
Б.И. Коган Определение экономической эффективности гибкого автоматизированного участка
.pdfМИНИСТЕРСТВО ОБРАЗОВАНИЯ РОССИЙСКОЙ ФЕДЕРАЦИИ
Государственное учреждение Кузбасский государственный технический университет
Кафедра технологии машиностроения
Кафедра экономики и организации машиностроительной промышленности
ОПРЕДЕЛЕНИЕ ЭКОНОМИЧЕСКОЙ ЭФФЕКТИВНОСТИ ГИБКОГО АВТОМАТИЗИРОВАННОГО УЧАСТКА
Методические указания по курсу «Проектирование производственных и ремонтных участков механосборочных цехов машиностроительных заводов» для студентов специальности 120100 «Технология машиностроения»
Составители Б. И. Коган Н. М. Тренихина
Утверждено на заседании кафедры Протокол № 9 от 18.04.02 Рекомендовано к печати учебнометодической комиссией специальности 120100 Протокол № 6 от 19.04.02 Электронная копия находится
в библиотеке главного корпуса ГУ КузГТУ
Кемерово 2002
1
Введение
Методические указания определяют сущность, содержание и последовательность работы студентов при экономической оценке эффективности создания гибкого автоматизированного участка механической обработки деталей в период дипломного проектирования. Они базируются на отечественном опыте [1].
1. Факторы эффективности гибких автоматизированных участков (ГАУ)
Прямой экономический эффект образуется на производственном участке, где внедряется ГАУ, по сравнению как со станками с ЧПУ, так и со станками с ручным управлением (РУ), за счет: увеличения коэффициента загрузки оборудования вследствие улучшения организации производства, что позволяет значительно сократить простои оборудования по организационным причинам путем введения средств диагностирования, автоматизации транспортных и погрузочно-разгрузочных работ, оптимизации планирования, упорядочения учета и диспетчирования; трехсменного режима работы ГАУ, состоящего из гибких производственных модулей (ГПМ), вместо двухсменного режима традиционного оборудования; сокращения длительности производственного цикла вследствие концентрации операций, сокращения времени межоперационного пролеживания.
Для работы в третью смену ГПМ, как минимум должен иметь уровень, обеспечивающий выполнение следующих функций: автоматическую загрузку-разгрузку деталей с применением накопителя деталей; автоматическую смену инструмента; автоматическое закрепление детали или приспособления с деталью; автоматическое удаление отходов (стружки); защиту рабочей зоны и принудительную ее очистку, аварийную защиту по предельным параметрам. Это позволяет работать во вторую и третью смены ограниченному количеству персонала при увеличении зоны обслуживания.
По сравнению с универсальными станками с РУ применение ГАУ способствует снижению станкоемкости обработки деталей в 2 раза и более за счет концентрации операции, сокращения вспомогательного времени на установку и снятие деталей и на холостые перемещения, уменьшения основного времени за счет оптимизации режимов обработки; уменьшению брака за счет устранения ошибок и нарушений технологических режимов, неизбежных при ручном труде; улучшению усло-
2
вий труда; устранению трудоемких и тяжелых операций, освобождению человека от малоквалифицированного и монотонного труда.
В отличие от станков с ЧПУ, работающих автономно, ГАУ способствует уменьшению времени переналадки путем автоматизации хранения, поиска и выдачи управляющих программ, ускорению обработки технологического процесса с помощью системы редактирования, автоматического обеспечения всех рабочих мест заготовками и оснасткой в необходимые моменты времени; а также уменьшению цикла обработки деталей в случае применения в составе ГАУ нового оборудования с ЧПУ с улучшенными техническими характеристиками по сравнению с освоенным в производстве оборудованием с ЧПУ базового варианта.
Действие указанных выше факторов приводит к тому, что в ГАУ, по сравнению с действующим производством, сокращаются количество единиц оборудования, необходимого для выполнения заданной программы выпуска, численность обслуживающего персонала, потребность в производственных площадях. В результате увеличивается съем продукции на единицу оборудования и на одного работающего (растет производительность оборудования и производительность труда), снижается себестоимость продукции.
