
РАМАЗАНОВА К.Р
..pdf
241
Сопротивления решёток под насадку. Площадь свободного сечения решётки fотв = 1,149 м2, площадь поперечного сечения колонны fк=2,01 м2, отношение f= fотв/fк = 0,57. Определение эквивалентного диаметра отверстий (по максимальной прорези):
dэкв= 4 f/отв/П/отв = 0,044 м, |
(8.6) |
Где f/отв = 0,022 1,6 |
= 0,0352 м2, П/отв=2 (0,022+1,6)=3,22 м. Критерий Рейнольдса Re |
= Wотв ρг dэкв /μг = |
6685, где Wотв= V0/fотв= 2,05 м/с. |
Если значение Re < 105, то значение коэффициента сопротивления решётки находили по формуле:
ξ = [ξ4 + ε0 ( ξ0 – f)2] f-2 = [0,03 + 0,03 (1,48-0,57)2] 0,57-2 = 0,17. |
(8.7) |
Потеря давления в решётке ∆Pр= ξW2отв
ρг/2 = 0,45 Па. Тогда общая потеря
давления в абсорбере ∆P = ∆Pкп + ∆Pкр + ∆Pр = 3239,5 Па или 0,033 кгс/см2.
Высота насадки абсорбционной колонны. Содержание кумола в абгазах окисления до очистки G1 = 85004 = 34 кг/ч и после очистки G2 = 8500
0,126 = 1,071
кг/ч, где 4 и 0,126 г/м3 – принятые значения содержания кумола в абгазах окисления до и после очистки. Количество кумола, уловленного в абсорбере кумола G = G1-G1 = 32,93 кг/ч. Исходя из молекулярной массы кумола 120 кг/кмоль и плотности паров кумола ρг = 5,357 кг/м3, содержание кумола в абгазах до y1=0,000747 кмоль/кмоль и после очистки y2 = 0,0000235 кмоль/кмоль. С учётом количества свежего ПАБ 1,5 м3/ч или Gп= 1300 кг/ч свежего ПАБ и молекулярной массы 162 кг/кмоль диизопропилбензола, количество кумола x2=0,034 кмоль/кмоль в нижней части, с учётом кумола, уловленного из абгазов, и в верхней части абсорбера x1 = 0,00379 кмоль/кмоль. По формуле y*=kx равновесные составы кумола y1* = k
x2=0,000170 в нижней части
и y2*=kx1= 0,0000379 в верхней части абсорбера при k = 0,005 для температуры -
3,7°С вычисляли обработкой экспериментальных данных табл. 8.2 и 8.3. Значение движущей силы абсорбции равно ∆yср=(∆yн - ∆yв)/2,3 Ig(∆yн/∆yв) = 112,4
10-6, тогда
число теоретических тарелок (число переноса) nг = ( y1-y2)/∆yср ≈ 7, где ∆yн = y1-y1* и ∆yв= y2-y2*. При этом высота насадки H= nг*ВЭТТ ≈ 3 м, эквивалентная теоретической тарелке:
ВЭТТ = k5 W-1*(ρж/ρг)0,5 (1+Dk)-1 h-0,25 (1-60 k6 LVf0,5) f d Dk-1 = 0,409, |
(8.8) |
где k5 = 0,55, k6 = 0,09, h=5 м – высота слоя насадки. Расчётная высота насадки 3 м, поэтому реальная или фактическая высота насадки 15 м в абсорбере с запасом обеспечит необходимую степень очистки абгазов окисления.
Расчёт температуры ПАБ, с которой должны поступать в абсорбер, чтобы температура смеси абгазов с ПАБ или абсорбции была tсм= -3,7ºС. Из уравнения теплового баланса:
Тп =[(Gа cа+Gп сп) Тсм–Gа cа Та]/Gп cп = -7ºС – температура абсорбции, |
(8.9) |
где для абгазов Gа =10625 кг/ч, cа=0,248 ккал/кгград (азот), Та = 2ºС и для ПАБ Gп =
10400 кг/ч, cп = 0,408 кг/кгград (кумол).
