
MetodVorobev1
.pdf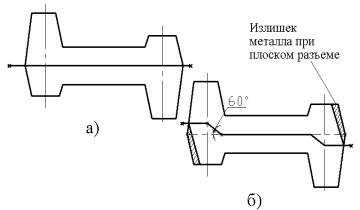
−определить форму и размеры наметок отверстий и перемычек под прошивку;
−рассчитать размеры исходной заготовки;
−назначить температурный интервал горячей объемной штамповки;
−определить вес падающих частей (для штамповки на молотах);
−оформить чертеж поковки.
2.ОБЩИЕ СВЕДЕНИЯ ПО МЕТОДИКЕ КОНСТРУИРОВАНИЯ ПОКОВКИ И РАЗРАБОТКЕ ТЕХНОЛОГИЧЕСКОГО ПРОЦЕССА ПРИМЕНИТЕЛЬНО К ШТАМПОВКЕ НА МОЛОТАХ
2.1. ВЫБОР ИСХОДНЫХ МАТЕРИАЛОВ
При изготовлении стальных поковок выбор марки стали производить с учетом назначения детали и пластичности по таблице П12. Материалы для горячей объемной штамповки должны иметь достаточно высокую пластичность, т.е. способность деформироваться без разрушения. При затруднении, в назначении материала по основному технологическому свойству (пластичности) необходимо учитывать дополнительное свойство - обрабатываемость резанием; материал должен быть как можно более дешевым.
Пользуясь справочной литературой [10]; [11], [12], подобрать марку материала и оценить его стоимость по биржевым ценам [13] или по ценам предприятия-поставщика (для студентов-заочников).
2.2. ОПРЕДЕЛЕНИЕ ПЛОСКОСТИ РАЗЪЁМА ШТАМПА
Расположение и форма разъёма штампа должны удовлетворять требованию свободного извлечения поковки из штампа.
Разъём рекомендуется делать плоским (рис 2.1,а), однако если это ведёт к увеличению объёма металла, то целесообразно линию разъёма делать ломаной (рис 2.1,6) в местах выступов, причём наклон её к горизонтальной плоскости не должен превышать 60 градусов для получения чистого среза облоя.
Рис 2.1. Плоскость разъема: а) - плоская, б) - ломаная
21
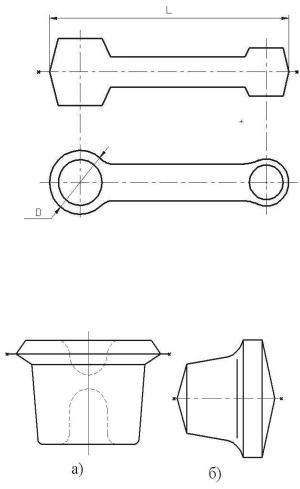
Плоскость разъёма должна быть расположена так, чтобы полости штампа имели минимальную глубину и максимальную ширину сечения. Обычно разъём делают в плоскости максимальных взаимно перпендикулярных размеров поковки (D и L) (рис. 2.2.), однако от этого правила следует отступать, если при ином разъёме достигается значительное снижение массы поковки за счёт штампованной полости (рис. 2.3,а).
Расположение линии разъёма, удовлетворяющее вышеперечисленным требованиям, обеспечивает возможность контроля за смещением половин штампа, проектирование поковки для полного изготовления в одной половине штампа полностью исключает возможность смещения и снижает стоимость штампа.
Окончательное решение по назначению линии разъёма принимают после назначения припусков и штамповочных уклонов.
Рис.2.2. К определению плоскости разъема штампа.
Рис. 2.3. Линия разъема штампа: а) - рекомендуемая; б) – не рекомендуемая
2.3. ОПРЕДЕЛЕНИЕ КОНСТРУКТИВНЫХ ХАРАКТЕРИСТИК
Класс точности поковки устанавливается в зависимости от вида оборудования и технологии изготовления, а также от требований к точности размеров.
По ГОСТ 7505-89 [14] поковки разделены на пять классов точности.
22
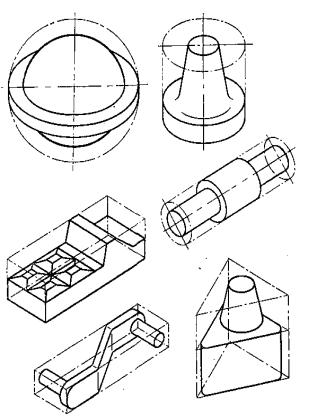
Наивысшие требования предъявляются к поковкам первого класса точности, которые изготовляются прецизионной штамповкой и объёмной калибровкой.
