
охт (6sem) / для курсача / MeOH / + / 11-010
.pdf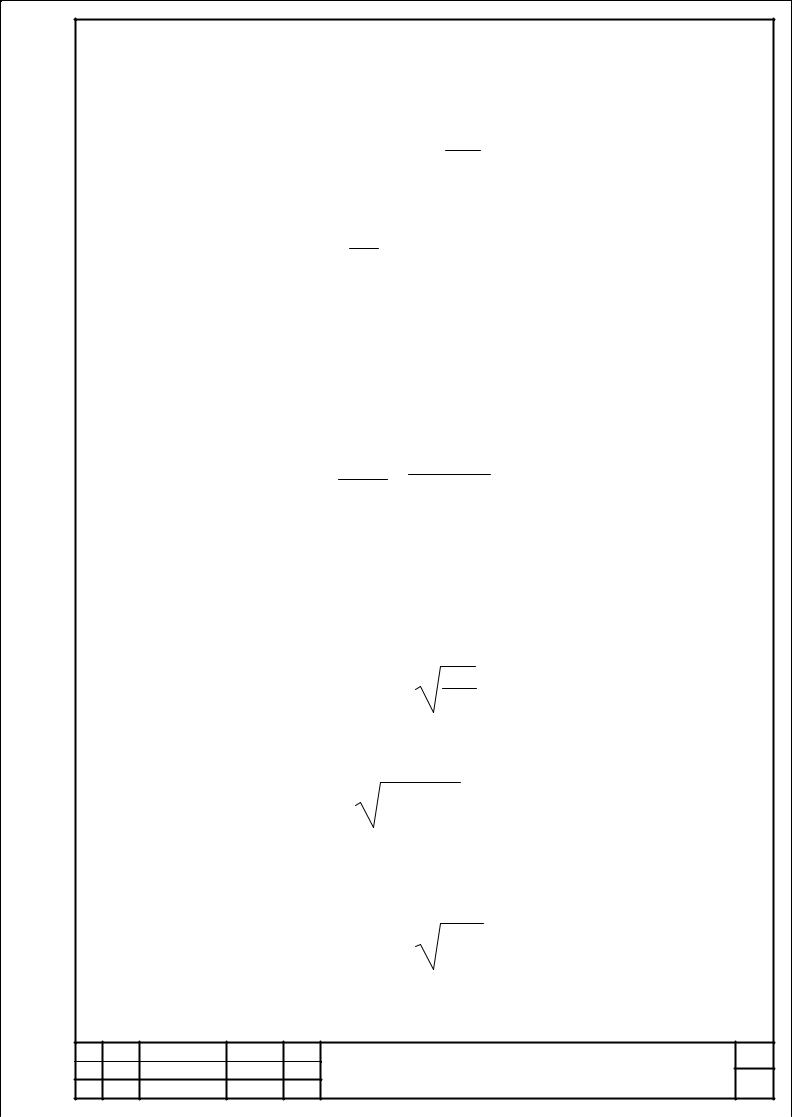
2.2.4 Расчет геометрических размеров колонны |
||||||
Для выбранного катализатора при давлении 5 МПа и температуре 300..350 °С |
||||||
объемная скорость реакции составляет 280…300 кг/(м3 × ч) [1]. Принимаем |
||||||
|
|
|
ω := 290 кг |
|||
|
|
|
|
|
|
3 |
|
|
|
|
|
|
м ч |
Тогда требуемый объем катализатора |
||||||
|
|
Vкат := Gвх |
= 16000 / 290 = 55,2 м3 |
|||
|
|
ω |
|
|
|
|
В соответствии с промышленным аналогом принимаем аппарат диаметром |
||||||
|
|
|
D = 3200 мм |
|||
Скорость движения газа в слое аппарата |
||||||
|
|
4 Vвых |
|
|
4 × 0.3897 |
|
|
|
ω = π D2 |
= |
|
3.14 × 3.22 = 0.048 м/с |
|
Тогда расчетная высота катализаторного слоя |
||||||
|
|
4 Vкат |
|
4 × 55.2 |
||
|
|
H := |
|
|
= 3.14 × 3.22 = 6.8 м. |
|
|
|
π D2 |
|
|
|
|
Принимаем два слоя по 3,5 м. Общая высота катализатора составит 7,0 м. |
||||||
Высота колонны будет выше примерно в два раза за счет различных внутренних |
||||||
устройств. |
|
|
|
|
|
|
Рассчитаем диаметры штуцеров ввода и вывода газа. Расчетный диаметр |
||||||
штуцера входа газа |
|
|
|
|
||
|
|
|
Dвх = |
4Vвх |
||
|
|
|
π ω, |
|||
где Vвх – объемный расход газов при рабочих условиях, м3/с; |
||||||
ω – линейная скорость, принимаем 10 м/с [4]; |
||||||
|
|
Dвх = |
4 × 0,3969 |
|||
|
|
|
3,14 × 10 = 0,475 м |
|||
Принимаем стандартное значение |
|
|||||
|
|
|
Dвх = 0,500 м |
|||
Расчетный диаметр штуцера выхода газа |
||||||
|
|
Dвых = |
4Vвых |
|||
|
|
π ω , |
||||
где Vвых – объемный расход газов при рабочих условиях, м3/с; |
||||||
ω – линейная скорость, принимаем 8 м/с [4]; |
||||||
|
|
|
|
|
|
Лист |
Изм. Лист |
N докум. |
Подп. Дата |
|
|
|
22 |
|
|
|
|

|
|
Vхр = 24 × Vм = 24 × 1,37 = 32,9 м3 |
||
Принимаем максимальное заполнение емкости ψ = 80%, тогда объем емкости |
||||
|
|
Vемк = Vхр / ψ = 32,9 / 0.8 = 41,1 м3 |
||
Принимаем отношение диаметра емкости к ее длине α = 5. Соответственно |
||||
диаметр емкости |
|
|
|
|
|
|
3 |
4 Vемк |
3 4 × 41,1 |
|
|
Dемк = |
π α = |
3.14 × 5 = 2.18 м |
Принимаем стандартный диаметр |
|
|||
|
|
|
Dемк = 2,2 м |
