
CHAPTER 3
FCC Catalysts
The introduction of zeolite in commercial FCC catalysts in the early 960s was one of the most significant advances in the history of cat racking. Zeolite catalysts provided a greater profit with little capital vestment. Simply stated, zeolite catalysts were and still are the iggest bargain of all time for the refiner. Improvements in catalyst chnology have continued, enabling refiners to meet the demands of eir market with minimum capital investment.
Compared to amorphous silica-alumina catalysts, the zeolite catalysts re more active and more selective. The higher activity and selectivity anslate to more profitable liquid product yields and additional crack- g capacity. To take full advantage of the zeolite catalyst, refiners ave revamped older units to crack more of the heavier, loweralue feedstocks.
A complete discussion of FCC catalysts would fill another book. his chapter provides enough information to select the proper catalyst nd to troubleshoot the unit's operation. The key topics discussed are:
•Catalyst Components
•Catalyst Manufacturing Techniques
•Fresh Catalyst Properties
•Equilibrium Catalyst Analysis
•Catalyst Management
•Catalyst Evaluation
•Additives
ATALYST COMPONENTS
FCC catalysts are in the form of fine powders with an average article size in the range of 75 microns. A modern cat cracking catalyst as four major components:
•Zeolite
•Matrix
84

FCC Catalysts |
85 |
* Binder
• Filler
eolite
Zeolite, or more properly, faujasite, is the key ingredient of the FCC atalyst. It provides product selectivity and much of the catalytic ctivity. The catalyst's performance largely depends on the nature and uality of the zeolite. Understanding the zeolite structure, types, racking mechanism, and properties is essential in choosing the "right" atalyst to produce the desired yields.
eolite Structure
Zeolite is sometimes called molecular sieve. It has a well defined attice structure. Its basic building blocks are silica and alumina etrahedra (pyramids). Each tetrahedron (Figure 3-1) consists of a ilicon or aluminum atom at the center of the tetrahedron, with oxygen toms at the four corners.
Zeolite lattices have a network of very small pores. The pore diameter f nearly all of today's FCC zeolite is approximately 8.0 angstroms (°A). hese small openings, with an internal surface area of roughly 600 square
Figure 3-1. Silicon/aluminum-oxygen tetrahedron [15].


|
|
|
|
FCC Catalysts |
8? |
|
|
|
|
Table 3-1 |
|
|
|
|
|
Properties of Major Synthetic Zeolites |
|
|
||
|
Pore Size |
Silica-to- |
|
|
|
|
Zeoiite |
Dimensions |
Alumina |
|
|
|
|
Type |
(°A) |
Ratio |
Applications |
|
||
eolite A |
4.1 |
|
2-5 |
Detergent manufacturing |
|
|
aujasite |
7.4 |
|
3-6 |
Catalytic cracking and |
hydrocracking |
|
SM-5 |
5.2 |
x 5.8 |
30-200 |
Xylene isomerization, |
benzene |
|
|
|
|
|
alkylation, catalytic cracking, |
|
|
|
|
|
|
catalyst dewaxing, and methanol |
|
|
|
|
|
|
conversion. |
|
|
ordenite |
6.7 |
x 7.0 |
10-12 |
Hydro-isomerization, |
dewaxing |
|
tability than the Y zeolite. Some of the earlier FCC zeolite catalysts ontained X zeolite; however, virtually all of today's catalysts contain
zeolite or variations thereof (Figure 3-2).
ZSM-5 is a versatile zeolite that increases olefin yields and octane. ts application is further discussed later in this chapter.
Until the late 1970s, the NaY zeolite was mostly ion exchanged with are earth components. Rare earth components, such as lanthanum and
USY Zeolite (~ 7 Al Atoms/u.c.) |
Equilibrium REY (-23 Al Atoms/u.c.) |
nit Cell Dimension =24.25 A (SiO2/AI2O3=54) |
Unit Cell Dimension= 24.39 A (SiO2/AI2O3 « 15) |
Figure 3-2. Geometry of USY and REY zeolites [14].

FCC Catalysts |
89 |
ossess any activity. The UCS is related to the number of aluminum toms per cell (NAf) by [1]:
NA, + 111 x (UCS - 24.215)
he number of silicon atoms (Nsi) is;
Nsi = 192 - NA,
The SAR of the zeolite can be determined either from the above two quations or from a correlation such as the one shown in Figure 3-3. The UCS is also an indicator of zeolite acidity. Because the alumium ion is larger than the silicon ion, as the UCS decreases, the acid ites become farther apart. The strength of the acid sites is determined y the extent of their isolation from the neighboring acid sites. The lose proximity of these acid sites causes destabilization of the zeolite tructure. Acid distribution of the zeolite is a fundamental factor ffecting zeolite activity and selectivity. Additionally, the UCS easurement can be used to indicate octane potential of the zeolite. lower UCS presents fewer active sites per unit cell. The fewer acid ites are farther apart and, therefore, inhibit hydrogen transfer reactions, hich in turn increase gasoline octane as well as the production of 3 and lighter components (Figure 3-4). The octane increase is due o a higher concentration of olefins in the gasoline.
Zeolites with lower UCS are initially less active than the conentional rare earth exchanged zeolites (Figure 3-5). However, the ower UCS zeolites tend to retain a greater fraction of their activity nder severe thermal and hydrothermal treatments, hence the name ltrastable Y.
A freshly manufactured zeolite has a relatively high UCS in the ange of 24,50°A to 24.75°A. The thermal and hydrothermal environent of the regenerator extracts alumina from the zeolite structure and, herefore, reduces its UCS. The final UCS level depends on the rare arth and sodium level of the zeolite. The lower the sodium and rare arth content of the fresh zeolite, the lower UCS of the equilibrium atalyst (E-cat).
Rare Earth Level. Rare earth (RE) elements serve as a "bridge" stabilize aluminum atoms in the zeolite structure. They prevent the


FCC Catalysts |
91 |
24.24 |
24.28 |
24.32 |
24.36 |
Unit Cell Size, A
6.0
5.5
>
s t
1 5.0
«*>
o
4.5
4.0
24.20 |
24.24 |
24.28 |
24.32 |
24.36 |
Unit Cell Size, A
Figure 3-4. Effects of unit cell size on octane and C3-gas make [4].



4 Fluid Catalytic Cracking Handbook
MOTOR OCTANE VS. SODIUM OXIDE
81.5 - , ;
81.0
O 5
80.5
80.0
0.2 |
0.3 |
0.4 |
0.5 |
0.6 |
Na2O, wt% on catalyst
RESEARCH OCTANE VS. SODIUM OXIDE
94
93
92
91
0 |
1 |
2 |
3 |
4 |
5 |
Na2O, wt% on zeolite
igure 3-7. |
Effects of soda on motor and research octanes: motor octane |
. sodium |
oxide [11]; research octane vs. sodium oxide [4]. |



Na^aoHte
Crystallization
00 F, 12-24Hr
Filtrate to waste treatment
Figure 3-8, Typical manufacturing steps to produce FCC catalyst.






Data |
|
|
|
|
|
|
|
|
|
|
|
|
C.F. |
G.F. |
S.A. |
P.V. |
ABD |
0-20 |
0-40 |
|
0-80 |
APS |
AI2O3 |
|
|
|
m2/gm, |
cc/gm |
gm/cc |
wt% |
wt% |
|
wt% |
|
ppm |
69 |
1.3 |
2.2 |
147 |
0.30 |
0.83 |
0 |
10 |
|
63 |
70 |
28.9 |
69 |
1.2 |
1.9 |
148 |
0.28 |
0.83 |
0 |
7 |
|
61 |
72 |
29.1 |
70 |
1.2 |
3.1 |
147 |
0.29 |
0.84 |
0 |
8 |
|
67 |
69 |
29.2 |
69 |
1.3 |
2.6 |
148 |
0.29 |
0.83 |
2 |
9 |
|
69 |
68 |
28.7 |
68 |
1.4 |
3.2 |
148 |
0.28 |
0.83 |
0 |
6 |
|
65 |
70 |
28.7 |
69 |
1.3 |
2.6 |
150 |
0,29 |
0.84 |
0 |
9 |
|
67 |
69 |
28.7 |
69 |
1.2 |
2.3 |
148 |
0.28 |
0.85 |
2 |
10 |
|
71 |
67 |
28.7 |
67 |
1.4 |
2.8 |
148 |
0.29 |
0.85 |
0 |
7 |
|
64 |
71 |
28.8 |
70 |
1.2 |
2.9 |
148 |
0.28 |
0.84 |
4 |
10 |
|
67 |
69 |
28.8 |
|
Fe |
C |
V |
Ni |
Cu |
Sb |
UCS |
RE203 |
Z |
M |
|
|
ppm |
wt% |
ppm |
ppm |
ppm |
ppm |
|
|
|
|
|
00 |
5600 |
0.23 |
4106 |
1997 |
25 |
416 |
24.27 |
|
1.79 |
130 |
17 |
00 |
5600 |
0.23 |
4093 |
1948 |
23 |
446 |
|
|
1,80 |
130 |
18 |
00 |
5600 |
0.16 |
4051 |
1940 |
24 |
440 ' |
24.27 |
r |
1.79 |
130 |
17 |
00 |
5600 |
0.23 |
4099 |
1974 |
24 r™44i |
|
TM |
130 |
18 |
||
00 |
5600 |
0.22 |
4017 |
1942 |
24 |
445 |
24.25 |
|
1.79 |
130 |
18 |
00 |
5600 |
0.20 |
3962 |
1910 |
23 [_ 420 |
|
|
1.80 |
132 |
18 |
|
00 |
5600 |
0.24 |
3892 |
1893 |
24 |
458 |
24.27 |
|
179 |
131 |
18 |
00 |
5600 |
0.15 |
3893 L_J885 |
25 |
432 |
|
|
1.79 |
130 |
18 |
|
00 |
5600 |
0.24 |
3875 |
1873 |
24 |
409 |
24.27 |
|
1.76 |
130] |
18 |
|
|
|
Figure 3-12. |
Typical E-cat analysis. |
|
|
|
|


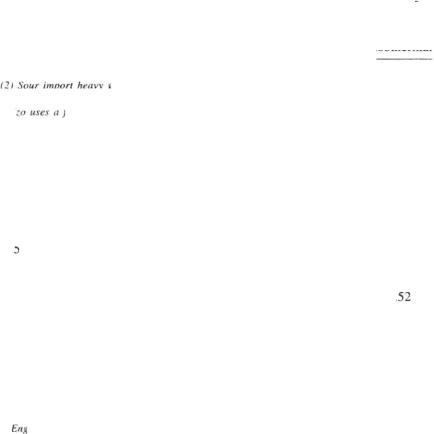

FCC Catalysts |
101 |
ore Volume (PV), cc/g
Pore volume is an indication of the quantity of voids in the catalyst articles and can be a clue in detecting the type of catalystdeactivation at takes place in a commercial unit. Hydrothermal deactivation has ery little effect on pore volume, whereas thermal deactivation decreases ore volume.
ore Diameter (°A)
The average pore diameter (APD) of a catalyst can be calculated om the E-cat analysis sheet by using the following equation:
APD(°A) = PV x 4 x 10,000
SA
Example 3-1
For an E-cat with a PV = 0.40 cc/g and SA = 120 m2/g, deterine APD,
APD = 133 °A
article Size Distribution (PSD) |
|
|
||
PSD |
is an important |
indicator of |
the |
fluidization characteristics |
f the |
catalyst, cyclone |
performance, |
and |
the attrition resistance of |
e catalyst. A drop in fines content indicates the loss of cyclone ficiency. This can be confirmed by the particle size of fines collected ownstream of the cyclones. An increase in fines content of the E-cat dicates increased catalyst attrition. This can be due to changes in esh catalyst binder quality, steam leaks, and/or internal mechanical roblems, such as those involving the air distributor or slide valves.
hemical Properties
The key elements that characterize chemical composition of the catalyst e alumina, sodium, metals, and carbon on the regenerated catalyst.
lumina (A12O3)
The alumina content of the E-cat is the total weight percent of umina (active and inactive) in the bulk catalyst. The alumina content




FCC Catalysts |
111 |
100
90
80
70
60
50
40
0.0 |
0.5 |
1.0 |
1.5 |
CRC(wt%)
igure 3-15. Catalyst activity retention vs. carbon on regenerated catalyst [12].
om the unit to control the catalyst level in the regenerator. Catalyst nes leave the unit with the regenerator flue gas and the reactor vapor. The catalyst ages in the unit, losing its activity and selectivity. The eactivation in a given unit is largely a function of the unit's mechanical onfiguration, its operating condition, the type of fresh catalyst used, nd the feed quality. The primary criterion for adding fresh catalyst to arrive at an optimum E-cat activity level. A too-high E-cat activity ill increase delta coke on the catalyst, resulting in a higher regenrator temperature. The higher regenerator temperature reduces the atalyst circulation rate, which tends to offset the activity increase.
The amount of fresh catalyst added is usually a balance between atalyst cost and desired activity. Most refiners monitor the MAT data om the catalyst vendor's equilibrium data sheet to adjust the fresh atalyst addition rate. It should be noted that MAT numbers are based n a fixed-bed reactor system and, therefore, do not truly reflect the ynamics of an FCC unit. A catalyst with a high MAT number may r may not produce the desired yields. An alternate method of measur- g catalyst performance is dynamic activity. Dynamic activity is alculated as shown below:

12 |
Fluid Catalytic |
Cracking Handbook |
r v |
. . . . |
(Second Order Conversion) |
Dynamic Activity =
(Coke Yield, Wt% of Feed)
here;
(MAT Conversion, Vol%)
Second Order Conversion =
(100 - MAT Conversion, Vol%)
or example, a catalyst with a MAT number of 70 vol% and a 3.0 t% coke yield will have a dynamic activity of 0.78. However, another atalyst with a MAT conversion of 68 vol% and 2.5 wt% coke yield ill have a dynamic activity of 0.85. This could indicate that in a ommercial unit the 68 MAT catalyst could outperform the 70 MAT atalyst, due to its higher dynamic activity. Some catalyst vendors have egun reporting dynamic activity data as part of their E-cat inspecon reports. The reported dynamic activity data can vary significantly om one test to another, mainly due to the differences in feedstock uality between MAT and actual commercial application. In addition, e coke yield, as calculated by the MAT procedure, is not very ccurate and small changes in this calculation can affect the dynamic
tivity |
|
appreciably. |
|
|
|
|
|
|
The most widely accepted model |
to predict E-cat activity is based |
|||||||
n a first-order decay type [7]: |
|
|
|
|||||
A |
- |
A |
X c~(S+K)t |
, A0 |
X S |
v n |
_, |
-<K+S)fv |
A(t) |
- |
A(0) |
xe |
c |
i i^ |
^ |
e |
' |
|
|
|
|
o |
4" IV |
|
|
|
t steady state, the above equation reduces to:
A |
- |
A |
(0) |
xx ce -(S+K)t I A° |
X |
S |
x f'1 - |
p-tK+S)') |
' |
(t) |
~~ |
|
c |
, |
v |
^ |
|
||
|
|
|
|
O |
+ |
IS. |
|
|
|
here:
t) = Catalyst microactivity at anytime
0= Catalyst microactivity at starting time
- Time after changing catalyst or makeup rate
=Daily fractional replacement rate = addition rate/inventory
=Deactivation constant = ln(At - A0)/-t



