
- •MODERN
- •POWER STATION PRACTICE
- •PERGAMON PRESS
- •Contents
- •Foreword
- •G. A. W. Blackman, CBE, FEng
- •Preface
- •Chapters 1 and 2
- •Chapter 3
- •Contents of All Volumes
- •CHAPTER 1
- •Power station siting and site layout
- •1 Planning for new power stations
- •1.1 Introduction
- •1.2 Capacity considerations
- •1.3 Economic considerations
- •1.4 Future requirement predictions
- •1.5 System planning studies
- •1.6 Authority to build a new power station
- •2 Site selection and investigation
- •2.1 Basic site requirements
- •2.3 Detailed site investigation
- •2.4 Environmental considerations
- •2.5 Site selection
- •3 Site layout — thermal power stations
- •3.1 General
- •3.2 Foundations
- •3.3 Site and station levels
- •3.4 Main buildings and orientation
- •3.5 Ancillary buildings
- •3.6 Main access and on-site roads
- •3.7 Station operation considerations
- •3.8 Cooling water system
- •3.9 Fuel supplies and storage
- •3.10 Ash and dust disposal
- •3.11 Flue gas desulphurisation plant materials
- •3.12 Transmission requirements
- •3.13 Construction requirements
- •3.14 Amenity considerations
- •3.15 Typical site layouts
- •4 Pumped storage
- •4.1 Introduction.
- •4.2 Suitable topology
- •4.3 Ground conditions
- •4.4 Site capacity
- •4.5 System and transmission requirements
- •4.7 Heavy load access
- •4.9 Environmental impact
- •5 Gas turbines
- •5.1 Introduction
- •5.2 The role of gas turbines
- •4.7 Heavy load access
- •Station design and layout
- •1 Introduction
- •2.1 Fossil-fired stations
- •2.2 Nuclear stations
- •2.3 Hydro-electric and pumped storage stations
- •2.4 Gas turbine stations
- •3 Future development options
- •3.1 Fossil-fired plant
- •3.2 Nuclear stations
- •3.3 Combined cycle gas turbines
- •3.4 Wind power
- •3.5 Tidal power
- •3.6 Geothermal energy
- •3.7 Combined heat and power
- •4 Station design concepts
- •4.1 Basic considerations
- •4.2 Design objectives
- •5 Plant operation
- •6 Station layout
- •6.1 General
- •6.2 Main plant orientation
- •6.3 Layout conventions
- •.7 Turbine-generator systems
- •7.1 Feedheating plant
- •7.2 Condenser and auxiliary plant
- •7.3 Erection and maintenance
- •8 Boiler systems
- •8.1 Pulverised fuel system
- •8.2 Draught system
- •8.3 Oil firing system
- •8.4 Boiler fittings
- •8.5 Dust extraction plant
- •8.6 Flue gas desulphurisation plant
- •9 Main steam pipework
- •10 Low pressure pipework and valves
- •11 Water storage tanks
- •12 Cranes
- •13 Fire protection
- •13.1 Introduction
- •13.2 Prevention of fires
- •13.3 Limiting the consequences of a fire
- •13.4 Reducing the severity of fires
- •14 Electrical plant layout
- •14.1 Introduction
- •14.2 Auxiliary switchgear
- •14.3 Turbine-generator auxiliaries
- •14.4 Main connections
- •14.5 Transformers
- •14.6 Cables
- •14.7 Batteries and charging equipment
- •14.8 Control rooms
- •15 Heating, ventilation and air conditioning
- •15.1 Introduction
- •15.2 Ventilation of nuclear stations
- •15.3 Smoke and fire control
- •15.4 General layout of HVAC plant
- •16 Air services
- •17 Water treatment plant
- •18 Cooling water plant
- •18.1 General design considerations
- •18.2 Cooling water pumphouse
- •18.3 Main cooling water pumps
- •18.4 Screening plant
- •18.5 Pump discharge valves
- •18.6 Section valves
- •18.7 Discharge pipework
- •18.8 Auxiliary systems
- •19 Chlorination plant
- •20 Coal handling plant
- •20.2 Water-borne reception and discharging
