
курлаев лекции
.pdf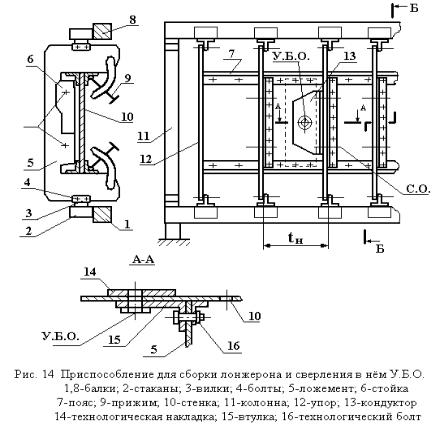
болтами с нижним.
4.Установить левую панель по УБО верхнего лонжерона, прижать лентами.
5.Сверлить отверстия в левой панели по НО нервюр и лонжеронов. Зенковать со стороны обшивки.
6.Установить уголки-компенсаторы, соединяющие стрингера с нервюрами, сверлить, клепать к нервюрам.
7.Снять левую панель.
8.Повторить операции 4, 5, 6 для правой панели. Клепать кроме шва с нижним лонжероном.
9.Установить левую панель на технологические болты.
10.Снять нижний лонжерон (для подхода к левой панели).
11.Клепать левую панель к нервюрам и верхнему лонжерону, клепать уголкикомпенсаторы к стрингерам.
12.Установить нижний лонжерон, клепать его к нервюрам и обшивкам заклепками для односторонней клепки.
Сборочная размерная цепь:
Hх = Lн + 2Lоб + 2Lбо-н + 2Lфикс. нерв.
Lн = Lсп.н + 2Lспн-н (сп.н. – сборочное приспособление нервюры)
Hх = Lсп.н + 2Lспн-н + 2Lоб + 2Lбо-н + 2Lфикс.нерв.
Производственная погрешность:
Hх = Lсп.н + 2 Lспн-н + 2 Lоб + 2 Lбо-н + 2 Lфикс.нерв. Сi
По точности приблизительно равна сборке по СО отсеков.

Сборка агрегатов по УБО
Осуществляется в стыковочных стендах. Стыковочный стенд обеспечивает 6 степеней свободы: перемещение по всем осям и повороты вокруг осей Ф-1, Ф-2,
Ф-3.
Вид поставки отсеков:
-Отсеки Ф-1 и Ф-3 подаются с двумя УБО для фиксаций в стыковочном стенде и с одним УБО для стыковки с Ф-2.
-Отсек Ф-2 подается с двумя УБО для фиксации в стыковочном стенде и по одному УБО и НО к отсекам Ф-1 и Ф-3.
УБО в отсеках сверлят в разделочных стендах, а кронштейн 4 в стыковочном стенде устанавливается по монтажным эталонам в этих отсеках.
Порядок сборки
1.Установить отсеки на ложементы стенда по УБО, прижать лентами.
2.Совместить отсеки между собой по УБО, вставить фиксаторы 6.
3.Сверлить отверстия под заклепки (винты) по НО стыковых шпангоутов Ф-2.
4.Зенковать со стороны обшивки.
5.Клепать.
УБО задаются из числа отверстий под крепеж или особо.
+ значительное упрощение сборочной оснастки и широкое использование.
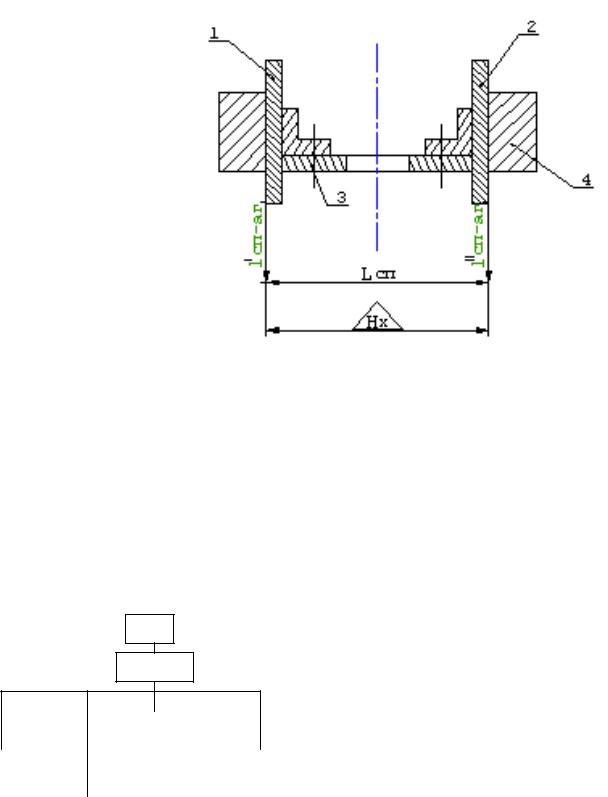
1.5. Расчет полных сборочных размерных цепей.
