
- •Стали
- •Магниевые сплавы
- •Титановые сплавы
- •Алюминиевые сплавы
- •2.1. Технологичность заготовок
- •Горячештампованные заготовки
- •Литые заготовки
- •Простановка размеров
- •Технологичность основных элементов конструкции деталей
- •Открытые плоскости
- •Сопрягаемые плоскости (колодцы, карманы, пазы, гнезда)
- •Наружные поверхности вращения
- •Внутренняя резьба
- •Фасонные поверхности
- •Монолитные панели
- •Панели, изготовляемые из плит
- •Панели из горячештампованных заготовок
- •Панели из горячепрессованных заготовок
- •Панели из специального литья
- •Крупногабаритные детали из алюминиевых и магниевых сплавов
- •Балки и лонжероны
- •Детали узлов поворота
- •Шпангоуты, рамы и их детали
- •Длинномерные детали из прессованных профилей
- •Фитинги и кронштейны
- •Рычаги и качалки
- •Фланцы и крышки
- •ЛИТЕРАТУРА

резко снижая трудоемкость изготовления деталей. При этом чертежные допуски на размеры, получаемые размерным химическим травлением, должны складываться из допусков на механическую обработку и размерное химическое травление.
Наружные поверхности вращения
При конструировании деталей с поверхностями вращения следует руководствоваться рядом специфических требований технологичности, среди которых важнейшими являются обеспечение жесткости конструкции детали и удобство ее установки базирования и закрепления.
Для этого в тонкостенных деталях диаметром 500 мм и более необходимо предусматривать ребра жесткости. При проектировании деталей типа валиков не рекомендуется задавать длины более 10 D.
Не следует поверхность детали проектировать конической по всей длине. Необходимо предусматривать цилиндрический поясок, который может служить базовой поверхностью в тонкостенных деталях диаметром более 500 мм и высотой свыше 200 мм не рекомендуется проектировать переход между диаметрами в виде конической поверхности, лучше – в виде уступа (рис. 2.69). Детали такого типа рационально обрабатывать на карусельных станках с креплением за уступ.
Рис. 2.69. Уступ на наружной цилиндрической поверхности крупной детали, обеспечивающий удобство ее крепления на карусельном станке
В стальных деталях, которые имеют точные наружные диаметры (7-го и 8-го квалитета) или кольцевые пояски, необходимо предусматривать центры (рис. 2.70, а) или центровые фаски (рис. 2.70, б) для дальнейшей обработки на шлифовальном станке, а размеры центров и центровых фасок оговаривать в чертеже.
Отсутствие центровых отверстий или фасок в чертежах требует введения технологических центров, что вызывает лишний расход материала, дополнительные операции для удаления технологических центров после окончательной обработки детали. Эти операции трудо-
59
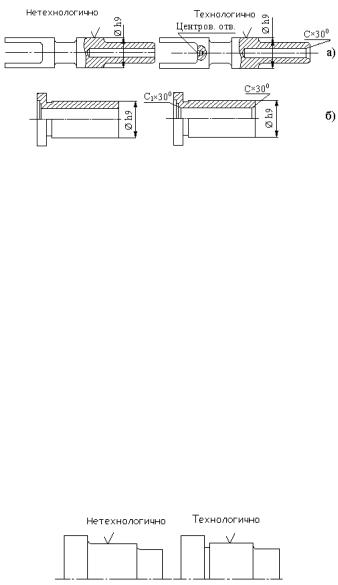
емки, т. к. часто выполняются после закаливания, а иногда и после гальванических операций. В последнем случае места технологических центров остаются без гальванопокрытий и требуют лакокрасочных защит.
Рис. 2.70. Выполнение в конструкции детали – тела вращения центров и центровых фасок, позволяющее выдержать единство баз на всех операциях обработки точных цилиндрических поверхностей
Ступенчатые цилиндрические поверхности деталей следует по возможности располагать по мере убывания диаметров от одного конца к другому (рис. 2.71, а) или от середины к обоим концам (рис. 2.71, б).
