
TLKMTs
.pdf
Перед проведением эксперимента валки сводят (зазор между валками должен быть 3 мм ), затем, слегка прижимая образец к вращающимся валкам, постепенно разводят их. Перед втягиванием металла в валки появится вибрация образца. При дальнейшем минимальном увеличении зазора между валками образец будет втянут и прокатан.
Прокатать два образца: без смазки и со смазкой. Измерить толщину образцов после прокатки.
ОПЫТ 2. Определение максимального угла контакта при установившейся прокатке
При проведении опыта используют клиновидные образцы (см.рис 3.4).. Образцы задают в валки тонким концом. Предварительный зазор в валках 2…3 мм. Валки будут втягивать клиновидную полосу, обжимая ее до толщины h1. Поскольку толщина участков клина, поступающих в валки, непрерывно возрастает, так же непрерывно растет и абсолютное обжатие h.
Рисунок 3.4 – Клиновидный образец
В какой-то момент времени валки начнут буксовать. После этого стан останавливают, валки разводят, образец извлекают из валков и на нем измеряют h0 и h1. По этим величинам определяют абсолютное обжатие h, а затем с помощью формул – максимальный угол αу и величину коэффициента трения fу. Прокатать два образца: один без смазки, а второй со смазкой.
Обработка результатов экспериментов Количественные результаты опытов занести в таблицу 3.1. Значение
углов αз, αу и коэффициентов трения fз, fу определить по формулам (3.3), (3.4).
На основе анализа результатов эксперимента сделать выводы о зависимости максимальных углов в момент захвата и при установившейся прокатке от коэффициентов внешнего трения, а также о степени отклонения опытного значения отношения αу/αз от теоретического. Проанализировать положительную и отрицательную роль трения при прокатке.
Контрольные вопросы
5.Как влияет внешнее трение на усилие деформации и расход энергии при прокатке?
6.Как распределяются касательные напряжения по закону сухого
трения?
7.Как распределяются касательные напряжения по закону Зибеля?
8.Как распределяются касательные напряжения по закону скольжения-прилипания?
9.В чем заключается метод определения коэффициента трения по максимальному углу контакта?
10.В чем сущность метода определения коэффициента трения по опережению?
11.В чем заключается метод Бленда-Форда?
12.Каково условие свободного захвата металла валками?
13.Как улучшить условие захвата металла валками при прокатке?
14.Как изменяется направление равнодействующей контактных сил при захвате, если зазор между валками возрастает?
15.Укажите технологические параметры, определяемые экспериментально, при нахождении коэффициента трения методом БлендаФорда.
16.Как определить максимальный угол контакта при установившейся прокатке?
17.Каково соотношение между углами контакта при установившейся прокатке и в момент захвата?
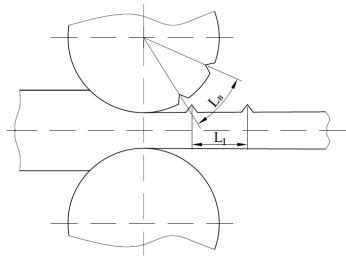
4 ЛАБОРАТОРНАЯ РАБОТА №4
ИССЛЕДОВАНИЕ ОПЕРЕЖЕНИЯ ПРИ ПРОКАТКЕ В ГЛАДКИХ ВАЛКАХ
Цель работы – практическое изучение явления опережения при прокатке; изучение влияния на величину опережения отношения l/hср и угла контакта.
Общие указания Вследствие закона наименьшего сопротивления и закономерностей ,
изученных в лабораторной работе №1, скорости переднего V1 и заднего V0 концов полосы, проходящей через очаг деформации , и окружная скорость
самих валков Vb не одинаковы: |
|
V0<Vb<V1. |
(4.1) |
Явление, когда скорость выхода полосы из валков превышает |
|
окружную скорость самих валков, называется опережением. |
|
Опережение определяется по формуле S=(V1-Vb)/Vb.
Опережение является важным параметром прокатки при настройке непрерывных станов. В зависимости от величины опережения при данной схеме обжатия и величины натяжений определяют угловую скорость валков.
