
ортопеда_8_занятие_Полимерные_материалы
.pdfЗанятие №8 Полимерные материалы
Полимерные материалы (пластмассы) - это материалы на основе полимеров
(высокомолекулярных соединений), в состав которых может входить значительное число компонентов как органического, так и минерального происхождения, обеспечивающих реализацию в материале широкого спектра разнообразных свойств.
Показания к применению
1 . Для изготовления базисов съемных пластиночных протезов, седловидных частей дуговых протезов — базисные материалы (этакрил, бакрил, фторакс).
2. Для исправления (перебазирования) протезов, их починки, изготовления временных протезов, шин, моделей, индивидуальных ложек (протак-рил, протакрил-М, редонт). 3 . Для изготовления челюстно-лицевых протезов, обтураторов, пелотов, мягких амортизирующих подкладок под базисы протезов (эладент, ортосил-М).
4. Для изготовления искусственных зубов
Полимерные материалы характеризуются сложным составом, обязательной частью которого, связующим, является синтетический полимер. В подавляющем большинстве случаев полимер объединяет компоненты в единое целое и поэтому называется связующим, в качестве которого могут использоваться все разновидности полимеров, то есть термопластичные и термореактивные, олигомеры и соолигомеры, полимеры, сополимеры и высокополимеры. Кроме того, в ПМ могут входить различные наполнители и вещества, обеспечивающие те или иные технологические и потребительские качества (текучесть, пластичность, плотность, прочность, долговечность, негорючесть, тепло– или электропроводность, звукопоглощение и пр.).
Полимеры - вещества, молекулы которых состоят из большого числа повторяющихся звеньев. Основными исходными соединениями для получения полимерных материалов являются мономеры и олигомеры. Для облегчения переработки полимеров и придания им комплекса требуемых свойств в их состав вводят различные компоненты - наполнители, пластификаторы, стабилизаторы, красители, сшивагенты, антимикробные агенты.
Наполнители - вещества, придающие изделию прочность, твердость, теплопроводность, стойкость к действию агрессивных сред, липкость и другие физико-механические свойства. Наполнители по происхождению делятся на органические и минеральные, по структуре на порошкообразные и волокнистые. В качестве наполнителя применяют древесную муку, стекловолокно, порошки различных металлов, минералов.
Пластификаторы - вещества, придающие материалам пластичность в процессе обработки, и обеспечивающие эластичность готового материала. В качестве пластификаторов используют дибутилфтолат, диоктилфтолат и другие.
Стабилизаторы - вещеста, тормозящие старение полимеров. Применяются антиоксиданты, препятствующие окислению;
фотостабилизаторы, ингибирующие фотолиз и фотоокисление; антиарды, препятствующие старению под действием излучения.
Красители применяют для окрашивания материалов, для получения эстетического эффекта и имитации мягких и твердых тканей. Для окраски полимеров используют различные органические красители и пигменты.
Сшивагенты - вещества, которые образуют поперечные связи между макромолекулами для повышения прочности полимерных материалов.
Антимикробные агенты - добавки, препятствующие зарождению и размножению микроорганизмов в полимерных материалах.
Антиоксиданты - это антиокислители, природные или синтетические вещества, способные тормозить или предотвращать процессы, приводящие к старению полимеров.
Классификация полимеров
1. По действию нагревания на свойства пластмасс:
-термопласты (при повышении температуры размягчаются, состав при этом не изменяется);
-обратимые термопласты (приобретают пластичность при нагревании, а при понижении температуры возвращаются в твердое состояние, при этом состав не изменяется). К ним относятся полиметилметакрилат, полистирол, капрон, поливинилхлорид, полиэтилен, фторопласт, поликарбонат и др.;
-реактопласты (термореактивные; необратимые полимеры), при нагревании до температуры 150-170°С, а иногда и без термического воздействия они теряют способность вторично размягчаться, при этом некоторые компоненты претерпевают химическое изменение или разрушаются. К этому виду пластмасс относятся бакелит, аминопласты, фенопласты и др.;
-термостабильные, при нагревании не переходят в пластичное соединение и сравнительно мало изменяются по физическим свойствам вплоть до температуры их термического разрушения.
