
Mechanical Properties of Ceramics and Composites
.pdf
220 |
Chapter 3 |
TABLE 3.3 Fracture Toughness, Flexure Strength, and Weibull Moduli Trends with Grain Structure for Si3N4 and Al2O3a
|
|
|
|
|
|
Fine G |
|
|
|
|
Medium G |
|
|
|
Larger G |
|
|
|
|
|
|
|
|
|
|
|
|
|
|
|
|||
Material |
Investigator |
K |
σ |
m |
|
K |
σ |
m |
|
K |
σ |
m |
||||
|
|
|
|
|
|
|
|
|
|
|
|
|
|
|||
Si3N4 |
Matsuhiro and |
6.5 |
0.96 |
|
|
8.3 |
0.81 |
|
9.7 |
0.9 |
|
|||||
|
|
|
|
Takahashi [297] |
|
|
|
|
|
|
|
|
|
|
|
|
Si |
3 |
N |
b |
Himsolt et al. [298] |
3.2 |
|
|
|
5.0 |
|
|
8.0 |
|
|
||
|
|
4 |
|
|
|
|
|
|
|
|
|
|
|
|
|
|
|
|
|
|
|
|
0.5 |
|
|
|
|
0.7 |
|
|
|
0.6 |
|
Si3N4 |
Tani et al. [241] |
4.5 |
0.6 |
|
|
6.0 |
0.55 |
|
6.0 |
0.55 |
|
|||||
Si3N4 |
Kim et al. [300] |
|
|
|
|
|
7.0c |
0.88c |
|
|
8.0d |
0.68d |
|
|||
Si3N4 |
Hoffmann [299] |
|
1.1 |
14–20 |
|
|
0.9 |
46 |
|
|
0.81 |
18 |
||||
Si3N4 |
Li et al. [244] |
|
|
20 |
|
|
|
|
33 |
|
|
|
22 |
|||
Al |
2 |
O e |
Price et al. [308] |
|
|
|
|
3.7 |
0.25 |
9 |
|
|
|
|
||
|
|
3 |
|
|
|
|
|
|
|
|
|
|
|
|
|
|
|
|
|
|
|
|
|
|
|
4.7 |
0.26 |
24 |
5.1 |
0.26 |
13 |
a G = grain size, K = fracture toughness in MPa·m-1/2, σ = flexure strength in GPa, and m = Weibull modulus.
b K and σ data shown on separate lines to reflect that the two properties were measured on bars from somewhat different processing, as opposed to all measurements being from bars from the same processing, as is the case where all data for a given G range are on the same line.
c Average grain diameter and length: 1 ± 0.3 and 5.3 µm. d Average grain diameter and length: 2 ± 1 and 12 µm.
e The top line gives results for G = 4 µm and an aspect ratio of 1.5, while the lower line is for bodies respectively with G =4 µm and 5 µm, both with aspect ratios of 2.6 due to slightly different compositions of the grain boundary glass in these 96% alumina bodies.
modest coarsening of the fine equiaxed grain structure, which was also corroborated by some decrease in HV (100 N) from 18.6 to 17.6 GPa. On the other hand, the HIPed bodies showed strength increasing from 420 to 550 MPa and toughness similarly increasing from 5 to 5.3 MPa·m1/2 as the DG content increased from 0 to 5 w/o. Increased addition, toughness, and strength in these samples were accompanied by greater coarsening and elongation of the grains, which was again reflected in lower hardnesses decreasing from 18.3 to 17.3 GPa as the addition increased. Thus opposite strength and toughness trends occurred for hot pressing versus HIPing as a function of additive content, showing important differences for two densification processes that often give the same results. However, the changes were consistent with each other, since strengths from both processes tracked with their toughness and reasonably well with the microstructural changes, i.e. higher strength from finer grain structure, with some countering of decreases from coarsening with development of an elongated but still reasonably fine grain structure. The corroboration of strength and toughnesses with microstructural changes by H trends is an example of the benefits of more property measurements.
