||
|
|
Коэффициент С |
|
1 |
|
|
0,97 |
|
|
0,9 |
|
|
11

|
|
|
|
|
а) |
б) |
в) |
|
|
|
Рис. 2.2-Размещение транспортируемого материала на ленте при различных формах поперечного сечения конвейера
а – плоская лента без бортов; б – плоская лента с бортами; в – желобчатая лента
Плоская лента с бортами (рис.2.2, б), м:
В |
F |
|
|
|
|||
2 |
|
|
|
|
|
||
0,25 c K |
tg |
|
K E |
||||
|
3 |
||||||
|
|
|
|
|
|
||
где Е – отношение, численно равное |
h |
|
0,25. |
||||
B |
|||||||
|
|
|
|
Желобчатая лента (рис.2.2, в), м:
,
(2.3)
В |
|
|
|
F |
|
|
2 |
tg |
|
|
(K |
2 |
|
|
|
|||||
|
0,25[c K |
3 |
|
|||
|
|
|
|
|
|
K |
2 |
)tg ] |
|
1 |
|||
|
|
,
(2.4)
где К1 – отношение, численно равное |
B |
0,38; |
|
|
|
|||||||
1 |
|
|
|
|||||||||
|
|
|
|
|
|
|
|
|
|
|
|
|
|
|
|
|
|
|
|
B |
о |
|
|
|
|
– угол наклона боковых стенок |
|
|
|
|
|
|||||||
|
|
|
=30 , tg 0,58; |
|
|
|
||||||
К – отношение, численно равное |
B |
0,85. |
|
|
|
|||||||
|
0 |
|
|
|
||||||||
|
|
|
|
|
|
|
|
|
|
|
|
|
|
|
|
|
|
B |
|
|
|
|
|
|
|
Значение полученной ширины ленты уточняем в сторону увеличения из таб- |
||||||||||||
лиц 2.4 и 2.5 для дальнейших расчетов. |
|
|
|
|
|
|
|
|
|
|||
|
|
|
Таблица 2.4-Характеристика резинотканевых лент |
|
|
|
||||||
Тип ленты |
|
Прочность ленты Р, Н/мм |
|
|
|
Число прокладок i, шт. |
|
Масса , кг/м2 |
||||
|
|
|
|
|
|
|
|
|
|
|
|
|
1 |
|
2 |
|
|
|
|
3 |
|
4 |
|
||
|
|
|
|
|
|
|
|
|
|
|
||
БКНЛ-65 |
|
55 |
|
|
|
|
3-10 |
|
|
8,7-17,6 |
|
|
БКНЛ-100 |
|
100 |
|
|
|
|
3-8 |
|
|
10-19 |
|
|
|
|
|
|
|
|
|
|
|||||
БКНЛ-150 |
|
150 |
|
|
|
|
3-8 |
|
|
13,4-25,5 |
|
|
|
|
|
|
|
|
|
|
|||||
ЛХ-120 |
|
120 |
|
|
|
|
3-12 |
|
|
12,4-28 |
|
|
|
|
|
|
|
|
|
|
|||||
ТА-150 |
|
150 |
|
|
|
|
3-8 |
|
|
11,4-18,6 |
|
|
|
|
|
|
|
|
|
|
|||||
ТА-300 |
|
300 |
|
|
|
|
4-10 |
|
|
13,3-20,7 |
|
|
|
|
|
|
|
|
|
|
|||||
ТЛ-150 |
|
150 |
|
|
|
|
3-8 |
|
|
10,4-20,2 |
|
|
|
|
|
|
|
|
|
|
|||||
ТЛ-200 |
|
200 |
|
|
|
|
3-8 |
|
|
11,8-21 |
|
|
|
|
|
|
|
|
|
|
|||||
ТЛК-150 |
|
150 |
|
|
|
|
3-8 |
|
|
11,4-20,2 |
|
|
|
|
|
|
|
|
|
|
|||||
ТЛК-200 |
|
200 |
|
|
|
|
3-8 |
|
|
11,8-21 |
|
|
|
|
|
|
|
|
|
|
|||||
ТК-300 |
|
300 |
|
|
|
|
4-10 |
|
|
14,2-26,4 |
|
|
|
|
|
|
|
|
|
|
|||||
ТК-400 |
|
400 |
|
|
|
|
4-8 |
|
|
16-26,4 |
|
|
|
|
|
|
|
|
|
|
|||||
МЛ-200 |
|
200 |
|
|
|
|
- |
|
|
16,5-25,3 |
|
|
|
|
|
|
|
|
|
|
|||||
МЛ-300 |
|
300 |
|
|
|
|
- |
|
|
16,5-25,3 |
|
|
|
|
|
|
|
|
|
|
|||||
МК-300 |
|
300 |
|
|
|
|
- |
|
|
16,5-25,3 |
|
|
|
|
|
|
|
|
|
|
|||||
МК-600 |
|
600 |
|
|
|
|
- |
|
|
16,5-25,3 |
|
|
|
|
|
|
|
|
|
|
12

Таблица 2.5-Характеристика резинотросовых лент
