
Переработка нефти-3
.pdfvk.com/club152685050 | vk.com/id446425943
ИТС 30-2017
реакций меняется, что и отражается на конверсии сырья, выходе и качестве целевых и побочных продуктов. Получаемые продукты каталитического крекинга по своему химическому составу имеют следующие особенности:
а) бензин содержит много изопарафинов и ароматических углеводородов; б) газ имеет высокую концентрацию изобутана и олефинов;
в) газойлевые фракции богаты полициклическими и ароматическими углеводородами.
Основными факторами, влияющими на процесс каталитического крекинга, являются:
а)
б)
в)
г)
д)
е)
Качество сырья
Тяжелое сырье дает больший выход бензина и меньший выход газа, сырье с большим содержанием ароматики дает наибольший выход кокса и наименьший выход бензина. Лучший выход бензина и наименьший выход кокса дает нафтеновое сырье.
Свойства катализатора
Для обеспечения максимального выхода целевых продуктов и достижения высоких технико-экономических показателей катализатор крекинга должен иметь следующие основные свойства:
а) высокую активность, определяющую глубину превращения исходного сырья при равных прочих условиях;
б) высокую избирательность, которая оценивается способностью катализатора ускорять реакции в требуемом направлении, снижать скорость побочных реакций;
в) стабильность. Катализатор должен быть стойким к истиранию, растрескиванию и давлению вышележащих слоев, а также не должен изнашивать аппаратуру;
г) регенерируемость. Характеризует способность быстро и многократно восстанавливать свою активность и избирательность при окислительной регенерации без нарушения поровой структуры и разрушения частиц.
Температура процесса
Каталитический крекинг обычно проводят в интервале температур 500 ч- 5400 С.
С ростом температуры в рабочей зоне увеличивается общая глубина превращения сырья, выход сухого газа, выход фракции Сз-Сл, количество пропилена и бутилена и в сравнительно небольшой степени повышается выход стабильного бензина. Повышение температуры в реакторе также увеличивает глубину превращения и выход кокса.
Увеличение подогрева сырья повышает температуру в регенераторе и уменьшает отложение кокса на отработанном катализаторе. Увеличение рециркуляции
133

vk.com/club152685050 | vk.com/id446425943
vk.com/club152685050 | vk.com/id446425943
ИТС 30-2017
Переработка сырья с высокой объемной скоростью (при сохранении неизменных прочих условий процесса) дает больший абсолютный выход бензина, чем крекинг с малой объемной скоростью. Относительный выход (в % вес. на сырье) бензина с ростом объемной скорости снижается. С уменьшением объемной скорости, особенно в области малых численных ее значений, увеличивается выход кокса и плотность каталитического газойля.
Сущность процесса регенерации катализатора состоит в окислительном отжиге кокса с поверхности катализатора при температуре 650-700 °С. Для равномерного выжига кокса процесс осуществляется в псевдоожиженном слое, поддерживаемом потоком воздуха.
Общая блок-схема секции представлена на рисунке 2.44. Поскольку реактор и регенератор каталитического крекинга конструктивно исполнены одним блоком, будет дано единое описание подпроцессов каталитического крекинга и регенерации катализатора.
Каталитический крекинг и регенерация катализатора в псевдоожиженном
слое
Крекинг данного типа представлен на отечественных заводах установками типа 43-102. Принципиальная схема реакторно-регенераторного блока установки такого типа приведена на рисунке 2.44. Сырье I после нагрева в печи до 470-490 °С поступает в реактор 1, где происходят реакции каталитического крекинга. Из зоны крекинга катализатор поступает в зону отпарки в нижней части реактора, где отпаривающим агентом выступает пар III.
Рисунок 2.44 - Принципиальная схема реакторно-регенераторного блока установок с движущимся шариковым катализатором: 1 - реактор, 2 - напорные стояки катализатора, 3 - регенератор, 4 - сепаратор, 5 - паросборник, 6 - насос, 7 - печь, 8 - воздуходувка, 9 ,1 0 - бункеры-сепараторы, 11,12дозаторы пневмотранспорта. I - сырье, II - продукты крекинга, III - водяной пар, IV - вода, V - воздух,
VI - дымовые газы, VII - водяной пар.
