
[SHipinsky_V.G.]_Oborudovanie_i_osnastka_upakovoch2(z-lib.org)
.pdf
(вместимостью до 0,5 дм3) производительность применяемого в агрегате экструдера настолько высока, что время выдачи из него заготовки оказывается гораздо меньшим допустимой продолжительности ее экструдирования τЭ, определяемой по формуле (12.2), и тем более времени охлаждения изделия в раздувной форме. Следовательно, непрерывно работающий экструдер способен в таких агрегатах последовательно обслуживать несколько раздувных форм, обеспечивая тем самым более высокую производительность. Этот принцип работы, в частности, реализуется в карусельных многопозиционных экструзионно-раздувных автоматах, содержащих на периодически вращающемся столе несколько установленных с одинаковым шагом раздувных форм. При этом на первой позиции карусельного стола 1 (рис.12.9а) осуществляется выдача заготовки 2 экструдером 3 через головку 4 в раздувную форму 5 и ее смыкание. После же поворота стола на заданный шаг на второй его позиции производится раздув изделия в сомкнутой форме 6 из ранее экструдированной заготовки, а на третьей промежуточной позиции в это время уже изготовленное изделие продолжает охлаждаться в форме 7. На четвертой позиции карусельного стола очередная форма 8 в это время размыкается и из нее удаляется готовое изделие, а затем осуществляется очередной поворот карусельного стола 1 и далее все операции процесса повторяются на всех позициях одновременно в следующем технологическом цикле. Время же выстоя карусельного стола и соответственно продолжительность цикла изготовления очередного изделия определяются наиболее продолжительной операцией, которая обычно заключается в выдаче заготовки экструдером в раздувную форму и смыкании формы на первой позиции.
Рис. 12.9. Схемы исполнения экструзионно-раздувных агрегатов
При изготовлении изделий средних размеров (вместимостью до 5 дм3) время τЭ выдачи экструдером более объемных заготовок существенно возрастает и в результате становится соизмеримым с суммарным временем всех последующих стадий технологического цикла. Поэтому для изготовления таких изделий целесообразно применять одноили двухпозиционные экструзионнораздувные агрегаты соответственно с одной стационарной или двумя возвратно-поступательно перемещающимися раздувными формами. При этом в более производительных двухпозиционных агрегатах (рис.12.9б) пока на первой позиции в раскрытую раздувную форму 1 из экструдера 2 через головку
81
3 выдается трубчатая заготовка 4 и осуществляется смыкание формы, в это время на второй позиции производится раздув изделия в сомкнутой форме 5 из ранее экструдированной заготовки, а также его охлаждение и удаление из размыкающейся формы. Затем формы подающим механизмом 6 поступательно перемещаются на шаг так, чтобы разомкнутая форма 5 стала соосно с экструзионной готовкой 3 и цикл повторяется. При использовании многоручьевой экструзионной головки 3, выдающей одновременно несколько трубчатых заготовок 4 в многоместную раздувную форму 1, на таких агрегатах можно изготовлять в одном цикле и по нескольку малогабаритных изделий. Применяются также экструзионно-раздувные агрегаты, в которых для увеличения скорости выдавливания заготовки на одну формующую головку одновременно работают два одночервячных экструдера.