По отношению к ГАУ такой традиционный показатель, как производительность оборудования, должен учитывать следующие моменты: повышение производительности по сравнению с оборудованием, работающим в две смены, за счет введения третьей смены в условиях малолюдной технологии; повышение коэффициента использования оборудования. Организационные факторы производства, которые не могут быть выражены через показатель производительности оборудования, но влияют на конечный результат, перечислены ниже.
1.Гибкость металлообрабатывающего оборудования, обеспечивающая резкое сокращение затрат по оснастке и сокращение цикла изготовления изделий, включая предпроизводственные затраты: внедрение новых изделий машиностроения с более высокими техникоэкономическими показателями, экономию капитальных вложений и сокращение оборотных средств в незавершенном производстве при комплексном внедрении ГАУ.
2.Повышение качества продукции за счет автоматизации, правильности получения формы деталей (изделий) и точности размеров обрабатываемых деталей, не требующих высокой квалификации рабочих.
3.Увеличение фондоотдачи, снижение фондоемкости за счет повышения коэффициента сменности автоматизированного оборудования,
3
сокращения производственных затрат и экономии оборотных средств в незавершенном производстве.
К социальным факторам относят: улучшение условий труда, предупреждение несчастных случаев и травматизма на производстве.
По данным иностранных фирм, в большинстве случаев ГАУ позволяет снизить время на подготовку выпуска новой продукции на 40%, увеличить загрузку оборудования на 30%, уменьшить удельные затраты на выпуск продукции на 10%, а потребности в рабочей силе – на 30%.
Высокий уровень автоматизации требует больших капитальных вложений, которые оправданы только в том случае, если обеспечено интенсивное использование автоматизированного оборудования. Поэтому, с одной стороны, непроизводительное время нужно довести до минимума, с другой стороны, есть необходимость в том, чтобы такое оборудование работало в несколько смен, но должны быть созданы условия для выведения человека из непосредственного процесса производства.
Перечисленные преимущества ГАУ учитываются в затратах на производство и использование ГАУ.
Суммарные интегральные затраты на разработку, производство и использование ГАУ определяются как сумма затрат на производство ЗТП и использованиеЗТИ :
(1)
При этом, если сметная стоимость ГАУ учтена в сфере производства, ее не учитывают в сфере эксплуатации при расчетеЗТИ . Суммы затрат на
производство и использование определяются следующим образом:
З |
= И |
t |
+ К |
t |
+ К1 |
+V E |
, |
(2) |
ТИ(ТП) |
|
|
t |
V |
|
|
||
где Иt − суммарные |
эксплуатационные издержки (без реновации на |
|||||||
полное восстановление) |
|
у потребителя |
при |
использовании ГАУ; |
Kt − суммарные капитальные вложения на создание ГАУ, равные его
сметной стоимости, включающие стоимость основного оборудования, транспортно-накопительной системы, управляющего вычислительного
комплекса, оснастки; Кt1 − сопутствующие капитальные вложения; V – основная заработная плата промышленно-производственного персонала; EV − норматив эффективности трудовых ресурсов.
В состав эксплуатационных издержек Иt, рассчитанных на годовой объем продукции деталей, обрабатываемых на ГАУ, включают затраты на все виды ремонта: заработную плату работающих; амортизацию служебно-бытовых площадей; расход режущего и вспомогательного ин-
4
струмента, средств контроля и диагностики стоимостью до 1000 р. за единицу; расходы на подготовку управляющих программ; обслуживание средств вычислительной техники; расходы на силовую электроэнергию, прочие расходы.
Всостав сопутствующих капитальных вложений входят стоимости производственных площадей служебно-бытовых помещений, оборотных средств в незавершенном производстве, оснастки.
Вметодике интегральной оценки статьи, учитывающие амортизационные отчисления, входят только в часть затрат на ремонт, исключая затраты на реновацию.