242
Расчёт холодильника. Тепловая нагрузка на холодильник Q = Gрcп
(t1-t2) =
26454 ккал/ч, где расход ПАБ в рецикле 12 м3/ч или Gр = 10560 кг/ч, t1 = -0,86ºС и Т2 = -7ºС. Рассчитали расход рассола, площадь поверхности холодильника 50 м2 и при фактической 68 м2 обеспечивается необходимая степень очистки абгазов. В результате расчётов установлено, что при подаче на каждую из четырёх колонн окисления по 2500 нм3/ч воздуха [35], общее количество абгазов окисления, поступающих на абсорбцию, составляет 8500 нм3/ч. Расчёт абсорбционной установки производился из условия начального 4 г/м3 и конечного 126 мг/м3 содержания кумола в абгазах. Предлагаемая в качестве абсорбера, имеющаяся в производстве прекурсора [35] колонна диаметром 1,6 м, при замене тарелок на три слоя по 5 м насадки – кольца Палля диаметром 3838 мм общей высотой 15 м, может быть использована для очистки
абгазов. Для обеспечения достаточной степени смачивания насадки необходим рецикл ПАБ с расходом 12 м3/ч, охлаждённых до Т = -7ºС при подаче 1,5 м3/ч достаточно для очистки 8500 нм3/ч абгазов окисления. Для охлаждения ПАБ до Т = -7ºС, необходимо установить два холодильника:
-водяной с поверхностью 39 м2 только на период пуска установки,
-рассольный с поверхностью 68 м2. При этом расход воды 38 м3/ч и рассола
22,6 м2/ч.
На основании расчётов равновесия газ-жидкость применительно к кумолу в абгазах (табл. 8.1 и 8.2; рис. 8.1, кр. 1-4), результатов исследований на лабораторных установках (табл. 8.3 и 8.4) и пилотной установке (рис. 8.3), технологических расчётов основного оборудования разработаны бизнес-план, исходные данные для проектирования опытно-промышленной установки, проект Т-48128 ООО «Саратоворгсинтез». Произведён монтаж установки очистки абгазов окисления в производстве прекурсора [34], проведены опытно-промышленные испытания, внесены соответствующие изменения в регламенты с внедрением в кумольное производство поликонденсационных мономеров [34-36].
На рис. 8.3 приведена технологическая схема на рис. 8.4 блок-схема опытнопромышленной установки очистки абгазов окисления кумола, а на рис. 8.5 фотография промышленной запатентованной абсорбционной установки очистки абгазов окисления [261а].

243
Рис. 8.3. Технологическая блок-схема опытно-промышленной установки очистки абгазов окисления (Патент РФ № 2300412, 30.08.2005): 1 – нейтрализатор; 2 – каплеотбойник; 3 – абсорбционная колонна; 4 – «утка»; 5 – насос рецикла ПАБ; 6 – холодильник водяной; 7 – холодильник рассольный; 8 – сборник свежих ПАБ
Свеча
АБГАЗЫ очищенные
|
ПАБ |
|
|
3 |
свежий |
|
Обратная |
|
|
|
|
2 |
8 |
6 |
ВОДА |
|
|||
|
|
|
|
1 |
|
|
Прямая |
|
5 |
|
Обратный |
4 |
|
|
|
|
7 |
РАССОЛ |
|
АБГАЗЫ |
|
|
|
|
|
|
|
окисления |
|
|
Прямой |
|
|
|
|
ПАБ |
|
|
|
в производство кумола |
|
|
|
Рис. 8.4. Блок-схема опытно-промышленной установки очистки абгазов окисления (Патент РФ № 2300412, 30.08.2005) (обозначение цифр см. рис. 8.3)

244
Рис. 8.5. Фотография абсорбционной колонны промышленной установки очистки абгазов окисления от кумола и вредных примесей (Патент RU №230041230.08.2005)
Опытно-промышленные испытания на установке (рис. 8.3 или 8.4) проводили следующим образом. Промышленный поток абгазов окисления производства ГПК [35] через общий коллектор с объёмным расходом 8500 нм3/ч и компонентным составом – кумола до 5000 мг/м3, альдегидов до 500 мг/м3, фенола до 100мг/м3 и органических кислот до 5 мг/м3, кислорода до 6 об.%, азота до 94 об.% и Т < 10ºС – поступал в нейтрализатор 1 с 2% -ным раствором щёлочи и после предварительной очистки от вредных примесей абгазы распределителем газа (см. пунктирную окружность на рис. 8.4) барботировались через ПАБ кубовой части абсорбера 3, где постоянный уровень ПАБ поддерживали с помощью «утки» 4.