Экспериментально опережение можно определить методом кернов
(рисунок 4.1) с учетом пропорциональности скоростей и перемещений: |
|
S=(l1-lb)/lb, |
(4.2) |
где lb – длина дуги между кернами на валке; |
|
l1 – расстояние между отпечатками на полосе. |
|
Рисунок 4.1 – Схема определения опережения методом кернов.
На поверхность валка на некотором расстоянии друг от друга накернивают углубления, которые при прокатке полосы дают отпечатки на ней в виде бугорков. При замере легко обнаружить, что расстояние между бугорками l1 на полосе больше расстояния между углублениями на поверхности валка lb.
При горячей прокатке, когда l1 измеряют после остывания металла,
необходимо делать поправку на изменение за счет температуры: |
|
||
|
|
l1 =l1[1+αT (t10 − t00 )], |
(4.3) |
где t0 |
и t0 |
– температуры прокатки и измерения; |
|
1 |
0 |
|
|
αт – коэффициент линейного температурного расширения материала полосы.
Величина опережения зависит от геометрических размеров очага
деформации, условий трения на контактной поверхности и |
натяжений |
||||||
(подпоров): |
|
|
|
|
|||
S=f(l/hcp;α; b0/l; σ0; f) , |
(4.4) |
||||||
где α – угол контакта; |
|
|
|
|
|||
σ1, σ0 – напряжения переднего и заднего натяжений; |
|
||||||
f – коэффициент трения. |
|
|
|
|
|||
Чем больше l/hcp;α; b0/l; σ1 и f1 тем больше опережение. |
|
||||||
Заднее натяжение уменьшает опережение. |
|
||||||
Опережение может быть подсчитано по формуле Дрездена: |
|
||||||
|
|
P1 |
|
γ2 , |
(4.5) |
||
|
|
h |
|||||
1 |
|
|
|
|
|
||
Где γ – нейтральный угол. |
|
|
|
|
|||
Нейтральный угол γ может быть определен при прокатке тонких полос |
|||||||
(l/hcp>3) по формуле Финка: |
|
|
|
|
|||
sin γ = |
sin α |
− |
1−cosα |
, |
(4.6) |
||
|
|
||||||
2 |
|
|
2f |
|
|||
где α – угол контакта. |
|
|
|
|
Эта формула получена в предположении равномерного распределения скоростей по высоте сечений очага деформации и дает удовлетворительные результаты при прокатке относительно тонких полос в условиях плоской деформации (l/hcp>3; b0/l>5).
При прокатке толстых и средних полос, когда l/hcp<3, опережение может быть подсчитано по формулам, полученным В.Ф.Потапкиным на основе метода полей линий скольжения и учитывающим неравномерное
распределение скоростей по вертикальным сечениям очага деформации: |
|
|
|
S=1+32αl/hcp – при l/hcp≤z; |
(4.7) |
|
S=3,8+0,62(α-5) – при 1<l/hcp<2,5, |
(4.8) |
где S – опережение, %; |
|
|
|
α – угол контакта, град. |
|
|
Материальное обеспечение |
|
1 |
Лабораторный прокатный стан. |
|
2 |
Свинцовые образцы размерами: |
|
8х50х150 мм -1 шт.; |
|
|
4х50х150 мм- 1 шт. |
|
|
3 |
Штангенциркуль. |
|
Порядок проведения экспериментов
ОПЫТ 1. Определение зависимости опережения от l/hcp при прочих равных условиях
Для этого образец размерами 8х50х150 мм прокатать за 5 пропусков с одинаковыми обжатиями h=1,5 мм.
Перед прокаткой на поверхности одного из валков наносят керны и замеряют расстояние между ними по дуге lb (см.рисунок 4.1).
ОПЫТ 2. Определение зависимости опережения от угла контакта при постоянном отношении l/hcp
Для этой цели прокатывают 2 свинцовых образца: образец размерами
8х50х150 мм прокатать с |
обжатием h =3,0 мм, а образец размерами |
4х50х150 мм – с обжатием |
h=0,9 мм. |
Обработка результатов экспериментов Исходные и конечные размеры образцов и расстояния между
отпечатками на полосе в опытах после каждого пропуска занести в таблицу 4.1.