При изготовлении крупногабаритной тары (вместимостью более 5 дм3) скорость выдачи заготовки большой длины должна быть высокой, что следует из формулы (12.1). Кроме этого такая заготовка по мере выхода из головки экструдера с недостаточно высокой скоростью склонна вытягиваться в верхней более пластичной части под воздействием собственного веса, что вызывает уменьшение площади ее поперечного сечения и соответственно разнотолщинность стенок у изготовляемого изделия. Поскольку даже высокопроизводительные экструдеры не обеспечивают необходимую скорость выдачи больших заготовок, то экструзионно-раздувные агрегаты, предназначенные для изготовления крупногабаритных изделий, выполняются со специальным аккумулирующим устройством 1 (рис.12.9в), которое накапливает требуемый объем пластифицируемого экструдером 2 материала, а затем поршнем, перемещаемым от гидроцилиндра 3, выдавливает его с высокой скоростью через формующий канал головки 4, выдающей трубчатую заготовку 5 в разомкнутую форму 6. В таких агрегатах время заполнения аккумулятора (копильника) 1 пластифицированным материалом из экструдера 2 соизмеримо с суммарным временем всех последующих стадий технологического цикла, поэтому изготовляются они, как правило, однопозиционными. Объемную же скорость V потока пластифицированного материала, выдавливаемого поршнем копильника из формующего канала экструзионной головки, можно рассчитать по следующей формуле:
|
p d |
|
|
|
2 |
V |
12 |
l |
|
, см3/с
(12.5)
где p – давление, создаваемое поршнем в пластифицированном материале до его выхода из отверстия головки, кгс/см2;
d, δ и l – средний диаметр, ширина и длина формующего канала головки соответственно, см;
µ– динамическая вязкость пластифицированного материала, (дин∙с)/см2.
Вэкструзионно-раздувных агрегатах аккумулирующее устройство
(копильник) может располагаться вертикально, наклонно или горизонтально. При наклонном или горизонтальном расположении копильника он обычно закрепляется вместе с экструдером на общей станине. Недостатком же такой компоновки является то, что выдавливаемому из копильника потоку расплава в экструзионной головке создается повышенное сопротивление, из-за изменения
82

направления движения на вертикальное. Вследствие этого наибольшее распространение получили агрегаты различных мощностей с вертикальным расположением копильника. В них гранулированный материал захватывается из бункера 1 (рис.12.10) червяком 2 экструдера и перемещается вдоль нагретых стенок материального цилиндра 3. При этом гранулы сжимаются, а затем материал пластифицируется, интенсивно перемешивается и гомогенизируется в однородный расплав, продавливаемый через соединительный канал в копильник 4, обогреваемый кольцевыми электронагревательными элементами сопротивления (ТЭНами) 5. Под давлением подаваемого и накапливающегося расплава плунжер 6 копильника постепенно перемещается вверх вместе с присоединенным к нему через шток 7 поршнем 8 гидроцилиндра 9. В этот период поршневая полость гидроцилиндра соединяется со сливной магистралью через подпорный клапан, создающий в ней противодавление, которое способствует уплотнению расплава в копильнике и удалению из него воздуха.
Рис. 12.10. Функциональная схема вертикального экструзионно-раздувного агрегата с копильником
При накоплении требуемого объема расплава закрепленный на штоке 7 кулачок 10, положение которого регулируется, воздействует на конечный выключатель 11, подающий команду в систему управления на переключение гидроцилиндра 9 в режим рабочего хода. При этом его поршень 8 ускоренно перемещает вниз плунжер 6, а он в свою очередь выдавливает с высокой скоростью из полости копильника накопленную дозу пластифицированного материала в головку 12, формующую из него в своем кольцевом канале очередную трубчатую заготовку 13. Червяк же 2 экструдера в этот период
