
Курс Лекций по Бабушкину
.pdf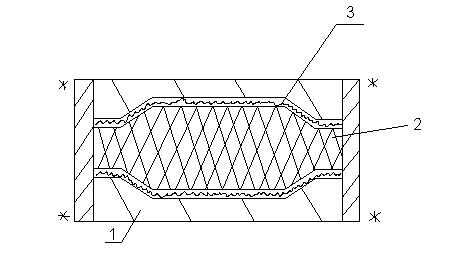
1.разборная форма
2.рабочий эластичный формующий элемент
3.формуемое изделие
Термокомпрессионный метод формования называют также формованием эластичных элементов или формованием с термическим расширением рабочего тела. Основные элементы оснастки: жесткая форма, эластичный элемент. Свое название метод получил благодаря тому, что в качестве рабочего тела используется силиконовый каучук и другие при нагревании. Вследствие температуры приблеженой к деформации и создается давление формования. Применяемые при этом способе формования силиконовые каучуки имеют коэффициент:
При этом способе пакет препрега вместе с эластичным элементом в жесткую оформляющую форму. при повышенных температурах рабочее тело расширяется в большой степени чем ограничивающая его оснастка, что и дает давление формования.
Преимущество:
1.простота аппаратурного обеспечения
2.возможность изготовления изделий сложной формы
Прессование.
Заключается в пластической деформации металла при одновременном воздействии тепла и давления с последующей фиксацией изделия. Проводится в пресс-формах, давление обеспечивается прессами.
Помещается в пресс-форму холодный или разогретый материал, разогревается до нужной температуры в нагреваемых пресс-формах.
Пултрузия.
Процесс, в котором волокна и пластичный материал матрицы одновременно истекают из фильеры, при чем волокна вытягиваются, а пластичный материал матрицы одновременно выдавливается. Этот процесс может быть непрерывным, а поперечное сечение меняется от применения фильеры.
Обычно установка состоит из нескольких модулей, позволяющей объединить следующие стадии этого процесса:
1.пропитка связующим пучка волокон
2.отжим избыточного связующего
3.придание материалу заданного сечения путем протягивания через фильеру
4.отверждение
5.разрезка на элементы заданной длины
Нагрев обычно индукционный, фильер может быть несколько. Для пултрузии используют расплавы смол не содержащих растворителя. Этот процесс прост и полностью автоматизирован.
Недостатки:
1.Скорость процесса ограничена, связано с скоростью отверждения.
2.Трудность обеспечения строго постоянного сечения за исключением простейших форм.
3.В качестве полимерных матриц используют поливиниловые акрилы и эпоксидные смолы.
4.В качестве связующих применяют полисульфоны, полиэфирсульфоны, полиамиды, так как эти связующие обладают высокой термостойкостью.
Наиболее совершенным и перспективным является применением связующим со скрытыми отвердителями полимеризующишися при ультрофиолетовом излучении за доли секунды.
Ролтрузия.
Способ формирования изделия из ПКМ ролтрузией заключается в пропускании препрега между гладкими или фасонными волокнами. При этом способе отверждение и придание необходимой конфигурации в 1 стадию.
Преимущества:
-малая стоимость образцов.
-возможность изготовления крупногабаритных конструкций.
-простота перестройки на произвольной конфигурации.
-высокая производительность (1 м/мин ).
При ролтрузии применяются связующие с низкой вязкостью и скоростью отверждения 1.5 мин. Это эпоксидные смолы отверждаются гетероцикличными аминами.

1.формуемое изделие
2.нижняя форма
3.зажим
4.смотровое окно
5.верхняя форма
6.патрубок впрыска связующего под давлением
7.патрубок подачи связующего из резервуара (а) метод впрыска (б) вакуумный метод
Изделие получают предварительно, помещая в форму армирующий материал
ивпрыскивая затем связующее. Либо методом впрыска (а), либо созданием в рабочей форме вакуума, в этом случае связующем самотеком поступает из резервуара.
Отсюда 2 разновидности: инжекционный – впрыском, инжекционный - вакуумом. Наилучшее результаты когда эти методы совмещены.
Преимущества:
1.сравнительно низкая стоимость пресс-формы и инжекционных устройств.
2.возможность автоматизации пресса
3.экологическая чистота процесса
4.возможность получать крупногабаритные изделия (кузова, корпуса)
Литье под давлением.
Литьевое формование используют для изготовления деталей сложной конфигурации в этой технологии используется исключительно рубленое молоко, как правило предварительно пропитанное связующем пресс-материал. Они занимают среднее место по прочности между изделиями из порошков и изделия с армирующими волокнами. Микронеоднородность структуры вызывает неоднородность свойств(20-30%). В качестве матрицы применяются термопласты. Этот метод используют для получения небольших по размеру, но
сложных форм, в которых невысокая степень армирования и произвольная ориентация волокон не препятствует получению требуемых механических характеристик.
