
TLKMTs
.pdfh1,b1,l1 – высота, ширина и длина параллелепипеда после деформации.
При прокатке является заданной наперед высотная деформация полосы h0/h1. Продольная деформация, или вытяжка, λ=l1/l0 может быть определена вполне точно лишь при знании величины поперечной деформации b1/b0.
В некоторых случаях (прокатка широких полос, листовb0 / h0 > 5)
величиной уширения можно пренебречь. То есть полагать b0=b1. Тогда из выражения (2.9) находим:
h0/h1=l1/l0
При прокатке толстых листов из слябов, когда ширина сляба недостаточна для того, чтобы прокатать лист требуемой ширины, процесс прокатки ведут в две стадии.
Сначала производят прокатку сляба в поперечном направлении до получения необходимой ширины. Для этого раскат прокатывают с "выверсткой", то есть с поворотом в горизонтальной плоскости на 900, при этом вследствие удлинения происходит раскатка исходной ширины, а начальная длина практически не изменяется. Затем, после получения необходимой ширины, раскат опять поворачивают на 900 и прокатку ведут в продольном направлении.
На практике закон постоянства объема используют при прокатке с "выверсткой" когда необходимо расчетом определить промежуточную толщину hпр, при которой ширина раската достигнет требуемого размера
bпр=b1. Это можно сделать, используя условие постоянства объема |
(2.10) |
h0b0l0=hпрbпрlпр=h1b1l1. |
|
Расчет ведут без учета уширения, принимая l0=lпр: |
|
hпр=h0 b0 / b1. |
(2.11) |
Конечную длину полосы также определяют из уравнения (2.10): |
|
ll=hпрbпрlпр/h1b1. |
(2.12) |
Настройка стана |
|
Настройка стана заключается в регулировке валков и установке требуемого расстояния между валками для получения полосы заданного размера.
Регулировка валков с гладкой бочкой сводится к достижению параллельности осей валков. Если валки непараллельны, то одна кромка прокатанной полосы получается тоньше другой.
Вытяжка отдельных элементов металла по ширине полосы зависит от величины обжатия, следовательно, после прокатки кромки полосы будут разной длины и поэтому она искривится, Искривление происходит в сторону большей толщины полосы (в сторону меньшей вытяжки).
При наличии искривления полосы производят регулировку валков, то есть поджатие одной стороны валков по отношению к другой. Это может быть осуществлено путем раздельной работы нажимными винтами.
Регулировка калиброванных валков наряду с установкой валков параллельно друг другу предусматривает совмещение ручьев верхнего валка с соответствующими ручьями нижнего валка.
После регулировки валков необходимо установить раствор валков, обеспечивающий прокатку полосы заданной толщины. При этом нужно учитывать, что под действием силы прокатки элементы рабочей клети упруго деформируются. Суммарная упругая деформация состоит из следующего:
•упругого прогиба валков и упругого радиального сжатия их бочек и шеек;
•упругого сжатия вкладышей, подушек, нажимных винтов;
•упругого растяжения (с изгибом) стоек станин;
•упругого изгиба верхней и нижней поперечин станин.
В результате всех перечисленных деформаций расстояние между валками при прокатке увеличивается и толщина полосы становится больше, чем установленный до прокатки зазор. Следовательно, чтобы получить требуемую толщину полосы h1 ,необходимо установить раствор валков:
h=h1-fc, |
(2.13) |
где fс – суммарная упругая деформация клети. |
полосы, ввиду ее |
При этом упругой деформацией самой |
незначительности, можно пренебречь. Величина fс обычно находится из зависимости
fс =f(Р), |
(2.14) |
которая иногда называется "упругой характеристикой стана". Получают эту зависимость для каждого стана в отдельности экспериментально, путем измерения усилия прокатки и величины упругой деформации рабочей клети.
Материальное обеспечение
1Лабораторный прокатный стан.
2Микрометр, штангенциркуль.
3Образцы из технического свинца:
h0=8 мм, |
b0=40 мм, |
l0=80 мм |
- 1 шт; |
h0=5 мм, |
b0=60 мм, |
l0= 80 мм |
- 1 шт. |
4 Прямоугольные полосы из алюминия толщиной 1,0…1,5 мм, шириной 20 мм (3 шт.) и 40 мм (3 шт.), длиной 100 мм
Порядок проведения экспериментов Работа состоит из трех частей.
