
Курс Лекций по Бабушкину
.pdfФедеральное агентство по образованию Государственное образовательное учреждение высшего профессионального
образования Пермский государственный технический университет
КУРС ЛЕКЦИЙ
Конструкционные и функциональные волокнистые композиционные материалы
Автор: |
|
доцент кафедры Механика композиционных |
|
материалов и конструкций, кан. техн. наук |
А.В. Бабушкин |
Пермь, 2007 г

Глава 1
Введение
1.1 Цели и задачи курса
ТКМ является комплексной общеинженерной дисциплиной, включающей основные положения физической химии, физики, и механики КМ, технологической механики.
Цель: усвоение принципов и методов технологии производства изделий из КМ на полимерной, углеродной и металлической матрице, понимание конструкционно-технологических особенностей этих материалов и правильный учет их в конструкциях создаваемых изделий, эффективное применение КМ и технологий.
1.2 КМ: общая характеристика, состав и классификация
КМ - материалы, состоящие из 2х или более компонентов (отдельных волокон или других армирующих составляющих и связующей их матрицы) и обладающие следующими признаками:
Не встречаются в природе, так как созданы человеком;
Состоят из 2х или более компонентов, различающихся по своему составу и разделенных выраженной границей (не должны растворяться или иными способами поглощать друг друга); Имеет новые свойства, отличных от свойств составляющих их компонентов; Неоднородны в микромасштабе и однородны в макромасштабе; Состав, форма и распределение компонентов запроектированы заранее; Свойства КМ определяются из взаимодействия компонентов.
Компонент КМ, непрерывный во всем объеме, называется матрицей (связующим), компонент прерывистый, разъединенный в объеме композиции называется армирующим элементом (наполнителем). Понятие "армирующий"означает введенный материал с целью изменения свойств. Изменение свойств может быть в ту или иную сторону, не обязательно упрочняющую.
КМ - материал неоднородный. Деление материалов на композиционные и некомпозиционные определяется объективной необходимостью применения тех или иных моделей.
КМ классифицируются по следующим признакам:
1.Материалы матрицы и армирующих элементов;
2.Геометрия компонентов;
3.Методы получения;
4.Назначение.
Общее название КМ как правило происходит от материала матрицы: ПКМ, МКМ, УУКМ и другие. КМ содержащие 2 или более различных по составу или природе матрицы называется полиматричным (если наполнителя, то полиармированным).
Вшироком смысле слова понятие КМ включает в себя любой материал с гетерогенной структурой (состоящий из 2х или более фаз).
Почти все металлические сплавы (сталь) содержат несколько фаз (ферритоцементит), которые либо создаются намеренно, для придания материалу заданных эксплуатационных и
технологических свойств, либо образуются в материале в результате наличия примесей. Более того, КМ часто встречаются в природе: дерево, кости животных, зубы людей. Первыми КМ можно назвать асфальт, железобетон, текстолит.
По виду армирующего наполнителя КМ делятся на:
1. КМ с дисперсными частицами (гранулированными, объемными); 2. КМ с поверхностными и плоскостными армирующими частицами; 3. Волокнистые КМ.
Волокнистые КМ можно классифицировать в зависимости от дисперсности или непрерывности волокон, а также от их ориентации:
1. Однонаправленные КМ с непрерывными волокнами;
2. КМ с дискретными волокнами; 3. КМ с непрерывными волокнами, ориентированными во многих направлениях.
Взависимости от геометрии армирующих компонентов и их взаимного расположения композиты бывают:

1.Изотропными;
2.Анизотропными.
К макроскопически изотропным композитам относят дисперсно упрочненные сплавы, псевдосплавы и хаотично армированные КМ.
локальная анизотропия Хаотично армированный материал
локальная анизотропия изотропный материал
макроанизотропия
Ортотропные (ортогонально изотропные) КМ характеризуются наличием в каждом элементарном объеме 3х взаимно перпендикулярных плоскостей симметрии свойств (КМ, армированные последовательно чередующимися слоями волокон в 2х взаимно перпендикулярных направлениях, КМ, армированные тканями с продольнопоперечной укладкой).
Трансверсально изотропные КМ - имеющие плоскость изотропии и перпендикулярную ей ось симметрии бесконечного порядка (однонаправленные КМ, слоистые КМ с так называемой
"звездной"укладкой волокон, при условии, что угол м/у направлениями укладки волокон в смежных слоях меньше 72 °C).
