
11_Isparitelnye_poverkhnosti_nagreva
.pdf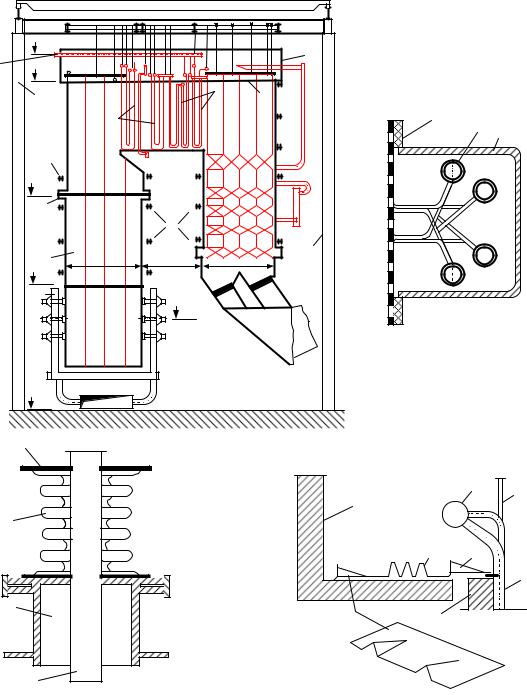
332
Выход |
61000 |
|
|
|
4 |
|
|
|
|
|
|
|
|
|
|
||
пара СКД |
55000 |
|
|
6 |
|
|
|
|
|
|
|
|
|
|
|
||
|
9 |
|
|
7 |
|
|
|
|
|
|
|
|
1 |
|
|
||
|
|
5 |
|
|
|
2 |
3 |
|
|
|
СРЧ |
|
|
|
|
||
|
|
|
|
|
|
|
|
|
|
8 |
|
|
|
|
|
|
|
|
35200 |
|
|
|
|
|
|
|
|
3 |
|
8 |
|
|
|
|
|
|
|
СРЧ |
|
|
|
|
|
|
|
1 |
10420 |
7980 |
|
9 |
|
|
|
|
|
10420 |
|
|
|
|||
|
22000 |
|
|
|
1 |
|
|
|
|
2 |
|
|
|
|
|
|
|
|
|
|
|
|
|
|
|
|
|
|
|
15600 |
|
|
|
|
|
|
|
НРЧ |
|
|
|
|
б) |
|
|
|
|
|
|
|
|
|
|
|
0,0 |
|
|
|
|
|
|
|
|
3 |
|
а) |
|
|
|
|
|
|
|
|
|
|
|
|
2 |
3 |
|
|
|
|
|
|
6 |
|
|
|
4 |
|
|
|
|
|
|
|
|
|
|
|
|
|
|
|
|
|
|
|
|
|
|
4 |
5 |
|
|
|
|
|
|
|
|
|
1 |
|
2 |
|
|
|
5 |
7 |
|
|
|
|
|
|
|
|
|
||
|
1 |
в) |
|
|
|
|
г) |
|
|
|
|
|
|
|
|
Рис. 11.8. Газоплотный паровой котел СКД и узлы его уплотнения: а – общий вид котла; 1
– топка; 2 – горелки; 3 – узел разъема экранных панелей; 4 уплотнительный верхний короб (щатер); 6 – конвективная поверхность пароперегревателя; 7 – потолочный экран; 8 – пояс жесткоти экранов; 9 – колонны котла; б – узел разъема экранных панелей; 1 – газоплотный экран; 2 – смесительный коллектор; 3 – уплотняющий металлический короб с тепловой изоляцией; в – узел уплотнения прохода трубы через стенку; 1 – отводящая труба; 2 – вы- водная камера; 3 – герметизирующая пластина; 4 – сильфон; г – соединение шатра со сте- ной топки; 1 – газоплотный экран; 2 – коллектор; 3 – подвеска экрана; 4 – сильфонный компенсатор; 5 – гофрированная пластина; 6 – стенка шатра топки; 7 – обмуровка топки
333
Потолочный экран выполняют из отдельных блоков газоплотных пане- лей. Для прохода труб ширм, подвесных труб конвективных пакетов в пото- лочных панелях специальной разводкой труб образуют отверстия, а места прохода уплотняют. Пример уплотнения прохода труб через потолок показан на рис. 11.8, в. Это конструкция сильфонного типа, позволяющая компенси- ровать термические перемещения труб относительно каркаса.