|
Тогда длина емкости |
|
|
||
|
|
Lемк = αDемк = 5 × 2,2 = 12,0 м |
||
Расчет аппарата воздушного охлаждения (см. поз. 16 на технологической |
||||
схеме). Аппарат предназначен для охлаждения газа от 150 °С до 50 °С. Объемный |
||||
расход газа в соответствии с технологическим расчетом колонны синтеза состав- |
||||
ляет |
|
|
|
|
|
|
|
Gг = 97,0 кг/с |
|
Схема к расчету АВО показана на рисунке 2.5. |
||||
tí |
|
tâê |
|
tâê |
|
|
|
|
|
Горячий газ |
|
|
|
|
Gã , Vã |
Gã |
|
|
Gã |
|
|
|
||
|
2 |
|
|
2 |
|
|
Áëîê 1 |
|
Áëîê 2 |
|
|
Q/2 |
|
Q/2 |
|
|
|
|
Охлажденный газ |
|
|
|
|
tê |
|
|
tâí |
|
t |
|
|
|
|
âí |
|
|
Рисунок 2.5 – Схема к расчету АВО |
||
|
|
|
|
Лист |
Изм. Лист |
N докум. |
Подп. Дата |
|
24 |
|
|

По справочным данным определяем теплоемкости воздуха при начальной и конечной температурах соответственно [4, прил. XIII]:
cвн := 1.005 кДжкг К
кДж cвк := 1.009 кг К
Тогда расход воздуха на охлаждение
Gв := |
Q |
= |
2080 |
|
= 102 кг/с |
|
1.009 × 40 – 1.005 × 20.6 |
|
|||
cвк tвк − cвн tвн |
Принимаем к установке два одинаковых теплообменника, в каждом из которых расход воздуха
Gв12 = Gв / 2 = 102 / 2 = 51 кг/с
Определим объемный расход воздуха
V := |
Gв |
, |
|
|
|
|||
ρв |
|
|
|
|||||
|
в |
|
|
|
|
|
||
где ρв – плотность воздуха при начальных условиях. |
||||||||
Плотность определим по формуле |
|
|
|
|
|
|
||
ρв := ρв0 |
|
T0 |
|
, |
||||
tвн + 273К |
||||||||
|
|
|
||||||
где ρв0 – плотность воздуха при нормальных условиях, ρв0 = 1.293 кг/м3 |
||||||||
[5, табл. IV]. Соответственно |
|
|
|
|
|
|
||
273 |
|
|
= 1.202 кг/м3 |
|||||
ρв = 1.293 × |
|
|
||||||
20.6 + 273 |
Тогда объемный расход воздуха
Vв = 1.20251 = 42 м3/с
Определим коэффициент теплопередачи для пучка гладких труб. Для теплообменника принимаем гладкие трубы из нержавеющей стали с внутренним диа-
метром d1 = 21 мм и толщиной стенки δтр = 2 мм. Длину трубок примем 8 м. Наружный диаметр
|
|
|
|
d2 := d1 + 2δтр = 21 + 2 × 2 = 25 мм. |
|
|
|
|
|
|
|
|
|
|
|
|
|
|
|
Лист |
|
|
|
|
|
|
|
|
|
|
|
|
|
26 |
Изм. |
Лист |
N докум. |
Подп. |
Дата |
|
|
|
|

110.5 – 28.9
∆Tср = 110.5 = 60.9 °C 2.3 × lg 28.9