2. По составу смеси: однокомпонентные, многокомпонентные, сополимерные (полимеры, содержащие в одной макромолекуле несколько типов мономерных звеньев).
3. По типу полимера:
-линейные (целлюлоза);
-разветвленные, имеют структуру, подобную крахмалу и гликогену;
-пространственные (сшитые), построены в основном как сополимеры;
-регулярные (целлюлоза);
-нерегулярные (нуклеиновые кислоты, белки).
4. По типу наполнителя.
5. По эксплуатационным характеристикам.
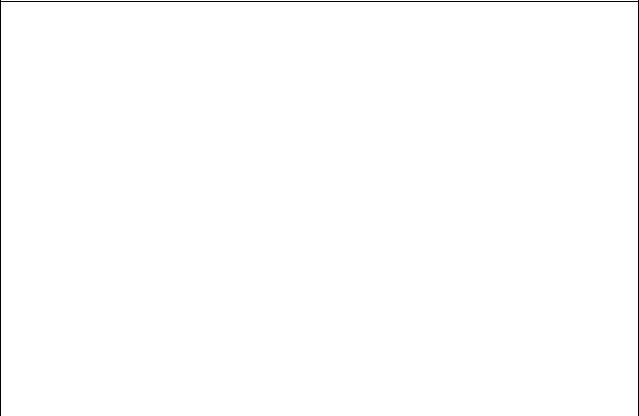
6. По числу атомов, входящих в молекулу: низкомолекулярные,
высокомолекулярные, органические (полиэтилен, полиметилметакрилат, биополимеры), неорганические (силикаты).
7. По химической структуре мономера: гомоцептные, имеющие связи углерод-углерод и гетероцептные, имеющие кроме углеродных связей связи с атомами кислорода, серы, галогенами.
Классификация полимеров по назначению:
1.Основные, используемые для изготовления съемных и несъемных зубных протезов:
- базисные (жесткие) полимеры; - эластические полимеры, или эластомеры (в том числе силиконовые,
тиоколовые и полиэфирные оттискные массы); - полимерные (пластмассовые) искусственные зубы;
- полимеры для замещения дефектов твердых тканей зубов (материалы для пломб, штифтовых зубов и вкладок); - полимерные материалы для временных несъемных зубных протезов; - полимеры облицовочные;
- полимеры реставрационные (быстротвердеющие).
2.Вспомогательные.
3.Клинические.
Классификация полимерных материалов для базисов съемных зубных протезов (в соответствии с международным стандартом №1567 и ГОСТ Р 51889-2002) представлена в таблице №3
Классификация полимерных материалов для базисов съемных зубных протезов
Акриловые полимермономерные материалы |
Термопласты, Тип |
|||||||
|
|
|
|
|
|
|
3 |
|
|
|
|
|
|
|
|
|
|
Инициирование |
Инициирование |
Для |
|
Для |
||||
полимеризации внешней |
полимеризации |
литья |
|
формов |
||||
|
энергией |
|
химической реакцией |
под |
|
ания из |
||
|
|
|
давле |
|
|
|||
|
|
|
|
|
|
|
листов |
|
|
|
|
|
|
|
|
|
|
Горячег |
Микров |
Свето |
Холодного отверждения, |
|
|
|||
нием |
|
ых |
||||||
о |
олновог |
|
|
|
|
|
||
вого |
|
Тип 2 |
|
|
|
|||
отверж |
о |
|
|
|
загото |
|||
отверж |
|
|
|
|
|
|||
дения, |
отверж |
|
|
|
|
|
|
|
Для |
|
Для заливки |
|
|
вок |
|||
дения, |
|
|
|
|||||
|
дения, |
формовани |
|
|
|
|||
Тип 1 |
|
|
|
|
|
|||
|
Тип 4 |
я |
|
|
|
|
|
|
|
Тип 5 |
|
|
|
|
|
||
|
|
|
|
|
|
|
|
|
|
|
|
|
|
|
|
|
|
Пластмассы в стоматологии
Пластмассы, применяемые в стоматологии для изготовления коронок и облицовки несъемных зубных протезов (штамповано-паяных и цельнолитых). Одними из самых распространенных являются пластмассы «Синма-74», «Синма-М», «Изо-зит» и др. Они представляют собой акриловую пластмассу горячего отверждения типа порошок - жидкость Материалы типа «Синма74» представляют собой комплект порошок - жидкость, относятся к устаревшим маркам. Порошок - суспензионный «привитой» фторсодержащий сополимер, дающий флюоресцирующий эффект; жидкость - метил-метакрилат, ингибированный гидрохиноном. Выпускаются де-сятицветный и одноцветные комплекты в соответствии с единой расцветкой АО «Стома». В комплект входят концентраты красителей (белый, желтый, коричневый, серый) для добавления к порошку основного цвета, с целью получения желаемого оттенка для корректировки шейки зуба или режущего края. Пластмасса