Частично очищенные из кубовой части абсорбера 3 от кумола абгазы проходили через три слоя насадки (кольца Палля), орошаемые распределителем ПАБ в верхней части абсорбера 3 (см. пунктирную окружность, рис. 8.4) встречным охлаждённым потоком ПАБ с расходом 12 м3/ч.
Извлечённый кумол вместе с ПАБ стекает с колец Палля в кубовую часть абсорбера 3, а очищенные абгазы от вредных примесей полностью и кумола до санитарных норм (не более 158 мг/м3) по выбросу на предприятии [34-36] после каплеотбойника (кольца Рашига) в верхней части абсорбера 3 сбрасываются через свечу в атмосферу. Кубовую жидкость абсорбера 3, насыщенные кумолом ПАБ через «утку» 4, насосом 5 циркулировали в верхнюю часть абсорбера 3 на орошение абгазов окисления, предварительно охлаждая водой в холодильнике 6 и рассолом в холодильнике
245
7. В зимнее время ПАБ с рецикла охлаждали только рассолом в холодильнике 7. Из ёмкости 8 рецикл ПАБ непрерывно подпитывали с объёмным расходом 1,5 м3/ч свежим ПАБ производства прекурсора [34] и такое же количество с рецикла насыщенные кумолом ПАБ непрерывно отводили с нагнетания насоса 5 на переработку в производство кумола [34].
В процессе испытаний по очистке абгазов окисления кумола на опытнопромышленной установке (рис. 8.3 и 8.4) проводили автоматический контроль со щита КИП и А температуры и расхода свежего и в рецикле ПАБ, его уровня в ёмкости 8, давление куба и температуру абсорбера 3, температуру и расход воды и рассола в холодильниках 6 и 7 и т.д., а такжепо метрологически аттестованным методикам анализа кумольного производства поликонденсационных мономеров [34-36] производили анализ содержания вредных органических примесей и кумола в абгазах окисления до и после очистки, а также кумола в ПАБ свежих, рецикле и ПАБ, передаваемых на переработку в производстве кумола [34]. Химический анализ вредных примесей (альдегидов, фенола и органических кислот) в абгазах окисления на входе и выходе абсорбера показал, что они на 100% и полностью очищаются в два этапа, так на первом 2%-ным раствором щелочи в нейтрализаторе 1 и ПАБ в абсорбере 3 (рис. 8.3 или 8.4). Испытания на опытно-промышленной установке проводили в течение года. Результаты анализа содержания кумола в абгазах окисления с расходом 8500 м3/ч, ПАБ рецикла с расходом 12 м3/ч и с подпиткой свежим ПАБ 1,5 м3/ч и отводом такого же количества насыщенного кумолом ПАБ на переработку в производство кумола [34], температура абсорбции кумола приведены в табл. 8.8.
