
75 группа 2 вариант / Режимы роботы и эксплуатации ТЭС / ПТ / Книги / Курс лекций. Режимы работы и эксплуатация паротурбинных установок ТЭС
.pdfусугубления последствий её аварийного останова. Случаи аварийного останова турбины со срывом вакуума регламентируются местными производственными инструкциями по эксплуатации турбоустановок. В других случаях останов турбоагрегата со срывом вакуума нежелателен по причине возникновения больших механических и температурных напряжений в элементах проточной части турбины.
В целом последовательность операций по переводу конденсационной установки из «Горячего» в «Неостывший» и далее в «Холодный резерв» обратна последовательности пусковых операций.
Отключение контура циркуляции основного конденсата, то есть перевод конденсационной установки из «Горячего» в «Неостывший резерв», может выполняться после отключения турбины и срыва вакуума, но не ранее отключения ПВД системы регенерации турбины по питательной воде, если конденсат с напора конденсатных насосов подается в схему привода быстродействующего впускного клапана группы ПВД.
Отключение системы циркуляционных водоводов, то есть перевод конденсационной установки из «Неостывшего» в «Холодный резерв», осуществляется при достижении контрольного значения температуры металла выхлопного патрубка турбины (50–80 °С).
Для оптимизации работы оперативного персонала турбинного цеха и повышения уровня эксплуатации конденсационной установки положение запорно-регулирующей арматуры для каждого оперативного состояния должно быть регламентировано местными инструкциями.
3.3. Контроль оборудования конденсационной установки, находящейся в оперативном состоянии «Работа»
Техническое состояние и показатели работы конденсационной установки, находящейся в оперативном состоянии «Работа», контролируются оперативным персоналом в процессе периодических обходов оборудования с записью показаний приборов технологического контроля в оперативной документации. Методы контроля работы конденсационной установки и периодичность этого контроля определяются местной инструкцией по эксплуатации оборудования.
В объем эксплуатационного контроля, как правило, должны входить измерения следующих параметров:
–давления пара в контрольной ступени турбины (используемой для определения расхода пара в конденсатор);
–давления пара в конденсаторе;
–температуры металла выхлопного патрубка турбины;
–давления и температуры охлаждающей воды до конденсатора;
–разрежения в верхней точке водяной камеры (сливной трубы) конденсатора;
–температуры охлаждающей воды после конденсатора;
–расхода охлаждающей воды через конденсатор (часто прямое измерение отсутствует, в этом случае расход воды определяется соответствующей службой электростанции по тепловому балансу конденсатора);
–температуры конденсата на выходе из конденсатосборника конденсатора;
–уровня конденсата в конденсатосборнике конденсатора;
–давления и температуры паровоздушной смеси на входе в воздухоудаляющее устройство;
–температуры и давления рабочей воды перед водоструйным эжектором или давления рабочего пара перед пароструйным эжектором;
–температуры паровоздушной смеси на выхлопе пароструйного эжектора;
–расхода воздуха, удаляемого пароструйным эжектором;
–массовой концентрации кислорода в турбинном конденсате на напоре конденсатных насосов;
11
– концентрации солей жесткости (солесодержание) в охлаждающей воде и турбинном конденсате на напоре конденсатных насосов.
Оперативный персонал должен контролировать значения измеряемых технологических параметров и не допускать выхода их за установленные местными инструкциями пределы. Общий контроль качества работы конденсационной установки осуществляет соответствующая служба производственно-технического отдела и административный персонал цеха на основании анализа суточных записей показаний контролируемых по конденсационной установке технологических параметров.
Оценка технического состояния конденсационной установки осуществляется путем сопоставления фактических значений эксплуатационных показателей ее работы с нормативными. Нормативные показатели работы определяются по соответствующим энергетическим характеристикам, входящим в состав нормативно-технической документации по топливоиспользованию. Такие характеристики получают, как правило, на основании обобщения результатов нескольких тепловых испытаний однотипных конденсационных установок во всем диапазоне изменения основных режимных параметров с учетом условий работы конкретной конденсационной установки.
