
цилиндрический редуктор
.pdf
3ТЕХНИЧЕСКИЙ ПРОЕКТ
3.1Конструктивная компоновка привода
Цель конструктивной компоновки – конструктивное оформление деталей и узлов редуктора открытой передачи и рамы.
Конструктивная компоновка редуктора выполняется на миллиметровой бумаге формата А1 карандашом в контурных линиях желательно в масштабе 1:1. Шестерню чаще всего выполняют заодно с валом (вал-шестерня).
Конструктивные размеры колеса приведены ниже. Колеса небольших размеров изготовляют обычно из штампованных заготовок без углублений и отверстий.
Конструктивные размеры корпуса приведены ниже. При конструировании корпуса редуктора придерживаются установленных литейных уклонов, размеров элементов сопряжений, фланцев. Для заливки масла и осмотра в крышке корпуса делают окно, закрываемое крышкой.
В основании корпуса делают отверстия под выбранный маслоуказатель и сливную пробку.
Подшипники закрываются чугунными глухими и сквозными привертными крышками. В сквозных крышках делаются отверстия под манжетные уплотнения и для прохода выходного конца вала dв 1...2 мм .
Для регулирования зазоров в подшипниках под фланец крышек устанавливается набор стальных прокладок (толщиной ~1 мм).
Между торцами подшипников и упорными буртиками валов (распорной втулкой) устанавливаются мазеудерживающие кольца. Зазор между кольцом и корпусом редуктора 0,1...0,3 мм ; выход на торец корпуса 1…2 мм.
Длина выходных концов валов определяется длиной полумуфты (длиной ступицы открытой передачи). Конструктивно выполняют валы в местах установки ступиц подшипников, распорных колец – выбираются фаски, радиусы закруглений (галтели), канавки для выхода шлифовального круга и резьбонарезного оборудования. Звездочка на тихоходном валу фиксируется концевой шайбой.
Для обеспечения точного относительного положения электродвигатель и редуктор располагаем на раме, которую изготавливаем из стального проката – швеллеров, уголков, листов. Для определения конфигурации и размеров рамы вычерчиваем на листе бумаги в масштабе контуры муфты. Одну полумуфту соединяем с валом электродвигателя, а другую – с валом редуктора. Подрисовываем контуры редуктора и электродвигателя. После этого вычерчиваем контуры рамы и определяем ее длину L и ширину B и разность высот h опорных поверхностей электродвигателя и редуктора. Размеры L и B округляем до стандартных значений. Определяем высоту основного
швеллера H 0,1L , по которой подбираем ближайший больший размер швеллера. Ширину полки швеллера проверяем на возможность размещения и монтажа крепежных деталей.
При небольшом размере h на раму наваривают листы требуемой толщины или опорные платики (высота платика 5…6 мм). При большом значении h раму наращивают швеллерами. Для крепления рамы применяем фундаментные болты (при длине рамы до 700 мм устанавливают 4 фундаментных болта диаметром d p 16...18 мм; при свыше 700…1000 мм – 6 болтов диаметром
21

d p |
20...22 мм; при L свыше 1000 до 1500 мм – 8 болтов диаметром |
d p |
24 мм ) На внутренней поверхности полок швеллеров по месту установки |
болтов привариваем косые шайбы для обеспечения торцов головок болтов и гаек относительно осей болтов.
В приводе с ременной передачей для регулирования натяжения ремней, электродвигатель устанавливают на салазках, которые крепят на раме болтами.
22

Конструктивные размеры корпуса редуктора.
