
Составление сборочного чертежа
.pdf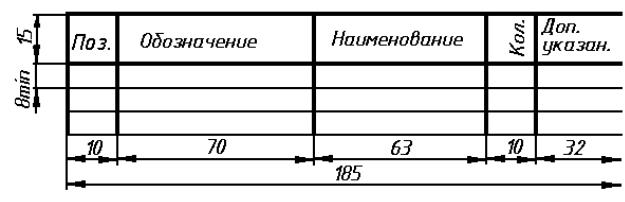
Таблица составных частей изделия состоит из разделов – «Покупные изделия», «Заимствованные изделия»,
«Вновь разрабатываемые изделия» (рисунок 38).
Таблица 3 – Таблица составных частей изделия для чертежа общего вида
Рисунок 20
Чертёж общего вида должен содержать необходимое и достаточное количество изображений (видов, разрезов и сечений) для того, чтобы по нему можно было установить:
1)устройство сборочной единицы и принцип её работы;
2)какие детали и в каком количестве входят в сборочную единицу;
3)форму каждой детали;
4)способы соединения деталей между собой (резьбой, пайкой, запрессовкой и т. д.);
5)обработку, выполняемую в процессе сборки (совместное сверление, обтачивание, пригонка, притирка и т. д.);
6)основные размеры сборочной единицы.
Чертёж общего вида рекомендуется выполнять в следующей последова-
тельности:
1)на листе бумаги определённого формата наносят внутреннюю рамку и в правом нижнем углу – основную надпись (форма 1) в соответствии с ГОСТ 2. 104 – 68 (см. рисунок 38);
2)над основной надписью оставляют место шириной 185 мм для размещения таблицы составных частей изделия и текстовой части в виде технических требований и технической характеристики. Текстовую часть помещают обязательно на первом листе чертежа;
3)на поле чертежа наносят все необходимые изображения: виды, разрезы, сечения, выносные элементы;
4)разрабатывается таблица составных частей, которую размещают над основной надписью или на отдельных листах формата А4, в качестве последующих листов чертежа общего вида;
31
5)на чертеже наносят линии-выноски от каждой детали и сборочной единицы. Над полками линий-выносок наносят номера позиций в соответствии с номерами позиций, указанными в таблице составных частей;
6)цифры, соответствующие номерам позиций, проставляют параллельно основной надписи чертежа вне контура изображения таким образом, чтобы они располагались на одной горизонтальной или вертикальной линии;
7)на чертеже проставляют габаритные, присоединительные, установочные и необходимые конструктивные размеры, причем, размерные линии не должны пересекать линии-выноски;
8)на поле чертежа над таблицей составных частей помещают текстовую часть (в виде технических требований и технической характеристики) в виде колонки шириной 185 мм. Все таблицы на чертеже заполняют
сверху вниз.
На основе чертежа общего вида выполняют сборочный чертёж, входящий в состав рабочей документации. Чертежами общего вида пользуются для разработки технологической документации и составлении чертежей деталей.
Учебные чертежи общего вида и сборочные чертежи отличаются от производственных количеством имеющейся в них информации: отсутствуют размеры (с предельными отклонениями) сопрягаемых поверхностей, требования к шероховатости поверхностей, условия испытаний и другие технические требования.
7 ПРИЛОЖЕНИЕ 1
7.1 Детали затворов арматуры общего назначения
7.1.1 Типы арматуры
Арматурой трубопроводов называются различные устройства, в которых осуществляется изменение площади прохода, а также направление движущейся в трубопроводе среды (жидкости, газа, пара).
В зависимости от характера движения затвора различают следующие основные типы арматуры (рисунок 21):
1)вентили – затвор (золотник, клапан) перемещается вдоль оси корпуса;
2)задвижки – затвор (клин или диск) перемещается перпендикулярно к оси прохода;
3)кран – затвор (пробка) поворачивается вокруг своей оси, скользя по уплотнительной поверхности корпуса, обычно конической (конусность
1:7);
4)поворотные клапаны – затвор (диск) поворачивается вокруг оси, расположенной сбоку от уплотнительной поверхности корпуса.