83
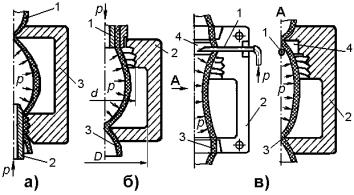
продолжает вращаться, предотвращая обратное выдавливание расплава из копильника. В конце хода плунжера 6 выдавливаемая заготовка 13 находит своим нижним торцом на ниппель 14 и в этот момент срабатывающими гидроцилиндрами 15 сводятся плиты 16 с полуформами 17. В результате раздувная форма смыкается и с усилием, развиваемым гидроцилиндрами 15, запирается. При этом на ниппеле 14 сопрягающимися поверхностями полуформ формируется наружная поверхность горловины изготовляемой тары, а верх трубчатой заготовки пережимается торцами (пресс-кантами) формы и сваривается. Далее срабатывает пневмоклапан, открывающий магистраль подачи через ниппель 14 в заготовку сжатого воздуха, раздувающего ее в изделие, плотно прижимаемое к стенкам полости формы. После выдержки времени, необходимого для охлаждения материала до достижения механической прочности, пневмоклапан выключается, перекрывая при этом магистраль сжатого воздуха и соединяя канал ниппеля 14 с атмосферой. Затем обратным ходом штоков гидроцилиндров 15 плиты 16 разводятся вместе с полуформами 17, и изготовленная тара удаляется из разомкнутой формы. Одновременно приводимым в действие ножом 18 с торца экструзионной головки 12 срезается и удаляется остывший пережатый конец заготовки 13. Непрерывно вращающийся червяк 2 экструдера за это время заполняет копильник 4 новой порцией пластифицированного материала и далее цикл повторяется. С целью повышения производительности экструзионно-раздувные агрегаты, предназначенные для изготовления пластмассовой тары большой массы и вместимости (более 0,5 м3), могут выполняться с копильником, который наполняют два и более одновременно работающих одночервячных экструдера.
Рис. 12.11. Способы раздува трубчатой заготовки в форме
При формовании изделия применяется три способа раздува экструдируемой трубчатой заготовки в форме: подачей сжатого воздуха через ниппель, расположенный снизу заготовки (рис.12.11а); подачей сжатого воздуха через дорн экструзионной головки (рис.12.11б) и подачей сжатого воздуха через раздувную иглу, прокалывающую заготовку при смыкании формы (рис.12.11в). Выбор же способа раздува зависит в основном от конфигурации и назначения изготовляемого изделия.
Время полного цикла τц изготовления изделия в экструзионно-раздувном агрегате рассчитывается по формуле:
Ц В С Р О Раз И , с |
(12.6) |
84

где τВ – длительность процесса выдачи заготовки; τС – длительность процесса смыкания формы; τР – длительность процесса раздува заготовки;
τО – длительность процесса охлаждения заготовки; τРаз – длительность процесса размыкания формы;
τИ – длительность процесса извлечения из формы готового изделия.
Длительность процесса выдачи заготовки τВ определяется в свою очередь по формуле:
|
|
|
L |
З |
|
|
|
|
|||
|
|
|
|
|
|
|
В |
|
v |
|
|
|
|
|
З |
||
|
|
|
|
, с
(12.7)
где LЗ – длина экструдируемой заготовки, см;
vЗ –скорость выдачи заготовки из экструзионной головки, см/с.
Длительность процессов смыкания τС и размыкания τРаз формы определяется по формуле:
|
|
|
|
|
L |
П |
|
|
|
||||
|
|
|
|
|
|
|
|
С |
|
Раз |
|
v |
|
|
|
|
|
|
|
|
|
|
|
|
|
С |
, с
(12.8)
где LП – расстояние между разомкнутыми полуформами в свету, см;
vЗ –скорость смыкания полуформ, см/с; принимается в соответствии с рекомендациями ГОСТ10767-87.
Независимо от способа подачи сжатого воздуха на раздув заготовки его рабочее давление несколько повышается вследствие расширения от нагрева. Это увеличение давления определяется уравнением:
р2 р1 Т 2 , кг/см2 (12.9)
Т
1
где р2 – давление сжатого воздуха при повышенной температуре Т2, кг/см2; р1 – давление сжатого воздуха при температуре Т1, кг/см2.