Grain Dependence of Ceramic Tensile Strengths at 22°C |
221 |
Turning directly to the issue of reliability, Table 3.3 clearly shows that the Weibull modulus can reach substantial levels in Si3N4 with development of intermediate grain structures consisting of finer, often more equiaxed, grains of a few microns diameter combined with similar, or somewhat larger, diameter, but more elongated, grains. Such m maxima do not correlate with strength maxima, and probably not with toughness maxima, but do appear to correlate with either preceding, or the onset of, larger grains or clusters of them acting as fracture origins. This raises the issue of whether the increase in m is due to crack branching and bridging or to a more uniform population of grains to initiate failures, or some combination of these two effects. Detailed study of fracture surfaces may help resolve this issue, as was previously discussed [293], but detailed study involving correlation with other factors is also needeed.
One of the few other materials for which there is similar, though very limited, data is Al2O3 (Table 3.3), which suggests similar effects but on a far more modest scale, especially of strength. The limited strength levels raise some question whether such effects are part of the normal σ – G behavior, since, as was noted earlier, K – G behavior is contrary to the σ – G behavior. No measurements of m as a function of grain size over any significant G range are known, but m can be calculated from the average strength (A) and the standard deviation (S) per Ref. 310 as
m = 1.21(A/S) – 0.47 |
(3.4) |
However, σ – G data commonly entails limited (e.g. 5–10 or fewer) measurements per grain size, severely limiting the accuracy of such calculations. Further, even with more data points, limited shifts in grain structure can shift Weibull moduli. Thus Ting et al. [133], who directly measured m for their sintered alumina bodies, showed m increasing from 7 to 8 with narrower G distributions from 0.5 to 4.5 µm to m 11 – 13 with G distributions of 1 to 8 µm. While this is consistent with data of Price et al., variations in these results again show the importance of having a reasonable data base for calculations of m as a function of G whether calculated directly or via Eq. (3.4).
The alumina data set of Tomaszewski [134] (Fig. 3.14) meets the above criteria, consisting of 15–25 measurements per data point for at least eight different G values, with four on the finer G branch and four on the larger G branch. These give an average m of 9 ± 4 for the larger G branch and 26 ± 14 for the finer G branch, indicating higher m values at finer, not at larger, G where greater toughening due to branching and bridging should occur. Thus while limited possible effects of increased toughness increasing reliability have been indicated by Price et al. [308] and possibly by Ting et al. [133], this clearly is not a large effect and is not associated with important σ – G changes, especially the change from finer G branch to larger G branch behavior, e.g. as suggested by Chantikul et al. [131].
Another material in which some data exists on toughness and strength
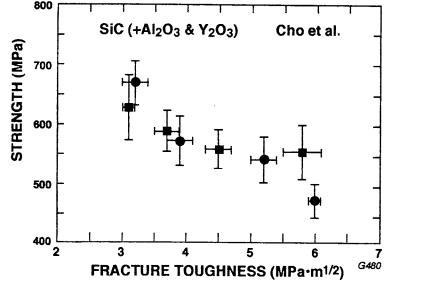
222 |
Chapter 3 |
changes with microstructure changes, especially with elongated grains, is SiC. Thus data of Cho and colleagues for in situ toughened silicon carbide [311, 312] shows strengths decreasing with any increase in toughness above the normal level ( 3 MPa·m1/2) (Fig. 3.40) in bodies sintered with 12 and 8 wt% respectively of Al2O3 and Y2O3 with or without 1% of α-SiC seeds. They showed that 5, 10, and 20% amounts of the combined additives, which resulted in the grain diameter respectively decreasing from 1 to 0.6 µm and aspect ratio increasing from 6 to 11, gave little change of strengths ( 600 MPa) or toughness 5.6–5.8 MPa·m1/2), i.e. consistent with the middle portion of the trend in Fig. 3.40. While apparently no direct measurements of Weibull moduli have been made in such studies of SiC, estimates of m from Eq. (3.4) indicate that if there are any changes in m as toughness increases, it is for m to decrease not increase with increased K.
The above review shows that increased toughness can lead to increased strength and reliability, i.e. increased Weibull modulus in some cases. These are mainly ZrO2 toughened bodies and in situ toughened Si3N4 bodies, but even in these bodies improved strengths and reliability become self-limiting with continued increased toughness, i.e. there is an optimum balance between these proper-
FIG. 3.40 Strengths versus toughness from tests at 22°C of in situ toughened SiC sintered with respectively 12 and 8 w/o of Al2O3 and Y2O3 with or without 1% of α- SiC seeds by Cho et al. [311, 312]. (Published with the permission of the
Journal of Materials Science.)
