
Цеха лекции
.pdf
станков образуются заделы, и движение деталей происходит с перерывами. Технологический процесс - дифференцирован или концентрирован. Станки – специальные или узкоспециализированные, как отдельно установленные, а также связанные в автоматическую линию. Режущий инструмент – специальный. Средства измерения – специальные. Себестоимость – низкая.
Форма организации работы – прямоточная (пульсирующий поток) и непрерывно-поточная.
Массовое производство достаточно выгодно при изготовлении большого количества изделий (деталей). Оптимальное количество деталей для массового производства выражается формулой:
n |
|
C |
3 |
|
|
|
|
||
|
|
|
|
|
C |
c |
C |
м |
|
|
|
|
; шт.
где n – оптимальное количество изделий.
С3 – величина затрат при переходе с серийного производства на массовое. Сс – себестоимость изделий при серийном производстве.
См – себестоимость изделий при массовом производстве.
Классификация цехов по характеру конструкции и весу изделий
I класс - изделия с черным весом до 100 кг.
металлорежущие станки для часовой промышленности и инструментального производства;
нормальный металлорежущий и измерительный инструмент;
подшипники качения;
спец. приборы;
II класс - изделия с черным весом до 2 т.
металлорежущие и деревообрабатывающие станки;
двигатели, дизели, компрессоры;
сельскохозяйственные машины, электродвигатели средней мощности. III класс - изделия с черным весом до 15 т (изделия тяжелого
машиностроения):
тяжелые металлорежущие и деревообрабатывающие станки;
кузнечные молоты, прессы;
водяные и паровые турбины;
дорожные машины;
IV класс - изделия особо тяжелого машиностроения (черный вес более 15
тонн).
Классификация по количеству металлорежущих станков
Класс цеха |
I |
II |
III |
IV |
|
|
|
|
|
Малый цех |
до 150 |
до 125 |
до 75 |
до 40 |
|
|
|
|
|
Средний цех |
150 - 300 |
125 - 250 |
75 - 125 |
40 - 75 |
|
|
|
|
|
Крупный цех |
свыше 300 |
свыше 250 |
свыше 125 |
свыше 75 |
|
|
|
|
|
Основные задачи при проектировании механосборочных цехов
При проектировании механосборочного цеха решаются три основные задачи: экономическая, техническая, организационная.
Вэкономическом разделе проекта решаются следующие вопросы:
1.Устанавливается экономическая программа с указанием номенклатуры и количества выпуска изделия (машин), массы, определяется себестоимость одного изделия и всей программы
2.Определяется источники снабжения сырьем, материалами, полуфабрикатами, топливом, газом, электроэнергией, водой и т.д.
3.Выбирается наивыгоднейшие географические точки расположения цеха.
4.Определяется необходимый размер основных и оборотных средств.
5.Определяется себестоимость продукции и эффективность затрат.
6.Решаются вопросы финансирования завода (цеха).
7.Составляется план развертывания производства.
8.Решаются вопросы кооперирования.
9.Определяется потребность в жилищном и социально-культурном строительстве.
Втехническом разделе проекта выполняются следующие работы:
1.Проектируется технологический процесс обработки сырья и полуфабрикатов
2.Определяется необходимое количество основного и вспомогательного оборудования
3.Определяется необходимое количество рабочих, их состав и общий фонд рабочего времени.
4.Определяется необходимое количество сырья, материалов и топлива.
5.Определяется потребное количество электроэнергии всех видов и способы обеспечения ею.
6.Решаются вопросы транспорта, освещения, отопления, вентиляции, водоснабжения, канализации и т.п.
7.Выполняются работы по планировке цеха, вспомогательных помещений.
8.Подсчитываются потребные площади.
9.Выбираются типы и формы зданий, разрабатываются их конструкции и вся строительная часть
10.Решатся вопросы техники безопасности, противопожарные мероприятия, вопросы санитарии и гигиены труда, решаются вопросы ГО.
Вчисло организационных задач входят:
1.Структура управления участками и цехами.
2.Распределение функций и установленные взаимосвязи между отделами и отдельными должностными лицами технического персонала.
3.Управление административной, технической и финансово-хозяйственной частью.
4.Разработка вопросов по организации труда.
5.Разработка рациональной организации рабочих мест.