Штамповка на молотах обеспечивает 4-5-й класс точности поковок, которые используются в качестве заготовок для последующей механической обработки.
Группа стали (M1, М2, МЗ) определяется для M1 по содержанию углерода и суммарной массовой доле легирующих элементов. Для групп М2, МЗ - или по содержанию углерода, или по суммарной массовой доле легирующих элементов (состав сталей см. в табл. П13).
Степень сложности поковки определяют, находя отношение объёма Vn поковки к объёму Vф геометрического тела, в которое вписывается поковка. Геометрическое тело может быть шаром, параллелепипедом, цилиндром с перпендикулярными к его оси торцами или прямой правильной призмой.
Справочные данные для определения конструктивных характеристик поковок приведены в табл. П.17. Взаимосвязи конструктивных характеристик нет.
Рис.2.4. Поковки, вписанные в геометрические тела.
2.4. РАСЧЁТ ОРИЕНТИРОВОЧНОЙ МАССЫ ПОКОВКИ
Для определения расчётной массы поковки Мп.р. необходимо разбить деталь на тела простой геометрической формы, рассчитать ее объём. Плотность стали принять 7,8 г/см3, бронзы - 8,8 г/см3.
23

Пользуясь табл. 4 и формулой
Мп.р.=Мд*Кр,
где Мд - масса детали, кг; Кр - расходный коэффициент, находим массу поковки.
2.5. ОПРЕДЕЛЕНИЕ ИСХОДНОГО ИНДЕКСА
Исходный индекс используется при назначении припусков, допусков и допускаемых отклонений. Его определяют по табл. П.19. В зависимости от массы поковки, группы стали, степени сложности и класса точности поковки.
На рис. 2.5 показана последовательность нахождения исходных индексов. Поковка массой 0,5 кг, с группой стали МЗ, степенью сложности С2 и классом точности Т1 имеет исходный индекс 4, а с группой стали Ml, степенью сложности С1 и классом точности Т2 - исходный индекс 3.
Для определения исходного индекса по табл. П19 находят строку, соответствующую расчётной массе поковки, и, смещаясь вправо до пересечения наклонной с вертикальными линиями, задающими группу стали, степень сложности и класс точности, устанавливают исходный индекс.
Если же заданы M1, C1, T1, то смещаться по утолщённым наклонным линиям не надо.
Масса поковки, |
Группа стали |
|
Степень сложности |
|
Класс точности |
|
Исходный |
|||||
кг |
|
|
|
|
|
|
|
|
|
|
|
индекс |
|
М1 |
М2 |
М3 |
С1 |
С2 |
С3 |
С4 |
Т1 |
Т2 |
Т3 |
Т4 |
Т5 |
До 0,5 включ. |
|
|
|
|
|
|
|
|
|
|
|
1 |
Св. 0,5-1,0 |
|
|
|
|
|
|
|
|
|
|
|
2 |
Св. 1,0-1,8 |
|
|
|
|
|
|
|
|
|
|
|
3 |
Св. 1,8-3,2 |
|
|
|
|
|
|
|
|
|
|
|
4 |
Св. 3,2-5,0 |
|
|
|
|
|
|
|
|
|
|
|
|
|
|
|
|
Рис.2. 5 Пример определения исходного индекса. |
|
|
|
|
2.6. ПРИПУСКИ НА МЕХАНИЧЕСКУЮ ОБРАБОТКУ
Припуски на механическую обработку назначаются в том случае, если шероховатость поверхности и точность размеров поковки не удовлетворяют требованиям, предъявляемым к готовой детали. Размер припуска зависит от вида механической обработки и определяется глубиной дефектного слоя
поковки. |
|
|
|
|
|
|
Припуск |
на |
механическую |
обработку |
включает |
в |
себя |
основной и дополнительные припуски, которые учитывают отклонения формы поковки. Величины припусков назначаются на одну сторону номинального размера поковки.
Основные припуски в зависимости от исходного индекса и шероховатости поверхности назначаются по табл. П.20.
Дополнительные припуски учитывают смещение поковки, изогнутость, отклонения от плоскостности и прямолинейности, межцентрового и межосевого расстояний, угловых размеров. Их назначают, исходя из формы поковки и технологии её изготовления, и устанавливают в зависимости от класса точности Т по ГОСТ 7505-89 [15].