1.Выбор пресс - материала зависит от назначения изделия.
2.Степень наполнения отражается на величине усадки и физических характеристик.
3.С дисперсными наполнителями не желательно, так как ведет к низким свойствам.
Центробежное формование (литье).
Сущность метода состоит в том, что полимеры, находятся в вязко-текучем состоянии, подвергаются действию центробежных сил. Под воздействием которых заполняет форму; приобретая конфигурацию и размеры готового изделия.
Этот метод позволяет получать изделия, не содержит пузырьков воздуха и не имеющих пор. В поле центробежных сил, в зависимости от вязкости происходит перераспределение и его миграция к поверхности формы, в результате чего повышается жесткость.
Наличие поля центробежных сил позволяет в наиболее мягких условиях распределять наполнитель по - которому не травмируя его. Это важно для углеродных и борных волокон.
Формование с помощью вспененного слоя ( с отжимом связующего ) Процесс проводят следующем образом .
1.С двух сторон пористого полимера (пенопласта) пропитывают полимером, укладывания материала в виде ткани, лент.
2.Пакет помещают в пресс-форму и одновременно с формованием выжимают связующие из пенопласта, который и пропитывает армирующий материал, повышая температуру, отверждают пакет и получают изделия, содержащие в центре слои пенопласта.
Этот процесс характерен простой технологией, позволяет получать легкие трехслойные конструкции. Позволяют получать легкие прочные изделия.
Вспомогательные материалы при формовании ПКМ.
Вспомогательные материалы при формовании ПКМ можно разделить на следующие группы:
1.пленки для создания вакуумных мешков или эластичных диафрагм;
2.герметизирующие материалы из которых изготавливаются жгуты, ленты с двусторонним нанесением липкого слоя для создания контакта пленки вакуумного мешка и поверхностью формы;
3.различные пористые материалы, служащие для создания равномерного давления при вакуумировании мешка обеспечении благоприятной работы;
4.разделительные пленки и смазочный материал, обладающие противоадгезионными свойствами;
5.материалы, применяемые для оформления поверхности в процессе полимеризации сборочного узла (декоративные);
6.материалы для дренажных систем.
Для вакуумных мешков используется специальная резина рабочей температуры до140 С, ткань, пропитанная смолами для температуры до 180 С, полиамидная пленка для рабочей температуры до 200 С – выполняется на основе синтетических материалов. Для предотвращения искажения элемента в пленки вводят амн. добавки или подвергают поверхность специальной обработке, например коронным разрядом. Термостойкость пленки из нейлона 6-6 до -204 С, из полиамида 6 рабочая температура 200-230 С.
Для герметизации стыков пленок вакуумного мешка при вакуумировании, пресскамерном формовании применяют пленки с двусторонней липкой основой устойчиво работающие при температуре до 170 С, в течении 80 часового цикла.
Вкачестве формующего материала, создающие равномерное давление в формуемых изделиях, в зонах переходов применяется не отверждаемый синтетический каучук близкий по теплостойкости к силиконовому каучуку. Для уплотнения в углах изделий применяют специальную композицию, вспенивающуюся при температуре автоклавного отверждения.
Вкачестве разделительной ткани можно применять ткань на лавсановой основе. Для разделения элементов наносят тонкий слой адгезионного вещества например смесь органического воска и поливинилового спирта, может применен в ряде случаях только воск. Перед нанесением противоадгезионного смазывающего слоя поверхность обезжиривают. В производстве для изготовления дренажных систем применяют стеклоткани пропитанные смазочным материалом.
Для оформления наружных поверхностей применяют цулоги, изготовляемые из алюминиевых t = 0.5-1.5мм или текстолитовых листов . t = 0.8-2.5мм
Ограничительные рамки, используемые при сборке пакетов, при формовании изготавливают из стеклопластиков и металла.
Конфигурация и высота рамки выбирается в соответствии с формой и размерами изделия. Для вакуумирования при сборке технологических пакетов используют вакуумные трубки, изготовленные из мягких металлов. Вакуумная трубка перфорируется по всей длине с шагом 10-12 мм, отверстием диаметром 1-4 мм. Термопары для контроля и регулирования режима термостатирования в количестве не менее 2 размещаются технологическом припуске. Концы термопар выводятся через швы вакуумного мешка перед их окончательной склейкой и закрепляются термостойкой липкой лентой.
Оборудование для переработки ПКМ.
Классификация оборудования:
По роду выполняемых технологических операций:
1.оборудование для получения и подготовки материалов и поверхностей;
2.оборудование для формообразования
3.оборудование для отверждения
4.оборудование для контроля
5.оборудование для утилизации
6.оборудование для разделительных операций
Не является строгой, так как оборудование совмещается в едином комплексе, где тот или иной вид оборудования выполняется в виде модуля, осуществляющего операцию в непрерывном технологическом процессе.