6.Установление порядка прохождения заказов, документации, формы отчетности и контроля.
7.Разработка мероприятий по подготовке кадров, обслуживанию рабочих создание благоприятных условий труда.
Задание на проектирование
Взадании на проектирование указываются следующие данные:
a)Наименование проектируемого предприятия, здания или сооружения.
b)Основание для проектирования (Постановление Правительства, приказ министерства или ведомства и т.п.).
c)Район, пункт и площадка строительства.
d)Номенклатура продукции и мощность производства по основным ее видам (в натуральном и стоимостном выражении) на полное развитие и в первую очередь.
e)Намечаемый режим работы предприятия, его специализация, производственное и хозяйственное кооперирование.
f)Основные технологические процессы и оборудование, а также необходимость разработки автоматизированных систем управления производством.
g)Основные источники обеспечения предприятия как в период строительства, так и, особенно при его эксплуатации сырьем, водой,
теплом, газом, электроэнергией, а также условия по очистке и сбросу сточных вод.
h)Намечаемые сроки строительства (в соответствии с нормами продолжительности), порядок его осуществления и ввода мощностей по очередям, а также предложения по дальнейшему расширению всего предприятия, его зданий или сооружений.
i)Данные для проектирования объектов жилищного и культурно-бытового строительства.
j)Намечаемый размер капитальных вложений и основные техникоэкономические показатели, которые должны быть достигнуты при проектировании.
k)Требования к разработке вариантов технического проекта или его частей, а также стадийность проектирования.
l)Наименование генеральной проектной и строительной организации – Генерального подрядчика, а также намечаемая и возможная кооперация при осуществлении строительства объекта, размещаемого в составе промышленного узла.
Основные этапы разработки проекта механического цеха
Получив исходные данные на проектирование механосборочного цеха проектировщик производит:
1.Анализ конструкции детали на технологичность.
2.Уточняет тип производства.
3.Выбор способа получения заготовки и ее технико-экономическое обоснование (сравнение нескольких конкурирующих вариантов).
4.Определение размеров партии запуска деталей при единичном, мелкосерийном, крупносерийном производстве и такта выпуска при поточном производстве.
5.Проектирование технологического процесса.
5.1.Составление плана обработки. 5.2.Выбор типов оборудования 5.3.Подбор технологической оснастки.
5.4.Проектирование и расчет специальной технологической оснастки. 5.5.Экономическое обоснование правильности подбора оснастки. 5.6.Составление спецификации на оснастку (СТО).
5.7.Расчет припусков на обработку и операционных размеров. 5.8.Расчет режимов резания.
5.9.Техническое нормирование и определение квалификации работы. 5.10. Технико-экономическое сравнение сопоставимых вариантов
обработки (2-х…3-х).
5.11.Составление технологической документации.
6.Расчет годовой трудоемкости работ и по станкоемкости.
6.1.Принятым режимам обработки.
6.2.Фонду времени работы оборудования.
6.3.Бюджету времени работы одного рабочего.
7.Уточнение размеров партии запуска деталей в производство.
8.Расчет количества основного оборудования и определение коэффициента его загрузки. Составление сводной ведомости на основное оборудование.
9.Уточнение типа производства и выбора формы организации работы.
10.Расчет поточных и автоматических линий и определение их типа. 11.Расчет и выбор типов подъемного и транспортного оборудования. 12.Выбор типов и определение количества вспомогательного оборудования. 13.Определение состава и расчета рабочей силы цеха.
14.Расчет площадей основных и вспомогательных отделений, служебных и бытовых помещений.
15.Планировка оборудования и рабочих мест. Выбор типов зданий. 16.Разработка мероприятий по технике безопасности и ГО.
17.схема организации управления и технического руководства цехом.
18.Экономическая часть.
18.1.Расчет годовой потребности в основных и вспомогательных материалах и их стоимость.
18.2.Расчет среднего разряда рабочих, фонда заработной платы по основному и вспомогательному персоналу.
18.3.Составление сметы затрат на производство.
18.4.Определение себестоимости выпускаемой продукции.
18.5.Определение размеров капитальных вложений.
18.6.Определение основных и оборотных средств, оборачиваемости оборотных средств.
18.7.Определение технико-экономических показателей цеха.
