
Технология машиностроения 2006 Махаринский
.pdf
171
Пружина 4, сила которой больше,
Рис. 3.109. Фрезерование фасонных по-
верхностей фасонными фрезами
чем вертикальная составляющая силы резания на фрезе, обеспечивает посто- янный контакт между пальцем и ко- пиром.
На рис. 3.110, б показана схема
копирования по системе непрямого действия с гидравлическим, пневмати- ческим или электронным управлени- ем. Стол 12 с копиром 14 и заготовкой 13 перемещается от редуктора 10 че- рез ходовой винт 11. При этом палец 1 под действием копира 14 перемеща- ется в корпусе 2, соединенном с баб- кой 5. Пружина 3 обеспечивает посто- янный контакт между пальцем и копи- ром. Незначительное перемещение пальца, как элементарную команду управления, можно увеличить, ис- пользуя электронные, гидравличе- ские, пневматические или другие уст- ройства. Это усиление происходит в устройстве 4, откуда поступает ко- манда двигателю 6; последний через редуктор и ходовой винт 7 перемещает
Рис. 3.110. Схемы копирования
по стойке 8 бабку 5. Соответственно фреза 9 обрабатывает заготовку по про- филю копира.
Системы прямого действия обычно применяют на копировальных станках с механическим или ручным управлением, а системы непрямого действия — на

172 |
|
|
копировальных станках с электронным, гидравлическим или пневма- |
Рис. 3.114. Компон |
|
тическим управлением. |
|
|
Накладной копир представлен на рис. 3.111. В процессе фрезе- |
консольного верти |
|
рования заготовке 1 и копиру 2 комбинированием двух подач сооб- |
но-фрезерного ста |
|
щатся необходимые движения с таким расчетом, чтобы поверхность |
|
|
постоянной соприка- |
|
|
салась |
с цилиндри- |
|
ческой |
частью 3 |
|
концевой фрезы. |
|
Рис. 3.111. Фрезерование фасонных поверхно-
стей по накладному копиру
Обработка фасонных круговых прямо-
угольных пазов или круговых контуров может осуществляться на вертикально-
фрезерном станке с помощью поворотного стола, который имеет ручной или механи-
ческий привод круговой подачи (3.112). При установке заготовки на поворот-
ный стол необходимо обеспечить совпадение центра фрезеруемой дуги с осью поворотного стола.
К станкам фрезерной группы относят: |
консольно- |
|
||
|
фрезерные (универсальные, го- |
|
||
|
ризонтальные, широкоунивер- |
|
||
|
сальные, вертикальные); про- |
|
||
|
дольно-фрезерные (одно- и |
|
||
|
двухстоечные); фрезерные не- |
|
||
|
прерывного действия (барабан- |
|
||
|
ные и карусельные); копиро- |
|
||
|
вально-фрезерные; бесконсоль- |
|
||
|
ные вертикально-фрезерные и |
Рис. 3.114. Компонов- |
||
|
разные (шпоночно-фрезерные, |
|||
|
фрезерно-центровальные, тор- |
ка консольного вер- |
||
Рис. 3.113. Компоновка |
тикально-фрезерного |
|||
цефрезерные и др.). |
|
станка |
||
консольного горизон- |
Компоновка |
консольного |
||
|
||||
тально-фрезерного |
горизонтально-фрезерного стан- |
|
||
станка |
ка показана на рис. 3.113., а вер- |
|
||
|
тикально-фрезерного – на рис. 3.114. |

173
Заготовки, обрабатываемые на фрезерных станках, устанавливаются на станке при помощи станочных приспособлений, которые можно разделить на три класса: универсальные, специализированные и специальные. К универсаль- ным приспособлениям общего назначения относятся: прихваты, прижимы, упо- ры, машинные тиски различных видов, угольники, угловые плиты, круглые по- воротные столы, делительные столы и головки.
Машинные тиски (рис. 3.115) широко применяются для закрепления заго- товок простой формы и относительно небольших размеров. По конструкции они делятся на следующие виды: 1) простые (см. рис. 3.115-а); 2) поворотные (поворот вокруг вертикальной оси, рис. 3.115-б); 3) универсальные (поворот вокруг двух осей, рис. 3.115-в). Поворотные и универсальные тиски применя- ются при фрезеровании наклонных поверхностей и скосов.
Рис. 3.115. Машинные тиски
Угловые плиты (рис. 3.116) подразделяются на: неповоротные (рис. 3.116- а); поворотные (вокруг горизонтальной оси, рис. 3.116-б); универсальные (по- ворот вокруг вертикальной и горизонтальной оси, рис. 3.116-в). Заготовки кре- пятся к угловым плитам прихватами или струбцинами.
Рис. 3.116. Угловые плиты
Призмы (рис. 3.117) служат для закрепления заготовок круглой формы при помощи прихватов. Последние следует располагать над призмами, чтобы уси- лием зажима не деформировать заготовку.