Синма-М» является улучшенной модификацией «Синма-74» и позволяет использовать более совершенные технологии изготовления металлопластмассовых несъемных протезов. Порошок - суспензионный «привитой» фторсодержащий сополимер. Жидкость представляет собой смесь акриловых мономеров и олигомеров. Благодаря наличию олигомера увеличено время жизнеспособности массы в пластичном состоянии (до 30 минут), что позволяет моделировать облицовку непосредственно на металлическом каркасе. Пластмассу Синма-М», как и Superpont («Spofa Dental», Чехия) и более совершенный аналог Isosit (Ivoclar, «Vivadent», Лих-тенштен), можно использовать для изготовления протезов методом моделирования облицовки непосредственно на металлическом каркасе с последующей полимеризацией пластмассы Синма-М в аппарате типа ПС-1 или «Ivomat» под давлением 5 атм, температуре 120° С в течение 10 минут. Также можно изготавливать мостовидные протезы более старым методом формирования пластмассы в кювету с последующей полимеризацией на водяной бане. В комплект «Синма-М» входят порошок-дентин 8 цветов, порошок-эмаль 2 цветов, жидкость, концентраты красителей и набор листов из целлофана. Материал обеспечивает более высокие эстетические свойства зубных протезов. При использовании «Синма-М» рекомендуется использовать специальные лаки - грунты (ЭДА-03, АО «Стома») для маскировки цвета металлического каркаса и создания более надежного соединения межу пластмассовой облицовкой и металлом каркаса. «Изозит» - группа материалов, не являются метилметакрилатами, их основой является уретандиметакрилат, они в большей степени удовлетворяют современным требованиям в отношении эстетики, цветостойкости, устойчивости к истиранию. Изготовление металлопластмассовых протезов из «Изозита» осуществляется следующим образом. Изготавливается гипсовая разборная комбинированная модель. Моделируется восковая композиция коронки, создаются ретенционные пункты (для механической связи металла и пластмассы). Осуществляется это установлением бусин (перл) из беззольных пластмасс, которые посыпаются на участки протеза, где предполагается нанесение пластмассы и фиксируются при помощи специального клея (микроадгезива). Подготовленную таким образом воскопо-лимерную конструкцию заменяют на металлическую. Способ нанесения облицовочного материала «Изозит»: вначале наносится грунтовый слой и конструкция помещается в специальный аппарат на 5-7 минут при температуре 120е С и давлении 6 атм. Далее по всей поверхности грунтового слоя наносится дентинная, а у режущего края - дополнительно прозрачная масса. Для получения различных оттенков пластмассы можно использовать имеющийся в наборе краситель изозит-интенсив. Перед окончательной полимеризацией вся поверхность покрывается тонким слоем активированного изозит-флюида, предотвращающего возникновение ингибированного слоя при полимеризации. Пластмассу полимеризуют в аппарате «Ивомат» на водяной бане в течение 7 минут под давлением 6 атм и при температуре 120°. Металлопластмассовые протезы из «Изозита» прочны и эстетичны. Их можно восстанавливать непосредственно в полости рта, используя в качестве пломбировочного материала Гелиозит или Гелиокор.
Пластмассы делятся на самотвердеющие, или холодного отвердения, т.е. затвердевающие при комнатной температуре, и пластмассы горячего отвердения, затвердевающие при термической обработке.