16 Fluid Catalytic Cracking Handbook
3, Obtain vendor responses
a.Obtain catalyst recommendation
b.Obtain alternate recommendation
c.Obtain comparative yield projection 4, Obtain current product price projections
a.For present and future four-quarters
5, Perform economic evaluations on vendor yields
a.Select catalysts for MAT evaluations 6, Conduct MAT of selected list
a.Perform physical and chemical analyses
b.Determine steam deactivation conditions
c.Deactivate incumbent fresh catalyst to match incumbent E-cat
d.Use same deactivation steps for each candidate catalyst
7, Perform economic analysis of alternatives
|
a. Estimate commercial yield from MAT evaluations |
8, |
Request commercial proposals |
|
a. Consult at least two vendors |
|
b. Obtain references |
|
c. Check references |
9, |
Test the selected catalysts in a pilot plant |
a.Calibrate the pilot plant steaming conditions using incumbent E-cat
b.Deactivate the incumbent and other candidate catalysts
c.Collect at least two or three data points on each by varying the catalyst-to-oil ratio
10.Evaluate pilot plant results
a.Translate the pilot plant data
b.Use the kinetic model to heat-balance the data
c.Identify limitations and constraints
11.Make the catalyst selection
a.Perform economic evaluation
b.Consider intangibles-research, quality control, price, steady supply, manufacturing location
c.Make recommendations
12.Post selection
a.Monitoring transition-% changeover
b.Post transition test run
c.Confirm computer model

FCC Catalysts |
117 |
13.Issue the final report
a.Analyze benefits
b.Evaluate selection methodology
There is a redundancy of flexibility in the design of FCC catalysts. ariation in the amount and type of zeolite, as well as the type of ctive matrix, provide a great deal of catalyst options that the refiner an employ to fit its needs. For smaller refiners, it may not be practical employ pilot plant facilities to evaluate different catalysts. In this ase, the above methodology can still be used with emphasis shifted ward using the MAT data to compare the candidate catalysts. It is mportant that MAT data are properly corrected for temperature,
soaking time," and catalyst strippability effects.
For many years, cat cracker operators have used additive compounds r enhancing cat cracker performance. The main benefits of these dditives (catalyst and feed additives) are to alter the FCC yields and duce the amount of pollutants emitted from the regenerator. The dditives discussed in this section are CO promoter, SOX reduction, SM-5, and antimony.
O Promoter
The CO promoter is added to most FCC units to assist in the ombustion of CO to CO2 in the regenerator. The promoter is added accelerate the CO combustion in the dense phase and to minimize e higher temperature excursions that occur as a result of afterburning the dilute phase. The promoter allows uniform burning of coke, articularly if there is uneven distribution between spent catalyst and
ombustion air.
Regenerators operating in full or partial combustion can utilize the enefits of the CO promoter. The addition of the promoter tends to crease the regenerator temperature and NOx emission. The metallurgy the regenerator internals should be checked for tolerance of the
gher temperature.
The active ingredients of the promoter are typically the platinum oup metals. The platinum, in the concentration of 300 ppm to 800

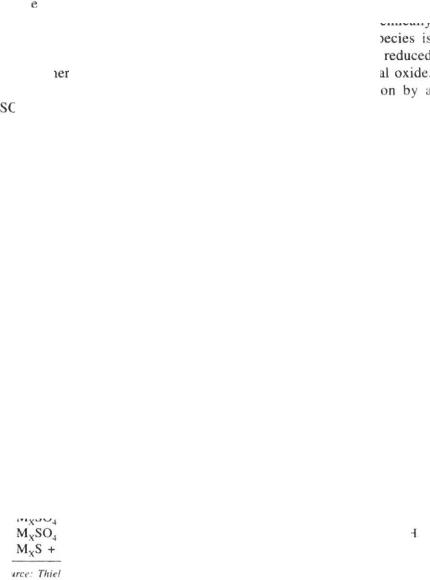





CHAPTER 4
Chemistry of FCC
Reactions
A complex series of reactions (Table 4-1) take place when a large as-oil molecule comes in contact with a 1,200°F to 1,400°F (650°C 760°C) FCC catalyst. The distribution of products depends on many ctors, including the nature and strength of the catalyst acid sites. lthough most cracking in the FCC is catalytic, thermal cracking actions also occur. Thermal cracking is caused by factors such as on-ideal mixing in the riser and poor separation of cracked products the reactor.
The purpose of this chapter is to:
•Provide a general discussion of the chemistry of cracking (both thermal and catalytic).
•Highlight the role of the catalyst, and in particular, the influence of zeolites.
•Explain how cracking reactions affect the unit's heat balance.
Whether thermal or catalytic, cracking of a hydrocarbon means the eaking of a carbon to carbon bond. But catalytic and thermal crack- g proceed via different routes. A clear understanding of the different echanisms involved is beneficial in areas such as:
• Selecting the "right" catalyst for a given operation
•Troubleshooting unit operation
•Developing a new catalyst formulation
Topics discussed in this chapter are:
•Thermal cracking
•Catalytic cracking
•Thermodynamic aspects
125


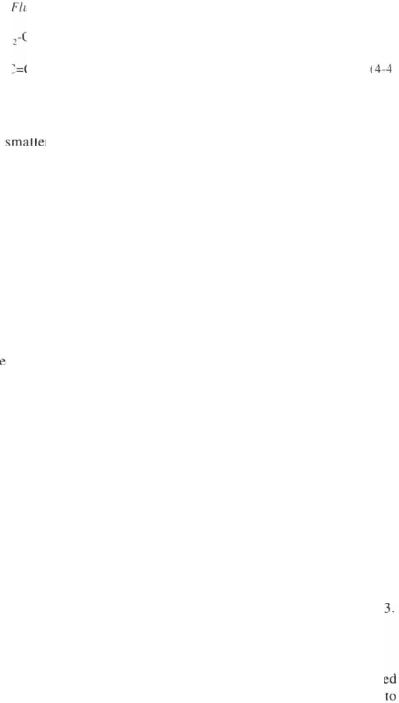




2 Fluid Catalytic Cracking Handbook
R — CH2 -—CH2 — CH2 — CH3 (removal of H~ @ Lewis site)
_» R _ c+H — CH2 — CH2 — CH3 |
(4-8} |
Both the Bronsted and Lewis acid sites on the catalyst generate rbenium ions. The Bronsted site donates a proton to an olefin olecule and the Lewis site removes electrons from a paraffin molele. In commercial units, olefins come in with the feed or are prouced through thermal cracking reactions.
The stability of carbocations depends on the nature of alkyl groups tached to the positive charge. The relative stability of carbenium ions as follows [2] with tertiary ions being the most stable:
Tertiary |
> |
Secondary > |
Primary |
|
+ |
> |
Ethyl |
+ |
> Methyl |
||
C ~ C |
+ |
P P P+ P R P |
P |
P P |
P* |
||||||
|
|
|
|||||||||
. '"•"""" V-- "" V.- |
|
V_^ \*s |
V~" |
V-"' |
JLX. V-' |
V_-- |
V-- |
*—• |
|
V,,' |
c
One of the benefits of catalytic cracking is that the primary and condary ions tend to rearrange to form a tertiary ion (a carbon with ree other carbon bonds attached). As will be discussed later, the creased stability of tertiary ions accounts for the high degree of anching associated with cat cracking.
Once formed, carbenium ions can form a number of different actions. The nature and strength of the catalyst acid sites influence e extent to which each of these reactions occur. The three dominant actions of carbenium ions are:
*The cracking of a carbon-carbon bond
*Isomerization
*Hydrogen transfer
racking Reactions
Cracking, or beta-scission, is a key feature of ionic cracking. Betaission is the splitting of the C-C bond two carbons away from the ositive-charge carbon atom. Beta-scission is preferred because the ergy required to break this bond is lower than that needed to break e adjacent C-C bond, the alpha bond. In addition, short-chain hydrorbons are less reactive than long-chain hydrocarbons. The rate of




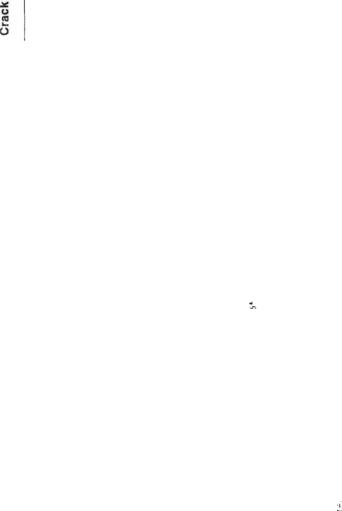
e Tabl4 4-
Som Thermodynami dDatr fo sIdealize Reactionf o Importancn i Catalytig Crac
|
|
|
t |
Kg Lo |
E |
|
|
|
m |
(equilibriu) |
constant |
Clas |
c |
nSpecifi Reactio |
F |
850°F 950°F 980° |
|
n-C10H22> - |
n-C7H61 + C3H6 |
|
4 |
|
2.0 |
|
6 |
2.4 |
|
— |
|||||||
transfe |
1~C8H61> - |
2C4Hg |
|
|
|
|
8 |
1.6 |
|
0 |
2.1 |
3 |
2.2 |
|||||
4C H» |
- |
3C H |
+ C H |
|
4 |
|
12.4 |
9 |
|
11.0 |
|
— |
||||||
|
6 |
21 |
|
|
6 |
41 |
6 |
|
6 |
|
|
|
|
|||||
atio |
cyclo-C6H32l |
+ |
1-C5H0!> - 3n-C5H21 |
+ C6H6 2 |
|
11.2 |
5 |
|
10.3 |
|
— |
|||||||
1-C4H»8 - |
trans-2-C4H8 |
|
|
|
2 |
|
0.3 |
|
|
|
|
|||||||
|
|
|
|
|
5 |
0.2 |
9 |
0.0 |
||||||||||
|
n-C |
H» |
- |
iso-C H |
|
|
|
0 |
-0.2 3 |
-0.2 6 |
-0.3 |
|||||||
|
6 |
01 |
|
|
|
4 |
01 |
|
|
|
||||||||
|
o-C6H4(CH3>)2 - m-C6H4(CH3)2 |
3 |
|
0.3 |
|
0 |
0.3 |
|
— |
|||||||||
|
cyclo-C H» |
- |
CH -cyclo-C H |
0 |
1.0 |
|
9 |
1.0 |
0 |
1.1 |
||||||||
ylatio |
|
|
6 |
21 |
|
|
3 |
|
5 |
9 |
|
|||||||
C6H6 + m-C6H4(CH3>)2 - |
|
2C6H5CH3 |
5 |
|
0.6 |
|
5 |
0.6 |
5 |
0.6 |
||||||||
o |
1-C H» |
- |
CH -cyclo-C H |
|
1 |
|
2.1 |
|
4 |
1.5 |
|
— |
||||||
tio |
7 |
41 |
|
|
|
3 |
|
6 |
11 |
|
|
|
|
|||||
iso-C3H7-C6H>5 |
- |
C6H6 |
+ C3H6 |
1 |
|
0.4 |
|
8 |
0.8 |
|
||||||||
|
|
5 |
1.0 |
|||||||||||||||
genatio |
n-C6H41 ^ |
1-C6H21H + |
|
2 |
|
1 |
-2.2 |
2 |
-1.5 |
|
— |
|||||||
zatio |
3C H |
—> 1-C H |
|
|
|
|
|
|
— |
|
|
— 2 -1. |
||||||
Alkylatio |
2 |
4 |
|
|
6 |
21 |
|
|
|
|
|
|
— |
|
|
|||
1-C H |
+ iso-C H> |
- |
iso-C H |
|
|
|
|
— |
3 3. |
|||||||||
|
4 |
8 |
|
|
|
4 01 |
|
|
8 |
81 |
|
|
|
|
|
nuto [2]
n
0
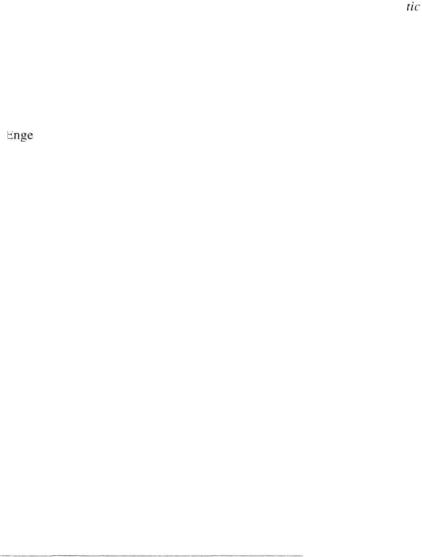
CHAPTER 5
Unit Monitoring
and Control
The only proper way to monitor the performance of a cat cracker by periodic material and heat balance surveys on the unit. By arrying out these tests frequently, one can collect, trend, and evaluate e unit operating data. Additionally, meaningful technical service to
ptimize the unit operation should be based on regular test runs. Understanding the operation of a cat cracker also requires in-depth nowledge of the unit's heat balance. Any changes to feedstock quality, perating conditions, catalyst, or mechanical configuration will impact e heat balance. Heat balance is an important tool in predicting and valuating the changes that will affect the quantity and the quality of CC products.
Finally, before the unit can produce one barrel of product, it must irculate catalyst smoothly. One must be familiar with the dynamics f pressure balance and key process controls.
The main topics discussed in this chapter are:
•Material Balance
•Heat Balance
•Pressure Balance
•Process Control Instrumentation
the material and heat balance sections, the discussions include:
•Two methods for performing test runs
•Some practical steps for carrying out a successful test run
•A step-by-step method for performing a material and heat balance survey
•An actual case study
139


Unit Monitoring and Control |
141 |
External Streams^-"
Figure 5-1. FCC unit input/output streams.
alance, gasoline and light cycle oil (LCO) yields and unit converion are reported based on fixed end points. The common end points re 430°F (221 °C) TBP for gasoline and 700°F TBP for LCO, Other opular cut points are 430°F (221°C) ASTM D-86 for gasoline and 50°F (343°C) or 670°F (354°C) ASTM D-86 for LCO. Using fixed


Sample probe
Gate and ball valves
Slop container
Figure 5-2, Reaction mix sampling [2].