Повышение давления нагретого воздуха приводит к увеличению внутреннего давления на стенки формуемого изделия и снижению количества сжатого воздуха, расходуемого за цикл. С учетом изложенного длительность процесса раздува заготовки τР определяется из зависимости:
|
Р |
|
|
V |
|
|
|
1 |
||
|
c |
|
|
|
|
|
p |
2 |
p |
|
1 |
|
|
|
p |
|
|
1 |
, с
(12.10)
где V – объем раздуваемого изделия, см3;
с – скорость прохождения сжатого воздуха, определяемая в зависимости от
диаметра сопла и давления в подводящей пневмомагистрали (таблица 12.1), см3/с;
р2 р1 – величина, учитывающая, в какой мере уменьшается время подачи
р1
сжатого воздуха в форму вследствие повышения давления воздуха при нагревании.
Длительность процесса охлаждения заготовки τО определяется по зависимости:
85

|
|
|
4 |
2 |
ln |
Т |
|
Т |
|
|
||
|
|
|
|
|
|
|
|
|
||||
|
|
|
|
|
|
З |
|
Ф |
||||
|
|
|
|
|
|
|
|
|
|
|||
|
О |
|
|
2 |
а |
|
Т |
|
Т |
|
||
|
|
|
|
|
И |
Ф |
||||||
|
|
|
|
|
|
|
|
|
|
|
, с
(1.43)
где δ – средняя толщина изделия, мм; а – коэффициент температуропроводности полимера в рабочем интервале
температур, мм2/с; ТЗ – температура заготовки, К;
ТИ – температура изделия в момент раскрытия формы, К; принимается на 20 градусов ниже температуры формоустойчивости;
ТФ – температура раздувной формы, К.
Таблица 12.1 – Скорость прохождения сжатого воздуха в зависимости от диаметра сопла и давления
Давление |
Скорость воздуха в см3/с |
Давление |
Скорость воздуха в см3/с |
|||||||||
перед |
при диаметре сопла в см |
перед |
при диаметре сопла в см |
|||||||||
соплом в |
|
|
|
|
соплом в |
|
|
|
|
|||
0,4 |
0,8 |
1,6 |
3,2 |
0,4 |
0,8 |
1,6 |
3,2 |
|||||
кГ/см |
2 |
кГ/см |
2 |
|||||||||
|
|
|
|
|
|
|
|
|
|
|||
0,07 |
|
0,79 |
3,17 |
12,5 |
50,9 |
2,45 |
|
4,98 |
19,9 |
79,6 |
319 |
|
0,14 |
|
1,13 |
4,48 |
17,4 |
71,7 |
2,8 |
|
5,5 |
21,9 |
87,7 |
351 |
|
0,21 |
|
1,36 |
5,49 |
21,6 |
87,8 |
3,15 |
|
5,97 |
23,8 |
95,6 |
382 |
|
0,28 |
|
1,58 |
6,31 |
24,8 |
101,0 |
3,5 |
|
6,5 |
25,8 |
103,7 |
416 |
|
0,35 |
|
1,75 |
7,02 |
27,6 |
112,2 |
4,2 |
|
7,46 |
30 |
119,2 |
480 |
|
0,42 |
|
1,93 |
7,7 |
30,8 |
122,7 |
4,9 |
|
8,5 |
33,9 |
135,5 |
543 |
|
0.49 |
|
2,07 |
8,3 |
33,1 |
132,4 |
5,6 |
|
9,49 |
37,9 |
151,6 |
605 |
|
0,63 |
|
2,35 |
9,4 |
37,4 |
150 |
6,3 |
|
10,47 |
42,8 |
168,2 |
671 |
|
0,84 |
|
2,69 |
10,7 |
43 |
171,6 |
7,0 |
|
11,5 |
45,8 |
183,6 |
736 |
|
1,05 |
|
2,98 |
11,9 |
47,5 |
190,5 |
7,7 |
|
12,52 |
49,8 |
199,8 |
862 |
|
1,4 |
|
3,48 |
13,9 |
55,2 |
222 |
8,4 |
|
13,5 |
54,1 |
216 |
895 |
|
1,75 |
|
3,97 |
16,0 |
63,6 |
254 |
8,75 |
|
14,0 |
56,0 |
224 |
961 |
|
2,1 |
|
4,48 |
18,0 |
71,5 |
286 |
|
|
|
|
|
|
И, наконец, длительность процесса извлечения из формы готового изделия τИ выбирается в зависимости от конструктивного исполнения и быстродействия применяемого съемного механизма.