Для случаев, когда l/hcp ≥3, величину опережения определить по формуле Дрездена, а при l/hcp<3 – по формуле В.Ф.Потапкина.
По опытным и расчетным данным построить графические зависимости S=f(l/hcp).
Таблица 4.1 – Опытные и расчетные исследования опережения при прокатке
|
Про-пуск |
h0, |
h1, |
h, |
b0, |
b1, |
|
l |
|
α, |
|
b0 |
|
Sэк, |
Sт.ср., |
Опыт |
|
hcp |
|
|
l |
|
|||||||||
мм |
мм |
мм |
мм |
мм |
|
|
|
рад |
|
|
|
% |
% |
||
|
|
|
|
|
|
|
|
|
|
|
|
|
|
Проанализировать влияние отношения l/hcp и угла контакта на величину опережения.
Контрольные вопросы
1.Какое явление называют опережением?
2.Назовите экспериментальные методы определения опережения. В чем их сущность?
3.Перечислите факторы, влияющие на величину опережения. Выделите группу факторов, вызывающих уменьшение опережения.
4.Как влияют на опережение переднее и заднее натяжения?
5.Как влияет на опережение ширина полосы? Объясните.
6.Как влияет на величину опережения степень деформации металла?
7.Какое влияние на опережение оказывает угол контакта?
8.Какое влияние на опережение оказывает рост диаметра валков при прочих разных условиях?
9.Какоевлияниенаопережениеоказываетизменениеотношенияl/hcp?
10.Как подпоры влияют на величину опережения?
11.На каких станах необходимо точно учитывать опережение? Почему?
12.Из каких соображений выбирают угловые скорости валков
непрерывных станов?
5 ЛАБОРАТОРНАЯ РАБОТА № 5
ИССЛЕДОВАНИЕ УШИРЕНИЯ ПРИ ПРОКАТКЕ В ГЛАДКИХ ВАЛКАХ
Цель работы – изучение влияния коэффициента внешнего трения, относительного обжатия, ширины полосы, числа проходов (дробности деформации) на уширение металла при прокатке; выявление зависимости распределения уширения по ширине полосы; ознакомление с формулами для подсчета уширения и оценка их точности.
Общие указания При прокатке наряду с уменьшением высоты заготовки (обжатием) и
ее удлинением (вытяжкой) происходит также увеличение ширины прокатываемой полосы, называемое уширением. В большинстве случаев уширение представляет собой отрицательное явление, так как оно снижает общую вытяжку при прокатке и вызывает в боковых кромках полосы значительные растягивающие напряжения. В то же время при прокатке фасонных профилей благодаря уширению добиваются лучшего заполнения калибров. Чаще всего для оценки величины уширения пользуются выражением (2.3).
Реже для этой цели используют понятия относительного уширения εb =(b1 −b0) / b0 и коэффициента уширения β= b1 / b0 .
При анализе уширения учитывают напряженное состояние полосы при прокатке, которое характеризуется трехосным сжатием (рисунок 5.1). Согласно закону наименьшего сопротивления при пластической деформации основная масса металла в результате обжатия перемещается в продольном направлении. Однако в некоторых случаях напряжения σZ и σ X по своей величине приближаются друг к другу и соответственно возрастает величина уширения.
Для теоретического анализа А.И. Целиковым , Б.П. Бахтиновым, Д.И. Старченко и другими принята схема развития уширения в очаге деформации, представленная на рисунке 5.1.
Согласно этой схеме очаг деформации делится на четыре зоны: две из них (I и II), прилегающие к боковым кромкам, называются зонами стремления металла к уширению. Необходимо отметить, что такое деление очага деформации условно, так как полоса в очаге деформации ведет себя как единое целое, и для ее движения характерно постоянство коэффициентов вытяжек элементарных полосок по ширине. В результате, благодаря влиянию внешних зон, часть металла, находящегося в зонах I и II, деформируется в продольном направлении и, наоборот, часть металла из зон III и IY смещается в поперечном направлении.