Grain Dependence of Ceramic Tensile Strengths at 22°C |
223 |
ties that depends on the microstructure and the crack-microstructure scale. Such benefits are likely to be dependent on both the size and shape of the component and the nature of the stress-crack situations to be addressed. Further, such effects show limited or no translation of these benefits to the few other materials investigated, i.e. Al2O3 and SiC, indicating effects that probably depend on combinations of grain boundary phase-grain interactions and of the properties of the grains, e.g. of their fracture characteristics.
Finally, note two important opportunities to understand better the relation of crack propagation, especially toughness, tests to normal strength behavior. The first is the study of composites, addressed in Chapters 8–12, which again shows some of the same basic differences between toughness and strength, again questioning the applicability of much large crack data to normal strength. The second is various aspects of fractography, which is often more successful with monolithic versus composite ceramics and is probably basic to determining the apparently limited contributions of bridging and related R-curve effects to normal strength behavior. One basic aspect is corroboration of microstructural aspects of crack propagation in the fracture origin area, such as fracture mode, e.g. intergranular fracture favorable to bridging, and detailed comparison of matching fracture surfaces, e.g. for evidence of crack bridging. Another potentially important aspect is comparison of fracture mirror and related dimensions as a function of flaw, microstructure, and property changes. As noted earlier, such dimensions show clear reductions as flaw sizes decrease in bodies with substantial TEA stresses reflecting their contributions to failure [102]. Since such dimensions also reflect the toughness controlling fracture, they should thus correspondingly show increases with bridging and related R-curve effects, i.e. if these increase the toughness controlling failure this should be reflected in the mirror and related dimensions. Though such specific studies have not been conducted, qualitative evaluation of existing data does not show obvious evidence of such increases, i.e. no increase in mirror size other than the normal decrease with decreasing flaw size. Further, specific comparison of strength–mirror size data for hot pressed Al2O3 (G 1–2 µm) and commercial sintered aluminas (G 4–10 µm) shows them being essentially idntical [313], contrary to expected increasing bridging effects as G increases.
X.SUMMARY, DISCUSSION, CONCLUSIONS, AND RECOMMENDATIONS
Alkali halides, which even in polycrystalline form often show some macroscopic yield, have a single σ–G-1/2 branch with a moderately positive σ–G-1/2 slope (depending on material composition and temperature) extrapolating to single crystal yield stresses at G= ∞. Similarly, some somewhat harder, more refractory materials with known or expected microplasticity in single crystals such as CaO,
224 |
Chapter 3 |
MgO, and BaTiO3 typically show a single branch, at least for large to moderate G, with σ > 0 extrapolation at G=∞ to the single crystal failure stress, again indicating microplastically controlled strengths. Limited yield-extrapolated σ differences are attributed to purity differences between single crystals and polycrystalline grains. Other manifestations of microplastic behavior are σ increases with alloying (e.g. as for CaO, MgO, and BaTiO3) and preferred orientation (e.g. of MgO, despite preferred orientation of {100} for easier fracture), as well as possible limited increases in strengths and internal failures as a result of surface work hardening from machining. Strengths, slopes, and intercepts decrease with increasing test temperature, moderately at first (reflecting decreases in both yield stresses and elastic moduli) and then more rapidly (e.g. above 1000°C or more commonly due to increasing grain boundary sliding) (Chap. 6).
Materials of intermediate hardness such as MgO and BaTiO3 clearly show a change to greatly reduced, possibly zero G dependence of σ at finer G, with this transition being a function of surface finish. More severe machining, e.g. use of coarser grits or machining transverse, as opposed to parallel, to the tensile axis results in lower strengths and a transition to substantially reduced G dependence of σ at finer G. While there is not yet any direct fractographic evidence, such finer G failure is attributed to generating flaws sufficiently large to cause failure at lower stresses than for microplastic induced failure. Microplastic controlled failure is typically associated with failure initiating from a single grain, implying a transition to flaw failure when c G. Such a transition to flaw controlled failure at finer G from microplastic control of σ at larger G is exactly the opposite of that proposed by Carniglia [8, 9]. There is also some evidence that very coarse machining, e.g. sawing, of MgO leads to strengths below the normal large G σ–G-1/2 trends, possibly due to failure from larger flaws or failure via the slip-as- sisted crack growth. Fairly extreme finishing is needed to observe such machining effects, since unless fairly deep cracks are introduced in the surface, their role in failure is probably limited by surface work hardening. Note that even with slip-induced failure, mist and hackle are generated within larger grains, e.g. of CaO (Figs. 3.4B–D) again showing cracks having reached catastrophic propagation before reaching a grain boundary, as in failure from preexisting flaws.