2. Особенности методики оценки производительности оборудования ГАУ
Производительность определяется не только технологическими возможностями оборудования, но и условиями его эксплуатации, т.е. уровнем подготовки и организации производства, технологической оснащенности и квалификации обслуживающего персонала, в том числе ремонтного.
Производственный процесс на ГАУ включает следующие этапы, характеризующиеся определенным временем Т и затратами: предварительную подготовку производства; текущую подготовку производства; процесс обработки; контроль обработанной партии деталей; доработку деталей; устранение отказов в работе оборудования; плановый ремонт оборудования; операции, связанные с транспортированием и хранением деталей в незавершенном производстве.
Предварительная подготовка производства выполняется общезаводскими службами, и затраты на нее входят в общезаводские расходы. Однако, если предварительная подготовка выполняется несвоевременно или на недостаточном техническом уровне, то это вызывает следующие негативные явления в производственном процессе: невозможность доработки определенной партии деталей; простои высокопроизводительного оборудования по организационным причинам, составляющие 3040 % общего фонда времени; изготовление деталей недостаточного количества или неполностью обработанных; дополнительные отказы оборудования из-за нестабильности технологического процесса. Такая подготовка производства осуществляется непосредственно в цехе на технологическом оборудовании и повторяется для каждой новой партии деталей.
5
Для традиционного производства в расчет закладывалась потенциальная производительность металлообрабатывающего оборудования (МОО), определяемая его технологическими возможностями, которая была значительно выше фактической, так как не учитывала потери по организационно-техническим причинам в условиях серийного производства. Основными причинами малопроизводительной работы МОО являются потери времени, связанные с отсутствием рабочих (целосменные простои), отсутствием заготовок, частые переналадки и ожидания обработки партий других деталей, проходящих те же операции, отказы оборудования (внутрисменные простои).
Основными факторами, обеспечивающими рост производительности принципиально нового МОО, являются: концентрация операции на одном рабочем месте, повышение уровня автоматизации загрузки, автоматизация уборки стружки или ее удаление в процессе резания, автоматический контроль и диагностирование, что в совокупности обеспечивает возможности работы в три смены, в том числе в условиях малолюдной технологии во вторую и третью смены.
При этом удалось поднять загрузку оборудования для автоматизированного участка из ГПМ до 77 % против 47-63% для автономно работающих на участках ГПМ. В первую очередь это произошло за счет сокращения простоев из-за отсутствия заготовок, инструмента, другой оснастки, управляющих программ при полной ликвидации простоев оборудования из-за отсутствия рабочих. Сравнительный анализ использования ГПМ (по фактическим данным производства), работающих автономно и в составе ГАУ, показан в табл. 1.
Для предварительных расчетов эффективности ГАУ рекомендуется применять коэффициенты использования оборудования, приведенные в табл. 2.