Всоответствии с классификацией КМ по структуре расположения компонентов разделяются на группы с каркасной, матричной, слоистой и комбинированной структурой.
Всоответствии с классификацией по методам получения КМ разделяют на: КМ, полученные жидко- и газофазными методами, методами осаждения, опыления и комбинированными методами.
К жидкофазным методам относятся пропитка и направленная кристаллизация сплавов, к твердофазным: прессование, прокатка, ковка, штамповка, уплотнение взрывом, диффузионную сварку, волочение, экструзию и т.п. При получении КМ методами осаждения (напыления) матрица наносится на волокна из растворов солей или других соединений, из парогазовой фазы, из плазмы и др.
1.3 Экономическая эффективность КМ
Пока КМ дороже обычных промышленных. Это объясняется тем, что объем их производства невелик, а некоторые из них существуют только в виде лабораторных образцов. Однако, в силу особенности КМ удовлетворять самые разнообразные потребности (имеется ввиду возможность применения свойств в самых широких пределах), спрос на КМ будет расти, а цена падать.
1.4 Общая характеристика компонентов КМ
Армирующий наполнитель КМ как правило несет силовую нагрузку. Выигрыш механических показателей связан с высокой прочностью наполнителя, например, борных или углеродных волокон. Матрица КМ служит для распределения деформаций и напряжений между волокнами и для придания композиту упругих свойств.
Однонаправленный

перекрѐстноармированный
Наполнителями в КМ могут служить твердые тонко-дисперсные, зернистые или пластинчатые частицы, полые сферы, но, главным образом, волокнистые материалы (нити, ровенги, жгуты, ленты, ткани, а также нитевидные кристаллы или усы). В конструкционных КМ применяют преимущественно волокнистые армирующие наполнители, при этом прочность композиции определяется двумя основными факторами: 1.регулярностью распределения волокон в объеме матрицы
регулярно |
нерегулярно |
2.взаимодействием между волокном и матрицей (межфазное взаимодействие, адгезия, механические и химические взаимодействия).
Характеристики матричных материалов определяют механические свойства КМ при сдвиге и нагружении их нормальными напряжениями в направлениях, отличных от ориентации волокон, а также термоустойчивость, химическую стойкость композита (хемостойкость) и технологические режимы получения изделий. Роль матрицы заключается также в придании формы изделию. Кроме основных компонентов - арматуры и связующего в состав КМ могут входить различные катализаторы, пластификаторы, стабилизаторы, отвердители, красители и т.п.
1.5 Характеристика конструкционных КМ
Конструкционные КМ в изделиях несут значительную механическую или тепломеханическую нагрузку.
К конструкционным КМ будем относить такие, в которых:
1.Частицы армирующего наполнителя имеют четко выраженную границу с матрицей;
2.Армирующий наполнитель, как правило волокнистый, закономерно распределен в объеме матрицы.
Прочность КМ максимальна, если волокна распределены в матрице не только регулярно, но и в строгом соответствии с тем, как распределены рабочие напряжения.
Важнейшими конструкционными свойствами являются:
1.Модули упругости;
2.Ударная прочность (вязкость);
3.Прочность при растяжении и изгибе;
4.Прочность при сжатии;
5.Твердость;
6.Теплостойкость;
7.Сопротивление ползучести;
8.Трещиностойкость;
9.Виброустойчивость и усталостная прочность;
10.Хемостойкость.
1.6 Характеристика функциональных КМ
На самостоятельную проработку.
Глава 2
ОСНОВЫ ПРОИЗВОДСТВА ВОЛОКОН
2.1. ПОЛУЧЕНИЕ НАПОЛНИТЕЛЕЙ
В композиционных материалах (КМ) применяют разнообразные волокнистые наполнители: керамические (стеклянные, углеродные, борные), полимерные (органические, поливинил-спиртовые и т. п.) и (редко) металлические. Основная функция наполнителя в КМ — обеспечение заданных прочностных и (частично) теплофизических свойств. Поэтому качество наполнителя оценивают его прочностными характеристиками, адгезионной способностью и термостабильностью. Эти характеристики в совокупности наиболее предпочтительны для стеклянного наполнителя (стекловолокна), прочность которого составляет 1470—4900 МПа; модуль упругости 49—123 ГПа; относительное удлинение при разрыве 1,5—5,4%; температура плавления 1710°С; допустимая температура длительной эксплуатации 350—800°С; адгезионная прочность к связующему 16—40 МПа [1, 2]. C учетом низкой стоимости и относительной простоты получения стекловолокна становятся понятными причины широкого применения его в производстве КМ.