Таблица 8.8 Содержание кумола в абгазах окисления и ПАБ рецикла при испытаниях
на опытно-промышленной установке
|
Температура |
Содержание кумола |
Степень извлечения |
Массовая доля |
|
№, |
абсорбции |
в абгазах окисления, мг/м3 |
кумола из абгазов |
кумола |
|
пп |
кумола, |
Исходных |
Очищенных |
окисления ПАБ, |
в ПАБ |
|
ºС |
% |
рецикла, % |
||
|
|
|
|||
1 |
20 |
3592 |
240 |
93,4 |
5,3 |
2 |
15 |
2640 |
189 |
92,8 |
1,4 |
3 |
10 |
4985 |
148 |
97,0 |
7,3 |
4 |
10 |
1845 |
151 |
91,8 |
2,5 |
5 |
10 |
3968 |
142 |
96,4 |
3,3 |
6 |
6 |
3007 |
128 |
95,7 |
6,4 |
7 |
5 |
1625 |
131 |
91,9 |
10,0 |
8 |
4 |
3387 |
125 |
96,3 |
5,7 |
9 |
3 |
2500 |
131 |
94,8 |
3,9 |
10 |
2 |
1792 |
118 |
93,4 |
10,0 |
11 |
1 |
4100 |
121 |
97,0 |
8,0 |
12 |
0 |
2180 |
112 |
94,9 |
4,2 |
13 |
-2 |
4560 |
95 |
97,9 |
15,0 |
14 |
-3 |
2706 |
108 |
96,0 |
6,2 |
15 |
-4 |
3552 |
121 |
96,6 |
13,3 |
246
16 |
-5 |
2650 |
90 |
96,6 |
9,3 |
17 |
-7 |
4576 |
34 |
99,3 |
22 |
При различном или случайном содержании кумола в абгазах окисления в широком температурном интервале абсорбции от -7 до 20ºС степень очистки абгазов окисления (извлечение кумола абсорбентом – ПАБ) довольно высокая 91,8-99,3 %. При этом имеется тенденция повышения эффективности очистки с уменьшением содержания кумола с 240 до 34 мг/м3 и с понижением температуры абсорбции от 20 до
-7ºС (табл. 8.8).
О процессе очистки абгазов окисления с извлечением кумола ПАБ свидетельствует и накопление кумола в рецикле ПАБ (табл. 8.8), от отсутствия кумола в свежих ПАБ до увеличения содержания кумола до 1,4-22 масс.%, поступающих с абсорбера 3 (рис. 8.3 или 8.4) на переработку в действующую схему кумольного производства поликонденсационных мономеров [34-36]. Испытания на опытнопромышленной установке (рис. 8.3 или 8.4) показали, что в летнее время при Т = 3040ºС реально достижимой низкой температурой в абсорбере 3 за счёт охлаждения рецикла ПАБ в водяном 6 и рассольном 7 холодильниках является диапазон температур от -2 до 0°С, а в зимнее время с использованием только рассольного холодильника 7 возможно достижение температуры абсорбции кумола и Т = -7ºС. В промышленных условиях эксплуатации установки (рис. 8.5) в диапазоне Т = -2÷10ºС содержание кумола в очищенных абгазах окисления не более 158 мг/м3 (табл. 8.8) и обеспечивает норму выброса кумола в атмосферу производства прекурсора – ГПК [35].
Весьма важным является вопрос переработки насыщенные кумолом ПАБ, выводимых из рецикла промышленной установки (рис. 8.3 или 8.4) в количестве 1,5 м3/ч. Установлено химическим и газохроматографическим методами анализа ПАБ с рецикла, что содержание альдегидов составляет до 10 мг/м3, фенола до 5 мг/м3 при отсутствии органических кислот, которые могут негативно повлиять на процесс алкилирования кумола и трансалкилирования ПАБ, окисления кумола, поскольку являются ингибиторами при синтезе ГПК [1а, 15-20]. Поэтому в качестве точки ввода насыщенного кумолом абсорбента ПАБ может быть выбран только узел нейтрализации производства кумола [34], где насыщенные кумолом ПАБ дополнительно очищаются от альдегидов и фенола. Далее, после извлечения кумола на стадии ректификации регенерированный абсорбент ПАБ возвращают на установку очистки абгазов окисления кумола (рис. 8.3 или 8.4), а извлечённый кумол используется по технологической цепочке в кумольном процессе производства поликонденсационных мономеров.