1. Толщина стенки корпуса и крышки редуктора:
|
0, 025 aWт |
3 |
0, 025 180 |
3 |
7.5 мм; |
|
|||||||
Т.к. |
|
8 , то примем |
|
|
8 мм. |
|
|
||||||
|
0, 02 aWт |
3 |
0, 02 180 |
3 |
6.6 мм; |
|
|||||||
Т.к. |
1 |
8 |
, то примем |
1 |
8 мм. |
|
|||||||
|
|
|
|
|
|
|
|
|
|
|
|
||
2. |
Толщина верхнего пояса (фланца) корпуса: |
|
|||||||||||
b |
1.5 |
|
1.5 |
|
8 |
12 мм; |
|
|
|
||||
3. |
Толщина нижнего пояса (фланца) корпуса: |
|
|||||||||||
b1 |
|
1.5 1 |
1.5 |
8 |
12 мм; |
|
|
|
|||||
3.Толщина нижнего пояса корпуса без бобышки: |
|||||||||||||
p |
|
2,35 8 |
18 мм. |
|
|
|
|
|
|
||||
5. Толщина ребер основания корпуса: |
|
||||||||||||
m |
|
0,85 |
1 |
|
0,85 |
|
1 |
8 |
8 мм. |
|
|||
6. Толщина ребер крышки: |
|
|
|
||||||||||
m1 |
|
0,85 |
1 |
1 |
|
0,85 |
|
1 |
8 |
8 мм. |
|
||
4. Диаметр фундаментных болтов (их число |
4 ): |
||||||||||||
d1 |
|
(0, 03 |
0, 036) |
аWт |
12 |
(0, 03 |
0, 036) 180 12 |
18 мм |
|||||
5. Диаметр болтов: |
|
|
|
|
|
|
|||||||
d2 |
|
(0, 7 |
0, 75) |
d1 |
(0, 7 |
0, 75) 18 14 - у подшипников; |
|||||||
d3 |
|
(0,5 |
0, 6) |
d1 |
(0,5 |
|
0, 6) 18 |
10 - соединяющих основание корпуса с |
|||||
крышкой. |
|
|
|
|
|
|
|
|
|
|
|||
9. Размеры, определяющие положение болтов d2 : |
|||||||||||||
e |
|
1 1, 2 |
d2 |
|
1 |
1, 2 |
|
14 |
14 16.8 15 мм. |
|
|||
q |
0.5d2 |
d4 |
|
0.5 14 |
|
12 |
19мм. |
|
|||||
Принимаем q |
20мм. |
|
|
|
|
|
10. Высоту бобышки под болт выбирают конструктивно так, чтобы образовалась опорная поверхность под головку болта и гайку. Желательно у всех бобышек иметь одинаковую высоту hб 60 мм.
11. Диаметр отверстия гнезда под подшипник:
DП |
по наружному диаметру подшипника. |
||||
DП1 |
80 мм, DП 2 |
110 мм. |
|||
l |
С2 |
Rб |
3...5 |
8 |
18 13 3 42 мм-длина гнезда подшипника. |
12. Диаметр штифта: |
|
||||
dш |
d3 |
10мм. |
|
|
|
13. Длина штифта: |
|
|
|||
lш |
b1 b |
5 |
12 12 |
5 |
29 мм. |
14. Наименьший зазор между наружной поверхностью колеса и стенкой корпуса:
A A1 1 1, 2 |
1 1, 2 8 8 мм. |
23

|
|
|
|
|
|
Конструктивные размеры колес. |
|||
Колесо на тихоходном валу: |
|||||||||
1. |
