
15_Truboprovody_i_armatura
.pdf410
15. ТРУБОПРОВОДЫ, АРМАТУРА И ГАРНИТУРА ПАРОВОГО КОТЛА
15.1.Трубопроводы паровых котлов
15.1.1.Классификация трубопроводов
Назначение трубопроводов, применяемых для энергетических устано- вок – транспортирование рабочей среды (воды, пара). По назначению и виду рабочей среди различают следующие виды трубопроводов: паропроводы, во- допроводы, маслопроводы и др. В зависимости от расположения по отноше- нию к оборудованию трубопроводы разделяются на внутренние (например, трубопроводы в пределах котла, теплообменника) и внешние (станционные трубопроводы). Внешние трубопроводы служат для соединения отдельных агрегатов в единый комплекс.
В соответствии с требованиями «Правил устройства и безопасной экс- плуатации трубопроводов пара и горячей воды» все трубопроводы, транс- портирующие водяной пар с рабочим давлением более 0,07 МПа или горя- чую воду с температурой выше 115 °С, делятся на четыре категории.
КI категории паропроводов относятся трубопроводы, выполненные из стали аустенитного класса и работающие при температуре пара 610–660 °С, а также из стали перлитного класса и при температуре пара 450–570 °С.
Ко II категории – паропроводы из углеродистой стали для пара давле- нием до 3 МПа и температурой 350–450 °С.
КIII категории – паропроводы из углеродистой стали марки 20 и 10 для пара давлением до 2 МПа.
КIV категории – трубопроводы из углеродистой стали 10 для давления 0,1–1,6 МПа. Аналогичное деление имеют и проводы для насыщенного пара
иводы.
Основные типы трубопроводов на тепловой электростанции – это глав- ные паропроводы от котлов к турбинам, трубопроводы питательной воды до деаэраторов к котлам, трубопроводы пара промежуточного перегрева. Для атомной электростанции – главные циркуляционные трубопроводы теплоно- сителя от реактора к парогенератору.
В зависимости от компоновки в установках применяются в основном две схемы паропроводов (рис. 15.1): схема с поперечной связью (рис. 15.1, а), включающая общий паропровод и отводы к каждому котлу (К) и турбине (Т), и блочная схема для системы котел – турбина (рис. 15.1, б).
Трубопроводы характеризуются двумя основными характеристиками:
условным проходом (условным диаметром) и условным давлением. Имеются стандарты на условные проходы, условные давления, а также на наружные диаметры труб и толщины стенок.
Условные проходы устанавливаются на диаметры прохода среды для трубопроводов и арматуры. При стандартах на наружный диаметр внутрен- ний диаметр трубы может быть разным в зависимости от толщины стенки.

411
Поэтому при расчетах внутренний диаметр подбирают ближайшим к услов- ному диаметру.
|
|
|
|
Условное |
|
|
|
давление связано |
|
||
|
|
с |
определенной |
||
|
|
предельно допус- |
|||
|
|
тимой |
температу- |
||
|
|
рой |
протекающей |
||
|
|
среды. |
Стандарт |
||
|
|
на условное дав- |
|||
|
|
ление |
устанавли- |
||
а) |
б) |
вает |
|
пробное |
и |
|
|
рабочее давление |
|||
Рис. 15.1. Принципиальные схемы паропроводов: а – секционная; |
для |
арматуры |
и |
||
б – блочная |
|
трубопроводов. |
В |
соответствии с ГОСТ все материалы разделены на несколько групп и для каждой группы в зависимости от рабочей температуры установлены темпе- ратурные ступени, в пределах которых дается количественная связь между рабочим, условным и пробным давлением. На пробное давление производит- ся испытание арматуры и трубопроводов на прочность.
15.1.2. Фасонные детали трубопроводов
При разветвлении трубопроводов, изменении их направления, а также при переходе от одного Диаметра трубопровода к другому используют фа-
сонные детали – отводы, тройники и переходы.
При сравнительно малых диаметрах ответвляемого трубопровода, а также в том случае, если толщина стенки основного трубопровода имеет большой запас прочности, ответвление осуществляется непосредственной врезкой трубы в трубу. Область и параметры применения деталей и элемен- тов трубопроводов определяются по ОСТ 34–42–481–80 ... ОСТ 34–42–500– 80.
