
Составление сборочного чертежа
.pdf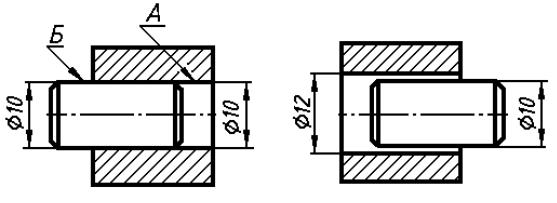
няют с относительно высокой точностью. Эти поверхности, как правило, подвергают механической обработке.
Свободные поверхности изготавливают с меньшей точностью и часто не подвергают механической обработке. Размеры свободной поверхности должны обеспечить необходимые механические свойства детали (прочность, жесткость и др.), соответствие технологическим требованиям (приливы, бобышки, проточки и т. п.), удобство эксплуатации, а также декоративные свойства детали.
На рисунке 2 приведен пример простейшего цилиндрического соединения. В этом соединении различают охватывающую (А) и охватываемую (Б)
поверхности и соответственно охватывающий и охватываемый размеры.
Рисунок 2 |
Рисунок 3 |
Размер ø 10 мм является для вала и отверстия номинальным. Номи-
нальный размер – это размер, который конструктор назначает или рас-
считывает, исходя из условий работы детали в изделии.
При изготовлении детали номинальный размер невозможно выполнить абсолютно точно. Поэтому действительный размер, полученный в результате измерения детали, несколько отличается от номинального и для партии деталей имеет разброс.
Характер соединения определяется алгебраической разностью между действительными значениями охватывающего и охватываемого размеров (положительная разность называется зазором, отрицательная - натягом).
Для обеспечения требуемого характера соединения действительные размеры деталей одной партии должны находиться в определённом интервале, ограниченном двумя предельными размерами – наибольшим и наименьшим. Алгебраическая разность между предельным и номинальным размерами называется предельным отклонением. На чертежах предельные отклоне-
ния указывают непосредственно после номинальных размеров при помощи условного обозначения или в цифровой форме, например, 10Н7 или 10+0,015;
10f 7 или 10 −−0,0130,028 .
В курсе черчения студенты определяют действительные размеры детали
11

путём измерения и наносят их как номинальные. Исключение составляют стандартные элементы детали: резьбы, проточки и т. п.; их размеры необходимо согласовывать со стандартами. Предельные отклонения студенты не указывают при выполнении работы «Сборочный чертёж».
Если номинальные размеры сопрягаемых поверхностей одинаковы, то на чертеже соединения эти поверхности изображают одной основной линией, как это показано на рисунке 2.
Если номинальные размеры сопрягаемых поверхностей различны, то имеющийся конструктивный зазор обязательно показывают (рисунок 3). Если размеры отверстия и вала, измеренные студентами, отличаются друг от друга на величину ≈1 мм и более, то зазор можно считать конструктивным.
Необходимость выполнения зазора определяется конструктивными соображениями, т. е. требованием обеспечения заданного характера соединения. С другой стороны, необоснованное усложнение технологии (отсутствие зазора там, где он мог бы быть) приводит к удорожанию производства.
На рисунке 4 приведен пример установки седла в корпусе. Соединение обеих деталей происходит по двум поверхностям: цилиндрической А и плоской Б. В то же время необходимо предусмотреть зазоры ∆1 и ∆2, т. к. одновременное сопряжение деталей по двум соосным цилиндрическим поверхностям и двум параллельным плоскостям не технологично (и не требуется по конструктивным соображениям).
Необходимо заметить, что соединение может быть не только цилиндрическим, но и коническим, а также плоским (образовано двумя плоскостями, см. рисунок 6) или сложным (образовано несколькими различными поверхностями или несколькими деталями, например, шпоночное соединение на рисунке 5).
На рисунке 6 показано соединение маховика 3 и втулки 1 с крышкой 2, обеспечивающее поворот деталей 1 и 3 относительно крышки без значительного люфта или заклинивания (при этом шпиндель 4 будет перемещаться вдоль оси). Здесь же даны примеры сопрягаемых (СП) и свободных (СВ) поверхностей.
Рисунок 4 |
Рисунок 5 |
12

Рисунок 6
На рисунке 7 показан валик, состоящий из двух соосных цилиндров вращения. Для его изготовления достаточно задать четыре размера. Они могут быть заданы различным образом, и от конструктора зависит выбор наиболее целесообразного варианта.
Пятый размер на рисунке 7г только затрудняет понимание чертежа, т. к. становится неясным, от какой плоскости заданы размеры l1 и l2 Размер L может быть указан только как справочный.