Продукты реакции II поступают на фракционирование, а катализатор - в бункер отработанного катализатора 12. Закоксованный катализатор поднимается по стояку 2 в
135
vk.com/club152685050 | vk.com/id446425943
ИТС 30-2017
бункер 10, а оттуда - в регенератор 3. В регенераторе при температуре 680-700 °С происходит выжиг кокса воздухом с поверхности катализатора, в нижней части регенератора температура снижается до 580-600 °С за счет охлаждающих змеевиков. Снятое тепло при этом используется для генерации пара. Регенерированный катализатор по трубопроводу поступает в бункер 11, откуда возвращается в распределительное устройство реактора 9. Для сохранения постоянного фракционного состава катализатора часть циркулирующего катализатора отдувается в сепараторе.
Технологический режим и примерный материальный баланс крекинга вакуумного газойля для установки с движущимся слоем катализатора приведены ниже:
Температура, °С: |
|
|
|
|
- |
нагрева сырья |
470 - 490 |
|
|
- |
в реакторе |
450 - 490 |
|
|
- |
в регенераторе |
680700 |
|
|
Давление, кгс/см2: |
|
|
|
|
- в реакторе |
1,7 |
|
|
|
- |
в регенераторе |
1,2 |
|
|
Кратность циркуляции катализатора, т/т сырья |
1,8 - |
2,5 |
||
Время контакта катализатора с сырьем, с |
|
1200 |
|
|
Выход продуктов, % мае.: |
|
|
|
|
сухой газ, |
|
1 ,5 -2,0 |
||
жирный газ (С3-С4 ) |
|
6,5 - |
9,5 |
|
бензин (С5-195°С) |
|
3 5 -3 8 |
||
легкий газойль (195-350°С) |
|
23 - |
27 |
|
тяжелый газойль (> 350°С) |
|
20 - 24 |
||
кокс |
|
2,5 - |
3,5 |
Большим недостатком установок с гранулированным катализатором явилась недостаточно большая мощность по сырью - фактически она составляла не выше 4000-5000 тонн в сутки из-за большого расхода транспортирующего агента (не менее 1 кг на 20 кг катализатора). Также длительное пребывание катализатора в зоне реакции (15-20 минут) приводит к недостаточно эффективному его использованию. По этой причине новых установок такого типа больше не строится, а старые по мере возможности выводятся из эксплуатации.
Каталитический крекинг в лифт-реакторе на микросферическом
цеолитсодержащем катализаторе
Открытие каталитической активности цеолитов и разработка промышленных цеолитсодержащих синтетических катализаторов крекинга привело к существенному изменению конструкции реакторного блока. Для наиболее полного использования активности цеолитсодержащих катализаторов процесс проводят в прямоточном лифтреакторе при повышенной температуре, высокой кратности циркуляции катализатора и времени контакта катализатора с сырьем порядка 3-5 с.
Принципиальная схема реакторно-регенераторного блока установок с лифтреактором и циркулирующим микросферическим катализатором приведена на рисунке 85. Сырье I проходит через теплообменник 2 и печь 1, где нагревается до 310-350 °С, после чего через форсунки поступает в низ прямоточного реактора. В реакторе сырье смешивается с катализатором, поступающим из регенератора, и поднимается в
136
vk.com/club152685050 | vk.com/id446425943
ИТС 30-2017
полусквозном потоке вверх по реактору 12, где протекают реакции каталитического крекинга. В низ реактора подается водяной пар для разгона катализатора, пар также подается в сырьевые форсунки для более тонкого распыла сырья. Предусмотрена подача шлама с низа основной ректификационной колонны в реактор.
Газокатализаторный поток из реактора поступает в сепаратор 9. Пары продуктов отделяются от катализатора сначала в сепарирующем устройстве, затем в высокоэффективных циклонах на выходе из сепаратора. Отработанный катализатор поступает в десорбер 10, где потоком пара с катализатора удаляются адсорбированные тяжелые углеводороды. Закоксованный катализатор VIII из десорбера поступает в регенератор 11, где в псевдоожиженном слое потоком воздуха III, подаваемого воздуходувкой 4, происходит его регенерация. Регенерированный катализатор XI поступает обратно в реактор, а дымовые газы регенерации VII сначала отделяются от катализатора в высокоэффективных циклонах 13, затем проходят через котел-утилизатор 8, где часть тепла используется для генерации пара, после чего происходит доочистка от катализаторной пыли в электрофильтре 7. Очищенные дымовые газы V выбрасываются в атмосферу. Уловленный катализатор поступает в бункер 5, куда также загружается свежий катализатор VI, предназначенный для компенсации потерь микросферического катализатора с продуктами реакции и дымовыми газами.