Диаметр вершин зубьев: |
||||||||
da |
316.8 мм - штампованная заготовка; |
||||||||
2. |
Диаметр ступицы стальных колес: |
||||||||
dст |
1, 6 dе |
1, 6 65 |
104 мм; |
|
|||||
3. |
Длина ступицы: |
|
|
|
|||||
lст |
(1...1,5) |
dв |
(1...1,5) 65 |
|
(65...98) мм; |
||||
Приму длину ступицы равной: |
|||||||||
lст |
b2 |
75 мм; |
|
|
|
|
|||
4. |
Толщина обода: |
|
|
|
|||||
0 |
(2,5...4) m |
(2,5...4) 2.5 |
|
8 мм; |
|||||
5. |
Толщина диска: |
|
|
|
|||||
С |
(0, 2...0,3)b |
(0, 2...0,3) |
55 |
14 мм; |
|||||
6. |
Диаметр центровой окружности: |
||||||||
Dотв 0,5(D0 |
dст ) |
0,5 (290 |
104) 200 мм; |
||||||
7. |
Диаметр отверстий: |
|
|
|
|||||
dотв |
D0 |
dст |
|
|
290 104 |
|
46 мм |
||
4 |
|
|
|
4 |
|
|
|||
|
|
|
|
|
|
|
|
||
D0 |
d f |
2 |
0 |
305.6 2 8 |
290 мм; |
||||
8. |
Фаска: |
|
|
|
|
|
|
|
|
n |
0.5 m 0,5 2.5 |
1.25 ; |
|
|
|
||||
Округляем до стандартного значения n 2 . |
|||||||||
9. |
Радиусы закруглений и уклонов: |
||||||||
R |
6 мм; |
|
7 . |
|
|
|
24
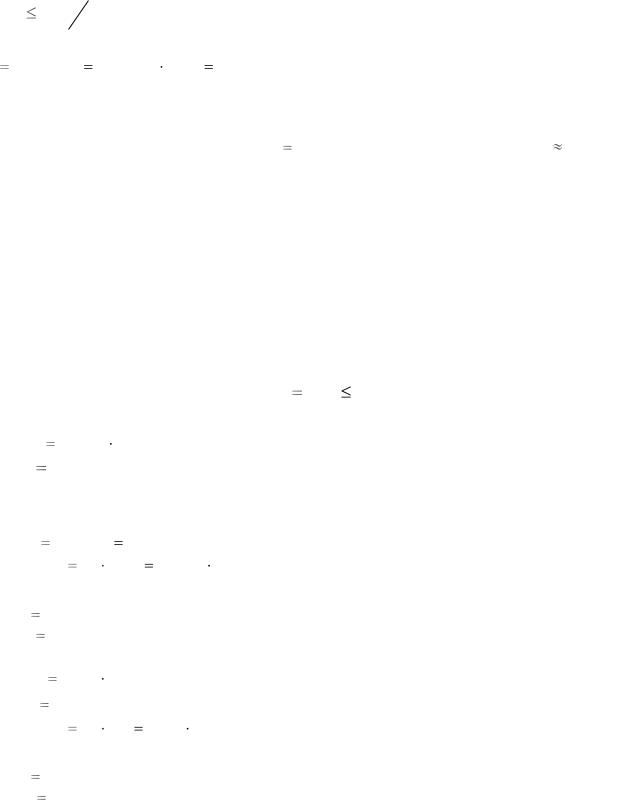
3.2Смазывание. Смазочные устройства
Вцилиндрическом косозубом редукторе применяется картерное смазывание
т. к. V 12 м |
с |
(окунанием колеса, в масло, залитое внутрь корпуса). Зубчатое |
|
|
|
колесо погружается в масло на высоту зуба |
||
(hм m...0, 25d2 |
|
2.5...0, 25 311.8 14 мм), где m - модуль зацепления; |
d2 - диаметр делительной окружности колеса;
Объем масляной ванны редуктора определяется из расчета 0,5...0,8 л масла на
1 кВт передаваемой мощности. Т. к. Pтр 9.26кВт , то V=4,63…7,4 л. При v 1,9 м/c
рекомендуемая вязкость масла должна быть примерно равна 34 cСт. По табл.
10.10[1] принимаем масло индустриальное И-40А (по ГОСТ 20799-75).
Подшипники смазывают разбрызгиванием масла колесом.
3.3 Выбор муфты
В приводах общего назначения рекомендуется применять муфту упругую втулочно-пальцевую (УВП). Типоразмер муфты определяем по диаметру концов, соединяемых валов и расчетному вращающему моменту:
M рас. kM1 M ;
Быстроходный вал:
М1 118.6Н м - расчетный момент на валу редуктора;
k 1,2 – коэффициент, учитывающий влияние эксплуатации при постоянной нагрузке.