Оборудование для подготовки материалов.
Относятся:
1.оборудование для предварительной обработки связующего перед совмещением с наполнителем;
2.оборудование для обработки наполнителя перед совмещением с матрицей;
3.пропитанное оборудование для получения препрегов, для повышения качества используют новые принципы: подготовка связующего, ультрозвуковая раскладка наполнителя, сушка с применением физических полей СВЧ, инфракрасный нагрев. Эти установки модульного типа.
Оборудование для формообразования.
Оборудование для формообразования: определяются конструкцией и тиражом выпускаемых изделий. Для изготовления тел, имеющих форму вращения применяют много координатные станки с программным управлением типа СНД, КУ. Для выкладки ленточным препрегом криволинейных и плоских применяют выкладочные центры. Выкладочные центры также выполняют операции зачистки обезжиривании нанесение антиадгезионных и клеевых комплексов, механическую обработку поверхностей.
Для непрерывного изготовления труб и профилей различного сечения разработаны установки для получения изделия методом намотки препрегом на термопластическим связующим и пултрузией.
Оборудование для отверждения.
Оборудование для отверждения: применяют печи электрические, аэродинамического нагрева АРП, автоклавы, гидроклавы Печи электрического нагрева применяют для изготовления изделий небольших размеров. Для изделий больших размеров специально созданы печи аэродинамического нагрева, где рабочая среда нагревается вентилятором. Преимущества: отверждение под давлением атмосферы с одновременным отсосом летучих. Наилучшие результаты получаются при отверждение в автоклавах и гидроклавах. Для физических методов отверждения разработаны установки: камеры СВЧ отверждения, установки токовой полимеризации.
Оборудование для разделительных операций.
При обработке готовых изделий традиционным режущем инструментов возможны межслойные разрушения в зоне обработки. При расскроении происходит разлахмачивания краев. Эти проблемы позволяют решить методы основанные на применении лазерного луча, ультразвука, резки водой под давлении. Установки для лазерной резки позволяют производить размерную
обработку и раскройную операцию толщиной до 20 мм. Эти станки лазерного типа СЛАП и ЛУР. Установки ультразвуковой резки и комплекса на его основе позволяют резать препреги и пакеты из ПКМ до 4 мм, а готовые конструкции до 15 мм. Для резки хрупких, мягких и липких волокнистых материалов и ПКМ применяют гидроструйную резку. Давление водной струи до 300 атм. Пример установка пагруз толщина разрезаемой резины, паралона равна 100 мм.
Оборудование для контроля.
Оборудование для контроля разнообразно, причина предприятие создавало само для своего профиля. В производстве изделий из ПКМ стоят неразрушающие методы контроля качества и физико-механических свойств: контроль сплошности, другие скрытые дефекты осуществляют установками ультразвук и ренгенового контроля.
Для непроводящих электрический ток применяют СВЧ метод. Преимущество возможность проводить послойное зондирование. Плотность токопроводящих композиций определяют токовихревыми методами. Модули упругости всех родов определяют акустическими методами. Прочность – томографическими методами. Универсальным средством контроля является вычислительный томограф. Для контроля геометрии сложных поверхностей наряду с контактными методами применяют установки с использованием лазерной техники. Применяют автоматизированный комплекс для неконтактного контроля с исплользованием до 5000 мм с точностью плюс минус 0.05 в любой точке контролируемой поверхности.
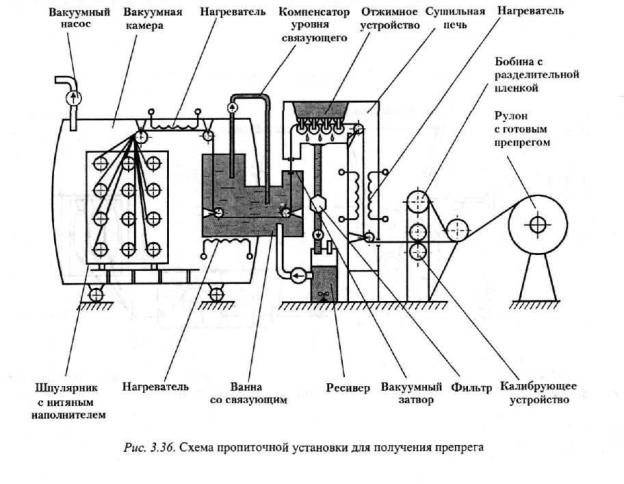
Из книги серии «Учебники НГТУ. Композиционные материалы» А.А. Батаев, В.А. Батаев Композиционные материалы: строение, получение, применение: Учебник. –Новосибирск: Изд-во НГТУ, 2002. -384 с.