Dry Air versus Relative Humidity & Temperature
50 |
70 |
80 |
100 |
1tO |
|
Temperature,Deg F |
|
|
|
Figure 5-3, |
Dry air versus relative humidity |
and temperature. |
|

52 Fluid Catalytic Cracking Handbook
Example 5-2
onversion of Input and Output Streams to the Unit of Weight (Ib/hr)
|
„ , „ |
. 50,000bbl |
1day |
|
141.5 |
350.3 Ib |
|
||
• Fresh Feed = —-—-- |
x - |
-x - |
• -- x - —— |
|
|||||
|
|
day |
24 hr |
|
(131.5+ 25.2) |
bbl |
|
||
|
|
= 658,964 lb/hr |
|
|
|
|
|
|
|
» |
„, |
3,000,000 SCF 1day |
1mole |
27.8 lbs ni« |
«,„,,. |
||||
v^UJVCIf^r\lrpir gasCTQG —*"_!_ " !_ ........ |
A.V |
, |
•*A. v |
. *„._„,„_ _^ |
V._.....,.._L... ,..,..,........u |
_.-_...-...-— Q« 1| JvJ.OSf\ x1U/m/nr111 |
|||
|
|
day |
24 hr |
379.5 SCF |
1mole |
|
|||
|
.™ .. |
16,000,000 SCF |
Iday |
Imole |
22.6 Ibs |
- |
|||
• FCC tail gas = —-- -- |
x - ^x - |
|
x |
||||||
|
|
day |
|
24 hr |
379.5 SCF |
Imole |
|
= 39,701Ib/hr
he amount of inerts in the FCC tail gas is:
KT |
16,000,OOOSCF |
1day |
_ _ _ „ |
Imole |
281bs |
3,542lb/hr |
|||
• N2 |
= —-- -- |
|
x - i-x 0.072 x - |
x - |
= 3,542 Ib/hr |
||||
|
|
day |
|
24 hr |
|
379.5 SCF |
Imole |
|
|
„ |
16,000,OOOSCF! |
A n -t |
1day |
1mole |
441bs |
,,»«,,„ |
|||
. CO2 = — - -- |
|
x 0.021 x - ^-x - - |
x - |
= 1,623 Ib/hr |
|||||
|
|
day |
|
|
24 hr |
379.5 SCF Imole |
|
||
• Inert-free |
FCC tail gas = 39,701 - (3,542 + 1,623) = 34,537 Ib/hr |
||||||||
. LpG=H.565bblxldayx |
141.5 |
|
X35031b = |
|
|||||
|
|
day |
24 hr (131.5+ 123.5) |
bbl |
|
|
|||
„ |
r |
30,000bbl |
day |
141.5 |
350.31b |
|
|||
• Gasoline = —-- |
|
x --x - |
|
x |
- |
|
|||
|
|
day |
|
24 hr |
(131.5 + 58.5) |
bbl |
|
= 326, 102Ib/hr
|
141.5 |
|
day |
24hr (131.5 + 21.5) |
bbl |
f
3,000bbl |
1day |
141.5 |
350.31b ., «--,.,, |
= —- x -i-x - |
x -- = 46,2731b/hr |
||
day |
24 hr |
(131.5+ 2.4) |
bbl |


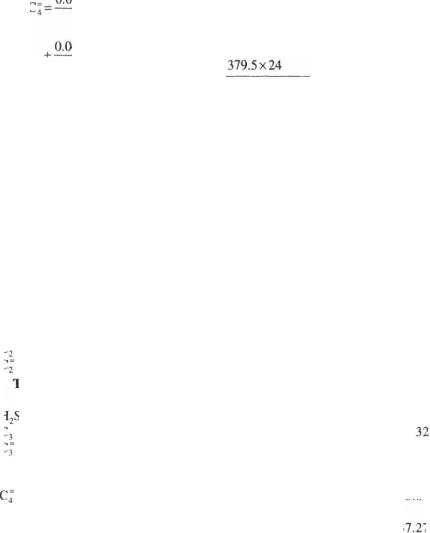
6 Fluid Catalytic Cracking Handbook
djustment of Gasoline and LCO Cut Points
As discussed earlier in this chapter, gasoline and LCO yields are enerally corrected to a constant boiling range basis. The most comonly used bases are 430°F TBP gasoline and 640°F TBP LCO end oints. Since TBP distillations are not routinely performed, they are ten estimated from the D-86 distillation data. The adjustments to the nd points involve the following:
* Adding to the raw LCO all the 430°F+ in the raw gasoline and subtracting the 430°F in the LCO stream.
«Adding to the raw LCO all the 650°F~ in the raw decanted oil and subtracting the 650°F~ in the decant oil stream.
*Adding to the raw gasoline all the 430°F~ in the raw LCO and subtracting the 430°F* in the gasoline stream.
•Adding to the raw decanted oil all the 650°F+ in the raw LCO and subtracting the 650°F~ in the decant oil stream.
Table 5-5 illustrates steps used to convert ASTM D-86 data to TBP. he laboratory usually converts D-1160 and reports the data as D-86, xtrapolation of the TBP data indicates the following:
« |
The 430°F+ content of the FCCU gasoline is |
3 vol%, or |
859 bpd. |
|
« |
The |
gasoline (430°F~) content of LCO is 8 vol%, or 806 bpd. |
||
« |
The |
650°F+ content ofLCO is 12 vol%, or |
1,209 bpd. |
|
•The LCO (650°F~) content of the decanted oil is 17 vol%, or 514 bpd.
herefore, the adjusted rates are as follows:
Gasoline (C5+ to 430°F TBP end point) = 28,650 - 859 + 806
= 28,597 |
bpd |
LCO (430°F to 650°F TBP end point) = 10,077 |
+ 514 - 1,209 - 806 |
+ 859 = 9,435 bpd DO (650°F+) = 3,023 + 1,209 - 514 = 3,718 bpd
able 5-6 shows the normalized FCC weight balance with the adjusted t points.



Unit Monitoring and Control |
159 |
Steam
team
Oil Feed
Figure 5-4. Reactor-regenerator heat balance.




W «M#
I 0J
f E
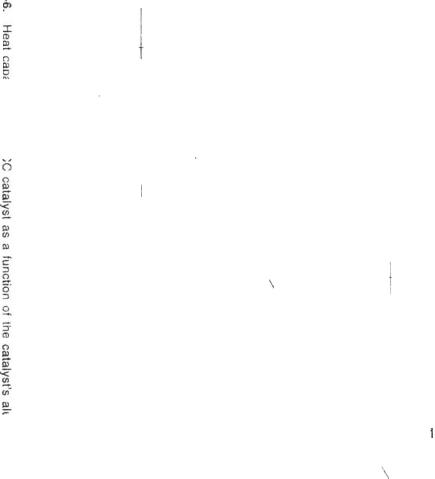
to |
20 |
30 |
40 |
50 |
60 |
|
|
Alumina Content, Wt.% |
|
|
|
yre |
of the FCC |
as |
a function |
of the |
content, |


1Fluid Catalytic Cracking Handbook
I.Calculation of heat of reaction
Total heat out = total heat in
Total heat out = 878 x 106 + 512.6 x 106 + 15.2 x 106 + 6.1 x 1C)6 +
overall heat of reaction =
Total heat in = 1,499.6 x 106Btu/hr
Overall endothermic heat of reaction = 84.5 x 106 Btu/hr or —» 128.2
Btu/lb of feed.
nalysis of Results
Once the material and heat balances are complete, a report must be ritten. It will first present the data. It will then discuss factors fecting product quality and any abnormal results. It will then discuss e key findings and recommendations to improve unit operation.
In the previous examples, the feed characterizing correlations in hapter 2 are used to determine composition of the feedstock. The sults show that the feedstock is predominantly paraffinic (i.e., 61.6% araffins, 19.9% naphthenes, and 18.5% aromatics). Paraffinic feedocks normally yield the most gasoline with the least octane. This onfirms the relatively high FCC gasoline yield and low octane bserved in the test run. This is the kind of information that should e included in the report. Of course, the effects of other factors, such catalyst and operating parameters, will also affect the yield structure d will be discussed.
The coke calculation showed the hydrogen content to be 9.9 wt%. s discussed in Chapter 1, every effort should be made to minimize e hydrogen content of the coke entering the regenerator. The hydroen content of a well-stripped catalyst is in the range of 5 wt% to wt%. A 9.9 wt% hydrogen in coke indicates either poor stripper peration and/or erroneous flue gas analysis.
RESSURE BALANCE
Pressure balance deals with the hydraulics of catalyst circulation in e reactor/regenerator circuit. The pressure balance starts with the atic pressures and differential pressures that are measured. The arious pressure increases and decreases in the circuit are then callated. The object is to:
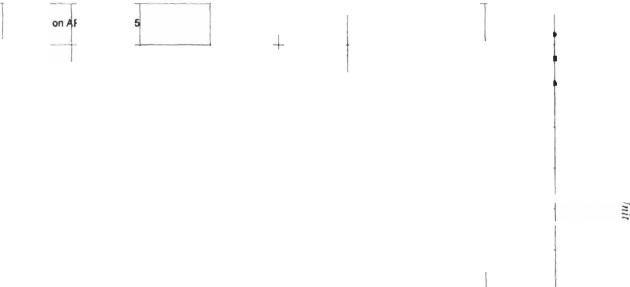

920 |
940 |
960 |
980 |
1000 |
1020 |
1040 |
1060 |
1080 |
Deg.F
-*-K«11 -*-K-t2 -*-K»13
Figyre 5-8. Hydrocarbon vapor enthalpies at various Watson K factors.

|
Unit Monitoring and Control |
169 |
« |
Maximize catalyst circulation |
|
* |
Ensure steady circulation |
|
* |
Maximize the available pressure drop at the slide valves |
|
* |
Minimize the loads on the blower and the wet gas compressor |
A clear understanding of the pressure balance is extremely important |
|
n "squeezing" the most out of a unit. Incremental capacity can come |
|
rom increased catalyst circulation or from altering the differential |
|
ressure between |
the reactor-regenerator to "free up" the wet gas |
ompressor or air |
blower loads. One must know how to manipulate |
he pressure balance to identify the "true" constraints of the unit. Using the drawing(s) of the reactor-regenerator, the unit engineer
ust be able to go through the pressure balance and determine whether makes sense. He or she needs to calculate and estimate pressures, ensities, pressure buildup in the standpipes, etc. The potential for mprovements can be substantial.
asic Fluidization Principals
A fluidized catalyst behaves like a liquid. Catalyst flow occurs in he direction of a lower pressure. The difference in pressure between ny two points in a bed is equal to the static head of the bed between hese points, multiplied by the fluidized catalyst density, but only if he catalyst is fluidized.
FCC catalyst can be made to flow like a liquid, but only if the ressure force is transmitted through the catalyst particles and not the essel wall. The catalyst must remain in a fluidized state as it makes loop through the circuit.
To illustrate the application of the above principals, the role of each ajor component of the circuit is discussed in the following sections, ollowed by an actual case study. As a reference, Appendix 8 contains luidization terms and definitions commonly used in the FCC.
Major Components of the Reactor-Regenerator Circuit
The major components of the reactor-regenerator circuit that either roduce or consume pressure are as follows:
*Regenerator catalyst hopper
*Regenerated catalyst standpipe





4 Fluid Catalytic Cracking Handbook
Rx Vapor
Reactor
Psi diff.
Oil Feed
Figure 5-9. Preliminary pressure balance survey.


6 Fluid Catalytic Cracking Handbook
Rx Vapor
Reactor
Psi diff.
Oil Feed
igure 5-10. Pressure balance survey with calculated standpipe densities.



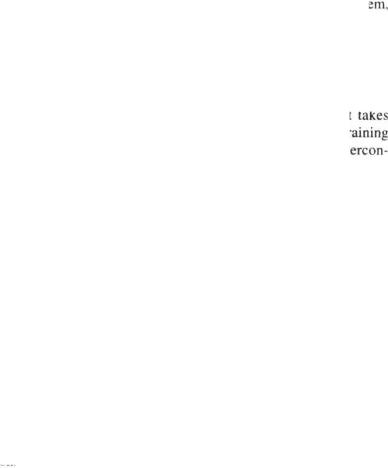
80 Fluid Catalytic Cracking Handbook
With a host computer framework, the control package is all in the oftware. Changing the program can still be agonizing, but the program an be tested off-line. There is more flexibility in the computer system, hich can be used for many other purposes, including on-line heat nd weight balances.
isadvantages of Multivariable Modeling and Control
A multivariable model is like a "black box." The constraints go in nd the signals come out. Operators do not trust a system that takes e unit away from them. Successful installations require good training nd continual communication. The operators must know the interconections in the system.
The model may need expensive work if changes are made during a rnaround. If the feed gets outside the range the unit was modeled r, results can be at best unpredictable. An upset can happen for which e system was not programmed.
The DCS-based APC is installed in a modular form, meaning operators an understand what the controlled variable is tied to more easily.
The host computer-based system may have its own problems, includ- g computer-to-computer data links.
In any APC, the operators must be educated and brought into it efore they can use it. The control must be properly designed, meaning e model must be configured and properly "tuned." The operators hould be involved early and all of them should be consulted since l four shifts may be running the unit differently.
UMMARY
The only proper method to evaluate the performance of a cat cracker by conducting a material and heat balance. One balance will tell here the unit is; a series of daily or weekly balances will tell where e unit is going. The heat and weight balance can be used to evaluate revious changes or predict the result of future changes. As discussed
the next chapter, material and heat balances are the foundation for etermining the effects of operating variables.
The material balance test run provides a standard and consistent pproach for daily monitoring. It allows for accurate analysis of yields nd trending of unit performance. The reactor effluent can be deter-

CHAPTER 6
Products and
Economics
The previous chapters explained the operation of a cat cracker. owever, the purpose of the FCC unit is to maximize profitability for e refinery. The cat cracker provides the conversion capacity that very refinery needs to survive. All crudes have heavy gas oils and el oil; unfortunately, the market for these products has disappeared. FCC economics makes the refinery a viable entity. Over the years, fineries without cat crackers have been shut down because they were ot profitable.
Understanding the economics of the unit is as important as underanding the heat and pressure balance. The dynamics of FCC economics hanges daily and seasonally. It is dependent on market conditions and e availability of feedstocks. The 1990 Clean Air Act Amendment CAAA) has imposed greater restrictions on quality standards for asoline and diesel. The FCC is the major contributor to the gasoline nd diesel pool and is significantly affected by these new regulations. This chapter discusses the factors affecting yields and qualities of CC product streams. The section on FCC economics describes several ptions that can be used to maximize FCC performance and the efinery's profit margin.
CC PRODUCTS
The cat cracker converts less valuable gas oils to more valuable roducts. A major objective of most FCC units is to maximize the onversion of gas oil to gasoline and LPG. The products from the cat racker are:
•Dry Gas
•LPG
•Gasoline
182





Products and Economics
0 |
5 |
10 |
15 |
ZSM-5 wt% in Catalyst Inventory
Figure 6-2. The effect of ZSM-5 on light-ends yield [5].
*Increasing reactor temperature (if the increase does not over-crack the already produced gasoline)
asoline Quality
The Clean Air Act Amendment (CAAA), passed in November 1990, as set new quality standards for U.S. gasoline. A complete discussion f the new gasoline formulation requirements can be found in Chap- r 10.


Products and Economics |
189 |
93
92
U
Z
o
91
90
20 |
22 |
24 |
26 |
Feed Gravity, "API
82
81
Q
Z
O
s
80
79
20 |
22 |
24 |
26 |
Feed Gravity, "API
Figure 6-3. Feed gravity comparisons (MON and RON) [7].


Products and Economics |
191 |
RONC vs.SODIUM
COMMERICAL DATA
0.40 |
0.60 |
EQUILIBRIUM CAT. SODIUM, WT.%
< 80.5 -
§80.0 -
79.5-
79.0-
78.5_
78.0
0.20 |
0.40 |
0.80 |
EQUILIBRIUM CAT SODIUM, WT. %
Figure 6-4. Effect of sodium on gasoline octane [8J.

92 Fluid Catalytic Cracking Handbook
84
83 |
PILOT PLANT DATA |
|
C5-265T/C5-129"C |
||
82 |
||
265-430"F/129-221*C |
; 81 o
80 |
|
|
|
|
79 |
|
|
|
—8 |
78 |
|
|
|
|
|
|
|
|
|
77 |
|
|
|
|
0.0 |
1.0 |
2.0 |
3.0 |
4.0 |
REO, WT.%
Figure 6-5. Effect of fresh REO on MON [9].
95 82
94
81
93
|
|
|
|
|
UJ |
|
|
|
|
|
|
|
|
|
z 80 |
|
|
|
|
|
|
|
|
|
O |
|
|
|
|
|
|
|
|
|
O |
|
|
|
|
91 |
|
|
|
|
o: 79 |
|
|
|
|
|
|
|
|
|
O |
|
|
|
|
auon |
|
|
|
|
I |
|
|
|
|
|
|
|
|
|
|
|
|
|
|
89 - |
|
|
|
|
78 |
|
|
|
|
|
|
|
|
|
|
|
|
|
|
88 |
I I I |
I |
I I |
I I |
77 |
|
I |
I |
i i |
24.20 |
24.24 |
24.28 |
24.32 |
24.36 |
24,20 |
24.24 |
24.28 |
24.32 |
24.36 |
|
UNIT CELL SIZE, A |
|
|
UNIT CELL SIZE, A |
|
Figure 6-6. Effects of unit cell size on research and motor octane [10].