Определение поверхности теплообмена. Поверхность теплообмена каждого (приято два теплообменника, общая тепловая нагрузка которых 20.08 МВт, а одного соответственно 10.04 МВт) теплообменника определяется по формуле
F := |
Q |
= |
10.04 |
= 8754 м2 |
|
|
|
30 × 60.9 |
|||
K ∆Tср |
Действительная поверхность теплообмена
Fд = N F1 = 14784 × 0.628 = 9284 м2
Запас поверхности теплообмена
ϕ = Fд – F = 9284 – 8754 × 100% = 6.05 % F 8754
Лист
|
|
|
28 |
|
Изм. Лист N докум. |
Подп. |
Дата |
||
|

Аппарат состоит из цилиндрической обечайки 2 и двух эллиптических днищ 1. Внутри аппарата на двух опорных тарелках 8 расположен слой катализатора, который закрывается сверху решетками 6.
Верхнее днище является съемным и крепится к обечайке при помощи фланцевого соединения 11. Нижнее днище приваривается к обечайке.
Аппарат установлен на цилиндрической опоре 9, в которой предусмотрены отверстия для штуцеров выгрузки насадки, вывода метанола и доступа внутрь опоры для обслуживания колонны. Вверху опоры есть небольшое отверстие для выхода газов, скапливающихся под колонной.
Для обслуживания внутренних устройств колонны над опорными тарелками размещены два люк-лаза.
3.2 Выбор материала для изготовления аппарата
Аппарат состоит из двух трех крупных блоков – обечайки, трубчатки и корзины с катализатором. Давление в аппарате равно 5,0 МПа
Для обечайки, подверженной действию температуры 350 °С, выбираем высоколегированную сталь 12Х18Н10Т, предназначенную для работы при температуре до 600 °С.
Определим допускаемые напряжения для стали 12Х18Н10Т. Для выбранного материала при 350 °С [5]
σB = 450 МПа, σB20 = 660 МПа,
σT = 180 МПа, σT20 = 250 МПа
Определим номинальное допускаемое напряжение. Согласно [6, табл. 14.5] расчет для легированной стали при рабочей температуре менее 525 °С необходимо вести по формулам
|
σ |
B ; |
σ |
|
, |
σ* = min |
|
|
T |
||
nB |
nT |
|
где nB – запас прочности по пределу прочности, для стального проката из ле-
гированной стали nB = 2,6 [6, табл. 14.6];
nT – запас прочности по пределу текучести, для стального проката из легированной стали при давлении в аппарате более 0,5 МПа nT = 1,5 [6, табл. 14.6].