Рисунок 2.45 - Принципиальная схема реакторно-регенераторного блока установок
|
с лифт-реактором. 1 - трубчатая печь; 2 - теплообменник; 3 - |
насос; |
4 |
- подогреватель воздуха; 5 - бункер для катализатора; 6, 13 - |
циклоны; |
7 - |
электрофильтр; 8 - котел-утилизатор; 9 - сепарационная зона реактора; |
10 - отпарная зона реактора; 11 - регенератор с кипящим слоем; 12 - лифт-реактор; 13 - емкость;
I - сырье; II - топливо на нагрев воздуха; III - воздух; IV - свежий катализатор на догрузку системы; V - очищенные дымовые газы; VI - катализаторная пыль; VII - дымовые газы; VIII - закоксованный катализатор; IX - продукты реакции; X - водяной пар; XI - регенерированный катализатор; XII - шлам.
137

vk.com/club152685050 | vk.com/id446425943
vk.com/club152685050 | vk.com/id446425943
ИТС 30-2017
Подписи к в: 1 - прямоточный реактор; 2 - сырьевые форсунки; 3 - шламовые форсунки; 4 - циклон грубой очистки; 5 - система охлаждения продуктов крекинга; 6 - двухступенчатая отпарная секция; 7 - парораспределительное устройство; 8 - одноступенчатые циклоны; 9 - транспортная линия; 10 - узел распределения отработанного катализатора; 11 - воздухораспределительное устройство; 1 2 - двухступенчатые циклоны; 13 - напорная камера; 14 - напорный стояк; 15 - шиберная задвижка; 16 - J-образный переток
Конкретная конструкция реактора и регенератора отличается по установкам (рисунок 2.46). Типовым для новых установок является реакторный блок типа Г-43- 107М (рисунок 2.46.а), отличающийся разновысотным расположением регенератора и реактора, соосным расположением сепаратора и лифт-реактора, а также наклонными напорными стояками, которые позволяют катализатору поступать из одного аппарата в другой самотеком под действием перепада давления. Устаревшие типы установок (1А/1М и ГК-3) модернизированы в зависимости от их исходной конструкции. В обоих случаях старый реактор переделан в сепаратор, а новый прямоточный лифт-реактор либо смонтирован взамен транспортной линии катализатора (1А/1М), либо сделан выносным (ГК-3).
Ф ракционирование продуктов крекинга
Разделение продуктов крекинга осуществляется в основной фракционирующей колонне. Пары продуктов крекинга из реактора по трансферной линии поступают в промывочно-сепарационную секцию основной фракционирующей колонны, оборудованную в нижней части ситчатыми двухпоточными тарелками. На тарелках происходит контакт перегретых и загрязненных катализатором паров, поступающих из реактора с жидкостью в колонне. При контакте паров с жидкостью происходит охлаждение паров для прекращения реакции крекинга, отмывка их от катализаторной пыли и частичная конденсация высококипящих углеводородов. Отмытые от катализаторной пыли и охлажденные до температуры насыщения пары поступают в концентрационную секцию колонны на разделение.
Тяжелый газойль в смеси с катализаторной пылью с низа колонны подается в шламоотстойник, в котором происходит отстаивание катализатора. С низа шламоотстойника шлам направляется в прямоточный реактор каталитического крекинга. Отстоявшийся от катализаторной пыли тяжелый газойль в постоянном количестве возвращается в основную колонну, а балансовый избыток выводится с установки после охлаждения в теплообменнике. Предусмотрена возможность осуществления рециркуляции тяжелого газойля в качестве сырья крекинга.
Фракция легкого газойля из колонны боковым погоном выводится в отпарную колонну (стриппинг). В стриппинге происходит отпарка легких фракций бензина из легкого газойля перегретым водяным паром. Пары из стриппинга возвращаются в колонну. Из куба стриппинга легкий газойль откачивается в теплообменники для охлаждения и далее выводится с установки.