Products and Economics |
113 |
0.1 |
|
|
High N VGO |
|
0.03 |
|
|
|
|
0.01 |
|
|
|
|
o.oos |
|
|
34% Recycle |
|
|
|
|
|
|
0,001 |
|
|
|
|
0.05 |
0.1 |
0.2 |
0.5 |
1 |
FCCU Feed Sulfur, wt%
Figure 6-7. FCC gasoline sulfur yield [4].
2,000
Non-Hydrotreated
1.000
.
.
Hydrotreated
FCCU FEEDSTOCK SULFUR (wt%)
Figure 6-8. Hydrotreating reduces FCC gasoline sulfur [4].

94 Fluid Catalytic Cracking Handbook
1,000
Guff Coast FCCU Feed. 0.62 w% S I
HT FCCU Feed, 0.68 w%S
350 |
450 |
|
FCC Gasoline End Point (°F) |
Figure 6-9. |
FCC gasoline sulfur increases with end point [4], |
400
.
"350
Octane Catalyst
3
300
Octane BBL Catalyst
250 |
|
|
|
475 |
500 |
525 |
550 |
FCC Reactor Isothermal Temperature (°C)
Figure 6-10. FCC gasoline sulfur increases with temperature [4j.






/O WHSV
EC
RX
Products and Economics |
201 |
=0.65
=cat-to-oil ratio
=weight of hourly space velocity, weight of total feed/hr divided by weight of catalyst inventory in reaction zone, hr-1
=activation energy ~ 2,500 Btu/lb-mole (5828 J/G - mole)
=gas constant, 1.987 Btu/lb-mole-°R (8.314 J/G- mole °K)
=reactor temperature, °R
The coke yield of a given cat cracker is essentially constant. The CC produces enough coke to satisfy the heat balance. However, more important term is delta coke. Delta coke is the difference etween the coke on the spent catalyst and the coke on the regenerated atalyst. At a given reactor temperature and constant CO2/CO ratio, elta coke controls the regenerator temperature.
Reducing delta coke will lower the regenerator temperature. Many enefits are associated with a lower regenerator temperature. The esulting higher cat/oil ratio improves product selectivity and/or rovides the flexibility to process heavier feeds.
Many factors influence delta coke, including quality of the FCC eedstock, design of the feed/catalyst injection system, riser design, perating conditions, and catalyst type. The following is a brief iscussion of these factors:
*Feedstock quality. The quality of the FCC feedstock impacts the concentration of coke on the catalyst entering the regenerator. A "heavier" feed containing a higher concentration of coker gas oil will directionally increase the delta coke as compared with a "lighter," resid-free feedstock.
* |
Feed/catalyst injection. A well-designed injection system provides |
|
a rapid and uniform vaporization of the liquid feed. This will |
|
lower delta coke by minimizing non-catalytic coke deposition as |
|
well as reducing the deposits of heavy material on the catalyst. |
• |
Riser design. A properly designed riser will help reduce delta coke |
|
by reducing the back-mixing of already "coked-up" catalyst with |
|
fresh feed. The back-mixing causes unwanted secondary reactions. |
• |
Cat/oil ratio. An increase in the cat/oil ratio reduces delta coke |
|
by spreading out some coke-producing feed components over |
|
more catalyst particles and, thus, lowering the concentration of |
|
coke on each particle. |

02Fluid Catalytic Cracking Handbook
«Reactor temperature. An increase in the reactor temperature will also reduce delta coke by favoring cracking reactions over hydrogen transfer reactions. Hydrogen transfer reactions produce more coke than cracking reactions.
*Catalyst activity. An increase in catalyst activity will increase delta coke. As catalyst activity increases so does the number of adjacent sites, which increases the tendency for hydrogen transfer reactions to occur. Hydrogen transfer reactions are bimolecular and require adjacent active sites.
CC ECONOMICS
The cat cracker's operational philosophy is dictated by refinery conomics. Economics of a refinery are divided into internal and xternal economics.
Internal economics largely depends on the cost of raw crude and e FCC unit's yields. The cost of crude can outweigh the benefit from e cat cracker yields. Refiners who operate their units by a kind of tuition may drive for more throughput, but this may not be the most rofitable approach.
External economics are factors that are generally forced upon the fineries. Refiners prefer not to have their operations dictated by xternal economics. However, they may have to meet particular quirements such as those for reformulated gasoline.
To maximize the FCCU's profit, the unit must be operated against l its mechanical and operating constraints. Generally speaking, the cremental profit of increasing feed is more than the incremental ofit from increasing conversion. The general target is to maximize asoline yield while maintaining the minimum octane that meets lending requirements.
Because of the high cost of new units and the importance of the CC on refinery profitability, improvements should be made to the xisting units to maximize their performance. These performance dices are:
*Improving product selectivity
*Enhancing operating flexibility
*Increasing unit capacity
*Improving unit reliability


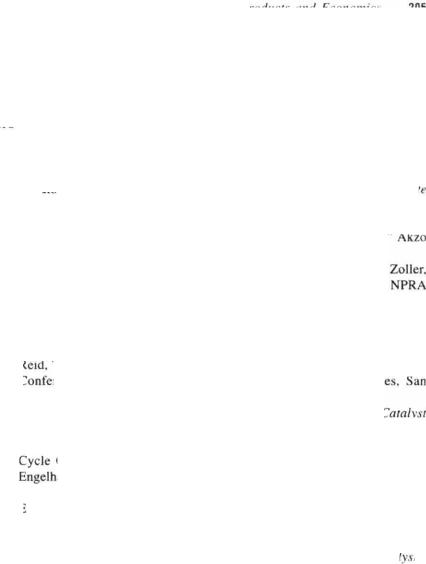
CHAPTER 7
Project Management
and Hardware Design
Since 1942, when the first FCC unit came onstream, numerous rocess and mechanical changes have been introduced. These changes mproved the unit's reliability, allowed it to process heavier feedstocks, operate at higher temperatures, and to shift the conversion to more
aluable products.
However, incorporating these changes in an existing unit is a major roject, usually more complicated than building a new unit. The two ritical components of a successful mechanical upgrade (or erection of a ew unit) are effective project management and proper design standards. This chapter addresses project management aspects of a revamp. It lso provides design guidelines that can be used by a refiner in electing the revamp components. The original driving force for a roject is often a particular mechanical problem or a process bottleeck. The ultimate objective of a revamp should be a safe, reliable, nd profitable operation.
ROJECT MANAGEMENT ASPECTS
F AN FCC REVAMP
The modifications/upgrades to the reactor and regenerator circuit are ade for a number of reasons: equipment failure, technology changes, nd/or changes in processing conditions. The primary reasons for upgrad- g the unit are improving the unit's reliability, increasing the quantity nd quality of valuable products, and enhancing operating flexibility.
The revamp (or erection of a new unit) requires successful execution f each phase of the project:
•Pre-project
•Process design
206








14Fluid Catalytic Cracking Handbook
*Standpipe system
*Air and spent catalyst distributors
*Reactor and regenerator cyclones
*Expansionjoints
*Refractory
eed Injection System
Any mechanical revamp to improve the unit yields should always egin with installing an efficient feed and catalyst distribution system. his is the single most-important component of the FCC unit. An fficient feed and catalyst injection system maximizes gasoline yield nd conversion at the expense of lower gas, coke, and decant oil and llows downstream technology to perform at its full potential.
Ideally, a well-designed feed and catalyst injection system will
chieve the following objectives: |
|
|
» |
Distribute the feed and regenerated |
catalyst throughout the cross- |
|
section of the riser to ensure that |
all feed components are sub- |
|
jected to the same cracking severity |
|
» |
Atomize the feed uniformly and instantaneously |
|
* |
Avoid re-contacting of the "spent |
catalyst" with the fresh feed |
*Produce proper oil droplet size to penetrate through the catalyst over the 360° cross-sectional area of the riser
* |
Avoid erosion of the riser |
wall and attrition of the catalyst |
* |
Perform without plugging |
or erosion |
rocess Design Considerations for Feed Nozzles
Table 7-1 contains a summary of the process and mechanical design riteria commonly used in specifying high-efficiency feed nozzles. The mechanical design of any feed nozzle should be robust and easy to aintain. Its long-term mechanical reliability is critical in achieving he expected benefits of the upgrade. The following mechanical problems re often encountered: erosion of the nozzle tip(s), erosion of the riser all, and blockage of the nozzles.
atalyst Lift Zone Design Considerations
To maximize the benefits of feed nozzles, the regenerated catalyst ust be distributed evenly throughout the cross-section of the riser.

16 Fluid Catalytic Cracking Handbook
Hydrocarbon
Feed
Dispersion Steam
Figure 7-1. Schematic of a typical feed nozzle.
Table 7-2
Process and Mechanical Design Guidelines for FCC Risers
Hydrocarbon |
1 second to 3 seconds based on the riser outlet |
|
residence time |
conditions. Depending on the degree of catalyst |
|
|
back-mixing in the riser, the catalyst residence |
|
|
time is usually 1.5 to 3.5 times longer than the |
|
|
hydrocarbons. |
|
Vapor Velocity |
20 ft/sec (6 m/s) minimum (without oil feed), |
|
|
65 ft/sec to 85 ft/sec (20 to 25 m/s) at the design |
|
|
feed rate. |
|
Geometry |
Vertical: to simulate plug flow and to minimize |
|
|
catalyst |
back-mixing |
ermination |
Riser-cyclone separator attached to another separation |
|
|
device to minimize re-cracking of hydrocarbon vapors. |
|
onfiguration |
External |
or internal. |
Material |
Carbon |
steel, "cold wall" as opposed to "hot wall," |
Project Management and Hardware Design |
217 |
To Reactor or Cyclone
T
3 to 5
Riser
Daimeters
Disf
ISteam
(Typical for Multiple Nozzles)
Superficial velocity
0.3 - 0.4 ft/sec
Steam or fuel gas
Drain
Figure 7-2. Schematic of a typical catalyst lift system.







4 Fluid Catalytic Cracking Handbook
Table 7-6
Process and Mechanical Design guidelines for Slide Valves
perating pressure drop |
Minimum 1.5 psi (10 Kp), maximum 10 psi |
|
(70 KP) |
opening @ design |
40%–60% |
circulation |
|
aterial |
Shell: carbon steel with 4-5 in. (10-12 cm) |
|
thick heavy weight, single-layer, cast-vibrated |
|
refractory with needles. |
|
Internals: 304H stainless steel for temperature |
|
>1,200°F (650°C) and Grade H, \\% chrome |
|
for <1,200°F. |
|
Internal components exposed to catalyst should |
|
be refractory-lined for erosion resistance. |
|
Sliding surfaces should be hard-faced, mini- |
|
mum thickness \ in. (3 mm). |
onnet design |
Sloped bonnet (30° minimum) for self-draining |
|
of catalyst. |
urge |
Purgeless design of stuffing box. Guides: |
|
slotted, hard-surfaced, and supplied with purge |
|
connections (normally closed). Nitrogen is the |
|
preferred choice of purge gas. |
ctuator type |
Electro-hydraulic for fast response and accu- |
|
rate control. |
ctuator response time |
A maximum of 3 seconds |
e said for spent catalyst distributors. This is particularly true in the se of side-by-side FCC units. Most side-by-side units suffer from neven distribution of the spent catalyst.
A well-designed air distributor system has the following characteristics:
•Distributes the air uniformly to the spent catalyst
•Mechanically withstands a wide range of operating conditions,
including start-up, shutdown, normal operation, and upset conditions
• Provides reliability with minimum maintenance


Project Management and Hardware Design |
227 |
rifice
Figure 7-5. Typical layout of a pipe grid distributor.

28 Fluid Catalytic Cracking Handbook
Outlet
Tube
Catalyst/Vapor
Barrel
Cone
Dustbin
Dipleg
Figure 7-6. Schematic of a typical cyclone.




Project Management and Hardware Design |
233 |
Ratterman, M., "An Approach to the Design and Analysis of Data from the Standpipe System on FCC Units," Gulf Research and Development, Pittsburgh, Pennsylvania, October 1983.
Wrench, R. E., and Glasgow, P. E., The M.W. Kellogg Company, "FCC Hardware Options," Paper No. 125C, presented at the AIChE National Meeting, Los Angeles, California, November 17–22, 1991.
CHAPTER 8
Troubleshooting
The cat cracker plays a key role in the overall profitability of the efinery. It must operate reliably and efficiently. It must also operate afely and comply with federal, state, and local environmental requireents. A typical FCC unit circulates tons of catalyst per minute, rocesses various types of feedstock and uses hundreds of control oops, any of which can make operation difficult. Proper troublehooting will ensure that the unit operates at maximum reliability and fficiency while complying with environmental concerns.
Troubleshooting deals with identifying and solving problems. Problems an be immediate or long term and can be associated with off-spec roducts, poor efficiency, process improvements, capacity increases, r potential shutdown items. Problems can be related to management, peration, hardware and equipment, or process issues. Solutions can nclude improved operating procedures and training, preventative aintenance, or installation of new equipment or controls.
This chapter outlines fundamental steps toward effective troublehooting. It provides a practical and systematic approach to developing solution. General guidelines are provided for identifying problems nd determining a diagnosis. In particular, the following FCC-related roblem areas are addressed in detail:
•CatalystCirculation
•Catalyst Loss
•Coking/Fouling
•Flow Reversal
•High Regenerator Temperature
•Afterburn
•Hydrogen Blistering
•Hot Gas Expander
•Products Quality and Quantity
234



I
o o
.c
CO
I
<
^>
CO
0
S
2
a.
CO

Low Pressure Upstream of the Slide Valve
Insufficient pressure |
Low Catalyst density |
build-up in the Standpipe |
in the Standpipe |
e-fluidization of the |
Too much, too little |
Improper placement |
Restriction |
|
Orifices are |
||||
talyst in the Standpipe |
or no Aeration Gases |
of the Aeration taps |
||
either plugged |
||||
|
|
|
||
|
|
|
or improperly |
|
|
|
|
sized |
|
Check if the |
|
i |
|
|
Verify Aeration Gas |
Use Rotameters |
||
ake sure instrument |
Catalyst |
instead of |
||
flow to maximize |
||||
adings are correct |
properties have |
Restriction |
||
pressure build-up |
||||
|
changed |
Oriffces(RO's) |
||
|
|
Figured-IB. Troubleshooting catalyst circulation.

High Pressure Downstream of the Slide Valve
r
High delta P across the Overhead Condensers
) r
• Add Fins to the Trim Coolers -19 flns per inch
* Water Wash the
Condensers
•Reduce No. of tube passes on the water
side
*Check pressure drop between Fin-Fans and Trim Coolers
High delta P across the Main Fractionator
r \^
\
f ^.
•Adjust the Pumparound rates
•Add Top or Side P/A
v |
^/ |
High Delta P across |
High Delta P |
the Reactor Ovhd. |
across the |
vapor line |
Riser |
J \. |
J V |
\( |
|
\ f |
|
|
|
|
• |
Increase |
Refer to |
|
Fluffing Gas or |
'Coking/Fouling' |
|
Steam to the |
Troubleshooting |
|
base of Riser |
Section |
« |
Replace the |
|
|
Curved section |
V |
J |
of the Riser |
|
||
|
V |
|
Figure8-1 C. Troubleshooting catalyst circulation.