Тп ленты |
|
Прочность, Н/мм |
|
|
Диаметр и шаг тросов, мм |
|
|
масса, кг/м2 |
|
РТЛ-1500 |
|
1 500 |
|
|
6,2/15 |
|
|
28 |
|
РТЛ-2500 |
|
2 500 |
|
|
7,6/14 |
|
|
37 |
|
|
|
|
|
|
|
||||
РТЛ-3150 |
|
3 150 |
|
|
8,6/15 |
|
|
43 |
|
|
|
|
|
|
|
||||
РТЛ-4000 |
|
4 000 |
|
|
8,0/15 |
|
|
48 |
|
|
|
|
|
|
|
||||
РТЛ-5000 |
|
5 000 |
|
|
10,5/17 |
|
|
55 |
|
|
|
|
|
|
|
||||
РТЛ-6000 |
|
6 000 |
|
|
11,5/18 |
|
|
65 |
|
|
|
|
|
|
|
Вычисляем мощность на валу приводного барабана конвейера, кВт:
N (0,003 П Н 0,00015 П L |
0,03 L |
B )k |
k |
2 |
k П, |
2 |
2 |
1 |
|
|
(2.5)
где Н – высота подъема материала (рис. 2.3), м: |
|
Н L sin , L2 L cos , |
(2.6) |
где L – длина конвейера, м (табл. 2.11); |
|
– угол наклона конвейера, рад. (таблица 2.11); |
|
L2 – длина горизонтальной проекции конвейера, м;
k1 – эмпирический коэффициент, учитывающий влияние относительной длины конвейера (табл.2.6);
k2 – коэффициент, учитывающий расход энергии на преодоление сопротивлений, возникающих при прохождении ленты через сбрасывающую тележку (табл.2.6);
k – коэффициент, учитывающий расход энергии на работу сбрасывающего устройства (табл.2.6).
Таблица 2.6-Величина коэффициентов k, k1 ,k2,
Величина коэффициентов k, k2,
|
|
|
|
|
|
|
|
Вариант |
Конструкция разгрузочного устройства |
|
k2 |
|
|
k |
|
|
|
|
|
|
|
|
|
а – 0,1,3,5,7,9 |
При наличии сбрасывающей тележки |
|
1,25 |
|
|
0,005 |
|
|
|
|
|
||||
б – 2,4,6,8,10 |
При разгрузке через натяжной барабан |
|
1,0 |
|
|
0,05 |
|
|
|
|
|
||||
|
|
|
|
|
|
|
|
Величина коэффициента k1
Относительная длина конвейера L, м |
|
до 16 |
|
15-30 |
|
30-50 |
|
|
свыше 50 |
|||
|
|
|
|
|
|
|
|
|
|
|
|
|
Коэффициент k1 |
|
1,25 |
|
|
1,15 |
|
|
1,05 |
|
|
1,0 |
|
|
|
|
|
|
|
|
|
|
|
|
|
|
Рис. 2.3-Схема ленточного конвейера
Вычисляем необходимую мощность электродвигателя, кВт:
N |
N |
, |
(2.7) |
|
|
||||
дв |
|
|
||
|
|
|
где – коэффициент полезного действия привода барабана, =0,75-0,8. Из таблицы 2.7 выбираем электродвигатель.
13

Вычисляем окружное усилие на приводном барабане, Н:
P = |
1000N |
дв |
, |
|
|||
|
|
||
|
|
|
и натяжение набегающего и сбегающего концов ленты: - сбегающего, Н:
|
|
S |
|
|
P |
|
|
1 |
|
, |
||
|
|
c |
|
e |
|
|
||||||
|
|
|
|
|
1 |
|||||||
|
|
|
|
|
|
|
|
|
||||
- набегающего, Н: |
|
|
|
|
|
|
|
|
|
|||
|
|
|
|
|
|
|
|
е |
|
|
||
|
|
S |
|
P |
|
|
|
, |
||||
|
|
н |
|
|
|
|||||||
|
|
|
|
|
e |
1 |
||||||
|
|
|
|
|
|
|
|
|||||
где |
– коэффициент трения ленты о барабан (табл.2.8); |
|||||||||||
|
– угол обхвата, рад (таблица 2.11); е - значение даны в таблице 2.9.