Для получения КМ c повышенной упругостью используют углеродные, борные и органические волокна, а сами материалы называют соответственно угле-, боро- и органопластиками. Эти виды КМ находят пока ограниченное применение в промышленности, поэтому далее под волокнистым наполнителем понимают преимущественно стекловолокно.
По химическому составу различают щелочные и бесщелочные стекловолокна. Первые более дешевы, но уступают вторым по прочностным свойствам и химической стойкости при высоких тепловых нагрузках. Поэтому при изготовлении слабо нагруженных изделий применяют щелочные волокна, а для так называемых ответственных изделий (эксплуатируемых в условиях больших силовых и температурных воздействий или в коррозионных средах) — бесщелочные наполнители, получаемые из алюмосиликатных и титанили борсодержащих стекол [3].
Для получения наполнителя применяют непрерывные и штапельные элементарные стекловолокна диаметром 3—20 мкм. Непрерывные волокна характеризуются большой длиной (до нескольких километров) и параллельной укладкой. Штапельные волокна короткие (несколько десятков см) и хаотически уложены. Из непрерывных волокон изготовляют нити (в каждую нить входит 2—48 волокон) и жгуты (ленты), объединяющие 20—100 нитей. Качество жгута или нити характеризуют линейной плотностью и средней прочностью (значение последней обычно заметно отличается от прочности КМ, так как полимерная матрица увеличивает запас прочности наполнителя). Нити и жгуты (ленты) используют, как правило, для производства ответственных изделий методом намотки. Другое направление переработки стекловолокна связано c получением из него рулонных наполнителей -- тканых и нетканых материалов. Тканые наполнители изготавливают методами традиционной текстильной переработки стеклонитей. Нетканые наполнители (холсты) вырабатывают из короткорубленых жгутов или штапеля. Для связи волокон в холсте применяют небольшие количества связующего или прошивку нитями.
Рулонные наполнители используют в производстве слабо нагруженных изделий (дренажные трубы, кровельные листы, воздуховоды и т. п.).
Прочность и адгезионная способность стекловолокна во многом определяется сохранностью его поверхности, прошедшей своеобразную «закалку» в процессе вытяжки через фильеру. Для защиты поверхностей волокна при его хранении и переработке применяют различные замасливатели в виде эмульсий из жирных кислот и парафинов. Эти покрытия снижают адгезионную способность стеклонаполнителя, поэтому перед его использованием замасливатель удаляют.
Элементарные волокна 8 получают вытягиванием расплава стекла через фильеры (малые отверстия c насадками или без них), расположенные на дне фильерного питателя 6 установки производства стекловолокна (рис. 1.1). Жидкое стекло поступает в питатель непосредственно из стекловаренной
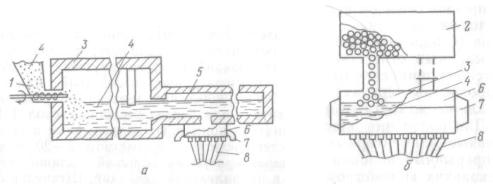
печи 3 (рис. l.l,fl) или образуется в корпусе питателя при плавлении стеклянных шариков (рис. 1.1,6), которые предварительно получают из стекломассы, охлаждают и хранят в бункере 2. Для плавления шариков используют электрический ток, который через токоподводы 7 пропускается через металлический корпус питателя. Первый способ производства стекловолокна называют одностадийным, второй — двухстадийным.
Рис. 1.1. Схема получения стекловолокна двухстадийным (а) и одностадийным (б) способами: / — загрузчик шихты; 2 — бункер шихты или стеклошариков; 3 — стекловаренная печь; 4 — расплавленная стекломасса; 5 — фидер; 6 — фильерный питатель; 7 — токоподводы; S — элементарные стекловолокна
Первоначально стекловолокно диаметром 2—9 мкм, используемое для выработки стеклотканей, производили двухстадийным способом. Однако для изготовления стекловолокна диаметром 9—20 мкм, которое широко используют в КМ, этот способ оказался экономически неэффективным из-за больших затрат энергии на охлаждение и повторное плавление стекло-ыариков. Поэтому большее распространение начинает получать одностадийный способ выработки стекловолокна диаметром 9— 20 мкм, хотя в этом случае требования к конструктивному оформлению технологического процесса и системе автоматизации более жесткие.
