
14_Metally_i_prochnost
.pdf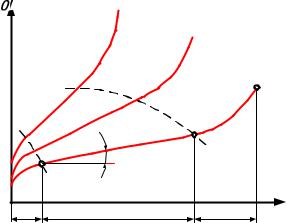
399
14. МЕТАЛЛ И РАСЧЕТ НА ПРОЧНОСТЬ ЭЛЕМЕНТОВ ПАРОВОГО КОТЛА
14.1. Работа металла при высокой температуре
Особенностями условий работы элементов современного парового кот- ла являются высокие давление и температура. В наиболее ответственных уз-
лах котла металл подвергается постоянному воздействию напряжения от внутреннего давления в условиях высокой температуры и действию дополни- тельных напряжений в переменных режимах работы (переход с одной нагруз- ки на другую, пуски и остановы котла). Кроме того, на металл снаружи воз- действуют коррозионно-активные составляющие продуктов сгорания, твер- дые частицы в потоке газов, вызывающие абразивный износ металла, а также некоторые примеси воды, определяющие коррозионное разъедание изнутри.
Элементы парового котла, работающие под избыточным давлением, ус- ловно можно разделить на две группы:
1)элементы, работающие при температуре ниже 350–400 °С: барабан, необогреваемые коллекторы, испарительные трубы, трубы экономайзера, а также необогреваемые трубопроводы и арматура водяного тракта и тракта на- сыщенного пара;
2)элементы, работающие при температуре выше 350–400 °С: паропере- греватели и их коллекторы, трубопроводы и арматура перегретого пара.
Под совместным воздействием температуры выше 450 °С и механиче- ских напряжений с течением времени в стали развивается опасное явление – ползучесть (крип). Ползучесть представляет собой медленное и непрерывное
|
|
|
|
|
|
увеличение пластической деформа- |
||
d |
σ = const |
t3 |
|
|
ции, например постепенное увели- |
|||
t2 |
|
чение диаметра трубы с утонением |
||||||
|
|
|
||||||
|
|
|
|
|
ее стенки. Это особый вид пласти- |
|||
|
|
|
|
|
|
|||
|
|
|
|
|
с |
ческой деформации, |
протекающий |
|
|
|
|
|
|
t1 |
при напряжении ниже предела те- |
||
|
|
|
|
b |
кучести. |
Опасной |
особенностью |
|
|
а |
α |
|
|
|
процесса ползучести является то, |
||
|
|
|
|
что по |
достижении |
определенной |
||
|
|
|
|
|
|
пластической деформации металл |
||
|
|
|
|
|
τ |
разрушается. Поэтому размеры де- |
||
|
|
|
|
|
талей, работающих в условиях раз- |
|||
|
|
|
|
|
|
|||
Рис. 14.1. Диаграмма ползучести стали при |
вития ползучести, необходимо не- |
|||||||
различных температурах и одинаковом на- |
прерывно контролировать. |
|||||||
пряжении |
|
|
|
|
Диаграмма ползучести стали |
|||
показана на рис. 14.1, где изображены кривые ползучести (увеличение диа- |
||||||||
метра трубы) при постоянном внутреннем напряжении для трех значений |
||||||||
температуры t1 < t2 < t3 |
Рассмотрим ход процесса на примере ползучести при |
400
температуре t1 . Кривая состоит из трех участков 0a, ab и bс. Участок 0а – за-
тухающей ползучести – соответствует короткому начальному периоду I, ко- гда металл в результате небольшой деформации даже несколько упрочняется.