Таблица 2.7-Типы и основные параметры электродвигателей
(2.8)
(2.9)
(2.10)
Тип двигателя |
|
NДВ, Квт |
|
|
nдв, |
|
Тип двигателя |
|
NДВ, |
|
|
nдв, |
|
|
|
|
|
|
|
|
|
||||||
|
|
|
об/мин |
|
|
Квт |
|
|
об/мин |
|
|||
|
|
|
|
|
|
|
|
|
|
|
|||
4АА50А2У3 |
|
0,9 |
|
|
3000 |
|
4А118М2У3 |
|
7,5 |
|
|
3000 |
|
|
|
|
|
|
|
|
|
||||||
4АА56А4У3 |
|
0,12 |
|
|
1500 |
|
4А160М8У3 |
|
11,0 |
|
|
750 |
|
|
|
|
|
|
|
|
|
||||||
4АА63А6У3 |
|
0,18 |
|
|
1000 |
|
4А160М6У3 |
|
15, |
|
|
1000 |
|
|
|
|
|
|
|
|
|
||||||
4АА63В6У3 |
|
0,35 |
|
|
1000 |
|
4А160М4У3 |
|
18,5 |
|
|
1500 |
|
|
|
|
|
|
|
|
|
||||||
4АА63В4У3 |
|
0,37 |
|
|
1500 |
|
4А180S2У3 |
|
22,0 |
|
|
3000 |
|
|
|
|
|
|
|
|
|
||||||
4АА63В2У3 |
|
0,55 |
|
|
3000 |
|
4А225М8У3 |
|
30,0 |
|
|
750 |
|
|
|
|
|
|
|
|
|
||||||
4А90LA8У3 |
|
0,75 |
|
|
750 |
|
4А225М6У3 |
|
37,0 |
|
|
1000 |
|
|
|
|
|
|
|
|
|
||||||
4А80В6У3 |
|
1,1 |
|
|
1000 |
|
4А200L4У3 |
|
45,0 |
|
|
1500 |
|
|
|
|
|
|
|
|
|
||||||
4А80В4У3 |
|
1,5 |
|
|
1500 |
|
4А225М2У3 |
|
55,0 |
|
|
3000 |
|
|
|
|
|
|
|
|
|
||||||
4А80В2У3 |
|
2,8 |
|
|
3000 |
|
4А280М8У3 |
|
75,0 |
|
|
750 |
|
|
|
|
|
|
|
|
|
||||||
4А112МВ8У3 |
|
3,0 |
|
|
750 |
|
4А280М6У3 |
|
90,0 |
|
|
1000 |
|
|
|
|
|
|
|
|
|
||||||
4А112МВ6У3 |
|
4,0 |
|
|
1000 |
|
4А280М4У3 |
|
110,0 |
|
|
1500 |
|
|
|
|
|
|
|
|
|
||||||
4А112МАУ3 |
|
5,0 |
|
|
1500 |
|
4А280М2У3 |
|
132,0 |
|
|
3000 |
|
|
|
|
|
|
|
|
|
Таблица 2.8-Значение коэффициента трения μ и величины скольжения ξ
Материал трущейся поверхности |
Состояние атмосферы |
|
μ |
|
|
|
ξ |
|
|
|
|
|
|
||||
Обработанный чугун |
Очень влажная |
|
0,10 |
|
|
|
0,03 |
|
|
|
|
|
|
||||
Обработанный чугун |
Влажная |
|
0,20 |
|
|
|
0,019 |
|
|
|
|
|
|
||||
Обработанный чугун |
Сухая |
|
0,30 |
|
|
|
0,008 |
|
|
|
|
|
|
||||
Футеровка из обрезиненной ленты |
Очень влажная |
|
0,25 |
|
|
|
0,006 |
|
|
|
|
|
|
||||
Футеровка из обрезиненной ленты |
Влажная |
|
0,15 |
|
|
|
0,01 |
|
|
|
|
|
|
||||
Футеровка из обрезиненной ленты |
Сухая |
|
0,40 |
|
|
|
0,002 |
|
|
|
|
|
|
||||
Футеровка из дерева |
Очень влажная |
|
0,15 |
|
|
|
0,02 |
|
|
|
|
|
|
||||
Футеровка из дерева |
Влажная |
|
0,25 |
|
|
|
0,012 |
|
|
|
|
|
|
||||
Футеровка из дерева |
Сухая |
|
0,25 |
|
|
|
0,004 |
|
|
|
|
|
|
Таблица 2.9-Значение еμα
Угол обхвата α, рад |
|
|
|
|
|
|
|
Коэффициент трения μ |
|
|
|
|
|
|
|
|
|||||
0,1 |
|
0,15 |
|
0,20 |
|
0,25 |
|
|
0,3 |
|
0,35 |
|
0,4 |
|
|||||||
|
|
|
|
|
|
|
|
|
|||||||||||||
3,14 |
|
1,36 |
|
|
1,60 |
|
|
1,37 |
|
|
2,19 |
|
|
2,56 |
|
|
3,00 |
|
|
3,51 |
|
3,67 |
|
1,44 |
|
|
1,73 |
|
|
2,08 |
|
|
2,50 |
|
|
3,01 |
|
|
3,61 |
|
|
4,34 |
|
|
|
|
|
|
|
|
|
|
|
|
|
|
|
||||||||
4,2 |
|
1,53 |
|
|
1,88 |
|
|
2,32 |
|
|
2,86 |
|
|
3,52 |
|
|
4,35 |
|
|
5,37 |
|
|
|
|
|
|
|
|
|
|
|
|
|
|
|
||||||||
4,8 |
|
1,08 |
|
|
2,09 |
|
|
2,61 |
|
|
3,32 |
|
|
4,32 |
|
|
5,37 |
|
|
6,82 |
|
|
|
|
|
|
|
|
|
|
|
|
|
|
|
14

Определяем количество прокладок и выбираем ленту по таблицам 2.4 и 2.5:
i |
S |
н |
, |
|
|||
|
|
|
|
|
ВР |
|
(2.11)
где Р – допускаемая нагрузка на 1 м ширины одной прокладки, (по табл. 2.4 и 2.5). Подсчитанное число прокладок должно находиться в пределах, приведенных в
таблице 2.10.