В первой части изучают геометрические параметры, характеризующие очаг деформации при прокатке, приобретая навыки практического их определения (опыт 1). Во второй части осуществляют опытную проверку закона постоянства объема и применяют его при
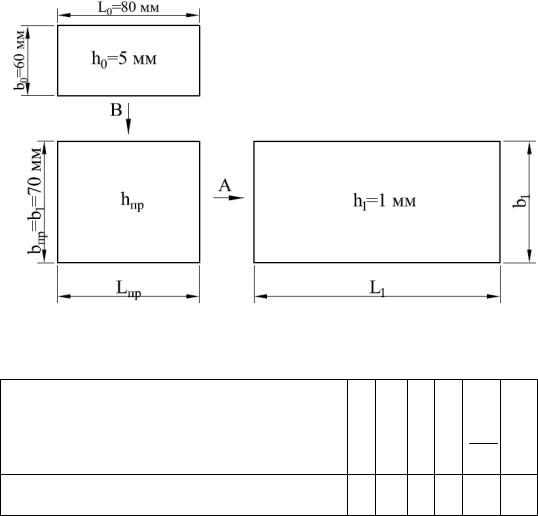
прокатке с "выверсткой" (опыты 2 и 3). В третьей части приобретают навыки настройки стана на прокатку полосы нужной толщины, определяют упругую деформацию рабочей клети (опыт 4).
Опыт 1. Прокатку свинцового образца размерами 8х50х100 мм произвести за 4 пропуска с обжатиями 3, 2, 1, 0,5 мм. Для каждого пропуска определить значения толщины и ширины образца, занести количественные результаты опыта в таблицу 2.1.
Опыт 2. Для опытной проверки закона постоянства объема и его практического применения взять образец размерами 5х60х80 мм. Тщательно измерить исходные размеры h0, b0,l0. Необходимо получить лист шириной 70 мм и толщиной 1 мм. Для получения требуемой ширины образец необходимо прокатать в направлении В (рисунок 2,2) за один пропуск. Предварительно необходимо расчетом определить промежуточную толщину hпр. Затем образец "выверстать" и катать в направлении А до получения конечной толщины h1=1 мм с обжатиями за каждый проход h≈1 мм. Замерив размеры образца после первого и второго пропусков, проверить закон постоянства объема.
Рисунок 2.2 – Схема прокатки с выверсткой
Таблица 2.1-Геометрические параметры очага деформации
Номер пропуска |
h |
h |
мм,h |
b |
b |
ммb, |
мм,l |
,α |
λ |
|
,мм |
,мм |
|
,мм |
,кН |
|
|
|
|
|
0 |
1 |
|
0 |
1 |
|
|
|
|
|
|
|
|
|
|
|
|
|
|
ε ,% F0 ,мм2 F1 ,мм2 h ,cp
l b0 hcp h0
Количественные данные опыта занести в таблицы 2.2, 2.3.

Таблица 2.2 – Данные опытной проверки закона постоянства объема
Замер |
h0, |
b0, |
|
l0,м |
h1, |
|
b1, |
|
l1, |
Объем образца, мм3 |
|
|
|||||
|
мм |
мм |
|
м |
мм |
|
мм |
|
мм |
|
|
|
|
|
|
|
|
|
|
|
|
|
|
|
|
|
|
|
|
|
|
Последеформации |
|
||
|
|
|
|
|
|
|
|
|
|
|
Додеформации |
|
|||||
Таблица 2.3 –Опытные данные прокатки с "выверсткой" |
|
|
|||||||||||||||
Параметры |
|
|
h0, |
|
|
b0, |
l0, |
|
hпр, |
h1, |
|
b1, |
l1, |
|
|||
полосы |
|
|
мм |
|
|
мм |
мм |
|
мм |
мм |
|
мм |
мм |
|
|||
Дано |
|
|
|
|
|
|
|
|
|
|
|
|
|
|
|
|
|
Получено |
|
|
|
|
|
|
|
|
|
|
|
|
|
|
|
|
|
расчетом |
|
|
|
|
|
|
|
|
|
|
|
|
|
|
|
|
|
Измерено |
|
|
|
|
|
|
|
|
|
|
|
|
|
|
|
|
|
фактически |
|
|
|
|
|
|
|
|
|
|
|
|
|
|
|
|
Пользуясь уравнением постоянства объема, определить расчетом конечную длину полосы.