Лист
|
|
|
30 |
|
Изм. Лист N докум. |
Подп. |
Дата |
||
|

Рисунок 3.2 – Схема к расчету толщины стенки цилиндрической обечайки Исполнительную толщину стенки s цилиндрической обечайки определяют по
формуле
|
|
s = sp + c , |
|||
где sр – расчетная толщина стенки |
|
|
|
||
|
|
ppD |
|
pиD |
|
sp = max |
|
|
; |
|
, |
2ϕ[σ] – pp |
2ϕ[σ]и – pи |
где pp и pи – расчетное давление в аппарате и давление при гидроиспытаниях соответственно, МПа;
D – внутренний диаметр обечайки;
ϕ – коэффициент прочности сварных швов стальных аппаратов, для автома-
тической сварки под слоем флюса ϕ = 1,0 [7, т. 1.7];
sp – расчетная толщина стенки цилиндрической обечайки, мм; c – прибавка к расчетной толщине, мм.
Расчетное давление в аппарате
pp = pт + рг,
где рт – технологическое давление в аппарате, определяемое в технологиче-
ском расчете, рт = 5,0 МПа;
рг – гидростатическое давление столба жидкости в аппарате, рг = 0 МПа рр = 5,0 + 0,0 = 5,0 МПа.
Давление при испытаниях
|
|
|
|
|
|
1,25 × 5,0 ×167/120 |
|
8,69 |
|
|
|||||
|
|
|
1,25pт[σ]20/[σ] |
|
= 8,69 МПа |
||||||||||
|
|
pт + 0,3 |
|
|
5,0 + 0,300 |
|
|
|
|
||||||
ри = max |
= max |
= max 5,30 |
|||||||||||||
|
Соответствующая расчетная толщина стенки |
|
|
|
|
|
|
||||||||
|
|
|
|
|
|
5,00 × 3200 |
|
|
|
|
|
|
|
||
|
|
|
|
|
|
2 × 1,0 × 120 – 5,00 |
|
|
68,1 |
|
|
|
|||
|
|
|
sp = max |
8,69 × 3200 |
= max |
|
|
|
|
|
|||||
|
|
|
65,5 = 68,1 мм |
||||||||||||
|
|
|
|
|
|
|
|
|
|
|
|
|
|
||
|
|
|
|
|
2 × 1,0 × 167 – 8,69 |
|
|
|
|
|
|
||||
|
Прибавка к расчетной толщине обечайки определяется по формуле |
||||||||||||||
|
|
|
|
|
|
|
|
с = Пτ + сэ, |
|
|
|
|
|
|
|
|
где П – скорость коррозии, П = 0,05 мм/год [6]; |
|
|
|
|
|
|||||||||
|
τ - срок службы аппарата, принимаем τ = 15 лет; |
|
|
|
|
|
|||||||||
|
|
|
|
|
|
|
|
|
|
|
|
|
|
|
|
|
|
|
|
|
|
|
|
|
|
|
|
|
|
|
Лист |
|
|
|
|
|
|
|
|
|
|
|
|
|
|
||
|
|
|
|
|
|
|
|
|
|
|
|
|
|
|
32 |
Изм. |
Лист |
N докум. |
Подп. |
Дата |
|
|
|
|
|
|
|
||||
|
|
|
|
|
|
|
|
|

sэp = max |
|
ppDэ |
; |
pиDэ |
|
|
|
|
|
||
2ϕ[σ] – 0,5pp |
2ϕ[σ]и – 0,5pи |
Расчетная толщина стенки
|
5,00 × 3200 |
|
|
|
|
||
|
2 × 1,0 × 120 – 0,5×5,00 |
|
68,9 |
|
|||
sэp = max |
8,69 × 3200 |
= max |
|
|
= 68,9 мм |
||
66,7 |
|||||||
|
|
|
|
|
|
||
2 × 1,0 × 167 – 0,5×8,69 |
|
|
|
Толщина стенки эллиптического днища с учетом прибавки sэ = 68,9 + 0,75 = 69.65 мм.