Таблица 2.10-Допустимое число прокладок в зависимости от ширины ленты
В, м |
0,3 |
|
0,4 |
|
0,5 |
|
0,6 |
|
0,8 |
|
1,0 |
|
1,2 |
|
1,4 |
|
||||||||
i, м |
|
3-4 |
|
|
3-5 |
|
|
3-6 |
|
|
3-7 |
|
|
4-8 |
|
|
5-10 |
|
|
6-10 |
|
|
7-10 |
|
Определяем диаметр приводного барабана и лебедки, м:
Дбар = ( 0,12 ÷ 0,15 )in ,
и передаточное отношение приводного редуктора:
(2.12)
i |
n |
дв |
, |
|
|
|
|||
|
|
|
|
|
|
n |
бар |
|
|
|
|
|
где пдв – частота вращения ротора электродвигателя, об/мин.
(2.13)
Значение пдв берем из таблицы 2.7 по марке подобранного электродвигателя.
пбар – частота вращения приводного барабана:
п |
|
|
60 |
, |
|
бар |
(1 ) |
||||
|
Д |
|
|||
|
|
|
|||
|
|
|
бар |
|
(2.14)
где – величина, характеризующая относительное скольжение и зависящая от материала трущейся поверхности барабана и состояния атмосферы (табл.2.8).
2.3 Выполнение работы.
1.Изучить устройство и принцип работы ленточного конвейера.
2.Рассчитать основные параметры конвейера.
3.Определить тяговое усилие и характеристики привода конвейера.
4.Оформить отчет.
2.4Содержание отчета.
1.Цель работы.
2.Назначение ленточного конвейера и краткое описание его узлов. 3.Расчет основных параметров, определяющих режим работы крана при определенных условиях.
4.Выводы по работе.
2.5Контрольные вопросы.
1.Назначение ленточных конвейеров, области их применения, устройство и принцип действия.
2.Основные конструктивные схемы, устройство и назначение роликоопор.
3.Условия, от которых зависит тип и место расположения приводов.
4.Барабаны ленточных конвейеров. Материалы для их изготовления и футеровки.
5.Как рассчитываются и от чего зависят геометрические размеры барабанов?
15

2.6 Исходные данные для расчета ленточного конвейера. |
|
|
|
|
||||||||||||
Основными исходными данными для расчета конвейеров являются (табл.2.10): |
|
|
|
|||||||||||||
а) |
характеристика транспортируемого материала; |
|
|
|
|
|
||||||||||
б) |
производительность; |
|
|
|
|
|
|
|
|
|
|
|
||||
в) режим и условия работы; |
|
|
|
|
|
|
|
|
|
|
|
|||||
г) параметры трассы перемещения груза; |
|
|
|
|
|
|||||||||||
д) длина и угол наклона трассы. |
|
|
|
|
|
|
|
|
|
|
|
|||||
|
|
|
Таблица 2.11-Варианты заданий |
|
|
|
|
|||||||||
В- |
Вид транспортиру- |
|
|
|
|
|
|
|
|
|
|
Материал тру- |
Состояние |
|
α, |
|
|
П, т/ч |
|
L, м |
|
β, рад |
|
щейся поверх- |
|
||||||||
ант |
емого материала |
|
|
|
|
атмосферы |
|
рад |
||||||||
|
|
|
|
|
|
|
|
|
|
ности барабана |
|
|||||
|
|
|
|
|
|
|
|
|
|
|
|
|
|
|
|
|
1 |
Руда |
|
100 |
|
|
100 |
|
|
0,07 |
|
|
чугун |
сухая |
|
3,14 |
|
|
|
|
|
|
|
|
|
|
|
|
|
|
влажная |
|
|
|
2 |
Камень |
|
105 |
|
|
50 |
|
|
0,0175 |
|
|
чугун |
|
3,67 |
|
|
3 |
Кокс |
|
110 |
|
|
40 |
|
|
0,07 |
|
|
чугун |
сухая |
|
4,2 |
|
|
|
|
|
|
|
|
|
|
||||||||
4 |
Песок |
|
115 |
|
|
30 |
|
|
0,105 |
|
|
резина |
очень влаж- |
|
4,8 |
|
|
|
|
|
|
|
|
|
|
||||||||
|
|
|
|
|
|
|