Отводы – это изогнутые под углом 180; 90; 60; 45 и 30° участки трубо- проводов, изготовленные способами гнутья, сварки и штамповки. В зависи- мости от этих способов отводы подразделяются на гладкие и сварные (секци- онные).
Гладкие отводы бывают нормальные и крутоизогнутые.
Нормальные отводы (рис. 15.2, а) имеют радиус изгиба R , равный (3– 4,5) Dн , где Dн – наружный диаметр трубы. Длина прямого участка (от нача-
ла изгиба) должна быть не менее Dm трубы, но не менее 100 мм, а овальность в месте изгиба не превышать 10% от DH трубы. Эти отводы изготовляют спо- собом холодного или горячего гнутья.
Крутоизогнутые отводы (рис. 15.2, б) имеют радиус изгиба, величина которого не превышает одного наружного диаметра трубы. У таких отводов нет прямых участков, а скос кромки под сварку расположен в месте оконча-

412
ния изгиба. Это дает возможность применять крутоизогнутые отводы в тес- ных местах, и, кроме того, позволяет сократить расход труб для изготовления отводов.
|
|
|
Крутоизогнутые отводы из- |
||
|
|
|
готовляют способом |
горячей |
|
|
|
|
штамповки или протяжки и вы- |
||
|
|
|
пускают изогнутыми |
под углом |
|
|
|
|
180; 90; 60 и 45°. Отводы с углом |
||
а) |
б) |
в) |
изгиба 180° обычно называют ка- |
||
лачами. Размеры и масса крутои- |
|||||
Рис. 15.2. Отводы: а – нормальный. б – кру- |
|||||
тоизогнугый. в – сварной |
|
зогнутых отводов меньше, чем у |
|||
воды для трубопроводов с Dу |
|
нормальных. Крутоизогнутые от- |
|||
от 40 до 600 мм изготовляют в соответствии с |
ГОСТ 17375–83.
Сварные отводы (рис. 15.2, в) изготовляют из отдельных вырезанных из труб секций, которые затем сваривают. Радиус изгиба R этих отводов со- ставляет не менее 1,5 диаметра трубы. Сварные (секционные) отводы приме- няют для трубопроводов с Dу более 600 мм.
Тройники – детали с помощью которых устраивают разветвления тру- бопроводов равнопроходные (без изменения диаметра ответвления) и пере- ходные (с изменением диаметра ответвления).
По способу изготовления тройники бывают сварные (рис. 15.3, а) и штампованные (рис. 15.3, б). В отличие от сварных штампованные тройники благодаря бесшовному плавному сопряжению горловины с корпусом обла- дают более высокой прочностью. Штампованные тройники (ГОСТ 17376–83) изготовляют из углеродистой стали с Dу от 40 до 400 мм на Pу от 0,1 до 10
МПа.
Переходы, применяемые для изменения диаметра трубопровода, разде- ляют на штампованные и сварные.
а) |
в) |
|
|
|
|
|
|
|
|
|
|
|
|
|
|
|
|
|
|
|
|
|
|
|
|
|
|
|
|
|
|
|
|
|
|
|
|
|
|
|
|
|
|
|
|
|
|
|
|
|
|
|
|
|
|
|
|
|
|
|
|
|
|
|
|
|
|
|
|
|
|
|
|
а) |
|
|
|
|
|
б) |
|
|
|
|
|
|
|
|
|
|
|||||||
|
|
|
|
|
|
|
|
|
|
|
|
|
|
|
|||||||||
|
|
|
|
|
|
|
|
|
|
|
|
|
|
|
|||||||||
|
|
|
|
|
|
|
|
|
б) |
г) |
|||||||||||||
Рис. 15.3. Тройники: а – сварной; б – штампованный |
|
|
|
|
|||||||||||||||||||
|
Рис. 15.4. Переходы: I – |
штампо- |
|||||||||||||||||||||
|
|
|
|
|
|
|
|
|
|
|
|
|
|
|
ванные; II – сварные; а – концен- |
||||||||
|
|
|
|
|
|
|
|
|
|
|
|
|
|
|
трические; б – эксцентрический; в – |
||||||||
|
|
|
|
|
|
|
|
|
|
|
|
|
|
|
из трубы; г – из листа |
|

413
Штампованные переходы, которые могут быть концентрические (рис. 15.4, а) и эксцентрические (рис. 15.4, б), изготовляют из труб методами горя- чей штамповки в соответствии с ГОСТ 17378-83 и применяют в трубопрово- дах, рассчитанных на давление от 0,1 до 10 МПа и температуру транспорти- руемого вещества до 450 °С. Преимущества штампованных переходов – ма- лая длина, гладкая внутренняя поверхность, уменьшающая внутренние со- противления в трубопроводе, высокая точность размеров.