а
б
Рис. 2.71. Примеры технологичных конструкций деталей с односторонними (а) и двусторонними (б) уступами
Точные цилиндрические поверхности следует отделять от других поверхностей канавками для выхода шлифовального круга (рис. 2.72). Если из-за условий прочности нельзя применить канавку, то на детали для всех ступеней предусматривать одну и ту же галтель, т. к. разные галтели требуют разной заправки абразивного круга.
На наружных поверхностях вращения следует избегать выступов, не вписывающихся в контур поперечного сечения (рис. 2.73).
60
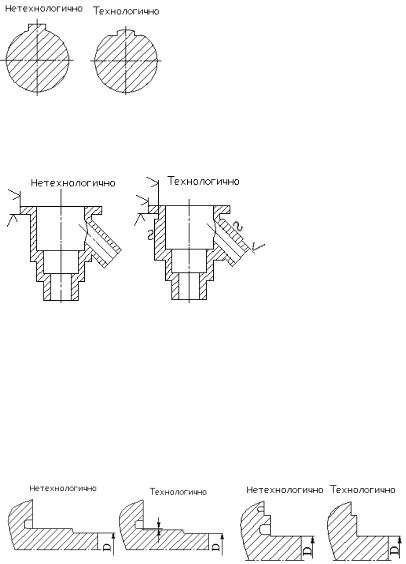
Рис. 2.72. Технологичное оформление шлифуемых цилиндрических поверхностей
ÕРис. 2.73. Пример технологичного выполнения выступа на цилиндрической поверхности
При сопряжении поверхностей вращения с другими поверхностями необходимы переходные участки (рис. 2.74).
Рис. 2.74. Формирование переходного участка на детали, облегчающего проектирование траектории движения резца при обработке цилиндриче-
ского участка
Торцевые поверхности вращения следует предусматривать плоскими, без радиальных канавок и выступов. Обработка прерывистых поверхностей снижает производительность, точность обработки, ухудшает шероховатость поверхности.
Необходимо разделять уступами поверхности, обрабатываемые разным инструментом (рис. 2.75) и избегать проектирования кольцевых выточек (рис. 2.76) на торце со стороны стержня, если торцы не требуют шлифования. Обработка выточек связана с применением специального инструмента и увеличением трудоемкости.
Рис. 2.75. Отделение уступом кольцевой |
Рис. 2.76. Исключение торцевой |
выточки, обрабатываемой канавочным рез- |
выточки, если не требуется шли- |
цом, и цилиндрической части, обрабатывае- |
|
61
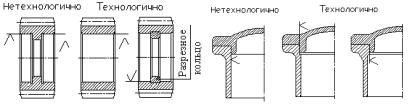
мой проходным резцом |
фование торца |
Обеспечение технологичности отверстий
В зависимости от требуемых квалитетов точности, шероховатости поверхности, а также конфигурации детали отверстия обрабатываются сверлением, зенкерованием, развертыванием, растачиванием, шлифованием, протягиванием и другими способами.
Отверстия подразделяются на обыкновенные и глубокие, к последним относятся отверстия, у которых отношение длины к диаметру не менее 5–8 (большие значения – для отверстий меньшего диаметра). Кроме того, отверстия делятся на сквозные и глухие. К глухим относятся отверстия, в которых резко ограничено осевое перемещение инструментов, изготовляющих отверстия (обработка «в упор»), а также отверстия ступенчатые со значительным перепадом ступеней.
Отверстия по возможности следует делать сквозными. Изготовление глухих отверстий, особенно таких, к которым предъявляются высокие требования в отношении точности, шероховатости поверхности и расположения их относительно других поверхностей, вызывает большие затруднения. В ступенчатых отверстиях наиболее точную ступень необходимо делать сквозной (рис. 2.77). При обработке сквозных отверстий можно добиться большей производительности. По возможности следует сокращать длину обрабатываемой поверхности
(рис. 2.78).