Далее по рассчитанному времени полного цикла τц определяется производительность экструзионно-раздувного агрегата.
Широкая номенклатура разнообразных моделей серийно изготовляемых многими фирмами экструзионно-раздувных агрегатов с их техническими характеристиками приведена в соответствующих справочниках.
Наряду с рассмотренными созданы также и такие агрегаты, которые в едином технологическом цикле обеспечивают не только изготовление выдувной тары, но и ее заполнение жидкой продукцией с герметичной заваркой горловины. К таковым, в частности, относится серия экструзионно-раздувных
автоматов типа «Боттл-Пак» фирмы «Роммелаг» (Швейцария).
Изготовление тары и упаковывание в нее продукции с заваркой горловины осуществляется в этих автоматах на двух позициях. При этом на первой позиции из экструдера через экструзионную головку 1 (рис.12.12а) в разомкнутую форму 2 выдается трубчатая заготовка 3, которая обрезается
86

механизмом 4 обрезки и удаления облоя по линии 5, а затем захватывается и перемещается вместе с формой 2 на вторую позицию. Здесь сверху в полость заготовки вначале вводится ниппель 6 (рис.12.12б) наполнительного устройства 7, а затем форма 2 смыкается, пережимая и сваривая при этом нижнюю часть заготовки 3 и формуя на ниппеле сопрягающимися поверхностями горловину тары. Далее в канал ниппеля 6 через штуцер 8 подается сжатый воздух, раздувающий заготовку во флакон, а затем через штуцер 9 и ниппель 6 изготовленная тара заполняется из дозатора устройства 7 порцией упаковываемой продукции, а воздух из нее удаляется в это время через соединяющийся с атмосферой штуцер 8. Заполнив тару, ниппель 6 устройства 7 извлекается из тары (рис.12.12в), а затем смыкаются нагреваемые электрическим током полуформы 10, подогревающие верхнюю часть заготовки и одновременно формующие из нее герметично завариваемую горловину.
Рис. 12.12. Схема работы агрегата типа «Боттл-Пак»
Далее механизмом 4 обрезаются остатки заготовки, располагающиеся над горловиной, и удаляется с нее облой, а также готовая упаковочная единица 11 удаляется из синхронно размыкающихся форм 2 и 10 на приемную позицию. Здесь на нее навинчивается колпачок, наклеивается этикетка и далее готовые флаконы 11 укладываются в транспортную тару, а разомкнутые формы 2 и 10 в это время возвращаются на первую позицию и цикл повторяется. Высокая же производительность в этих автоматах достигается за счет применения многоручьевых экструзионных головок (до 4 ручьев) и многоместных форм.