18.8.Анализ проекта цеха и заключение по проекту.
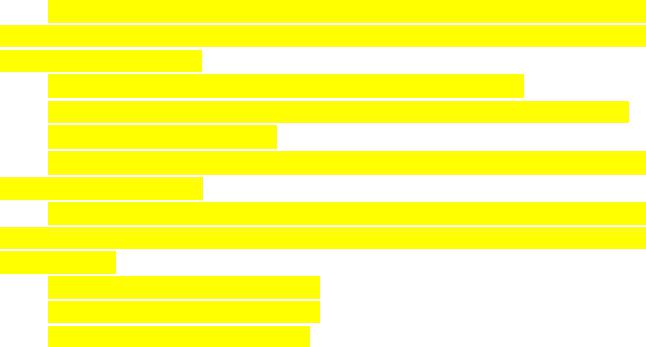
Основные принципы проектирования технологических процессов
В общем числе вопросов, подлежащих разрешению при проектировании механосборочных цехов, разработка технологического процесса является одним из сложных и важных вопросов. Проектируя технологический процесс необходимо установить наиболее рациональный и экономичный способ обработки. В связи с этим необходимо учитывать следующее:
1.Форма заготовки детали должна быть близкой по размерам готовой
детали.
2.Интенсификации технологии обработки за счет: применения высокопроизводительного оборудования, прогрессивного режущего инструмента, приспособлений (СТО) с быстродействующими зажимными механизмами, автоматизации загрузки и разгрузки деталей на станки, механизации, автоматизации процессов и т.д.
3.Применение отделочно-упрочняющей технологии.
4.Концентрации или дифференциации технологического процесса.
5.Применение поточного метода обработки и сборки изделий
6.Применение автоматизации производства.
7.Применение для обработки тяжелых деталей переносных станков.
Фонды рабочего времени
В процессе проектирования машиностроительных заводов различают календарный, номинальный и действительный фонды времени работы оборудования и рабочих.
Календарный годовой фонд времени: 20 365 = 7300 часов Номинальный годовой фонд времени работы (40 рабочий час в неделю):
Рабочих Фкр = 2070 часов
Оборудования: 1 сменная работа - 2070 час; 2-х сменная - 4140 часов; 3-х сменная - 6210 часов;
Действительный годовой фонд времени: состоит из номинального фонда времени за исключением неизбежных потерь (отпуска, болезни, декретные отпуска и т.д.)
15 дней отпуска Фдр = 1860 часов;
18 дней отпуска Фдр = 1840 часов;
24 дня отпуска Фдр = 1820 часов.

Действительный фонд рабочего времени оборудования, включая потери от простоя оборудования в планово-предупредительном ремонте (3 - 4 %) и составляет (4029 - 4015 часов) для обычного оборудования; и 3904 (6% потерь) - для уникального оборудования.
Производственная программа цеха
Основой для проектирования цеха является его производственная программа, составленная исходя из производственной программы завода. В зависимости от типа производства, характера выпускаемой продукции и стадии проектирования производственная программа может быть ТОЧНОЙ, ПРИВЕДЕННОЙ и УСЛОВНОЙ.
При проектировании цеха по ТОЧНОЙ программе номенклатура изготовляемых изделий точно установлена и обеспечена рабочими чертежами, спецификациями и техническими требованиями. Технологический процесс разрабатывается на каждую деталь. Точная программа характерна для цехов массового, серийного и крупносерийного производств, при проектировании которых требуется большая точность технологически расчетов. Исходные данные при проектировании цеха по точной программе сводятся в ведомость.