- •20.3 Road-borne reception and discharging
- •20.4 Coal storage
- •20.5 Conveyance from unloading point to station bunkers or coal store
- •20.6 Plant control
- •21 Ash and dust handling plant
- •21.1 Ash handling plant
- •21.2 Dust handling plant
- •21.3 Ash and dust disposal
- •22 Auxiliary boilers
- •23 Gas generation and storage
- •23.1 Hydrogen
- •23.2 Carbon dioxide
- •23.3 Nitrogen
- •23.4 Miscellaneous gases
- •24 Pumped storage plant
- •24.1 Hydraulic machines
- •24.2 Generator-motors
- •24.3 Main inlet valves
- •24.4 Draft tube valves
- •24.5 Gates
- •24.6 High integrity pipework
- •25 Gas turbine plant
- •25.1 Introduction
- •25.2 Operational requirements
- •25.3 Aero-engine-derivative gas turbines
- •25.4 Industrial gas turbines
- •25.5 Gas turbine power station layout
- •26 References
- •CHAPTER 3
- •Civil engineering and building works
- •Introduction
- •2 Geotechnical investigations
- •2.1 General and desk studies
- •2.2 Geophysical investigations
- •2.3 Trial excavations and boreholes
- •2.3 Trial excavations and boreholes
- •2.4 In-situ tests
- •2.5 Groundwater investigations
- •2.6 Ground description and classification
- •2.7 Laboratory tests
- •2.8 Factual reports
- •2.9 Interpretation of site investigations
- •3 Seismic hazard assessment
- •3.1 Geology
- •3.2 Earthquakes
- •3.3 Crustal dynamics
- •3.4 Ground motion hazard
- •3.5 Ground rupture hazard
- •4 Types of foundations
- •4.1 Isolated column foundations
- •4.2 Strip foundations
- •4.5 Piled foundations
- •4.5 Piled foundations
- •4.6 Caisson foundations
- •4.7 Anti-seismic foundations
- •5 Foundations design and construction
- •5.1 Concrete
- •5.2 Bearing pressures and settlement
- •5.3 Test piling
- •6 Foundations for main and secondary structures
- •6.1 Boiler house foundations
- •6.2 Turbine hall foundations
- •6.3 Turbine-generator blocks
- •6.4 Basement of ground floor
- •6.5 Track hoppers
- •6.6 Chimney foundations
- •6.7 Cooling tower foundations
- •6.8 Reactor foundations
- •7 General site works
- •7.1 Flood embankments
- •7.2 Roads
- •7.3 Drainage
- •7.4 Railways
- •7.5 Coal storage
- •7.3 Oil tank compounds
- •7.7 Ash disposal areas
- •8 Methods of construction
- •8.1 Site clearance, access roads and construction offices
- •8.2 Underground construction
- •8.3 Groundwater lowering
- •8.4 Excavating machinery
- •8.6 Formwork and reinforcement
- •8.7 Mixing and placing of concrete
- •9 Direct cooled circulating water systems
- •9.1 Civil engineering structures in direct cooling systems
- •9.2 Culverts
- •3.3 Pumphouse and screen chamber intake
- •9.4 Cooling water tunnels
- •9.5 Submersible cooling water structures
- •9.6' Maintenance considerations
- •10 Harbours and jetties
- •10.1 General
- •10.2 Types of harbours and jetties
- •10.3 Construction of harbours and jetties
- •11 Loadings
- •11.1 Definitions
- •11.2 Imposed loads due <o plant
- •11.3 Distributed imposed loads
- •II. 6 Reduced loadings in main beams and columns
- •11.4 Cranes
- •11.5 Wind and snow loads
- •12 Steel frames
- •12.1 Steelwork
- •13 Reinforced concrete
- •13.1 General
- •13.2 Formwork
- •13.3 Reinforcement
- •1^.4 Design of reinforced concrete
- •12.2 Design of members
- •12.3 Connections
- •12.4 Protection of steelwork
- •13.5 Movement joints
- •13.6 Curing
- •13.7 Precast concrete
- •14 Prestressed concrete
- •14.1 Prestressing
- •14.2 Prestressed piling
- •14.2 Prestressed piling
