
3108 ЭИ
.pdf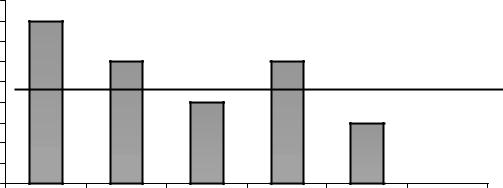
|
|
|
|
|
|
|
|
Таблица 3 |
|
|
Характеристика режимов работы и оценка значимости элементов в баллах |
||||||||
|
|
|
|
|
|
|
|
|
|
Элемент |
Режим |
Состав |
Структура |
Свойство |
Функион. |
Оценка |
Лимитир. |
||
работы |
нагружения |
нагружения |
нагружения |
влияние |
Оi |
|
элемент |
||
|
|
на систему |
|
||||||
|
|
|
|
|
|
|
|
|
|
1 |
|
непрерыв- |
сложный |
сосредото- |
стационар- |
непосред- |
8 |
|
V |
|
|
ный |
|
ченный |
ный |
ственное |
|
|
|
2 |
|
непрерыв- |
сложный |
распреде- |
периодичес- |
непосред- |
6 |
|
V |
|
|
ный |
|
ленный |
кое |
ственное |
|
|
|
3 |
|
импульсный |
простой |
распреде- |
случайное |
косвенное |
4 |
|
|
|
|
|
|
ленный |
|
|
|
|
|
4 |
|
непрерыв- |
сложный |
распреде- |
случайное |
непосред- |
6 |
|
V |
|
|
ный |
|
ленный |
|
ственное |
|
|
|
5 |
|
непрерыв- |
сложный |
распреде- |
случайное |
непосред- |
3 |
|
|
|
|
ный |
|
ленный |
|
ственное |
|
|
|
На рис. 3 приведена диаграмма для графического определения лимитирующих элементов по третьему признаку. После построения гистограммы в масштабе размерности вертикальной оси, на график наносится контрольная горизонтальная линия (пунктиром), соответствующая среднему значению показателя. Те элементы, столбцы гистограммы которых пересекаются с контрольной линией, считаются лимитирующими по рассматриваему признаку.
О, балл
9
8
7
6
5
4
3
2
1
0
элемент |
элемент |
элемент |
элемент |
элемент |
1 |
2 |
3 |
4 |
5 |
Рис. 3. Гистограмма значимости узлов
Определение двух–трех лимитирующих элементов с описанием предельных параметров или характеристик
Окончательный выбор лимитирующих узлов проводится по трем признакам в соответствии с попаданием в число лимитирующих по каждому из этих признаков (табл. 4).
11
|
|
|
|
|
Таблица 4 |
|
|
|
Выбор лимитирующих элементов |
||||
|
|
|
|
|
|
|
Элемент |
|
|
Признаки |
|
Лимитирующий элемент |
|
I |
|
II |
III |
|
||
|
|
|
|
|||
1 |
√ |
|
√ |
√ |
√ |
|
2 |
√ |
|
|
√ |
√ |
|
3 |
√ |
|
|
|
|
|
4 |
|
|
|
√ |
|
|
5 |
|
|
|
|
|
|
|
|
|
|
|
|
|
Далее необходимо привести предельные значения параметров или числовых характеристик лимитирующих элементов, по которым они могут быть забракованы для нормальной эксплуатации или их ресурс может быть исчерпан до наступления очередного планового ТОР.
РАЗРАБОТКА КАРТЫ НЕИСПРАВНОСТЕЙ
Для повышения эффективности контроля технического состояния локомотивов целесообразно разрабатывать карты неисправностей. Такая карта представляет собой чертеж (рисунок) узла или отдельных деталей, на котором стрелками указаны места появления неисправностей. В сопровождающей каждую стрелку надписи в верхней строке указывается характер неисправности, а под чертой – наиболее характерные признаки, по которым оперативно можно определить наличие данной неисправности при контроле локомотива ремонтным персоналом или локомотивными бригадами (см. рис. 4).