174
Правильное положение тисков, угловых плит и призм на столе относитель- но его продольной подачи обеспечивается за счет направляющих шпонок, ко- торые имеются в названных приспособлениях и входят в паз стола.
|
|
Круглые |
поворотные |
столы |
|
|
(рис. 3.118) применяются для за- |
||||
|
крепления заготовок на своем ра- |
||||
|
бочем столе, для обработки круго- |
||||
|
вых контуров или для поворота за- |
||||
|
готовки на заданный угол. В цен- |
||||
|
тре |
поворотного |
стола |
имеется |
|
|
точное конусное отверстие для ус- |
||||
|
тановки центрирующего пальца. |
||||
|
|
Из приспособлений для закре- |
|||
|
пления заготовок |
при обработке |
|||
Рис. 3.117. Закрепление заготовки на |
многогранников, шлицов, зубчатых |
||||
и храповых колес, зубчатых муфт и |
|||||
призмах |
других деталей, где требуется де- |
||||
|
лительная головка, наиболее широ- |
||||
|
кое применение нашли трехкулачко- |
||||
|
вые самоцентрирующие патроны, по- |
||||
|
стоянные центры, хомутики, люнеты и |
||||
|
оправки. |
|
|
|
|
|
В |
единичном |
и |
мелкосерийном |
|
|
производстве выгодно использовать |
||||
Рис. 3.118. Круглый поворотный |
универсально-сборные приспособле- |
||||
ния (УСП). Это специальные приспо- |
|||||
стол |
собления, собираемые |
из нормализо- |
ванных деталей и сборочных единиц. Основными элементами УСП являются базовые, корпусные, установочнонаправляющие и крепежноприжимные дета- ли. В элементах УСП предусмотрены взаимно перпендикулярные Т-образные пазы. Фиксация деталей осуществляется способом «шпонка-паз». Недостаточ- ная жесткость УСП заставляет снижать режимы резания. Число деталей и узлов в комплекте УСП составляет 2400…4200 единиц.
При помощи универсальных делительных головок (УДГ) можно:
1)периодически поворачивать заготовку вокруг ее оси на заданное число делений (равные и неравные части);
2)устанавливать ось обрабатываемых заготовок под заданным углом к го- ризонтальной плоскости;
3)непрерывно вращать заготовку в процессе фрезерования винтовых кана-
вок;
4)производить разметку заготовок.
На рис. 3.119 показана универсальная делительная головка, которая работа- ет следующим образом: делительный диск 2 непосредственного деления установ- лен на шпинделе 3 головки и фиксируется защелкой 1. Сменный делительный