Особенно велико значение высокой плотности в котлах, работающих под наддувом, в которых избыточное давление продуктов сгорания наиболее велико в топочной камере. Обеспечение плотности в потолочном экране та- ких котлов представляет наибольшие трудности в связи с тем, что через него проходит вверх к коллекторам огромное количество труб поверхностей на- грева. Поэтому над потолочным экраном помещают вторую ограждающую стенку, и между ними образуется так называемый «шатер» (см. рис. 11.8, а). Все паропересбросные трубы между отдельными пакетами перегревателя на- ходятся внутри «шатра». «Шатер» находится под давлением воздуха выше топочного, поэтому неплотность в проходе труб поверхностей нагрева к кол- лекторам не приводит к выбросу газов вовне. Более совершенные уплотнения должны иметь отводящие трубы на выходе из «шатра», но их число значи- тельно меньше, и они выводятся через уплотнения типа показанного на рис. 11.8, г.
11.4. Методы повышения надежности газоплотных экранов
Топочные экраны, особенно котлов сверхкритического давления, рабо- тают в тяжелых условиях: высокие температура и давление рабочего тела, высокая температура факела, большая интенсивность обогрева, агрессивная среда топочных газов. Поэтому очень важно повысить надежность работы топочных экранов.
В газоплотных паровых котлах допустимый градиент температуры сты- куемых крайних труб соседних лент по условиям прочности не должен пре- вышать 50–100 °С в зависимости от конструкции экрана. Это условие выпол-
няется для параллельно расположенных соседних труб в одном ходе рабочей среды, у которых различие в температуре рабочей среды и металла труб не- значительно.
При двухходовой схеме движения панели экранов конструктивно со- единены между собой параллельно, а по рабочему телу – последовательно (рис. 11.9, а). В результате в крайних трубах состыкованных панелей из-за большой разности температур (если tвх = t2′ − t1′ > 50 °С) между соединенны-
ми сваркой трубами (рис. 11.9, б) может возникнуть чрезмерное напряжение в металле, приводящее к нарушению газовой плотности экрана.
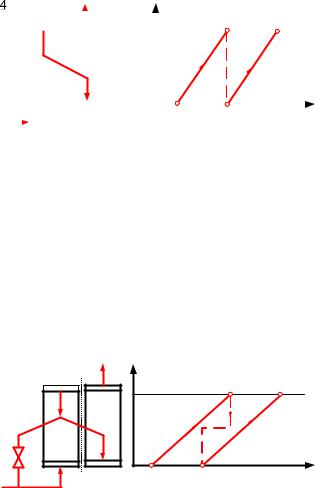
334
|
|
|
t1′′ |
|
|
t |
2′′ |
Н |
|
|
|
В схеме байпасирования |
||||
|
|
|
|
|
|
|
t1′′ |
t2′′ |
|
(рис. 11.10, а) часть рабочего те- |
||||||
|
|
|
||||||||||||||
|
|
|
|
|
|
|
|
|
|
|
|
|
||||
|
|
|
|
|
|
|
|
|
|
|
|
|
|
|
ла проходит мимо первой пане- |
|
|
|
|
|
|
|
|
|
|
|
|
|
|
|
|
ли обогреваемых экранов, что |
|
|
|
|
|
|
|
|
|
|
|
|
|
|
|
|
увеличивает восприятие теплоты |
|
|
|
|
|
|
|
|
|
|
|
|
|
|
|
|
на единицу оставшегося расхода |
|
|
|
|
|
|
|
|
|
|
|
|
|
|
|
|
||
|
|
|
|
|
t1′ |
|
t2′ = t1′′ |
а) |
|
t1′ |
t2′ |
б) |
t |
|||
|
|
|
|
|
|
|
в ней и приводит к повышению |
|||||||||
|
|
|
|
|
|
|
|
|
||||||||
Рис. 11.9. Схема двухходового цельносварного |
температуры на выходе из пер- |
|||||||||||||||
