
Машстройлекции_зубч
.pdf
Делительный диаметр колеса |
d2 |
d2= m z2 |
|
|
|
Диаметр вершин зубьев колеса |
da2 |
da2=d2+2 ha |
Диаметр впадин колеса |
d f2 |
df2= d2-2 hf |
Длина ступицы колеса |
LCT2 |
LCT2=1,5 Dв2 |
Наружный диаметр ступицы |
Dст2 |
Dст2=1,6 Dв2 |
колеса |
|
|
|
|
|
Диаметр вала колеса (уступ) |
2 |
D2=1,2 Dв2 |
|
D |
|
Ширина зубчатого венца |
b |
b= 6…7 m |
|
|
|
Толщина обода зубчатого |
δ 1 |
δ 1=2,25m |
венца |
|
|
|
|
|
Толщина диска |
δ 2 |
δ 2=⅓ b |
|
|
|
Межосевое расстояние |
a |
а=0,5(d 1+ d |
|
2) |
|
|
|
Рис 14. Пример оформления чертежа ”Зацепление зубчатое” (Основную надпись по возможности выполнить поГОСТу)
Вычерчивание начинают с проведения штрихпунктирных линий, касательных одна к другой делительных окружностей. Затем проводят окружности вершин, которые очерчивают сплошными основными линиями (в том числе и в зоне зацепления). Сплошными тонкими линиями проводят окружности впадин. При этом между окружностями
вершин колеса и впадин шестерни (и наоборот) остаются радиальные зазоры, равные 0,25m (рис.12) . Показывают шпоночные канавки и шпонки. Проводят другие линии, определяемые конструкцией колес и валов. Вычерчивают валы.
При выполнении фронтального разреза зуб шестерни в месте зацепления показы вают
линиями видимого контура (рис.12), считая его расположенным впереди. Дно впадины колеса проводят сплошной основной линией, а контур зуба колеса в месте зацепления
11
проводят штриховой линией. Валы и шпонки, когда секущая плоскость проходит вдоль
них, не рассекают и не заштриховывают.
ТЕМА 2
ШПОНОЧНЫЕ СОЕДИНЕНИЯ
Общие сведения
Шпоночное соединение предназначено для передачи крутящего момента от одной из двух соприкасающихся деталей к другой, чаще всего от вала к расположенным на нем деталям, например шкивам, зубчатым колесам, маховикам, кулачкам, полумуфтам, рычагам и др. Эти соединения применяют в тех случаях, когда к точности центри рования соединяемых деталей не предъявляются особые требования.
Шпоночные соединения могут обеспечивать неподвижное или подвижное вдоль оси соединение деталей.
По форме шпонки разделяются на призматические, клиновые, сегментные и тангенциальные.
Форма и размеры сечений шпонок и пазов стандартизованы и выбираются в зависимости от диаметра вaлa, а вид шпоночного соединения определяется условиями работы соединяемых деталей.
На продольных разрезах шпоночных соединений шпонки всех типов условно изображают нерассеченными.
Материалом для изготовления шпонок служит сталь для шпонок по ГОСТ 8786—68* с временным сопротивлением разрыву не менее 590 МПа.
Соединения с призматическими шпонками
Наибольшее распространение имеют призматические шпонки (рис. 15), которые, располагаясь в пазу вала, несколько выступают из него и входят в паз, выполненный во втулке (ступице) детали, соединяемой с валом. Передача вращения от вала к втулке (или наоборот) производится рабочими боковыми гранями шпонки.
После сборки шпоночного соединения (рис. 16) между пазом втулки и верхней гранью шпонки должен быть небольшой зазор, который получается благодаря выбору размеров соединения по ГОСТ 23360—78* ( СТ СЭВ 189—79) и ГОСТ 10748—79* (СТ СЭВ 5615—86) в зависимости от диаметра вала.
Условное обозначение призматических шпонок состоит из : 1. слова «Шпонка»;
2. обозначения исполнения (исполнение 1 не указывают); 3. размеров сеч ения b x h и длины l шпонки;
4. обозначения стандарта . Примеры условных обозначений:
1. Призматическая шпонка исполнения 1 с размерами
b=14 мм, h= 9 мм, l= 80 мм : Шпонка 14x9x80 ГОСТ 23360 —78. 2. То же исполнения 2 :Шпонка 2 — 14x9x80 ГОСТ 23360 —78.
12

