
ПиОФ
.pdf
струмента, его износ, смазочно-охлаждающие жидкости и др.
Рис. 5.1. Сила резания при точении и ее составляющие
Рассмотрим влияние элементов режима резания на составляющие силы резания Зависимость составляющих силы резания от глубины резания, подачиискорости резанияможно выразитьстепеннымиуравнениями:
P |
= C |
PZ |
t X PZ s Y PZ V Z PZ |
(5.1) |
|
z |
|
t X PY sYPY V Z PY |
(5.2) |
||
P |
= C |
PY |
|||
y |
|
|
|
|
|
P |
= C |
PX |
t X PX s YPX V Z PX |
(5.3) |
|
x |
|
|
|
где Срz, Срy, Срx − постоянные коэффициенты, зависящие от условий обработки; хр, zр, yр показатели степени, характеризующие интенсивность влияния переменных (t, s, V) на составляющие силы резания.
Чем больше глубина резания и подача, тем больше площадь поперечного сечения среза и объем деформируемого металла, тем, следовательно, больше сопротивление металла стружкообразованию, и процесс резания будет протекатьсбольшимисиламиPz, Px, Ру.
Однако глубина резания больше влияет на силу резания, чем подача. Различная интенсивность влияния глубины резания и подачи на силы резания вызвана их неодинаковым действием на степень деформации срезаемого слоя.
Изменение ширины срезаемого слоя не сказывается на изменении степени его деформации (коэффициент усадки стружки остается постоянным). Увеличение же толщины срезаемого слоя снижает величину коэффициента усадки стружки, т. е. уменьшает степень деформации срезаемого слоя. Главная составляющая силы резания Pz пропорциональна той степени деформации, которую получил срезаемый слой при превращении его в стружку. При увеличении ширины срезаемого слоя, вследствие увеличения пло-
51
щади сечения среза, сила Pz должна увеличиться во столько же раз, во сколько возросла ширина h, т.к. при этом степень деформации срезаемого слоя не изменяется. Поэтому и показатель степени хр при ширине h срезаемого слоя близок к единице. Увеличение толщины а срезаемого слоя также увеличивает его площадь, но при этом степень деформации слоя уменьшается и рост силы Pz отстает от роста толщины срезаемого слоя. Вследствие этого показатель степени ур при толщине срезаемого слоя а не может быть равным единице, а всегда несколько меньше ее. Поскольку физические и технологические размеры срезаемого слоя связаны друг с дру-
гом только через главный угол в плане ( t = b sin ϕ, s = |
a |
), то |
|
sin ϕ |
|||
|
|
влияние t и s на силу Pz остается таким же, как влияние b и a , т.е. показателистепенивформуле (5.1) приглубине хрс = 1, априподаче урс = 0,75.
Более сильное влияние на силу Pz ширины срезаемого слоя, чем толщины, позволяет сделать вывод: для уменьшения главной составляющей силы резания при заданной площади сечения срезаемого слоя во всех случаях необходимо стремиться работать с возможно меньшим отношением и b/а, увеличивая толщину среза за счет уменьшения ширины.
Изменение скорости резания влияет на составляющие силы резания так, как оно влияет на изменение коэффициента усадки стружки. При резании материалов, не склонных к наростообразованию, коэффициент усадки монотонно убывает при увеличении скорости резания. Так же ведут себя и составляющие силы резания, уменьшающиеся при увеличении
V вначале быстро, |
а затем более медленно. При резании материа- |
лов, склонных |
к наростообразованию, кривая Pz = f(V) так же, как и |
кривая К1 = f(V), немонотонна (рис. 5.2), причем обе кривые совпадают по фазам. Начиная от V1 до V2, при которых высота нароста растет, сила Рz уменьшается, достигая минимума при максимально развитом наросте (за счет благоприятного изменения геометрии резца (рис. 5.3) и уменьшения пластической деформации срезаемого слоя. При скоростях резания от V2 до V3 , при которых высота нароста уменьшается (Нн → 0, следовательно, γн → γ), сила Pz вновь возрастает. При скоростях резания, больших скорости V3, соответствующей исчезновению нароста, сила Pz при увеличении скорости резания в дальнейшем непрерывно уменьшается за счет уменьшения сопротивления срезаемого слоя пластической деформации и уменьшения сил трения.