Сопоставление фактических значений эксплуатационных показателей с нормативными проводится для следующих показателей работы конденсационной установки:
1. Абсолютное давление пара в конденсаторе. Этот показатель является интегральным, отражающим влияние всех режимных факторов и состояния всех элементов конденсационной установки на эффективность ее работы. Увеличение давления отработавшего пара в конденсаторе в сравнении с нормативными значениями приводит к увеличению удельного расхода тепла на выработку электроэнергии турбоагрегатом при постоянном значении электрической мощности или к снижению вырабатываемой электрической мощности при постоянном значении расхода свежего пара на турбину. Существенное повышение давления в конденсаторе приводит и к увеличению температуры металла выхлопного патрубка турбины, что может вызвать расцентровку и появление повышенной вибрации агрегата, а также усталость рабочих лопаток в среде более плотного пара. Предельная допустимая температура металла выхлопного патрубка устанавливается заводом-изготовителем турбины и зависит, в частности, от её типа. Для большинства конденсационных турбин значение этой температуры устанавливается на уровне 50–80 °С, а для теплофикационных турбин на некоторых режимах оно может достигать 85 °С. Особое место занимает турбина Т-250/300-240, для которой заводом-изготовителем установлен диапазон предельной температуры металла выхлопного патрубка 80–120 °С.
Абсолютное давление пара в конденсаторе может быть определено по следующей формуле Рк=(В-Н)/735.6, кг/см2 ;
где В – барометрическое давление, мм. рт. ст.; Н – показание вакуумметра, мм. рт. ст.;
Рк – абсолютное давление в конденсаторе, кг/см2 Величина вакуума в конденсаторе турбины в процентном выражении может быть
определена как V=(В/Н)*100%.
Существует понятие номинального, предельного и экономического вакуума.
Номинальный вакуум – это расчетное значение вакуума при проектировании турбоагрегата.
Предельный вакуум - определяется расширяющей возможностью рабочих лопаток последней ступени турбины.
Экономический вакуум – такой, при котором прирост затрат мощности на создание вакуума меньше, чем прирост дополнительной мощности турбины вызванный снижением Рк.
По условиям эксплуатации в принципе вакуум может быть изменен от минимального до предельного и даже в некоторых случаях больше.
12
Предельный вакуум, и тем более, сверх предельный нежелателен как с точки зрения экономичности, так и с точки зрения надёжности работы турбины, так как в этом случае наблюдается усиленный эрозийный износом последних ступеней турбины.
2.Температурный напор конденсатора (недогрев охлаждающей воды до температуры насыщения пара при давлении в конденсаторе). Увеличение температурного напора в сравнении с нормативными значениями в соответствующих режимах работы конденсатора указывает или на большие присосы воздуха в вакуумную систему турбоустановки, или на загрязнение внутренней поверхности трубок конденсатора, или на обе причины одновременно.
3.Нагрев охлаждающей воды в конденсаторе. Повышенный по сравнению с нормативным нагрев охлаждающей воды может указывать на ее недостаточный расход и уменьшение из-за этого кратности охлаждения.
4.Концентрация солей жесткости или общее солесодержание турбинного конденсата на напоре конденсатных насосов. Увеличение солесодержания конденсата указывает на увеличение присосов охлаждающей воды в конденсаторе вследствие нарушения герметичности его трубной системы.
5.Гидравлическое сопротивление конденсатора. Гидравлическое сопротивление определяется как разность давлений охлаждающей воды на выходе и входе конденсатора. Значение гидравлического сопротивления ниже нормативного характерно при недостаточном расходе охлаждающей воды. Повышенное гидравлическое сопротивление указывает на загрязнение трубных досок и трубной системы в целом.