Соотношение порошок-жидкость
Большое значение имеет правильное соотношение порошокжидкость (по весу в % 2,0/1,0, по объему в %
1,6/1,0). Слишком большое количество порошка может привести к недостаточному заполнению мономером свободного пространства между его гранулами и в конечном итоге привести к ослаблению материала. Слишком большое количество мономера вызовет чрезмерную полимеризационную усадку и снижение качества прилегания протеза к протезному ложу.
Добавки к порошку склонны к оседанию на дно контейнера, поэтому перед использованием важно встряхнуть контейнер для гарантии равномерного распределения компонентов порошка.
Процесс схватывания пластмассы проходит несколько стадий:
первая стадия – насыщения, заключается в смешивании порошка и жидкости, при этом не допускается наличия, как свободной жидкости, так и порошка. Оптимальным является объемное соотношение мономера к полимеру 1:3; вторая стадия – песочная, масса напоминает смоченный водой песок;
третья стадия – тянущихся нитей, масса становится более вязкой, а при её растягивании появляются тонкие нити; четвертая стадия – тестообразная, отличается еще большей плотностью и исчезновением тянущихся нитей при разрыве;
пятая стадия – резиноподобная или стадия затвердевания пластмассы. Работают с пластмассой в тестообразной стадии. Пластмассы горячего
отвердения при правильном режиме полимеризации содержат 0,5% , быстроотвердевающие – 3,5% остаточного мономера.
Формование пластмассой
Заготавливают по описанной выше методике пластмассу. Затем чистыми руками берут нужное количество пластмассового теста и формуют в кювету.
Предварительно зубы, кламмеры обезжиривают мономером. Поверх пластмассы покрывают слоем целлофана, увлажненного в воде. Верхнюю часть кюветы надевают на основание и подвергают прессованию.
Чтобы не повредить модель, прессовку ведут осторожно. При работе с пластмассой модель загипсовывают обратным способом и, следовательно, она оказывается в верхней части кюветы и служит контрформой. Поэтому лучше ставить кювету основанием к винту пресса и вести прессование без применения усилий.
После прессовки кювету открывают и, удалив излишки пластмассы, снова ставят под пресс на 5—10 минут. Вслед за этим кювету помещают в бюгель и закрепляют в нем.
При комбинированном способе загипсовки, когда передние зубы покрыты валиком, а коренные зубы и кламмеры переходят в контрформу, формовку проводят одновременно в обеих частях кюветы. После прессования и контроля снимают целлофан, лишнюю пластмассу срезают. Границы соединения пластмассы смазывают мономером для лучшего соединения и кювету ставят под пресс для окончательной прессовки. После контрольной прессовки кювету фиксируют в бюгель и приступают к полимеризации пластмассы (см. Полимеризация).
Выемка пластмассовых протезов из кювет. После полимеризации и полного охлаждения кюветы раскрывают бюгель.
Выемку протезов следует производить осторожно и придерживаться определенных правил. Снимают крышку той части кюветы, где загипсован протез, шпателем делают надрез вдоль стенок кюветы и удаляют весь гипс с протезом. Затем шпателем откалывают небольшие куски гипса, постепенно освобождая протез от гипса.
Протезы из пластмассы трудно извлечь из кюветы после полимеризации, так как полимеризация проводится при температуре 100° и гипс при этом становится еще прочнее. Полное охлаждение кювет на воздухе предохраняет от деформации, способствует разрыхлению гипса и облегчает выемку протезов из кювет. Несоблюдение этих правил ведет к деформации, а иногда и к поломке протезов. Для выдавливания протеза с гипсом из кювет имеется пресс, облегчающий выемку пластмассовых протезов.
Методы и режим полимеризации пластмассы. Последствия его нарушений. Виды пористости пластмасс
Основные методы получения пластмасс - полимеризация и поликонденсация. При полимеризации молекулы мономеров связываются в полимерные цепи без высвобождения побочных продуктов реакции (вода,
спирт и др.). При поликонденсации происходит образование некоторых побочных, не связанных с полимером веществ.
Полимеризация имеет три стадии.
1.Активация молекул мономера (разрыв двойных связей, распад инициатора па радикалы, имеющие свободные валентности, по месту которых и происходит рост полимерных цепей).