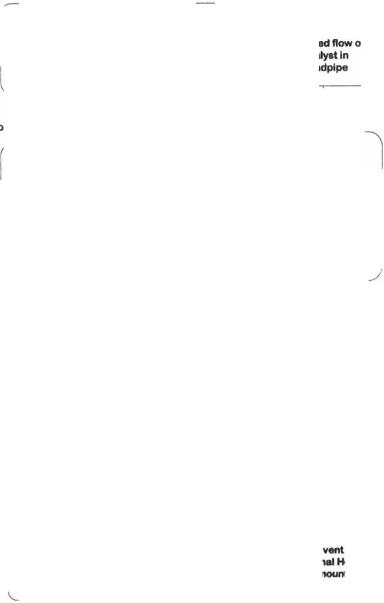


8Fluid Catalytic Cracking Handbook
•Confirm that the restriction orifices used for instrument purges are
in proper working condition and that the orifices are not missing.
•Consider switching to a harder catalyst. For a short-term solution, if the losses are from the reactor side, consider recycling slurry to the riser. If the catalyst losses are from the regenerator, consider recycling catalyst fines to the unit.
igure 8–4 is a summary of the above discussions.
Nearly every cat cracker experiences some degree of coking/fouling. oke has been found on the reactor walls, dome, cyclones, overhead apor line, and the slurry bottoms pumparound circuit. Coking and uling always occur, but they become a problem when they impact roughput or efficiency.
vidence of Coking/Fouling
Coking/fouling in the reactor and the main column can be detected by:
*Cavitation and/or loss of the main column bottoms pumps
*Fouling and subsequent loss of heat transfer coefficient in the bottoms pumparound exchange
*High pressure drop across the reactor overhead vapor line
*Excessive catalyst carryover to the main column
auses of Coking/Fouling
Coke forms in the reactor and main column circuit because of:
*Changes in operating parameters
*Changes in catalyst properties
*Changes in feedstock properties
*Changes in mechanical condition of the equipment
hanges in Operating Parameters
The operating conditions of the unit, particularly during startups and ed interruptions, will have a large influence on the formation of coke. oke normally grows wherever there is a cold spot in the reactor stem. When the temperature of the metal surfaces in the reactor


50 Fluid Catalytic Cracking Handbook
alls and/or the vapor line falls below the dew point of the vapors, ondensation occurs. Condensation and subsequent coke buildup are ue to cooling effects at the surface.
A high fractionator bottoms level, a low riser temperature, and a igh residence time in the reactor dome/vapor line are additional perating factors that increase coke buildup. If the main column level ses above the vapor line inlet nozzle, "donut" shaped coke can form t the nozzle entrance.
A low reactor temperature may not fully vaporize the feed; unvaorized feed droplets will aggregate to form coke around the feed ozzles on the reactor walls and/or the transfer line. A long residence me in the reactor and transfer line also accelerate coke buildup.
Insufficient bottoms pumparound to the main column heat-transfer one can also form coke.
hanges in Catalyst Properties
Certain catalyst properties appear to increase coke formation. Catalysts ith high rare earth content tend to promote hydrogen transfer reacons. Hydrogen transfer reactions are bimolecular reactions that can roduce multi-ring aromatics.
hanges in Feedstock Properties
The quality of the FCC feed also impacts coke buildup in the reactor ternals and vapor line and fouling/coking of the main column circuit. he asphaltene or the resid content of the feed, if not converted in e riser, can contribute to this coking.
hanges in Mechanical Condition of the Equipment
Damaged or partially plugged feed nozzles can contribute to coke rmation due to poor feed atomization.
Damaged shed-trays in the bottom section of the main cloumn can ause coke formation due to non-uniform contact between upflowing apors and downflowing liquid.
roubleshooting Steps
The following are some of the steps that can be taken to minimize oking/fouling:


Unscheduled Unit interruptions
loss of profit and higher maintenance costs
: |
Cavitation and/or loss |
Fouling and loss of |
of Main ColumnBottoms |
Heat Transfer in |
|
|
Pumps |
Bottoms Exchanger |
Higher pressure drop across the Reactor Overhead vapor line
in Operating
ns |
|
intheReactor |
High Levelof Rare- |
heat-up |
Earth in the |
Column Bottoms |
Catalyst |
or temperature |
Low Catalyst Micro |
Activity Test (MAT) |
|
dence Time in the |
|
d Main Column |
|
ms temperature |
|
msPumparoundRate |
|
nger tube wall |
|
Changes in feedstock Properties
High Moleweight Asphaltene & Resins, precipitate and bind to process equip.
High Levelsof
Cracked Feedstock
Changes in Mechan
Conditions of the
Equipment
Damaged or par plugged Feed N Loss of the Shed Feed leaking thr Bottoms exchan Feed Diversion
re |
J |
Figure 8-5A. Troubleshooting coking/fouling.
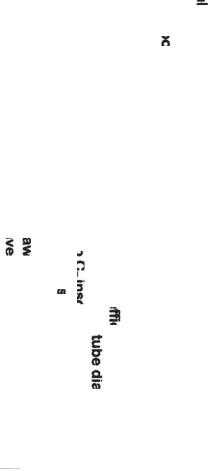
Recommendations:
erly insulate RXOverhead piping Main Column Inlet nozzle
p the tube velocity > 7ft/sec p Main Column Bottoms perature < 700°F
a "dry"Dome SteamSystem
mber:
comesto Coking, g Residence Time is e as increasing
s temp, by 25°F
*Increase Bottomstraffic
*Inject a continuous CycleOilflush into inlet Bottoms PAExchangers
*Install duplex filters upstream of Bottoms Pumps
*Install high efficiency feed nozzles
*Use 1" or larger tube diameter
*Keep C7 insolublesin Slurry System less than 5% wt
*Use U-tube for BottomsExch.
*Draw more Bottoms Product
*Have a spare BottomsExchanger bundle
Figure 8-5B. Troubleshooting coking/fouling.




Table 8-1
A Cause and Effect Shutdown Matrix
Effect: |
Regan |
Riser |
|
|
|
Spent |
Regan |
|
Catalyst |
Emergency |
Feed to |
Slurry |
HCO |
Catalyst |
Emergency |
|
Slide Valve |
Steam |
Riser |
Recycle |
Recycle |
Slide Valve |
Steam |
|
Process |
Closed |
Process |
Process |
Process |
Process |
Closed |
ue low |
|
|
|
|
|
|
|
sure |
|
|
|
|
|
|
|
ue |
Close |
Open |
Close |
Close |
Close |
|
|
ntial |
|
|
|
|
|
|
|
slide |
|
|
|
|
|
|
|
rential |
|
|
|
|
|
|
|
slide |
|
|
|
|
|
Close |
Open |
ssure |
|
|
|
|
|
|
|
/low |
Close |
Open |
Close |
Close |
Close |
|
Open |
eed |
Open |
Close |
|
|
|
|
|
|
|
|
Close |
|
|
|
|
r high |
Close |
Open |
Close |
Close |
Close |
|
|
wn |
Close |
Open |
Close |
Close |
Close |
Close |
Open |

Low Catalyst/Oil ratio Poor Yields
Loss of Catalyst Activity Equipment Wear
V |
, |
'Feedstock
•High Fraction of 1050°F+ Material
V
^ |
' Catalyst |
|
Operating |
Mechanical |
|
• High Level |
|
Conditions |
Conditions |
|
|
|
|
|
|
of Rare |
|
Low StrippingSteam |
• Damaged Strippin |
|
Earth |
|
Low Dispersion |
Steam distributor |
|
• High Level |
|
Steam |
• Damaged Feed |
) |
of MaWx |
|
High Preheat |
Nozzles |
Activity |
J |
Temperature |
• Damaged Air or |
|
|
v |
High Reactor |
Catalyst Distributo |
|
|
|
|
||
|
|
|
Temperature |
|
|
|
|
Low Cat/Oil Ratio |
|
endations |
Install high efficiency Feed Nozzles |
|
|
|
Lower Preheat Temperature |
|
Inject Naphtha Quench to Riser |
|
increase Stripping and Dispersion Steam |
|
Switch to a Coke Selective Catalyst |
|
Figure 8-7, Troubleshooting high regenerator temperature. |



o
O O
<Dc
3 CO
-o o -
0)
2
•*-* 0)
s |
go £« |
|
0) |
|
Q ffll |
« |
|
o |
|
o |
CD |
w |
|
X |
|
|
|
|
0) |
|
|
|
|
O) |
|
|
|
|
.£ |
|
|
|
|
o |
|
|
|
|
o |
|
|
|
|
x: |
|
|
|
|
(o |
|
|
|
|
_© |
|
|
|
|
xj |
|
|
|
|
o |
|
|
|
|
op |
|
|
|
|
CO |
|
|
|
|
3 |
|
|
|
|
O) |
perating Cond |
|
|
|
II |
|
iig |
rt |
T3 tJ |
|
|
|
|||
|
|
£ < < |
||
|
|
|
2 |
T3tJ |
:sasneo
Q.

oblem: |
Hydrogen Blistering, Cyanide Attack |
Feed |
Catalyst |
Operating |
Properties |
Properties |
Conditions |
ncrease in |
•Increase in |
•A lower Main Column |
eed Nitrogen |
Matrix Activity |
top temperature |
|
|
•Partial Combustion |
|
|
•Higher Reactor |
|
|
Temp. |
/Mechanical Conditi
•Lack of stress relief •Poor material & workmanship
• Inadequate Reside Time to Separate G Lean OH, & Water
nitor Ammonia & Chloride in the Overhead Water, keep Ammonia Sulfide <5,000 ppm e Steam Condensate as Water Wash at a Rate of 1-2 gpm/1000 bbl of Fresh Feed
e Ammonium Polysulfide Solution (especially if HCN > 25 ppm) to 10–20ppm Residual HCN ke sure the WashWater is injected uniformly into the Gas Stream
e "Feed Forward" Water Wash Scheme instead of "ReverseCascade" tall & monitor Hydrogen probes in the key areas ect a Dehazer Additive into the High Pressure Separator (HPS)
tall Coalescer in the Lean Oil and Sponge Oil Streams ess relieve carbon steel
Figure 8-9. Troubleshooting hydrogen blistering.

64 Fluid Catalytic Cracking Handbook
invisible while everything is running well. Compare the readings month-to-month to spot trends.
3.Continuous monitoring of the third-stage separator performance. If catalyst is showing up downstream, consider using more than the "standard" 3% flue gas underflow. The blowcase needs more attention than it usually gets.
4.On-line cleaning—inject walnut hulls into the inlet of the expander weekly.
5.Thermal shocking—reduce feed in 20% increments while maintaining maximum air rate to the regenerator. Cool the expander inlet temperature to around 1,000°F (540°C) and hold for at least one hour. This is not a procedure that the expander vendor supports, but it is practiced by many refiners.
Figure 8-10 provides an outline of the above discussion.
The performance of the unit is a function of feed quality, catalyst roperties, operating variables, and the mechanical condition of the nit. The indicators used to measure the unit's performance are:
*Conversion
*Dry gas yield
• Gasoline quality * Light olefin yield
Observing a Low Conversion
"True" conversion is affected by feed quality, catalyst, operating ariables, and mechanical conditions (Figure 8–11A).
eedstock Quality
The feed properties that lower conversion are:
• Increase in residue (1,050°F+) (565°C+) content
•Increase in feed impurities such as nickel, vanadium, sodium, or nitrogen
« Increase in naphthene and aromatic fractions of the feed


Problem: |
Loss of Revenue |
Reduce Gasoline Olefins |
|||
Off-Spec Products |
|
Figure 8-11E |
|||
wer Conversion |
High Dry Gas Yield I.ower GasolineYield |
|
Lower GasolineOcta |
||
Fig. 8-11 B |
Figure 8-1 1C |
[ |
Figure 8-11D |
||
|
^ |
f |
^ t |
|
Changes in |
|
Changes in |
||
eed Properties |
Catalyst Conditions |
|
|
• |
• |
*
re Residue
re Contaminants sParaffins
re Aromatics
d of run for Feed T
ew Fee^ perties
ck for changes in gen, Nl, V,
0°F
d APIgravity, K tor, Rl & 650°F
\ |
r•Loss of Micro |
> |
|
* |
|
|
Activity |
|
•Loss of Surface Area dueto Thermal and Hydro-thermal Oeact. increase in
J CRC
•Change in Catalyst ^formulation j
i
•Track Catalyst
Activity
•Cheek Fresh Catalyst
availability & source
,•Verify Catalyst
•addition rate
> r
Changes in
Operating Conditionss
•I
•Lower Reactor temp.
•Lower cat/oil Ratio •Lower Dispersion Steam
^ |
J |
^Trend Reactor Temp, ^ cat/oil Ratio and Dispersion SteamRate •Check recent temp, and/or press, excursions
•Verify accuracy of VReactortemo J
^ f
Changes in
Mechanical Conditio
\f
c•Damaged or plugged^ feednozzles
•Damaged Stripper
Steam Distributor
V
|
\t |
f |
» |
•Check pressure profil around FeedNozzles •Track H2 in Coke •Survey ttie Stripper
>-
Figure 8-11A. Troubleshooting desired product quantity and quality.

Troubleshooting 267
The decreases in microactivity and surface area are strong functions thermal deactivation in the regenerator and the presence of metals the feed.
perating Variables
The following operating parameters lower conversion:
•Decrease in the reactor temperature
•Decrease in the catalyst-to-oil ratio
•Decrease in the atomizing steam
•Decrease in the fresh catalyst addition rate
echanical Conditions
Damaged or plugged feed nozzle(s) and/or damaged stripping steam stributor(s) are the common causes of mechanical failures that fect "true" conversion. Note that the "apparent" conversion, as scussed in Chapter 5, is affected by the distillation cut point and ain column operations.
roubleshooting Steps
•Trend the feedstock properties; look for changes in the K factor, 1,050°F+ (565°C+), aniline point, refractive index, and °API
gravity. The feed endpoint may have been increased to fill the unit. The conversion penalty may be a small price to pay for the increased capacity, but the penalty can be minimized. Verify that the refinery LP reflects current data on yields and product quality.
•Plot properties of the fresh and equilibrium catalysts; ensure that the catalyst vendor is meeting the agreed quality control specifications. Verify that the catalyst vendor has the latest data on feed properties, unit condition, and target products. Verify the fresh makeup rate. Check for recent temperature excursions in the regenerator or afterburning problems.
•Trend the reactor temperature, cat-to-oil ratio, and atomizing steam rate. Verify the accuracy of the reactor temperature thermocouple and atomizing steam flow meter.
•Perform a single-gauge pressure survey around the feed nozzles. Calculate the hydrogen content of the spent catalyst. Conduct a

68 Fluid Catalytic Cracking Handbook
gamma ray scan test to verify the mechanical condition of the stripping steam distributor.
Observing a High Dry Gas Yield
Dry gas yield is affected by everything that affects conversion Figure 8-11B). Changes to increase conversion can increase the dry as yield.
High gas yield shows up as higher speed on the compressor (if entrifugal). In many cases, lower molecular weight (due to higher ydrogen content) can have the same effect.
eedstock Quality
The feed parameters that increase the dry gas yield are:
* |
Increase |
in nickel and vanadium content |
* |
Increase |
in naphthene, olefin, and aromatic concentration, which |
|
is indicated by an increase in the refractive index and decreases |
|
|
in aniline point and K factor |
atalyst Properties
The E-cat properties that increase dry gas yield are:
* Increase in the level of nickel, vanadium, and sodium
*Decrease in E-cat activity, surface area, fresh catalyst activity, and rare earth content
*Increase in the gas and coke factors of the E-cat
perating Variables
Operating parameters that increase dry gas yield are:
*Increase in the reactor temperature
*Increase in the regenerator temperature
«Decrease in the atomizing steam
*Increase in slurry or HCO recycle
echanical Conditions
Mechanical conditions that can increase dry gas yield are:
» |
A failing reactor temperature thermocouple |
* |
Partially plugged or damaged feed nozzles |