Для определения ожидаемой погрешности сборки Hх необходимо задать:
1.метод сборки
2.метод обеспечения взаимозаменяемости.
Рассмотрим сборку отсека фюзеляжа по базе "внешняя поверхность обшивки".
1 – панель;
2 – панель;
3 – стенка шпангоута;
4 – рубильник стапеля.
Порядок расчета
1. Составление сборочной размерной цепи по внешнему обводу агрегата.
Hх = Lсп + 2lсп-аг
Hх = Lсп + 2 lсп-аг Сi
2. Составление схемы увязки оснастки (принимаем эталонно-шаблонный метод)
ТП – теоретический плаз ШКК – шаблон контрольно-контурный
ШКС – шаблон контура сечения
|
|
|
|
|
|
|
|
|
|
|
|
|
|
|
|
|
|
|
|
Обшивка |
|
|
|
|
|
|
|
Стенка |
|
|
|
Стапель |
|
||||||
|
|
|
|
|
|
||||
|
|
|
|||||||
|
|
|
|
|
|
|
|
|
|
|
|
|
|
|
|
|
|
|
|
|
Стрингер |
|
|
|
|
|
|||
|
|
|
|
|
|
|
|
|
|
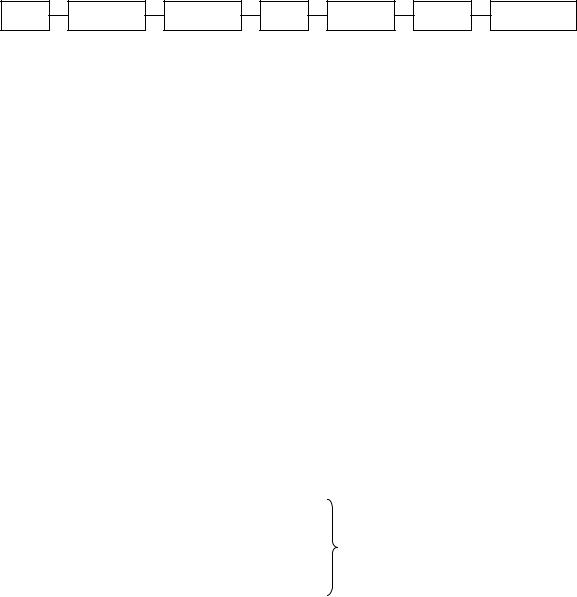
3. Составление структурной схемы получения обводов рубильника-стапеля (на основании схемы-увязки). Выбираем те схемы, которые необходимы для расчета размерной цепи (РЦ).
ЭП – эталон поверхности; |
КЭИ – контр эталон инструментальный; |
|
МЭ – монтажный эталон. |
|
|
Отсюда: |
Lсп = Lмэ + 2lмэ-сп |
Lмэ = Lкэи + 2lкэи-мэ
4. Составление полной технологической размерной цепи. Образование внешнего обвода.
Hх = Lтп + 2lтп-шкк + 2lшкк-шкс + 2lшкс-эп + 2lэп-кэи + 2lкэи-мэ + 2lмэ-сп + 2lсп-аг
Hх = Lтп + 2 lтп-шкк + … Сi
Все операционные погрешности берутся из таблиц.
5. Вычисление Hх. (Например, по методу полной взаимозаменяемости)
( Hх)в = В.О.i
сравниваем с т.у.
( Hх)н = Н.О.i
В.О.i, Н.О.i – соответственно верхнее и нижнее отклонение i-того составляющего звена РЦ.
Если по точности расчеты не прошли, то меняем либо метод сборки, либо метод увязки, либо ужесточаем допуски изготовления эталонно-шаблонной оснастки.

2. Технология выполнения соединений, применяемых
при сборке планера.
2.1. Классификация соединений.