При составлении карт выбор признаков неисправностей и их рациональной совокупности определяется отрешением к повышению достоверности контроля и снижению вероятности ошибок 1-го рода (пропуск дефекта) и 2-го рода (ложная тревога). Возможность таких ошибок определяется, прежде всего, следующими обстоятельствами:
-трудность распознавания признака;
-незнание признака конкретным исполнителем, осуществляющим контроль (часто так: работник знал, но забыл и не использует в своей работе какой-то признак);
-небрежность и невнимательность исполнителя;
-связь одного признака с несколькими неисправностями.
Одним из путей повышения эффективности и достоверности контроля является увеличение числа признаков, которые рекомендуются исполнителям для обнаружения той или иной неисправности. Нетрудно показать, что с увеличением числа признаков ограниченно повышается вероятность обнаружения неисправности, и, следовательно, снижается вероятность ошибки 1-го рода.
12
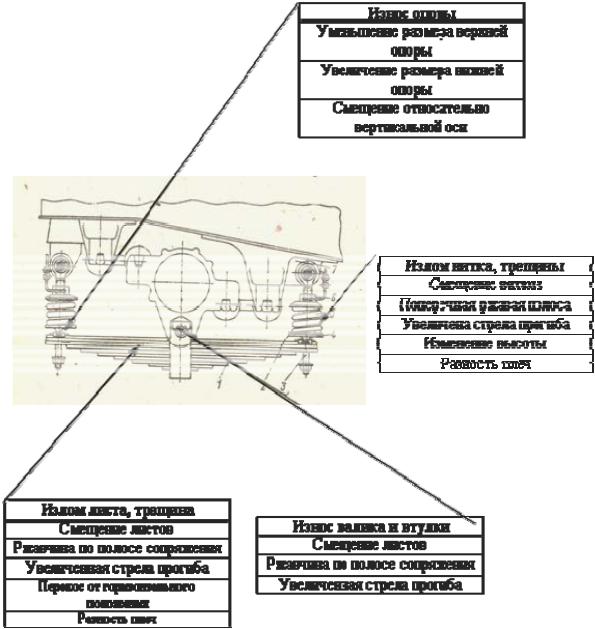
Однако, как показывает анализ вероятностных зависимостей для реальных значений вероятностей ошибок 1-го и 2-го рода, существенные изменения происходят при увеличении числа признаков до 3, 4..., а дальнейшее увеличение дает обычно незначительный эффект. Поэтому при составлении карт неисправностей необходимо стремиться, чтобы число признаков, соответствующих каждой неисправности, было, как правило, равно 3–4, а число блоков с признаками не менее 5.
На разработанной карте в тексте или в графической части отметить наиболее сложные неисправности в отношении влияния на нормальную эксплуатацию и их устранения в ремонте, присвоив номера в порядке убывания сложности, т. е. 1; 2; 3…, а также выделить элементы под замену, т. е. неремонтопригодные.
Рис. 4. Карта неисправностей рессорного подвешивания электровоза
13
СОСТАВЛЕНИЕ ТЕХНИЧЕСКОГО РЕГЛАМЕНТА ОБОРУДОВАНИЯ УЧАСТКА (ОТДЕЛЕНИЯ, ЦЕХА)
Технический регламент устанавливает требования к оснащенности цехов, отделений и участков депо основным специализированным нестандартизированным технологическим оборудованием и средствами диагностики.
Техническим регламентом следует руководствоваться при оценке технологической оснащенности ремонтных предприятий, а также при выполнении проектных работ по реконструкции и новому строительству.
Номенклатура и количество оборудования в регламенте указываются исходя из обеспечения безусловного комплексного выполнения технологических операций данного вида ремонта и в каждом конкретном случае определяются с учетом программы ремонта, производительности оборудования и особенностей организации ремонтного производства.
По своему составу документ выполняется в виде перечня, который представляет собой таблицу с указанием наименования технологических операций и основного оборудования, необходимого для их выполнения. Технологическое оборудование и средства диагностики группируются по производственным участкам.