M - допускаемый момент вращения муфты.
dэ 48мм, d1 36мм -диаметры концов, соединяемых валов.
М расч.1 1, 2 118.6 142.3Н м;
Муфта УВП 500-48-1.1-36-1.1 ГОСТ 20742-81 l 70мм - длина полумуфты;
L 185мм - длина муфты.
Тихоходный вал:
М 2 719Н м ;
d1 55мм - диаметр выходного вала.
М расч.1 1, 2 719 863Н м;
Муфта УВП 1000-55-1.1-55-1.1 ГОСТ 21424-75 l 90мм - длина полумуфты;
L 190мм - длина муфты.
25
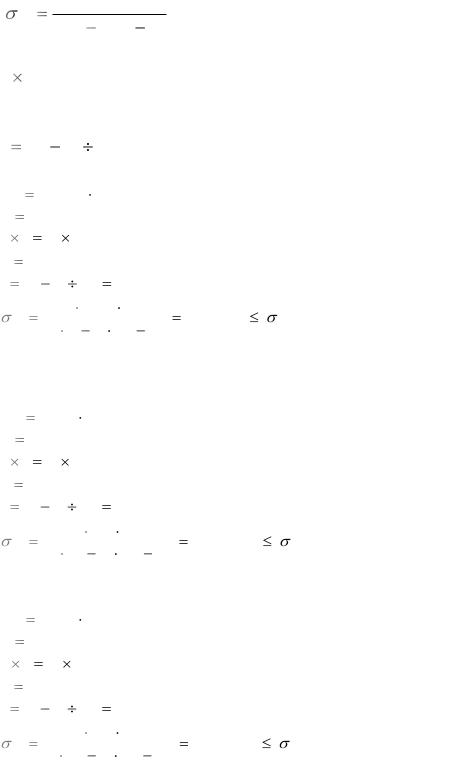
3.4 Расчет шпоночных соединений
Для шпоночных соединений быстроходного вала с полумуфтой или шкивом и тихоходного вала с зубчатым колесом или полумуфтой принимаем призматические шпонки со скругленными концами. Размеры поперечных сечений шпонок и пазов выбираем по ГОСТу 23360-78.
Проверяем прочность шпонок на смятие по формуле:
2M
см. d h t1 l b , где
d - диаметр вала в месте расположения шпонки; b h - сечение шпонки;
l - длина шпонки; t1 - глубина паза;
l lст. 5 10
Быстроходный вал:
М1 118.6Н м; d 36мм;
b h 10 8;
t1 5мм;
l 70 (5 10) 63мм.
|
|
2 118.6 103 |
|
41.4МПа |
см . |
||
см. |
36 |
(8 |
5) |
(63 |
10) |
||
|
|
|
Тихоходный вал:
Колесо:
М2 |
|
719Н м; |
|
|
|
|
|||
d |
65мм; |
|
|
|
|
|
|
||
b |
h |
18 |
11; |
|
|
|
|
|
|
t1 |
7мм; |
|
|
|
|
|
|
||
l |
75 |
(5 |
10) |
70мм. |
|
||||
|
|
|
|
2 719 103 |
|
106.4МПа |
см . |
||
см. |
65 (11 |
7) |
(70 |
18) |
|||||
|
|
|
|
На выходе:
М2 |
|
719Н м; |
|
|
|
|
||||
d |
55мм; |
|
|
|
|
|
|
|||
b |
h |
16 |
|
10; |
|
|
|
|
|
|
t1 |
6мм; |
|
|
|
|
|
|
|
||
l |
90 |
(5 |
10) |
|
80мм. |
|
||||
|
|
|
|
|
2 719 103 |
|
102.1МПа |
см . |
||
см. |
55 |
(10 |
6) |
(80 |
16) |
|||||
|
|
|
|
26

3.5Уточненный расчет валов
Цель уточненного расчета валов – определение коэффициентов запаса прочности в опасных сечениях каждого вала и сравнение их с допускаемым значением S 1.3...3.