Рис.15 Элементы шпоночного соединения
Рис.16 Размеры призматических шпонок и шпоночных пазов ГОСТ 23360-78* (мм) а - вал, шпонка, главный вид и вид слева, втулка; б- вал; в- втулка.
Размеры призматических шпонок и шпоночных пазов выбираются в зависимости от диаметра вала d ( Табл.2).
Табл.2
13
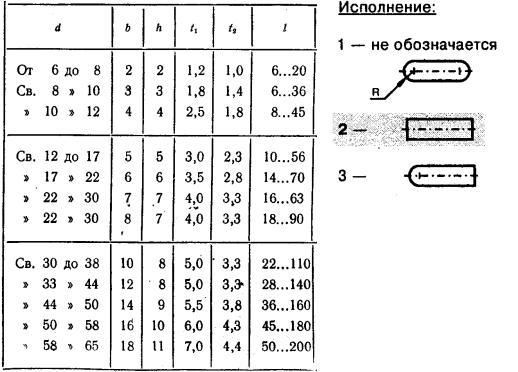
Рис.17 Исполнение шпонок (вид сверху на шпонку)
Длины шпонок следует выбирать из ряда: 6; 8; 10; 12; 14; 16; 18; 20; 22; 25; 28;
32; 36; 40; 45; 50; 56; 63; 70; 80; 90; 100; 110; 125; 140; 160; 180; 200; 220; 250; 280;
320; 360; 400; 450; 500 мм.
Призматические шпонки с креплением на валу по ГОСТ 8790-79
Призматические направляющие шпонки с креплением на валу также имеют три исполнения (рис.18). Шпонки закрепляются в пазах вала винтами, для отжима шпонки при демонтаже служит резьбовое отверстие.
Размеры сечений шпоночных пазов для шпонок с крепежными отверстиями соответствуют размерам для обыкновенных призматических шпонок, приведенным в ГОСТ 8790-79.
14

Рис.18 Соединение c призматической направляющей шпонкой по ГОСТ 8790-79 с креплением на валу
Примеры условных обозначений:
1. Призматическая направляющая шпонка исполнения 1, с размерами b = 14 мм, h = 9 мм, l = 120 мм; Шпонка 14х9x120 ГОСТ 8790—79.
2. То же исполнения 3: Шпонка 3 — 14x9x120 ГОСТ 8790—79.
15

Соединения с клиновыми шпонками по ГОСТ 24068-80
Клиновые шпонки (рис.19) находят применение, в основном; в тихоходных передачах, не требующих точного центрирования деталей на валу.
Форма клиновой шпонки — четырехгранная призма, у которой верхняя широкая грань имеет уклон 1 : 100. Нижняя широкая грань уклона не имеет.
Клиновая шпонка устанавливается в пазы вала и втулки с боковыми зазорами, причем верхняя грань паза втулки имеет такой же уклон, как грань шпонки.
Рис.19 Соединение с клиновой шпонкой по ГОСТ 24068-80
Соединения с сегментными шпонками по ГОСТ 24071-97
Сегментные шпонки (рис.20) по назначению аналогичны призматическим шпонкам и применяются при коротких ступицах колес. Шпонки выполняют в виде сегмента, что обеспечивает технологичность изготовления шпоночного паза на валу путем фрезерования дисковой фрезой, а также удобство сборки шпоночного соединения. Относительно большая глубина шпоночного паза уменьшает прочность вала, поэтому сегментные шпонки применяют для передачи небольших крутящих моментов или только лишь для фиксации элементов шпоночного соединения.
ГОСТ 24071—80* (СТ СЭВ 647—77) устанавливает два исполнения сегментных шпонок (рис.20). Размеры сечений сегментных шпонок и пазов, а также их диаметры выбираются в
зависимости от диаметра d вала.
16

Рис.20 Соединение с сегментной шпонкой
Соединения с тангенциальными шпонками
Тангенциальные шпонки (рис.21) — нормальная по ГОСТ 24069—80* (СТ СЭВ 646—77) и усиленная по ГОСТ 24070—80* (СТ СЗВ 646—77) — состоят из двух односкосных клиньев прямоугольного сечения с уклоном 1: 100. Паз втулки под эти шпонки выполняют с таким же уклоном, а паз вала уклона не имеет.
Тангенциальные шпонки применяют при передаче больших знакопеременных крутящих моментов; при этом устанавливают две шпонки под углом 120° относительно друг друга. Шпонки в соединении устанавливают так, чтобы широкая грань была направлена по касательной к валу, а одна из узких граней — по радиусу вала. В шпоночных соединениях, работающих с повышенными ударными нагрузками или с частым изменением направ ления вращения, необходимо применять шпонку большего сечения — усиленную.
Положение шпонок друг относительно друга после сборки должно быть зафиксировано с помощью штифта или другим способом.
Рис.21 Соединение с тангенциальными шпонками по ГОСТ 24069-97
и ГОСТ 24070-97