Стекловолокно получают преимущественно из бесщелочного стекла «Е», которое вырабатывают в стеклоплавильных печах [3]. Эти небольшие по размерам ванныепечисотношениемдли-ны к ширине не менее 3: 1, отапливаемые пламенными горелками, в которых сжигают газ, мазут, керосин (некоторые печи оборудованы электрическими нагревателями). Используемый для сжигания топлива воздух подогревается в рекуператорах или (реже) регенераторах. Плавильная печь (рис. l.l,c) оборудована c одного конца несколькими загрузочными отверстиями, через которые в нее из бункера 2 шнеком / подается шихта и отходы стекловолокна; сваренная стекломасса 4 вытекает c противоположного конца печи в раздаточный фидер (распределитель) 5.
Качество стекла зависит от состава и однородности шихты и наличия различных примесей в стекломассе. В частности, неоднородность шихты вызывает местные изменения вязкости стекломассы, которые влияют на ее расход через фильеры и могут приводить к обрыву элементарных волокон. Твердые даже субмикронные включения в непрерывном волокне действуют как концентраторы напряжений и также способствуют обрыву элементарных волокон.
Сваренное стекло поступает из печи по раздаточным фидерам либо к автоматам для получения стеклянных шариков, либо к питателям, установленным в дне фидерных каналов. В обоих случаях фидер обеспечивает «доводку» температуры и вязкости стекломассы до требуемых значений. Фидеры для производства стеклошариков имеют небольшую длину и поэтому стабилизация температуры, а, следовательно и вязкости, стекломассы не вызывает затруднений. Длина фидеров одностадийной установки значительна (до 50 м); конструкция всей фидерной системы может быть различной для установок разной производительности. Наибольшее распространение получили так называемые Т-образные и Н-образные конструкции фидеров лля установок малой и средней производительности. Для печей большой производительности фидерная система может иметь вид гребенки. Стабилизация температуры и вязкости движущейся стекломассы в таких фидерах требует применения отопительных газовых горелок или электрических нагревателей.
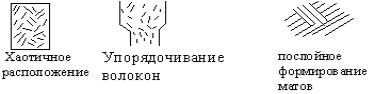
При газовом отоплении в основном используют газовоздушную смесь c требуемым соотношением «газ — воздух», подаваемую на горелки фидера. Эта схема отопления экономически выгоднее той, в которой топливо смешивается c воздухом непосредственно в каждой горелке.
Фильерные питатели, из которых вытягивают стеклянные волокна, представляют собой нагревательную печь, изготовленную из платинового сплава и обогреваемую пропускаемым через нее переменным током от «печных» трансформаторов. При одностадийном способе получения волокна необходимо лишь точно поддерживать заданную температуру расплава стекла в фильерном питателе, поэтому применяют маломощные «печные» трансформаторы. Для двухстадийного способа, в котором значительная часть мощности расходуется на плавление стеклянных шариков, требуются весьма мощные трансформаторы. Разные функции фильерных питателей определили и различие в их конструкции (см. рис. 1.1). Если конструкция питателя ' для одностадийного способа относительно проста, то фильерный питатель для двухстадийного способа содержит ряд дополнительных конструктивных элементов для обеспечения плавления холодных стеклянных шариков c требуемой скоростью и предотвращения попадания их в нижнюю зону питателя и нарушения температурного режима расплава. Число фильер в дне питателя колеблется от 200 до 6000 и зависит от требуемых диаметра элементарных волокон и их линейной плотности. Под фильер-ной пластиной между рядами фильер располагают ребра или трубки, служащие для быстрого охлаждения стеклянных волокон и стабилизации процесса их вытягивания.
Элементарные волокна после фильер собираются в комплексную нить, которая проходит через замасливающее устройство в виде смоченного определенным составом валка (ленты), и далее, пройдя через нитесборник и раскладчик, наматывается на вращающуюся бобину, установленную на наматывающем аппарате.
2.2. МЕТОДЫ ПОЛУЧЕНИЯ И СВОЙСТВА АРМИРУЮЩИХ СТЕКЛОВОЛОКОН
В армированных КМ основную нагрузку воспринимают волокна. Вводят их в матричный материал в виде отрезков, непрерывных нитей (длина которых соответствует длине армированного изделия), либо в виде тканей различного плетения, войлока, матов. Дискретные волокна могут располагаться в матрице хаотично или ориентированно.
