
- •Стали
- •Магниевые сплавы
- •Титановые сплавы
- •Алюминиевые сплавы
- •2.1. Технологичность заготовок
- •Горячештампованные заготовки
- •Литые заготовки
- •Простановка размеров
- •Технологичность основных элементов конструкции деталей
- •Открытые плоскости
- •Сопрягаемые плоскости (колодцы, карманы, пазы, гнезда)
- •Наружные поверхности вращения
- •Внутренняя резьба
- •Фасонные поверхности
- •Монолитные панели
- •Панели, изготовляемые из плит
- •Панели из горячештампованных заготовок
- •Панели из горячепрессованных заготовок
- •Панели из специального литья
- •Крупногабаритные детали из алюминиевых и магниевых сплавов
- •Балки и лонжероны
- •Детали узлов поворота
- •Шпангоуты, рамы и их детали
- •Длинномерные детали из прессованных профилей
- •Фитинги и кронштейны
- •Рычаги и качалки
- •Фланцы и крышки
- •ЛИТЕРАТУРА

Рис. 2.95. Диаметр резьбы на шейке детали |
|
||
На деталях, |
термически |
обработанных на прочность |
свыше |
σв = 1100 МПа, |
рекомендуется |
применять изотермическую |
светлую |
калку, исключающую операцию калибрования резьбы после термообработки.
Внутренняя резьба
При серийном производстве внутренние резьбы на материалах, термически обработанных на прочность не выше σв = 1100 МПа, рекомендуется изготовлять нарезанием метчиками (наиболее производительный способ) и гребенками, фрезерованием, а также нарезанием резцами на материалах, термически обработанных на прочность свыше σв = 1100 МПа. Резьбошлифование шлифовальными кругами является наиболее трудоемким способом.
Фрезерование и нарезание гребенками и резцами внутренней резьбы выполнимо при номинальном размере резьбы от 16 мм и выше. Нарезание метчиками по целому материалу рекомендуется производить до 30–33 мм номинального размера резьбы, большие диаметры желательно изготовлять предварительно резцом, а затем калибровать метчиком.
Диапазон размеров внутренней резьбы, изготовляемой шлифованием, ограничивается существующим оборудованием. Шлифование для незакаленных деталей обычно не предусматривается.
Рис. 2.96. Часто встречающиеся конструкции внутренних резьбовых поверхностей
На рис. 2.96 показаны наиболее часто применяемые в конструк-
71
циях внутренние резьбовые поверхности (отверстия).
На внутренних резьбовых поверхностях рекомендуется предусматривать заходную фаску, создающую благоприятные условия для работы режущего инструмента.
В резьбовых отверстиях с несквозной резьбой, нарезаемой метчиком или фрезой, следует предусматривать сбег резьбы (рис. 2.96, а). Отверстие под резьбу должно быть по возможности большой глубины, а при коротких изделиях – сквозным.
При изготовлении резьбы резцом, гребенкой или шлифовальным кругом в глухих резьбовых отверстиях (диаметром от 12 мм и выше) предусматриваются канавки (проточки) для выхода режущего инструмента (рис. 2.96, б, в).
Внутренние резьбы изготавливают по возможности сквозными. На рис. 2.96, г показан наиболее технологичный вариант изготовления резьбового отверстия.
Длинных внутренних резьб следует избегать. Длина резьбы не должна превышать 1,5–2 D (D – наружный диаметр резьбы). В глубоких отверстиях рекомендуется резьбу делать не длиннее 1,5–2 D, рассверливая остальную часть отверстия сверлом большего диаметра
(рис. 2.96, д).
Не следует применять резьбы с номинальным диаметром менее 6 мм вследствие частой поломки метчиков при нарезании таких резьб.
На деталях, термически обработанных на прочность свыше σв = 1100 МПа, внутреннюю резьбу по возможности нарезать до термообработки с последующим калиброванием после термообработки. Это вызывается причинами как технологического характера (трудностью изготовления резьбы), так и прочностного.
Необходимо унифицировать размеры применяемых резьб по изделию в целом для уменьшения номенклатуры режущего и измерительного инструмента.
Фасонные поверхности
Фасонные поверхности тел вращения в большинстве случаев изготовляются на универсальных токарных станках профилированными резцами или на танках с ЧПУ. При изготовлении фасонными резцами точность профиля и шероховатость поверхности зависят от точности и шероховатости режущих кромок инструмента, жесткости детали и состояния станка.