Далее наступает длительный период II – установившейся ползучести – участок ab, в пределах которого труба может работать длительно, надежно, не разрушаясь. Скорость ползучести в этом периоде постоянна:
υ = |
d |
= tgα . |
(14.1) |
п τ
Наконец, следует опасный период III – нарастающей ползучести – уча- сток bс, до наступления разрушение детали – точка с, которому предшествует сильная пластическая деформация, например раздутие трубы поверхности на- грева. Надежная работа деталей возможна только в пределах периода II уста- новившейся ползучести. При более высокой температуре (t2 и t3 ) процесс
ползучести протекает аналогично, но более активно во времени: скорость ус- тановившейся ползучести повышается, а разрушение наступает раньше. При- ближенно считают, что при увеличении температуры на 40 °С сверх расчет- ного значения длительность надежной работы стали сокращается в 10 раз. Напряжение, при котором скорость ползучести в периоде II не превышает за- данной, называют условным пределом ползучести σп . Для большинства ма-
рок стали допускается предельная суммарная деформация металла в 1 % за 100 тыс. ч работы. Этому соответствует скорость ползучести σп = 10–7
мм/(мм·ч), или 10–5 %/ч. Испытания металлов на ползучесть проводят за от- носительно короткое время, до момента, когда металл выходит на участок равномерной скорости ползучести. Полная длительность периода II во време- ни рассчитывается по допустимой деформации металла. Для уверенности в том, что деталь (труба) не разрушится раньше, чем рассчитано по σп прово-
дят испытания на длительную прочность. Они производятся также, как и на ползучесть, но образцы при этом доводятся до разрушения. Это можно осу- ществить за ограниченное время испытаний (1000–2000 ч), но при более вы- соких скоростях ползучести, т. е. при более высоких напряжениях, прило- женных к образцу. Затем производится построение полученных характери- стик времени до разрушения образца от приложенного напряжения и опреде- ляется допустимое напряжение для установленного времени работы детали,
которое называют пределом длительной прочности σд.п .
Предел длительной прочности металла паровых котлов постепенно снижается в зависимости от времени работы (времени процесса ползучести). Он также зависит от температуры: снижается по мере увеличения рабочей температуры металла. Поэтому предел длительной прочности обязательно сопровождается указанием температуры, при которой проходило испытание,
401
и обозначают σ′д.п (t – значение температуры металла). В настоящее время
элементы паровых котлов, работающие в условиях ползучести» рассчитыва- ют по σ′д.п .
При коэффициенте использования рабочего времени установленного оборудования kраб = 0,85, время работы металла 100 тыс. ч эквивалентно сро-
ку службы при расчетных параметрах пара 13,5 лет. Для дорогостоящего обо- рудования, каким являются паровой котел и турбина с труднозаменяемыми элементами, этот срок службы в настоящее время считается недостаточным.
Внормах расчета на прочность [6] рекомендуется его увеличить примерно в 2 раза, т. е. до 200 тыс. ч. Это может несколько снизить длительную прочность металла к концу периода его работы.
Однако, учитывая улучшение технологии производства сталей и их термообработки, повышение культуры эксплуатации оборудования, улучше- ние методов контроля состояния металла в эксплуатации, можно обеспечить надежную работу металла при таком удлинении срока его службы (до 30 лет).
Вусловиях длительной работы металла с переменными тепловыми нагрузка- ми (переменная температура) развивается явление тепловой усталости ме- талла. Усталостные трещины изредка возникают в турбинах, насосах и вспо- могательных механизмах котельного цеха. В самих котлах опасность пред- ставляет тепловая усталость стали, возникающая при многократном быстром изменении ее температуры. При этом отдельные участки труб и коллекторов оказываются более нагретыми и стремятся расшириться, чему препятствуют сопряженные с ними менее нагретые участки. В итоге сначала на поверхности металла появляются небольшие трещины (риски), которые постепенно углуб- ляются и увеличиваются, затем происходит разрыв трубы. Такие условия прежде всего возникают во впрыскивающих пароохладителях, когда испаре-
ние капель влаги продолжается за пределами внутренней защитной обечайки и они попадают на сильно разогретую поверхность корпуса. Опасными по
возникновению тепловой усталости являются лобовые участки экранных труб в зоне ядра факела, когда языки пламени периодически касаются экрана и резко увеличивают температуру наружной поверхности труб.
Сильнее других подвержена явлению тепловой усталости аустенитная сталь, теплопроводность которой примерно в 1,5 раза меньше, чем перлитной, а коэффициент линейного расширения больше в 1,7 раза. Из опыта эксплуа- тации установлено, что нежелательно изготовление из аустенитной стали змеевиковых поверхностей перегревателя, расположенных близко к выходу из топки, так как здесь сильнее проявляются изменения температур газа в пе- ременных режимах работы.