ОПЫТ 3. Проверить параллельность валков. С этой целью прокатать алюминиевый образец шириной 20 мм с относительным обжатием ε=20…30%. Предварительно установить раствор валков, равный исходной толщине полосы. Для этого заготовку ввести между вращающимися валками с выходной стороны клети на длину 20…30 мм и верхний валок опускать до тех пор, пока полоса не будет выброшена валками.
Если прокатанная полоса имеет "серповидность", то необходимо опустить или поднять соответствующий винт нажимного механизма. Параллельность валков можно считать достигнутой по устранении "серповидности" полосы.
Для определения упругой деформации рабочей клети прокатать 3 образца шириной b0 =20 мм и 3 образца шириной b0=40 мм с обжатиями 20,30 и 40%. Образцы должны быть вырезаны из одного листа.
При прокатке фиксировать величину обжатия по указателю раствора
валков ( |
z) и усилие прокатки P с помощью месдоз. Размеры образцов до и |
||||||||||
после прокатки и значения ( |
z) и Р занести в таблицу 2.4. |
|
|
|
|||||||
|
Таблица 2.4 – Опытные данные по определению упругой деформации |
||||||||||
|
|
|
|
клети |
|
|
|
|
|
|
|
|
Геометрические |
Обжатие |
|
|
|
|
|
||||
|
параметры полосы |
P, |
|
z, |
F, |
|
|||||
|
|
|
|
|
|||||||
|
h0, |
|
b0, |
h1, |
h, |
|
|
|
|||
|
|
ε,% |
кН |
|
мм |
мм |
|
||||
|
мм |
|
мм |
мм |
мм |
|
|
||||
|
|
|
|
|
|
|
|
Обработка результатов экспериментов. Количественные результаты опытов занести в таблицы 2.1 и 2.4.
Вычисление геометрических параметров очага деформации произвести по формулам (2.1)…(2.8). Расчет необходимого промежуточного обжатия при прокатке с "выверсткой" осуществлять по формуле (2.11), а расчет конечной длины полосы – по формуле (2.12). По формуле (2.14) определить величину упругой деформации клети и построить графики зависимостей fc=f(P) и fc=f( h) для полос шириной b0=20 и 40 мм. По расчетным данным опыта 1 построить диаграмму фактического распределения обжатий и вытяжек по проходам.
На основе анализа результатов экспериментов сделать заключение о возможности использования закона постоянства объема в практических расчетах.
Проанализировать характер упругой характеристики рабочей клети лабораторного стана.
Контрольные вопросы
5Что такое очаг деформации?
6В чем отличие между геометрическим и физическим очагами деформации?
7Какие величины характеризуют геометрический очаг деформации?
8Какие параметры очага деформации определяют напряженно- деформи-рованное состояние и кинематику течения металла в очаге деформации?
9Каковы условия моделирования процесса прокатки?
10Как диаметр валков влияет на длину очага деформации при прокатке?
11Как определяется вытяжка полосы при прокатке?
12В чем заключается закон постоянства объема?
13Каково практическое значение закона постоянства объема?
14Как опытным путем проверить проявление закона постоянства
объема?
15Что такое прокатка с "выверсткой", и в каких случаях к ней прибегают?
16В каких случаях прокатки уширение можно не учитывать?
17Какой параметр стана ограничивает длину сляба при прокатке с "выверсткой"?
18Почему происходит уплотнение литого металла при горячей прокатке?
19В чем заключается настройка стана?
20Чем обусловлен дефект "серповидности" полосы?
21Укажите составляющие упругой деформации клети, Как определить упругую характеристику клети?
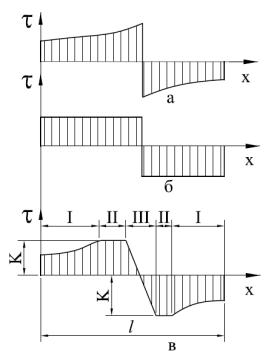
3 ЛАБОРАТОРНАЯ РАБОТА №3
ИЗУЧЕНИЕ УСЛОВИЙ ЗАХВАТА МЕТАЛЛА ПРИ ПРОКАТКЕ. ОПРЕДЕЛЕНИЕ КОЭФФИЦИЕНТА ТРЕНИЯ
Цель работы – определение максимального угла контакта в момент захвата и при установившейся прокатке, а также соотношения между этими величинами; изучение влияния внешнего трения на условия захвата металла валками; практическое определение коэффициента трения.