В период испытаний и эксплуатации промышленной установки очистки абгазов окисления (рис. 8.3 или 8.4) влияние вредных примесей альдегидов и фенола на процессы алкилирования и окисления кумола не обнаружено. Согласно акту приёмки опытно-промышленная установка (рис. 8.3) принята в эксплуатацию и переведена в разряд промышленной (рис. 8.5) с соответствующими внесёнными изменениями в технологические регламенты производства промежуточных прекурсоров [34, 35]. Продуктами запатентованной [261а] промышленной установки очистки абгазов окисления (рис. 8.5) являются очищенные абгазы окисления от вредных примесей полностью с содержанием кумола не более 158 мг/м3 и извлечённый кумол, используемый в кумольном производстве поликонденсационных мономеров [1а, 34-36].
247
Таким образом, в результате исследований разработана и внедрена в производство фенола и ацетона промышленная установка комплексной очистки абгазов окисления – полной от вредных примесей (альдегиды, органические кислоты, фенол и др.), а кумола рециклом ПАБ с возвратом в производство до санитарных норм кумола. При этом снижена ПДВ кумола в 53 раза, что позволило получить (период и цены 2004-2008 гг.) экономический эффект в размере 12,6 млн. руб., в том числе сэкономить платежи за выбросы кумола 1,6 млн руб.
8.2. Установка регенерации ацетона из отходов
Как было указано в аналитическом обзоре [1а], важным сегментом рынка ацетона является применение его в качестве растворителя синтеза полимерных пленкообразователей для производства широкого круга лакокрасочных композиций. К тому же, ацетон как растворитель используется для промывки трубопроводов и технологического оборудования при смене цветов в производстве органически разбавляемых лакокрасочных композиций или полимерных материалов, а также в технологических процессах окрасочного производства машиностроительных заводов для обезжиривания деталей или очистки инструментов. При этом на предприятиях скапливается значительное количество отработанного ацетона или ацетон содержащих отходов [48, 149]. С другой стороны, отработанные растворители или жидкие отходы, кроме ценного растворителя, в частности, ацетона, до 20-40% содержат ценные полимерные компоненты и наполнители, которые представляют коммерческий интерес для использования их в качестве бифункциональной добавки – одновременно пластификатора и наполнителя в производстве битумных мастик [1а, 148, 149].
В настоящее время проблема переработки и утилизации жидких органических отходов или отработанных растворителей, в частности, ацетона для повторного использования в полимерных лакокрасочных композициях является одним из актуальных вопросов для промышленных предприятий.
Данный раздел является сопутствующим основному содержанию работы и посвящён (кратко) разработке технологии и установки регенерации растворителей, в частности ацетона из некондиционных ацетон содержащих полупродуктов, жидких органических отходов или отработанных растворителей промышленных предприятий, производства и применения лакокрасочных композиций для энерго- и ресурсосбережения.
Одним из наиболее современных и эффективных методов переработки жидких отработанных органических отходов является регенерация растворителей на установках. Использование продуктов регенерации позволяет сэкономить значительные средства, поскольку регенерированный растворитель в режиме рецикла используется в технологических процессах производства и применения полимерных лакокрасочных композиций, резко сокращаются хранящиеся объёмы отработанных растворителей, повышается культура производства и улучшается общая экологическая ситуация. При этом растворители регенерируют методом простой дистилляции с последующим охлаждением периодическим способом [148, 149].
Задачей, на решение которой направлена предложенная полезная модель [262а], является разработка установки регенерации растворителей (ацетона), для осуществления непрерывной безотходной технологии разделения отработанных рас-
248
творителей на чистый регенерированный растворитель или смесь растворителей и жидкую транспортабельную кубовую жидкость с содержанием до 80-95% полимерных компонентов и наполнителей (твёрдых загрязнителей).