Принимаем исполнительную толщину стенки днища sэ = 70 мм
Допускаемое давление в рабочем состоянии и при испытаниях
[p] = |
|
2φ[σ](sэ – c) |
= |
2 × 1,0 × 120 × (70 – 0,75) |
= 5,12 МПа |
|
D + 0,5(sэ – c) |
|
3200 + 0,5 × (70 – 0,75) |
||||
[p]и = |
|
2φ[σ]и(sэ – c) |
= |
2 × 1,0 × 167 × (70 – 0,75) |
= 8,78 МПа |
|
|
D + 0,5(sэ – c) |
3200 + 0,5 × (70 – 0,75) |
3.5 Расчет фланцевых соединений
3.5.1 Штуцер ввода сырья
Определение геометрических размеров фланца. В зависимости от выбранно-
го типа обтюрации определяются геометрические размеры поверхностей под уплотнения по справочным таблицам. Для уплотнения типа шип-паз (Dу = Dвх = 500, Pу = 5,0 МПа, t = 350 °C) размеры канавки и паза приведены в таблице [6, табл. 20.5]. Схема, поясняющая числовые значения, изображена на рисунке 3.4
Лист
|
|
|
34 |
|
Изм. Лист N докум. |
Подп. |
Дата |
||
|

Принимаем изгибающий момент от действия внешних нагрузок
Mи = 0 МН×м
Константа жесткости соединения при неметаллической прокладке в металлической оболочке [6, табл. 20.28].
|
|
|
|
|
|
|
|
|
|
|
|
|
|
|
|
|
|
|
α := 1.45 |
|
|
|
|
|
|
|
|
|
Расчетное растягивающее усилие в шпильках при затяжке соединения |
||||||||||||||||||||||||||
|
|
Pб1 |
:= α Pс + Pn + |
4Mи |
= 1.45 × 1.19 + 1.21 + |
4 × 0 |
= 2.93 МН |
||||||||||||||||||||
|
|
|
|
||||||||||||||||||||||||
|
|
|
|
|
|||||||||||||||||||||||
|
|
|
|
|
|
|
|
|
|
Dn |
|
|
|
|
|
|
0.549 |
|
|||||||||
|
В рабочих условиях |
|
|
|
|
|
|
|
|
|
|
|
|
|
|
|
|
|
|
||||||||
|
|
|
Pб2 := Pс + Pn + |
4Mи |
= 1.45 + 1.21 + |
4 × 0 |
= 2.66 МН |
||||||||||||||||||||
|
|
|
|
||||||||||||||||||||||||
|
|
|
|
|
|
|
|||||||||||||||||||||
|
|
|
|
|
|
|
|
|
|
|
|
|
Dn |
|
|
|
0.549 |
|
|
||||||||
|
Диаметр окружности размещения шпилек для выбранного фланца [6, табл. |
||||||||||||||||||||||||||
21.9] |
|
|
|
|
|
|
|
|
|
|
|
|
|
|
|
|
|
|
|
|
|
|
|
|
|
|
|
|
|
|
|
|
|
|
|
|
|
|
|
|
|
|
|
|