Сварные переходы (рис. 15.4, в) предназначенные для работы под дав- лением до 1,6 МПа при температуре до 200 °С. изготовляют из труб путем вырезки соответствующих клиньев и подгибки (в горячем состоянии) обра- зовавшихся на трубе лепестков до соприкосновения их один с другим. Для подгибки на лепестках снимают фаски. Сварные переходы изготовляют так- же из листового металла (рис. 15.4, г).
Фасонные детали для трубопроводов пара и горячей воды могут изго- товляться заводами, имеющими разрешение местных органов Ростехнадзора РФ. К каждой партии деталей для трубопроводов пара и горячей воды дол- жен быть приложен сертификат, в котором указываются параметры приме- нения деталей, механические свойства примененных материалов, а также разрешения Ростехнадзора РФ на изготовление данных деталей.
15.1.3. Соединение трубопроводов
Соединения трубопроводов бывают неразъемные и разъемные. К не- разъемным относятся соединения, получаемые путем сварки, пайки или склеивания, к разъемным – резьбовые, фланцевые, раструбные и др. В ко- тельных установках трубопроводы соединяют на резьбовых муфтах, фланцах и сварке.
Резьбовое соединение применяют во внутренних системах водопровода и газоснабжения котельной для трубопроводов с Dу до 100 мм и Pу до 1
МПа. Трубы соединяют резьбовыми муфтами на короткой и длинной резьбе. |
||
|
Короткая резьба (рис. 15.5, а) |
|
|
труб должна иметь сбег на участке |
|
а) |
двух последних ниток резьбы и ко- |
|
|
роче половины длины муфты на од- |
|
|
ну нитку резьбы. Благодаря сбегу |
|
|
одна резьба заклинивается в другой |
|
б) |
и плотность соединении повышает- |
|
ся. |
||
|
||
|
В тех случаях, когда необхо- |
|
|
димо создать разъемное соединение, |
|
|
применяют соединение на длинной |
|
Рис. 15.5. Соединение стальных труб на |
резьбе (рис. 15.5, б), для чего на од- |
|
муфте: а – с короткой резьбой; б – с длин- |
ной из труб делают длинную резьбу, |
|
ной резьбой |
а на другой – короткую. Такое со- |

414
единение принято называть сгоном. Длинную резьбу выполняют такой вели- чины, чтобы на нее можно было полностью навернуть (согнать) контргайку и муфту и сверх этого осталось бы еще не менее двух свободных ниток резьбы.
Для уплотнения стыков резьбовых соединений применяют льняную прядь с суриком, затертым на натуральной олифе, или со свинцовыми белилами. Прядь наматывают тонким ровным слоем на нарезку. Контргайка со стороны муфты имеет фаску для уплотнительного материала.
Фланцевые соединения – наиболее распространенный вид разъемных соединений трубопроводов, что объясняется простотой конструкции, легко- стью сборки и разборки, а также тем, что в котельных чаще всего используют фланцевую арматуру. Недостатки фланцевых соединений – большая трудо- емкость и высокая стоимость изготовления, а также меньшая по сравнению со сварными соединениями надежность в эксплуатации, так как при измене-
нии температуры и давления транспортируемой среды возможно ослабление соединения и возникновение утечки.
Фланцевые соединения состоят из двух фланцев, крепежных деталей (болтов или шпилек и гаек), прокладки или уплотнительного кольца.
|
|
Фланцы (ГОСТ 12815-80) по |
|
|
способу присоединения к трубам бы- |
|
|
вают плоские (рис. 15.6, а), которые |
|
|
привариваются угловым швом, и |
|
|
приварные встык (рис. 15.6, б) – во- |
а) |
б) |
ротниковые. Соединения с примене- |
Рис. 15.6. Приварные фланцы: а – плоские; |
нием воротниковых фланцев удобны |
|
б – воротниковые |
|
и экономичны. Трудоемкость сборки |
такого соединения в среднем на 20% меньше, чем сборка с использованием плоских фланцев. Кроме того, использование воротниковых фланцев сокра- щает объем сварочных работ в два раза.