Рисунок 7
13
Черными треугольниками (рисунок 7) условно отмечены плоскости, от которых должны отсчитываться соответствующие размеры – l1, l2 или L. Эти плоскости (на рисунках 7а, 7б – торцы, на рисунке 7в - заплечик) назы-
вают базовыми.
Правильный выбор баз – необходимое условие создания работоспособного изделия.
Всоответствии с ГОСТ 21495 – 76, база – поверхность или выполняющее ту же функцию сочетание поверхностей, ось, точка, принадлежа-
щая заготовке или изделию и используемая для базирования.
Базирование – придание заготовке или изделию требуемого положения относительно выбранной системы координат.
Базы по назначению разделяются на три вида: конструкторские, тех-
нологические и измерительные.
Конструкторская база (КБ) – база, используемая для определения положения детали или сборочной единицы в изделии.
Основная конструкторская база (ОКБ) – конструкторская база дан-
ной детали или сборочной единицы, используемая для определения её поло-
жения в изделии.
Вспомогательная конструкторская база (ВКБ) – конструкторская ба-
за данной детали или сборочной единицы, используемая для определения по-
ложения присоединяемого к ним изделия.
Технологическая база – база, используемая для определения относи-
тельного положения заготовки или изделия при изготовлении или ремон-
те.
Измерительная база – база, используемая для определения относи-
тельного положения заготовки или изделия и средств измерения.
Согласно ГОСТ 2.307 – 68, размеры, определяющие расположение сопрягаемых поверхностей, проставляют, как правило, от конструкторских баз с учётом возможностей выполнения и контроля этих размеров.
Вприведенном на рисунке 6 примере при сборке соединения втулку 1 устанавливают снизу в крышке 2 так, чтобы основная конструкторская база втулки (ОКБ - 1) совместилась со вспомогательной конструкторской базой (ВКБ - 2) крышки. Затем маховик 3 навинчивают на втулку до упора так, чтобы плоскость его основной конструкторской базы (ОКБ - 3) совпала со вспомогательной конструкторской базой (ВКБ - 1) втулки. При этом между основной конструкторской базой (ОКБ - 3) маховика и верхней плоскостью крышки должен получиться небольшой зазор (примерно от 0,1 до 0,2 мм) для подвижности соединения. Чтобы обеспечить требуемую величину зазора при наименьшей точности изготовления деталей, размер А должен быть про-
ставлен на эскизах обеих деталей от конструкторской базы (рисунок 8).
Вэтом случае при равенстве номинальных размеров А втулки и крышки зазор представляет собой разность их действительных размеров (предельные отклонения размеров А задают так, чтобы наименьший размер втулки был больше наибольшего размера крышки).
14
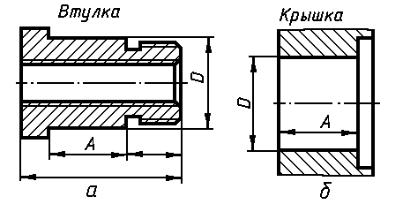
Подвижный характер цилиндрического соединения втулки и крышки при одинаковых номинальных значениях диаметра D также обеспечивают на производстве за счёт соответствующего выбора предельных отклонений этих диаметров.
Рисунок 8
Все остальные размеры длин втулки, могут быть заданы в зависимости от технологии изготовления, например, так как показано на рисунке 8а.
Таким образом, на основе анализа конструкции предложенного изделия студенты должны определить конструкторские базы каждой детали и задать размеры поверхностей от этих баз.
Простановку размеров на эскизе каждой детали следует начинать с размеров сопрягаемых поверхностей, согласовывая их с размерами других сопрягаемых деталей. Затем наносят размеры свободных поверхностей, как правило, от технологических баз с учётом технологии изготовления деталей.
При выполнении эскизов студенты должны учитывать соответствующие стандарты на элементы деталей (резьбы, проточки, фаски, конусности и т. п.), на размерные числа, на оформление чертежей ряда изделий (пружин, зубчатых колёс и т. п.). Резьбы на нестандартных деталях студенты должны измерить, т. е. определить профиль, номинальный диаметр, шаг, число заходов и направление нарезки резьбы. Если по этим параметрам может быть подобрана стандартная резьба, то на эскизе наносят только её стандартное изображение и обозначение.
Для резьбы с нестандартным профилем необходимо показать этот профиль на изображении детали или выносном элементе и привести все необходимые размеры (см. рисунок 18).
Формы и размеры проточек для выхода резьбообразующего инструмента, фасок для стандартных метрических резьб следует выбирать по ГОСТ
10549 – 80.
Специальные канавки для выхода шлифовального круга выбирают по ГОСТ 8820 – 69. Размеры «под ключ», формы и размеры канавок под сальниковые уплотнения, размеры шпоночных пазов следует также выбирать по соответствующим стандартам.