Общие указания В валки металл втягивается благодаря силам трения, которые
появляются на поверхности контакта металла с валками под влиянием усилия, возникающего при обжатии полосы по высоте. Контактное трение оказывает влияние на условия захвата металла валками, а характер распределения на контакте касательных напряжений влияет на напряженное состояние и кинематику течения металла в очаге деформации. Поэтому выявление величины и характера распределения касательных напряжений на контакте является необходимым условием при определении силовых и кинематических параметров процесса прокатки теоретическим путем.
а – по закону сухого трения; б – по закону постоянных касательных напряжений; в – по закону скольжения-прилипания
Рисунок 3.1 – Схемы распределения касательных напряжений на контактных поверхностях валков
Существует несколько предположений о законе распределения касательных напряжений на контактных поверхностяхвалков.
Кнаиболее распространенным следуетотнеститакиезаконы:
Закон сухого трения (закон Кулона-Амонтона). Законоснованна предположении, что прокатываемый металл по поверхности валков скользит по всей дуге контакта: в зоне отставания – против направления вращения валков, а в зоне опережения – по направлению вращениявалков(рисунок3.1,а).
Контактные касательные напряжения τ пропорциональны
нормальным напряжениям Px: ( закон Зибеля). Согласно этому закону касательные напряжения принимают
τ = Pxf , |
(3.1) |

где f – коэффициент внешнего трения.
Закон постоянных касательных напряжений. Согласно этому закону касательные напряжения принимают по всей длине дуги контакта постоянными (рисунок 3.1,б):
τ = 2Kf =const , |
(3.2) |
где К – сопротивление металла чистому сдвигу.
Закон скольжения-прилипания. Согласно этому закону по длине дуги контакта имеют место зоны скольжения и прилипания (рисунок 3.1,в).
Относительная протяженность этих зон, а также характер распределения касательных напряжений на контакте зависят от ряда
факторов, в том числе от l/hср и f. Зона прилипания имеет место при
τx = K .
При прокатке величина угла контакта α не может увеличиваться безгранично. Пределы, до которых при данном диаметре валков можно увеличивать обжатие, а следовательно, и угол контакта, могут быть установлены из условия свободного захвата металла валками, если рассмотреть равновесие сил, действующих со стороны валков на прокатываемую полосу, в момент соприкосновения валков с ее передним концом. При этом в точке А, положение которой определяется величиной угла α, будут действовать силы: радиальная (нормальная) Р и сила трения (касательная) Т (рисунок 3.2).
Рисунок 3.2 – Схема сил при захвате полосы валками
Очевидно, что соотношение между горизонтальными проекциями Рх и Тх этих сил будет определять возможность осуществления захвата полосы валками. При Тх>Рх захват произойдет. При Тх=Рх будет иметь
место равновесие: вращающиеся валки не будут ни втягивать полосу в очаг деформации, ни выталкивать полосу из него.
Поскольку Тх=Тcosα, Px=Psinα, а Т=fР, то tgαз=f.
Так как захват металла валками возможен лишь при Тх>Рх, то tgαз=f. (3.3)
При установившейся прокатке, то есть когда весь очаг деформации заполнен металлом, можно провести аналогичные рассуждения. В первом приближении можно принять равномерное распределение контактных напряжений по дуге контакта. При таком допущении равнодействующая Р переместится к середине очага деформации. Точка ее приложения определится половиной угла контакта α/2.
При этом условии установившийся процесс становится осуществим, когда
tg(αy / 2) < f. |
(3.4) |
В пределах практически осуществимых углов контакта можно приближенно принять tgα ≈ α, тогда полученные неравенства запишутся в
виде: |
|
αз <f ; αу / 2 <f. |
(3.5) |
Из сопоставления указанных выражений следует, что |
|
αу / αз ≈ 2, |
(3.6) |
то есть после захвата металла валками можно увеличивать обжатие |
h . |
Методы определения коэффициента трения Из известных наиболее распространены следующие методы
определения коэффициента трения при прокатке: по максимальному углу захвата, по опережению, клещевой метод, метод Бленда-Форда.