6.Переохлаждение конденсата (разность между температурой насыщения при давлении пара на входе в конденсатор и температурой конденсата на выходе из конденсатосборника). Повышенное переохлаждение конденсата может быть обусловлено либо переполнением конденсатосборника конденсатора (заливанием нижних рядов трубок), либо увеличенными присосами воздуха в вакуумную систему.
В соответствии с требованиями правил технической эксплуатации электрических станций и сетей Российской Федерации при эксплуатации конденсационной установки должна быть обеспечена экономичная и надежная работа турбины во всех режимах эксплуатации с соблюдением нормативных температурных напоров в конденсаторе и норм химического качества конденсата. Для удовлетворения этих требований при эксплуатации конденсационной установки должны проводиться следующие мероприятия:
– профилактические действия по предотвращению загрязнения конденсатора; к ним относятся обработка охлаждающей воды химическими и физическими методами, применение установок шариковой очистки трубной системы конденсатора и пр.;
– периодическая чистка конденсатора при увеличении давления пара в конденсаторе вследствие загрязнения поверхности теплообмена более чем на 0,005 кгс/cм2 (5 кПа) по сравнению с нормативным значением в заданном режиме работы;
– визуальный контроль чистоты поверхности теплообмена и трубных досок конденсатора;
– контроль расхода охлаждающей воды через конденсатор (путем непосредственного его измерения или определения по тепловому балансу конденсатора), оптимизация расхода охлаждающей воды в соответствии с её температурой и паровой нагрузкой конденсатора (поддержание режимов работы конденсационной установки с наивыгоднейшим вакуумом);
– проверка плотности вакуумной системы и её уплотнение;
– проверка гидравлической плотности конденсатора;
– проверка содержания растворенного кислорода в конденсате после конденсатных насосов.
Типовыми неисправностями при эксплуатации конденсационной установки являются:
– снижение расхода охлаждающей воды из-за завоздушивания сливного циркуляционного водовода;
13
–запаривание пароструйных эжекторов, обычно обусловленное недостаточным расходом конденсата через холодильники эжекторов;
–захлебывание эжектора, выражаемое в увеличении уровня конденсата в его холодильнике, и затопление эжекторов;
–внезапное ухудшение вакуума, которое может быть обусловлено прекращением подачи пара на концевые уплотнения турбоагрегата, упуском уровня конденсата в конденсатосборнике, срывом конденсатных насосов, запариванием эжекторов, переполнением конденсатора (чрезмерным увеличением уровня конденсата в конденсатосборнике) с перекрытием трубопроводов отсоса из конденсатора паровоздушной смеси, нарушением вакуумной плотности конденсационной установки вследствие появления значительных неплотностей в корпусе конденсатора или выхлопном патрубке турбины.
3.4.Контроль вакуумной плотности конденсационной установки
Как было указано выше, расход воздуха с присосами в вакуумную систему турбоустановки GВ, кг/ч, в диапазоне паровой нагрузки конденсатора от 40 до 100 % не должен превышать значений, рассчитываемых по формуле
GВ =8+0,065 · NТ,
где NТ – номинальная электрическая мощность турбоустановки в конденсационном режиме работы, МВт.
На практике контроль воздушной плотности конденсатора при работе турбоагрегата осуществляется по содержанию кислорода в основном конденсате на напоре конденсатных насосов. Косвенно увеличенные присосы воздуха в вакуумную систему можно установить по перегрузке воздухоудаляющих устройств, ухудшению вакуума в конденсаторе, увеличению температурного напора конденсатора.
В случае выявления неудовлетворительной вакуумной плотности конденсационной установки необходимо определить причины увеличения присосов воздуха. Места увеличенных присосов воздуха можно установить различными методами.
Недостаточно глубокий вакуум может быть следствием низкого качества ремонтных работ, а также несоблюдения правил эксплуатации конденсационной установки.