Рис. 2.77. Технологичное выполнение |
Рис. 2.78. Уменьшение длины класс- |
сквозных классных отверстий |
ной цилиндрической поверхности, |
|
снижающее трудоемкость обработки |
Необходимо по возможности ограничивать применение отверстий высокого квалитета точности. Наличие таких отверстий увеличивает стоимость деталей и производственный цикл их изготовления. В связи с тем, что для изготовления более точных отверстий требуется большее число переходов, необходимо и большее количество инструментов. Сами инструменты должны быть очень точными и более дорогими. Кроме того, такие инструменты быстрее теряют свои размеры в процессе изнашивания при работе. Для изготовления отверстий высоких квалитетов точности требуется очень тщательная наладка станка и
62

инструмента. Особенно технологически сложно и трудоемко выполнение классных отверстий малых диаметров (до 9 мм) в термически обрабатываемых материалах с σв≥ 1000 МПа. Обработку таких отверстий производят инструментом, оснащенным твердым сплавом, после закаливания детали. Изготовление и эксплуатация такого инструмента представляет большие производственные трудности.
Конфигурация глухих отверстий, обрабатываемых осевым инструментом, должна соответствовать конструкции применяемого инструмента. Осевой режущий инструмент (сверло, зенкер, развертка) имеет коническую заборную часть, которая образует у дна отверстия переходную поверхность. Так как зенкер и развертку нельзя установить точно на глубину отверстия и они имеют разные по величине заборные конусы, то форма переходной поверхности получается ступенчатой (рис. 2.79). Подрезка торца в глухих отверстиях (эскиз в) является малопроизводительной операцией. Поэтому при обработке глухих отверстий следует применять инструменты для обработки сквозных отверстий (эскиз б и г), предусматривая в чертежах участок f (эскиз е) нерабочей части отверстия (переходной поверхности).
Кроме того, при проектировании изделия следует учитывать (особенно при прессовых соединениях деталей), что при изготовлении отверстий развертками для глухих отверстий диаметр последних у входа на некоторой длине (3–6 мм, в зависимости от диаметра отверстия) выходит из заданных допусков, это отклонение необходимо предусматривать чертежом.
Рис. 2.79. Конфигурация поверхности, полученная при сверлении (а), растачивании зенкером (б), зенкером глухих отверстий (в), развертывании разверткой сквозных (г) и глухих отверстий (д).
При проектировании точных глухих отверстий (6, 7, 9-го квалитета точности) с высоким классом шероховатости необходимо предусматривать у дна отверстия переходной уступ (рис. 2.80, а) или кольцевую ка-
63
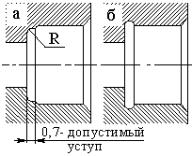
навку для выхода инструмента (рис. 2.80, б). При наличии переходного уступа в чертеже следует указывать: «Допускается уступ не более 0,7 мм».
Если отверстия предварительно обрабатываются на сверлильных, фрезерных, расточных или агрегатных станках, т. е. деталь в процессе обработки не вращается, то канавки у дна отверстия делать не следует, т. к. ее получение в этом случае связано с применением дорогостоящей оснастки или совсем невозможно.
Рис. 2.80. Выполнение переходного уступа (а) и кольцевой канавки для растачивания точного глухого отверстия
Точные отверстия с поверхностью высокого класса шероховатости обрабатывают тонким растачиванием, шлифованием и хонингованием. Для выполнения этих операций наиболее удобными являются отверстия диаметром d свыше 18 мм при отношении l/d ≈ 0,5–1,0 (большие значения для меньших диаметров). Под хонингование не следует предусматривать отверстия диаметром менее 20 мм.
При обработке глухих отверстий хонингованием выполняются выточки шириной 0,5–1,0 d (меньшие значения для больших диаметров). Если такие выточки не могут быть предусмотрены по условиям конструкций, то следует применять у дна отверстия рассмотренные выше канавки (рис. 2.80, б). В этом случае хонингование нельзя проводить на всей длине глухого отверстия. Следует оговаривать в чертеже длину хонингования l (рис. 2.81).
64

Рис. 2.81. Указание на чертеже детали длины хонингования
При проектировании отверстий следует предусматривать возможность их обработки нормализованными осевыми режущими инструментами (сверлами, зенкерами, развертками). Не рекомендуется проектировать поперечные отверстия, выходящие в обрабатываемую зону точного отверстия. В этом случае необходим вывод отверстия во внутреннюю кольцевую канавку (рис. 2.82).