На величину уширения оказывает влияние большое количество факторов.
Вследствие закона наименьшего сопротивления с изменением величины обжатия происходит изменение напряженного состояния по всем трем осям.

Рисунок 5.1 – Схема очага деформации при прокатке
При прокатке с малыми обжатиями происходит уменьшение протяженности очага деформации в продольном направлении при сохранении его поперечных размеров. Таким образом, объемное напряженное состояние характеризуется в этом случае сильным возрастанием поперечных напряжений по сравнению с продольными, что способствует увеличению вытяжки и уменьшению уширения.
При больших обжатиях соотношение между продольными и поперечными напряжениями за счет увеличения продольной протяженности очага деформации изменяется в пользу уширения и величина последнего возрастает. По этой причине при прокатке полосы в несколько отдельных пропусков с общим обжатием hc суммарное уширение получается меньшим по сравнению с прокаткой за один проход с тем же обжатием hc ..
Изменение коэффициента трения в первую очередь повлияет на деформацию в том направлении, в котором происходит преимущественное перемещение металла относительно валков, то есть для обычных случаев прокатки– в направлении вытяжки. Но так как продольная и поперечная деформации связаны между собой уравнением постоянства объема, то при постоянстве обжатия изменение коэффициента трения скажется прямым образом на вытяжке и косвенно– на уширении.
С понижением коэффициента трения (смазка валков) при данном обжатии, когда облегчается течение металла в продольном и поперечном направлениях, получает приращение лишь вытяжка, а уширение, напротив, уменьшается. С ростом коэффициента трения уменьшается вытяжка

металла и возрастает уширение. Если есть отступление от этого правила, то причину следует искать в особых условиях напряженного состояния.
При изменении ширины полосы напряженное состояние изменяется, главным образом, в направлении одной оси. Если увеличивать ширину полосы, то при постоянстве всех прочих условий происходит резкое возрастание поперечных напряжений с соответствующим ростом отношения этого напряжения к продольному. Понятно, что при этом поперечная деформация затрудняется, а продольная облегчается. При
прокатке узких |
полос, |
напротив, значения напряжений |
σX и σY |
(см. рисунок 5.1) |
более |
близки друг к другу, как и |
величины |
соответствующих деформаций.
Внешние зоны вызывают существенное уменьшение уширения. Поэтому в средней по длине части полосы уширение всегда меньше, чем на концах. Действие внешних зон на уширение состоит в стремлении выровнять вытяжки, то есть деформации в продольном направлении центральной и боковых частей (кромок) прокатываемой полосы.
С увеличением переднего и заднего натяжений уширение уменьшается. Однако переднее натяжение оказывает значительно меньшее влияние на величину уширения, чем заднее. Установлено, что при наличии заднего натяжения на подходе металла к валкам в нем появляется зона утяжки, где ширина и высота сечения полосы незначительно уменьшаются. В связи с наличием этой зоны фактическая ширина полосы, входящей в валки, будет меньше исходной. Поэтому суммарная величина уширения получается значительно меньше, чем при прокатке металла без заднего натяжения.
Для подсчета уширения различными авторами было предложено довольно большое количество формул, отличающихся в основном числом учтенных факторов.
Наиболее полно все факторы, влияющие на уширение, учтены в формуле А.И.Целикова:
b = 0,58C |
|
C |
|
|
h |
h |
0 |
, |
(5.1) |
b |
σ |
R h − |
ln |
|
|||||
|
|
|
2f |
h |
|
|
|||
|
|
|
|
|
|
|
1 |
|
|
где Сb, Сσ – коэффициенты, учитывающие влияние ширины полосы (рисунок 5.2) и натяжения.
Значение коэффициента Cσ может быть найдено из выражения
Cσ =1−2σ0 / σф,
где σ0 – напряжение заднего натяжения; σф - напряжение растяжения, при котором наступает пластическая
деформация металла.