ПОЛУЧЕНИЕ ЗАГОТОВОК ДЛЯ ПОЛИМЕРНЫХ КОМПОЗИЦИОННЫХ МАТЕРИАЛОВ В ВИДЕ ПРЕПРЕГОВ
ПОЛУЧЕНИЕ ПРЕПРЕГОВ МЕТОДОМ ПРОПИТКИ АРМАТУРЫ В СМОЛАХ
При производстве полимерных композиционных материалов широко используются промежуточные полуфабрикаты в виде препрегов. Полуфабрикаты этого типа обладают большой жизнеспособностью. При комнатной температуре срок хранения препрегов составляет — 3 месяца. Охлажденные препреги могут сохранять свои свойства до I года. Лучшие условия хранения препрега реализуются при температуре сухого льда. Препрег представляет собой полуфабрикат, хранящийся в виде рулонов или пакетов. Слои препрега разделены пленкой. При комнатной температуре препреги приобретают технологические свойства


«чистых» материалов. Степень липкости, характерная для данной температуры, делает удобным процесс ручной выкладки. Препреги могут раскраиваться на станках с числовым программным управлением.
Для изготовления препрегов используют пропиточные установки вертикального или горизонтального типов. На рис. 3.36 [5] приведена схема пропиточной машины вертикального типа. Нити наполнителя поступают со шпулярника, формируются в ленту, сушатся нагревателем, после чего попадают в ванну со связующим. Пропитанная связующим лента отжимается в специальном устройстве и сушится в печи. Готовый препрег покрывается разделительной пленкой и сматывается в рулон.
Препрег, полученный на специальных пропиточных установках, отличается высоким качеством пропитки, минимальными повреждениями волокон, равномерностью содержания связующего.
На рис. 3.37 приведена схема малогабаритной установки для получения препрегов. Исходные нити поступают с бобин, протягиваются с высокой скоростью через пропиточную ванну, отжимаются валками, раскладываются в ленту и попадают в цилиндрическую камеру сушки. Подсушенная до требуемого состояния лента покрывается разделительной пленкой и сматывается на приемный барабан. Разделительная пленка предохраняет препрег от склеивания.
3.3.2. ПОЛУЧЕНИЕ ПРЕПРЕГОВ С ИСПОЛЬЗОВАНИЕМ ПОРОШКОВЫХ ДИСПЕРСНЫХ ПОЛИМЕРОВ
Для получения препрегов могут быть использованы различные типы связующего материала. Обычно связующее используется в виде смол. В последние годы разрабатываются и применяются методы получения препрегов с использованием полимеров, находящихся в тонкодисперсном порошкообразном состоянии [36]. Промышленностью выпускается множество полимеров в порошкообразном состоянии, в том числе полиэтилен низкого и высокого давления, полипропилен, фторопласты, поливинилхлорид, поливинилбутираль, полиамиды, поликарбонат, полисульфон и другие материалы. По сравнению со многими используемыми смолами дисперсные полимеры отличают меньшая себестоимость переработки, более высокое качество получаемого материала, простота автоматизации технологических процессов их нанесения, меньшая степень загрязнения биосферы. Для нанесения порошковых материалов на волокнистый наполнитель их переводят в псевдоожиженное («кипящее») состояние Это состояние порошка достигается при определенных режимах продувания через него газа. Перевод порошкообразной системы в подвижное (виброожиженное) состояние возможен также под действием механических колебаний или при совместном воздействии продуваемого газа и механических колебаний (вибрации) [36].
Для получения препрегов на основе дисперсных полимеров используют электростатическое нанесение порошков на волокнистую арматуру. Процесс нанесения полимеров заключается в электрозаряжении частиц порошка, переносе их во внешнем электрическом поле, осаждении и удержании на волокнах. В результате этого в объеме волокнистого наполнителя формируется электроосажденный слой заряженных частиц.
Разработано несколько схем нанесения порошкообразных полимеров на непрерывную волокнистую арматуру. Одна из них показана на рис. 3.38 [36]. Препрег получают путем одностороннего нанесения порошкового связующего при просыпании поступающих из дозатора частиц через вибрирующую сетку на заземленную ленту арматуры. Закрепление связующего на ленте происходит при нагреве материала в термической камере. Сформированная таким образом лента препрега наматывается на приемный барабан. В устройстве, изображенном на рис. 3.39, лента, являющаяся основой препрега, поступает в верхнюю зону камеры псевдоожижения, контактирует с заземленным электродом и с прилипшими частицами выходит из камеры. Слой заряженных частиц образуется на поверхности и внутри ленты. Закрепление частиц на ленте происходит в процессе дальнейшего нагрева ленты в камере термической обработки.