The great bulk of refractory ceramic materials, which are of moderate, and most commonly substantial, hardness, and which fail from preexisting flaws, show a two-branch σ–G-1/2 behavior over the normal G range (e.g. 1–100 µm). The larger G branch shows a substantial positive slope, which is typically between single crystal (or grain boundary) and polycrystalline KIC values, reflecting varying extents of subcritical growth of flaws initially < G. Such c < G subcritical crack growth may be due to environmental effects or simply to propagation starting at single crystal (or grain boundary) KIC values, but being arrested by surrounding grains, with resultant failure occurring at higher, e.g. polycrystalline, KIC. However, even if c does not = G/2 at failure, there can still be mea-
Grain Dependence of Ceramic Tensile Strengths at 22°C |
225 |
surable, frequently intrinsic G-1/2, σ dependence. Similarly, observations of single crystal mist and hackle patterns in large grains show limits on flaw growth prior to failure (e.g. Figs. 3.7 and 3.12), and evidence of fracture related to single crystal instead of polycrystalline toughnesses. Thus substantial further work documenting local K values and understanding their effects on crack propagation and strength is needed. While this larger G branch may frequently extrapolate to σ = 0 at G = ∞, this is both uncertain and probably irrelevant since there must be a transition to single crystal (or bicrystal; i.e. grain boundary) strengths. Larger G strengths can frequently extend to a fraction, e.g. 1/5 to 1/2, of typical single crystal strengths for weaker orientations with comparable surface finishes. While some lower polycrystalline strengths can be due to defects, much of this appears to be intrinsic, e.g. due to lower grain boundary strengths/toughnesses as well as probable ontributions of TEA and possibly EA stresses to failure. Such factors may also mean that the larger G branch slope is not constant.
The transition from the larger G to the finer G region of σ – G-1/2 behavior can intrinsically cover a range of c/G ratios (e.g. from 2 to 1/3) not just 2 (due to c being a radius and G a diameter). This approximate equivalence of c and G at the transition is born out by most data. It also implies less subcritical crack growth, and less effects of machining direction on σ. Data does show much more limited effects of the range of normal machining variables, e.g. machining direction or grit size on σ, when G the size of the flaws for the specific machining, with increasing effects at larger G (i.e. greater for single crystals) and finer G (where they tend to have the greatest effect).
The finer G branches result from c > G, so σ is controlled by polycrystalline KIC (typically with limited or no contribution of R-curve). There may be multiple finer G branches, or more scatter in them, with the number or width being dependent on different or varying flaw populations, e.g. as occur from significantly different machining conditions, or varying types of flaws. Each finer G branch intersects the larger G branch when c G (with variations noted earlier). Finer G branches always have substantially lower slopes than the larger G branch. However, the assumption made by some (mainly those using Gm), that the slope of these finer G branches is intrinsically 0, is not supported by the majority of the data, nor with a variety of mechanisms that are known or expected to introduce some limited G dependence in this region. Several mechanisms that can give positive slopes are (1) reductions in machining flaw sizes or severity of grain boundary grooves (on as-fired or annealed surfaces) as G decreases, (2) possible grain-related cracks around pores, (3) decreasing contributions of EA, TEA, and related stresses as G decreases (relative to c) (4) increased grain boundary concentration of impurities or additives as G increases, and (5) reduced SCG as G decreases. Preferred grain orientation (e.g. from green body extrusion) can also affect this slope. This may give a negative slope due to increasing orientation with increasing G, as indicated for some BeO. Finer G
226 |
Chapter 3 |
slopes of 0 could occur by effects yielding negative slopes being balanced by those giving positive slopes. It is also possible that KIC and σ begin to decrease intrinsically at very fine G, e.g. nm, beyond probable reductions in the crack deflection, branching, bridging, and related microstructural scale mixed mode effects. Such decreases may occur due to more disordered grain boundary structure becoming a measurable fraction of the specimen volume, i.e. such a fraction of the specimen so it has more disordered structure, e.g. like a glass, causing strength to decrease intrinsically. However, observed strength reductions at G 1 µm or less, e.g. in oxides and MgF2 (Fig. 3.24), are primarily or exclusively due to anion impurities.
