
ПиОФ
.pdf
а) б) в) Рис. 1.4. Классификация резцов по типу станков:
а − токарные, б − строгальные, в − долбежные
Рис. 1.5. Классификация резцов по направлению движения подачи
5)по виду обработки − проходные, проходные упорные, подрезные, отрезные, расточные (для глухих и сквозных отверстий), резьбовые и др.;
6)по характеру обработки − обдирочные (черновые), чистовые и резцы для тонкого точения;
7)по способу изготовления − цельные, составные, сборные (рис. 1.7).
11

а) |
б) |
в) |
г)
Рис. 1.6. Классификация резцов по форме головки:
а − прямые, б − отогнутые, в − изогнутые, г − с оттянутой головкой
Рис. 1.7. Классификация резцов по способу крепления режущей части:
а− цельный, б − составной с головкой, в − составной с пластинкой,
г− с механическим креплением пластинки
1.4.Поверхностиикоординатныеплоскостирезца
Слой металла, срезаемый с заготовки в процессе изготовления детали, называется припуском на обработку. Величина припуска определяется разностью размеров заготовки и обработанной детали.
На обрабатываемой заготовке различают следующие поверхности
(рис. 1.8):
1 − обрабатываемая поверхность − поверхность, с которой снимается
12
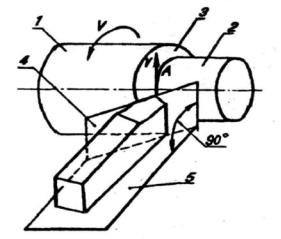
и превращается в стружку слой металла, оставленный как припуск; 2 − обработанная поверхность − поверхность, полученная после сня-
тия слоя металла, оставленного как припуск; 3 − поверхность резания − поверхность, образуемая на обрабатывае-
мой детали непосредственно режущей кромкой инструмента и являющаяся переходноймежду обрабатываемойиобработаннойповерхностями.
4 − плоскость резания − плоскость, проходящая через главное режущее лезвие и вектор скорости любой точки (точки А).
5 − основная плоскость − плоскость, перпендикулярная к вектору скорости резания.
Поверхность резания соединяет обрабатываемую и обработанную поверхности.
Рис. 1.8. Поверхности и координатные плоскости
1.5. Геометрическиепараметрырежущейчастирезца
Геометрию режущего инструмента целесообразно рассматривать двояко:
−как геометрического тела, параметры которого необходимо знать при изготовлении и заточке;
−в процессе резания, когда при неизменной форме инструмента геометрические параметры могут изменяться в зависимости от режима резания и установки инструмента относительно обрабатываемой детали.
Положение передних и задних поверхностей, главных и вспомогательных режущих кромок, образующих режущие элементы (зубья), координируется относительно, корпуса инструмента системой угловых размеров, называемых геометрическими параметрами.
Геометрические параметры, присущие режущим элементам различных инструментов, могут быть рассмотрены на примере проходного токарного резца (рис. 1.9а).
13