Техническим результатом использования полезной модели [262а] является совмещение технологических процессов непрерывного получения регенерированного растворителя или смеси растворителей для использования в режиме рецикла в производстве и применении полимерных лакокрасочных композиций, а кубовой жидкости с содержанием 90-95% полимерных компонентов и наполнителей в качестве бифункциональной добавки – пластификатора и наполнителя в производстве битумных мастик. На рис. 8.6 представлена технологическая блок-схема установки регенерации растворителей (вариант выполнения) и показана принципиальная схема рекуперации тепла дымового газа.
Основными технологическими параметрами работы установки регенерации растворителей (рис. 8.6) являются:
-скорость подачи 0,3-0,7 м3/ч насосом 6 осветлённого отработанного растворителя из отстойника 2 через вентиль 3 в подогреватель 7;
-температура кубовой жидкости испарителя 9 до Т = 2000С в зависимости от содержания в отработанном растворителе твёрдой фазы (полимерных компонентов и наполнителей) и органических жидкостей (ацетона), их компонентного состава и температуры кипения или фракционного состава;
-величина давления паров в испарителе 9 пределах 1-2 атм;
-оптимальный уровень кубовой жидкости в испарителе 9 по высоте «утки» 11 по смотровому стеклу 12.
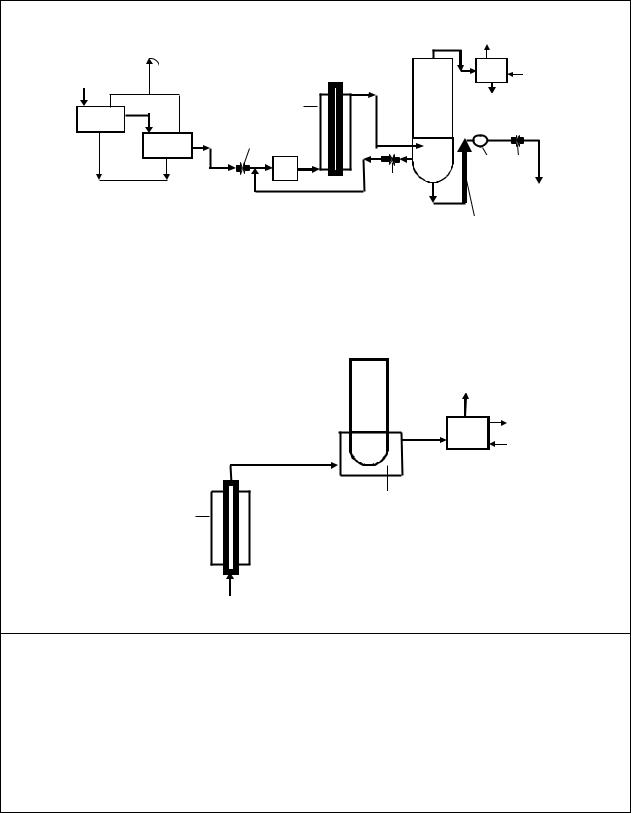
249
Отработанный |
Воздушная |
|
Холодная |
|
|
|
|
||
|
линия |
13 |
|
|
растворитель |
|
вода |
||
|
|
|
|
|
|
|
7 |
Регенерированный |
|
|
|
|
растворитель |
|
|
|
3 |
|
|
|
|
6 |
12 |
5 |
Зачистка в |
|
4 |
|
|
|
|
Кубовая |
||
производство |
|
|
||
|
|
жидкость |
||
битумных |
|
|
||
|
11 |
|
||
мастик |
|
|
|
|
|
|
|
|
Выбросы |
|
9 |
|
|
Горячая |
10 |
вода |
|
|
|
Холодная |
|
вода |
8
7
Горячий дымовой газ от горелки
Рис. 8.6. Блок-схема промышленной установки непрерывного процесса регенерации ацетона из отходов с получением бифункциональной добавки (пластификатор и наполнитель) в производстве битумных мастик (Патент РФ № 128508, 26.10.2012): 1, 2 – отстойники; 3, 4, 5 – вентили; 6 – насос с манометром; 7 – подогреватель; 8 – рубашка; 9 – испаритель; 10 – холодильник; 11 – «утка»; 12 – смотровое стекло; 13 – конденсатор (на рис. 8.6 не показаны автоматическая газовая горелка, её обвязка с термопарой кубовой части испарителя 9, заслонка регулировки дымового газа и изогнутый под углом 90° патрубок входа, приваренный на внутренней поверхности кубовой части испарителя 9, фильтр на выходе из отстойника 2)
Испытания показали эффективность предлагаемой установки регенерации растворителей для переработки в непрерывном режиме по безотходной технологии отработанных растворителей однокомпонентного и многокомпонентного состава или смесевых растворителей, содержащих 20-40% полимерных компонентов и наполнителей или твёрдых загрязнителей [262а]. Совмещение процесса разделения отработанного растворителя по непрерывной безотходной технологии на регенерированный