Рис. 2.82. Поперечное отверстие, пересекающее классное отверстие, с выходом в канавку
При обработке отверстий должен быть предусмотрен свободный доступ для ввода режущего инструмента. Располагать отверстия относительно других поверхностей детали следует так, чтобы инструмент имел свободный подход. При проектировании отверстий в ребрах глухих карманов, что весьма нежелательно, отверстия должны располагаться на высоте не менее 12 мм (для отверстий не свыше 5 мм) от внутренней плоскости стенки (рис. 2.83).
65
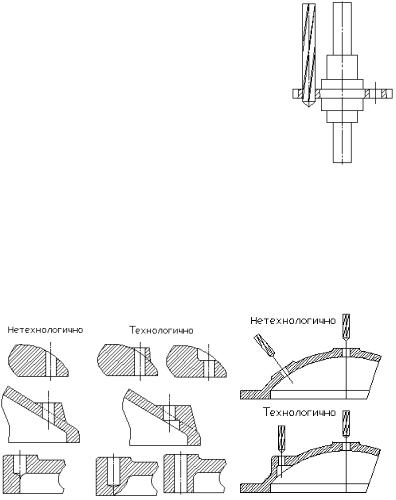
Рис. 2.83. Размещение отверстий в ребрах глухих карманов
Рис. 2.83 a. Обеспечение доступа для ввода осевого инструмента Ö
Не рекомендуется располагать оси отверстий под углом к поверхности детали (рис. 2.84). При таком расположении отверстий на режущий инструмент действуют односторонние усилия резания, снижающие точность и шероховатость обработки поверхности. Инструмент малых диаметров при этом подвержен частой поломке. Без специальной оснастки (кондуктора) такие отверстия обрабатывать нельзя.
Рис. 2.84. Вход и выход осевого инструмента под углом к поверхности детали
Выполнение выточек в деталях на сверлильных, расточных, фрезерных и агрегатных станках очень затруднительно и требует применения специальной малопроизводительной оснастки. В ряде случаев этого можно избежать введением разрыва в детали (рис. 2.85, а). В литых деталях следует применять необрабатываемые выточки (рис. 2.85, б). В глухих отверстиях выточку выполнять в заготовках до сварки детали (рис. 2.85, в). По возможности применения механически обрабатываемых выточек следует избегать.
66

Рис. 2.85. Примеры оформления выточек в отверстиях
Конструкция ступенчатых отверстий должна допускать обработку их с одной стороны. Обработка ступенчатых отверстий диаметром, уменьшающимся к середине детали, с обеих сторон (рис. 2.85, г) обычно требует расчленения обработки на операции. Обработка отверстия за две установки приводит к увеличению отклонения отверстия от соосности. На рис. 2.85, д показаны отверстия, изготовляемые за одну операцию, с диаметрами ступеней, убывающими в одном направлении. В этом случае обеспечивается наивысшая, практически достижимая точность по соосности отверстий и сокращается вспомогательное время.
Необходимо избегать по возможности применения конических отверстий, особенно больших диаметров. Обработка таких отверстий связана с применением специальной оснастки.
Классные отверстия должны иметь нормальные диаметры в соответствии с ГОСТом (рис. 2.86). Отклонения от ГОСТа ведут к применению специального режущего и измерительного инструмента.
В центровых отверстиях следует предусматривать предохранительную фаску во избежание их повреждения при последующей механической обработке (рис. 2.87).
Рис. 2.86. Назначение диаметров отверстий |
Рис. 2.87. Предохранительная |
из предпочтительного ряда |
фаска на центровом отверстии |
Цекование торца, где это возможно, следует заменять обточкой или фрезерованием (рис. 2.88), избегать цекования поверхностей, закрытых для доступа инструмента другими поверхностями.