24
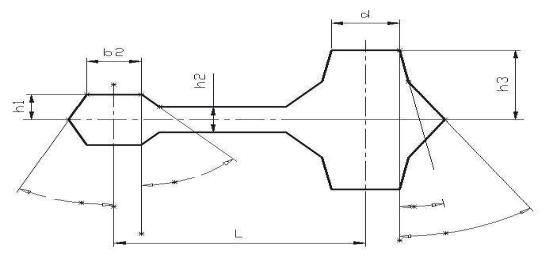
Линейные размеры поковки разрешается округлять до 0,5 мм.
При назначении величины припуска на поверхность, положение которой задано несколькими размерами поковки, устанавливается наибольшее значение припуска.
Значения дополнительных припусков см. [14, табл. 4-6].
2.7. ШТАМПОВОЧНЫЕ НАПУСКИ, УКЛОНЫ, ДОПУСКИ.
Напуски. В случае если отдельные части поковки проштамповать невозможно, делаются напуски сверх требуемого припуска на механическую обработку, что упрощает конфигурации поковки.
Уклоны. Для облегчения удаления готовых поковок из полостей штампа делаются штамповочные уклоны боковых поверхностей поковки. Порядок назначения уклонов регламентирован ГОСТ 7505-89 [14],.
В целях унификации режущего и мерительного инструментов, и упрощения изготовления ручьёв штампа обычно делают уклоны в 3,5,7,10,12 градусов, причём для наружных боковых поверхностей принят номинальный уклон в 7 градусов, для внутренних 10 градусов.
Данные о штамповочных уклонах для поковок из стали и медных сплавов в зависимости от соотношения их размеров (рис. 2.6) приведены в сопутствующей табл. П.21.
β
α |
α |
γ
Рис2..6 . Штамповочные уклоны (град) для стальных поковок.
Допуски – это величина допустимого отклонения от номинальных размеров поковки, проставляемых на чертеже, ввиду невозможности получения абсолютно точных размеров. На величину допуска влияют многие причины, например, точность изготовления и конструктивные особенности штампа, степень его износа, температура конца штамповки и др. Допуски назначаются по табл. П.22.
2.8. РАДИУСЫ ЗАКРУГЛЕНИЙ И ПЕРЕХОДОВ
Для предотвращения поломки (появления трещин) и улучшения заполнения полости штампа у поковки выполняются внешние радиусы
25
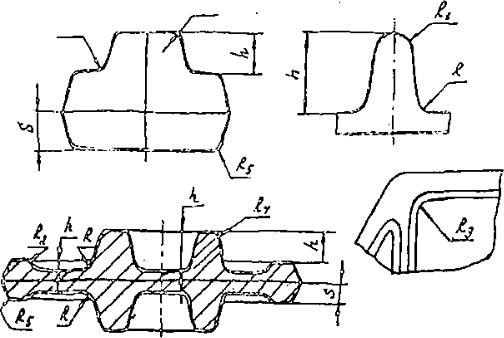
закруглений r. Для предотвращения сминания и появления заусенцев, складок, что ведёт к затруднению извлечения поковки из ручья, назначаются внутренние радиусы R. Малые величины радиусов могут привести к неправильному течению металла, рассеканию волокон, поэтому к их назначению предъявляются строгие требования в зависимости от глубины полости ручья штампа. Минимальная величина радиусов закруглений наружных углов поковок выбирается из табл. П.23.
Внутренние радиусы (R) заготовки можно определить по формуле:
R= 2,5r+0,5 ,мм
При назначении радиусов закруглений следует также иметь в виду, что если радиусы меньше, чем величина припуска, их следует увеличивать до размера припуска. Если же припуск меньше радиуса r, то его также увеличивают до величины радиуса.
Для высоколегированных марок стали, цветных металлов и сплавов следует увеличивать r и R на 20-30%.
Допуски радиусов закруглений для классов точности Т4, Т5, см. в табл.
П.24.
Радиусы для поковок из цветных сплавов представлены на рис. 2.7. и в таблице П.25.