Работа поверхностей нагрева в условиях контакта с топочными газами сопровождается электрохимической коррозией. В результате реакций наруж- ная поверхность труб покрывается продуктами коррозии в виде слоя окали- ны. Окалинообразование на наружной поверхности топочных экранов и па-
402
роперегревателя при температурах металла более 580–600 °С может быть на- столько значительным, что толщина стенки трубы со временем уменьшается до опасных пределов, влекущих за собой преждевременное разрушение труб.
Коррозионное разрушение металла усугубляется интенсивными тепловыми нагрузками и высокой температурой в зоне коррозии. Утонение металла вследствие окалинообразования учитывают в прочностных расчетах. Многие элементы конструкции котла, особенно детали водяной и паровой арматуры и поверхности нагрева, работают в условиях эрозионного и абразивного износа.
Предельно допустимые значения температур наружной поверхности труб по условию окалинообразования для разных марок сталей приведены в табл. 14.1.
Таблица 14.1
Предельные допустимые температуры наружной поверхности труб по жаростойкости (окалинообразованию в среде продуктов сгорания)
Марка стали |
|
|
|
Топливо |
|
|
|
Сернистый мазут |
|
Каменный и бурый уголь, |
|
|
|
|
|
|
газ |
12Х1МФ |
|
|
540 (585) * |
|
585 |
12Х2МФСР |
|
|
585 |
|
595 |
12Х2МФБ |
|
|
620 |
|
630 |
12Х18Н12Т |
|
|
610 |
|
640 |
* Допускается только при q |
|
< 400 кВт/м2. |
|
|
|
|
мест |
|
|
|
Внутри труб при контакте металла с рабочей средой также могут про- исходить коррозионные процессы. Например, в змеевиках пароперегревателя при высоких температурах металла (более 400 °С) может возникнуть паровая
коррозия металла по реакции
3Fe+4H2O → Fe3O4 +4H2
Окcид железа – магнетит Fe3O4 – создает защитную пленку, которая задер-
живает дальнейшее развитие коррозии, если не происходит ее разрушение, а
свободный водород насыщает за счет диффузии поверхностный слой стали и вызывает ее растрескивание.
Высокие термические напряжения металла экранных труб и барабана в контакте с концентрированным раствором едкого натра NaOH , образующе- гося за счет упаривания котловой воды в узких пазах, выточках, зазорах, при- водит к развитию межкристаллитных (по границе между зернами) трещин в структуре металла с последующим разрывом трубы или коллектора (так на- зываемая щелочная хрупкость). При пульсациях в подаче воды в радиацион- ные поверхности прямоточных котлов, неустойчивом расслоении пароводя-
ного потока в трубах возникают циклические тепловые перенапряжения в
403
стенке металла, приводящие при наличии агрессивной среды (кислорода, ще- лочи) к появлению трещин на внутренней поверхности металла (так называе- мая коррозионная усталость). Напряженные элементы, выполненные из ау- стенитных сталей, также подвергаются коррозионному растрескиванию, осо- бенно при наличии в рабочей среде хлориона, которое имеет транскристал- литый характер (разрушение проходит через структуру зерен металла).
При повышенной температуре постепенно изменяется структура метал- ла, а следовательно, изменяются и его свойства. Под длительным воздействи- ем повышенной температуры в углеродистой и низколегированной стали, особенно вблизи сварных швов, может происходить нарушение химических связей железа с углеродом с выделением свободного углерода в форме графи- та – графитизация стали. При этом сталь теряет прочность и возникает опас- ность аварийного разрушения конструкции.
Изложенное выше об условиях работы металла при высоких температу- рах и давлениях позволяет сформулировать основные требования к стали, обеспечивающей длительную и падежную работу котельной установки: вы- сокий предел длительной прочности; высокая стойкость против окисления и окалинообразования; стабильность структуры металла, отсутствие опасного изменения свойств в процессе длительной работы; хорошая свариваемость, отсутствие металлургических и механических дефектов поверхности (вмятин, забоин, трещин и т. п.), ослабляющих сечение элементов и являющихся кон- центраторами напряжений.