The question of what G value to use in plotting σ is important, since it impacts the slope of both larger and finer G branches, as well as their intersection and hence quantitative evaluation of mechanisms involved, and the benefits to be achieved from G refinement. From a procedural standpoint, the G value should be consistent with the σ value used. The most effective way of doing this is via fractography, in order to determine not only the specific G value pertinent to the fracture origin but also the location of the fracture origin and hence any possible σ corrections. If fractography is not successful or is simply not conducted, use of Gm is not appropriate unless there is reasonable evidence for it being significant, since the maximum σ (which is all that is normally directly available from a flexure test) is more appropriate to Ga than Gm. Also, applicability of Gm will generally be substantially less for the finer than for the larger G branch.
For measuring appropriate G values, use of the common linear intercept method is not recommended. Instead, it is suggested that an average G diameter be measured for each grain along some, e.g. random, lines (preferably on the fracture surface) and averaged. Such a surface average grain diameter should be more appropriate for fracture, and both individual and average values can be compared to different G (e.g. Gm) values and weighted, to account for G distribution. With heterogeneous grain structures, the spatial and size distributions need to be considered. Such G measurement can, at least partially, account for grain shape effects, but they may also require more detailed evaluation of grain shapes. Grain orientation is often important, especially on a global scale, and may increase significantly with increasing G; it needs to be directly addressed and often is related to grain shape effects.
Another very important set of parameters are those of testing. Thus larger G, e.g. Gm, values may be more pertinent to larger specimens and stressed volumes (e.g. uniform tension tests) and less so for smaller specimens and stressed volumes (e.g. flexure, especially three point). Test atmosphere and temperature can provide important clues to subcritical crack growth, and probable G effects on this (as can machining effects as a function of G). Higher temperature tests, e.g. at 500–1000°C, can be important for differentiating microplastic and brittle failures (Chap. 6). Thus for both a σ decrease similar to that of E with tempera-
Grain Dependence of Ceramic Tensile Strengths at 22°C |
227 |
ture would be expected, e.g. is indicated for microplastic materials, e.g. CaO and MgO, but for brittle failure there can be a temperature dependence to EA, and there clearly is for TEA. This can lead to, at least initially, either less decrease of σ or a limited σ increase with temperature, especially in the G regime where these effects are most important, as is indicated for several orders.
A variety of other parameters need to be considered in accessing σ–G behavior. These include residual porosity (whose effects may not be fully independent of G), machining, whose effects can clearly change with G, and other body constituents. Constituents in solid solution generally have limited effect on failure from preexisting flaws or microcracks (e.g. via EA or TEA) but can have substantial effect on failure due to microplasticity. Constituents as second phases (temporarily or permanently) affect σ mainly via G (often significantly reducing it) but may have various other positive or negative effects on σ.
In a broader perspective, analysis of σ – G-1/2 behavior and application of fractography have proved valuable for defining failure mechanisms, especially when combined with other studies such as of machining and different materials. Thus the first of two broad basic results are the fundamental differences in primarily the grain size and secondarily the shape and orientation dependence of much large crack toughness and normal strengths, which are often opposite, i.e. increasing toughness with decreasing strength. This results from two factors, namely from larger versus small crack effects as discussed in Chap. 2 and from changing c/G ratios (Figure 2.16) and some dependence of flaw sizes, especially from machining, on G via local values of elastic moduli, hardness, and toughness. This importance of local properties impacting the introduction of flaws and resultant body strengths is contrary to the typical focus on explaining ceramic strength behavior based on large crack toughness values with limited, or often no, attention to flaws causing failure and their microstructural dependence. This reduced relevance of large crack toughness values to normal strength behavior is controlling propagation of small cracks versus the importance of material and microstructure on properties controlling machining flaw generation is the second broad result [294]. However, such tests are relevant to strengths controlled by larger cracks, e.g. from serious thermal shock (Chap. 6) or impact damage. These basic results are corroborated and reinforced by similar evaluation of ceramic composites (Chaps. 8, 9, and 12).