Пары с верха основной колонны (углеводородный газ, нестабильный бензин, водяной пар) поступают в конденсаторы-холодильники и далее в рефлюксную емкость, где происходит разделение на нестабильный бензин, жирный газ и воду. Нестабильный бензин из емкости частично возвращается в колонну в качестве острого
139
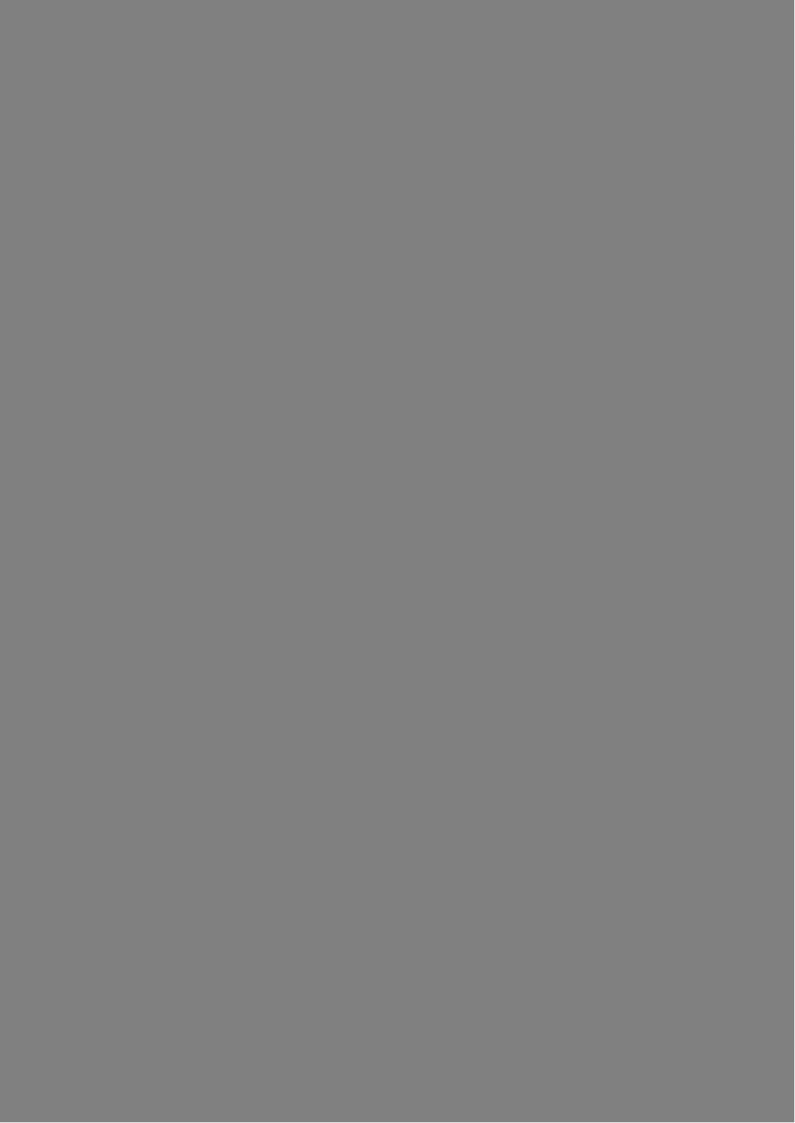
vk.com/club152685050 | vk.com/id446425943
vk.com/club152685050 | vk.com/id446425943
ИТС 30-2017
стабильным бензином крекинга в специальном аппарате - фракционирующем абсорбере. Разделение углеводородов С1-С2 и более тяжелых возможно вследствие их разной растворимости; так, растворимость пропана в бензине крекинга примерно в 2030 раз выше, чем этана.
Нестабильный бензин крекинга после выделения в основной фракционирующей колонне поступает во фракционирующий абсорбер. Туда же подается жирный газ крекинга после проведения его очистки от сероводорода раствором амина. Абсорбентом в колонне служит стабильный бензин. С низа абсорбера выводится нестабильный бензин в стабилизационную колонну, где он разделяется на две фракции - НК-70 °С и 70-220 °С.
С верха абсорбера выводится сухой газ, который далее подается во второй абсорбер для улавливания унесенных углеводородов Сз-Сб. Абсорбентом во втором абсорбере служит легкий газойль. Очищенный от тяжелых углеводородов сухой газ доочищается от сероводорода раствором амина и поступает в топливную сеть завода, а также на горелки печей установки каталитического крекинга. Насыщенный абсорбент с низа абсорбера возвращается в основную ректификационную колонну секции каталитического крекинга.
Примерный технологический режим работы абсорберов и колонны стабилизации приведен в таблице 2.30.