250
растворитель и подвижную транспортабельную кубовую жидкость позволяет в режиме рецикла использовать регенерированный растворитель в производстве полимерных лакокрасочных композиций. При этом кубовую жидкость и зачистки с отстойников, содержащие уже до 80-95% полимерных компонентов и наполнителей возможно использовать в качестве бифункциональной добавки – пластификатора и наполнителя в производстве битумных мастик; применение горячей и тёплой воды с конденсатора и холодильника для нужд производства позволило резко повысить экономические показатели предприятия. Установка регенерации ацетона (растворителей) (рис. 8.6) внедрено в производство лакокрасочных композиций.
8.3.Безотходная технология переработки сернокислотного маточника
Вразделе 5.3.1 и далее были определены «…оптимальные условия нейтрали-
зации растворов сернокислотного маточника газообразным аммиаком или аммиач-
ной водой…». При этом отмечалось, что после фазового разделения полимерной органики образуется очищенный насыщенный раствор сульфата аммония, содержащий примеси введённого специально алюмохлорида или солей алюминия. Поэтому во-
просы нейтрализации и кристаллизации (NH4)2SO4, выделение его из маточного раствора и превращение его в товарный продукт явились (в определённом смысле) дополнительным и необходимым исследованием [238а-244а].
Установлены оптимальные технологические условия нейтрализации растворов сернокислотных маточников производства ММА и ММА при получении товарного сульфата аммония, позволяющие предотвратить «старение» растворенного полимера или переход в твёрдое взвешенное состояние, кристаллизацию и влияние ионов алюминия на эти процессы [238а, 243а, 244а].
Реакция нейтрализации сернокислотного маточника производства (мет)акриловых мономеров газообразным аммиаком является экзотермическим процессом:
NH3 |
+ H2SO4 |
= NH4HSO4 + 39,44 ккал/моль |
(8.1) |
NH3 + NH4HSO4 = (NH4)2SO4 + 26,29 ккал/моль |
(8.2) |
||
2NH3 |
+ H2SO4 |
= (NH4)2SO4 + 65,73 ккал/моль |
(8.3) |
Поэтому температура нейтрализуемого раствора зависит от скорости подачи аммиака или от времени нейтрализации и поскольку рН раствора является регулируемым параметром, то существенную роль на агрегатное состояние растворимого полимера оказывает температура. Как говорилось выше (разделе 5.3.1) эксперименты проводились на стендовой установке непрерывного действия (рис. 5.11) и на опытной установке (рис. 5.12) с использованием нейтрализатора-смесителя, конструкции которого показана на рис. 8.7.
Растворенный в маточнике полимер в виде темной маслянистой плёнки всплывает на поверхность очищенного насыщенного раствора сульфата аммония, и при этом наблюдаются следующие особенности [238а], а именно, при:
-рН > 2 (Т = 40-60 С) цвет раствора изменяется от темнодо светлокоричневого;
-рН = 4-5,5 (Т = 80-92 С) выпадают кристаллы сульфата аммония белого цвета, а рабочий раствор светлеет до слегка соломенного, оставаясь прозрачным;