Загрузка ГПМ, % |
Таблица 1 |
||
|
|
||
|
|
|
|
Элементы затрат времени |
Автономно |
В составе |
|
|
работающие |
ГАУ |
|
Оперативное время |
63 |
77 |
|
Наладка |
5,0 |
3,15 |
|
|
|
|
|
Все простои |
32 |
19,85 |
|

6
Продолжение табл. 1
Элементы затрат времени |
|
|
Автономно |
|
В составе |
|
||||
|
|
|
работающие |
|
|
ГАУ |
|
|||
из них по техническим причинам |
|
16,2 |
|
|
|
17,5 |
|
|
||
|
|
|
|
|
|
|
|
|
|
|
в том числе: |
|
|
|
|
|
|
|
|
|
|
|
|
|
|
|
|
|
|
|
|
|
электрической части |
|
3,8 |
|
|
|
8,2 |
|
|
||
|
|
|
|
|
|
|
|
|
|
|
механической части |
|
12,4 |
|
|
|
9,3 |
|
|
||
|
|
|
|
|
|
|
|
|
|
|
Отсутствие рабочего |
|
|
10 |
|
|
|
- |
|
|
|
|
|
|
|
|
|
|
|
|
|
|
прочие |
|
|
6,2 |
|
|
|
2,35 |
|
|
|
|
|
|
|
|
|
|
|
|
|
|
|
|
|
|
|
|
|
|
Таблица 2 |
||
Коэффициенты использования оборудования и ГАУ1 |
||||||||||
|
Простои, в % от эффек- |
Коэффициент использования |
|
|
||||||
|
органипозационным причинам |
|
технипоческим причинам |
итого |
|
|
||||
|
тивного фонда времени |
|
|
|
||||||
Тип оборудования |
|
|
|
|
|
|
|
|
|
|
|
|
|
|
|
|
|
|
|||
Универсальный станок с РУ |
37-47 |
|
3 |
40-50 |
0,5-0,8 |
|
|
|||
Станок с ЧПУ |
29 |
|
|
11 |
40 |
|
0,6 |
|
|
|
ГПМ (без автоматической на- |
18 |
|
|
12 |
30 |
|
0,7 |
|
|
|
ладки) |
|
|
|
|
|
|
|
|
|
|
Гибкая автоматизированная ли- |
0 |
|
|
14 |
20 |
|
0,8 |
|
|
|
ния (ГАЛ) |
|
|
|
|
|
|
|
|
|
|
В отличие от разработанных ранее методик по автоматизированному оборудованию в методике ЭНИМСа (см. табл. 2) имеются новые подходы к оценке суточной производительности ГПМ как основной ячейки ГАУ, работающей в трехсменном режиме работы.
Так как в условиях малолюдной технологии модуль должен работать без переналадки не менее суток и каждые сутки должна производиться подготовка его к работе, за основной базовый отрезок времени при расчетах производительности ГПМ принят выпуск за сутки.
1 Приняты по отраслевой методике экономической эффективности ГПС и других видов автоматизированного оборудования, разработанных в ЭНИМСе.
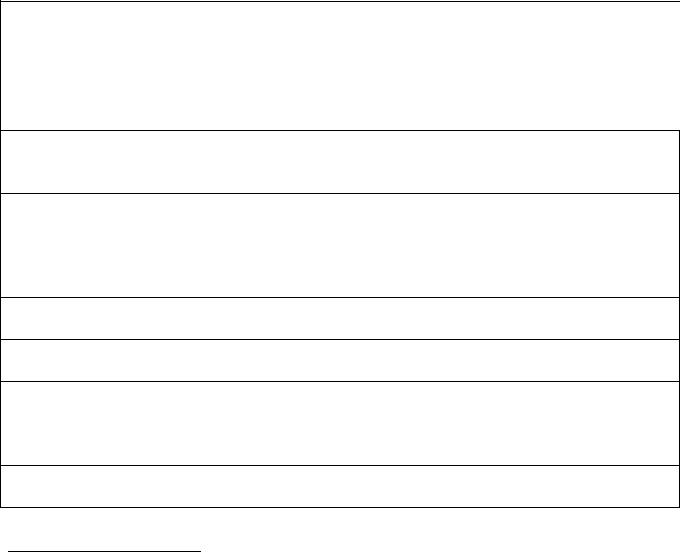
7
Рост производительности рассчитывается как общий коэффициент роста суточной (годовой) производительности ГПМ за счет сокращения штучного времени и повышения сменности его работы по сравнению с оборудованием базового варианта по формуле