2.Рост полимерной цепи из активных центров (на концах цепей постоянно присутствуют свободные радикалы, обеспечивающие рост полимерной цепи). При соединении мономолекул с одной двойной связью образуются линейные полимеры. Если мономеры имеют больше одной двойной связи или под воздействием активных веществ образуются поперечные связи, полимер приобретает "сшитый" вид.
3.Окончание процесса полимеризации, обрыв полимерной цепи при прекращении действия факторов, вызывающих полимеризацию. Полимеры, полученные при полимеризации различных мономеров, обладающих несходными свойствами, носят название сополимеров.
Режим полимеризации
Процесс полимеризации преследует цель перевести пластмассу из пластического в твердое состояние. Мономер - полимерная смесь, может затвердевать и в обычных условиях, при комнатной температуре, но для этого потребуется значительное время. Для ускорения процесса полимеризации необходимо повысить температуру.
1)После контрольной прессовки обе части кюветы стягивают специальным фиксатором (бюгелем) и подвергают пластмассу в кювете полимеризации. Кювета закрывается и погружается в воду комнатной температуры, и на электрической плитке или газовой горелке, постепенно, в течение 45-60 минут, доводится до 80°, и от 80° до 100° - 45 минут. При этом, во время повышения температуры до 60° С процесс полимеризации протекает плавно, при температуре выше 65° С остаточная перекись бензоила быстро расщепляется и скорость полимеризации возрастает. В этот период за счет полимеризации мономера масса уменьшается в объеме. По достижении 6568° С масса начинает увеличиваться в объеме вследствие термического расширения. Расширение в данном случае является основным фактором, компенсирующим усадку при полимеризации, и изделия получаются меньше восковой модели всего на 0,2-0,5 % в линейных размерах.
2)Следует учесть, что полимеризация есть цепной радикальный процесс, и повышение температуры приводит к увеличению молекулярной массы
полимера, что вызывает изменения физико-химических свойств (прочности и др.), поэтому для достижения оптимальной молекулярной массы заключительную стадию полимеризации проводят при температуре 100е выдерживая точно 30-45 минут.
3) Затем огонь выключается и кювета находится в воде до полного остывания (медленное охлаждение) в течение 40-60 минут.
Различают следующие виды пористости:
ГАЗОВАЯ пористость возникает в толще пластмассы, когда темпераура внутри пластмассы резко повышают до 100 С. Мономер быстро переходит в парообразное состояние, внутри массы при этом возникают пузырьки,которые из-за малого времени и высокой вязкости полимеризующейся массы не имеют возможности улетучится и остаются внутри протеза.
ГРАНУЛЯРНАЯ ПОРИСТОСТЬ выглядит в виде меловых полос или пятен, она возникает как результат недостатка мономера, Наиболее часто мономер улетучивается из открытой минзурки, где созревает пластмассовое тесто. Или при контрольном раскрытии кюветы, и длительном нахождении ее в таком состоянии. Поверхность открытой массы высыхает, преобретает матовый оттенок. Формовка такой массой приводит к появлению шеловых полос и пятен, а так же гранулярная пористость резко ухудшает физикохимические свойства пластмассы.
ПОРИСТОСТЬ СЖАТИЯвозникает при недостаточном давлении внутри формы, вследствии чего некоторые места формы остаются пустыми, этот вид пористости наблюбаются при концевых истонченных краях протеза, а так же когда нет соединения зубов с базисом.
Остаточный мономер
Оставшаяся в полимере часть исходного мономера, не вошедшая в состав полимерных молекул, называется остаточным мономером. Его количество характеризует уровень биосовместимости данного полимерного материала.
Внутренние напряжения в пластмассе. Предупреждение их возникновения
Внутреннее остаточное напряжение - приводит к растрескиванию.
Возникает при нарушении режима полимеризации (длительное, более 1 часа нахождение в кипящей воде). Протез подлежит переделке.
Остаточные напряжения. В пластмассовых изделиях, независимо от способа их приготовления, всегда имеются значительные остаточные напряжения. Внутренние напряжения в акриловых протезах вызывают их преждевременное растрескивание и коробление. Протез представляет собой армированное изделие, в котором зубы, кламмеры, дуги и др. детали являются арматурой. Температурные изменения размеров материалов арматуры меньше, чем пластмассы в 10-20 раз.