В Московском институте химического машиностроения был разработан способ и создан экспериментальный агрегат, позволяющий выполнять все операции по изготовлению, заполнению и укупорке полимерной тары на одной позиции. В нем поверхности деталей угловой экструзионной головки, соприкасающиеся с расплавом термопласта, имеют обтекаемую форму и хорошо отполированы. Этим исключается образование застойных зон, приводящих к термической деструкции материала. Особенностью этой головки является и отсутствие в ней решетки – дорнодержателя, что позволяет избежать рассечения потолка расплава на отдельные струи и образования продольных полос, обусловливающих наличие «холодных» спаев. В отверстии дорна этой головки располагается в свою очередь фасовочная трубка, образующая с ним кольцевой зазор, через который подается сжатый воздух для раздува. В процессе работы после выдачи экструдером агрегата через головку трубчатой
87

заготовки в разомкнутую форму она смыкания. При этом верх формы охватывает сопрягающуюся часть дорна и формует из заготовки на нем горловину, а снизу заготовка пережимается и сваривается пресс-кантами. Затем через кольцевой зазор в отверстии дорна внутрь заготовки подается сжатый воздух, раздувающий ее в тару. По окончании времени выдержки по фасовочной трубке в полость отформованной тары из дозатора заливается порция упаковываемой жидкости, а воздух из нее в это время вытесняется через кольцевой зазор в отверстии дорна, соединяющийся с атмосферой. После окончания процесса заполнения фасовочная трубка выводится из горловины тары и далее производится ее заварка с помощью электронагреваемого инструмента, две части которого при смыкании обжимают разогретый участок горловины и выдавливают часть ее пластичного материала в фасовочное отверстие, формируя там герметичный укупорочный шов. Опыт работы на этом экспериментальном агрегате показал, что от правильности выбора метода заварки и конструкции сварочного инструмента во многом зависит качество изготовленных упаковочных единиц.
Применяются приведенные и подобные агрегаты для упаковывания в полимерные флаконы различных минеральных масел, моющих средств, фармацевтических жидкостей и суспензий, а также другой жидкой продукции.
12.3.Инжекционно-раздувное технологическое оборудование
Винжекционно-раздувных агрегатах литьем под давлением изготовляются вначале на оправках ампулообразные заготовки с отформованной горловиной и дном (рис.12.2), а затем в горячем состоянии они переносятся в выдувные формы и там оформляются в готовые изделия.
Инжекционно-раздувные агрегаты классифицируют:
по числу рабочих позиций – на двух-, трех и многопозиционные;
по кинематике движения заготовки – на агрегаты с возвратнопоступательным периодическим движением, а также с ротационным периодическим или непрерывным движением;
по числу одновременно формуемых изделий – на одно- и многоместные;
по способу формования – с неориентированным и ориентированным формованием.
Вчастности, двухпозиционный многоместный инжекционно-раздувной агрегат состоит из станины 1 (рис.12.13) на которой соосно установлены:
возвратно-поступательно перемещающаяся от гидроцилиндра 2 плита 3, несущая смыкающиеся в горизонтальной плоскости выдувные полуформы 4;
Рис. 12.13. Схема двухпозиционного многоместного инжекционно-раздувного агрегата
88

поворачивающийся на 180о стол 5, несущий на противолежащих вертикальных стенках две пары оправок 6;
плита 7, на которой со стороны стола 5 закреплены смыкающиеся в горизонтальной плоскости литьевые формы 8, соединяющиеся каналами 9 с литниковым отверстием 10 плиты;
червячное инжекционно-пластикационное устройство 11, сопрягающееся своим соплом 12 с литниковым отверстием 10 плиты 7.
Вначале рабочего цикла гидроцилиндром 2 плита 3 и стол 5 перемещаются к плите 7, запирая сомкнутые формы 4 и 8, в полостях которых при этом размещаются соответствующие оправки 6. Затем инжекционно-пластикационным устройством 11 через сопло 12 и литниковое отверстие 10 в литьевые формы 8 под давлением подается пластифицированная полимерная масса, из которой на оправках 6 формуются ампулообразные заготовки. Одновременно в выдувных формах 4 сжатым воздухом, подаваемым через оправки 6, ранее отлитые в формах 8 заготовки раздуваются в готовые изделия, плотно прижимаемые к стенкам их оформляющей полости. После окончания этих процессов, гидроцилиндром 2 плита 3 и стол 5 перемещаются в исходное положение, одновременно с этим формы
4 и 8 размыкаются, а готовые изделия удаляются с оправок 6. Затем стол 5 поворачивается на 180о, перенося оправки 6 с вновь отлитыми заготовками к выдувным формам 4, и цикл повторяется.