175
диск 5 установлен на оси рукоятки 6, на которой расположены также раздвиж- ные втулки 4, фиксирующие угол развилки при делении.
Заготовку устанавливают на оправку, которую закрепляют
между центрами делительной головки и задней бабки фрезер- ного станка. На шпинделе может быть установлен патрон, предна- значенный для закрепления заго- товки, не имеющей центровых отверстий.
Делительную головку снабжают тремя дисками 5, в
каждом из которых имеется по шести расположенных по ок- ружности рядов отверстий. От- верстия в каждом ряду располо- жены на равном расстоянии од- но от другого.
Для поворота заготовки на требуемый угол выводят штифт 7 из делительного диска; затем рукояткой поворачивают шпиндель на требуемый угол и после этого вводят штифт в соответствующее отверстие диска.
Если оси заготовки нужно придать наклонное положение относительно плоскости стола, поворотную часть универсальной головки устанавливают под требуемым углом и закрепляют болтами.
Режущий инструмент на фрезерных станках устанавливается и закрепляет- ся при помощи вспомогательного инструмента. Это центровые и концевые оп- равки, переходные втулки, установочные кольца, цанговые патроны и др.
Центровые оп- равки (рис. 3.120)
применяются для установки цилинд- рических, дисковых,
угловых и фасонных фрез на горизон- тально-фрезерном станке. Оправка ко- ническим хвостови- ком 2 устанавлива-
ется в коническом отверстии шпинделя и крепится натяж- ным винтом (шом- полом) 1. Для вос-
приятия крутящего
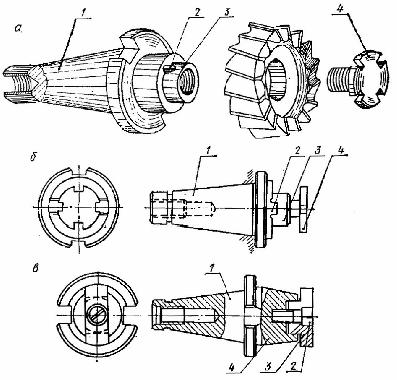
176
момента от сил резания прямоугольные пазы на фланце оправки совмещают с поводковыми шпонками, расположенными в пазах торца шпинделя.
На цилиндрическую часть 4 оправки со шпо- ночной канавкой насажи-
вают установочные кольца 3 и фрезу. Комплект за- крепляется гайкой 6. Вто- рой сводный конец оправ- ки поддерживается под- шипником подвески, за- крепляемой на хоботе. В
подшипники подвески вводится направляющая опора 7 (см. рис. 3.120-а)
или поддерживающая букса 7 (см. рис. 3.120-б).
Концевые оправки (рис. 3.121) служат для за- крепления насадных тор-
Рис. 3.121. Концевые оправки цевых фрез на вертикаль- но- и горизонтально- фрезерных станках. Они
закрепляются в шпинделе станка так же как центровые оправки. Крутящий мо- мент от сил резания концевая оправка воспринимает продольной призматиче- ской шпонкой (рис. 3.121-а), торцевой шпонкой (рис. 3.121-б) или вкладышем 3 (рис. 3.121-в), который входит в торцовый паз фрезы. Последний вариант при- меняется для установки торцовых фрез большого диаметра с коническим поса- дочным отверстием.
Размерная настройка при фрезеровании плоскостей инструментов выпол- няется методом пробных проходов.
Точность фрезерования зависит от типа станка, режущего инструмента, режима резания и других факторов. В обычных условиях точность обработки при фрезеровании достигает 11...8-го квалитета, а при скоростном и тонком фрезеровании — 7-го квалитета.
Плоское шлифование применяют в качестве чистовой операции после стро-
гания или фрезерования плоскостей для достижения высокой точности и малой шероховатости обрабатываемой поверхности, а также для окончательной обра- ботки плоскостей заготовок из закаленной стали. В ряде случаев плоское шли- фование может быть более рациональным, чем фрезерование, особенно при об- работке твердых материалов, наличии твердой корки или небольших припусков на обработку.
Шлифование плоских поверхностей применяется как для обдирочной, так и для черновой и чистовой обработки. Обдирочное шлифование плоскостей

177
может быть предварительной или окончательной операцией, если не требуется высокой точности и небольшой высоты микрогребешков.
Припуск для обдирочного шлифования должен быть значительно меньше, чем для фрезерования и строгания. При больших припусках обдирочное шли- фование оказывается неэкономичным. Обдирочное шлифование плоскостей применяется в том случае, когда наличие твердой корки на поверхности дета- ли или большая твердость материала затрудняют фрезерование или строга- ние. Оно применяется также при обработке плоских поверхностей деталей с малой жесткостью.
Обдирочное шлифование применяется для чугунных отливок, поковок и сварных конструкций и реже — для стальных отливок.
Черновое и чистовое шлифование плоскостей производится для получения высокой точности поверхности, когда не представляется возможным достигнуть этого фрезерованием или строганием.
Круги больших диаметров для шлифования изготовляют составными из отдельных частей-брусков и сегментов, прикрепленных к металлическому диску (рис. 3.122). При работе такими кругами уменьшается выделение теп- ла, улучшается удаление пыли и мелкой стружки, образующихся при шлифо- вании, повышается безопасность шлифовальных работ.
Чистовое шлифование плоскостей производится мел- козернистыми, большей частью цельными кругами. Шлифова- ние производится торцовой ча- стью или периферией круга. При шлифовании торцовой ча-
стью круга применяют круги чашечной или тарельчатой формы. При такой форме круга
изнашивается только та часть его, которая находится в со- прикосновении с обрабатывае-
мой поверхностью и поэтому отпадает необходимость пра- вить всю поверхность круга. Кроме того, при такой форме различие скоро-
стей вращения отдельных точек торца круга меньше влияет на точность и ка- чество обработки поверхности.
Шлифование торцом круга более производительно, чем шлифование пе- риферией, так как в процессе работы торцом круга большая площадь круга находится в соприкосновении с обрабатываемой поверхностью и большее ко- личество абразивных зерен одновременно работает. К тому же этот способ шлифования обеспечивает достаточно высокую точность, и поэтому он явля- ется весьма распространенным.
Шлифование периферией круга менее производительно, но при этом дос- тигается более высокая точность, чем при шлифовании торцом круга, поэто-