|
|
||||||||
|
|
|
|
|
|
|
но |
|
|
|||||||
|
|
|
|
|
|
|
|
|
|
|
|
|
|
|
|
|
5 |
Цемент |
|
120 |
|
|
20 |
|
|
0,140 |
|
|
резина |
очень влаж- |
|
3,14 |
|
|
|
|
|
|
|
|
|
|
||||||||
|
|
|
|
|
|
|
|
|
||||||||
|
|
|
|
|
|
|
но |
|
|
|||||||
|
|
|
|
|
|
|
|
|
|
|
|
|
|
|
|
|
6 |
Руда |
|
125 |
|
|
10 |
|
|
0,3675 |
|
|
резина |
сухая |
|
3,67 |
|
|
|
|
|
|
|
|
|
|
||||||||
7 |
Щебень |
|
130 |
|
|
100 |
|
|
0,2625 |
|
|
дерево |
очень влаж- |
|
4,2 |
|
|
|
|
|
|
|
|
|
|
||||||||
|
|
|
|
|
|
|
|
|
||||||||
|
|
|
|
|
|
|
но |
|
|
|||||||
|
|
|
|
|
|
|
|
|
|
|
|
|
|
|
|
|
|
|
|
|
|
|
|
|
|
|
|
|
|
|
|
|
|
8 |
Уголь |
|
135 |
|
|
50 |
|
|
0,035 |
|
|
дерево |
влажная |
|
4,8 |
|
|
|
|
|
|
|
|
|
|
||||||||
9 |
Гравий |
|
140 |
|
|
40 |
|
|
0,2275 |
|
|
дерево |
сухая |
|
3,14 |
|
|
|
|
|
|
|
|
|
|
||||||||
10 |
Мел |
|
145 |
|
|
30 |
|
|
0,350 |
|
|
чугун |
сухая |
|
3,67 |
|
|
|
|
|
|
|
|
|
|
||||||||
11 |
Руда |
|
150 |
|
|
20 |
|
|
0,385 |
|
|
чугун |
влажная |
|
4,2 |
|
|
|
|
|
|
|
|
|
|
||||||||
12 |
Камень |
|
155 |
|
|
10 |
|
|
0,1225 |
|
|
чугун |
очень влаж- |
|
4,8 |
|
|
|
|
|
|
|
|
|
|
||||||||
|
|
|
|
|
|
|
|
|
||||||||
|
|
|
|
|
|
|
но |
|
|
|||||||
|
|
|
|
|
|
|
|
|
|
|
|
|
|
|
|
|
|
|
|
|
|
|
|
|
|
|
|
|
|
очень влаж- |
|
|
|
|
|
|
|
|
|
|
|
|
|
|
|
|
|
|
|
|
|
|
|
|
|
|
|
|
|
|
|
|
|
|
|
|
|
13 |
Кокс |
|
160 |
|
|
100 |
|
|
0,245 |
|
|
резина |
|
3,14 |
|
|
|
|
|
|
|
|
|
но |
|
|
|||||||
|
|
|
|
|
|
|
|
|
|
|
|
|
|
|
|
|
14 |
Земля |
|
165 |
|
|
50 |
|
|
0,3325 |
|
|
резина |
влажная |
|
3,67 |
|
|
|
|
|
|
|
|
|
|
||||||||
15 |
Гипс |
|
170 |
|
|
40 |
|
|
0,210 |
|
|
резина |
сухая |
|
4,2 |
|
|
|
|
|
|
|
|
|
|
||||||||
16 |
Руда |
|
175 |
|
|
30 |
|
|
0,0875 |
|
|
дерево |
очень влаж- |
|
4,8 |
|
|
|
|
|
|
|
|
|
|
||||||||
|
|
|
|
|
|
|
|
|
||||||||
|
|
|
|
|
|
|
но |
|
|
|||||||
|
|
|
|
|
|
|
|
|
|
|
|
|
|
|
|
|
17 |
Щебень |
|
180 |
|
|
20 |
|
|
0,1575 |
|
|
дерево |
влажная |
|
3,14 |
|
|
|
|
|
|
|
|
|
|
||||||||
18 |
Уголь |
|
185 |
|
|
10 |
|
|
0,315 |
|
|
дерево |
сухая |
|
3,67 |
|
|
|
|
|
|
|
|
|
|
||||||||
19 |
Песок |
|
190 |
|
|
100 |
|
|
0,2275 |
|
|
чугун |
очень влаж- |
|
4,2 |
|
|
|
|
|
|
|
|
|
|
||||||||
|
|
|
|
|
|
|
|
|
||||||||
|
|
|
|
|
|
|
но |
|
|
|||||||
|
|
|
|
|
|
|
|
|
|
|
|
|
|
|
|
|
20 |
Цемент |
|
195 |
|
|
50 |
|
|
0,385 |
|
|
чугун |
влажная |
|
4,8 |
|
|
|
|
|
|
|
|
|
|
||||||||
21 |
Руда |
|
200 |
|
|
40 |
|
|
0,0175 |
|
|
чугун |
сухая |
|
3,14 |
|
|
|
|
|
|
|
|
|
|
||||||||
22 |
Камень |
|
205 |
|
|
30 |
|
|
0,0525 |
|
|
резина |
очень влаж- |
|
3,67 |
|
|
|
|
|
|
|
|
|
|
||||||||
|
|
|
|
|
|
|
|
|
||||||||
|
|
|
|
|
|
|
но |
|
|
|||||||
|
|
|
|
|
|
|
|
|
|
|
|
|
|
|
|
|
23 |
Кокс |
|
210 |
|
|
20 |
|
|
0,105 |
|
|
резина |
влажная |
|
4,2 |
|
|
|
|
|
|
|
|
|
|
||||||||
|
|
|
|
|
|
|
|
|
|
|
|
|
сухая |
|
|
|
24 |
Гравий |
|
215 |
|
|
10 |
|
|
0,1925 |
|
|
резина |
|
4,8 |
|
|