Образец ведомости точной (подетальной) производственной программы предприятия:
|
|
№ детали по чертежу |
Материал |
Количество |
|
|
|
|
|
|
|
деталей на |
|
|
|
|
|||
|
|
(наименов |
|
|
Вес всех деталей |
||||
№ п/п |
Наименование |
годовую |
|
|
|||||
ание и |
Вес 1 детали |
на год. |
|||||||
детали |
программу с |
||||||||
марка по |
|
|
программу |
||||||
|
учетом |
|
|
||||||
|
ГОСТ) |
|
|
|
|
||||
|
|
|
|
|
|
||||
|
|
|
запчастей) |
|
|
|
|
||
|
|
|
|
|
|
|
|
||
|
|
|
|
|
|
|
|
|
|
|
|
|
|
|
черный |
чистый |
черный |
чистый |
|
|
|
|
|
|
|
|
|
|
|
1. |
… |
|
|
|
|
|
|
|
|
2. |
|
|
|
|
|
|
|
|
|
3. |
|
|
|
|
|
|
|
|
|
|
|
|
|
|
|
|
|
|
Для единичного, мелкосерийного и серийного производства программа составляется в виде перечня изготовленных в цехе изделий или узлов с указанием их количества и массы. При этом подетальная ведомость составляется только для типового изделия. Все остальные изделия, входящие в программу, приводятся к типовым. В этом случае нет необходимости иметь полный перечень обрабатываемых деталей. Чертежи, как правило, имеются только на изделия-представители, по которым ведутся расчеты. Такая
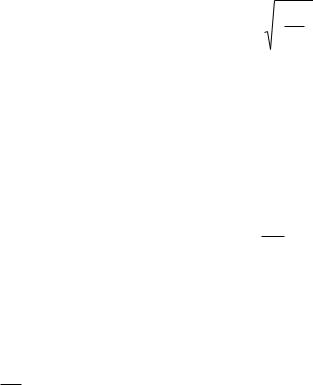
производственная программа называется ПРИВЕДЕННОЙ.
При проектировании цеха по ПРИВЕДЕННОЙ программе всю номенклатуру деталей цеха разбивают на группы по конструктивным, технологическим, геометрическим и весовым признакам. Приведенная программа определяется следующим образом:
вся номенклатура изделия разбивается на группы, в каждую из которых входят изделия, сходные по конструкции и технологии изготовления;
в каждой группе намечается типовое изделие представитель, по которому ведутся все расчеты;
все другие изделия группы приводятся по трудоемкости к изделию представителю с учетом их различия в массе, серийности программы и сложности механической обработки. Эти различия оцениваются коэффициентом приведения:
Коэффициент приведения определяется по формуле:
Кпр = Кв · Кс · Ксл,
где Кв – коэффициент приведения по массе изделия; Кс – коэффициент приведения по серийности; Ксл – коэффициент приведения по сложности.
Весовой коэффициент определяется по формуле:
где
Q |
x |
|
К |
в |
|
- масса приводимого изделия,
Q
|
Q |
|
2 |
|
3 |
|
|||
|
x |
|
|
|
|
|
Q |
|
|
|
|
|
|
- масса изделия представителя.
Эта формула применяется для определения соотношения времени на механическую обработку двух сравнимых геометрически подобных деталей.
Коэффициент приведения по серийности Кс определяется в зависимости от соотношения годовых программ в штуках приводимого изделия – представителя.
К |
|
|
N |
с |
|
|
|
|
|
|
|
|
|
|
N x |
0,15... |
0,2 |
где N – годовой выпуск изделия – представителя, Nx – годовой выпуск приводимого изделия: 0,15 – показатель для среднего и малого машиностроения, 0,20 – для тяжелого.
В практике проектирования обычно пользуются следующими коэффициентами:
N = 0,5; 1; 2; 3; 4; 5; 6; 7; 10; 15; 20
N x
Кс = 0,97; 1; 1,12; 1,17; 1,22; 1,25; 1,31; 1,45; 1,5
Коэффициент,
К |
с |
|
учитывающий различие в сложности изделий (деталей),
входящих в данную группу определяется проектантом и обычно принимается равным 1, так как при разбивке изделий на группы в каждую группу включаются изделия (детали) подобные по конструктивным и технологическим признакам. Приведенная программа применяется для проектирования цехов единичного, серийного и крупносерийного производства.