Метод определения коэффициентов трения по максимальному углу захвата
Метод заключается в следующем (см.рисунок 3.2).
Для сведенных валков горизонтальная составляющая Тх, которая способствует втягиванию металла в валки, мала и естественного захвата не произойдет. Если начать разводить валки, а полосу держать в соприкосновении с валками, то наступит момент, когда горизонтальные составляющие Тх и Рх будут равны. При наступлении равновесия системы сил наблюдается легкое вздрагивание образца.
При дальнейшем минимальном увеличении зазора между валками произойдет захват металла, так как выполняется условие (3.3).
Данный метод позволяет определить коэффициент внешнего трения в момент захвата.

Метод определения коэффициента трения по опережению Опережение может быть теоретически подсчитано по формуле
S = R γ2 , (3.7) h1
Где R – радиус валка;
γ – нейтральный угол; h1 – конечная толщина.
Формула, связывающая значения углов (нейтрального γ, захвата α и
трения β), имеет вид |
|
|
|
γ = α(1− |
α |
) |
(3.8) |
|
|||
2 |
2β |
|
|
Величину опережения S получают экспериментально (методом |
|||
кернов), подставляют в теоретическую формулу |
(3.7) и решают ее |
относительно величины γ.
Коэффициент трения определяют по зависимости (3.8) с учетом того,
что f = tgβ.
Однако этот метод недостаточно точен из-за большого числа допущений при выводе формул опережения и трудности точного измерения опережения.
Клещевой метод определения коэффициента трения Метод служит для определения коэффициента трения
непосредственно при прокатке. Полосу задают в валки, а с задней стороны захватывают клещами для создания натяжения Т0, обеспечивающего пробуксовку полосы (рисунок 3.3).
Рисунок 3.3 – Схема сил в очаге деформации и распределение касательных напряжений при определении коэффициента трения клещевым методом

Из условия равновесия: Т0+2Рх-2Тх=0; Т0+2Руtg(α/2)-2Руf=0 находят:
f=Т0/2Ру + tg(α/2).
Величины Т0 и Ру определяют экспериментально, угол α вычисляют. Этот метод предполагает равномерное распределение касательных напряжений одного знака на контактной поверхности.
Метод Бленда-Форда В этом методе задним натяжением Т0 полосы добиваются, чтобы
опережение S стало равным нулю, то есть скорость движения полосы на выходе из валков была равна окружной скорости валков (V1=Vb). В этом случае нейтральное сечение будет близким нулю, то есть γ→0, и тогда силы трения будут действовать на контактной поверхности в одном направлении. По измеренным крутящему моменту М на валке и равнодействующей контактных сил Р можно определить коэффициент трения μу при установившемся процессе прокатки:
fy = PRM ,
где R – радиус валка.
Материальное обеспечение
1.Лабораторный прокатный стан.
2.Микрометр (или штангенциркуль).
3.Образцы из технического свинца в виде параллелепипеда с
размерами |
|
|
10х30х80 мм |
- 2 шт. |
|
4. Клиновидные образцы (рисунок 3.4) |
- 2 шт. |
Порядок проведения экспериментов В соответствии с особенностями определения углов контакта и
коэффициентов трения при захвате и установившейся прокатке работа предусматривает два опыта.
ОПЫТ 1. Определение максимального угла αз при захвате При проведении опыта используют образцы с размерами 10х30х80
мм. Перед прокаткой тщательно измеряют их толщину и записывают результаты измерения в таблицу 3.1.
Необходимо следить за тем, чтобы передняя грань образца была строго перпендикулярна его продольной оси, чтобы передние кромки образца были прямолинейны и на них не было заусенцев, так как эти дефекты существенно влияют на условия захвата.
Таблица 3.1 – Опытные данные определения углов контакта
|
|
и коэффициентов внешнего трения при прокатке свинца |
|||||||
Образец |
h0, |
H1 |
|
D1 |
|
|
fз |
|
Состояние |
h, |
αз, |
αy, |
fу |
поверхности валков, |
|||||
|
мм |
, |
, |
рад |
рад |
|
|
условия смазки |
|
|
|
мм |
мм |
мм |
|
|
|
|
|