Непрерывные волокна в зависимости от требований к КМ вводятся в матрицу, как правило, слоями, которые могут быть ориентированны под разными углами. По структурному признаку армирующие элементы можно разделить на волокна с:
1.монокристаллической,
2.поликристаллической,
3.полимерной,
4.аморфной структурой.
2.2.1 Состав стекла, применяемого при производстве стекловолокон
Стекло является аморфным материалом, занимающим по своим физико-механическим свойствам место между твердым телом и жидкостью. Химические стекла состоят в основном из кремнеземной основы, сост. из полимерных цепочек диоксида кремния (SiO4), однако диоксид кремния (кварц) в чистом виде требует высоких температур для размягчения и вытягивания (в волокна и др.), поэтому необходима модификация состава стекла (кварца) для снижения уровня рабочих температур, при которых стекломасса обладает вязкостью, позволяющей проводить вытяжку волоком.
Различают 4 вида промышленно производимых стекол (для производства стекловолокон): 1. Марка A применяется для создания волокон, обладающих высокой хемостокостью;
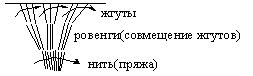
2.Марка C - особо высокая хемостойкость;
3.Марка E - электроизоляционные свойства;
4.Марка S - для создания волокон с высокими прочностными характеристиками.
Также существуют специальные стекла: марка M - высокомодульное стекло (E=113ГПа),
марка D - низкие диэлектрические свойства, применяются в электронике, марка L - радиационно защитные свойства.
2.2.2 Свойства стекловолокон
Свойства стекловолокон зависят от состава стекла и термической предыстории. Стекловолокна обладают следующими свойствами:
1.Высокая прочность при растяжении;
2.Тепло§ и огнестойкость (не горят);
3.Хемостойкость (химическая пассивность, а также устойчивость к воздействиям грибков, бактерий и насекомых);
4.Влагостойкость (не набухают, не растягиваются, не гниют);
5.Термические свойства (низкий КЛТР, коэффициент теплопроводности);
6.Электрич. свойства (низкая диэлектрическая постоянная в большом диапазоне частот).
2.2.3 Основные физико-технические характеристики стекловолокон
|
A |
C |
E |
S |
Плотность |
2500 |
2490 |
2540 |
2480 |
Предел прочности при 22 C |
3033 |
3033 |
3448 |
4585 |
Предел прочности при 533 C |
- |
- |
1724 |
2413 |
E |
- |
69.0 |
72.4 |
85.5 |
КЛТР |
8.6 |
7.2 |
5.0 |
5.6 |
Температура размягчения |
727 |
749 |
841 |
- |
2.1.4 Высокосиликатные и кварцевые волокна
Имеют наиболее высокие удельные прочностные характеристики. При этом кварцевое волокно часто характеризуется пределом прочности при растяжении приблизительно в 5 раз большем чем прочность высокосиликатного волокна. Удлинение при разрушении составляет около 1%. Высокосиликаты состоят на 99.23% из SiO2, кварц - из 99.95% SiO4.
2.3. ВИДЫ АРМИРУЮЩИХ ЭЛЕМЕНТОВ СИСТЕМ
Армирующие элементы (волокна) вводят в матричную основу как разориентированными, так и придавая им определенную ориентацию. Одним из главных способов изготовления армирующих систем с требуемой ориентацией волокон является их текстильная переработка.
Дисперсные волокна можно перерабатывать в пряжу, длинные волокна используют для получения ровенгов.
Пряжа - нить из коротких волокон, соединенных при помощи кручения. Может быть однородная и смешанная. Предназначена как для непосредственного армирования материалов, так и для последующей ткацкой переработки нитей.

2.3.1 Стекловолоконные ровенги
Ровница - объединение непрерывных и параллельных жгутов или элементарных волокон. Традиционный ровенг производится совместным прядением (скручиванием) нескольких простых жгутов ровницы (или волокон), число которых определяется требованиями последующей переработки.
Параметром ровенга является длина единицы его массы, так называемый развес. Развес ровенга лежит в основном в пределах 3600…450 м/кг.