В местах монтажа арматуры полимер растягивается при охлгшдении и возникают местные напряжения. Большее напряжение возникает около фарфоровых зубов, чем пластмассовых. Таким образом, наличие арматуры повышает вероятность появления трещин.
К внутренним напряжениям приводит различная толщина отдельных частей изделия. Толстые части дают большую усадку по абсолютной величине, тонкие - меньшую, в связи с чем в местах перехода появляются напряжения. Остаточные напряжения возникают в процессе изготовления полимера. При нагревании кюветы вначале повышается температура наружного слоя пластмассы и затвердевание начинается в поверхностных слоях, сопровождаясь усадкой. Внутренние слои вначале имеют более низкую температуру. Опережение затвердевания наружного слоя в пластмассах горячей полимеризации приводит к возникновению в нем внутренних напряжений растяжения. В дальнейшем затвердевание внутренних слоев вызывает уменьшение их объема и они оказываются под воздействием растягивающего напряжения, т.к. к этому времени наружные слои приобретают жесткость.
Поскольку напряжения обязательно возникают в процессе изготовления протеза, их следует снимать. Для этого протез следует обработать при определенном температурно-временном режиме в различных средах. При этом улучшаются механические свойства изделия, стабилизируются геометрические размеры и увеличивается срок эксплуатации. В качестве сред теплоносителей используют воздух и жидкости. Из различных видов термической обработки наиболее эффективным является отжиг, который надо проводить при такой температуре, когда изделие еще не деформируется.
М. М. Гернер и М. А. Нападов предлагают следующую термообработку протезов. Отжиг в термошкафу, нагревая изделие со скоростью 0,7-1,5°С в минуту до 80±3°С. После 3-4 часовой выдержке при этой температуре изделие медленно охлаждают до 30-40 С.
Растрескивание. Одним из самых распространенных видов разрушения пластмасс является возникновение трещин на поверхности материала при одновременном действии напряжения и окружающей среды.
При растрескивании, в зависимости от величины и характера распределения напряжений, возникает одна магистральная трсгцнпа илм сстк?» мел ких трещин. При воздействии больших напряжений образуется обычно одна магистральная трещина, при малых напряжениях возникает множество трещин. Растрескивание проявляется особенно быстро при воздействии органических растворителей (этиловый спирт, ацетон, бензол и др.).
Внутренние напряжения через некоторое время могут привести к трещинам на поверхности базиса. Например, можно часто видеть трещины, радиально расходящиеся в пластмассовом базисе от шеек фарфоровых зубов. Если протез, которым пользуется больной, часто высыхает при извлечении изо рта и вновь увлажняется, то со временем могут возникнуть трещины в результате чередующегося сжатия (при высыхании) и расширения (при поглощении воды). Базисные материалы с увеличенной водопоглащаемостыо более склонны к растрескиванию. Если при полимеризации формовочная масса контактировала с водой, то получается полимер с повышенной водопоглощаемостью.
Пластмассы горячего отвердения для базисов протезов: Этакрил, Бесцветная, Фторакс
Акрилаты – на основе акриловой и метакриловой кислот. Несколько десятилетий удерживают первенство в стоматологии благодаря своим главным свойствам: относительно низкой токсичности, удобству переработки, химической стойкости, механической прочности, эстетическим качествам. Большинство материалов в качестве основного ингредиента содержат полиметилметакрилат (ПММА).
Представители:
а) «Этакрил» – синтетический материал на основе акрилового сополимера, окрашенного под цвет слизистой оболочки полости рта; б) «Фторакс» – пластмасса горячего отверждения типа порошок-жидкость на
основе фторсодержащих акриловых сополимеров. Состоит из порошка и жидкости. Протез из «Фторакса» обладает повышенной прочностью и эластичностью и хорошо гармонирует по цвету с мягкими тканями полости рта; в) «Акронил» – сшитая и привитая пластмасса;
г) бесцветная пластмасса – на основе очищенного от стабилизатора полиметилметакрилата, содержащего антистаритель (тинувин). Состоит из порошка и жидкости.