Кпричинам монтажного (ремонтного) характера относятся: недостаточная плотность вакуумной системы, неправильное выполнение схемы дренажей турбоустановки
итрубопроводов подачи пара на уплотнения, неправильная сборка эжекторов, неплотность предохранительных клапанов отборов пара, загрязнения в трубопроводах, идущих к эжекторам, и другие причины. Эти причины должны быть выявлены оперативным персоналом в ходе приемки оборудования конденсационной установки из ремонта.
Кпричинам эксплуатационного характера относятся: недостаточная подача пара на уплотнения, недостаточный расход охлаждающей воды, переполнение парового пространства конденсатора конденсатом, недостаточное давление рабочего пара перед соплами эжекторов и др.
Наиболее надежным методом контроля вакуумной плотности конденсационной установки является непосредственное измерение количества удаляемого эжектором воздуха, для чего на выхлопном патрубке пароструйного эжектора устанавливается дроссельный воздухомер. Такой метод, однако, неприменим для конденсационных установок с водоструйными эжекторами.
Проверка вакуумной плотности системы может осуществляться также путем гидравлического испытания. Гидравлическое испытание целесообразно проводить после монтажа или ремонта турбоагрегата, особенно если ремонт проводился на оборудовании конденсационной установки. Порядок проведения такого испытания следующий:
1. На подготовительном к испытаниям этапе выполняется сборка схемы вакуумной системы с открытием всей арматуры на трубопроводах обвязки конденсатора с таким расчетом, чтобы вода заполнила все узлы. Между опорными лапами (опорной рамой) конденсатора и фундаментом необходимо установить временные металлические
14
подпорки, для того чтобы при увеличении массы конденсатора от наливаемой воды не возникла нерасчетная нагрузка на выхлопной патрубок турбины, которая может вызвать его деформацию или нарушение плотности соединения горловины конденсатора с турбиной. Конденсато-сборник и конденсатор должны быть очищены от мусора, попавшего в них при выполнении монтажных или ремонтных работ.
2.В ходе испытаний вакуумная система заполняется химически очищенной (обессоленной) водой через трубопроводы, присоединенные к паровому пространству конденсатора, до тех пор, пока уровень ее не достигнет лопаток турбины. Наблюдение за уровнем воды производят через открытый люк на выхлопной части цилиндра низкого давления. По мере подъема уровня проверяют плотность сварки и фланцевых соединений на конденсатосборнике, трубопроводах, подогревателях низкого давления, в соединении горловины конденсатора с выхлопным патрубком турбины и других элементах. Для создания плотности системы необходимо, чтобы нигде не было ни малейших пропусков воды.
3.Для обнаружения мест неплотностей в ходе испытаний все узлы системы должны быть хорошо освещены. Уровень воды следует поднимать ступенями, наблюдая за плотностью системы. Особое внимание следует обращать на сварные швы и фланцевые соединения, расположенные в труднодоступных местах. Если течь незначительна, ее место следует отметить мелом и продолжать заполнение системы. Спускать воду и устранять неплотность следует только при наличии значительной неплотности, когда вытекающая вода мешает осмотру. Спуск воды производят через дренажные трубопроводы.
Недостатком проверки гидравлической плотности вакуумной системы методом гидравлического испытания является невозможность выявления неплотностей, расположенных выше уровня воды, залитой в паровое пространство конденсатора. Такие неплотности могут иметь место вблизи концевых уплотнений цилиндра низкого давления турбоагрегата, в разъемах самого цилиндра низкого давления, в атмосферных разрывных диафрагмах, во фланцевых соединениях перепускных труб, расположенных над цилиндрами турбины, в системе трубопроводов отсоса паровоздушной смеси, идущих к эжекторам, и других элементах.