25 |
Мел |
|
220 |
|
|
100 |
|
|
0,3325 |
|
|
дерево |
сухая |
|
3,14 |
|
|
|
|
|
|
|
|
|
|
||||||||
26 |
Руда |
|
225 |
|
|
50 |
|
|
0,210 |
|
|
дерево |
влажная |
|
3,67 |
|
|
|
|
|
|
|
|
|
|
||||||||
27 |
Щебень |
|
230 |
|
|
40 |
|
|
0,0275 |
|
|
дерево |
очень влаж- |
|
4,2 |
|
|
|
|
|
|
|
|
|
|
||||||||
|
|
|
|
|
|
|
|
|
||||||||
|
|
|
|
|
|
|
но |
|
|
|||||||
|
|
|
|
|
|
|
|
|
|
|
|
|
|
|
|
|
28 |
Камень |
|
235 |
|
|
20 |
|
|
0,0525 |
|
|
резина |
очень влаж- |
|
3,07 |
|
|
|
|
|
|
|
|
|
|
||||||||
|
|
|
|
|
|
|
|
|
||||||||
|
|
|
|
|
|
|
но |
|
|
|||||||
|
|
|
|
|
|
|
|
|
|
|
|
|
|
|
|
|
29 |
Кокс |
|
240 |
|
|
20 |
|
|
0,0105 |
|
|
резина |
влажная |
|
4,2 |
|
|
|
|
|
|
|
|
|
|
||||||||
30 |
Уголь |
|
245 |
|
|
10 |
|
|
0,3675 |
|
|
чугун |
сухая |
|
4,5 |
|
|
|
|
|
|
|
|
|
|
16
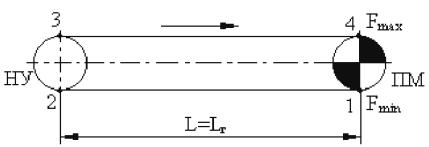
ПРАКТИЧЕСКАЯ РАБОТА №3 ТЕМА: ИЗУЧЕНИЕ ПРИНЦИПА ДЕЙСТВИЯ ПЛАСТИНЧАТОГО КОНВЕЙЕРА.
Цель работы: Изучить конструкцию и принцип работы пластинчатого конвейера. Рассчитать пластинчатый конвейер.
3.1 Краткие теоретические сведения.
Пластинчатый конвейер |
служит для непрерывного транспортирования |
насыпных и штучных грузов |
по трассе, расположенной в вертикальной плоско- |
сти или в пространстве. |
|
По конструкции настила, тяговой цепи и расположению трассы различают пластинчатые вертикально-замкнутые конвейеры общего назначения и изгибающиеся конвейеры с пространственной трассой. К специальным пластинчатым конвейерам относят разливочные машины для транспортирования и охлаждения жидкого металла, пассажирские конвейеры и конвейеры с настилом сложного профиля.
Пластинчатые конвейеры применяются на складах, в металлургической, химической, угольной, энергетической и других отраслях промышленности.
Преимуществами пластинчатых конвейеров являются возможность транспортирования тяжелых и горячих грузов при больших производительности и длине перемещения; спокойный и бесшумный ход; применение трасс с наклоном до 60°.
К недостаткам пластинчатых конвейеров относятся значительные массы настила, цепей, а также их высокая стоимость.
Пластинчатый конвейер состоит из станины, по концам которой установлены две звездочки – приводная с приводом и натяжная с натяжным устройством (рис.3.1). Бесконечный настил, состоящий из отдельных металлических, или реже, деревянных пластин, прикреплен к одной или двум тяговым цепям, которые огибают концевые звездочки и находятся в зацеплении с их зубьями. Вертикально замкнутые тяговые цепи снабжены опорными катками и движутся вместе с настилом по направляющим путям станины вдоль продольной оси конвейера.
3.2 Расчет пластинчатого конвейера.
Рассчитать пластинчатый горизонтальный конвейер при заданной производительности Q (т/ч) для перемещения штучных грузов плотностью ρ, с размером по диагонали b, массой m. Длина конвейера L. Разгрузка – в конце загруженной ветви. Условия работы – средние.