0 Fluid Catalytic Cracking Handbook
roubleshooting Steps
The following steps should be carried out:
•Track changes in feed metals content, trend the aniline point, and refractive index.
•Trend changes in catalyst activity, surface area, rare earth, and metals content. Consider adding/increasing metals inhibitor.
•Trend changes in the molecular weight of the gas at the firststage suction. Verify that overhead cooling and wash systems are in order.
•Verify the position of the wet gas compressor spillback. Determine if the compressor turbine needs water washing. Trend the level
of inert gases in the dry gas.
«Calibrate the reactor temperature controller. Conduct a pressure survey around the feed nozzle piping to verify its mechanical
integrity.
•If no significant problems are found other than feedstock changes, verify that the refinery LP team has current data on unit yields and product quality with this feedstock. The result of troubleshooting may be that increasing dry gas may be a necessary price for changes in the feed.
bserving a Lower Gasoline Yield
The FCC "true" gasoline yield largely depends on changes in feed uality, catalyst properties, operating variables, and mechanical contions (Figure 8–11C).
eedstock Quality
Paraffinic feedstocks produce the most gasoline yield (but the west octane). The common indicators of any increase in feed parfinicity are:
•Increase in the K factor
•Increase in the aniline point
•Increase in the nickel-to-vanadium ratio
•Decrease in the fraction of "cracked" material

c .2
§
_ c
«
0 J.
1
o
O fd o
o
lt!0J
•o
S
> m J» c* *•
s .1 8 § .s>
-J _J CO Q O X
">.
o
!»
«C
O)
o
o o x:
OT
CD
00
3
£


sin mditions
a
o
C *»?
n? C
0)0
e O
CO -M
•C 091
o2?1
O
™_^
0}
_ 0)
Properti
Ganges ir
o o>
0)
u.
^ i® §• |O
|
|
|
|
|
« |
a. |
|
|
|
|
|
CO |
> |
|
M |
|
0£ |f |
O |
ce |
|
|
|
|
|
|
u |
i. |
|
Q h- if |
_l Q O |
|
|
||
|
VI |
|
|
|
|
J |
|
^ |
|
X |
A |
|
|
|
o £ |
o |
|
|
||
|
*• fci_J?'i_ |
|
|
|||
|
® ® o 5 <5 |
|
|
|||
^w, |
aw |
SI I |
|
|
||
1 |
1 |
|
|
|
|
|
|
.S |
.S' S O o |
|
|
||
|
* |
* • |
• |
|
|
V.J
|
1^•£ C |
C |
.1 |
|
|
|
E |
|
•^ |
|
<0(0SI |
|
(0 |
^ W |
|
|
^ w |
M W n* ^ |
|
|
O w "f» u SL i" "0 ^ |
||
(1) |
|
|
3 2J « |
S 2 m 2 S !5 0 2 |
|||
|
Q i u. £ |
(O: ui. c- |
|
V) |
V |
|
_J |
3 |
|
CO
O
*ls, |
|
|
8 |
|
o1" |
«? |
|
<»> |
|
0 - |
SW |
|
eg |
|
0} x |
fl) (8 2> |
g> |
||
><r>Oir |
||||
v |
|
|
y |
o |
|
|
|
|
o |
|
|
|
|
XT |
__ |
|
"^v |
|
J3 |
S |
o |
—i |
|
|
3 |
< |
0 |
|
Q |
T3 |
|
|||
. o |
K |
|
••" |
|
11 5 81 |
S |
|||
H O T Z O Q |
|
a, |
||
V. * |
* |
• |
I |
^ |
|
|
|
|
v» |
C |
|
|
|
A «• |
i |
--o-S |
a |
|
|
|
ou c o i. Z |
|
||
|
, >,^ «S T |
|
||
(/) |
Bfl-gJ |
|
||
S O < oto |
|
|||
C |
y |
|||
o v |
• |
• |
"o
CO
74 Fluid Catalytic Cracking Handbook
Higher Feed K Factor
Increase in the Catalyst Rare
Earth content
olutions:
Decrease in the Catalyst Matrix
Activity
Larger Zeolite Unit Cell Size
Add ZSM-5 Additive
Higher Cat/Oil ratio
Higher Mix Zone temperature
Split Feed injection
Riser Quench
Figure 8-11E. Troubleshooting high gasoline olefins.
eedstock Quality
Gasoline octane is increased by:
•Increases in the refractive index
•Decrease in the K factor and aniline point
•Increase in the bromine number
atalyst Properties
The fresh catalyst's chemical properties also influence the FCC asoline octane. Gasoline octane is increased by:
• Decrease in rare earth and unit cell size
•Decrease in sodium content
•Increase in matrix activity
perating Conditions
A number of operating variables can change the octane value. The ctors that increase octane are:
• Increase in the reactor temperature. In general, one research octane number increase per 17°F (10°C) increase in the reactor temperature.
• Decrease in the catalyst-to-oil ratio (by increasing thermal reactions).
Troubleshooting 275
•Increase in coke content of the regenerated catalyst.
•Increase in the regenerator temperature.
•Increase in the naphtha quench or HCO recycle.
•Decrease in the gasoline end point.
•Decrease in the gasoline vapor pressure.
echanical Conditions
The main mechanical conditions that affect octane are the type and ondition of the feed nozzles. Low-efficiency feed nozzles actually crease the gasoline octane due to promotion of thermal reactions in e mix zone. High-efficiency feed nozzles improve feed/catalyst ixing and increase the gasoline yield, but decrease gasoline octane.
roubleshooting Steps
• Plot the feed refractive index, °API gravity, and aniline point. Determine any shift in the amount of cracked gas oil in the feed.
•Track the unit cell size, matrix activity, and rare earth content of the catalyst.
•Determine if coke on the catalyst has changed.
« |
Verify accuracy of |
the reactor temperature. |
• |
Check for changes |
in the gasoline end point and vapor pressure. |
•Check the conditions of the feed nozzles and amount of atomizing steam.
asoline Vapor Pressure/Light Olefln Yield
Reformulated gasoline specifications require lower vapor pressure the blended gasoline. It also requires maximum feed to the alkylaon unit. This puts more pressure on the gas plant, particularly the ebutanizer. Floating the tower pressure is often the best way to meet oth constraints.
This chapter highlights the common problems, symptoms, and obable causes that may be encountered in troubleshooting FCC units. addition, a systematic approach is outlined to provide solutions and rrective action. The suggested solutions are necessarily generic but ply to a wide variety of units.
CHAPTER 9
Debottlertecking
and Optimization
Troubleshooting, optimization, and debottlenecking are three steps a continuous process. There is some overlap and gray area among them. Troubleshooting refers to the solution of short-term problems. The signment is usually initiated by operations or maintenance. The lution usually involves something that can be done online. Troubleooting was discussed in Chapter 8.
Optimization refers to maximizing feed rate and/or conversion with e existing equipment while reaching as many constraints as possible. can be the response to changes in the feed quality, ambient contions, or the market demands. Although it is not discussed separately ere, it is the incentive for most debottlenecking projects.
Debottlenecking often refers to hardware changes, small or large. It is rected at the bottlenecks identified during optimization. It includes rojects that cannot be completed online, such as installing new ternals in a vessel. Debottlenecking is the main focus of this chapter.
NTRODUCTION
Most FCC units are big profit makers. Therefore, they are operated several constraints. Debottlenecking is the effort to locate and vercome these constraints. The profitability of an FCC operation is aximized when the unit is "pushed" simultaneously against multiple nstraints. Debottlenecking means finding the constraint or combinaon of constraints that cost the refinery lost opportunities and arriving
the right fix.
A properly configured advanced process control (APC) system could low for on-line, continuous optimal unit operation and push the FCC perations to multiple constraints simultaneously.
The main purpose of debottlenecking is to increase the refinery's ofit margin. In the FCC, this usually means:
276

|
Debottlenecking and Optimization |
27? |
• |
Raising the feed rate |
|
» |
Processing lower quality feedstocks |
|
•Reducing dry gas and coke yields, therefore, increasing total liquid products
As with troubleshooting, a proper debottlenecking exercise must onsider the effects of feedstock, catalyst, operating conditions, mechanical ardware, environmental issues, and the ability of the rest of the finery to handle the additional feed/product rates and quality.
PPROACH TO DEBOTTLENECKING
Debottlenecking requires a comprehensive test run to determine the peration's present status. Elements of a test run include:
« Overall and component material balance
•Reactor/regenerator heat balance
•Hydrogen balance
•Sulfur balance
•Reactor/regenerator pressure survey
•Utility balance
•Evaluation of the interaction among feed quality, catalyst properties, and operating conditions
•Main fractionator and gas plant modeling
If the object of debottlenecking is to run heavier feeds, multiple test ns may be needed with heavy feed added in stages.
The next step is to identify the incremental value of:
» Fresh feed rate
•Each FCC product
•Octane and cetane numbers
•Other product quality issues (sulfur, slurry ash level, etc.)
ith this information, the constraints on operation can be identified nd the value of addressing them can be evaluated.
mproving FCC Profitability through Proven Technologies
Once the performance of the FCC unit is optimized through the use f new catalyst and operating practices, the unit's profitability can be rther improved by installing proven hardware technologies. The urpose of these technology upgrades is to enhance product selectivity




|
|
|
Debottlenecking and |
Optimization |
281 |
|
|
|
Example 9-2 |
|
|
Changing Piping in Furnace from Two-Pass |
to Four-Pass |
|
|||
Case I: Two-Pass Furnace |
|
|
|
||
50,000 BPD total charge (25,000 BPD to each pass) |
|
||||
°API gravity of feed |
= 25 |
|
|
||
Furnace outlet temp. = 500°F |
|
|
|||
Furnace tube diameter (I.D.) = 4.5 in. |
|
|
|||
AP100= 0.0216 x |
|
|
|
|
|
here: |
|
|
|
|
|
Pi(K) = Pressure |
drop |
(psi) per |
100 feet of pipe |
|
|
f = Friction |
factor |
= 0.017 |
lb/ft3 |
|
|
p = Flowing density = 47.4 |
|
|
Q = Actual flow rate = 864 GPM d = Tube inside diameter = 4.5 in.
AP!00 = 7.0 psi
Assuming a total 700 ft of equivalent pipe in the furnace, the total essure drop is 49 psi
Case II: Switching to Four-Pass
AP1(X!= 1.9 psi
Assuming a total 500 ft of equivalent pipe in the furnace, the total essure drop is 9.4 psi
aving in pressure drop = 49.0 - 9.5 = 39.5 psi or an 81% reduction
This section addresses the following:
* |
Mechanical limitations |
||
• |
Riser |
termination |
device |
« |
Feed |
and catalyst |
injection system |




Debottlenecking and Optimization |
285 |
Stripper
Gas
(D
</>
be
P 1 > P 2 > P 3
Figure 9-2. Lummus direct-coupled cyclone design.
surance in case the trickle valves stick open. In this design, the riser clones operate at a positive pressure and sealing the diplegs miniizes carry-under of reactor vapors into the reactor housing.
The catalyst must be fluidized to provide an effective seal for the plegs. Fluidization is critical; without it, the diplegs cannot discharge e catalyst and will plug, with possible massive carry-over to the main actionator. To ensure this uniform fluidization, the system uses an ditional steam distributor.

86 Fluid Catalytic Cracking Handbook
Cyclone Dipleg*
Restraint
Figure 9–3. Typical trickle valve.
Cyclone Dipleg
Pivot
Counterweight
\
Figure 94. Typical flapper valve.
In KBR closed cyclone technology, each set of riser and upper eactor cyclones is connected via the use of a "slip joint" conduit. The tripper steam and hydrocarbons, as well as dome steam, exit e reactor housing by entering through this conduit as shown in igure 9-5.

Debottlenecking and Optimization |
287 |
Cyclone
Dipleg
05
16 o
Braces (as required)
Splash Plate
Figure 9-4A. Typical splash plate.
OP VSS System
UOP's current RTD offering is the vortex separation system (VSS), shown in Figure 9-6. VSS is for FCC units having an internal riser nd a similar design (VDS) is for external risers. The catalyst-vapor ixture travels up the riser through the chamber and exits through veral arms. These arms generate a centrifugal flow pattern that parates the catalyst from the vapor inside the chamber. The catalyst ccumulates in a dense phase at the base of chamber, where it is "pre~ ripped" prior to flowing into the reactor stripper. The stripped ydrocarbon vapors are fully contained in the chamber and exit with e rest of the riser effluent vapors to the secondary cyclones.
The reactor vapors leave the VSS through an outlet pipe. Secondary clones are directly connected to this outlet pipe through an expansion
88 Fluid Catalytic Cracking Handbook
Product
Dome
Riser
Catalst
Level
Splash
Plate
Figure 9-5. KBR closed cyclone system.
int. The VSS outlet pipe contains several vent pipes in which the actor dome steam and a portion of the stripping steam/hydroarbon vapors leave the reactor through these vent pipes.
tone & Webster Engineering Corporation (SWEC)
SWEC offers a reactor quench system rather than a closed cyclone ystem. Their typical RTD is an external, rough-cut cyclone (see Figure -7). The vapors from the rough-cut cyclone enter the reactor vessel.

Debottlenecking and Optimization |
289 |
Expansion
Joint
Flapper
Valve
Spent
Catalyst to Stripper
Figure 9-6. UOP vortex separation system.

0 Fluid Catalytic Cracking Handbook
LCO
Quench
To Catalyst
Pre-Stripping Stripper
Steam
Figure 9-7. SWEC external cyclone with quench.