Материал сталь 40Х, термическая обработка-улучшение.
ув =900 МПа - предел прочности;
1.Предел выносливости при симметричном цикле изгиба для углеродистых сталей:
10,43 в ;
2.Предел выносливости при симметричном цикле касательных
напряжений кручения:
10,58 1;
3.Коэффициент запаса прочности по касательным напряжениям:
s |
|
|
|
|
|
1 |
|
; |
|
|
|||
|
k |
|
|
|
|
|
|
||||||
|
|
|
|
|
|
|
|
|
|
||||
|
|
|
|
|
|
|
|
a |
m |
|
|
||
|
|
|
|
|
|
|
|
|
|
||||
|
|
|
|
П |
|
|
|
|
|
|
|
||
4. Амплитуда и среднее напряжение цикла: |
|
|
|||||||||||
|
|
|
|
max |
|
|
|
M |
; |
|
|||
|
|
|
|
|
|
|
|
|
|
||||
a m |
2 |
|
|
|
2Wk нетто |
|
|||||||
|
|
|
|
|
|||||||||
|
|
|
|
|
|
|
|
||||||
5. Момент сопротивления кручению сечения вала мм : |
|||||||||||||
Wk нетто |
|
|
dв31 |
|
bt1 |
dв1 t1 |
2 |
; |
|||||
|
16 |
|
|
|
|
|
2dв1 |
|
|||||
|
|
|
|
|
|
|
|
|
|
6. kф - эффективный коэффицент концентрации напряжений; еф-масштабный фактор;
еП - коэффициент влияния шероховатости поверхности еП =0,98...0,9 ; шф - коэффициент чувствительности материала к асиметрии цикла
для стали шф=0,05 ; 7.Коэффициент запаса прочности по нормальным напряжениям изгиба:
s |
|
1 |
; |
k |
|
||
|
|
|
a m
П
8. Амплитуда цикла нормальных напряжений:
|
M A A |
; |
|
a |
Wнетто |
||
|
|||
|
|
9. Момент сопротивления изгибу:
|
|
рd3 |
bt |
1 |
d |
в1 |
-t |
1 |
2 |
|
|
W |
= |
в1 |
- |
|
|
|
|
; |
|||
|
|
|
|
|
|
|
|
||||
k нетто |
|
32 |
|
|
|
2dв1 |
|
|
|
||
|
|
|
|
|
|
|
|
10. Среднее напряжение цикла нормальных напряжений:
|
Fa1 |
; |
|
m |
dв1 |
||
|
|||
|
|
27

1.k - эффективный коэффициент концентрации нагрузки.
-масштабный фактор;
-коэффициент чувствительности материала к асимметрии цикла ( 0,1для углеродистой стали);
12. Общий коэффициент запаса прочности:
s |
s |
s |
|
|
s . |
|
|
|
|
|
|
||
|
|
|
|
|
||
|
|
|
|
|||
|
|
s2 |
|
s2 |
13. Суммарный изгибающий момент в сечении А-А:
M |
A A |
M 2 |
M 2 |
|
A Ay |
A Ax |
Тихоходный вал:
1
1
0,43 900 387 МПа ;
0,58 387 224,46 МПа;
1. Проведем расчету по сечению А-А, где
dd1 |
d3 |
65мм; |
|
|
|
|
|
|
|
|
|
|
|
|
|
|
|
|
|
||||||||||
b |
18мм; |
|
|
|
|
|
|
|
|
|
|
|
|
|
|
|
|
|
|
|
|
|
|
||||||
t1 |
7 мм |
|
|
|
|
|
|
|
|
|
|
|
|
|
|
|
|
|
|
|
|
|
|
|
|||||
W |
|
|
|
|
|
|
|
|
|