Dб = 620 мм |
|
|
|
|
|
|
||||
|
Диаметр шпилек для выбранного фланца [6, табл. 21.9] |
||||||||||||||||||||||||||
|
|
|
|
|
|
|
|
|
|
|
|
|
|
|
|
|
|
dб = 32 мм |
|
|
|
|
|
|
|
|
|
|
Количество шпилек для выбранного фланца [6, табл. 21.9] |
||||||||||||||||||||||||||
|
|
|
|
|
|
|
|
|
|
|
|
|
|
|
|
|
|
|
z = 20 |
|
|
|
|
|
|
|
|
|
Площадь поперечного сечения шпилек |
|
|
|
|
|
|
|
|
||||||||||||||||||
|
|
|
|
|
Fб = |
πdб2 |
= |
3,14 × 322 |
|
|
2 |
|
|
|
|||||||||||||
|
|
|
|
|
4 |
|
|
4 |
= 804 мм |
||||||||||||||||||
|
Принимаем материал шпилек - сталь 15ХМ с характеристиками при t = 350 |
||||||||||||||||||||||||||
°C [6] |
|
|
|
|
|
|
|
|
|
|
|
|
|
|
|
|
|
|
|
|
|
|
|
|
|
||
|
|
|
|
|
|
|
|
|
|
|
|
|
[σ]б20 = 450 МПа |
||||||||||||||
|
|
|
|
|
|
|
|
|
|
|
|
|
[σ]бт = 370 МПа |
||||||||||||||
|
Напряжение в шпильках при затяжке и в рабочих условиях соответственно |
||||||||||||||||||||||||||
|
|
|
|
σб1 = |
|
Pб1 |
= |
|
|
|
|
2,93 |
|
|
= 182 МПа |
||||||||||||
|
|
|
|
z Fб |
|
20 × 804 × 10-6 |
|||||||||||||||||||||
|
|
|
|
σб2 = |
Pб2 |
= |
|
|
|
|
2,66 |
|
|
= 165 МПа |
|||||||||||||
|
|
|
|
z Fб |
|
|
20 × 452×10-6 |
|
|||||||||||||||||||
|
Результаты расчетов позволяют сделать вывод, что принятое фланцевое со- |
||||||||||||||||||||||||||
единение обеспечит герметичность стыка. |
|
|
|
|
|
|
|
|
|||||||||||||||||||
|
|
|
|
|
|
|
|
|
|
|
|
|
|
|
|
|
|
|
|
|
|
|
|
|
|
|
|
|
|
|
|
|
|
|
|
|
|
|
|
|
|
|
|
|
|
|
|
|
|
|
|
|
|
|
Лист |
|
|
|
|
|
|
|
|
|
|
|
|
|
|
|
|
|
|
|
|
|
|
||||||
|
|
|
|
|
|
|
|
|
|
|
|
|
|
|
|
|
|
|
|
|
|
|
|
|
|
|
36 |
Изм. |
Лист |
N докум. |
|
Подп. |
Дата |
|
|
|
|
|
|
|
|
|
|
|
|
|
|
|
|||||||
|
|
|
|
|
|
|
|
|
|
|
|
|
|
|
|
|
|
|
|
|
|
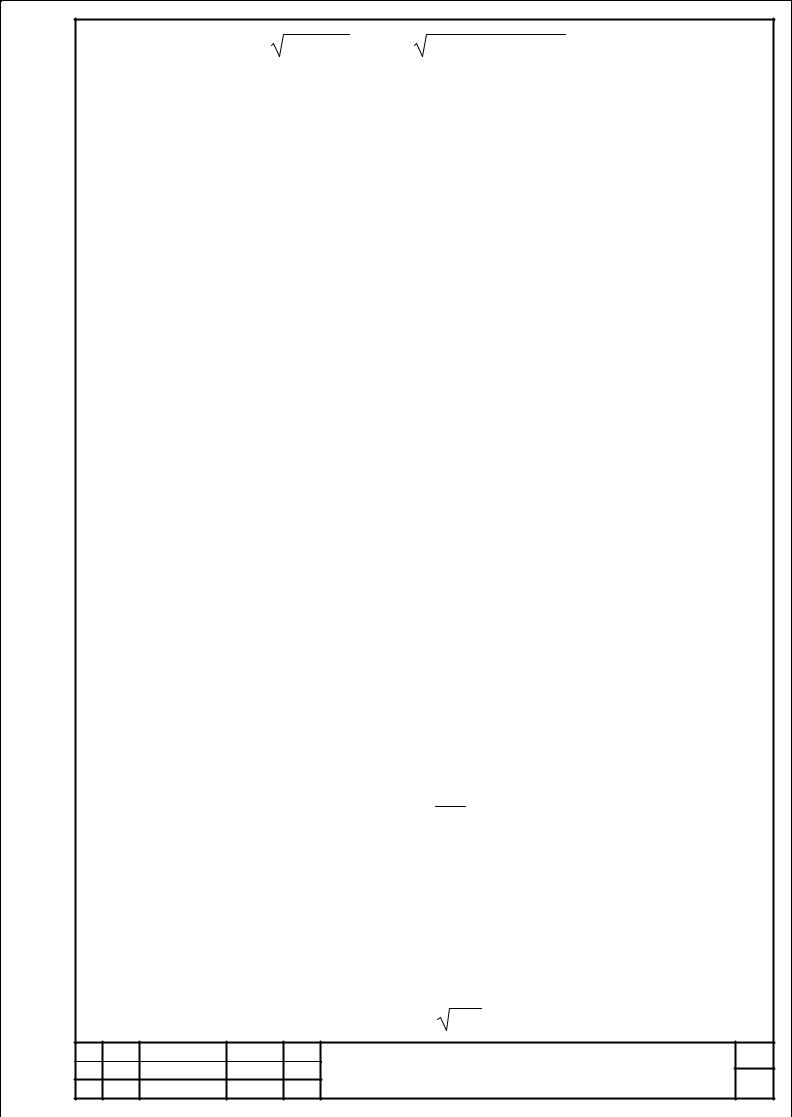
|
|
hв = 0,5 D(s0 – c) = 0,5 × |
3200 × (80 – 0,75) = 177,5 мм |
|||||
Принимаем hв = 180 мм. Диаметр шпилечной окружности фланцев |
||||||||
|
|
Dб ≥ D + 2(s0 + dб + u), |