92 Fluid Catalytic Cracking Handbook
eed Nozzles
Important features of a feed injection system include:
• Fine atomization of feed
• High velocity coverage of riser cross-section
•Intimate mixing of catalyst and oil
•Rapid heat transfer from catalyst to oil
•Instantaneous vaporization of feed
•Minimum catalyst back-mixing
•Maximum catalytic reactions while minimizing thermal reactions
A good feed injection system will produce:
•Small droplet size
•Efficient mixing of oil and catalyst
•Complete riser coverage
The feed injection system has come a long way. The early designs eatured open pipes with no consideration for feed vaporization or atalyst/vapor mixing. Currently, FCC technology licensors offer many ersions of feed injection systems. Figure 9-8 is a typical modern feed ozzle. In general, these nozzles incorporate some of the following esign features:
Oil Inlet
Diverging Dual Slot |
Target Bolt |
Figure 9-8. SWEC feed nozzle.
Debottlenecking and Optimization |
2§3 |
* Steam is used to disperse and atomize the oil/residue feed
•The spray pattern of the oil/steam leaving the nozzle tips tends to be flat (fan spray)
•The assembly includes multiple nozzles in a radial pattern
*The nozzles are designed for a "medium" oil-side pressure drop, generally in the order of 50 psi
Some of the general criteria for choosing feed injection technology clude:
• Total installed cost
* Dispersion steam and/or lift steam/gas requirements, including flow rate, temperature, and pressure
* Oil pressure requirement
• Proven track-record of operational reliability
he choice of the feed injection system should be based on the endor's experience in similar units with similar feeds and on his yield rojection and/or performance guarantee. However, it may be difficult substantiate the guarantee when other changes are being made in
he unit.
pent Catalyst Stripper
Spent catalyst from the reactor/cyclones discharges into the stripper. tripping steam displaces hydrocarbon vapors entrained with the atalyst and removes volatile hydrocarbons from the catalyst.
As part of optimizing the unit, the stripping steam rate should be djusted up or down by 5%. The regenerator temperature and/or CO2/ O ratio will be the main indicator of insufficient stripping. The test ends hen there is no significant response in the regenerator temperature. In the past several years, more attentions have been given to improv- g mechanical performance of the reactor stripper. Proprietary stripper esigns are being offered by the FCC technology licensers in attempts o improve the catalyst/steam contact.
ebottlenecking Catalyst Circulation
Any attempt to increase the unit feed rate will generally require an crease in catalyst circulation. The unit pressure balance and catalyst irculation were covered in Chapter 8.
94 Fluid Catalytic Cracking Handbook
The following should be considered when debottlenecking:
*Differential pressure alarm/shutdown
*Increasing slide valve size
*Standpipes
*Catalyst selection
ifferential Pressure Alarm/Shutdown
Differential pressure shutdowns are a critical part of the unit's safety ystem. No attempt to lower the setting on the shutdown should be ade without adequate consideration. On the other hand, pressure is ost across the slide valves and costs money.
Multiple, independent differential pressure alarm/shutdown switches an be installed with two out of three voting. This can satisfy the afety requirement, increase the comfort factor, and gain valuable ressure drop.
Radial feed nozzles also minimize the possibility of a reversal. New alve actuators can operate more quickly and reliably, also increasing he safety factor.
The test run may indicate that the slide valve is open too far. Most perators prefer to keep the valve in the 40% to 60% range. They lose major comfort zone if the valves open more than this. A larger valve r larger port can be installed in the existing valve.
tandpipes
If the unit pressure balance |
indicates that either the pressure gain |
n the Standpipes is inadequate |
or the delta P across the slide valves |
erratic, standpipe aeration and instrumentation should be examined. edesigning the aeration systems or replacing the Standpipes can gain aluable pressure drop. Proper instrumentation can include independent eration flow to each tap, flow indicators/controllers on each, and ifferential pressure indicators between the taps.
Beyond the Standpipes, the available delta P across the valve is
ffected by the pressure drop in other circuits. For |
the regenerated |
|
atalyst slide valve, downstream pressure is affected |
by: |
|
* |
Feed injection system |
|
» |
Riser |
|

96 Fluid Catalytic Cracking Handbook
Other more capital-intensive modifications include installing a edicated air blower for the spent catalyst riser. The spent catalyst riser ften requires a higher back-pressure than the main air blower to eliver the catalyst into the regenerator. Therefore, less total combuson air would be available if one common blower is used to transfer pent catalyst and provide combustion air to the air distributors.
Taking higher-pressure services off the main air blower can allow to run out on the curve and deliver more air. The main air blower an also be upgraded to provide added capacity. This includes reducing eal clearance, increasing the flow passing area, and increasing the heel tip diameter. The original equipment manufacturer (OEM) can e contacted for feasibility of this upgrade.
egeneration
Regenerator designs have changed since most units were built. If he unit test run indicates high CRC or if the catalyst will benefit from lower CRC, the regenerator internals should be reviewed. If the data ndicates wide temperature differences across the bed or afterburning, r if the unit has had some excursions, it should be examined.
The regenerator review will include spent catalyst distribution, air istribution, and cyclones. If the test run with heavy feed indicates a emperature limitation, catalyst coolers, partial combustion, or riser uench should be considered.
LUE GAS SYSTEM
The FCC is usually constrained by environmental permits. If the unit ndergoes significant expansion, it may lose "grandfather" protection. he environmental limits include the amount of coke burned in the egenerator and emission rates of particulates, SOx, NOX, and gasoline ulfur. Increasing the feed rate or running heavier crude can increase ll of these emissions. The technology for control is discussed in hapter 10.
CC CATALYST
The FCC catalyst's physical and chemical properties dictate how uch feed can be processed. Chemical properties, such as rare earth

Debottlenecking and Optimization |
2§7 |
nd unit cell size (UCS), affect the unit heat balance and wet gas ompressor loading. Physical properties, such as particle size distriution and density, can limit catalyst circulation.
Consider reformulating the catalyst—custom formulations are availble. Increasing rare-earth content can reduce the wet gas rate. Catalyst usually selected for properties other than its ability to flow. Howver, if it does not flow, it is not going to work well. Catalyst physical roperties should be compared with those of catalysts that have circuted well. Evaluate the economics of using metal passivation additives nd other catalyst enhancing additives.
ebottlenecking Main Column and Gas Plant
Debotflenecking usually results in more feed. Both the main fractionator nd the gas plant must be able to recover the incremental product. The main fractionator can be limited by several factors including:
• Heat removal limitations » Tray flooding
• Fouling and coking
Heat removal can be limited by several factors including:
• Fixed reboiling duties in the gas plant
•Lack of heat exchanger in the pumparound circuits
•Jet or liquid flooding in one or more sections of the main fractionator
•High bottoms temperature leading to fouling or high LCO endpoint
•Overhead condensing capacity
Moving heat up the tower improves fractionation by increasing the apor-liquid traffic. This is limited by flooding constraints and excesve temperature in the bottom.
One method of maximizing the LCO end point is to control the main actionator bottoms temperature independent of the bottoms pumpound. Bottoms quench ("pool quench") involves taking a slipstream om the slurry pumparound directly back to the bottom of the tower, ereby bypassing the wash section (see Figure 9-9). This controls the ottoms temperature independent of the pumparound system. Slurry kept below coking temperature, usually about 690°F, while increas- g the main column flash zone temperature. This will maximize the CO endpoint and still protect the tower.




Debottlenecking and Optimization |
301 |
•Closing the spillback valves.
•Removing external streams. If gas comes from another unit or vents from a column in the gas concentration unit, consider routing it to the interstage rather than the suction. The refinery needs to evaluate if external streams are worth recovering or whether they can be routed elsewhere.
•Installing an advanced surge control system.
•Verifying that the flow rates of corrosion inhibitor and antifoulant are adequate for the new operating conditions.
mproving Performance of Absorber and Stripper Columns
The objective of the primary absorber/stripping towers is to maxiize recovery of C3 and heavier components while rejecting C2 and ghter to fuel. C3 is first absorbed and then C, and lighter components e stripped. Although maximizing C3-C4 recovery for alkylate feed very profitable, lower recoveries are often accepted to maximize the CC conversion and/or feed rate.
Propane/propylene recovery can be enhanced by:
•Increasing the gas plant pressure. A 10 psi increase in absorber pressure increases C3 recovery by 2% (Figure 9-10). However, this can reduce the wet gas compressor capacity. Fractionation efficiency decreases as the column pressure increases.
•Reducing the operating temperature. Consider adding an intercooler on the absorber. Minimize lean oil temperature. Consider the use of a chiller. Each 10°F reduction in lean oil temperature will increase C3's recovery about 0.8% (Figure 9–11).
•Increasing lean oil rate. This rate is often limited by the debutanizer hydraulic and reboiling/cooling capacity. A 50% increase
in lean oil/off-gas ratio increases C3's recovery about 2%.
• Removing waterfrom the lean oil. Installation of water draws and/ or a coalescer can improve recovery. Water can become trapped in the tower and cause poor tray efficiencies, foaming, and premature flooding.
•Minimizing over-stripping. Over-stripping can start a wheel with
the absorber. A 10% cut in stripping rate can increase C3's recovery by 0.8% (see Figure 9-12).
(text continued on page 304)


3-
1
lg



CHAPTER 10
Emerging Trends in
Fluidized Catalytic
Cracking
Although the demand for transportation motor fuels in North America projected to be limited, economic growth in other parts of the world ill require crude oil-based fuels. The Far East, Latin America, and e former Soviet Union are areas where there will be substantial mand for transportation fuels. The collapse of communism, the ivatization of state-owned oil companies, and the global awareness "environmentally clean fuels" will cause this growth.
In the coming years, the refining industry will be experiencing major allenges. In the United States, refiners are faced with excess refining pacity, projected slow growth, and high capital and operating costs comply with environmental health and safety regulations. The oil dustry in general, and the refining industry in particular, are techlogically sophisticated. They have a long history of innovations and oven track records in responding to challenge.
It is likely that the reliable crude oil supply will not diminish any me soon. Petroleum-derived fuels will remain the primary source of ansportation energy for well into the twenty-first century. Producers d refiners have been, and will be, environmentally responsible. The isting infrastructure of advanced product distribution systems can mpete with alternative fuels readily. Future fuels will be competitive, th economically and environmentally. New global market conditions ill dictate closure of inefficient facilities and investment in new chnology. Larger and more efficient operations will survive and will cus on the "niche market."
In the U.S., the crude processing capacity is expected to increase odestly, at a projected rate of 0.5 percent per year. No new refinery
307
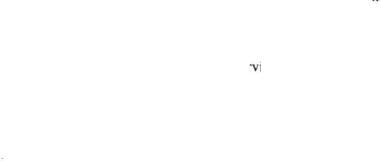










400 |
410 |
420 |
430 |
440 |
|
Gasoline EndPoint, Deg. F |
|
|
|
Figure 10-3, |
Gasoline |
sulfur versus its end point |
|


ui
O
8 ti
%'|OA '


22 Fluid Catalytic Cracking Handbook
.0 Volume of propylene + 1.3 volume of isobutane -> 1.80 volume alky late.
utyiene Alk\ lation
CH3
CH3 — C = CH2 + CH3 — CH — CH2 -> CH3 — CH — CH, — CH — CH3
CH, |
CH3 |
CH, |
CH3 |
PROPYLENE + ISOBUTANE -» 2,2,4 TRIMETHYLPENTANE
ypical Yield:
.0 volume of butylene +1.2 volume of isobutane —>1.70 volume alkylate.
Example 10-2
Etherification of Isobutviene
CH3 — C — CH3 + CH3 — OH -> CH3 — C — O — CH3
CH? CH3
ISOBUTYLENE + METHANOL -> METHYL TERTIARY BUTYL ETHER (MTBE)
ypical Yield:
0 volume of isobutane + 0.43 volume of methanol —> 1.27 volume MTBE.
There are etherification processes, such as MTBE and TAME, aimed producing ethers from C5, C6, and C7 tertiary olefins.
Both alkylate and ether have excellent properties as gasolineblending omponents. They have a low RVP,a high road octane, no aromatics, nd virtually zero sulfur. The emphasis on alkylation and etherification ill continue in both the U.S. and the rest of the world.

24 Fluid Catalytic Cracking Handbook |
|
|
|
Table 10-6 |
|
|
U.S. Crude Characteristics |
|
Year |
°APi Gravity |
Wt% Sulfur |
1983 |
32.92 |
0.88 |
1984 |
32.96 |
0.94 |
1985 |
32.46 |
0.91 |
1986 |
32.33 |
0.96 |
1987 |
32.22 |
0.99 |
1988 |
31.93 |
1.04 |
1989 |
32.14 |
1.06 |
1990 |
31.86 |
1. 10 |
1991 |
31.64 |
1.13 |
1992 |
31.32 |
1.16 |
1993 |
31.30 |
1.15 |
Source: Swain [24]
pgrade the atmospheric and/or vacuum bottoms in the residual fluidzed catalytic cracking (RFCC) unit. Although residue upgrading in he United States is mostly delayed coker based, most new FCC units re either residue crackers or have in-place provisions to process esidue at a later date. This is more pronounced in the new units built n the Far East, Europe, and Australia. The residue from their crude ils is more paraffinic and contains less metals than North Sea or Middle Eastern crude oils, which makes them more suitable for RFCC.
An RFCC is distinguished from a conventional vacuum gas oil FCC n the quality of the feedstock. The residue feed has a high coking endency and an elevated concentration of contaminants.
Coking Tendency
Residue feedstocks have a higher coking tendency, which is indiated by higher levels of Conradson carbon and a higher boiling point. he common definition of residue is the fraction of the feed that boils bove 1,050°F and Conradson carbon levels greater than 0.5 wt%. The esidual portion of the feed contains hydrogen-deficient asphaltenes nd polynuclear compounds. Some of these compounds will lay down n active catalyst sites as coke, reducing catalyst activity and selectivity.




28 Fluid Catalytic Cracking Handbook
Table 10-7
EPA's New Source Performance Standards (NSPS) for Gaseous Emissions from the FCC Regenerators
Source |
|
Allowable Limits |
arbon monoxide |
(CO)* |
Less than 500 ppmv in the flue gas |
itrogen oxides (NOX) |
None (local and regional only) |
|
articipates** |
|
A maximum of 1.0 pound of solids in the |
|
|
flue gas per 1,000 pounds of coke burned |
ulfur oxides (SO2 |
+ SO3)* |
Exempt if the feed sulfur is less than |
|
|
0.30 wt% |
If there is no add-on control such as a wet gas scrubber, 9.8 kilograms of (SO2 + SO3) per 1,000 kilograms of coke burned. This is approximately equal to 500 ppmv. Add-on device: reduce (SO2 + SO3) by at least 90% or no more than 500 ppmv, whichever is less stringent.
Effective January 1984
*Effective June 1973
he quality of FCC stocks, operating conditions, catalyst type, and echanical condition of the unit. Processing feeds that contain a high oncentration of residue, sulfur, nitrogen, and metals will release a reater amount of SOX, NOX, and particulates. Various technologies re available to reduce flue gas emissions.
articulates
Electrostatic precipitators (ESP) and wet gas scrubbers (WGS) are idely used to remove particulates from the FCC flue gas. Both can ecover over 80% of filtrable solids. An ESP (Figure 10-6) is typically nstalled downstream of the flue gas heat recovery (prior to atmosheric discharge) to minimize particulate concentration. If both low articulate and low SOX requirements are to be met, a wet gas scrubber uch as Belco's (Figure 10-7) should be considered. If SOX removal
BUS DUCT-
INSULATOR COMPARTMENT,
ROOF
EN
ORMER
FIER
DISCHARGE ELECTRODE
RAPPER
RAPPER INSULATOR
HIGH-VOLTAGE SYSTEM
SUPPORT INSULATOR
COLLECTING SURFACE
RAPPER
•SIDE
DOO
DISCHARGE ELECTRODE
HOPPER-
Figure 10-6. Typical electrostatic precipitator (ESP),

C SODA
CULATING
PUMP
Figure 10-7. Schematic of Belco scrubbing system (courtesy of Belco Corporation).