Технический регламент является отраслевым руководящим документом. Студенты, исходя из разрабатываемого технологического процесса ремонта выбранного узла, составляют перечень необходимого оборудования, средств контроля и инструмента. Обозначения оборудования и изготовитель, при отсутствии точных данных, могут быть записаны условно с пояснением в тексте.
РАЗРАБОТКА КАРТЫ ТЕХНОЛОГИЧЕСКОГО ПРОЦЕССА
При разработке карты технологического процесса за основу берутся типовые технологические процессы с учетом достижений передового опыта ремонтного производства (Типовая технолого-нормировочная карта приведена в прил. 1).
Примерная форма карты технологического процесса приведена в табл. 5. Карта технологического процесса составляется по всему объекту ремонта
или на часть операций (согласовывается с преподователем).
Принимаемые технологические и организационные решения должны обеспечивать экономное высококачественное, быстрое и безопасное выполнение работ согласно требованиям существующих норм, правил и инструкций.
14
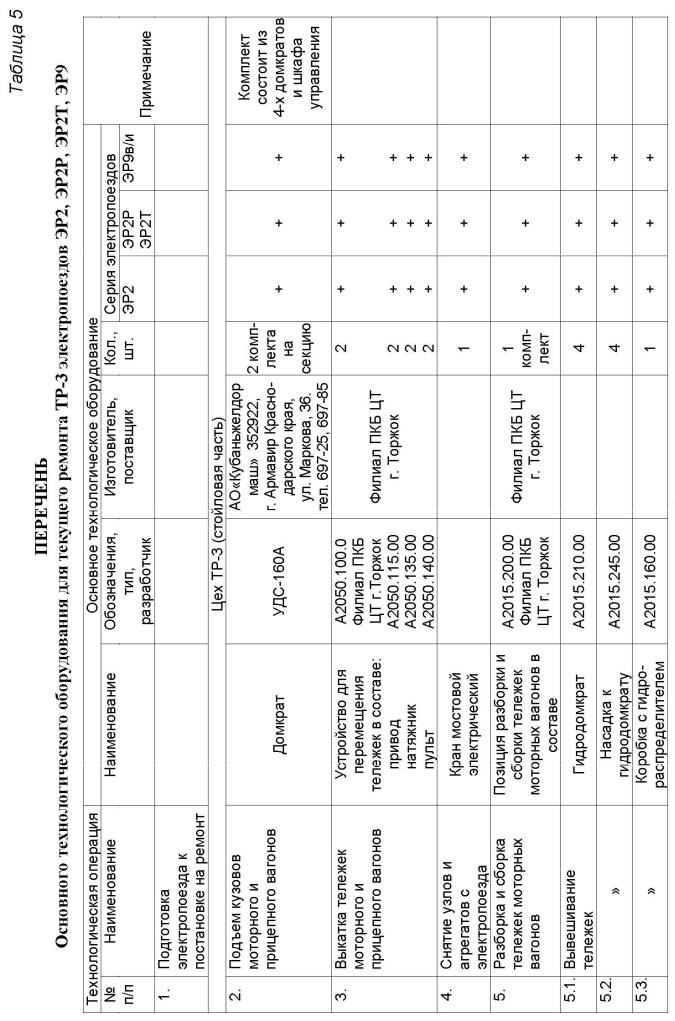
15
Текстовая часть карты технологического процесса излагается сжато и четко в повелительной форме. Внутри операций текст подразделяется на пункты. Профессия и разряд рабочих, норма времени устанавливаются по нормативным данным или данным ремонтного предприятия и корректируются в связи с применением прогрессивных решений, разработанных студентом в данном курсовом проекте. Карта технологического процесса должна разрабатываться с учетом предлагаемых устройств или технологии и содержать операции, которые выполняются с помощью комплекта оборудования и технологии. В завершении раздела рассчитывается общее технологическое время Тобщ и устанавливается вид производственного процесса основной или вспомогательный из условий:
Тр ≥ 0,5Тобщ; Тобщ = Тпз + Тки + Ттр + Тр,
где Тр – время выполнения ремонтных операций; Тпз – время подготовительно-заключительных операций; Ттр – время подъемно-транспортных операций; Тки – время контроля и испытаний.