14.2. Основные материалы элементов котла
Основными материалами котлостроения служат углеродистая, а также легированная стали. В состав последней включены хром, никель, молибден, вольфрам, ванадий и другие легирующие элементы, которые являются доро- гими материалами, однако введение их в состав стали сообщает ей ряд цен- ных свойств, недостижимых для обычной углеродистой стали.
Углеродистая сталь. Воздухоподогреватели и каркасы котла изготав- ливают из углеродистой стали 3. Для изготовления элементов котла, которые работают в условиях отсутствия ползучести (tст < 450 °C), применяют качест-
венную малоуглеродистую сталь марок 10 и 20. В последнее время сталь 20 стала превалирующей, поскольку по прочности она превосходит сталь 10, а по свариваемости и коррозионной стойкости практически не уступает ей. Ос- нова микроструктуры металла углеродистой стали – феррит – это мягкая и пластичная составляющая, в основном содержащая железо (по латыни «фер- рум» – железо). Количество упрочняющей составляющей – перлита – невели- ко. В структуру перлита входит цементит – прочное соединение железа с уг- леродом.
В состав стали этого класса для повышения прочности вводят в не- большом количестве кремний (0,2–0,3%) и марганец (0,3–0,5%). Листовая
404
сталь имеет повышенное содержание углерода, в среднем от 0,15% (сталь 15К) до 0,25% (сталь 25К), что повышает показатели ее прочности; сваривае- мость этой листовой стали вполне удовлетворительна. Сталь марки 22К с до-
бавлением в состав этой стали небольшого количества титана применяют для изготовления барабанов высокого давления (до 12,5 МПа).
Низколегированная сталь перлитного класса. Низколегированной явля-
ется сталь, содержащая, не больше 4–5% легирующих элементов. К перлит- ному классу их относят потому, что после охлаждения на воздухе структура этой стали сохраняет перлит. Такую сталь применяют для конструкций, рабо- тающих в условиях высоких температур и давлений, где сталь подвержена явлению ползучести. Принято легирующие добавки, вводимые в сталь, обо- значав определенными буквами. Первая цифра марки стали указывает на среднее содержание в данной стали углерода в сотых долях процента. Цифра за буквой, обозначающей легирующий элемент, характеризует среднее со- держание его в целых процентах. Если количество какого-нибудь элемента содержится меньше 1%, то цифра за его обозначением обычно отсутствует. При наличии подряд нескольких букв, обозначающих легирующие элементы, содержание добавки каждого следующего элемента примерно в 2 раза мень- ше предыдущего. Условные обозначения добавляемых элементов следующие: Б – ниобий, В – вольфрам, Г – марганец, Д – медь, М – молибден, Н – никель, Р – бор, С – кремний, Т – титан, Ф – ванадий, X – хром, Ю – алюминий.
Широкое применение получили низколегированная хромомолибдено- вая сталь перлитного класса 15ХМ (0,15% углерода, 1% Cr и 0,5% Mo ) и мо- либденохромовая сталь 12МХ (0,12% углерода, 0,6% Mo и 0,4 % Cr ); первую применяют для условий работы при t ≤ 530 °С, вторую – при t ≤ 510 °С. Хром, кремний и алюминий повышают окалиностойкость, а молибден – дли- тельную прочность и сопротивление ползучести. Эти стали, особенно 15ХМ, отличаются хорошей свариваемостью, повышенным сопротивлением ползу- чести и малой склонностью к графитизации.
Стремление к дальнейшему повышению температуры перегретого пара при использовании недорогих низколегированных сталей перлитного класса привело к дополнительному легированию хромомолибденовой стали ванади- ем в количестве 0,2–0,3%. Ванадий как сильный карбидообразователь способ- ствует повышению предела ползучести.
В настоящее время широко применяют хромомолибденованадиевую сталь 12Х1МФ и более стойкую против ползучести сталь 15Х1М1Ф с не- сколько повышенным содержанием углерода и значительно повышенным со- держанием молибдена. Эти стали предназначены для работы при температуре до 580 °С.
Наиболее окалиностойка и жаропрочна сталь перлитного класса марки 12Х2МФСР, содержащая для окалипостойкости 2% Cr и 1–1,5% кремния. Присадка очень незначительного количества бора (0,003–0,005%) повышает
405
ее жаропрочность. Эта сталь, из которой изготовляют главным образом трубы пароперегревателя, очень чувствительна к режиму термической обработки.