178
му шлифование периферией круга применяют обычно для окончательной от- делки деталей измерительных инструментов, приборов и др.
Схемы плоского шлифования приведены на рис. 3.123.
Рис. 3.123. Схемы плоского шлифования:
а — торцом круга на станках карусельного типа; б — торцом круга на станках продольного типа; в — периферией круга на станках продольного типа; г — периферией крута на станках карусельного типа
179
Протягивание наружных контуров является более производительным ме- тодом, чем строгание и фрезерование при одновременном обеспечении высокой точности и малой шероховатости обрабатываемой поверхности.
Высокие показатели точности и шероховатости поверхности при протяги- вании обусловливаются в основном весьма малым влиянием упругих деформа- ций на процесс резания, малой толщиной стружки и низкими скоростями реза- ния. Однако следует учитывать, что себестоимость протяжных работ в значи- тельной степени зависит от затрат на изготовление и заточку протяжек, а также на приобретение протяжного оборудования.
Протягивание наружных плоских поверхностей (как и фасонных) благо-
даря высокой производительности и низкой себестоимости обработки находит все большее применение в крупносерийном и массовом производстве. Этот метод экономически выгоден, несмотря на высокую себестоимость оборудо- вания и инструмента. Многие операции вместо фрезерования выполняются посредством наружного протягивания. К числу таких операций относится протягивание пазов, канавок, плоскостей блоков двигателей и других деталей, зубьев шестерен и т.д.
Протягивание наружных плоских поверхностей (как и фасонных) благо-
даря высокой производительности и низкой себестоимости обработки находит все большее применение в крупносерийном и массовом производстве. Этот метод экономически выгоден, несмотря на высокую себестоимость оборудо- вания и инструмента. Многие операции вместо фрезерования выполняются посредством наружного протягивания. К числу таких операций относится протягивание пазов, канавок, плоскостей блоков двигателей и других деталей, зубьев шестерен и т.д.
При обработке протягиванием наружных черных (предварительно не об- работанных) поверхностей за один ход протяжки достигаются высокая точ- ность и низкая высота микрогребешков. В процессе обработки каждый режущий зуб протяжки снимает слой металла, составляющий часть припус- ка, а калибрующие зубья зачищают поверхность, при этом они долго не теря- ют своей режущей способности и формы.
При обработке черных поверхностей поковок и отливок более целесооб- разно применять не обычные плоские протяжки (рис. 3.124, а), а прогрес- сивные (рис. 3.124, б, в, г). У обычных плоских протяжек каждый зуб снимает стружку по всей ширине обрабатываемой поверхности, поэтому при обработке черной поверхности, имеющей корку, первые зубья протяжки быстро ту- пятся или выкрашиваются. Режущие зубья прогрессивных протяжек делают переменной ширины, постепенно увеличивающейся, и каждый режущий зуб срезает металл не по всей ширине обрабатываемой поверхности, а полосой, причем ширина этих полос с каждым зубом увеличивается и только калиб- рующие зубья зачищают обрабатываемую поверхность по всей ширине.
Для обработки наружным протягиванием широких плоскостей (более 50 мм) устанавливают несколько протяжек рядом.
Протягивание наружных поверхностей производится большей частью на вертикально-протяжных станках– полуавтоматах и автоматах.

180
Рис. 3.124. Схемы плоских протяжек: а — обычные; б, в, г — прогрессивные
3.5. Нарезание зубьев цилиндрических зубчатых колес методом копирования дисковыми и пальцевыми фрезами
Нарезание цилиндрических зубчатых колес с прямым зубом можно выпол- нить на горизонтальных и универсальных фрезерных станках при помощи де- лительной головки модульными дисковыми фрезами. Этот метод, называемый методом копирования, заключается в последовательном фрезеровании впадин между зубьями фасонной дисковой модульной фрезой. Такие фрезы изготов- ляются набором из 8, 15 или 26 штук для каждого модуля. Обычно применяют набор фрез из 8 штук, обработка которыми позволяет получать зубчатые колеса 9-й степени точности по ГОСТ 1643-81, но для изготовления более точных зуб- чатых колес требуется набор из 15 или 26 штук. Такое количество фрез в каж- дом наборе необходимо потому, что для различного числа зубьев колес профи- ли впадин между зубьями различны. Каждая фреза набора предназначена для определенного интервала числа зубьев.
Зубчатые колеса обычно нарезаются по одной (рис. 3.125, а) или по не- сколько штук на оправке (рис. 3.125, б), что увеличивает производительность за счет времени, затрачиваемого на врезание и выход фрезы, а также за счет вспо- могательного времени. Если на шпиндельной оправке расположить две или три фрезы (рис. 3.125, в), каждая из которых будет прорезать впадины зубьев у од- ной группы заготовок, то производительность будет еще больше. В этом случае применяют многошпиндельные делительные головки (рис. 3.125, г). Примене- ние для этих целей полуавтоматических станков, у которых все вспомогатель- ные движения (подход заготовок к фрезам, отход их в исходное положение, по- ворот заготовок на один зуб и останов станка) совершаются автоматически,