Таблица 6
Карта технологического процесса
|
|
|
Основная |
|
|
|
№ |
Наименование |
Технологические |
технологическая |
|
Разряд |
|
п/п |
операции |
условия, |
оснастка, |
Исполнитель |
работы |
Время |
|
|
правила, ГОСТ |
приспособления, |
|
|
|
|
|
|
инструмент |
|
|
|
|
|
|
|
|
|
|
1 |
2 |
3 |
4 |
5 |
6 |
7 |
|
|
|
|
|
|
|
РАЗРАБОТКА МОДЕЛИ ОТКАЗОВ
Модель отказов предназначена для структурного вероятностного анализа отказов узлов (элементов) электроподвижного состава с целью оперативного принятия мер по повышению их надежности.
Студенты на основе классификации отказов определяют пути возникновения, устанавливают основные причины и первопричины их появления, разрабатывают организационные и технологические меры по снижению и устранению отказов в эксплуатации.
Модель отказов представляет собой многоуровневую вероятностную структуру с использованием логических элементов анализа:
16
первый уровень: наименование объекта (узла);
второй уровень: условное разделение узла на отдельные элементы;
третий уровень: характерные для каждой детали неисправности и отказы, возникающие в процессе эксплуатации;
четвертый уровень: причины возникновения отказов;
пятый уровень: первопричины возникновения отказов.
При построении модели отказов учитывается вероятность возникновения отказов и их причины.
На модели отказов определяются пути возникновения отказов по величине общей вероятности отказа. Вероятность возникновения данного отказа при указанных причинах вычисляется по формуле:
Р = Р1 × Р2 × Р3 × Р4,
где Р1 – вероятность отказа отдельной элемента узла; Р2 – вероятность возникновения отдельного вида отказа; Р3 – вероятность возникновения причины отказа;
Р4 – вероятность возникновения первопричины отказа.
Критический путь – определяется по наибольшей расчетной вероятности возникновения отказов.
Подконтрольный путь – соответствует второй по величине вероятности. Путь устойчивой работы – соответствует наименьшей расчетной
вероятности на модели отказов.
Модель отказов лимитирующего узла изображается на листе 2 графической. Модель строится на основе выявления лимитирующих элементов, карты неисправностей и наблюдений за объектом ремонта во время практики и лабораторных занятий. Критический и другие пути на модели выделяются разным цветом.
В качестве результата решения модели отказов на критическом и подконтрольном пути разрабатываются оперативные меры по сокращению отказов и контролю технического состояния лимитирующих элементов узла (привести 3÷5 мероприятий).
ТЕХНИКО-ЭКОНОМИЧЕСКОЕ ОБОСНОВАНИЕ ПРИНЯТОГО ТЕХНОЛОГИЧЕСКОГО ПРОЦЕССА
При оценке годового экономического эффекта целесообразно основываться на типовом расчете, принятом на ж.д. транспорте.
Годовой экономический эффект (Пг) в результате внедрения разработанного (модернизированного) оборудования определяется по формуле, руб.:
17

Пг = Эг – Ним – Нпр, , |
(1) |
где Эг – экономия годовых эксплуатационных расходов железной дороги (локомотивного депо) при внедрении нового устройства по сравнению со «старой» технологией, руб.;
Ним. – прирост налога на имущество в результате внедрения новой техники; Нпр. – налог на прибыль, формирующуюся в результате экономии
эксплуатационных расходов при внедрении нового устройства, руб.
Эг = Э1 – Э2 – А.о., |
(2) |
где Э1 – затраты на обслуживание при «старой» технологии ремонта; Э2 – затраты на обслуживание при внедрении новой технологии;
А.о. – годовые амортизационные отчисления на полное восстановление нового устройства (определяется отношением стоимости изготовления Эиз к сроку эксплуатации Тэ).