По своей природе сталь перлитного класса может обеспечить надежную работу металла при температуре не выше 580– 585 °С. Поэтому средняя тем- пература перегретого пара должна быть меньше на 20– 30 °С.
В котлостроении широко применяются низколегированные стали, рабо- тающие при относительно невысокой температуре, когда явление ползучести не проявляется. Для изготовления барабанов котлов высокого давления (свыше 12 МПа) применяют сталь марок 16ГНМ и 16ГНМА (1% Mn ; 1,2% Ni ; 0,5% Mo ). Буква А характеризует тщательность соблюдения технологии варки стали (высококачественная сталь). Для трубопроводов питательного тракта сверхкритического давления применяют марган-цевокремниевую сталь марки 15ГС (1,1% Mn ; 0,8% Si ). Предел текучести этой стали значи- тельно выше предела текучести углеродистой стали марки 20.
Высоколегированная сталь аустенитного класса. Повышение темпера-
туры перегретого пара до 570–580 °С, а в экспериментальных установках до 600–650 °С потребовало применения еще более жаропрочных и окалиностой- ких сталей. Структурной основой таких сталей служит высоколегированный хромоникелевый или хромоникелемарганцевый аустенит. Повышению ус- тойчивости аустенита способствуют главным образом никель и марганец. Высокое содержание хрома в аустенитной стали делает её жаростойкой (ус- тойчивой против окалинообразования). В отличие от низколегированной ста-
ли в высоколегированной аустенитной стали добавка только никеля и хрома достигает 30% и более общей массы металла, при этом стоимость ее стано- вится выше в несколько раз.
Из марок стали аустенитного класса наибольшее распространение по- лучила классическая нержавеющая, кислотоупорная и жаропрочная сталь
1X18H9T (0,1% C ; 18% Cr ; 9% Ni ; 1% Ti ). Титан и ниобий – элементы-
стабилизаторы. Являясь сильными карбидообразователями, эти элементы связывают весь углерод в прочные карбиды. Из сталей с повышенным отно- шением NiCr в первую очередь следует отметить сталь 1Х18Н12Т, далее
сталь 1XI4H14B2M с вольфрамом и молибденом. Молибден и вольфрам до- бавляют к аустенитной стали с целью дальнейшего повышения жаропрочно- сти (устойчивость против ползучести).
Стремление к снижению стоимости жаропрочной стали при одновре- менном устранении недостатков, присущих аустенитной стали, привело к разработке более дешевых безникелевых сталей на основе 11–13% Cr с до- бавкой молибдена, вольфрама и ванадия для повышения жаропрочности. При
такой композиции легирующих элементов структура этой стали представляет собой низкоуглеродистый мартенсит или мартенсит в смеси с ферритом.
Перспективной представляется сталь мартенситно-ферритного класса марки Х12В2М (ЭИ-756). Пароперегревательные и паропроводные трубы из этой стали установлены на некоторых блоках сверхкритических параметров.
406
Чугун. Из чугунов, вырабатываемых промышленностью в больших масштабах, в котлостроении получили широкое применение серый, ковкий и окалиностойкий чугун. Серый чугун (СЧ) имеет высокие литейные свойства. Из него изготовляют гарнитуру топочных устройств: лазы, гляделки, лючки, взрывные клапаны, арматуру для крепления и подвески обмуровки. Наи- большая температура применения чугуна 250–350 °С. Ковкий чугун (КЧ) главным образом применяют для изготовления деталей насосов, вентиляторов и вспомогательного оборудования. Окалиностойкий чугун легирован элемен- тами, повышающими его жаростойкость. Из него изготовляют дистанцион- ные гребенки пароперегревателей, подвески для крепленая труб и другие де- тали, работающие в зоне высоких температур.
14.3. Расчет на прочность основных элементов парового котла
В основу расчета положен принцип оценки прочности металла по пре- дельной нагрузке при расчетном давлении рабочей среды.