Уплотнительные поверхности фланцев при рабочем давлении Pраб до 2,5 МПа выполняют гладкими, а при Pраб выше 2,5 МПа на уплотнительных
поверхностях протачивают риски (рис. 15.7, а), размеры и количество кото- рых зависят от диаметра трубопровода и давления в нем. Уплотнительные поверхности для фланцев с впадиной и выступом приведены на рис. 15.7, б.
Рис. 15.7. Уплотнительные поверхности фланцев: а – гладкая с рисками; б – выступ-
впадина
415
По форме фланцы бывают круглые и овальные. Наиболее распростране- ны круглые фланцы; овальные чаше всего применяют в местах подсоедине- ния трубопроводов к аппаратам и механизмам.
Крепежные детали – стандартные болты, шпильки и гайки – служат для сборки фланцевых соединений. Крепежные детали выбирают в зависимости от рабочих параметров среды и указывают в проекте.
Длину болтов и шпилек выбирают с таким расчетом, чтобы после за- тяжки гаек выступали концы не менее 5 мм.
Материал для изготовления крепежных деталей выбирают в зависимо- сти от давлении и температуры транспортируемого продукта: при PY до 2,5
МПа и температуре до 300 °С применяют малоуглеродистую сталь обыкно- венного качества Ст. 3, Ст. 4; при Pу от 4 до 10 МПа и температуре до 450 °С
– качественную углеродистую сталь 25, 35 и 40. При более высоких темпера- турах и давлениях используют легированные стали.
Прокладочные материалы, предназначенные для уплотнения фланце- вых соединении, должны быть пластичны, прочны, а также устойчивы к тем- пературным условиям и коррозионному действию среды. В качестве прокла- док для трубопроводов, работающих при давлении до 6,4 МПа, применяют листовой паронит (ГОСТ 481–80), асбестовый картон (ГОСТ 2850–80), про- кладочный картон (ГОСТ 9347–74), листовую техническую резину и другие материалы.
Паронит – основной прокладочный материал для трубопроводов, транспортирующих воду и пар температурой до 450 °С. Его хранят в темном помещении при температуре не выше 30 °С. Плоские неразъемные соедине- ния типа «гладких», «шип-паз», «выступ-впадина» уплотняют паронитом об- щего назначения (ПОН).
Размеры прокладок соответствуют размерам уплотнительных поверх- ностей фланцев, при этом внутренний диаметр прокладки должен быть на 1–2 мм больше внутреннего диаметра фланцев.
Сварные соединения более надежны, чем фланцевые и резьбовые, что особенно важно при высоких давлении и температуре рабочей среды. Приме- нение сварки дает также значительную экономию металла. Поэтому о боль- шинстве случаев трубы соединяют между собой с помощью сварки. Основ- ные виды сварных соединений и швов трубопроводов изображены на рис. 15.8. Чаще всего используют сварное стыковое соединение, которое выпол- няют после тщательной обработки кромок и калибровки труб.
Заглушками, которые по конструкции подразделяются на плоские (при- варные и фланцевые) и сферические, закрывают концы трубопроводов.
Плоские приварные заглушки (рис. 15.9, а) используют в трубопроводах, условное давление в которых до 1,5 МПа. Изготовляют их с условным прохо- дом от 40 до 600 мм.
Фланцевые заглушки (рис. 15.9, б) по форме, конструкции уплот- нительных поверхностей, присоединительным размерам Н точности обработ-
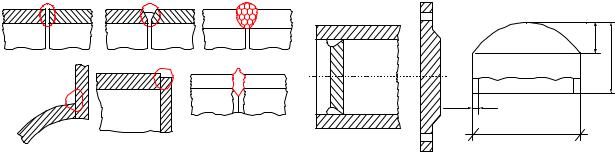
416
ки должны полностью соответствовать требованиям, предъявляемым к флан- цам.