экрана (а) и график перепада температур сопря- |
вой панели. После смешения ра- |
|||||||||||||||
женных панелей на входе |
tвх и выходе |
tвых |
бочей среды за первой панелью |
|||||||||||||
(б): 1 и 2 – панели экрана; 3 и 4 – вход и выход |
||||||||||||||||
с частью холодного потока тем- |
||||||||||||||||
рабочего тела |
|
|
|
|
|
|
пература на входе во вторую па- |
|||||||||
|
|
|
|
|
|
|
|
|
|
|
|
|
|
|
нель снижается (рис. 11.10, б), что обеспечивает приемлемое значение tвх в
нижней части состыкованных труб панелей. |
|
|
|
|
|
||||||
В этой схеме массовая скорость увеличивается по тракту: в первой па- |
|||||||||||
нели она меньше, чем во второй. Долю байпасируемой среды выбирают в за- |
|||||||||||
|
|
|
|
|
|
висимости от соотношения мас- |
|||||
t1′′ |
t2′′ Н |
|
t1′′ |
t 2′′ |
|
совых скоростей среды и энерго- |
|||||
|
|
|
|
выделения в топке. Ориентиро- |
|||||||
|
|
|
|
|
|
вочно она равна 20% Dном , |
что |
||||
|
|
|
|
|
|
обеспечивает |
удовлетворитель- |
||||
t ′ |
t′ |
t ′ |
t2′ |
|
|
ный температурный режим и на- |
|||||
б) |
t |
дежную работу экранов. |
|
||||||||
1 |
2 а) |
1 |
|
||||||||
Рис. 11.10. Схема двухходового цельносварного |
Эффективным |
средством |
|||||||||
повышения надежности работы |
|||||||||||
экрана с байпасированием (а) и график перепада |
|||||||||||
температур сопряженных панелей на входе |
tвх |
экранов |
является |
рециркуляция |
|||||||
– (а) и выходе |
tвых |
– (б): Обозначения тс же, |
части |
продуктов |
сгорания |
из |
|||||
конвективной |
шахты (за эконо- |
||||||||||
что и на рис. 11.9 |
|
|
|
|
|||||||
|
|
|
|
майзером) в топочную камеру. В |
|||||||
|
|
|
|
|
|
||||||
результате происходит снижение температуры горения в топке и заметно |
|||||||||||
снижается тепловой поток, падающий на экран. Это особенно важно для га- |
|||||||||||
зомазутных котлов, топочные экраны которых без рециркуляции восприни- |
|||||||||||
мают тепловые потоки примерно в 1,5–2 раза более высокие, чем в пыле- |
|||||||||||
угольных топках. Обычно в таких топках большой тепловой мощности со- |
|||||||||||
храняют при номинальной нагрузке рециркуляцию газов в топку в количестве |
|||||||||||
до 10–15% объема образующихся при горении газов. |
|
|
|
11.5. Высокотемпературная коррозия экранов
Под термином высокотемпературная коррозия понимается коррозион- ное разрушение металла труб поверхностей нагрева, соприкасающихся с про- дуктами сгорания высокой температуры (ϑг > 700 °С). Сюда относятся два
335
вида коррозии металла, происходящие в разных зонах котла и имеющие раз- личный химический характер. Одним из них является коррозия экранов то- почной камеры в зоне расположения ядра, определяемая контактом серни- стых газов с металлом труб. Другой характеризуется коррозией труб паропе-
регревателей и разрушением элементов их креплений за счет присутствия в газовом потоке окислов ванадия.