||||||
где dб – наружный диаметр шпилек, для проектируемого фланца рекомен- |
||||||||
дуемый диаметр составляет 48 мм [1, т. 1.40]; |
|
|
||||||
u – нормативный зазор между гайкой и втулкой, u = 15 мм [1, с. 95]. |
||||||||
Соответственно |
|
|
|
|
|
|
||
|
|
Dб = 3200 + 2 × (80 + 48 + 15) = 3485 мм |
||||||
Наружный диаметр фланца |
|
|
|
|
|
|
||
|
|
|
Dн = Dб + a, |
|||||
где a – конструктивная добавка для размещения гаек по периметру, a = 120 |
||||||||
мм [1, т. 1.41]. Итого |
|
|
|
|
|
|
||
|
|
Dн = 3485 + 120 = 3605 мм. |
||||||
Наружный диаметр прокладки |
|
|
|
|
|
|
||
|
|
|
Dнп = Dб - e, |
|||||
где e – нормативный параметр, зависящий от типа прокладки, для плоских |
||||||||
прокладок и dб = 48 мм e = 80 мм. Тогда |
|
|
|
|
||||
|
|
Dнп = 3485 – 80 = 3405 мм. |
||||||
Средний диаметр прокладки |
|
|
|
|
|
|
||
|
|
|
Dсп = Dнп – b, |
|||||
где b – ширина прокладки, мм. |
|
|
|
|
|
|
||
Для плоских металлических прокладок b = 15 мм [1, т. 1.42]. Значит |
||||||||
|
|
Dсп = 3405 – 15 = 3390 мм. |
||||||
Количество шпилек, необходимое для обеспечения герметичности соедине- |
||||||||
ния |
|
|
|
|
|
|
|
|
|
|
|
nб ≥ |
πDб |
, |
|
||
|
|
|
|
tш |
|
|||
где tш – рекомендуемый шаг расположения шпилек, для p = 5 МПа tш ≈ 4dб = |
||||||||
4 × 48 = 192 мм [1. т. 1.43]. Соответственно |
|
|
|
|||||
|
|
nб ≥ |
3,14 × 3485 |
= 57,0 |
||||
|
|
|
192 |
|
|
|||
Принимаем значение, кратное четырем nб = 56 шт. Ориентировочная высота |
||||||||
фланца |
|
|
|
|
|
|
|
|
|
|
|
hф = λф |
Dsэк, |
||||
|
|
|
|
|
|
|
|
Лист |
Изм. Лист |
N докум. |
Подп. Дата |
|
|
|
|
|
38 |
|
|
|
|
|
|

Реакция прокладки |
|
|
|
|
|
|
|
|
|
|
|
|
|
|
|
|
|
|
|
|
|||
|
|
|
|
|
|
R п π.D сп.b 0.K пр.p p, |
|
|
|||||||||||||||
|
|
|
|
|
|
|
|
R п = 0.298 МН |
|
|
|
|
|
||||||||||
Равнодействующая внутреннего давления |
|
|
|
|
|
|
|
||||||||||||||||
|
|
|
|
|
|
|
F д |
p p.π. |
D |
сп2 |