а) |
б) |
в) |
г) |
д) |
е) |
Рис. 15.8. Основные виды сварных соеди- нений и швов трубопроводов: а – соеди- нение встык однослойное; б – соединение встык двухслойное; в – соединение встык многослойное; г – угловой шов; д – тор- цовый шов; е – шов контактной сварки
а) |
|
h |
|
Н |
S |
|
|
D |
б) |
в) |
Рис. 15.9. Заглушки: а – плоская приварная; б – фланцевая; в – эллиптическая
Эллиптические заглушки (рис. 15.9, в) в соответствии с ГОСТ 17379–83
изготовляют с условным проходом от 40 до 500 мм.
15.1.4. Компенсаторы
При нагревании трубопроводы удлиняются. Удлинение трубо- проводов зависит от их длины, материала, из которого они изготовле- ны, и температуры транспортируемого вещества. При изменении ли- нейных размеров трубопроводов могут быть разрушены сварные, резь- бовые и фланцевые соединения и повреждены другие детали. Поэтому трубопроводы проектируют и конструктивно выполняют так, чтобы они могли удлиняться при нагревании и укорачиваться при охлажде- нии.
Способность трубопровода компенсировать тепловые удлинения за счет своей геометрической формы и упругих свойств металла без специальных устройств, включенных в трубопровод, называется само- компенсацией. В других случаях надо устанавливать компенсаторы, которые подразделяются на гнутые, линзовые, сальниковые и волни- стые.
Гнутые компенсаторы из труб, воспринимающие удлинение за счет их изгиба без остаточных деформаций, удобны для эксплуатации. Изготовляют их П-образной формы из тех же труб, что и сам трубо- провод.
П-образные компенсаторы (рис. 15.10) сваривают из отдельных изогнутых труб или из отводов и прямых отрезков труб между ними. Некоторые компенсаторы нельзя выполнить целиком, так как их раз-

417
меры превышают габариты, допустимые для перевозки к месту монта- жа. В этом случае компенсаторы собирают и сваривают на месте мон- тажа.
П-образные компенсаторы рекомендуется применять для трубо- проводов диаметром до 600 мм. Компенсирующая способность П- образных компенсаторов зависит от их геометрических размеров и мо- жет достигать 600–700 мм. Недостатки таких компенсаторов: дополни- тельный расход труб, увеличение сопротивления движению продукта по трубопроводу, большие размеры и необходимость сооружения специ- альных опор.
R
R
а)
R
Сварной |
шов |
R
в)
Сварной
шов
R
|
R |
б) |
Сварной шов |
R
г)
Рис. 15.10. П-образные компенсаторы: а – из целой трубы; б – из двух частей; в – из трех частей, г – из семи частей
Линзовые компенсаторы (рис. 15.11) состоят из включенных в тру- бопровод линз. Линза представляет собой сварную конструкцию, состоя-
щую из двух тонкостенных стальных штампованных тарельчатой формы полулинз. Форма линзы позволяет легко изменять ее длину. Компенси- рующая способность каждой линзы сравнительно небольшая – 10–16 мм. Количество линз выбирают в зависимости от необходимой компенсирую- щей способности. Что бы уменьшить сопротивление движению продукта, внутри компенсаторов устанавливают стаканы 4 (манжеты), которые при- варивают к трубе со стороны входа транспортируемого продукта. Наруж- ный диаметр стакана должен быть меньше внутреннего диаметра компен- сатора на 2 мм. Для спуска конденсата в нижних точках каждой линзы вварены штуцера 3, к которым присоединяют дренажные или продувоч- ные устройства.
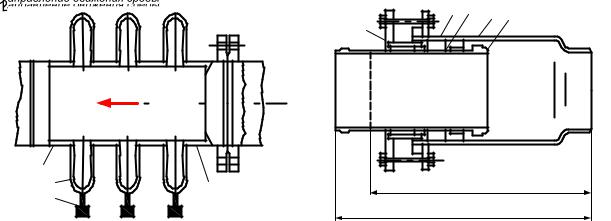
418
Lmin |
Lmаx |
Рис. 15.11. Линзовый компенсатор: 1 – |
Рис. 15.12. Сальниковый компенсатор: 1 – |
рубашка; 2 – полулинза; 3 – дренажный |
грундбукса; 2 – сальниковое уплотнение; 3, |
штуцер; 4 – стакан (манжета) |
4 – патрубки; 5 – упорное кольцо |
Линзовые компенсаторы, обладающие небольшими размерами и массой, применяют для трубопроводов диаметром от 200 до 1400 мм, рас- считанных на условное давление транспортируемой среды Pу до 1,6 МПа.