Размеры отдельных элементов деталей приведены в [6].
Измеренные размеры деталей (диаметры, длины и т. п.) следует округ-
15
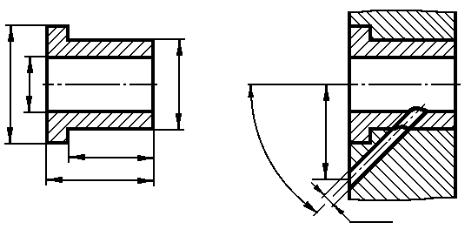
лять до ближайших целых значений, используя по возможности ряд нормальных линейных размеров по ГОСТ 6636 – 69 - Нормальные линейные размеры.
У сопрягаемых конических поверхностей целесообразно задать конусность (или угол конуса), при этом значение конусности, полученное измерением и расчётом, должно быть округлено до ближайшего стандартного значения по ГОСТ 8593 – 81 [6]. Использование нормальных линейных размеров и конусностей уменьшает номенклатуру режущего и измерительного инструмента и удешевляет производство.
При выполнении эскизов пружин, зубчатых колёс необходимо пользоваться стандартами, устанавливающими условные изображения и правила выполнения чертежей этих изделий. ГОСТ 2.401 – 68 – Правила выполнения чертежей пружин, ГОСТ 2.403 – 75 – Правила выполнения чертежей цилиндрических зубчатых колёс и реек.
4.3 Оформление чертежей совместно обрабатываемых деталей по ГОСТ 2.109 – 73
На эскизе (чертеже) детали наносят только те размеры, которые должны быть выполнены и проконтролированы перед сборкой. Например, деталь, которая при сборке изделия должна быть деформирована (расклёпана, обжата, развальцована и т. п.) или приварена к другой детали, изображают на эскизе в том состоянии, которое она имеет до сборки.
Когда в детали обработка отверстий под винты, заклёпки, шпильки, штифты и т. п. должна производиться при сборке её с другими деталями, на чертеже (эскизе) детали отверстия не изображают и никаких указаний в технических требованиях не помещают (см. рисунок 9).
Рисунок 9 |
Рисунок 10 |
Все необходимые данные для обработки таких отверстий (изображения, размеры, координаты расположения, количество отверстий), а также указания о развальцовке, обжатии и т. п. помещают на сборочном чертеже (см. рисунок 10).
Если отдельные элементы детали необходимо до сборки обработать со-
16

вместно с другими деталями то, их временно соединяют и скрепляют (например, вкладыши подшипников скольжения, крышка и корпус редуктора). При этом эскизы (чертежи) деталей оформляют следующим образом (рисунок 11):
-на каждую деталь выпускают отдельный эскиз с указанием на нём всех размеров;
-размеры элементов, обрабатываемых совместно, заключают в квадратные скобки;
-в технических требованиях, располагаемых над основной надписью, помещают указания, приведённые на рисунке 11.
1. Обработку по размеру в квадратных скобках производить совместно с дет. … 2. Детали применять совместно …
Рисунок 11
Если отдельные элементы изделия должны быть плотно пригнаны друг к другу, то на чертеже (эскизе) одной из деталей следует выполнить тонкими линиями упрощённое изображение другой детали, отметить размеры этих элементов буквенным обозначением и в технических требованиях привести соответствующие указания (рисунок 12).
1.Поверхность А обработать по дет. …, выдержать размер Б.
2.Детали применять совместно.
Рисунок 12
17
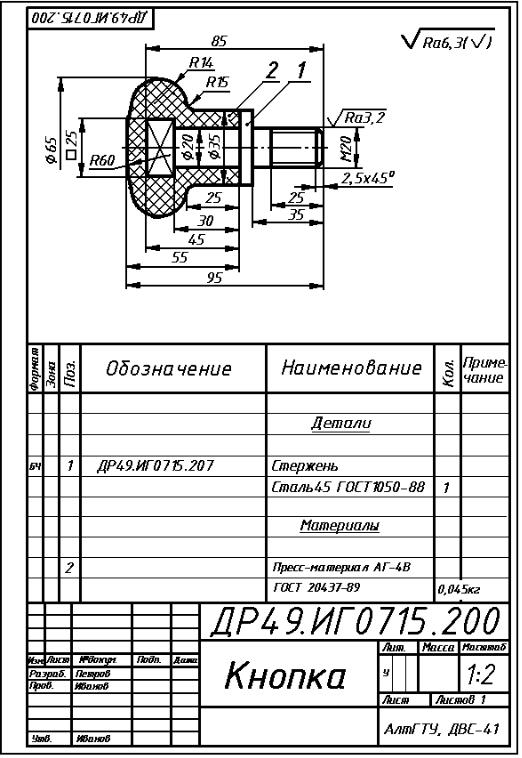
4.4 Выполнение чертежей армированных изделий, изделий с наплавкой и заливкой
В составе ряда сборочных единиц есть изделия, изготовленные наплавкой и заливкой металла или сплава или опрессовкой пластмассой, резиной и др. (например, клапаны вентиля, вкладыши подшипников скольжения, армированные маховички из пластмассы, ручки). Каждая армированная деталь состоит из арматуры и заполнителя.