Для обеспечения благоприятных условий работы режущего инструмента углы α между осью вращения детали и касательной к образующей профиля не должны превышать 800 (рис. 2.97, а).
При изготовлении фасонных поверхностей по копирам на точность обработки и шероховатость поверхности кроме точности копира влия-
72
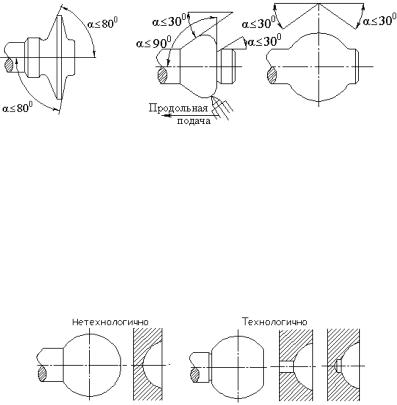
ет также инерционность копировальной системы. Поэтому шероховатость обрабатываемой фасонной поверхности и точность обработки при изготовлении по копирам не превышают шероховатость и точность при изготовлении фасонным инструментом.
Длина обрабатываемой фасонной поверхности практически ограничивается возможностями станка и устройством копировальной системы. Усилия резания примерно равны усилиям, возникающим при обработке детали обычным проходным резцом.
При обработке по копиру углы α между осью вращения детали и касательной к образующей профиля не должны превышать величин, указанных на рис. 2.97, б. Углы α во всех случаях рекомендуется уменьшать.
а |
б |
в |
Рис. 2.97. Допускаемые углы между осью вращения детали и касательной к образующей профиля при обработке на токарном станке (а), копировальном с гидравлической (б) и механической (в) системами копирования
Наружные и внутренние сферические поверхности не должны быть сплошными. Для улучшения технологичности торец детали оставлять плоским. Кроме того, желательно предусматривать переходную проточку (рис. 2.98). Сплошная внутренняя сферическая поверхность нетехнологична. Для улучшения технологичности в детали рекомендуется предусматривать центральное отверстие или засверловку.
Рис. 2.98. Исполнение сферических поверхностей
Механически обрабатываемые фасонные поверхности следует четко отделять от других поверхностей. Для обработки галтели, сливаю-
73
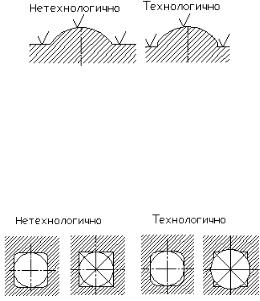
щейся с другой поверхностью, фрезу приходится устанавливать для каждой детали в зависимости от фактического размера заготовки с последующей слесарной доработкой. Изменение формы выступа устраняет этот недостаток, улучшает технологичность детали и позволяет производить обработку детали по настроенному процессу (рис. 2.99).
Рис. 2.99. Отделение фасонной поверхности от других поверхностей улучшает технологичность ее изготовления
Фасонные отверстия должны иметь симметричный профиль. Наиболее производительным методом получения таких отверстий является протягивание. Желательно, чтобы для облегчения работы протяжки профиль был максимально образован окружностью (рис. 2.100). В профильных отверстиях не должны применяться внутренние выточки, т. к. это приводит к поломке инструментов.
Рис. 2.100. Максимальное приближение профиля протягиваемого отверстия к окружности, улучшающее технологичность обработки фасонного отверстия
2.3. Технологичность основных классов деталей авиационной техники
В число основных классов механически обрабатываемых деталей вертолетов относятся: монолитные панели, крупногабаритные детали из магниевых сплавов, балки и лонжероны, монорельсы, узлы поворота, шпангоуты и рамы, длинномерные детали из прессованных профилей, профили разъема, фитинги и кронштейны, рычаги и качалки, фланцы и крышки.
Обработка крупногабаритных деталей на металлорежущих станках является наиболее трудоемким процессом, требующим особо сложных средств технологического оснащения. Основными факторами, способствующими снижению трудоемкости изготовления таких деталей, является повышение технологичности геометрических форм обрабатываемых поверхностей, правильное назначение точности и шероховатости обработки, снижение объема механической обработки. Поэтому
74