32

Рисунок 21
В сборочных чертежах арматуры все виды затворов изображают в закрытом положении, за исключением пробковых кранов, которые изображаются в открытом положении.
7.1.2Конструктивные элементы затвора
1.Уплотнительные кольца (рисунок 22). Крепление мягких уплотнительных колец представлено на рисунке 22а, запрессовка металлических колец – на рисунке 22б. Конструкция крепления колец должна предусматривать выполнение зазоров ∆1 и ∆2 .
а б
Рисунок 22
2. Клапаны (см. рисунки 23, 24, 25). Клапан на головке шпинделя или штока должен крепиться с небольшим люфтом. Это способствует центрированию клапана в гнезде корпуса, обеспечивая плотное соприкосновение их рабочих поверхностей при возможном перекосе шпинделя. Крепление клапана на головке шпинделя должно обеспечивать свободный поворот клапана.
По характеру соединения клапана со шпинделем конструкции делятся на разъёмные и неразъёмные. Часто употребляемыми разъёмными соединениями клапана со шпинделем являются:
33
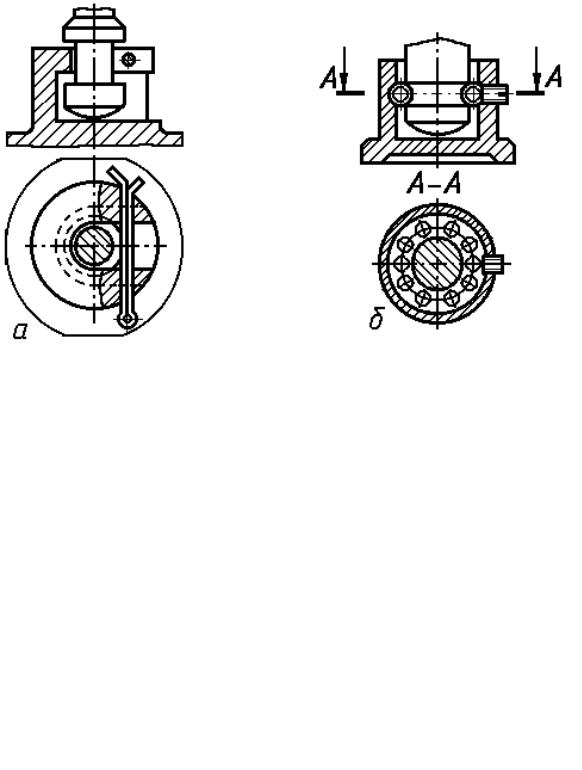
1.Соединение проволочной скобой (рисунок 23а );
2.Соединение закаткой проволоки (рисунок 23б );
3.Соединение закладное (рисунок 24а ).
Рисунок 23
Рисунок 24
34

Рисунок 25
Для вентилей малых проходов (до ø55 мм) крепление клапанов осуществляется обжимкой (рисунок 25), проволочной скобой или кольцом из проволоки (рисунки 23 а, 23б ).
Крепление клапанов для вентилей больших проходов показано на рисунке 24б. Крепление клапана при помощи шариков (рисунок 24б) рекомен-
дуется применять в арматуре, работающей при повышенной температуре (до
3000 С).
3.Сальниковые уплотнения. Со времени изобретения паровой машины
вкачестве уплотняющего материала применяли паклю, пеньку, из которой плели шнуры, а затем их проваривали в растопленном бараньем сале, откуда и пошло название «Сальниковое уплотнение». В настоящее время уплотняющими материалами служат: хлопчатобумажные, пеньковые, асбестовые шнуры, набивка из отдельных колец (асбест, кожа, резина и пр.).
Сальниковые устройства ставят между корпусом и подвижными деталями сборочной единицы, которые служат для предотвращения прохода пара или жидкости через неплотности. Такие устройства применяют в вентилях, пробковых кранах и других механизмах.