Расчетным является давление, полученное как сумма давления на выхо-
де из котла рпп и гидравлических потерь при номинальной нагрузке тракта от выходного коллектора пароперегревателя до места расположения рассчиты- ваемого элемента å рг . Заполнение элементов водой или пароводяной сме-
сью учитывается гидростатическим давлением столба (нивелирного напора), расположенного над рассчитываемым элементом рнив . Следовательно, рас-
четное давление
р = рпп + å рг + рнив . |
(14.2) |
Гидравлические сопротивления и нивелирное давление учитываются, если их сумма составит от давления за пароперегревателем не менее чем 3%. Дополнительной является нагрузка, обусловленная силой тяжести, дейст- вующей на этот элемент и присоединенные к нему детали.
Расчетная температура зависит от условий обогрева и охлаждения рабочей поверхности. Для необогреваемых элементов расчетная температура принимается равной температуре рабочей среды: для барабана — температу- ре насыщения при давлении в нем, в коллекторах поверхностей нагрева и со- единяющих трубопроводах – температуре протекающей через них рабочей среды. Для обогреваемых элементов расчетную температуру стенки вычис- ляют по формуле (9.110), учитывающей характер теплового воздействия на поверхность нагрева. Учитывают также, что некоторые трубы или группа труб этой поверхности работают с тепловой разверкой, т. е. имеют темпера- туру, превышающую среднюю расчетную температуру на tразв .
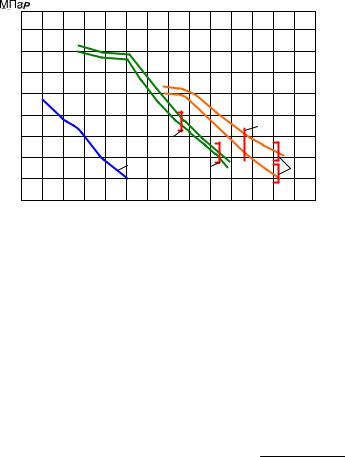
|
|
|
|
|
|
407 |
|
|
|
Расчет элементов котла на прочность производят по номинальному до- |
|||||||||
пустимому напряжению, которое должно обеспечить заданный ресурс работы |
|||||||||
металла при средней расчетной температуре и наименьшей металлоемкости |
|||||||||
|
|
|
|
|
|
|
|
|
′ |
элемента. Последнее принимают с некоторым запасом по сравнению с σд.п с |
|||||||||
учетом особенностей конструкции и эксплуатации каждого элемента. |
|||||||||
Допускаемое напряжение σдоп определяют по формуле |
|
||||||||
|
|
|
|
|
|
σдоп = ησ*доп , |
|
(14.3) |
|
где σ*доп – номинальное допускаемое напряжение, МПа; |
η <1 – коэффициент, |
||||||||
учитывающий конструктивные и эксплуатационные особенности рассчиты- |
|||||||||
ваемого элемента. |
|
|
|
|
|
|
|
|
|
В зависимости от качества стали значения σ*доп существенно различают- |
|||||||||
ся (рис. 14.2) и снижаются по мере роста рабочей температуры металла. |
|||||||||
В связи с настоятельной необходимостью повышения надежности мощ- |
|||||||||
ных блоков сверхкритического давления в расчет поверхностей нагрева, а |
|||||||||
также водо- и пароперепускных труб в пределах котла вводят пониженное |
|||||||||
допустимое напряжение, для чего коэффициент η принимают равным 0,9. |
|||||||||
σ*доп |
|
|
|
|
|
|
Снижают также σ доп для |
||
|
|
|
|
|
|
|
трубок пароохладителей и па- |
||
|
|
|
|
|
|
|
ропаровых теплообменников до |
||
|
1 |
|
|
|
|
|
η = 0,7 , так как они работают в |
||
|
|
|
|
|
|
напряженных условиях и труд- |
|||
|
Х |
|
|
|
|
||||
|
|
1 |
|
|
|
|
|||
С |
|
8 |
|
|
|
||||
|
|
Н |
|
|
|||||
т |
|
|
|
1 |
|
|
|
|
|
. |
|
|
|
|
2 |
одоступны |
для |
ремонта. Для |
|
2 |
Э |
|
|
|
|
Т |
|||
0 |
|
|
|
|
|
||||
|
И |
|
|
|
|
|
|||
|
- |
|
|
|
|
|
|||
|
75 |
|
|
|
|
||||
|
|
6 |
|
|
|
барабанов |
η = 1, |
обогреваемых |
|
|
|
|
|
|
|
|
|||
|
|
|
|
|
|
|
коллекторов и камер – 0,9, |
||
|
|
|
|
|
|
|
трубных досок – 0,85. |
||
|
|
|
|
|
|
|
Основной |
конструктив- |
|
Рис. 14.2. Допускаемые напряжения для металла в |