2.9. РАЗМЕРЫ ЗАУСЕНЕЧНОЙ КАНАВКИ
Штамповка бывает двух разновидностей: закрытой и открытой (рис.2.8.) Применение закрытых штампов (рис.2.8.а) обеспечивает оптимальный расход металла на поковки, но предъявляет высокие требования к точности объёма заготовок перед штамповкой. При штамповке в открытом штампе (рис.2.8,б) излишек металла вытекает через узкую щель, устроенную по всему периметру ручья в плоскости разъёма, называемую заусенечной канавкой.
Рис.2.7. Радиусы сопряжений R, переходов R3, закруглений R1, R2, R4, R5, и толщина ребер 2R1, мм, для поковок из цветных сплавов.
26
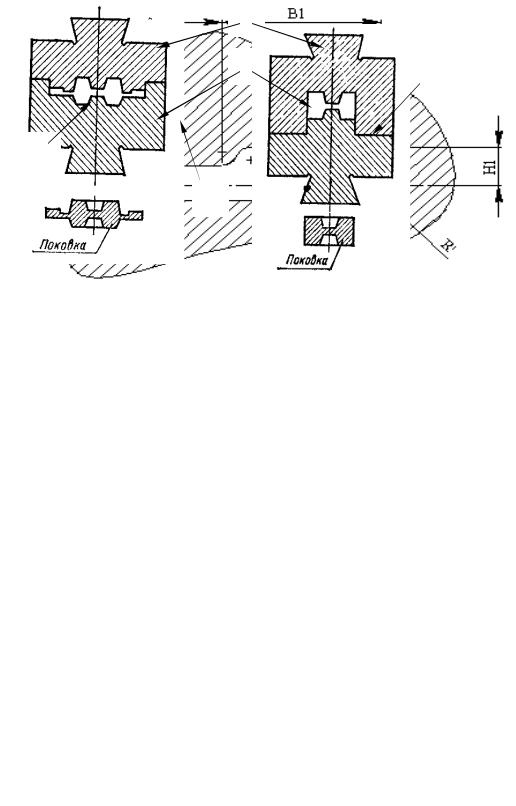
1
2
3
3
4
а) |
б) |
Рис.2.8. Молотовые штампы: а - закрытый; б - открытый; 1 - хвостовик типа «ласточкин хвост» для крепления штампа; 2 - ручей; 3 - замок; 4 - заусенечная канавка
Поковка при этом получается с облоем но наружному контуру, который удаляется затем а обрезком штампе. Наличие заусенечной канавки позволяет снизить точность изготовления заготовки, гарантируя при этом заполнение ручья, т.к. вытекание излишков металла в узкую облойную канавку затруднено, что создаёт повышенное давление на металл в полости ручья.
Профиль заусенечной канавки представлен на рис. 2.9.
Рис.2.9. Заусенечная канавка.
Величина H3 определяется по формулам:
H3 = 0,015 D;
H3 = 0,015 ÖF.
где D -.диаметр поковки в плоскости разъема, мм; F - площадь поковки в плоскости разъема, мм2.
27

Данные о соотношении размеров в зависимости от толщины мостика заусенца H3 приведены в табл. П.26.
2.10 ПОЛОСТИ И НАМЕТКА ОТВЕРСТИЙ В ПОКОВКАХ
Для экономии металла и снижения трудоемкости механической обработки деталей, имеющих центровое отверстие, у поковок делается наметка отверстий, которые затем прошиваются в специальном штампе на обрезном прессе.
Условия выполнения и размеры прошиваемых отверстий и углублений в стальных поковках оговорены в ГОСТ 7505-89 [14].
Впадины и углубления в поковке, когда их оси параллельны направлению движения одной из подвижных частей штампа, а диаметр или наименьший поперечный размер не менее 30 мм, выполняют глубиной до 0,8 их диаметра или наименьшего поперечного размера.
Выполнение сквозных отверстий при двустороннем углублении обязательно, если диаметр их больше или равен высоте поковки.
Вследствие малой стойкости кузнечных знаков и прошивных пуансонов, оформляющих наметки отверстий, полости диаметром менее 30 мм не выполняются.
На рис. 2.10 представлены наметки различных видов для стальных поковок.
Для глухой наметки (рис.2.10,а) при D/H<0,6 без последующей пробивки: hmax <0,8D, mm,
R1 = |
D − (2hmaxtgβ ) |
||||||
|
|
|
|
|
, мм |
||
2tg( |
π |
− |
β |
) |
|||
|
|
||||||
|
4 |
|
|||||
|
|
2 |
|
|
Сквозные отверстия получают последующей пробивкой перемычек, предварительно оформляемых в штампах. Излишне толстая перемычка затрудняет пробивку отверстия, а слишком тонкая снижает стойкость кузнечных знаков.