Поджатие сальниковых набивок, асбестовых шнуров для теплоизоляции и уплотнения неподвижных деталей может осуществляться накидной гайкой (рисунок 26а) или резьбовой втулкой (рисунок 26б). Накидную гайку или резьбовую втулку изображают на сборочных чертежах в поднятом положении. При этом необходимо обеспечить зазор между стержнем шпинделя и внутренним отверстием накидной гайки ( или втулки сальника)
∆ = 0,5…1 мм.
35
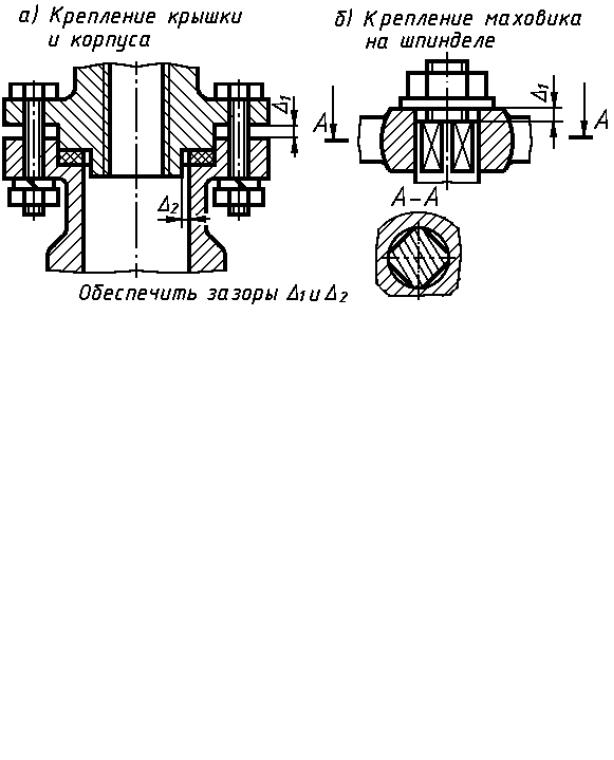
Рисунок 26
4. При креплении крышки и корпуса (см. рисунок 27а), креплении ма-
ховика на шпинделе (см. рисунок 27б) необходимо обеспечить зазоры ∆1и ∆2.
Рисунок 27
36
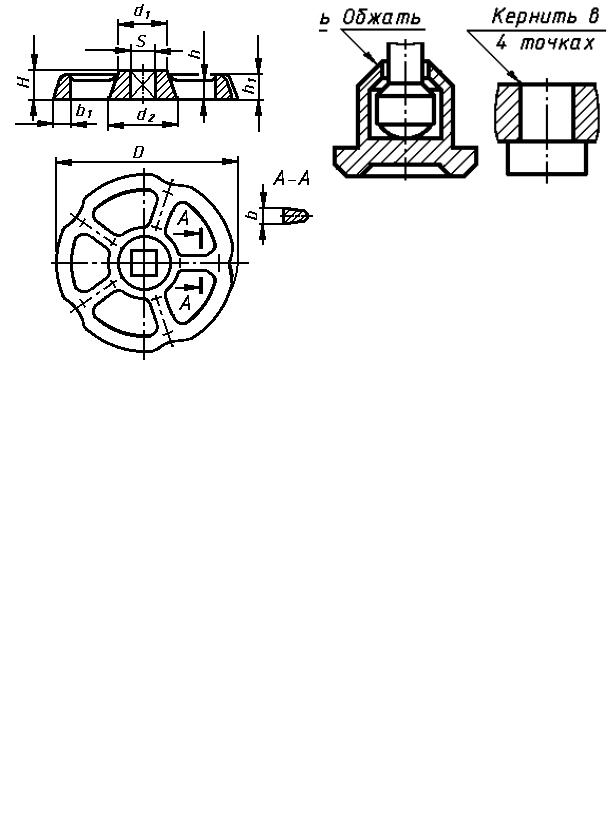
5. Неразъёмные соединения. Некоторые сборочные операции (обжатие, развальцовка, клепка и т. п.) на сборочных чертежах указывают краткой записью (см. рисунок 28).