67
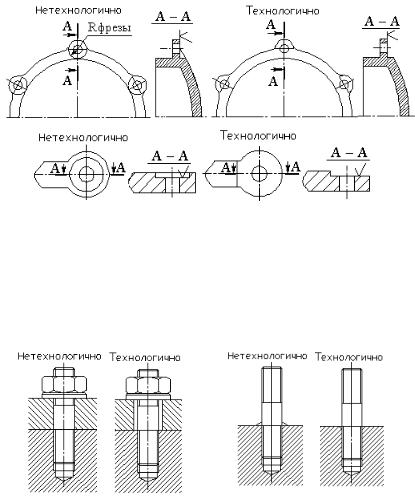
Рис. 2.88. Возможные варианты замены цековки обточкой и фрезерованием
В связи со сборкой к конструкции отверстий предъявляется ряд дополнительных технологических требований.
Отверстия под шпильки (нерабочую их часть) необходимо проектировать с зазором по отношению к телу шпильки (рис. 2.89).
Во избежание выпучивания материала у кромок отверстия при завертывании шпилек рекомендуется на выходе отверстия предусматривать фаску (рис. 2.90).
Рис. 2.89. Выполнение зазора |
Рис. 2.90. Оформление резьбового |
в отверситях под шпильки |
отверстия под шпильку и болт фаской, |
|
предотвращающей выпучивание мате- |
|
риала |
При сборке деталь не должна одновременно садиться по нескольким поверхностям. Если деталь имеет ступенчатые или конические отверстия, только одно из них должно быть сопрягаемой поверхностью. Не допускается посадка сопрягаемых деталей по нескольким поверхностям (рис. 2.91). При неподвижных посадках по нескольким
68

концентричным поверхностям посадочные места должны быть ступенчатыми во избежание задиров при монтаже (рис. 2.92).
а
Рис. 2.91. Пример посадки сопрягаемых деталей
б
Рис. 2.92. Посадка на ступенчатые концентрические отверстия, предотвращающая задиры при монтаже
Следует по возможности уменьшать диаметр центрирующих кольцевых выточек у крупногабаритных деталей в целях более точной посадки, защиты посадочных мест от повреждения и компактности узла
(рис. 2.93).
Рис. 2.93. Уменьшение диаметра центрирующих кольцевых выточек, улучшающее технологичность сборки узла
Резьба и резьбовые соединения Наружная резьба
При серийном производстве изготовление наружной резьбы производится накатыванием (если позволяют габаритные размеры и кон-
69

фигурация детали); фрезерованием (кроме деталей, термически обработанных на прочность σв≥1100 МПа); нарезанием резцом или гребенками. Наихудшим в отношении качества резьбовой поверхности является изготовление резьбы нарезанием круглыми плашками (лерками). Шлифование резьбы представляет собой весьма трудоемкую операцию, которую следует по возможности избегать, заменяя шлифование накатыванием.
На наружных резьбовых поверхностях рекомендуется предусматривать заходную фаску с углом 450, которая обеспечивает благоприятные условия для работы резьбообразующего инструмента и способствует предохранению начальной нитки резьбы от механических повреждений. Ширина фаски должна равняться шагу нарезаемой резьбы.
Рис. 2.94. Часто встречающиеся конструкции наружных резьбовых поверхностей
Проточка канавок (рис. 2.94, а, б) на деталях с наружной резьбой является дополнительной технологической операцией и должна предусматриваться в чертеже при нарезании резьбы резцом и шлифовальным кругом; при нарезании резьбы на деталях из высокопрочных легированных сталей типа 40ХНМА, 30ХГСНА с последующей термообработкой и калибровкой. При изготовлении резьбы фрезерованием, нарезанием круглыми плашками и накатыванием целесообразно предусматривать сбег резьбы.
На рис. 2.94, в приведен вариант резьбы, где вместо канавки предусмотрен сбег. Вариант наиболее технологичного изготовления резьбы способом накатывания, исключающим редуцирование стержня перед накатыванием, приведен на рис. 2.94, г. Средний диаметр резьбы примерно равен диаметру стержня.
Шлифуемые диаметры должны быть больше диаметра резьбы. Это позволяет производить шлифование более производительными мето-
дами (рис. 2.95).
70