β = (В |
2 |
′ / В ′) /(δ |
2 |
/ δ |
1 |
), |
(3) |
|
1 |
|
|
|
где δ1 , δ2 − коэффициенты использования базового и нового оборудо-
вания; В1′, В2′ − выпуск деталей (изделий) за сутки с помощью базового и нового оборудования. Расчет этих и других данных приведен в табл. 3
Таблица 3
Расчет производительности ГПМ
Показатель
1.Эффективный фонд времени работы оборудования, ч/сут
2.Расчетный фонд времени работы оборудования (фонд штучно-калькуляци- онного времени), ч
3.Цикловое время на одну деталь, ч
3.1.Вспомогательное время смены
3.2.Обслуживание рабочего места, личные надобности, отдых
Итого штучное время, ч
|
Станок с ЧПУ |
|
|
ГПМ |
|
|
||
на одну деталь |
на партию деталей |
25 шт. |
в сутки |
за год работы станка |
на одну деталь |
в сутки |
за год работы станка |
|
- |
- |
|
14,8 |
38501 |
- |
21 |
57152 |
|
|
|
|||||||
|
|
|
(3850: |
|
|
(5715:27 |
|
|
|
|
|
:260) |
|
|
1) |
|
|
- |
- |
|
12,59 |
3272 |
- |
17,9 |
4858 |
|
|
|
|
(3272: |
(3850× |
|
(4858: |
(5715× |
|
|
|
|
:260) |
×0,83) |
|
:271) |
×0,85) |
|
2,5 |
62,5 |
|
11,7 |
3042 |
2,15 |
14,5 |
3929 |
|
0,024 |
0,6 |
|
0,1 |
26,2 |
0,024 |
0,18 |
48,78 |
|
0,3 |
- |
|
- |
- |
- |
- |
- |
|
2,82 |
70,6 |
|
11,8 |
3068 |
2,17 |
13,9 |
3977 |
|
|
|
|
|
|
|
(17,9-4) |
|
|
1Фонд времени ГПМ при трехсменном режиме – 271 день в год.
2Фонд времени станка с ЧПУ – 250 дней в году.
30,85 – коэффициент загрузки ГПМ и станка с ЧПУ, работающего автономно (15% простоев по оргпричинам).
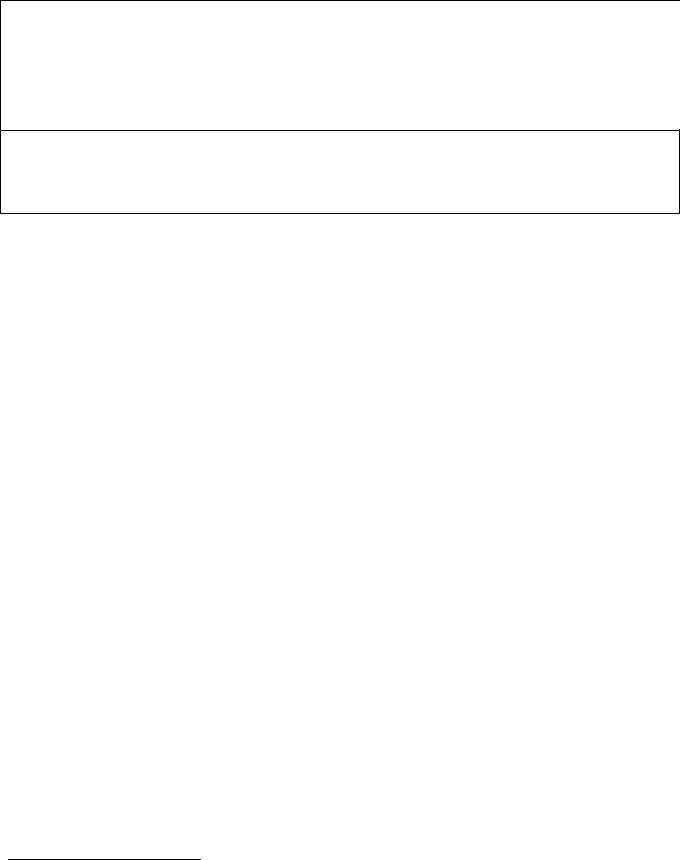
Показатель
4.Наладка станка, ч
втом числе установка инстру-
мента в магазине
1
8
Продолжение табл. 3
|
Станок с ЧПУ |
|
|
ГПМ |
|
|
||
на одну деталь |
на партию деталей |
25 шт. |
в сутки |
за год работы станка |
на одну деталь |
в сутки |
за год работы станка |
|
0,19 |
4,83 |
|
0,79 |
205,4 |
0,60 |
4,0 |
1040 |
|
|
|
|||||||
|
|
|
|
|
(4:6,4) |
|
|
|
- |
0,33 |
|
- |
- |
- |
(30:4): |
- |
|
|
|
|
|
|
|
:0,12 |
|
|
Для ГПМ
В2 = |
ТШ |
2 |
, |
(4) |
|
tШ2 |
|||||
|
|
|
где В2 − годовой выпуск деталей (изделий) за 2712день в году для ГПМ; ТШ2 – суточный фонд штучного времени, мин; tШ2 – штучное
время обработки детали на ГПМ, мин.