- •14.3 Prestressed concrete pressure vessels and containments
- •15 Brickwork and blockwork
- •15.1 General
- •15.2 Bricks
- •15.3 Mortar
- •15.4 Brickwork
- •15.5 Blocks
- •15.8 Openings
- •15.6 Blockwork
- •16 Lightweight walling systems
- •16.1 Sheeting
- •16.2 Insulation
- •16.3 Fixings
- •16.4 Durability
- •17 Roofing
- •17.1 Structural elements
- •17.2 Insulation and weatherproofing layers
- •17.3 Application to power stations
- •17.4 Durability
- •17.5 Rainwater disposal
- •18 Finishes
- •18.1 Floor finish considerations
- •18.2 Types of floor finish
- •18.3 Finishes to walls and ceilings
- •18.4 Wall tiling and other special finishes
- •18.5 Internal painting
- •18^6 External painting
- •19 Turbine hall and boiler house construction
- •19.1 General
- •19.2 Structural considerations
- •19.3 Erection of steelwork
- •19.4 ''Cladding
- •19.5 Ventilation
- •19.6 Floor and wall finishes
- •20 Reactor construction
- •20.1 Reactors
- •20.2 Reactor buildings
- •21.2 Control room building
- •21.3 Gas turbine house
- •21.4 CW pumphouse
- •21.6 Workshops and stores
- •21.7 Offices, welfare blocks, laboratories and similar buildings
- •22 Chimneys, cooling towers and precipitators
- •22.1 Chimneys
- •22.2 Cooling towers
- •22.3 Precipitators
- •23 Architecture and landscape
- •23.1 General power station architecture
- •23.2 Landscape considerations
- •23.3 Preparatory works
- •23.4 Landscape layout
- •24 Regulations
- •24.1 Government instruments
- •24.2 Factories Act
- •24.4 Building regulations
- •24.5 Nuclear station licensing
- •25 Civil engineering contracts
- •25.2 Forms of contract
- •25.3 Contract strategy
- •25.4 Contract placing
- •25.5 Contract administration
- •25.6 Budgetary approval and control
- •26 References
- •Appendix A
- •SUBJECT INDEX

btauon design |
Chapter 2 |
|
58.0m |
|
COAL BUNKERS |
|
AND MILLS |
Fig. 2.21 Layouts showing alternative boiler orientations
to the influence that the choice of fuel and its properties exert on the plant design.
Figures 2.22, 2.23 and 2.24 show how such factors influence both the boiler design and also the choice and layout of auxiliary plant. Such variations can obviously have a major impact on overall station design directly by the addition or omission of equipment, or by the relationship of weight and size of the boiler to the supporting structure and enclosure envelope. Second ary areas such as the storage volume of coal bunkers and the type and capacity rating of auxiliary plant such as coal pulverising mills, fans, etc., are also determined by these factors and can influence some of the principal
overall dimensions of the station layout, particularly the minimum boiler centreline spacing.
6.3 Layout conventions
In reviewing the basic layout concepts outlined, the reader should have identified a number of layout practices which are consistent between all the options discussed. These practices have evolved over the years within the CEGB and have been demonstrated to provide economic and practical designs in a UK situa tion. Such practices are regularly reviewed in relation
82
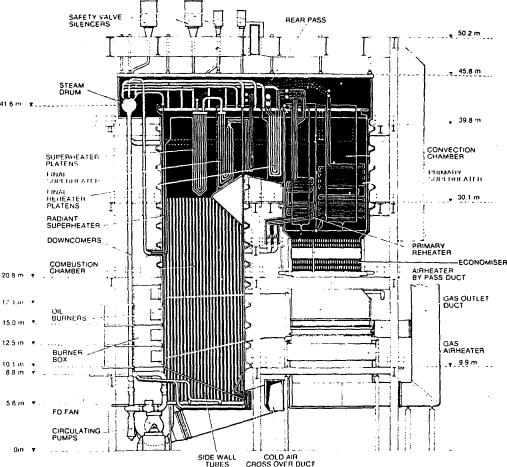
Station layout
I-'ig. 2.22 500 MW oil-fired boiler and auxiliary plant
to new plant designs and operational procedures and amended accordingly, but represent the knowledge gained by years of experience within the CEGB on station design, construction and operation of large fossil-fired units.