Таблица 2.30 - Технологический режим работы фракционирующих абсорберов выделения сухого газа и колонны стабилизации бензина________ _
Параметр |
Фракционирующий |
Повторный |
Колонна |
Температура верха °С |
абсорбер |
абсорбер |
стабилизации |
45 |
45 |
TT5D |
|
Температура низа, °С |
80-115 |
50 |
195-230 |
2 авление верха, атм |
a .o -ii.b |
8,5-11,0 |
7,8-10,0 |
Иавление низа, атм |
10,0-12,0 |
9,0-11,0 |
7,8-11,0 |
Демеркаптанизация легкого бензина
Технология процесса очистки фракции НК-70 °С направлена на максимальное извлечение из сырья меркаптанов и остаточного количества сероводорода с целью получения при дальнейшем фракционировании углеводородных фракций (ППФ, ББФ, легкого бензина), пригодных для использования в качестве сырья для нефтехимии и производства высокооктановых компонентов товарного бензина.
Процесс очистки включает в себя:
а) приготовление катализаторного комплекса (КТК), представляющего собой 15%-ый водный раствор гидроксида натрия, также содержит 0,1% катализатора окисления сульфидов;
б) |
стадию демеркаптанизации сырья, состоящую из следующих процессов: |
в) |
экстракция меркаптанов раствором КТК; |
г) |
водная промывка очищенного продукта; |
д) |
регенерацию раствора КТК; |
е) |
отделение дисульфидов от раствора КТК. |
Экстракция сероводорода и меркаптанов происходит по следующим реакциям: RSH + NaOH <-> RSNa + Н2О
H2S + 2NaOH -> Na2S + 2НгО
141
vk.com/club152685050 | vk.com/id446425943
ИТС 30-2017
Регенерация раствора КТК в присутствии катализатора происходит по следующим реакциям:
3Na2S + 402 + Н2 О (Kat) -> Na2S04 + Na2S203 + 2 NaOH 2RSNa + 0,5 O2 + H2O (Kat) -> RSSR + 2 NaOH
Фракция НК-70 °C, содержащая меркаптаны и остаточное количество сероводорода после аминовой очистки, подается в куб экстрактора меркаптанов. Циркулирующий раствор КТК из сепаратора дисульфидов подается на верхнюю первую тарелку экстрактора. Давление экстракции составляет 18 атм, температура - 40-50 °С.
Очищенная фракция НК-70 °С с верха экстрактора направляется в сепаратор щелочи, где происходит ее отделение от унесенных капель раствора КТК. Раствор КТК с низа сепаратора выводится в дегазатор, а фракция НК-70 °С с верха сепаратора направляется на стадию водной промывки от следов раствора КТК в колонну водной промывки. Колонна работает при 17-19 атм и температуре 30-40 °С. Очищенная и отмытая фракция НК-70 °С с верха колонны направляется в колонну выделения фракций Сз и С4.
Раствор КТК, насыщенный сульфидами и меркаптидами натрия, из дегазатора подается в куб регенератора, который представляет собой насадочную прямоточную колонну, реакционная зона которой заполнена массообменной насадкой, в качестве которой используются стальные кольца Палля размером 50x50x1. Температура нагрева раствора КТК на входе в регенератор регламентируется 50(±2) °С, т.к. уменьшение температуры ниже 45 °С ведет к снижению скорости регенерации, а увеличение температуры раствора КТК выше 60 °С ведет к дезактивации катализатора окисления.
В куб регенератора под опорную решетку через распределительное устройство для окисления сульфидов и меркаптидов подается технологический воздух от компрессора с давлением не менее 6 атм. Отработанный воздух и унесенный регенерированный КТК с дисульфидами из регенератора поступает в сепаратор воздуха, где происходит разделение отработанного воздуха и раствора КТК, содержащего дисульфиды. Отработанный воздух направляется к горелкам печи, а регенерированный раствор КТК с дисульфидами поступает в сепаратор дисульфидов, где за счет гравитационного отстоя дисульфиды отделяются от раствора КТК.
Бензин крекинга и растворенные в нем дисульфиды с верха сепаратора дисульфидов перетекают в емкость дисульфидов, а оттуда периодически, по мере накопления откачиваются на блок гидроочистки тяжелого бензина крекинга Регенерированный раствор КТК с низа сепаратора дисульфидов подается в обратно в экстрактор меркаптанов. По мере разбавления раствора КТК (за счет образования реакционной воды и солей) до концентрации активной щелочи порядка 6 % масс, часть его периодически, без прекращения циркуляции откачивается в дренажную емкость. Балансовое количество раствора КТК восполняют путем подкачки концентрированного раствора КТК.
142