Рисунок 28
7.1.3 Маховики
Маховики состоят из обода, ступицы и спиц. За главный вид выбирается тот, который не проецируется в окружность. На главном виде маховика выполняется полный разрез, который обычно не обозначается, независимо от того, симметрично или нет расположены спицы. Размер отверстия квадратного сечения в ступице маховика выбирается по размеру «под ключ» для гаек и головок болтов.
Стандартные конструкции маховиков установлены по ГОСТ 5260-75. Маховики изготовляются следующих типов:
1. тип 1- плоский маховик с волнистым ободом;
2. тип 2 – плоский маховик с круглым ободом;
3. тип 3 – вогнутый маховик с волнистым ободом.
Основные параметры и размеры маховиков типа 1 должны соответствовать указанным на рисунке 29 и в таблице 4 .
Рисунок 29
37
Маховики должны изготовляться:
типов 1 и 2 – из серого чугуна марки не ниже СЧ 15 по ГОСТ 1412 – 85 или ковкого чугуна марки не ниже КЧ 30 по ГОСТ 1215 – 85;
типа 3 – из серого чугуна марки не ниже СЧ 18 по ГОСТ 1412 – 85 или ковкого чугуна марки не ниже КЧ 30 по ГОСТ 1215 – 85.
Таблица 4 – Основные размеры маховиков типа 1, мм
Диа- |
|
|
Ступица |
|
|
Спица |
|
|||
метр |
|
|
|
|
|
|
|
|
Ширина |
|
h1 |
|
|
|
|
|
|
Количест- |
|||
махови- |
H |
S |
d1 |
d2 |
h |
b |
обода |
|||
ка |
|
во, |
b1 |
|||||||
D |
|
|
|
|
|
|
|
шт. |
|
|
|
|
|
|
|
|
|
|
|
||
50 |
10 |
10 |
6;7 |
14 |
18 |
6 |
5 |
|
5 |
|
65 |
16 |
20 |
7 |
6 |
|
|||||
|
|
|
|
|
||||||
80 |
12 |
12 |
7;9 |
18 |
22 |
10 |
5 |
6 |
||
|
||||||||||
100 |
14 |
14 |
7;9;11 |
22 |
26 |
11 |
7 |
7 |
||
|
||||||||||
120 |
16 |
16 |
9;11;14 |
26 |
30 |
12 |
8 |
|
8 |
|
140 |
18 |
18 |
11;14 |
32 |
36 |
13 |
9 |
|
9 |
Пример условного обозначения маховика типа 1, размерами D = 100 мм и S = 9 мм:
Маховик 1 – 100 х 9 ГОСТ 5260 – 75.
8 ПРИЛОЖЕНИЕ 2
8.1 Пример составления чертежа общего вида, сборочного чертежа и спецификации
Приступая к выполнению чертежа общего вида, сборочного чертежа изделия или его части (сборочной единицы), необходимо ознакомиться с назначением, устройством и взаимодействием отдельных частей этого изделия. На рисунке 30 показан вентиль запорный, на который требуется выполнить чертёж общего вида, сборочный чертёж и составить спецификацию.
8.1.1 Описание работы вентиля
Вентиль запорный монтируется на трубопроводе, по которому движется жидкость или газ (пар). С помощью вентиля можно периодически отключать одну часть трубопровода от другой.
Чтобы отключить часть трубопровода, нужно опустить запорный клапан 7 до соприкосновения торцевой рабочей поверхности клапана с торцом корпуса 1.
Рабочая поверхность клапана представляет собой кольцо 8 из теплостойкого и вязкого материала, например, никеля, запрессованного в клапан.
Перемещение клапана в вертикальном направлении производится вра-
38
щением маховика 11, насаженного на квадратный конец шпинделя 3; шайба 12 и гайка 13 крепят маховик на шпинделе. Крышка 2 соединена с корпусом 1 четырьмя шпильками 10 с гайками 14. Между крышкой и корпусом поставлена кольцевая уплотняющая прокладка 15 из паронита.