3,14 653 |
|
18 7 |
(65 |
7)2 |
50.6 103 мм3; |
|
|||||||||||||
|
|
|
|
|
|
|
|
|
|
|
|
|
|
|
|
|
|
|
|
|
|
|
|
|
|
|
|||
kнетто(круч) |
|
|
16 |
|
|
|
|
|
|
|
2 65 |
|
|
|
|||||||||||||||
|
|
|
|
|
|
|
|
|
|
|
|
|
|
|
|
|
|
|
|
||||||||||
2. |
|
|
|
|
|
|
|
719 103 |
|
|
7.1МПа; |
|
|
|
|||||||||||||||
a |
|
|
Т |
|
|
|
|
|
|
|
|
3 |
|
|
|
|
|||||||||||||
|
|
|
|
|
|
|
|
2 50.6 10 |
|
|
|
|
|
|
|
|
|
|
|
|
|
||||||||
|
|
|
|
|
|
|
|
k |
=1,9; |
|
|
|
|
|
|
|
|
|
|
|
П |
=0,97; |
|||||||
|
|
|
|
|
|
|
|
|
|
|
|
|
|
|
|
|
|
|
|
|
|
|
|
|
|
|
|
|
|
|
|
|
|
|
|
|
|
|
|
0,05; |
|
|
|
|
|
|
|
|
|
|
|
0,59; |
|||||||
3. |
S |
|
|
|
|
|
|
|
|
224, 46 |
|
|
|
|
|
|
|
9.2; |
|
|
|
||||||||
|
|
|
|
|
|
|
|
|
|
|
|
|
|
|
|
|
|
|
|
|
|
|
|
|
|
|
|||
|
|
|
|
|
|
1, 9 |
|
|
|
|
7.1 |
0,1 7.1 |
|
|
|
|
|||||||||||||
|
|
|
|
|
|
|
|
|
|
|
|
|
|
|
|
|
|||||||||||||
|
|
|
|
|
|
|
|
|
|
|
|
|
|
|
|
|
|
||||||||||||
|
|
0, 59 |
|
0, 97 |
|
|
|
|
|
||||||||||||||||||||
|
|
|
|
|
|
|
|
|
|
|
|
|
|
|
|
|
|
|
|||||||||||
4. |
М А А |
|
147.62 |
115.32 |
|
|
187кН м; |
|
|||||||||||||||||||||
5. |
W |
|
|
|
3,14 653 |
|
|
18 7 |
(65 |
7)2 |
23.7 103 мм3; |
|
|||||||||||||||||
|
|
|
|
|
|
|
|
|
|
|
|
|
|
|
|
|
|
|
|
|
|
||||||||
|
|
kнетто(изгиб ) |
|
|
32 |
|
|
|
|
|
2 65 |
|
|
|
|||||||||||||||
|
|
|
|
|
|
|
|
|
|
|
|
|
|
|
|
|
|
|
|
|
|
|
|||||||
6. |
|
187 103 |
|
|
|
|
7.9МПа; |
|
|
|
|
|
|
|
|
||||||||||||||
а |
|
|
|
|
|
|
|
|
3 |
|
|
|
|
|
|
|
|
|
|
|
|
||||||||
|
|
23.7 10 |
|
|
|
|
|
|
|
|
|
|
|
|
|
|
|
|
|
|
|
||||||||
|
|
|
|
|
|
|
|
k |
=1,9; |
|
|
|
|
|
|
|
|
|
|
|
П =0,95; |
||||||||
|
|
|
|
|
|
|
|
|
|
|
|
|
0,1; |
|
|
|
|
|
|
|
|
|
|
|
|
0,7; |
|||
7. |
S |
|
|
|
|
|
|
|
|
|
|
|
387 |
|
|
|
|
|
|
|
|
|
17.2; |
|
|
||||
|
|
|
|
|
|
|
|
|
|
|
|
|
|
|
|
|
|
|
|
|
|
|
|
|
|
||||
|
|
|
|
|
1.9 |
|
|
7.9 |
|
0.05 |
7.9 |
|
|
|
|||||||||||||||
|
|
|
|
|
|
|
|
|
|
|
|
|
|
|
|||||||||||||||
|
|
|
|
|
|
|
|
|
|
|
|
|
|||||||||||||||||
|
|
0.7 |
0.97 |
|
|
|
|
|
|||||||||||||||||||||
8. |
S |
|
|
|
|
|
9.2 17.2 |
|
|
|
|
13.2 |
|
|
S . |
|
|
|
|
||||||||||
|
|
|
|
|
|
|
|
|
|
|
|
|
|
|
|
|
|
|
|
|
|
||||||||
|
|
|
|
|
|
|
|
|
|
|
|
|
|
|
|
|
|
|
|
|
|
||||||||
|
|
|
|
|
9.22 |
|
17.22 |
|
|
|
|
|
|
|
|
||||||||||||||