Э1 = Спб + Ср + Снп + Сзч+ Сор + Сзам, |
(3) |
где Спб – затраты на плановый ремонт оборудования; Ср – затраты на плановый ремонт выбранного узла; Сзч – стоимость запасных частей;
Снп – затраты на неплановый ремонт (условно принимаются на 10 % меньше предыдущего отчетного периода);
Сор – стоимость остановки на перегоне при отказе выбранного узла (и отсутствии резервирования могут приниматься усредненными на определенный период для конкретного полигона эксплуатации);
Сзам – затраты на замену вышедшего из строя оборудования.
Э2 = Спб + Ср + Снп + Сзч+ Сор + Сзам. |
(4) |
При определении экономического эффекта от внедрения оборудования для конкретных условий эксплуатации расчетные показатели эксплуатационных расходов, содержащиеся в формулах (2), (4) определяются на основании фактических затрат (по данным бухгалтерии) в ценах отчетного периода.
Срок окупаемости определяется соотношением, год:
Эиз |
|
|
Ток = Пг |
, |
(5) |
где Эиз – затраты на внедрение нового устройства или новой технологии. Эффективным в данной работе можно условно считать внедряемое
оборудование, срок окупаемости которого не превышает три года.
18
ТРЕБОВАНИЯ ОХРАНЫ ТРУДА И ТЕХНИКИ БЕЗОПАСНОСТИ
Студент должен изучить и в общем виде ответить на следующие вопросы данного раздела:
1.Общие требования безопасности;
2.Требования безопасности перед началом работы;
3.Требования безопасности во время работы:
-требования электробезопасности;
-требования безопасности при подаче и снятии напряжения в контактной сети депо, пунктов технического обслуживания и экипировки локомотивов (по необходимости);
-требования безопасности при выполнении отдельных операций ремонта
итехнического обслуживания ЭПС;
-требования безопасности при использовании инструмента или других приспособлений;
4.Требования безопасности в аварийных ситуациях;
5.Требования безопасности после окончания работы.
При ответе на данные вопросы необходимо учитывать разрабатываемую студентом технологию и устройства, увязывая с местом выполнения работ (участок, отделение, цех).
ЗАКЛЮЧЕНИЕ
В заключении должны быть представлены полученные в разделах результаты и по ним итоговые выводы.
19
Библиографический список
1.Правила текущего ремонта и технического обслуживания электровозов постоянного тока / МПС РФ. – М.:Транспорт, 2000. – 328 с.
2.Сборник типовых технически обоснованных норм времени на слесарные работы при техническом обслуживании и текущем ремонте электровозов ВЛ 10 / МПС РФ. – М.: Транспорт, 1996. – 560 с.
3.ГОСТ 23605-79. Надежность в технике. Статистическая оценка нагруженности машин и механизмов. Методы типизации режимов нагружения; введен 01.01.80. – М.: Издательство стандартов, 1979. – 16 с.
4.Находкин В.М. Технология ремонта тягового подвижного состава / В.М. Находкин, Р.Г. Черепашенец. – М.: Маршрут, 2005. – 461 с.
5.Нормативы затрат рабочей силы (трудоемкости) на техническое обслуживание ТО-3 и текущий ремонт тягового подвижного состава / МПС РФ. –
М.: Транспорт,1996. – 40 с.
6.Типовые нормы времени на слесарные работы по ремонту электрических машин / МПС РФ. – М.: Транспорт, 1995. – 50 с.
7.Типовая инструкция по охране труда для слесарей по ремонту электроподвижного состава ЦТ-535. – М.: Нейроком-Электротранс, 1998. – 29 с.
8.Петропавлов Ю.П. Технология ремонта ЭПС. – М.: Маршрут, 2006. – 432 с.
9.Добровольская Э.М. Устройство и ремонт электропоездов. – М.: ИКЦ
«Академкнига», 2005. – 455 с.
20