Наружная коррозия труб экранов. Этот вид коррозии возникает при
сжигании топлив с малым выходом летучих и сернистого мазута и связан с образованием вблизи поверхности труб экранов заметной концентрации се- роводорода H2S. Коррозия развивается интенсивно на уровне расположения
горелок в зоне экранов, которые непосредственно омываются расширяющей- ся струей на выходе из горелки (рис. 11.11, а).
Скорость коррозионного разрушения металла лобовой части труб при неблагоприятных условиях может составить 3–4 мм/год, т.е. трубы экранов в этой зоне выходят из строя менее чем через год (при толщине стенки 5–6 мм допустимое локальное уменьшение толщины составляет 2 мм). Износ труб имеет вид «спиливания» лобовой части стенки трубы (рис. 11.11, б).
Исследованиями установлено, что неблагоприятными условиями явля-
ется локальное снижение коэффициента избытка воздуха в пылевоздушной струе αЛОК < 0,7 при быстром росте температуры струи по мере удаления ее
от амбразуры горелки. В процессе выхода летучих веществ из частиц топлива в газовой среде накапливаются горючие вещества H2 , CO , CH4 . При высо-
кой температуре в газообразные соединения переходят 70 − 80%Sp топлива. Нехватка кислорода приводит к тому, что при наличии свободных H2 и S2 в
газовой среде протекает реакция
S2 +2H2 → 2H2S. |
(11.1) |
Даже при незначительных объемных концентрациях H2S у поверхности
экранов (0,04–0,07%) скорость коррозии металла возрастает в 5–10 раз по сравнению с допустимой при содержании H2S=0,01%. Первичным продуктом
реакции H2S с металлом труб является сульфид железа FeS, который затем
преобразуется в порошкообразные сульфаты. Последние легко сдуваются (удаляются) с поверхности, давая возможность дальнейшему развитию про- цесса окисления.
Для исключения коррозионного разрушения экранов необходимо обес- печить равномерную раздачу топлива и воздуха по горелкам так, чтобы в ка- ждой из них постоянно имел место избыток воздуха больше единицы. Нерав- номерностью такой раздачи особенно «грешат» крайние горелки. Кроме того,
следует исключить прямой удар пылевоздушной струи из горелки в боковой экран на близком расстоянии от амбразуры. Для этого отодвигают крайние
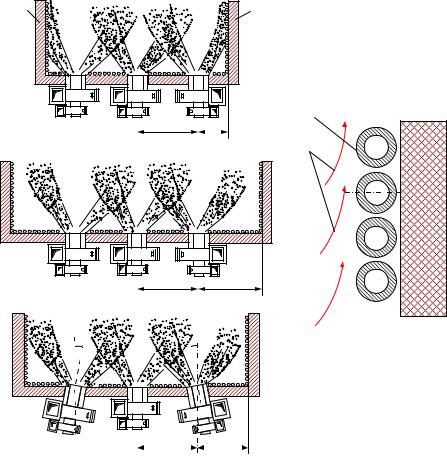
336
горелки от стен на большее расстояние (близкое к межгорелочному) и развер- тывает их оси на 5–10° к центру топки (рис. 11.11, в, г).
1 |
|
1 |
а) |
L |
2 |
|
L / 2 |
|
|
|
3 |
в) |
L L
б)
г)
L |
|
L / 2 |
Рис. 11.11. Наружная коррозия экранных труб и ее ограничение; а – зона активной корро- зии при фронтовой компоновке горелок; б – характер коррозии труб; в – удаление горелок от боковых стен; г – разворот горелок к центру топки; 1 – зона активной коррозии труб; 2
– место износа металла; 3 – направление движения газов
Коррозия пакетов пароперегревателей. Второй вид коррозии связан с окислением труб и крепежных деталей пароперегревателей, когда температу- ра металла превышает 610–620°С. Этот тип коррозии определяется участием оксидов ванадия и называется ванадиевой коррозией. Она проявляет себя при сжигании мазутов, зола которых содержит оксид V2O4 . В процессе горения
углеводородов V2O4 окисляется до V2O5 и с участием других компонентов газовой среды образует ванадаты –5V2O5 × Na2O × V2O4 – и при наличии серы в топливе – пиросульфаты натрия – Na2S2O7 , имеющие температуру плавления около 600°С. На поверхности труб или крепежных деталей при tст > 610 °С
они образуют жидкую пленку, обладающую высокой окислительной способ- ностью по отношению к сталям разного типа (углеродистой, легированной, аустенитной).