|
|
|
|
|
|
|
|
|
|
|
|
|
|
|
|
|
|
|
|
|
|
28

1. Проведем расчету по сечению Б-Б, где
dd1 d3 55мм; b 16мм;
t1 6мм
2. |
W |
|
|
|
3,14 553 |
|
16 6 (55 |
6)2 |
30.6 103 мм3; |
|||||
|
|
|
|
|
|
|
|
|
|
|
|
|||
|
kнетто(круч) |
|
|
16 |
|
|
2 55 |
|
|
|||||
|
|
|
|
|
|
|
|
|
|
|
||||
3. |
|
|
|
|
719 103 |
|
|
11.7МПа; |
|
|
||||
a Т |
|
|
|
|
3 |
|
|
|
|
|||||
|
|
|
2 30.6 10 |
|
|
|
|
|
|
|
||||
|
|
|
|
|
|
k |
=1,9; |
|
|
|
|
|
||
|
|
|
|
|
|
|
0,05; |
|
|
|
|
|||
4. |
S |
|
|
|
|
|
224, 46 |
|
|
|
5.7 S . |
|||
|
|
|
|
|
|
|
|
|
|
|
||||
|
1, 9 |
|
11.7 |
|
0, 05 11.7 |
|
||||||||
|
|
|
|
|
|
|
|
|||||||
|
|
|
|
|
|
|
|
|||||||
|
|
0, 59 |
0, 97 |
|
|
|
П =0,97; 0,59;
В сечении Б-Б вал испытывает только касательные напряжения кручения, поэтому
S 0 S S 5.7 S .
29

3.6Сборка редуктора
Перед сборкой внутреннюю полость редуктора тщательно очищают и покрывают маслостойкой краской.
Сборку производят в соответствии со сборочным чертежом редуктора, начиная с узлов валов.
На быстроходный вал устанавливают радиальные шарикоподшипники легкой серии, предварительно нагретые в масле до 80...100 С .
В тихоходный вал закладывают шпонку и напрессовывают зубчатое колесо. Затем ставят распорную втулку и устанавливают радиальные шарикоподшипники легкой серии, предварительно нагретые в масле до
80...100 С .
Собранные валы укладывают в основание корпуса редуктора и надевают крышку корпуса. Стыковые поверхности крышки и основания корпуса должны быть покрыты спиртовым лаком. Крышку центрируют с помощью двух конических штифтов и затягивают болты, крепящие крышку к корпусу.
Перед постановкой сквозных крышек в проточки закладывают манжеты, пропитанные горячим маслом. Проверяют проворачиванием валов отсутствие заклинивания подшипников (валы должны проворачиваться от руки) и закрепляют крышки винтами.
Далее на конец ведомого вала в шпоночную канавку закладывают шпонку и устанавливают муфту. Затем ввертывают пробку маслоспускного отверстия с прокладкой и жезловый маслоуказатель.
Заливают в корпус масло и закрывают смотровое отверстие с прокладкой из технического картона; закрепляют крышку болтами.
Собранный редуктор обкатывают и подвергают испытанию на стенде по программе, устанавливаемой техническими условиями.
30