|
|
|
|
|
||||||||
|
|
|
|
|
|
|
|
|
|
4 |
|
|
|
|
|
|
|||||||
|
|
|
|
|
|
|
|
|
|
|
|
|
|
|
|
|
|
|
|
|
|
|
|
|
|
|
|
|
|
|
|
F д = 3.272 |
|
|
МН |
|
|
|
|
|
|||||||
Для определения коэффициента жесткости фланцевого соединения опреде- |
|||||||||||||||||||||||
лим несколько вспомогательных величин. Линейная податливость неметалличе- |
|||||||||||||||||||||||
ской прокладки |
|
|
|
|
|
|
|
|
|
|
|
|
|
|
|
|
|
|
|
|
|
|
|
|
|
|
|
|
|
|
|
|
|
|
|
k п.h п |
|
|
|
|
|
|
|||||
|
|
|
|
|
|
y п π.E п.D сп.b |
|
|
|
|
|
||||||||||||
|
|
|
|
|
|
|
|
y п = 13.925 |
|
|
мм |
|
|
|
|
|
|||||||
|
|
|
|
|
|
|
|
|
|
|
|
|
|
|
|
МН |
|
|
|
|
|
||
Угловая податливость фланца |
|
|
|
|
|
|
|
|
|
|
|
|
|
|
|
||||||||
|
|
|
y ф |
1 |
|
|
ν. 1 |
|
0.9.λ |
ф2 |
. |
ψ |
2 |
|
|||||||||
|
|
|
|
|
|
|
|
|
|
|
|
|
|
|
|
|
|||||||
|
|
|
|
|
|
|
|
|
3. |
E ф |
|
|
|
|
|
||||||||
|
|
|
|
|
|
|
|
|
|
|
|
|
|
|
|
|
|
||||||
|
|
|
|
|
|
|
|
|
|
|
h ф |
|
|
|
|
|
|
|
|||||
Значения входящих коэффициентов |
|
|
|
|
|
|
|
|
|
|
|
|
|||||||||||
|
|
ν |
|
|
|
|
|
|
1 |
|
|
|
|
|
|
|
|
|
|
|
|
|
|
|
|
|
|
|
|
|
|
|
|
|
|
|
|
|
|
2 |
|
|
|
|
|
h ф |
|
|
|
1 |
0.9 |
. |
λ ф2 |
. |
1 |
ψ 1 |
. |
h ф |
|
|
λ |
ф2 |
|||||||||
|
|
s эк |
|
|
|
|
D.s эк |
||||||||||||||||
|
|
|
|
|
|
, |
|
|
|
|
|||||||||||||
|
|
|
ψ 1 |
|
|
|
|
. |
|
D |
н |
|
|
ψ |
|
|
D н |
|
D |
||||
|
|
|
|
1.28 |
|
log D |
, |
|
|
|
2 |
|
D н |
|
D |
||||||||
Вычисления |
|
|
|
|
|
|
|
|
|
|
|
|
|
|
|
|
|
|
|
|
|
|
|
|
ψ 1 = 0.031 |
, |
ψ 2 = 35.667 |
|
, λ ф2 = 0.461 |
, ν = 0.5 |
|||||||||||||||||
|
|
|
|
|
|
y ф = 2.378 10 4 |
|
|
|
|
1 |
|
|
|
|
||||||||
|
|
|
|
|
|
|
|
|
МН.мм |
|
|
||||||||||||
Линейная податливость шпилек |
|
|
|
|
|
|
|
|
|
|
|
|
|
||||||||||
|
|
|
|
|
|
|
|
|
|
|
|
|
|
|
|
|
|
|
|
|
|
|
Лист |
Изм. Лист |
N докум. |
Подп. |
Дата |
|
|
|
|
|
|
|
|
|
|
|
|
|
|
|
|
|
|
|
40 |
|
|
|
|
|
|
|
|
|
|
|
|
|
|
|
|
|
|
|
|