Скорости резания, с которыми работают при точении твердосплавными резцами, выше, чем скорость V3. Поэтому участок кривой сила-
скорость |
для V > V3 можно описать частной зависимостью |
Pz = C PI z |
V − z pz , показатель степени в которой по экспериментальным |
52

данным zpz = 0,35...0,1. При высоких скоростях резания процессы стружкообразования и трения на поверхностях инструмента стабилизируются и скорость резания практически перестает влиять на составляющие силы резания, показатель степени zpz → 0.
Рис. 5.2. Схема влияния скорости резания |
Рис. 5.3. Изменение геометрии резца |
на высоту нароста Н, коэффициент |
за счет наростообразования |
усадки стружки |
|
5. 3. Методика проведенияэксперимента иобработкирезультатов
Оборудование и аппаратура
Эксперименты по определению сил резания выполняются на токарновинторезном станке 16К20. Вместо резцедержателя на станке установлен динамометр с закрепленным в нем резцом.
Существует большое количество различных конструкций динамометров. По принципу действия они разделяются на гидравлические, механические и электрические. Наиболее современными являются электрические динамометры, так как они малоинерционны, чувствительны и компактны. Благодаря этому электрические динамометры обеспечивают высокую точность измерения и ими можно определять как большие, так и малые значения сил резания.
Электрические динамометры состоят из трех основных частей: датчиков, воспринимающих нагрузку, органов связи, соединяющих датчики, и приемников. Датчики преобразуют упругие деформации или малые перемещения в электрическую энергию. Применяются датчики различного типа: индуктивные, пьезоэлектрические, проволочные, емкостные идр.
Одним из распространенных приборов для измерения сил резания является универсальный динамометр ВНИИ, с помощью которого можно измерять силы резания при точении, фрезеровании, плоском шлифовании, а также осевую силу и крутящий момент при сверлении. Комплект прибора состоит из динамометра-датчика УДМ-600, усилителя ТА-5, приборного щита с микроамперметрами М266 и осциллографа Н-700. Схема соединения этих устройств показана на рис. 5.4. По показаниям микроамперметров, установленных на приборном щите, определяют среднюю величину сил ре-
53

зания. Мгновенные значения сил резания в диапазоне частот от 0 до 500 Гц можно измерять с погрешностью не свыше 10%, регистрируя показания динамометра наосциллографе.
Рис. 5.4. Схемасоединенияустройств, входящихвкомплектдинамометра
Динамометр состоит из корпуса 1 и державки 2, выполненной в виде квадратной плиты с круглым фланцем на верхней части (рис. 5.5а), который предназначен для закрепления сменных приспособлений: резцедержателя при точении, круглого стола при сверлении, тисков при фрезеровании и шлифовании. Державка установлена в корпусе на 16 опорах (рис. 5.5б). Оси первых восьми опор расположены вертикально, а оси остальных восьми опор − горизонтально.
Под действием силы Pz деформируются вертикальные опоры, а под действием сил Ру и Рх − горизонтальные.
Каждая опора состоит из двух ножек и тонкостенной втулки (рис. 5.5в). Площади сечений втулки и ножек опор равновелики и выбраны так, чтобы материал опор при нагрузке работал в области упругих деформаций. На втулки опор наклеены проволочные датчики сопротивления с номинальным сопротивлением100 Ом.
В работе опоры динамометра упруго деформируются, в результате чего в датчике возникает электрический ток малой величины, который поступает на вход электронного усилителя, усиливается и передается на параллельно соединенные микроамперметр и вибратор осциллографа, с помощью которых регистрируются показания динамометра.
54

Рис. 5.5. Универсальныйдинамометр
Для проверки стабильности чувствительности динамометр периодически (перед каждой серией опытов) подвергается тарированию.
Тарирование следует производить на тарировочном стенде в следующей последовательности:
1)установить динамометр на тарировочный стенд;
2)подготовить динамометр к работе согласно инструкции;
3)нагрузить динамометр эталонной нагрузкой отдельно по каждой измеряемой составляющей силы резания (рис. 5.6а) и зафиксировать показания динамометра по этой же составляющей;
В пределах диапазона измерения динамометра дают 3 ... 4 различных значения эталонной нагрузки. По данным тарирования строят тарировочные графики (рис. 5.6б).
а) |
б) |
Рис. 5.6. |
СхематарировкидинамометраУДМ600: |
а- схеманагружения; б- тарировочныйграфик; 1 − нагрузка; 2 − разгрузка
Тарировочные графики динамометра строят в следующих координатах: по горизонтали откладывают показания динамометра в единицах отсчетного прибора А мкА, а по горизонтали − величину Р/т, т.е. величину действующей силы Р, поделенную назначениекоэффициентаусиленияm по измеряемой составляющей силы резания. Под коэффициентом усиления m понимается цифра, соответствующая положению переключателя
55
усилителя.