С трубопроводами компенсаторы соединяют на фланцах и с помощью сварки. Их недостатки: небольшие допускаемые давления и малая ком- пенсирующая способность.
Сальниковый компенсатор (рис. 15.12) представляет собой патрубок 4, вставленный в фасонный патрубок 3 большего диаметра. Компенсация происходит за счет перемещения патрубков один относительно другого. В зазоре между патрубками установлено сальниковое уплотнение с грун- дбуксой.
Сальниковые компенсаторы отличаются высокой компенсирующей способностью и небольшими размерами. Их недостатки; трудность со- держания сальников в состоянии надежной плотности, сложность изго- товления и монтажа, сравнительно быстрый износ сальниковой набивки.
Сальниковые компенсаторы применяют в трубопроводах, транспор- тирующих пар, горячую и холодную воду, рассчитанных на давление Pу =
1,6 МПа.
Для надежной работы сальникового компенсатора необходимо, что-
бы между ним и неподвижной опорой трубопровода была установлена (возможно, ближе к компенсатору) хотя бы одна направляющая опора с тем, чтобы исключить перекос в сальнике.
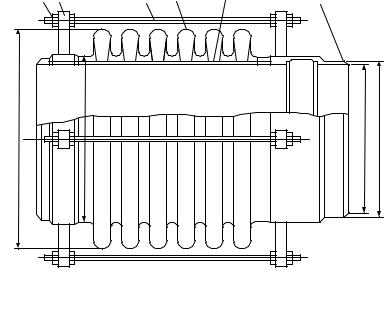
|
|
|
|
419 |
|
|
|
|
|
|
6 5 |
4 |
3 |
2 |
1 |
|
Волнистые |
осевые |
|||
компенсаторы |
(рис. |
|||||||||
|
|
|
|
|
15.13) |
применяют |
для |
|||
|
|
|
|
|
трубопроводов с Dу до |
|||||
|
|
|
|
|
400 мм и Pу до 6,4 МПа. |
|||||
|
D |
|
|
|
Основную |
деталь |
волни- |
|||
D |
|
|
|
S H |
стых |
компенсаторов |
– |
|||
|
|
|
гибкий элемент 3 – изго- |
|||||||
|
|
|
D D |
|||||||
|
|
|
|
|
||||||
|
|
|
|
|
товляют |
из одношовной |
||||
|
|
|
|
|
цилиндрической |
обечай- |
||||
|
|
|
|
|
ки гидравлическим фор- |
|||||
|
|
|
|
|
мованием. Концы гибкого |
|||||
|
|
|
|
|
элемента |
приварены |
к |
|||
Рис. 15.13. Волнистый осевой компенсатор: 1 – патру- |
патрубкам |
1. Компенса- |
||||||||
бок; 2 – внутренняя обечайка; 3 – гибкий элемент; 4 – |
ция |
температурного |
из- |
|||||||
шпилька; 5 – стойка; 6 –гайка |
|
|
менения длины трубопро- |
|||||||
водов между двумя неподвижными опорами осуществляется за счет осе- |
||||||||||
вого перемещения (сжатия – растяжения) гибкого элемента компенсато- |
||||||||||
ра. |
|
|
|
|
|
|
|
|
|
|
Волнистые осевые компенсаторы обладают большей компенси- |
||||||||||
рующей способностью, меньшими размерами и более длительным сро- |
||||||||||
ком эксплуатации, чем линзовые. При использовании этих компенсато- |
||||||||||
ров сокращается расход труб, а также снижается трудоемкость монтажа. |
15.1.5. Опоры и подвески
Нормальные условия работы трубопроводов в значительной степе- ни зависят от правильной их установки и прочности закрепления. Трубо- проводы закрепляют с помощью опор, которые по назначению и устрой- ству подразделяются на неподвижные и подвижные. По способу крепле- ния к ним трубопровода различают приварные, привариваемые непо- средственно к трубе, и хомутовые опоры, которые крепят к трубе хому- тами.
Неподвижные опоры должны жестко удерживать трубу и не допус- кать ее перемещения ни по вертикали, ни по горизонтали. Корпуса не- подвижных опор приваривают или крепят болтами к несущим конструк- циям трубопровода. Конструкции наиболее распространенных непод- вижных опор изображены на рис. 15.14.