Необходимо отметить особенности измерения ширины образцов в процессе экспериментов. Дело в том, что в зависимости от условий прокатки получается различное очертание боковых граней полосы: выпуклое, вогнутое или прямолинейное. В связи в этим существует несколько методов подсчета средней ширины полосы после прокатки.
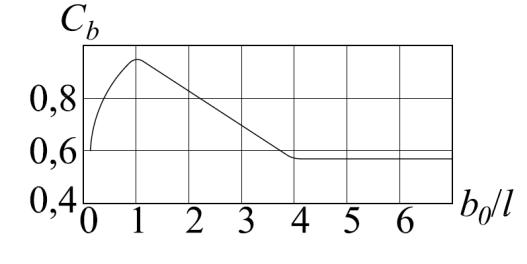
Рисунок 5.2 – Зависимость коэффициента Cb от b0/l
Метод постоянства объема Этот метод пригоден, если опытным путем определены высотная и
продольная деформации. |
Тогда из условия постоянства объема находим: |
||||||||
b |
|
= b |
h0 / h1 |
или |
b = b |
η |
, |
||
1 |
|
o l |
/ l |
0 |
|
1 |
0 λ |
|
|
|
|
|
1 |
|
|
|
|
|
а полное усредненное уширение
b= b1 −b0 = bo η −1
λ .
Метод равновеликих площадей Метод заключается в подсчете площади поперечного сечения полосы
после прокатки и в превращении сечения в равновеликий прямоугольник с высотой, равной высоте полосы. Другую сторону равновеликого прямоугольника считают шириной полосы после прокатки. Истинная площадь поперечного сечения может быть определена, например, путем вычерчивания контура поперечного сечения с последующим планеметрированием либо как частное от деления объема полосы на ее длину после прокатки.
Эмпирический метод (И.Я.Тарновского)
Ширину полосы после прокатки определяют по эмпирической формуле (рис.5.3):
b |
= b" |
+a(b' |
−b"), |
(5.2) |
1 |
1 |
1 |
1 |
|
где а=0,5…0,67 – коэффициент, учитывающий степень выпуклости боковой поверхности.

Рисунок 5.3 – Схема к расчету уширения по методу И.Я.Тарновского
Материальное обеспечение
1Лабораторный прокатный стан.
2Образцы из технического свинца:
клиновидная полоса размерами, указанными на рисунке 5.4 – 2 шт.; клиновидная полоса размерами, указанными на рисунке 5.5 – 2 шт.; полоса размерами 10х10х130 мм- 2 шт.
3Полоса из алюминия размерами 1,0х40х150 мм – 1 шт.
4Штангенциркуль, масштабная линейка, рейсмасс.
Порядок проведения экспериментов С учетом факторов, влияющих на величину уширения, работа
предусматривает выполнение нескольких отдельных опытов.
ОПЫТ 1. Установление зависимости уширения от относительного обжатия
На боковых поверхностях клиновидной полосы (см.рис. 5.4) с двух сторон произвести вертикальные риски через 10 мм. Измерить толщину образца по каждой риске и результаты занести в таблицу 5.1.
Установить зазор между валками 4…4,5 мм и прокатать образец тонким концом вперед в сухих валках. После прокатки измерить ширину и толщину образца у каждой риски. Ширину образца измерить по контактной
поверхности b" и по бочке b' . |
|
|
|
|
|
|
|
|
|
|||||
|
|
1 |
|
1 |
|
|
|
|
|
|
|
|
|
|
Таблица 5.1 – Опытные и расчетные данные исследования |
|
|
||||||||||||
|
|
|
уширения при прокатке |
|
|
|
|
|
|
|||||
Опыт |
h0, |
h1, |
h, |
ε, |
|
b0, |
b1' |
|
b1" |
b1, |
bф, |
, |
bn |
bp , |
|
мм |
мм |
мм |
% |
|
мм |
, |
|
, |
мм |
мм |
|
мм |
|
|
|
|
|
|
|
|
мм |
|
мм |
|
|
мм |
||
|
|
|
|
|
|
|
|
|
|
|
|
|