В вентиле применено сальниковое устройство. Оно состоит из втулки 6, сальника 9 (мягкой набивки из асбестового просаленного шнура), кольца сальника 5 и гайки накидной 4. При затягивании накидной гайки 4 втулка 6 опускается и сжимает набивку. Конические поверхности втулки 6 и кольца 5, между которыми находится набивка, при сжатии плотно прижимают последнюю к поверхности шпинделя, обеспечивая герметичность соединения. Такую же коническую поверхность имеет и кольцо сальника 5.
8.1.2 Схема сборки вентиля (схема деления структурная)
На рисунке 32 приведена развернутая схема сборки изделия, где сборочные единицы, непосредственно входящие в окончательную сборку изделия, состоят из сборочных единиц первого порядка, в которые в свою очередь входят сборочные единицы второго порядка, состоящие из деталей – первичных элементов собираемого изделия.
Из схемы видно, что в окончательную сборку изделия, кроме сборочных единиц и сборочных единиц разных порядков, входят частично и отдельные детали.
8.1.3 Особенности сборки вентиля
Базовая деталь в этом изделии (вентиля запорного) – корпус вентиля. С этой детали и начинается сборка. Сначала в корпус 1 вентиля ввинчивают четыре шпильки 2, поэтому корпус вентиля вместе со шпильками рассматривается как сборочная единица. Вычерчивается отдельно сборочная единица 100 корпуса в сборе (см. рисунок 33). Затем к корпусу 1 присоединяется прокладка 15, поступающая самостоятельной деталью на сборку.
Далее следует крышка в сборе – сборочная единица первого порядка 300, так как в её состав входит сборочная единица второго порядка (клапан в сборе 200). В сборочную единицу первого порядка (крышка в сборе 300, базовая деталь – крышка 1) входит непосредственно шпиндель 3, кольцо сальника 5, сальник 9, втулка 6, гайка накидная 4 и сборочная единица второго порядка в сборе 200, состоящая из базовой детали – клапана 7 и кольца 8. Сборочная единица первого порядка (крышка в сборе 300) крепится к корпусу четырьмя гайками 14 и пружинными шайбами 16, затем следует маховик 11, шайба 12 и гайка 13. Эти детали поступают на сборку самостоятельно.
Сборочная единица вентиля запорного собрана и может быть вмонтирована в паровую установку.
39
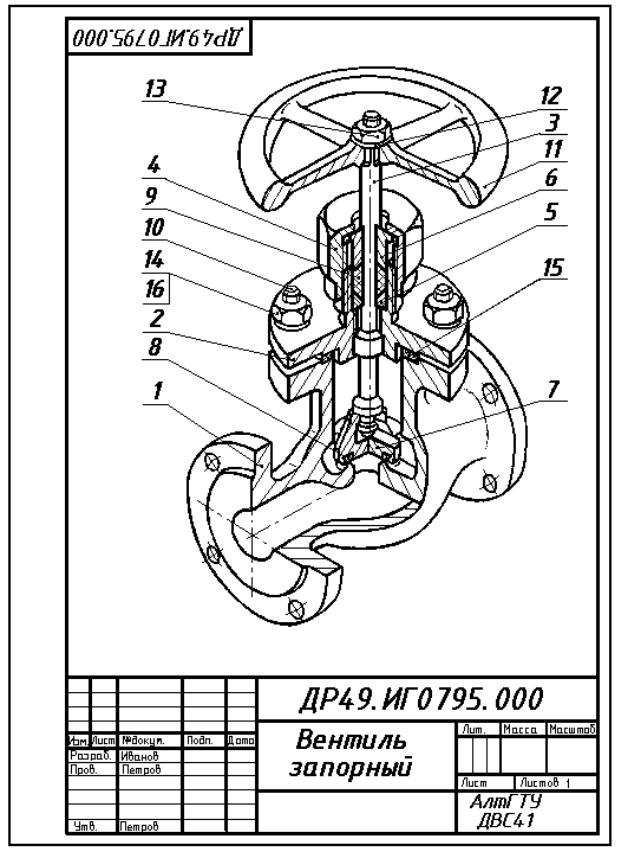
Рисунок 30
40