Снижение избытка воздуха в зоне горения, введение в зону горения ще- лочных присадок (жидких типа водного раствора MgCl, твердых – в форме
337
порошка магнезита и доломита), хотя и дает определенный эффект, но не приводит к кардинальному подавлению ванадиевой коррозии. Радикальным средством предупреждения коррозии могла бы быть очистка сжигаемого ма- зута от примесей ванадия и натрия, но такая нефтепереработка довольно до- рогая и потребует строительства специальных заводов. Поэтому кардиналь- ным решением этой проблемы для паровых котлов, сжигающих мазут, яви- лось понижение температуры перегретого пара (основного и промежуточного перегревателей) до 545 °С, хотя при этом снижается термодинамический КПД цикла перегретого пара. Но зато в эксплуатационных условиях (с учетом тем- пературных разверок) температура металла труб пароперегревателя не дости- гает 600 °С и коррозии могут подвергаться лишь крепежные конструкции «горячих» пакетов, которые выносят за пределы газохода. В конвективной шахте котла, где часто располагаются выходные «горячие» пакеты паропере- гревателя из горизонтальных змеевиков, широко используют так называемые подвесные трубы, охлаждаемые водой или слабоперегретым паром в качестве крепежных элементов, что исключает их коррозию. При сжигании других ви- дов топлив этот тип коррозии не имеет место.
11.6.Примеры и контрольные вопросы
11.6.1.Примеры
1.Определить плотность экранирования стен топочной камеры котель- ного агрегата ПК-10 Ш, если ширина топочной камеры bт = 9,77 м, наружный
диаметр труб dн |
= 0,076 м, число труб фронтового экрана n = 102 шт. |
||||
Решение: шаг труб фронтового экрана определяем по формуле: |
|||||
S = |
bт |
|
= |
9, 77 |
= 0, 095 мм. |
|
|
||||
1 |
n +1 |
|
102 +1 |
||
|
|
Плотность экранирования стен топочной камеры находим по формуле:
sэ = S1 / dн = 0,095/0,076 =1,25 .
2. Определить ширину топочной камеры котельного агрегата ПК-10 Ш, если наружный диаметр труб dн = 0,06 м, плотность экранирования стен то-
почной камеры sэ = 1,33, число труб фронтового экрана n = 180 шт. Решение: шаг труб фронтового экрана определяем по формуле:
S1 = sэ × dн =1,33 × 0,06 = 0,08 м.
Ширину топочной камеры определяем по формуле:
338
bт = S1 (n + 1) = 0,08(180 + 1) =14,48 м.
11.6.2.Контрольные вопросы
1.Назовите типы экранов, используемые в топках паровых котлов.
2.Зачем производят секционирование экранов при естественной цирку- ляции? Как обеспечивается самостоятельная работа секции?
3.Что такое пояс жесткости? Какие задачи он решает?
4.Почему в топке прямоточного котла не удается обеспечить однохо- довое подъемное движение рабочей среды по всем стенам топки?
5.Перечислите возможные схемы размещения лент (панелей) на стенах топки прямоточного котла.
6.В чем состоят преимущества газоплотных топочных экранов?
7.Как обеспечивается газовая плотность топки, работающей под надду-
вом?
8.Как обеспечивают надежную работу футерованного экрана?
9.Каким показателей определяется надежность сваренных газоплотных панелей? Какие методы применяют для повышения надежности?