|
|
|
|
|
|
|
|
|
|
|
Приведен |
изделия |
|
Заданная программа |
Приведенная программа |
ное |
|||||||
|
количеств |
||||||||||
|
|
|
|
|
|
|
|
|
|
||
|
|
|
|
|
|
|
|
|
|
о изделий |
|
|
|
|
|
|
|
|
|
|
|
на |
|
|
|
|
|
|
|
|
|
|
|
||
Наименование |
Годовое кол-во шт., ком-тов |
Масса в т |
|
|
Коэффициент |
|
годовую |
||||
Наимено |
|
|
приведения |
|
программ |
||||||
|
|
|
|
|
|||||||
|
|
|
|
|
у |
||||||
|
|
вание |
|
|
|
|
|
|
|||
|
|
|
|
|
|
|
|
|
|||
|
годовой |
базового |
по |
|
по |
по |
|
|
|
||
|
изделия |
|
сери |
слож |
|
общ |
|
||||
одного изделия |
программ |
масс |
|
|
|
||||||
|
|
йнос |
ност |
|
ий |
|
|||||
|
ы |
|
е |
|
|
|
|||||
|
|
|
ти |
и |
|
|
|
||||
|
|
|
|
|
|
|
|
|
|
||
|
|
|
|
|
|
|
|
|
|
|
|
Изд. А |
400 |
0,8 |
320 |
|
1,0 |
|
1,0 |
1,0 |
|
1,0 |
400 |
Изд. Б |
200 |
0,8 |
160 |
Изд. А |
1,0 |
|
1,12 |
1,3 |
|
1,46 |
292 |
Изд. В |
100 |
0,4 |
40 |
|
0,63 |
|
1,22 |
1,5 |
|
1,16 |
116 |
|
|
|
|
|
|
|
|
|
|
|
|
Всего: |
700 |
- |
520 |
|
|
Всего: |
|
|
|
808 |
|
|
|
|
|
|
|
|
|
|
|
|
|
При проектировании цехов для обработки деталей изделий, конструкции которых еще не разработаны, и точная номенклатура изготовляемых цехом изделий неизвестна (экспериментальные цехи), выбираются условные представители, по которым можно с достаточным приближением получить необходимые исходные данные. По принятым условным представителям и ведется проектирование. В этом случае программа является УСЛОВНОЙ.
По УСЛОВНОЙ программе так же вся номенклатура изделий разбивается на группы. На представителя группы составляется весь расчет, и результат расчета распространяется на все детали (машины) данной группы без применения коэффициента приведения.
Основные формы организации работ в цехе
Каждому из видов производств (единичному, серийному и массовому) свойственны соответствующие формы организации работы и способы расположения оборудования, которые определяются характером изделия и производственного процесса, объемом выпуска и рядом других факторов.
Существуют следующие основные формы организации работы:
1.По видам оборудования – форма, свойственная, главным образом единичному производству; для отдельных деталей применяется в серийном производстве. Станки располагаются по признаку однородности обработки, т.е. создаются участки станков одного вида обработки - токарных, строгальных, фрезерных и др.
2.Предметная – форма, свойственная, главным образом серийному производству; для отдельных деталей применяется в массовом производстве. Станки располагаются в последовательности технологических операций для одной или нескольких деталей, требующих одинакового порядка обработки. В этой же последовательности образуется и движение деталей. Обработка деталей на станках производится партиями; при этом время выполнения операции на отдельных станках может быть не согласовано с временем операции на других станках. Изготовленные детали во время работы хранятся у станков и затем транспортируются целой партией. Здесь же может производиться и контроль деталей.
3.Поточно-серийная или переменно-поточная – форма, свойственная
серийному производству. Станки располагаются также в последовательности технологических операций для деталей, обрабатываемых на данной станочной линии. Производство идет партиями, причем детали каждой партии могут несколько отличаться одна от другой размерами или конструкцией, допускающими, однако обработку их на одном и том же оборудовании. Производственный процесс ведется таким образом, что время выполнения операции на одном станке согласовано с временем работы на следующем станке; детали данной партии перемещаются со станка на станок в последовательности технологических операций, создавая непрерывность движения деталей по станкам. Переналадка станков, приспособлений и инструментов при переходе на обработку сходных деталей других партий обеспечивается предварительной подготовкой. Норма времени на каждую операцию должна быть примерно одинакова.
4.Прямоточная – форма свойственная массовому (и в некоторой мере, крупносерийному) производству; станки располагаются в последовательности технологических операций, закрепленных за определенными станками; детали со станка на станок передаются поштучно. Но синхронизация времени операций выдерживается не на всех участках линии, т.е. время выполнения отдельных операций не всегда равно (или кратно) такту; вследствие этого около станков, у которых время выполнения операции больше такта, создаются заделы