Суточный фонд штучного времени рассчитывается по формуле
Т |
Ш |
= Ф |
|
−t |
2 |
− |
tн |
, |
(5) |
|
|
||||||||
|
СУТ |
2 |
|
|
F |
|
|
||
|
1 |
|
|
|
|
|
|
||
|
|
|
|
|
|
|
|
|
где ФСУТ2 – расчетный суточный фонд штучно-калькуляционного времени ГПМ, мин; t2 – время на подготовку к работе во вторую и третью
смены и другие элементы, выполняемые ежедневно в начале первой смены, мин; tн – время наладки на партию, включающее установку ин-
струмента в магазине, установку программоносителя из нулевого положения, время пробной обработки деталей, мин; F – продолжительность обработки партии деталей (в сутках), определяемая исходя из типа производства (количество переналадок в месяц).
Рост производительности ГПМ по сравнению с производительностью станка с ЧПУ составит В2 : В1 = 1734 : 1092 = 1,59. Могут быть два
способа функционирования ГПМ: 1) работа партиями, когда накопитель загружается деталями одного наименования, при этом партия запуска
2 Принято по методикам ЭНИМСа для оборудования, работающего в три смены – 271 день, в две смены – 260 дней.
9
должна быть такой, чтобы загрузить ГПМ на одни сутки или несколько суток; 2) работа сборочными комплектами.
При первом способе смена приспособлений и переналадка производятся после обработки партии деталей. Фактором, понижающим эффективность эксплуатации такого ГПМ, например ГПМ для корпусных деталей, по сравнению с многоцелевыми станками с ЧПУ, является то, что ГПМ должен иметь столько спутников, сколько потребуется для бесперебойной работы в течение хотя бы одной смены, в то время как для многоцелевого станка достаточно двух спутников. Указанное обстоятельство приводит к увеличению затрат времени на сборку приспособлений, так как на каждую партию нужно собрать для ГПМ столько приспособлений, сколько имеется спутников, а для многоцелевого станка только два.
Например, при штучном времени на деталь 60 минут, в составе ГПМ на рабочую смену должно быть как минимум 6-8 спутников. Указанное обстоятельство приводит к увеличению затрат времени на сборку приспособлений, так как на каждую партию нужно собрать для ГПМ столько приспособлений (6-8), сколько имеется спутников, а для многоцелевых станков – только два, поскольку при этом остается рабочий у станка.
При втором способе накопитель загружается комплектом деталей одного изделия, но разных наименований, которые обрабатываются в течение длительного времени (месяц, квартал, полугодие и т.д.), после чего осуществляются смена приспособлений и переход на обработку комплекта другого изделия. В этом случае ГПМ ежесуточно выдает на сборку комплект деталей.
Второй способ целесообразно применять в крупносерийном производстве (число различных операций, выполняемых в течение месяца на одном ГПМ, меньше 10) с ограниченной номенклатурой выпускаемых изделий и отработанной технологией. Преимущества второго способа состоят в уменьшении объема незавершенного производства, сокращении затрат на сборку приспособлений (за год), уменьшении времени на переналадку, а следовательно, увеличении роста производительности и загрузки оборудования.