Рисунок 13
18
Так как армированное изделие является сборочной единицей, то относящаяся к нему конструкторская документация должна состоять из спецификации и сборочного чертежа (ГОСТ 2.109 - 73).
На сборочном чертеже армированного изделия указывают размеры элементов под наплавку (заливку) и размеры окончательно готовой сборочной единицы, указывают сведения о материале в спецификации. Чертежи на составные части (детали) сборочной единицы можно не выпускать. Правила заполнения спецификации приведены в разделе 4.5.
Наименование наплавляемого металла или сплава, пластмассы, резины, которыми заливают армирующие детали, записывают в спецификацию данной сборочной единицы в разделе «Материалы». Допускается совмещение спецификации со сборочным чертежом, при условии их размещения на листе формата А4 (см. приложение 2, рисунок 34).
На рисунке 13 приведен пример совмещения спецификации армированного изделия и сборочного чертежа. Конструкторская документация оформлена так, что для изготовления армирующей детали не требуется специальный чертёж. Стержень (поз. 1) может быть изготовлен по размерам, приведённым на сборочном чертеже из материала, указанного в спецификации.
4.5 Составление спецификации
Согласно ГОСТ 2.102 – 68 основным конструкторским документом для сборочной единицы является спецификация. Спецификация (ГОСТ 2.108 - 68) определяет состав сборочной единицы, комплекса и комплекта и необходима для их изготовления, комплектования конструкторских документов и планирования запуска в производство указанных изделий.
Спецификацию выполняют на отдельных листах формата А4 по формам, указанным на рисунках 14 (форма 1 - заглавный лист) и 15 (форма 1а - последующий лист).
Спецификация в общем случае состоит из разделов, которые располагаются в следующей последовательности: документация, комплексы, сбо-
рочные единицы, детали, стандартные изделия, прочие изделия, материалы, комплекты.
Наименование каждого раздела указывают в виде заголовка в графе «Наименование» и подчёркивают сплошной тонкой линией. Выше и ниже каждого заголовка должна быть оставлена свободная строка.
Враздел «Документация» вносят данные о конструкторских документах, относящихся ко всему изделию в целом, например, сборочный чертёж, монтажный чертёж, технические условия.
Вэтом разделе студенты вписывают «Сборочный чертёж», «Схема деления структурная».
19
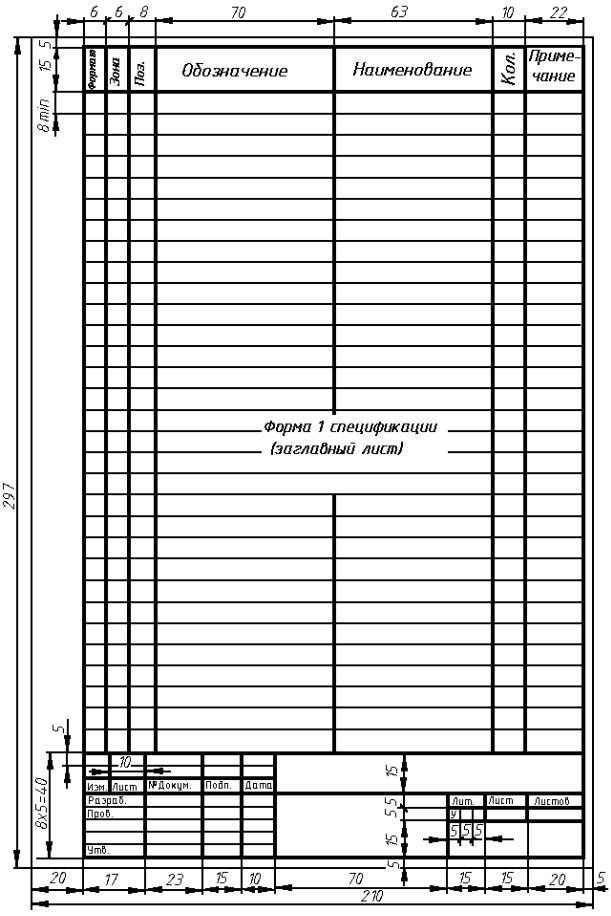
Рисунок 14
20