Рис.3.1-Расчетная схема конвейера.
НУ - натяжное устройство; ПМ - приводное устройство.
17

Расчет транспортирующей машины состоит: в определении основных пара-
метров, расчете и выборе рабочего органа, определении мощности и выборе двигателя, выборе элементов передач.
3.2.1 Выбирается тип конвейера в зависимости от его назначения. Пластинчатые конвейеры различаются преимущественно конструкцией настила (табл.3.1).
Таблица 3.1-Типы пластинчатых конвейеров.
Обозначение типа |
|
Тип конвейера. |
|
|
Область применения. |
|
конвейера |
|
|
|
|
|
|
ПР |
|
Плоский разомкнутый |
|
|
Для транспортирования штучных |
|
ПС |
|
Плоский сомкнутый |
|
|
грузов |
|
В |
|
Безбортовый волнистый |
|
|
Для транспортирования |
|
|
|
|
|
|||
БВ |
|
Бортовый волнистый |
|
|
штучных и насыпных грузов |
|
КМ |
|
Коробчатый мелкий |
|
|
Для транспортирования насыпных |
|
|
|
|
|
|||
КГ |
|
Коробчатый глубокий |
|
|
грузов |
|
3.2.2 Исходя из размеров груза, рассчитывается ширина настила, мм:
|
B ≥ b1 +B1, |
(3.1) |
где b1 |
– наибольший поперечный размер груза, мм; |
|
B1 |
– запас ширины настила: для безбортовых конвейеров B1= 100 мм, |
|
для бортовых B1= 150 мм. |
|
3.2.3 По ГОСТ 22281-76 (табл.3.2) принимается стандартная ширина настила. По таб.3.3 выбирается шаг цепи tц. Из таблицы 3.4, в зависимости от ширины настила, выбирается скорость ходовой части v, которая принимается из стандартного ряда по таблице 3.5.
Таблица 3.2-Основные размеры пластинчатых конвейеров (ГОСТ 22281-76).
Ширина настила ходовой |
|
Шаг тяговой цепи t, мм |
|
|
|
Числа зубьев |
|||
части В, мм |
|
|
|
|
|
|
звездочек z |
||
400, 500, 650, |
800, 1000,1200, |
|
80, 100, 125, 160, 200, 250, |
|
|
6, |
7, 8, 9, 10,11, 12, 13 |
|
|
1400, 1600 |
|
315, 400, 500, 630 |
|
|
|
|
|
||
Таблица 3.3-Рекомендуемый шаг цепей пластинчатых конвейеров. |
|||||||||
|
Ширина настила, мм |
|
Шаг цепи, мм |
||||||
|
400 |
|
|
|
|
|
|
250 |
|
|
500 |
|
|
|
|
|
|
320 |
|
|
|
|
|
|
|
|
|
||
|
650 |
|
|
|
|
|
|
400 |
|
|
|
|
|
|
|
|
|
||
|
800 |
|
|
|
|
|
|
400 |
|
|
|
|
|
|
|
|
|
||
|
1000 |
|
|
|
|
|
|
500 |
|
|
|
|
|
|
|
|
|
||
|
1200 |
|
|
|
|
|
|
500 |
|
|
|
|
|
|
|
|
|
||
|
1400 |
|
|
|
|
|
|
630 |
|
|
|
|
|
|
|
|
|
||
|
1600 |
|
|
|
|
|
|
630 |
|
|
|
|
|
|
|
|
|
18

Таблица 3.4-Рекомендуемая скорость движения полотна пластинчатых конвейеров.
Ширина настила, мм |
|
Скорость движения полотна, м/с |
||
400; |
500 |
|
0,125 … 0,4 |
|
650; |
800 |
|
0,125 … 0,5 |
|
|
|
|||
1000; |
1200 |
|
0,2 … 0,63 |
|
|
|
|||
1400; |
1600 |
|
0,25 … 0,63 |
|
|
|
Таблица 3.5-Скорость движения ходовой части пластинчатых конвейеров (ГОСТ
22281-76).
Скорость движения ходовой части, м/с
0,01; 0,016; 0,025; 0,04; 0,05; 0,063; 0,08; 0,1; 0,125; 0,16; 0,2; 0,25; 0,315; 0,4; 0,5; 0,63; 0,8; 1,0
3.2.4 В качестве тягового органа по таблице 3.6 предварительно выбирается цепь для конвейера и разрушающая нагрузка (ГОСТ 588-81 ).
Таблица 3.6-Основные параметры тяговых пластинчатых цепей.