Втрехпозиционных инжекционно-раздувных агрегатах, например модели FIB-517, выпускаемых фирмой «Фишер» (ФРГ), технологические позиции
последовательно располагаются вокруг револьверного стола 1 (рис.12.14), несущего три оправки 2, которые установлены под углом в плане 120о.
Рис. 12.14. Схема трехпозиционного инжекционно-раздувного агрегата модели FIB-517 фирмы «Фишер» (ФРГ)
При этом на первой позиции этого агрегата в литьевой форме 3, установленной на плите 4, из пластифицированной полимерной массы, подаваемой под давлением из инжекционно-пластикационного устройства 5 через сопло 6 и литниковое отверстие, на оправке 2 формуется ампулообразная заготовка. Одновременно в сомкнутой выдувной форме 7, установленной на плите 8, выдвигающейся головкой оправки 2 заготовка предварительно вытягивается в продольном направлении, а затем подаваемым через нее сжатым воздухом раздувается в готовое изделие, по конфигурации оформляющей полости формы. При раздуве с предварительной вытяжкой совместное действие продольного и
89
тангенциального растяжений приводит к возникновению двухосной ориентации полимера, в результате чего существенно улучшаются его механические и оптические свойства, а также уменьшается газопроницаемость стенок изготовляемого изделия. На третьей же позиции в это время готовое изделие 9 снимается с оправки 2 съемником 10 и направляется по лотку 11 в накопитель. По окончании этих процессов формы 3 и 7 размыкаются в горизонтальной плоскости, а съемник 10 возвращается в исходное положение. Затем револьверный стол 1 приподнимается и поворачивается на 120о, перенося при этом на оправках 2 отлитую заготовку на вторую позицию, а готовое изделие – на третью позицию. После этого стол опускается в исходное положение, формы снова смыкаются и цикл повторяется.
Четырехпозиционный многоместный инжекционно-раздувной агрегат
модели АИПТ-0,5, предназначенный для изготовления из термопластов тары вместимостью до 0,5 дм3, в свою очередь содержит сварную станину 1 (рис.12.15), устанавливаемую на семи регулируемых виброопорах 2. На станине же располагаются следующие его функциональные устройства и механизмы:
Пластикационное устройство, червяк которого, находящийся в материальном цилиндре 3, приводится во вращение гидромотором 4 и продольно перемещается штоком гидроцилиндра 5, а также содержащее на материальном цилиндре нагревательные элементы сопротивления и бункер 6 с гранулированным материалом;
Блок измерительный 7, термореле 8 которого электрически связаны с нагревательными элементами сопротивления пластикационного устройства и обеспечивают установку на них по зонам требуемой температуры нагрева и автоматическое ее поддержание;
Револьверный стол 9, который несет на своих четырех гранях комплекты из трех оправок 10 и циклически поворачивается в плане на 90о от гидромотора с фиксацией положения, а также перемещается вертикально штоком расположенного под ним гидроцилиндра;
Механизм запирания 11, несущий на вертикально перемещающейся от гидроцилиндра верхней и неподвижной нижней плитах смыкающиеся литьевые трехместные полуформы 12, в формообразующих полостях которых соосно размещается первый комплект оправок 10;
Обогреваемая головка впрыска 13, закрепленная на сопле материального цилиндра 3 и обеспечивающая разделение потока подаваемого пластифицированного материала на три порции, а также их впрыск через литниковые каналы стыковочной колодки 14 в формообразующие полости сомкнутой литьевой формы 12, где на оправках 10 формуются ампулообразные заготовки;
Механизм смыкания 15, несущий на вертикально перемещающейся от гидроцилиндра верхней и неподвижной нижней плитах смыкающиеся раздувные трехместные полуформы 16, в формообразующих полостях которых соосно размещается второй комплект оправок 10 с отлитыми на них ампулообразными заготовками;
Блок 17, три гидроцилиндра которого подводят к смыкающейся раздувной форме 16 части, формирующие дно раздуваемых в ней изделий;
90