REFERENCES
1.F. P. Kundsen. Dependence of Mechanical Strength of Brittle Polycrystalline Specimens on Porosity and Grain Size. J. Am. Cer. Soc. 42(8):376–388, 1959.
2.R. W. Rice. Review, Ceramic Tensile Strength: Grain Size Relations: Grain Sizes, Slopes, and Branch Intersections. J. Mat. Sci. 32:1673–1692, 1997.
3.R. W. Rice. Microstructure Dependence of Mechanical Behavior of Ceramics. Treatise Mat. Sci. Tech., Properties and Microstructure 11 (R. C. McCrone ed). Academic Press, New York, 1997, pp. 199–381.
228 |
Chapter 3 |
4.R. W. Rice. Evaluation and Extension of Mechanical Property-Porosity Models Based on Minimum Solid Area. J. Mat. Sci. 31:102–118, 1996.
5.R. W. Rice. Comparison of Physical Property-Porosity Behavior with Minimum Solid Area Models. J. Mat. Sci. 31:1509–1528, 1996.
6.R. W. Rice. Porosity of Ceramics. Marcel Dekker, New York, 1998.
7.E. Ryshkewitch and D. W. Richerson. Oxide Ceramics, Physical Chemistry and Technology. 2d ed., General Ceramics, Inc., Haskell, NJ, 1985.
8.S. C. Carniglia. Petch Relation in Single-Phase Oxide Ceramics. J. Am. Cer. Soc 48(11):580–583, 1965.
9.S. C. Carniglia. Reexamination of Experimental Strength-vs.-Grain-Size Data for Ceramics. J. Am. Cer. Soc. 55(5):243–249, 1972.
10.H. P. Kirchner and R. M. Gruver. Strengthening Oxides by Reduction of Crystal Anisotropy. Cer. Fin. Co., Report No. 6 for Contract N00014-66-C0190, 1972. (See also H. P. Kirchner. Strengthening of Ceramics: Treatments, Tests, and Design Applications. Marcel Dekker, New York, 1979.)
11.R. W. Rice. Strength/Grain-Size Effects in Ceramics. Proc. Brit. Cer. Soc. 20:205–213, 1972.
12.R. W. Rice. Fractographic Identification of Strength-Controlling Flaws and Microstructure. Frac. Mech. Cer. 1 (R. C. Bradt, D. P. H. Hasselman, and F. F. Lange, eds.). Plenum Press, New York, 1974, pp. 323–343.
13.R. W. Rice. Machining Flaws and the Strength-Grain Size Behavior of Ceramics. The Science of Ceramic Machining and Surface Finishing II (B. J. Hockey and R. W. Rice, eds.). NBS Special Pub. 562, 1979, pp. 429–454.
14.S. M. Wiederhorn, B. J. Hockey, and D. E. Roberts. Effect of Temperature on the Fracture of Sapphire. Phil. Mag. 28(4): 783–795, 1973.
15.R. W. Rice. The Effect of Grinding Direction on the Strength of Ceramics. The Science of Ceramic Machining and Surface Finishing (S. J. Schneider and R. W. Rice, eds.). NBS Special Pub. 348, US Govt. Printing Office, Washington DC 1972, pp. 365–376.
16.R. W. Rice. Processing Induced Sources of Mechanical Failure in Ceramics. Processing of Crystalline Ceramics (H. Palmour III, R. F. Davis, and T. M. Hare, eds.). Plenum Press, New York, 1978, pp. 303–319.
17.R. W. Rice. Machining of Ceramics. Proc. of 2d Army Mat. Tech (J. J. Burke, A. E. Gorum, and R. N. Katz, eds.). Metals and Ceramic Info. Center, Columbus, OH, 1974, pp. 287–343.
18.R. W. Rice and J. J. Mecholsky, Jr. The Nature of Strength Controlling Machining Flaws in Ceramics. The Science of Ceramic Machining and Surface Finishing II (B. J. Hockey and R. W. Rice, eds.). US Govt. Printing Office, Washington DC, 1979, pp. 351–378.
19.R. W. Rice, J. J. Mecholsky, Jr., and P. F. Becher. The Effect of Grinding Direction on Flaw Character and Strength of Single Crystal and Polycrystalline Ceramics. J. Mat. Sci. 16:853–862, 1981.