Соединения планера самолета
|
|
|
|
|
|
|
|
|
|
|
|
|
|
|
|
|
|
|
|
|
|
|
|
|
Неподвижное |
|
|
|
Неподвижное |
|
Подвижное |
||||||||||||||||
|
|
неразъемное |
|
|
|
|
разъемное |
|
|
разъемное |
|||||||||||||
|
|
соединение |
|
|
|
|
соединение |
|
соединение |
||||||||||||||
|
|
|
|
|
|
|
|
|
|
|
|
|
|
|
|
|
|
|
|
|
|
|
|
|
|
|
|
|
|
|
|
|
|
|
|
|
|
|
|
|
|
|
|
|
|
|
|
Клепанные |
|
Сварные и паянные |
|
Клеевые |
|
Комбинированные |
|
|
Винтовые |
|
Болтовые |
|
|
|
Шарнирные (вильчатые, шлицевые, цапфовые) |
|
|||||||
|
|
|
|
|
|
|
|
|
|
|
|
||||||||||||
|
|
|
|
|
|
|
|
|
|
|
|
|
|
|
|
|
|
|
|
|
|
|
|
|
|
|
|
|
|
|
|
Силовыми точками |
|
Непрерывным швом |
|
|
Комбинированные |
||
|
|
|
|
|
|
|
|
По конструктивному признаку
По конструктивно-технологическому признаку
Неподвижное неразъемное соединение - обеспечивает неизменное взаимное положение деталей, разборка их не предусмотрена без повреждения конструкции и крепежа.
Соединения силовыми точками (заклепочное, болтовое, точечная сварка) характеризуются:
а) ослабленным сечением шва за счет отверстий или нагрева, б) концентратором напряжения в зоне точки,
в) дискретностью процесса, которая снижает производительность. Соединения непрерывным швом (роликовая сварка, клеевой шов)
характеризуются:
а) незначительным ослаблением сечения шва за счет нагрева, б) незначительными концентраторами напряжений,
в) непрерывностью процессов, что позволяет использовать автоматы. Комбинированные соединения (клепка + склеивание) включают все
признаки предыдущих видов и имеют следующую особенность:
Ркомб = (Рс.т. + Ркл)
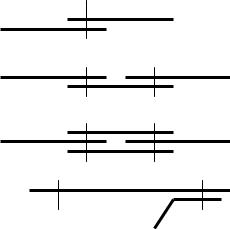
Р – прочность;
– коэффициент редуцирования 1, учитывает разницу пластических свойств соединительных сред.
Вид выбираемого соединения определяется материалом и особенностями конструкции.
Пример, в самолете среднего класса: заклепки - 60%, сварка - 20%, болты - 20%).
2.2. Технология выполнения заклепочных соединений.
2.2.1. Общие сведения
Заклепочное соединение - самое распространенное для самолетов с числом М 3, так как планер их обычно выполнен из алюминиевых сплавов (пример: ТУ144 имеет 1,3 млн. заклепок).
Преимущества заклепочных соединений:
1) возможность выполнения соединений непосредственно в стапелях, обеспечивающих требуемую точность внешних обводов;
2)отсутствие технологических выдержек;
3)простота контроля и исправления дефектов.
Недостатки:
1)увеличение массы конструкции за счет наличия выступающих частей заклепок;
2)снижение прочности и выносливости за счет наличия отверстий и концентрации напряжений в зоне отверстий;
3)большая трудоемкость;
4)вредность работ из-за шума и вибраций;
5)большая шероховатость поверхности по сравнению с пайкой и склеиванием;
6)нарушение антикоррозионного покрытия из-за трещин при ударной клепке.
2.2.2. Виды швов
По конструктивному признаку:
- внахлест (узлы каркаса планера)
- встык с одной накладкой (обшивки, узлы каркаса)
- встык с двумя накладками (силовые узлы планера)
- стрингерное
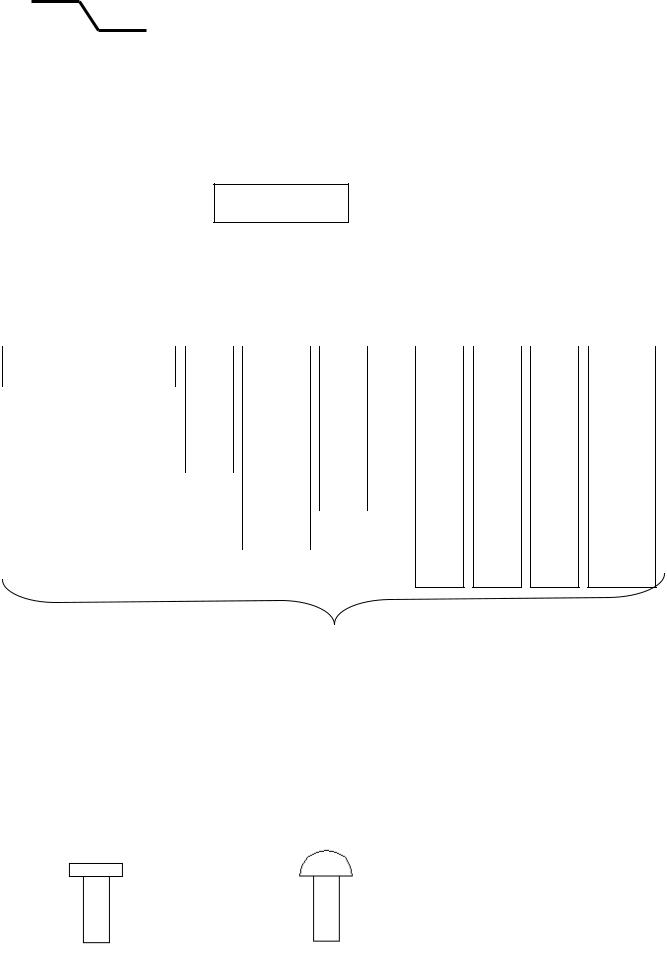
По степени герметичности:
1)прочные швы;
2)прочные - плотные (т.е. герметичные).