6.3.1 The unit principle
The unit principle is the association of a single turbine generator and boiler, together with its immediate auxiliary services, to form a complete, virtually selfcontained generating unit.
Many power station engineers will be familiar with ‘range’ stations where all boilers steam into a common receiver and from which individual turbine-generators take their supplies. Feedwater is similarly returned to a common receiver from which individual boilers draw their supplies, This arrangement gives the maximum flexibility in relation to overall boiler and turbine availability, but CEGB experience is that the reliability of large modern units makes such a provision unecon
omic. It has therefore been CEGB practice for many years to build completely integrated units where the boiler and turbine are matched in capacity.
Many services however remain as station-based systems, e.g., cooling water system, town water ser vices, fuel handling and storage systems, etc., but this does not invalidate the unit concept.
6.3.2Mirror imaging
‘Mirror imaging’ is the complete or partial handling of plant and systems between pairs of boiler/turbine units to give a symmetrical layout about their common centreline. Such a concept is shown in Fig 2.25.
A mirrored design gives an attractive layout but CEGB experience suggests it has many practical dis advantages. It requires the production of two sets of engineering and design details, encourages manufactur ing and construction errors and it potentially precipi tates operator error.
_____ ......... |
83 |

Station desigtf and layout |
Chapter 2 |
COLUMN
CENTRE
LINES
KEY |
|
|
|
1 |
STEAM DRUM |
24 COAL BUNKER |
|
2 |
FO FAN SUCTION DUCT |
2$ PA FAN |
|
3 |
SECONDARY REHEATER ELEMENTS |
26 |
PA FAN DISCHARGE DUCT |
4 |
PRIMARY REHEATER ELEMENTS |
27 |
PA FAN SUCTION DUCT |
5 |
REAR WALL BURNER AREA VENTILATION DUCT |
28 |
FURNACE HOPPER |
6 |
FD DISCHARGE ANO CROSS OVER DUCT |
20 COLD AIR BUS MAIN |
|
7 |
SOOTBLOWER AIR CONNECTION |
30 |
HOT AIR TO MILLS DUCT |
8 |
PRIMARY SUPERHEATER ELEMENTS |
31 |
MAIN AIRHEATER AIR BY-PASS DUCT |
0 FURNACE GAS EXIT HOPPER |
32 |
HOT AIR RECIRCULATION |
|
10 |
SECONDARY SUPERHEATER ELEMENTS |
33 |
MAIN AIRHEATER AIR OUTLET DUCT |
11 |
PLATEN SUPERHEATER ELEMENTS |
34 |
GAS TO MAIN AIRHEATER |
12 |
RADIANT SUPERHEATER |
35 |
SECONDARY AIR BUS MAIN |
13 |
DESUPERHEATERS |
36 |
SECONDARY AIR TO PLENUM CHAMBER |
14 |
PULVERISED FUEL PIPES |
37 |
TERTIARY AIR DUCTS |
15 |
HORIZONTAL CYCLONES |
38 |
PLENUM CHAMBER |
16 |
THREE * WAY DISTRIBUTORS |
30 BUNKER OUTLET VALVE |
|
17 MAIN AIRHEATER AIR INLET DUCT |
40 |
COAL FEEDERS |
|
18 |
MAIN AIRHEATER GAS OUTLET DUCT |
41 |
BALL MILL |
10 MAIN AIRHEATER |
42 |
MAIN STEAM PIPES |
|
20 MILL AIRHEATER GAS OUTLET DUCT |
43 |
DUST PIPES |
|
21 |
HOT GAS TAP |
44 |
OUST VALVES |
22 MILL AIRHEATER GAS INLET DUCT |
45 |
ECONOMISER |
|
23 |
MILL AIRHEATER |
|
|
Fig. 2.23 500 MW coat-fired boiler designed for downshot firing and low volatile fuel
84

Station layout
KEY |
|
|
|
|
|
1 |
STEAM DRUM |
15 PRIMARY REHEATER |
28 VENTURI |
||
2 |
DOWNCOMER A |
15 SECONDARY REHEATER |
» FORCED DRAUGHT FAN |
||
3 |
DOWNCOMERS |
17 |
STEAM PARTITION WALL |