Рис. 1.9. Геометрические параметры резцы
Положение главной и вспомогательной режущих кромок определяется как проекции на основную плоскость. Сечения А-А и Б-Б являются следами соответственно главной и вспомогательной секущих плоскостей. Углы, измеряемые в главной секущей плоскости, называются главными и определяют режущий клин, а во вспомогательной − вспомогательными.
Угол ϕ и ϕ1 называют углами в плане. Главным углом в плане ϕ называется угол, измеряемый в основной плоскости между проекцией на нее вектора скорости подачи и проекцией главной режущей кромки.
Вспомогательным углом в плане ϕ1 называется угол, измеряемый в основной координатной плоскости между проекцией на нее вспомогательной режущей кромки и вектором скорости подачи.
Угол при вершине ε − угол между проекциями главного и вспомогательного режущих лезвий на основную плоскость: ϕ+ϕ1+ε=180°
Положение передней и главной задней поверхностей определяется главным углом γ и главным задним углом α.
Углы α и γ измеряются в главной секущей плоскости А-А. Главным
14
передним углом γ называется угол между касательной к передней поверхности и плоскости, проходящей через рассматриваемую точку перпендикулярно плоскости резания. Главным задним углом α называется угол между главной задней поверхностью и плоскостью резания. Угол заострения β и угол резания δ так же измеряются в главной секущей плоскости. Угол β измеряется между касательной к передней поверхности и главной задней поверхностью. Угол δ измеряется между касательной кпереднейповерхностииплоскостьюрезания. α+ β + γ= 90°, γ+ δ = 90°. Угол наклона главной режущей кромки λ измеряется в плоскости резания между главнойрежущейкромкойиплоскостью, проходящейчерезвершинурезцапараллельно основной плоскости. Угол λ может иметь нулевое, положительное и отрицательноезначение(см. рис. 1.9б). Вспомогательныепередниеизадниеуглыизмеря- ютсявовспомогательнойсекущейплоскостиБ-Б.
1.6. Кинематические(рабочие) углырезца
Рабочие углы отличаются от статических ввиду того, что плоскость резания, касательная к поверхности резания, в процессе резания не перпендикулярна к основной плоскости по следующим причинам:
1) рассматриваемая точка режущей кромки расположена выше или ниже оси центров либо из-за погрешности установки и закрепления инст-
румента на станке, либо из-за наличия угла λ ;
2)поверхность резания не кольцевая поверхность усеченного конуса, а винтовая поверхность;
3)в результате износа контактных поверхностей непрерывно изменяется и положение режущей кромки;
4)при обработке материалов, склонных к наростообразованию, роль режущей кромки выполняет нарост.
Рассмотрим влияние первых двух причин на значения γ иα.
Как уже отмечалось, если резец получает движение подачи, то поверхность резания − это винтовая поверхность с шагом, равным подаче, и касательная к ней плоскость резания будет расположена под углом наклона винтовой поверхности. Чем больше отношение S/2π , называемое кинематическим параметром обработки, тем больше наклон винтовой поверхности и тем больше изменение рабочих углов γр αр.
На рис. 1.10 представлено действительное положение поверхности резания и касательной к ней плоскости резания А-А с учетом движения
подачи при ϕ = 90° и λ = 0° (В-В − положение плоскости резания при
отсутствии движения подачи). Как видно, действительное положение плоскости резания ближе к задней поверхности резца, в связи с чем рабо-
15

чий задний угол αρ будет меньше статического α на величину угла η
(см. рис. 1.10). Изменяется так же положение плоскости С-С, перпендикулярной к плоскости резания в рассматриваемой точке режущей кромки,
следовательно изменится и значение рабочего переднего угла γ ρ .
Таким образом имеем: |
|
αρ =α −η, γ ρ =γ +η |
(1.1) |
где α и γ − статические углы резца; η − угол наклона траектории точки режущей кромки.
а) б) Рис.1.10. Изменение углов резца в процессе резания:
а) продольное точение; б) поперечное точение
Если развернуть на плоскость окружность вращения и винтовую траекторию точки режущей кромки, то получим треугольник (рис. 1.11), в котором катетами будут подача и окружность вращения, а гипотенузой − винтовая траектория (отрезок архимедовой спирали при поперечном точении). Отсюда:
η = arctg ( S / πD ) |
(1.2) |
Если у резца угол ϕ ≠ 90°, то угол между положениями плоско-
сти резания, измеренный в главной секущей плоскости ηϕ, можно определить по формуле:
tgηϕ = tgη sin ϕ |
(1.3) |
Тогда рабочие углы в главной секущей плоскости будут равны:
16