ной формой элементов котла, |
||||||||
зависимости от температуры: 1 – предельная тем- |
работающих под давлением ра- |
||||||||
пература применения стали; 2 – ограничение ра- |
бочей среды, является цилинд- |
||||||||
бочей температуры при сжигании сернистых топ- |
рическая (барабаны, коллекто- |
||||||||
лив |
|
|
|
|
|
|
ры и трубы поверхностей на- |
||
грева котлов ТЭС, корпуса, камеры и трубы теплообменников АЭС). Для ци- |
|||||||||
линдрических элементов, подверженных внутреннему давлению, обычно оп- |
|||||||||
ределяют расчетную толщину стенки δ, мм, при известных значениях избы- |
|||||||||
точного давления |
р , МПа, |
|
наружного диаметра d , мм, и принятой марки |
||||||
стали по формуле |
|
|
|
|
|
pd |
|
|
|
|
|
|
|
|
|
|
|
|
|
|
|
|
|
|
|
δ = 2ϕσдоп + р |
+ С , |
|
(14.4) |
408
где ϕ – коэффициент прочности элемента, ослабленного продольным сварным
швом или сверлениями для присоединения трубной системы; С – прибавка к расчетной толщине стенки, мм.
Прибавка делается для компенсации минусового допуска толщины стен- ки при производстве трубы, камеры, корпуса, для компенсации утонения тол-
щины стенки в местах гибов и на потери металла при окалинообразовании в течение расчетного срока службы. В общем случае прибавка составляет С = 0,1 мм. Дополнительная прибавка на окалинообразование делается для легиро- ванных сталей при температуре стенки 580 °С и выше.
Барабан котла относится к числу наиболее напряженных элементов. В нем возникают напряжения от внутреннего давления, термические напряже- ния, определяемые разностью температур по толщине стенки барабана; и на- пряжения, возникающие из-за разности температур между верхом и низом ба- рабана. Наиболее напряженными являются режимы пуска и останова котла, когда температурные перепады оказываются наибольшими. Наиболее заметное
влияние на увеличение толщины стенки оказывают многочисленные сверления для ввода и вывода труб. В формуле (14.4) это учитывается коэффициентом прочности ϕ < 1, значение которого зависит от диаметра сверлений и расстоя-
ния между ними. Наибольшие напряжения от внутреннего давления возникают в продольном сечении цилиндрической части барабана, коллектора, поэтому больший шаг между отверстиями должен быть в этом сечении. Отверстия в поперечном сечении цилиндра можно располагать более часто. При размеще- нии отверстий в барабане стремятся к тому, чтобы коэффициент прочности стенки приближался к значению ϕш – коэффициенту прочности продольного
сварного шва барабана, который в зависимости от материала и технологии сварки изменяется в пределах 0,85–1,0. Дальнейшее повышение коэффициента прочности при ослаблении его отверстиями нецелесообразно. В барабанах котлов, работающих с давлением 11,5 МПа, толщина стенки составляет 105 мм, а при давлении 15,5 МПа – 115 мм. Барабаны котлов изготовляются внут- ренним диаметром 1600 мм. Особый расчет производят для обеспечения проч- ности приварных эллиптических днищ с отверстием (лазом) диаметром 400 мм (ранее лаз выполняли овальным размером 425х320 мм).
Расчет коллекторов ведут аналогично расчету барабана. Торцы коллек- тора в отличие от барабана имеют плоские приварные донышки, которые рас- считываются по специальным указаниям.
14.4.Примеры и контрольные вопросы
14.4.1.Примеры
1.Определить на сколько фактическая толщина стенки барабана больше её расчетного значения для котельного агрегата ПК-10 Ш, если фактическая толщина стенки барабана δф = 85 мм, наружный диаметр dн = 1470 мм, давле-