2.2.3.Типы заклепок
Заклепки
|
|
|
|
|
|
|
|
|
|
|
|
|
|
|
|
|
|
|
|
|
|
|
|
|
|
|
|
|
|
|
|
|
|
|
|
|
|
|
|
|
|
|
|
|
|
|
|
|
|
|
|
|
|
|
|
Для двухсторонней клепки |
|
|
Для односторонней клепки |
|
|
|
|
||||||||||||||||||||
|
|
|
|
|
|
|
|
|
|
|
|
|
|
|
|||||||||||||
|
|
|
|
|
|
|
|
|
|
|
|
|
|
|
|
|
|
|
|
|
|
|
|
|
|
|
|
|
|
|
|
|
|
|
|
|
|
|
|
|
|
|
|
|
|
|
|
|
|
|
|
|
|
|
|
Стержневые
|
|
|
|
|
|
|
|
|
|
|
Обыкновенные |
|
С компенсатором |
|
Стержни |
|
|||
|
|
|
|
|
|
|
|
|
|
Трубчатые |
|
С высоким сопротивлением срезу |
|
Болт-заклепки |
С сердечником |
Гайки-пистоны |
Взрывные |
высоким сопротивлением |
срезу (винтовые) |
|
|||||||||
|
|
|
|
|
|||||
|
|
|
|
|
|
|
|
|
|
|
|
|
|
|
|
|
|
С |
|
Специальные типы Специальные типы заклепок составляют в настоящее время 20%.
Материал заклепок:
алюминиевые сплавы: В94, В65, Д18П, Д19П, АМг, АМц; стали: 30ХГСА, Х18Н9Т, 20Г2.
Форма головок заклепок:
Плоская (ЗП) (бочкообразная) Полукруглая
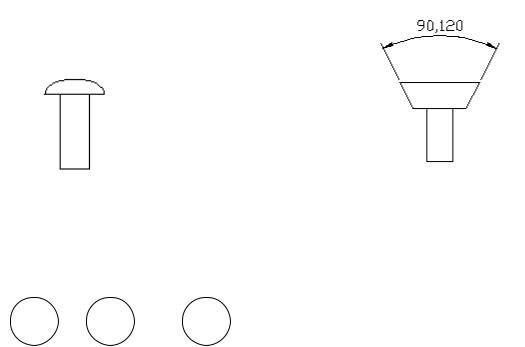
Плосковыпуклая (чечевицеобразная) |
Потайная (ЗУ) |
||||
Головки заклепок маркируют: |
|
||||
|
В94 |
В65 |
АМц |
|
|
|
|
|
|
. . |
|
|
|
|
|
|
|
|
|
|
|
|
|
|
вып. |
|
вып. |
|
Все заклепки нормализованы: 3531, А-2, 6-7.
2.2.4.Основные технологические операции постановки обыкновенных стержневых заклепок
1.Образование отверстия.
2.Упрочнение (при необходимости).
3.Образование гнезда под потайную головку заклепки (при необходимости).
4.Вставка заклепок и натяжка пакета.
5.Клепка.
6.Контроль.
Образование отверстия
Это подготовительная операция, от качества которой во многом зависит качество заклепочного шва.
Методы образования отверстия:
1) пробивка.
Пробивка осуществляется на прессах с применением дыропробивных штампов. + высокая производительность
- а) снижение прочности и выносливости вследствие наклепа стенок отверстий и микротрещин;
б) низкая чистота стенок из-за заусенцев; в) выпучивание листов в зоне отверстия;
г) невозможность образования отверстия непосредственно в стапелях. Поэтому применяется только для Н.О.