Большая часть стекловолокна перерабатывается в грубые ткани. Ткань выпускается с плотностью 0.407..1.356 кг/м2 и с толщиной 0.51..1.02 мм.
2.3.2 Ткани
В результате ткацкой переработки пряжи, нитей, ровенгов получают сетки и ткани, эти армирующие элементы характеризуются заданным порядком взаимного расположения нитей, определяющим их структуру и свойства. Нити продольной системы (основы) и поперечной (утка) переплетаются так, что их осевые линии изогнуты. Наиболее простые виды переплетения нитей в тканях и сетках: полотняная и саржевая.
Однако, тканые сетки обладают рядом существенных недостатков, главный из которых состоит в том, что их можно изготовить из достаточно пластичных пряж и волокон. Еще один недостаток состоит в том, что наличие контакта между продольными и поперечными нитями приводит к их пережимам в процессе уплотнения композиций.
Приведенных недостатков лишены трикотажные (вязанные) сетки или ткани. Сетки типа "курлиная гладь"состоит из петель, дающих петельные ряды и столбиков, которые образуются из нанизанных друг на друга петель и располагаются в направлении перпендикулярных к петельным рядам. Более сложным строением обладают трикотажные ткани типа "ластик", в которых лицевые петелечные столбики чередуются с изнаночными. Волокна в полотняных сетках начинают работать гораздо раньше, чем волокна в трикотажных сетках. Существуют также: саржевое ломаное 3-1 переплетение,
восьмиремизсковое сатиновое переплетение, однонаправленные ткани (прочная основа, тонкий уток), нетканые однонаправленно армированные системы.
Саржевое ломаное 3-1 переплетение - одна нить основы перекрывается 3мя нитями утка сверху и одной снизу с образованием нерегулярного рисунка.
Восьмиремизсковое сатиновое переплетение - одна нить основы перекрыта семью нитями утка сверху и одной снизу, с образованием нерегулярного рисунка. Эта ткань обладает максимальной изотропной прочностью.
Стекловолоконная пряжа может перерабатываться также в тесьму, контурные ткани, ткани с гофрированными волокнами и трехмерные многослойные ткани.
Тесьма представляет собой узкую (до 30 см) ткань, которая может содержать распущенную кромку. Контурные ткани - такие, у которых геометрия и форма совпадает с деталью. Ткани с гофрированными нитями состоят из 2х слоев, соединенных вместе нитями так, что конфигурация соединений представляет собой треугольник или прямоугольник. Трехмерные ткани - обычные плоскостные ткани, соединенные пряжей в третьем
направлении (по сравнению с тканями с гофрированными нитями имеют большее количество слоев и более сложную систему сшивки).
2.3.3 Стекловолоконные маты
3 основных типа:
1.Маты из резаных нитей;
2.Из непрерывных нитей;
3.Декоративные маты (покрытия).
Маты из резанных волокон изготавливают обычно в виде нетканых материалов, в которых стекловолокна получают резкой путками или непрерывного жгута на штапельки длиной
25…50 мм.
Волокна имеют преимущественно случайное распределение в горизонтальной плоскости и удерживаются вместе химическим связующим.
Плотность матов составляет обычно 0.229..0.916 кг/м2 и могут иметь толщину 50..2000мм. При изготовлении матов, получаемых из нарезанных непрерывных жгутов стекловолокна, раскладываются и соединяются в виде спирали, такие маты не требуют дополнительной связи за счет механического переплетения.
Декоративные маты - очень тонкие маты, которые изготавливают из непрерывных мононитей и используют для отделки и армирования поверхностей.
2.4. ВОЛОКНА, ИСПОЛЬЗУЕМЫЕ ДЛЯ АРМИРОВАНИЯ МЕТАЛЛОКОМПОЗИТОВ
Для армирования КМ на основе металлической матрицы применяются волокна различной природы:
1.Металлические волокна;
2.Неметаллические волокна (в чистом виде);
3.Волокна из оксидов, карбидов, боридов.
Металлическая проволока - один из самых доступных типов волокон, который по конструкционной прочности часто превосходит другие виды. Она также более технологична, выгодна с экономической точки зрения и более надежна в эксплуатации.
Для армирования КМ применяют металлическую проволоку из сталей: Wf, Mo, Be, Ti, Nb и прочих металлов и сплавов.
2.4.1 Стальная проволока
Высокопрочная проволока из нержавеющей стали - один из наиболее распространенных упрочнителей КМ.