Другой метод проверки вакуумной плотности – установление скорости снижения вакуума при отключении воздухоудаляющих устройств на работающей конденсационной установке. Отключение воздухоудаляющих устройств производится путем закрытия арматуры на трубопроводе отсоса паровоздушной смеси из конденсатора. Вакуумная плотность системы считается хорошей, если скорость снижения вакуума составляет 0,26–0,39 кПа/мин, удовлетворительной при скорости 0,39–0,52 кПа/мин.
Выявление неплотностей во время работы турбоустановки может быть выполнено также при помощи свечи, пламя которой будет затягиваться к неплотности, галоидных течеискателей, а также с использованием флуоресцеина.
Суть метода поиска неплотностей вакуумной системы с использованием галоидного течеискателя состоит в следующем. Газ, содержащий галоид, находится в сжатом состоянии в баллоне течеискателя, из которого он выходит через редукционный клапан, гибкий шланг и сопло. Струю выходящего из сопла газа направляют на места, где предполагается наличие дефектов. Если они действительно имеются, газ проникает в аппарат, а затем достигает трубопровода для отсоса воздуха. Датчик галоидного течеискателя целесообразно располагать в этом трубопроводе как можно ближе к конденсатору, что обеспечивает быстрое и надежное обнаружение газа, содержащего галоид.
Вкачестве вещества, содержащего галоид, часто используется фреон-12.
Для выявления неплотностей с помощью флуоресцеина паровое пространство конденсатора заполняют конденсатом, после чего через люк или штуцер добавляют раствор флуоресцеина. Затем места возможных протечек облучают с наружной стороны переносной ультрафиолетовой лампой. Вода, содержащая флуоресцеин, в лучах ультрафиолетового света имеет яркий желто-зеленый цвет, поэтому малейшие протечки на обследуемой поверхности становятся заметными. Во время облучения по-
15

верхности ультрафиолетовыми лучами вблизи не должно быть белого света, так как при этом эффект свечения флуоресцеина резко снижается. Качество контроля повышается при увеличении давления воды в аппарате до 0,1–0,2 МПа.
3.5. Контроль гидравлической плотности конденсатора
Контроль гидравлической плотности конденсатора осуществляется по значениям солесодержания или общей жесткости конденсата греющего пара. При нарушении герметичности конденсатора с водяной стороны вследствие трещин или обрыва трубок охлаждающая вода попадает в конденсат, что проявляется в увеличении концентрации солей жесткости в этом конденсате сверх нормативных значений. Допустимое содержание в конденсате солей жесткости регламентировано соответствующими нормативными документами. Измерение солесодержания производится обычно один – два раза в смену в отобранных пробах турбинного конденсата.
Техническими условиями на поставку конденсаторов заводами-изготовителями присосы охлаждающей воды ограничиваются на уровне 0,001 % ее расхода. Значение присоса (П) в процентном отношении определяется по результатам химических анализов теплоносителей по соотношению
где Dк – сумма расходов конденсата отработавшего пара и дренажей, поступающих в конденсатор; W – расход охлаждающей воды через конденсатор; СК, Со – жесткость конденсата и охлаждающей воды соответственно.
Обнаружение мест присоса охлаждающей воды в паровое пространство конденсатора на работающем турбоагрегате возможно при отключении по воде одной из половин конденсатора. При этом к трубной доске прижимается тонкая пластиковая пленка или на нее наносится слой пены, а соответствующий участок в противоположной водяной камере чем-либо закрывается. Наличие крупных неплотностей обнаруживается в этом случае по вдавливанию пленки или засасыванию пены внутрь поврежденных трубок.