2) сверление.
Сверление менее производительно, но дает хорошее качество стенок отверстия.
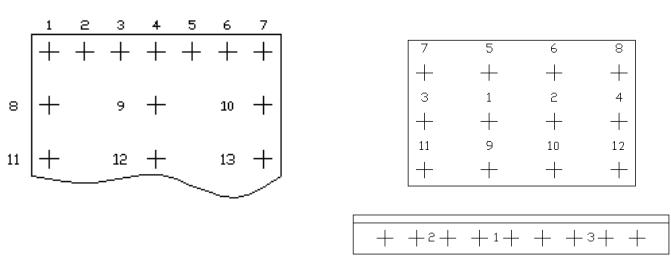
Оборудование:
1)пневмодрели n = 500 ... 17000 об/мин.;
2)универсальные станки: вертикально-сверлильный, радиально-сверлильный;
3)специальные сверлильные и сверлильно-зенковальные установки: СУ-Н, СУ-Ш, СЗУ-Ф1, СЗУ-ПК - состоящие из поддерживающих устройств и сверлильно-зенковальных элементов (СЗА – рабочая головка) или радиальносверлильного станка;
4)СЗВУ - сборочное приспособление со встроенным СЗА;
5)автомат ГСЗ (группового сверления и зенкования).
Инструмент:
спиральные сверла из У7А, У10А (для AL-сплавов); быстрорез Р9, Р18 (для сталей);
быстрорез с пластинками из твердых сплавов Т15К6, ВК8 и др. (для 30ХГСНА, Ti-сплавов).
Режимы сверления:
n = 500 ... 3500 об/мин. для Ti-сплавов и для AL-сплавов s = 0,03...0,15 об/мин.
Порядок сверления: для длинномерных деталей каркаса и обшивок для исключения коробления, увода и образования "хлопунов".
Существуют два метода последовательности сверления и клепки:
1. Концевой |
2. Центральный |
|
накладка |
стрингер
Способы ориентирования сверла по центру отверстия:
1)По разметке, погрешность по шагу t = 0,5 мм;
2)по шаблону с втулками, t = 0,2 мм;
3)по кондуктору, t = 0,1 мм;
4)по НО, t = 0,2 мм;
5)по программе на станках с ЧПУ, t = 0,05 мм.
Контролируемые параметры:
1) диаметр отверстия: dотв = dз + (0,1 … 0,2), где dз – диаметр заклепки. Проверяется калибром-пробкой.
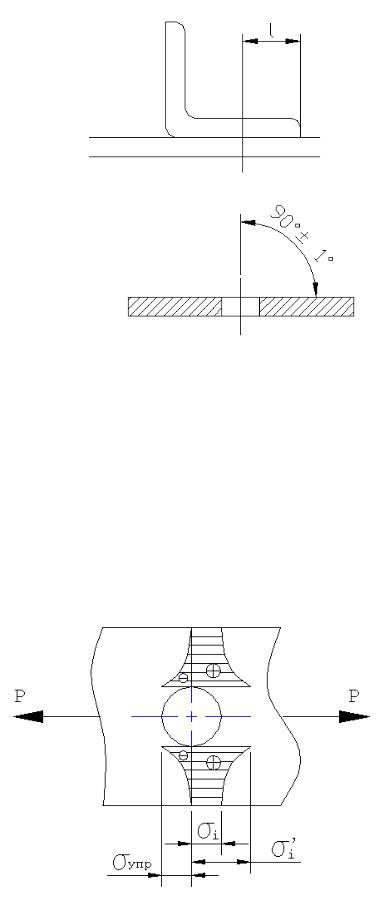
2)шаг: t 1 мм.
3)перемычка: l 2dз
4)перпендикулярность оси отверстия. Проверяется калибром-пробкой с фланцем, щупом.
5)отсутствие эллипсности и огранки. Проверяется нутромером и индикатором.
6)отсутствие заусенцев.
7)отсутствие трещин по стенкам отверстий. Проверяется лупой четырехкратного увеличения.
8)плотность прилегания листов и отсутствие стружки между ними.
Упрочнение отверстия
Для увеличения прочности и выносливости заклепочных швов в ответственных местах применяют упрочнение материала детали в зоне отверстия.
i’ – максимальное растягивающее напряжения в зоне отверстия.
упр – максимальное упрочняющее (сжимающее) напряжение в зоне отверстия.