Наклон прямой тарировочного графика характеризуется величиной коэффициента К.
К = |
Аm , |
(5.4) |
|
P |
|
|
где А − показания микроамперметра; Р − сила резания или эталонная сила; т − величина коэффициента усиления, установленная перед опытом.
Значения сил резания определяются по формуле
P = |
Аm |
, H , |
(5.5) |
K |
|
||
|
|
|
где А − показания микроамперметра, т − величину коэффициента усиления, К − коэффициент тарировочного графика.
5.4. Охрана труда и техника безопасности
Источниками повышенной опасности при работе на токарно-винторезных станках в первую очередь являются вращающиеся части и стружки. Не следует пренебрегать предохранительными устройствами, предусмотренными конструкцией станка, будь это щиток, экран, кожух или ограничения. Заготовку следует надежнозакреплятьвпатронеилицентрахстанка. Всяработанатокарномстанке и приборах производится учебным мастером или преподавателем, проводящим занятие. Студентамотводитсярольфиксированиярезультатовопытов.
5 . 5 . Порядок выполнения экспериментальной части работы
1.Изучить схему и конструкцию динамометра УДМ600 и ознакомиться с процессом измерения сил при точении.
2.Изучить инструкцию по технике безопасности при работе на токарных станках.
3.Составитьпланэксперимента, занести его втабл. 5.1.
4.Собрать схему (см. рис. 5.4) измерения сил резания на станке 16К20. Провести испытание схемы пробным резанием.
5.Произвести резание заготовки с различными значениями глубины резания при постоянных значениях скорости резания и подачи. Измерить составляющие сил резания Р, в мкА, соответствующие заданным значениям глубинырезания.
6.При постоянных скорости и глубине резания измерить составляю- щиеР-сил резания, соответствующие различным значениям подачи.
7.При постоянных значениях глубины резания и подачи измерить состав-
ляющие Pz Ру Рх сил резания, соответствующие различным значениям скорости резания. Режимырезаниядлякаждойсерииопытовзадаютсяпреподавателем.
8.Результаты измерений составляющих Pz, Ру, Рх сил резания для всех трех серий опытов занести в табл. 5.1.
56
9. По тарировочному графику (рис 5.6б) или по формуле (5.5) эти результаты в мкА перевести в значения сил резания в Н.
|
Результаты измерения силы резания |
Таблица 5.1. |
||||
|
|
|
||||
№опыта |
|
Режимырезания |
|
Показания |
|
Силарезания |
|
t, мм |
s, мм/об |
V, м/мин |
прибора, мкА |
|
Pz, Н |
|
|
Зависимость |
Pz=f(t) |
|
|
|
1 |
t1 |
|
|
|
|
|
2 |
t2 |
s=const |
V=const |
|
|
|
3 |
t3 |
|
|
|
|
|
|
|
Зависимость |
Pz=f(s) |
|
|
|
4 |
t=const |
s1 |
|
|
|
|
5 |
s2 |
V=const |
|
|
|
|
6 |
|
s3 |
|
|
|
|
|
|
Зависимость |
Pz=f(V) |
|
|
|
7 |
t=const |
s=const |
V1 |
|
|
|
8 |
V2 |
|
|
|
||
9 |
|
|
V3 |
|
|
|
10.По полученным значениям сил резания построить графики зави-
симости Pz = f(t), Pz = f(s) и Pz = f(V).
11.Провести анализ влияния режимов резания на составляющие сил
резания.
5.6. Содержание отчета
1.Цель работы.
2.Схемы расположения сил резания.
3.Таблица с результатами измерения сил резания.
4.Графики зависимости сил резания от режимов резания.
5.Привестианализвлиянияэлементоврежимарезаниянасилырезания.
5.7.Контрольные вопросы
1.Перечислить составляющие силы резания.
2.Назовите факторы, влияющие на силы резания.
3.Поясните характер влияния t, s, V на составляющие сил резания.
4.Устройство и принцип действия динамометра УДМ600.
5.Поясните графики Рz,y,x=f(t, s, V).
57
6. ЛАБОРАТОРНАЯ РАБОТА № 6
КИНЕМАТИКА РЕЗАНИЯ ПРИ СВЕРЛЕНИИ
6.1. Цель работы
Целью работы является:
1.Изучение конструктивных и геометрических элементов спирального сверла.