Нарушение гидравлической плотности конденсатора может происходить в результате коррозионных и эрозионных повреждений трубок с паровой и водяной сторон, механических повреждений трубок, дефектов крепления трубок в трубных досках, дефектов приварки основных трубных досок к корпусу конденсатора или сварки между собой частей сборных трубных досок и др. Около 70 % повреждений трубок происходит из-за их коррозионного разрушения вследствие агрессивного воздействия содержащихся в охлаждающей воде примесей. Эрозия трубок с паровой стороны характерна для их первых рядов в зоне входа пара, несущего капельную влагу, или в зонах повышенных скоростей пара, а также в местах ввода в конденсатор горячих дренажей. К механическим повреждениям относят образование усталостных трещин металла вблизи трубных досок, истирание трубок в отверстиях промежуточных перегородок или при взаимном соударении трубок в длинных пролетах. В 20 % случаев причиной механических повреждений трубок является их вибрация. Кроме того, механические повреждения возникают из-за дефектов изготовления трубок, несоблюдения правил их транспортировки и хранения.
В случае выявления увеличенных присосов охлаждающей воды в конденсаторе необходимо устранить причины их появления. К мероприятиям по повышению гидравлической плотности конденсатора относятся: применение двойных трубных досок, нанесение специальных мастик в месте вальцовки трубок, приварка трубок к трубным доскам, заглушка поврежденных трубок и др. Если конденсатор выполнен двухпоточным, то работы по уплотнению могут выполняться при работающей турбине. Для этого турбоагрегат разгружают, вскрывают половину конденсатора, устраняют неисправность и восстанавливают работу турбины.
16
3.6.Очистка водяного тракта конденсационной установки
Впроцессе эксплуатации происходит загрязнение водяного тракта конденсаторов, выраженное в появлении отложений осадочных примесей воды и продуктов коррозии металла оборудования и трубопроводов. Загрязнение поверхности теплообмена влечет за собой ухудшение вакуума в конденсаторе из-за увеличения термического сопротивления теплопередаче и уменьшения расхода охлаждающей воды, связанного с повышением гидравлического сопротивления водяного тракта. Кроме того, образование отложений интенсифицирует процессы подшламовой коррозии металла, а содержащиеся в воде твердые примеси, включая продукты коррозии, вызывают его эрозионный износ.
Используемые для охлаждения конденсаторов природные воды всегда содержат растворенные коллоидные и грубодисперсные примеси, а также растительные и животные организмы. Попадая в систему технического водоснабжения, природная вода под действием специфических факторов изменяет свой физико-химический и биологический состав, что приводит к образованию отложений в конденсаторах турбин. Основными причинами загрязнения водяного тракта конденсационных установок являются :
– выделение нерастворимых солей при нагреве воды в конденсаторе (накипные отложения);
– наличие микро- и макроорганизмов, способных поселяться и развиваться на поверхностях теплообмена (биологические отложения);
– наличие механических взвесей (шлама, ила, щепы, листьев и др.), которые могут оседать, особенно в присутствии микроорганизмов, на поверхностях трубок конденсаторов (механические отложения).
Загрязнения конденсаторов возникают из-за несовершенства любых имеющихся в настоящее время систем предварительной очистки, которые необходимо совершенствовать. В случае невозможности предотвращения образования отложений в конденсаторах турбин следует проводить их периодическую очистку. В настоящее время разработан ряд методов очистки и предотвращения загрязнения водяного тракта конденсационных установок:
1. Механическая очистка щетинными ершами, резиновыми цилиндриками или поршеньками, в том числе при использовании гидравлических или пневматических пистолетов. Отложения удаляются при механическом воздействии на них используемого при очистке инструмента. Каждая трубка конденсатора чистится отдельно. Требуется отключение конденсатора или, по возможности, его половины. Механическая очистка сопряжена с большими трудозатратами и занимает длительное время.
2. Очистка гидравлическим пистолетом или с помощью установки высокого давления. Вода под давлением 0,4–1,2 МПа с помощью гидравлического пистолета или установки высокого давления подается в каждую трубку конденсатора. Отложения удаляются при воздействии на них потока воды. Возможно добавление в воду абразивных добавок, однако при этом интенсифицируется эрозионный износ металла трубок. Метод также требует останова или разгрузки турбины с отключением конденсатора или его половины.