30 |
PRIMARY AIR FAN SUCTION DUCT |
4 |
DOWNCOMER C |
18 |
REAR ENCLOSURE DIVISION WALL |
31 |
PRIMARY AIR FAN |
9 DOWNCOMER 0 |
10 SAFETY VALVE SILENCERS |
32 |
PRIMARY AIR FAN DISCHARGE DUCT |
||
8 FURNACE SIDEWALL |
20 |
COAL BUNKER |
33 |
MILL AIRHEATER |
|
7 |
WATER SEAL |
21 |
BUNKER OUTLET VALVE |
34 |
HOT AIR BUS MAIN |
8 |
ASH HOPPER |
22 |
COAL FEEDER |
35 |
MAIN AIRHEATER |
9 |
DESUPERHEATER |
23 |
PULVERISING MILL |
38 |
GAS OUTLET TO PRECIPITATORS |
10 |
ECONOMISER |
24 |
FOUR - WAY DISTRIBUTOR |
37 |
COAL CONVEYORS |
11 |
PRIMARY SUPERHEATER |
25 |
BURNER |
38 |
DEAERATOR |
12 |
STEAM DIVISION WALL |
28 FORCED DRAUGHT FAN AIR INLET |
39 |
DEAERATOR STORAGE TANK |
|
13 |
PLATEN SUPERHEATER |
27 COMBUSTORS |
40 RESERVE FEED WATER TANKS |
||
14 |
SECONDARY SUPERHEATER |
|
|
|
|
Fig. 2.24 500 MW coal-fired boiler designed for frontwall firing and UK bituminous fuel
85

Station design and layout |
Chapter 2 |
Current station layout practice within the CEGB does not favour mirror imaging plant layout but is based on replication of complete boiler/turbine packages.
6.3.3Turbine island concept
It is conventional practice for turbine-generators to.be supported by foundation blocks which are elevated above the basement or ground floor level of the power station. The height at which the turbine-generator is located is termed the operating floor and the designer has to decide whether to install a complete floor throughout the turbine house at this level or just to elevate the turbine-generator and its immediate walk ways and local laydown areas for small turbine com ponents. The latter concept is shown in Fig 2.26.
Elevation to operating floor level of the turbine
generator alone is termed an island |
layout |
and has |
been adopted by the CEGB as its |
preferred |
option. |
This preference is based on the need to provide clear and unhindered access to main plant items. The layout allows direct crane access to all parts of the turbine hall, good maintenance access and efficient lighting and
ventilation to all areas. Defined laydown areas for heavy plant are provided at basement level as are clearways for personnel and equipment movement.
A continuous operating floor level throughout the turbine hall requires that the supporting structure be designed to accommodate plant loads imposed when the unit is dismantled for maintenance. Additionally, separate provisions for plant maintenance, ventilation and lighting arc required for the basement area or any intermediate floor levels.
The benefits claimed for the continuous operating floor are the opportunities for equipment location in intermediate floor levels, better facilities for turbine maintenance, ample laydown space local to the turbine and the generally pleasing and uncluttered appearance of the turbine hall.
Overall, the CEGB considers that the island concept provides the most economic and practical plant layout, and gives the best access and facilities for plant maintenance.
, The appearance of the turbine hall is a question of preference to be exercised by an individual utility, but the CEGB approach is that the station should be seen
86

' v U.5U eotour photograph between pp 66 and pp 67)
layout Station