2.Изучение конструкции и принципа работы измерительных инструментов, применяемых при контроле сверл.
3.Приобретение практических навыков при измерении конструктивных и геометрических элементов сверла.
4.Исследование изменения переднего и заднего углов сверла вдоль главной режущей кромки.
6.2. Конструктивные и геометрические элементы сверла
Сверление − основной метод получения отверстий в сплошном материале. Сверлением получают отверстия 11...12 квалитета с шероховатостью обработанных поверхностей Rz 20...80.
Кинематическая схема сверления − процесс резания осуществляется за счет двух совместных движений: вращения сверла или детали вокруг оси отверстия (главное движение резания Dr) и поступательного движения сверла вдоль оси (движение подачи Ds). На сверлильных станках сверло совершает оба движения, на токарных и револьверных станках и автоматах вращается обрабатываемая заготовка, сверлу придается только поступательное движение подачи.
Спиральное сверло (рис. 6.1) состоит из рабочей части, включающей режущую и калибрующую части, шейки и хвостовика. Конические хвостовики сверл имеют лапку, цилиндрические выполняются с поводком или без него.
На рис. 6.2 показаны поверхности лезвий сверла и его режущие кромки:
1− передняя поверхность Ау лезвия − часть поверхности винтовой стружечной канавки.
2− главная задняя поверхность Ау лезвия может быть конической поверхностью, винтовой или плоскостью.
3− вспомогательная задняя поверхность А\, лезвия (ленточка) - часть конической поверхности с очень малой конусностью, ось которой совпадает с осью сверла.
4 − главная режущая кромка К, образуемая пересечением передней Ау и главной задней Аа поверхностей.
58
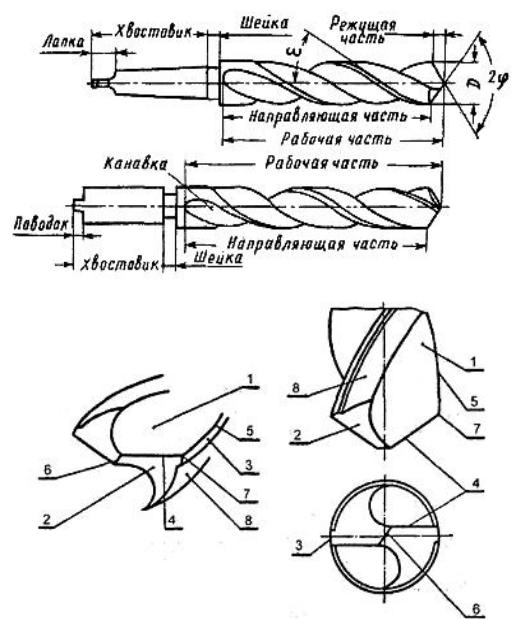
5 − вспомогательная режущая кромка К, образуемая пересечением передней Ау и вспомогательной задней А'а поверхностей.
Рис. 6.1. Конструктивные элементы сверла
Рис. 6.2. Поверхности лезвий сверла и его режущие кромки
6 − поперечная кромка (перемычка) образуется при пересечении двух главных задних поверхностей сверла.
7 − вершина лезвия – точка пересечения главной К и вспомогательной К режущих кромок.
59

8 − спинка сверла, заниженная относительно ленточки поверхность, предназначенная для уменьшения трения между сверлом и обработанной поверхностью отверстия.
Геометрические параметры сверла изображены на рис. 6.3. Передний угол сверла γ измеряется в плоскости N-N проходящий через точку режущей кромки, нормально к ней. Задний угол измеряется в плоскости О- О, проходящей через эту же точку, касательно к образующему цилиндру, на котором лежит рассматриваемая точка (параллельно оси сверла).
Рис. 6.3. Статические углы сверла
Передний угол γ − угол между касательной к передней поверхности и нормалью в этой же точке к поверхности, которую описывает режущая кромка при вращении ее вокруг оси сверла (усеченный конус). Значение переднего угла является величиной переменной вдоль режущей кромки и зависит от диаметра, на котором лежит рассматриваемая точка. Максимальное значение γ на периферии сверла (в плоскости N1-N1) и минимальное в районе перемычки.
Задний угол − угол между касательной к окружности, которую описывает точка режущей кромки при вращении ее вокруг оси сверла и касательной в той же точке к задней поверхности сверла. Значение заднего угла является так же величиной переменной, максимальное значение в районе перемычки, а минимальное значение на периферии сверла (в плоскости О1-О1).
Двойной угол в плане 2ϕ измеряется между проекцией двух режу-
60