Нанесение размеров и предельных отклонений на чертежах шпоночных соединений
На чертежах деталей шпоночных соединений с призматическими шпонками следует наносить следующие размеры:
1.длину l1 шпоночного паза (рис.22), которую принимают на 0,5—1,0 мм больше длины шпонки;
2.ширину b шпоночного паза вала и ступицы;
3.глубину пазов:
на валу — размер d-t1, (рис. 22)
вступице — размер d+t2,(рис. 23);
4.диаметры вала и отверстия ступицы.
Кроме того, допускается наносить в качестве справочного размера радиус закругления паза (для выбора радиуса фрезы), а радиус сопряжения дна паза с боковыми гранями указывают только для ответственных шпоночных соединений.
Пазы не доводят до торца вала (рис.22) на расстояние k = 3 ... 5 мм при d ≤ 30 мм и k = 5 ...
7 мм при d ≥ 30 мм.
Рис.22 Нанесение размеров шпоночного паза на валу
Рис.23 Нанесение размеров шпоночного паза на втулке (на ступице колеса)
18
При наличии на ступенчатом валу нескольких шпоночных пазов их рекомендуется располагать в различных плоскостях.
Предельные отклонения размеров указывают непосредственно после номинальных размеров в соответствии с правилами по ГОСТ 2,307—68* (СТ СЭВ 1976—79, СТ СЭВ 2180—80).
Допуски симметричности и параллельности расположения шпоночного паза относительно осей цилиндрических поверхностей вала (рис.22) и отверстия ступицы (рис.23) указывают в соответствии с ГОСТ 2.308—79*(СТ СЭВ 368—76).
Шероховатость поверхностей выбирается в зависимости от полей допусков размеров шпоночного соединения.
Чертежи клиновых, сегментных и тангенциальных шпоночных соединений выполняются так же, как чертежи призматических шпоночных соединений, с учетом кон структивных особенностей шпонок каждого вида.
ТЕМА 3
ШЕРОХОВАТОСТЬ ПОВЕРХНОСТИ
Параметры шероховатости
Шероховатость поверхностей является одной из основных геометрических характеристик качества поверхностей деталей и оказывает весьма существенное влияние на эксплуатационные показатели. Термины и определения шероховатости поверхностей установлены ГОСТ 25142—82 ( СТ СЭВ 1156—78), параметры и характеристики ГОСТ 2789— 73* (СТ СЭВ 638—77). Последний введен в действие в январе 1981 г.; при этом была изменена терминология, упразднены классы шероховатости, введены новые таблицы.
Шероховатость поверхности — совокупность неровностей поверхности с
относительно малыми шагами на базовой длине.
Шероховатость поверхностей оценивается по неровностям профиля (чаще поперечного) путем сечения реальной поверхности плоскостью (в основном, в поперечном сечении).
Шероховатость рассматривают в пределах ограниченного участка (рис. 24), длина l которого называется базовой длиной. База для отсчета отклонений профиля — средняя линия т профиля. В соответствии с ГОСТ 2789—73* (СТ СЭВ 638—77) приняты шесть параметров шероховатости: три высотных
( Ra, Rz, Rmax ), два шаговых (Sm, S ) и параметр относительной опорной длины профиля (tp).
Ra — среднее арифметическое отклонение профиля, мкм;
Rz — высота неровностей профиля по десяти точкам, мкм;
Rmax — наибольшая высота неровностей профиля, мкм;
Sm — средний шаг неровностей, мм;
S — средний шаг неровностей по вершинам, мм;
tp — относительная опорная длина профиля, %, где р -числовое значение уровня сечения профиля.
Под шероховатостью поверхности понимают совокупность неровностей на базовой длине l, образующих рельеф поверхности. Пример профиля неровностей поверхности с обозначением параметров шероховатости поверхности приведен на рис. 24.
Базовая длина l — длина базовой линии, на которой выделяются неровности,
19

характеризующие шероховатость поверхности, используемая для количественного определения ее параметров.
Среднее арифметическое отклонение профиля Ra — среднее арифметическое абсолютных значений отклонений профиля профиля в пределах базовой длины l .
Высота неровностей профиля по десяти точкам Rz — среднее расстояние между пятью высшими точками выступов Н i max и пятью низшими точками впадин H i min в пределах базовой длины l.
Шероховатость поверхности классифицируется по числовым значениям параметров Ra и Rz вместо классов шероховатости, применявшихся в технической документации до 1980 г. В ГОСТ 2789-73 ( СТ СЭВ 638-77).
Имеется таблица для перевода обозначений шероховатости поверхности с помощью классов на обозначения по параметрам Ra и Rz (рис.24).
Рис.24 Пример профиля неровностей поверхности с обозначением параметров шероховатости поверхности
m - средняя линия профиля, l-базовая длина.
Обозначения шероховатости поверхностей
Шероховатость поверхности обозначают на чертежах в соответствии с
ГОСТ 2.309—73* (СТ СЭВ 1632—79).
Этим стандартом предусмотрены и правила нанесения обозначений на чертежах изделий всех отраслей промышленности.
Шероховатость поверхности должна быть обозначена на чертеже для всех выполняемых по данному чертежу поверхностей изделия, кроме тех из них, для которых нормирование требований к шероховатости не обусловлено требованиями конструкции.
Структура обозначения шероховатости поверхности приведена на рис.25.
Полку знака чертят, когда в обозначении шероховатости имеются кроме параметра дополнительные данные.
В обозначении шероховатости следует применять один из знаков, изображенных на рис.26.
Выполняют знаки сплошной тонкой линией, толщина которой приблизительно равна половине толщины сплошной основной линии, применяемой на чертеже. Высота h должна быть приблизительно равна применяемой на чертеже высоте цифр размерных чисел (5 мм). Высота Н равна (1,5 ... 3) h т.е. 7мм.
20