αρ =α −ηϕ , γρ = γ +ηϕ |
(1.4) |
Рис 1.11. Развертка траектории точки режущей кромки резца
Смещение точки режущей кромки от линии центров (рис. 1.12) может быть вызвано наклонным расположением режущей кромки при
λ ≠ 0°, ошибками установки или стремлением улучшить условия резания. Из рисунка видно, что рабочие углы в этом случае изменяются на величину:
τ = arcsin( h / R ) при ϕ = 90 ° или tgτϕ = tgτ cos ϕ при ϕ ≠ 90 °
Тогда с учетом смещения рабочие углы:
γτ = γ ±τϕ и ατ =α ±τϕ .
С учетом движения подачи и смещения точки режущей кромки, окончательно имеем:
α ρ = α −ηϕ ± τϕ , γ ρ = γ +ηϕ ±τϕ . |
(1.5) |
1.7. Методические указания по выполнению работы
Для выполнения работы необходимо иметь два-три комплекта разных типов токарных резцов. Каждый комплект должен содержать следующие основные типы резцов: проходные (правый и левый, прямой и отогнутый), подрезные, отрезные. По конструкции резцы должны быть с напайными пластинками и с механическим креплением пластин.
Конструктивные и геометрические элементы резцов измеряются универсальными и специальными инструментами - штангенциркулем, универсальным угломером и другими измерительными средствами, имеющимися в лабораториирезания.
Передний угол, задние углы, угол наклона главной режущей кромки измеряют настольным угломером.
Настольный угломер (рис. 1.13) состоит из основания 1, стойки 2, по
17

которой перемещается сектор 5 со шкалой, поворотного шаблона с указателем 4 изажимных винтов 3.
а) б)
Рис. 1.12. Геометрические параметры резца в зависимости от положения
его вершины относительно оси центров при: а − наружном точении; б − растачивании
При установке указателя 4 на 0° сектора 5 горизонтальная сторона шаблона расположится параллельно опорной плоскости угломера, на которую устанавливаете при измерении резец.
Для измерения переднего угла у (рис. 1.13) резец устанавливается так, чтобышаблон располагался нормально к проекции главной режущей кромки на основную плоскость (в главной секущей плоскости). Горизонтальная сторона шаблона совмещается без просвета с передней поверхностью лезвия, а указательотсчитывает пошкалесекторавеличину углау.
Для измерения заднего угла α (рис. 1.14) при той же установке резца вертикальная сторона шаблона совмещается без просвета с задней поверхностью лезвия резца. Указатель отсчитывает величину угла а.
Для измерения угла наклона режущей кромки λ (рис. 1.15) резец устанавливают так, чтобы горизонтальная сторона шаблона совпала без просве-
18

та с главной режущей кромкой.
Углы в плане ϕ и ϕ1 измеряют универсальным угломером. При измерении главного угла в плане ϕ (рис.1.16) планку 1 угломера прикладывают к режущей кромке лезвия, а планку 2 - к боковой стороне резца 3. Показания на шкале угломера дают значения ϕ. Подобным же методом измеряют вспомогательныйуголвпланеϕ1.
Рис. 1.13. Измерение угла γ токарного проходного резца
Рис. 1.14. Измерение угла α токарного проходного резца
1.8. Охрана труда и техника безопасности
При проведении работы в лаборатории должны выполняться требования действующей инструкции по технике безопасности при работе с металлорежущим оборудованием и оснащением. Более конкретно, в данной работе
19

следует особое внимание обращать на опасность травматизма при обращении с остро заточенными лезвиями металлорежущих инструментов. Необходимо предотвращать падение инструментов и случайное резкое воздействие их лезвий на кожный покров человека.
Рис. 1.15. Измерение угла λ токарного проходного резца
Рис. 1.16. Измерение угла ϕ токарного проходного резца
1.9. Задание для самостоятельного выполнения работы
1.Ознакомиться с содержанием и методикойпроведения работы.
2.Изучить конструкцию различных типов резцов.
3. Ознакомиться с конструкцией и принципом действия измерительных приборов.
20