Номер цепи |
|
Разрушающая нагрузка Fраз, не менее кН |
|
|
Шаг цепи tц, мм |
||
М20 |
|
20 |
|
|
40 |
– 160 |
|
М28 |
|
28 |
|
|
50 |
– 200 |
|
|
|
|
|
||||
М40 |
|
40 |
|
|
63 |
– 250 |
|
|
|
|
|
||||
М56 |
|
56 |
|
|
63 |
– 250 |
|
|
|
|
|
||||
М80 |
|
80 |
|
|
80 |
– 315 |
|
|
|
|
|
||||
М112 |
|
112 |
|
|
80 |
– 400 |
|
|
|
|
|
||||
М160 |
|
160 |
|
|
100 – 500 |
|
|
|
|
|
|
||||
М224 |
|
224 |
|
|
125 – 630 |
|
|
|
|
|
|
||||
М315 |
|
315 |
|
|
160 – 630 |
|
|
|
|
|
|
||||
М450 |
|
450 |
|
|
200 – 800 |
|
|
|
|
|
|
||||
М630 |
|
630 |
|
|
250 |
– 1000 |
|
|
|
|
|
3.2.5 По формуле (3.2) определяется погонная масса груза (средняя масса гру-
за на 1 м длины загруженного участка рабочей ветви конвейера), кг/м: |
|
|
|
||||||
q = Q / (3,6·ν). |
|
|
|
(3.2) |
|||||
3.2.6 По формуле (3.3) определяется шаг расположения грузов на настиле, м: |
|||||||||
tг= m/q. |
|
|
|
|
|
(3.3) |
|||
3.2.7 Погонная масса (масса 1 м длины тягового органа) ходовой части кон- |
|||||||||
вейера рассчитывается, кг/м: |
|
|
|
|
|
|
|
|
|
q х.ч. ≈ 60·В + К, |
|
|
|
|
|
(3.4) |
|||
где В – ширина настила, м; К – коэффициент, принимаемый по табл. 3.6. |
|||||||||
Таблица 3.6-Значение К. |
|
|
|
|
|
|
|||
Характеристика груза по плотности ρ, |
|
Ширина настила без бортов, м |
|||||||
т/м3 |
|
0,4-0,5 |
|
0,65-0,8 |
|
|
1,0 и более |
||
Легкий, ρ <1 |
|
35 |
|
|
45 |
|
|
60 |
|
Средний ρ=1 …2 |
|
50 |
|
|
60 |
|
|
90 |
|
|
|
|
|
|
|
||||
Тяжелый ρ > 2 |
|
70 |
|
|
100 |
|
|
130 |
|
|
|
|
|
|
|
19
3.2.8 Наименьшее натяжение цепей, для горизонтально расположенного конвейера, находится в точке их сбегания с приводных звездочек и принимается Fmin=F1= 1000 … 3000 Н. В соответствии с этим тяговая сила конвейера определяется, Н:
F0= 1,05 [Fmin +q (ω q L + 2 ω qхч L)], |
(3.5) |
|||||||
где ω =0,07 … 0,12 – коэффициент сопротивления перемещению груза. |
||||||||
По таблице 3.2 определяем число зубьев для тяговых цепей. |
|
|
|
|||||
3.2.9 Определяем динамическую нагрузку, H: |
|
|
|
|||||
F |
дин |
≈ ((60·ν2·L)/(z2· t )) (q + k ·q |
хч |
), |
(3.6) |
|||
|
ц |
1 |
|
|
|
|
||
где z – число зубьев ведущей звездочки, м; k1 – коэффициент приведения |
||||||||
массы (табл.3.7). |
|
|
|
|
|
|
||
|
|
Таблица 3.7-Значения k1 |
|
|
|
|||
|
|
Длина конвейера, м |
|
|
|
|
k1 |
|
|
|
Менее 25 |
|
|
|
|
2 |
|
|
|
25 … 60 |
|
|
|
|
1,5 |
|
|
|
|
|
|
|
|
||
|
|
Более 60 |
|
|
|
|
1 |
|
|
|
|
|
|
|
|
3.2.10. Определяется натяжение цепи в характерных точках конвейера методом обхода по контуру и уточняется значение F0. Обход начинают, как правило, от точки с наименьшим натяжением Fmin= F1.
Сопротивление:
– на участке холостой ветви конвейера определяется, Н:
Fх = qхч g L ω, |
(3.7) |
где g=9,81 м/с. |
|
– на загруженной ветви, Н: |
|
Fг = (q + qхч) ·g L·ω. |
(3.8) |
3.2.11. Натяжение цепей в точке набегания цепей на натяжные звездочки |
|
определится, Н: |
|
F2 = F1 + Fх . |
(3.9) |
Сопротивление на натяжных звездочках, Н: |
|
Fпов = F2·(1 ,05 – 1). |
(3.10) |
Натяжение цепей в точке сбегания с натяжных звездочек, Н: |
|
F3= F2 +Fпов= F2+ 0,05·F2. |
(3.11) |
Натяжение цепей в точке набегания загруженных ветвей цепей на приводные |
|
звездочки, Н: |
|
F4= F3 +Fг. |
(3.12) |
Уточненное значение тяговой силы конвейера определяется, Н: |
|
F´0= F4 - F1. |
(3.13) |
20 |
|