3. Непрерывная или периодическая шариковая очистка. Эластичные шарики из пористой резины циркулируют через трубную систему конденсатора по специально созданному замкнутому контуру. Касаясь внутренних стенок конденсаторных трубок, шарики счищают имеющиеся на поверхности загрязнения. Система шариковой очистки
взависимости от её типа может работать постоянно или периодически. Возможно использование шариков с абразивными включениями. Для работы системы необходим постоянный номинальный расход охлаждающей воды для создания достаточного перепада давлений между входной и выходной водяными камерами конденсатора. При работе системы несколько увеличиваются затраты мощности на привод циркуляционных насосов из-за увеличения гидравлического сопротивления конденсатора.
17
4.Очистка водовоздушной смесью. В охлаждающую воду периодически дозируется воздух, что обеспечивает удаление рыхлых илистых и органических отложений, слабо сцепленных со стенками трубок. Метод применим на работающей турбине, однако существует опасность прекращения расхода воды через конденсатор из-за скопления воздуха в верхней части сливной водяной камеры при увеличении расхода воздуха больше допустимого значения.
5.Термическая сушка воздухом или паром. Через трубную систему организуется проток подогретого воздуха или пара от стороннего источника. Удаляются отложения, способные к растрескиванию и отслаиванию при высыхании. Метод требует разгрузки или останова турбоагрегата из-за необходимости отключения конденсатора или его половины. В настоящее время паровая термическая сушка запрещена нормативнотехническими документами.
6.Вакуумная сушка воздухом. В отключенной и осушенной водяной камере одной половины конденсатора создается вакуум более глубокий, чем в паровом пространстве конденсатора работающей турбины, при этом происходят вскипание и выпаривание влаги, содержащейся в отложениях, приводя к их отслоению и растрескиванию. Впоследствии отложения смываются охлаждающей водой. Метод требует высокой герметичности трубопроводов охлаждающей воды, необходима установка шиберных заглушек на подводящем и отводящем водоводах.
7.Импульсная электрогидравлическая очистка. Метод основан на том, что при создании электрического разряда в жидкости возникают ударные волны, разрушающие отложения. Метод применим на работающей турбине, но эффективен лишь применительно к накипным отложениям.
8.Промывка обратным потоком охлаждающей воды. Отложения удаляются при изменении направления движения воды, реализуемом с использованием специальной схемы.
9.Промывка нагретой охлаждающей водой. Удаляются в основном биологиче-
ские загрязнения, чувствительные к повышению температуры среды. Метод требует больших затрат тепловой энергии на проведение очистки.
10.Коррекционная обработка охлаждающей воды химическими реагентами. Та-
кая обработка применяется в системах оборотного водоснабжения. Скорость образования накипных отложений уменьшается при дозировании в воду ингибиторов отложений. Для такого метода, как и других химических методов, характерно негативное влияние на окружающую среду из-за увеличения сбросов химически активных веществ.
11.Кислотная или другая реагентная промывка. Отложения удаляются химиче-
скими методами. При этом необходимо отключение всего конденсатора или его половины. Метод также сопряжен с загрязнением окружающей среды сбросами реагентов. Кроме того, при использовании такого метода снижается ресурс конденсационной установки из-за активации процессов химического разрушения металла.
Таким образом, любой из методов очистки или профилактики загрязнений водяного тракта конденсаторов имеет свои преимущества и недостатки. Выбор метода зависит от условий работы конкретной конденсационной установки и во многом определяется химическим и биологическим составом примесей охлаждающей воды.
Лекция 4
4.1. Общие сведения о системе регенерации турбоустановки
Регенеративная установка предназначена для подогрева питательной воды в регенеративных подогревателях паром, частично отработавшим в турбине. Применение регенеративного подогрева позволяет повысить термический КПД цикла и экономичность турбоустановки.