32 Fluid Catalytic Cracking Handbook
pm. For units operating in partial combustion, the flue gas must e sent to a CO boiler. For units operating in complete combustion, he concentration of CO largely depends on the operating conditions f the regenerator (mainly temperature and excess oxygen), the CO romoter level, and the efficiency of the air/spent catalyst distriution system.
OX
NOX levels in the FCC flue gas typically range from 50-500 ppm. itrogen content of the feed, excess oxygen, regenerator residence me, dense phase temperature, and CO promoter all influence the oncentration of NOX.
In the regenerator, most of the NOX is formed as NO, with little 2O or NO2. About 90% of organic nitrogen in the spent catalyst is onverted to inorganic nitrogen, and a very small amount becomes NO. O can be lowered by reducing excess oxygen and CO promoter. The resent platinum-based promoter oxidizes intermediates such as HCN nd NH3 to NO and decreases the reducing agent such as CO.
To reduce nitrogen oxide, thermal and catalytic processes are availble. The thermal process is licensed by Exxon. NH3 or urea is injected nto the flue gas at an elevated temperature (-1600°F, 870°C); NOX reduced to nitrogen. This process is applicable to FCC units that ave CO boilers. NOX can also be reduced over a catalyst at 500°F
o 750°F (260°C to 400°C).
MERGING DEVELPMENTS IN CATALYSTS, ROCESSES, AND HARDWARE
The FCC process has a long history of innovation and will continue o play a key role in the overall success of the refining industry. The ontinuing developments will primarily be in the areas of catalyst, rocess, and hardware technologies.
atalyst
Since the mid-1960s, formulation of FCC catalysts has improved teadily. The focus of the research is in the following areas:






APPENDIX 2
Correction to Volumetric Average Boiling Point
WABP C 80) F V
==• ""^
WABP O 603F VABP
A8TM Diet, 10% - 90 %Slop*
339
APPENDIX 3
TOTAL Correlations
romatic Carbon Content:
CA = -814.136 + 635.192 x RI(20) - 129.266 x SG + 0.1013 x MW- 0.340 x S - 6.872 x ln(v)
ydrogen Content:
H2 = 52.825 - 14.26 x RI(20) - 21.329 x SG- 0.0024 x MW - 0.052 x S + 0.757 xln(v)
olecular Weight:
MW = 7.8312 x 10-3 x SG-0-0976 x AP°C1238
efractive Index @ 20°C:
RI(20) = 1 + 0.8447 x SG1-2056 x (VABPoc+273.16r)0557 x
efractive Index @ 60°C:
RK60) = 1 + 0.8156 x SG12392 x (VABP0(: + 273.16)-0.0576 x
ource: Dhulesia, H., "New Correlations Predict FCC Feed Characterization Paramers," Oil & Gas Journal, Jan. 13, 1986, pp. 51-54.
340
APPENDIX 4
n-d-M Correlations
v = 2.5 x (RI20OC - 1.4750) - (d2()OC - 0.8510)
05 |
= (d2()OC - 0.8510) - |
1.11 x (RI2fn, |
- 1.4750) |
If v is positive: %CA |
= 430 x v + |
3660 |
|
|
|||
If |
v is negative: %CA |
= 670 x v + |
|
|
|
|
M |
If 03 is positive: %CR = 8 2 0 x G J - 3 x S + 10,000/M
If 03 is negative: %CR = 1440 x 03 - 3S +10,600
M
%CN = %CR — %CA |
|
%C_ = 100— %CR |
|
r |
K |
verage Number of Aromatic Rings per Molecule (RA):
RA |
= 0.44 + 0.055 |
x M x v If v is positive |
|||
R^ |
= 0.44 + 0.080 |
x M x v If v is negative |
|||
verage Total Number of Rings per Molecule (RT): |
|||||
RT |
= 1.33 + 0.146 |
x M x (03- |
0.005 |
x S) |
If 03is positive |
RN |
= RT — RA |
|
|
|
|
RT |
= 1.33 + 0.180 x M x (03- |
0.005 |
x S) |
If 05is negative |
verage Number of Napthene Rings per Molecule (RN):
RM = RT—RA
urce: ASTM Standard D-3238-80. Copyright ASTM. Used with permission.
341
APPENDIX 5
Estimation
of Molecular Weight
of Petroleum Ofts
from Viscosity
Measurements
Tabulation of H Function
H
40 |
334 |
336 |
339 |
341 |
343 |
345 |
347 |
349 |
352 |
354 |
50 |
355 |
357 |
359 |
361 |
363 |
364 |
366 |
368 |
369 |
371 |
60 |
372 |
374 |
375 |
377 |
378 |
380 |
381 |
382 |
384 |
385 |
70 |
386 |
387 |
388 |
390 |
391 |
392 |
393 |
394 |
395 |
397 |
80 |
398 |
399 |
400 |
401 |
402 |
403 |
404 |
405 |
406 |
407 |
90 |
408 |
409 |
410 |
410 |
411 |
412 |
413 |
414 |
415 |
415 |
00 |
416 |
417 |
418 |
419 |
420 |
420 |
421 |
422 |
423 |
423 |
10 |
424 |
425 |
425 |
426 |
427 |
428 |
428 |
429 |
430 |
430 |
20 |
431 |
432 |
432 |
433 |
433 |
434 |
435 |
435 |
436 |
437 |
30 |
437 |
438 |
438 |
439 |
439 |
440 |
441 |
441 |
442 |
442 |
40 |
443 |
443 |
444 |
444 |
445 |
446 |
446 |
447 |
447 |
448 |
50 |
448 |
449 |
449 |
450 |
450 |
450 |
451 |
451 |
452 |
452 |
60 |
453 |
453 |
454 |
454 |
455 |
455 |
456 |
456 |
456 |
457 |
70 |
457 |
458 |
458 |
459 |
459 |
460 |
460 |
460 |
461 |
461 |
80 |
461 |
462 |
462 |
463 |
463 |
463 |
464 |
464 |
465 |
465 |
0 |
465 |
466 |
466 |
466 |
467 |
467 |
468 |
468 |
468 |
469 |
342

Molecular Weight of Petroleum Oils |
343 |
Viscosity-Molecular Weight Chart
LINES OF CONSTANT 210*F (98,89*C) VISCOSITY, cST
500
5400
300
too |
)0 j/ |
400 |
500 |
600 |
|
RELATIVE MOLECULAR MASS
ource: ASTM Standard D-2502-92. Copyright ASTM. Used with permission.
APPENDIX 6
Kinematic Viscosity
o Saybolt Universal
Viscosity
|
Equivalent Saybolt |
Universal |
inematic Viscosity, cSt |
Viscosity, Sus |
|
|
At 100°F |
At 210°F |
1.81 |
32.0 |
32.2 |
2.71 |
35.0 |
35.2 |
4.26 |
40.0 |
40.3 |
7.37 |
50.0 |
50.3 |
10.33 |
60.0 |
60.4 |
13.08 |
70.0 |
70.5 |
15.66 |
80.0 |
80.5 |
18.12 |
90.0 |
90.6 |
20.54 |
100.0 |
100.7 |
43.0 |
200.0 |
202.0 |
64.6 |
300.0 |
302.0 |
86.2 |
400.0 |
402.0 |
108.0 |
500.0 |
504.0 |
129.5 |
600.0 |
604.0 |
139.8 |
648.0 |
652.0 |
151.0 |
700.0 |
|
172.6 |
800.0 |
|
194.2 |
900.0 |
|
215.8 |
1000.0 |
|
xtracted from ASTM Method D-2161-87. Copyright ASTM. Used with permission.
344
APPENDIX 7
API Correlations
Xr = a + b x (R.) + c x (VG)
Xn = d + e x (R.) + f x (VG)
Xn = g + h x (R.) + i x (VG)
here constants vary with molecular weight range given below:
onstants |
Heavy Fractions 200 < MW < 600 |
|
a |
|
+2.5737 |
b |
|
+1.0133 |
c |
|
-3.573 |
d |
|
+2.464 |
e |
|
-3.6701 |
f |
|
+1.96312 |
g |
|
-4.0377 |
h |
|
+2.6568 |
j |
|
+1.60988 |
. |
= Refractivity Intercept |
|
GC = Viscosity Gravity Constant |
||
K |
K |
|
R, |
~-Ri(20) |
|
here:
(2()) = Refractive Index @ 20°C
= Density @ 20°C
ource: Riazi, M. R., and Daubert, T. E., "Prediction of the Composition of Petroleum actions," Ind. Eng. Chem. Process Dev., Vol. 19, No. 2, 1982, pp. 289-294.
345

46 Fluid Catalytic Cracking Handbook
VGC = SG ~ °-24 - °-022 x log(V210 ~ 35.5) 0.755
Where:
= Saybolt Universal Viscosity @ 210°F in seconds
efractive Index @ 20°C (68°F):
I = A x exp(B x MeABP + C x SG + D x MeABP x SG)
x MeABPE x SGF
onstants |
2.341 * 10~2 |
A |
|
B |
6.464 xIQ"4 |
C |
5.144 |
D |
-3.289 x 10-4 |
E |
-0.407 |
F |
-3.333 |
MW = a x exp(b x MeABP + c x SG + d x MeABP x SG)
x MeABP6 x SGf
here: |
|
onstants |
|
a |
20.486 |
b |
1.165 x10~4 |
c |
-7.787 |
d |
1.1582 x 10-3 |
e |
1.26807 |
f |
4.98308 |

APPENDIX 8
Definitions of
Fluidization Terms
eration. Any supplemental gas (air, steam, nitrogen, etc.) that increases fluidity of the catalyst.
ngle of Internal Friction—a. Angle of internal friction, or angle of shear, is the angle of solid against solid. It is the angle at which a catalyst will flow on itself in the nonfluidized state. For an FCC catalyst, this is about 80°.
ngle of Repose—p. The angle that the slope of a poured catalyst will make with the horizontal. For an FCC catalyst, this is typically 30°.
SoHdSurfaca
347

Definitions of Fluidization Terms |
349 |
keletal Density—SD. The actual density of the pure solid materials that make up the individual catalyst particles. For an FCC catalyst, the skeletal density can be calculated as follows:
SD =
3.42.1
Where: Al = Alumina content of the catalyst, wt%
Si = Silica content of the catalyst, wt%
ip Factor. The ratio of vapor velocity to catalyst velocity.
ick Slip Flow. The continuous sudden stoppage and resumption of catalyst flow in a standpipe. This is usually caused by underaeration.
uperficial Velocity. The velocity of the gas through the vessel or pipe without any solids present. It is a volumetric flow rate of fluidization gas divided by the cross-sectional area.
APPENDIX 9
Conversion of ASTM
50% Point to TBP
50% Point
Temperature
The following equation can be used to convert an ASTM D-86 50% mperature to a TBP 50% temperature.
TBP (50) = 0.87180 x ASTM D-86 (50)1.0258
here: |
|
|
BP(50) |
= true boiling point distillation temperature at 50 vol% |
|
|
distilled, |
°F |
STM D86(50) = observed |
ASTM D-86 distillation temperature at |
|
|
50 vol% distilled, °F |
xample:
iven ASTM D-86(50) = 547°F, determine TBP 50% temperature:
BP(50) = 0.87180 x (547)1.058
BP(50) = 561°F
ource: Daubert, T. E., "Petroleum Fraction Distillation Interconversions," Hydrocarbon ocessing, September 1994, pp. 75-78.
350
APPENDIX 10
Determination
of TBP Cut Points
from ASTMD-86
The difference between adjacent TBP cut points can be determined y the following equation:
Y.= A XB
!I
here:
. = difference in TBP distillation between two cut points, °F
i |
= observed difference in ASTM D-86 distillation between two cut |
|
points, °F |
||
|
,B = constants varying for cut points ranges, shown in the following table:
i |
Cut Point Range |
A |
B |
1 |
100%–90% |
0.11798 |
1 .6606 |
7 |
90%-70% |
3.0419 |
0.75497 |
3 |
70%–50% |
2.5282 |
0.820072 |
4 |
50%–30% |
3.0305 |
0.80076 |
5 |
30%– 10% |
4.9004 |
0.71644 |
6 |
10%–0% |
7.4012 |
0.60244 |
ource: Daubed, T. E., "Petroleum Fraction Distillation Interconversions," Hydrocarbon ocessing, September 1994, pp. 75-78.
351
2 Fluid Catalytic Cracking Handbook
BP (0) |
= TBP(50) - Y4 - Y5- Y6 |
BP (10) |
= TBP(50) - Y4 - Y~ |
BP (30) |
= TBP(50) - Y4 |
BP (70) |
= TBP(50) + Y3 |
BP (90) |
= TBP(50) + Y3 + Y2 |
BP (100) |
= TBP(50) + Y" + Y, + Y, |
APPENDIX 11
Nominal Pipe Sizes
|
|
|
Identification |
|
|
|
ominal |
|
Steel |
Stainless |
Wall |
Inside |
|
|
|
|
||||
Pipe |
Outside |
Iron |
|
Steel |
Thickness |
Diameter |
Size |
Diameter |
Pipe |
Sched. |
Sched. |
(t) |
(d) |
nches |
Inches |
Size |
No. |
No. |
Inches |
Inches |
1/4 |
0.540 |
STD |
40 |
40S |
.088 |
.364 |
|
|
xs |
80 |
80S |
.119 |
.302 |
3/8 |
0.675 |
STD |
40 |
40S |
.091 |
.493 |
|
|
XS |
80 |
SOS |
.126 |
.423 |
1/2 |
0.840 |
STD |
40 |
40S |
.109 |
.622 |
|
|
XS |
80 |
80S |
.147 |
.546 |
|
|
— |
160 |
.__ |
.187 |
.466 |
|
|
xxs |
— |
— |
.294 |
.252 |
3/4 |
1 .050 |
STD |
40 |
40S |
.113 |
.824 |
|
|
XS |
80 |
80S |
.154 |
.742 |
|
|
— |
160 |
— |
.219 |
.612 |
|
|
XXS |
— |
— |
.308 |
.434 |
1 |
1.315 |
STD |
40 |
40S |
.133 |
1.049 |
|
|
XS |
80 |
80S |
.179 |
.957 |
|
|
— |
160 |
— |
.250 |
.815 |
|
|
XXS |
— |
— |
.358 |
.599 |
1-1/4 |
1.660 |
STD |
40 |
40S |
.140 |
1.380 |
|
|
XS |
80 |
80S |
.191 |
1 .278 |
|
|
— |
160 |
_ |
.250 |
1 . 1 60 |
|
|
XXS |
— |
— |
.382 |
.896 |
1-1/2 |
1.900 |
STD |
40 |
40S |
.145 |
1.610 |
|
|
XS |
80 |
80S |
.200 |
1.500 |
|
|
— |
160 |
— |
.281 |
1.338 |
|
|
XXS |
— |
— |
.400 |
1.100 |
353

4 Fluid Catalytic Cracking Handbook
|
|
|
Identification |
|
ominal |
|
|
Siteei |
Stainless |
|
|
|
||
Pipe |
Outside |
Iron |
|
Steel |
Size |
Diameter |
Pipe |
Sched. |
Sched. |
nches |
Inches |
Size |
No. |
No. |
2 |
2.375 |
STD |
40 |
40S |
|
|
XS |
80 |
80S |
|
|
— |
160 |
— |
|
|
xxs |
— |
— |
2-1/2 |
2.875 |
STD |
40 |
40S |
|
|
XS |
80 |
80S |
|
|
— |
160 |
— |
|
|
XXS |
— |
— |
|
|
|
||
3 |
3.500 |
STD |
40 |
40S |
|
|
XS |
80 |
80S |
|
|
— |
160 |
— |
|
|
xxs |
— |
— |
3-1/2 |
4.000 |
STD |
40 |
40S |
|
|
XS |
80 |
80S |
4 |
4.5 |
STD |
40 |
40S |
|
|
XS |
80 |
80S |
|
|
— |
120 |
— |
|
|
— |
160 |
— |
|
|
xxs |
— |
— |
5 |
5.563 |
STD |
40 |
40S |
|
|
XS |
80 |
80S |
|
|
— |
120 |
— |
|
|
— |
160 |
— |
|
|
xxs |
— |
|
|
|
— |
||
6 |
6.625 |
STD |
40 |
40S |
|
|
XS |
80 |
80S |
|
|
— |
120 |
— |
|
|
— |
160 |
|
|
|
— |
||
|
|
XXS |
— |
|
|
|
— |
||
|
|
|
|
Wall inside Thickness Diameter
(t)(d)
Inches |
Inches |
.154 |
2.067 |
.218 |
1.939 |
.344 |
1.687 |
.436 |
1.503 |
.203 |
2.469 |
.276 |
2.323 |
.375 |
2.125 |
.552 |
1.771 |
.216 |
3.068 |
.300 |
2.900 |
.438 |
2.624 |
.600 |
2.300 |
.226 |
3.548 |
.318 |
3.364 |
.237 |
4.0.26 |
.337 |
3.826 |
.438 |
3.624 |
.531 |
3.438 |
.674 |
3.152 |
.258 |
5.047 |
.375 |
4.813 |
.500 |
4.563 |
.625 |
4.313 |
.750 |
4.063 |
.280 |
6.065 |
.432 |
5.761 |
.562 |
5.501 |
.719 |
5. 187 |
.864 |
4.897 |