Толщина плоской (обычной) перемычки (рис.2.10,б) определяется в зависимости от диаметра прошиваемого отверстия D и глубины прошивки h (при D/H=1,0 и D/H=l,1...2,5) по эмпирической формуле
S = 0,45D − 0,25h − 5 + 0,6
h , мм
при этом R1 = R + 0,1h +2, мм,
где R - внутренний радиус закруглений для данной поковки, мм.
Если глубина прошивки меньше диаметра прошиваемой полости в 2,5 раза и более, т.е. при D/H = 2,5... 15, для облегчения раздачи металла применяется наметка с раскосом (рис.10, в), в этом случае:
Smin = 0,65 S, мм;
Smax= 1,35 S, мм; d1≤0,12D + 3, мм;
R1 = R + 0,lh + 2, мм;
S = 0,45D − 0,25h − 5 + 0,6
h , мм
Для низких поковок при D/H>15 рекомендуется наметка с карманом
28

(рис.10, г), в этом случае:
S=0,4ÖD, мм; S1 = 5S, мм;
S=0,45Ö(D-0,25h-5)+ 0,6Ö h, мм R1= R+0,1h+2,мм
R2=5h, мм; R3 – находят графически, мм
На рис. 2.11. представлены наметки отверстий для поковок из цветных металлов и сплавов и соответствующие формулы для расчета конструктивных элементов. Данные к рис. 2.11,г сведены в табл. П.27. и П.28.
Рис. 2.10. Перемычки в наметках отверстий и углубления: а) плоская, б) с раскосом, в) с магазином, г) сдвоенная поковка,
д) и е) детали, ж) перемычка с карманом, з) глухая наметка (углубление)
Рис. 2.11.
29

2.11 РАСЧЕТ РАЗМЕРОВ ИСХОДНОЙ ЗАГОТОВКИ.
Объем заготовки (Vзаг) для открытой штамповки на молоте рассчитывается по формуле
Vзаг = Кy(Vп+Vз+Vпер),
где Кy - коэффициент угара металла; при нагреве в пламенных печах Кy=1,02; при электронагреве Кy=1,005..1,01;
Vп – объем поковки с учетом уклонов и припусков; Vз – объем заусенца;
Vпер – объем перемычки.
Vз=КSзPп,
где К=0,5..0,8 - коэффициент заполнения канавки, зависящий от сложности формы поковки;
Sз - площадь поперечного сечения заусенечной канавки; Pп - периметр поковок по линии среза заусенца.
По расчётному объёму исходной заготовки Vз.и определяется её диаметр:
Dç .è. = 1,083 Vç .è. ;
m
где m= Lз.и/ Dз.и рекомендуется принимать равной 2.5.
Расчётный диаметр Dз.и. округляется до ближайшего большего в соответствии с сортаментом, ГОСТы на который приведены а табл. П.29.
По ГОСТ 2590-88 [ ] предусматривается следующий сортамент круглой горячекатаной стали (диаметр, мм ): 5; 5, 6; б, 3; 6, 5; 7; 8; 9: 10; 11; 12; 13; 14;
15; 16; 17; 18; 19; 20; 21; 22; 24; 25; 26; 28; 29; 30; 32; 34; 38; 40; 42; 45; 48; 50; 53; 56; 60; 63;65; 70; 80; 85; 90; 95; 100: 105; 110; 120; 125; 130; 140; 150; 160;
170; 180; 190; 200; 210; 220 240; 250.
После выбора (Dз.и) исходной заготовки по ГОСТу рассчитывается длина
заготовки (Lз.и) |
|
4Vз.и. |
||
Lз.и. |
= |
|||
πD2 |
з.и. |
|||
|
|
2.12 НАЗНАЧЕНИЕ ТЕМПЕРАТУРНОГО ИНТЕРВАЛА ГОРЯЧЕЙ ОБЪЕМНОЙ ШТАМПОВКИ
Температурный интервал штамповки может быть назначен по диаграмме состояния железо-углерод по эмпирической формуле
Тш=(0,7...0,9 Тпл) или на основании технологических экспериментальных исследований.
При выполнении курсовой работы следует пользоваться справочными данными [15], [16],часть из которых приведена в таблице П.30.
30