Регенеративные подогреватели делятся на две группы: подогреватели низкого и
18

высокого давлений (ПНД и ПВД).
ПНД устанавливаются в тракте основного конденсата, и конденсат через них прокачивается конденсатными насосами при сравнительно небольшом давлении.
ПВД устанавливаются на напоре питательных насосов, вода через них прокачивается под давлением, превышающем давление в котле
С точки зрения технико-экономического обоснования количество регенеративных подогревателей на ПТУ не должно превышать 7÷9, то есть 4÷5 ПНД и 2÷3 ПВД.
ПНД разделяются на поверхностные и смешивающие.
Основным недостатком поверхностных ПНД является их высокая стоимость (трубки выполняются из нержавеющей стали) и значительный (до 10 °С) недогрев.
В термодинамическом отношении смешивающие подогреватели являются более эффективными, так как в них практически отсутствует недогрев. Однако существуют трудности в реализации многоступенчатого регенеративного подогрева с применением смешивающих подогревателей. Поэтому в реальных схемах регенерации низкого давления, как правило, устанавливается ПНД -2 смешивающего типа или ПНД -1 и ПНД-2 смонтированных по гравитационной схеме.
Принципиальные схемы ПНД с поверхностными и смешивающими подогревателями представлены, соответственно, на рисунках 4.1. и 4.2.
Рис. 4.1. Принципиальная схема регенерации низкого давления с поверхностными подогревателями
Рис. 4.2. Принципиальная схема регенерации низкого давления со смешивающим ПНД-2
19
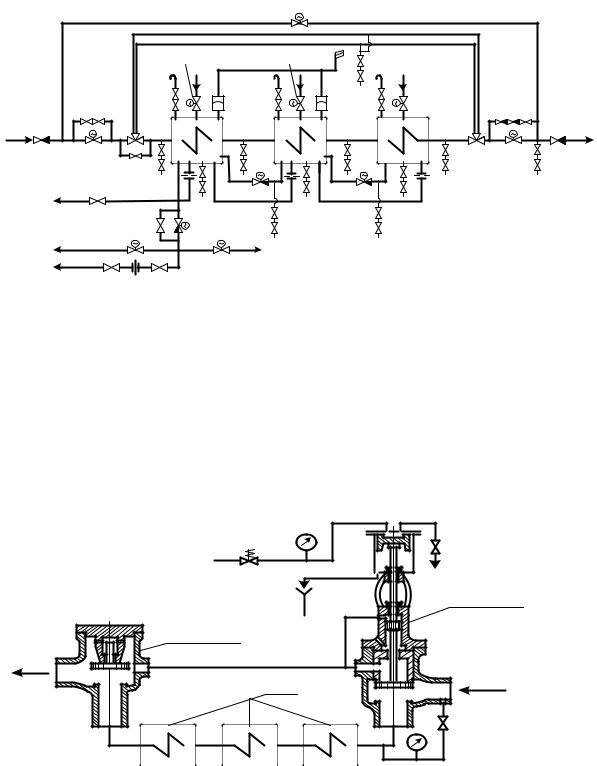
В современных системах регенерации ПТУ могут применяться камерные и коллекторные ПВД. В нашей стране применяются только вертикальные коллекторные ПВД со спиральными змеевиками из стальных углеродистых труб диаметром 32 мм и 22 мм в ПВД нового поколения.
Рис. 4.3. Принципиальная схема регенерации высокого давления
Регенеративные подогреватели снабжаются указателями уровня конденсата греющего пара, системами сигнализации и защиты.
В современных турбоустановках существует групповая защита ПВД от недопустимого повышения уровня конденсата в любом из подогревателей (рис. 4.4.), отключающая группу ПВД. Кроме того, в блочных установках устанавливается защита, отключающая энергоблок при повышении уровня до второго предела.
Рис. 4.4. Принципиальная схема защиты от недопустимого повышения уровня кон- денсата в корпусе любого ПВД
20