20.R. W. Rice, J. J. Mecholsky, Jr., S. W. Freiman, and S. M. Morey. Failure Causing Defects in Ceramics: What NDE Should Find. NRL Memo. Report 4075, 10/30/1979.
21.R. W. Rice. Ceramic Fracture Features, Observations, Mechanisms, and Uses.
Grain Dependence of Ceramic Tensile Strengths at 22°C |
229 |
Fractography of Ceramic and Metal Failures (J. J. Mecholsky, Jr. and S. R. Powell, Jr., eds.). ASTM, STP 827, 1984, pp. 5–103.
22.R. W. Rice. Perspective on Fractography. Adv. Cer. 22, Fractography of Glasses and Ceramics (V. D. Frechette and J. R. Varner, eds.). Am. Cer. Soc., Westerville, OH, 1988, pp. 3–56.
23.R. L. Coble. Thermal Grooving in Polycrystalline Ceramics and Initiation of Brittle Fracture. J. Am. Cer. Soc. 54(1):59–60, 1971.
24.R. E. Tressler, R. A. Langensiepen, and R. C. Bradt. Surface-Finish Effects on
Strength-vs.-Grain-Size Relations in Polycrystalline Al2O3. J. Am. Cer. Soc. 57(5):226–227, 1974.
25.R. C. Bradt, J. L. Dulberg, and R. E. Tressler. Surface Finish Effects and the Strength-Grain Size Relationship in MgO. Acta Met. 24:529–534, 1976.
26.D. C. Cranmer, R. E. Tressler, and R. C. Bradt. Surface Finish Effects and the Strength-Grain Size Relation in SiC. J. Am. Cer. Soc. 60(5–6):230–237, 1977.
27.N. McN. Alford, K. Kendall, W. J. Clegg, and J. D. Birchall. Strength/Microstructure Relation in Al2O3 and TiO2. Ad. Cer. Mat’s. 3(2):113–117, 1988.
28.R. W. Rice, S. W. Freiman, and J. J. Mecholsky, Jr. The Dependence of StrengthControlling Fracture Energy on the Flaw-Size to Grain-Size Ratio. J. Am. Cer. Soc. 63(3–4):129–36, 1980.
29.B. R. Emrich. Technology of New Devitrified Ceramics—A Literature Review. Technical Doc. Rpt. No. ML-TDR-64-203 to AFML, 9/1964.
30.W. H. Rhodes and R. M. Cannon. Microstructure Studies of Polycrystalline Refractory Compounds. Summary Report for Contract N00019-C-0376, US Naval Air Syst., Washington, DC, 1974.
31.R. J. Stokes and C. H. Li. Dislocations and the Strength of Polycrystalline Ceramics. Materials Science Research 1 (H. Stadelmaier and W. Austin, eds.). Plenum Press, New York, 1963, pp. 133–157.
32.P. F. Becher and R. W. Rice. Strengthening Effects in Press Forged KCl. J. Appl. Phys. 44(6):2915–2916, 1973.
33.M. W. Benecke, C. R. Porter, and D. W. Roy. R and D on the Application of Polycrystalline Zinc Selenide and Cadmium Telluride to High Energy IR Laser Windows. Report No. AFML-TR-72-177, 1972.
34.J. C. Wurst. Thermal, Electrical, and Physical Property Measurements of Laser Window Materials. Proc. Conf. On High Power Infrared Laser Window Materials (C. A. Pitha ed.). AQFCRL-TR-73-0372(1), Special Report No. 162, Air Force Cambridge Research Labs 2:565–592, 6/1973.
35.F. Buch, and C. N. Ahlquist. The Yield Strength of Polycrystalline CdTe as a Function of Grain Size. Mat. Sci. Eng. 13:191–196, 1974.
36.M. Weinstein. Preparation of Fine-Grained PbTe by Ultrasonic Agitation of a Solidifying Melt. Trans. Met. Soc. AIME 230:321, 1964.
37.H.-E. Kim, and A. J. Moorhead. Effect of Doping on the Strength and Infrared Transmittance of Hot-Pressed Cesium Iodide. J. Am. Cer. Soc. 74(1):161–165, 1991.
38.D. W. Roy and P. E. Natale. Processing and Properties Study of IR Windows. Final Report No. AFAL-TR-66-349, for Contract AF 33(615)-2733, 9/1966.